
Want to create or adapt books like this? Learn more about how Pressbooks supports open publishing practices.

Chapter 1: Introduction to DFMA
The history of dfma.
Review the DFMA timeline below to become familiar with the most significant milestones leading to the development and use of DFMA in engineering practices. Select the arrow on the right side of the interactive timeline to progress through the decades. You can also select the icon in the upper right corner to expand your view.
So, what is DFMA?
Design for Manufacture and Assembly (DFMA) is an engineering methodology which focuses on reducing time-to-market and total production costs by prioritizing the following during the early design phases of the product life cycle.
- Ease of manufacture for the product’s parts.
- Simplified assembly of those parts into the final product
DFMA is comprised of two components: Design for Manufacturing (DFM) and Design for Assembly (DFA).
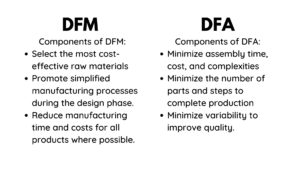
The goal is to design a product which makes the customer happy and is the lowest overall cost, but there are other factors as well:
- Best material for the process and product
- Minimum number of components
- Easy to acquire to the components
- Easy to assemble
- Easy to maintain the device
- Easy to recycle at the end of the product’s life
The product starts and ends with the customer. It could be called the voice of the customer, stakeholder input/analysis, customer request, scope of work, or critical quality requirements. Learn more about how to manufacture success by reviewing the following plan by David M. Vranson: A Plan for Manufacturing Success (2011)
Boothroyd Dewhurst, Inc. (2018). What is DFMA? [Video]. YouTube. https://www.youtube.com/watch?v=H6XtXCvhaec
Boothroyd Dewhurst, Inc. (2010). Case study: Desgin in cost reduction. Quality Magazine. Retrieved on May 8, 2023 from https://www.qualitymag.com/articles/84738-case-study-design-in-cost-reduction
DFMA (2023). How do you reduce cost while still achieving function, reliability, and time to market objectives? Retrieved on May 8, 2023 from https://www.dfma.com/
Dong, D., Zou, Y., Pan, H., Zhou, G., Feng, Y., & Tang, Y. (2023). DFMA-oriented modular and parametric design and secondary splitting of vertical PC components. Scientific Reports, 13. https://doi.org/10.1038/s41598-023-30192-z
Favi, C., Mandolini, M., Campi, F., Cicconi, P., Raffaeli, R., & Germani, M. (2021). Design for manufacturing and assembly: A method for rules classification. Advanances on Mechanics, Design Engineering, and Manufacturing III. https://doi.org/10.1007/978-3-030-70566-4_56
Formentini, G., Rodriguez, N., & Favi, C. (2022). Design for manufacturing and assembly methods in the product development process of mechanical products: A systematic literature review. The International Journal of Advanced Manufacturing Technology, 120. https://doi.org./10.1007/s00170-022-08837-6
Goldense, B. (2022). A history of design for manufacturing and assembly. MachineDesign. Retrieved on June 23, 2023 from https://www.machinedesign.com/automation-iiot/article/21213546/a-history-of-design-for-manufacturing-and-assembly
Liu, H., Zhang, Y., Lei, Z., Li, H., Han, S. (2021). Design for manufacturing and assembly: A BIM-Enabled generated framework for building panelization design. Smart Manufacturing for Industrialized Construction. https://doi.org/10.1155/2021/555455
Maverick, J. (2023). Is it more important for a company to lower costs or increase revenue? Investopedia. Retrieved on May 8, 2023 from https://www.investopedia.com/ask/answers/122214/company-it-more-important-lower-costs-or-increase-revenue.asp
de Oliveira, S., dos Santos, M., Kieling, A. (2021). The integration of DFMA and reverse engineering applied to a landing gear redesign. Journal of Engineering and Technology for Industrial Applications, 7 (31). https://doi.org/10.5935/jetia.v7i31.775
Roxas, C., Bautistia, C., Cruz, O., Dela Crus, R., De Pedro, J., Bungca, J., Lejano, B., & Ongpeng, J. (2023). Design for manufacturing and assembly and design for deconstruction in the construction industry: Challenges, trends, and developments. Buildings, 13 (5). https://doi.org/10.3390/buildings13051164
Siemens (2023). Design for manufacturing and assembly. Retrieved on May 8, 2023 from https://www.plm.automation.siemens.com/global/en/our-story/glossary/design-for-manufacturing-and-assembly-dfma/53982
Design for Manufacture and Assembly by Roberta Gagnon and Andrea Bearman is licensed under a Creative Commons Attribution 4.0 International License , except where otherwise noted.
Share This Book
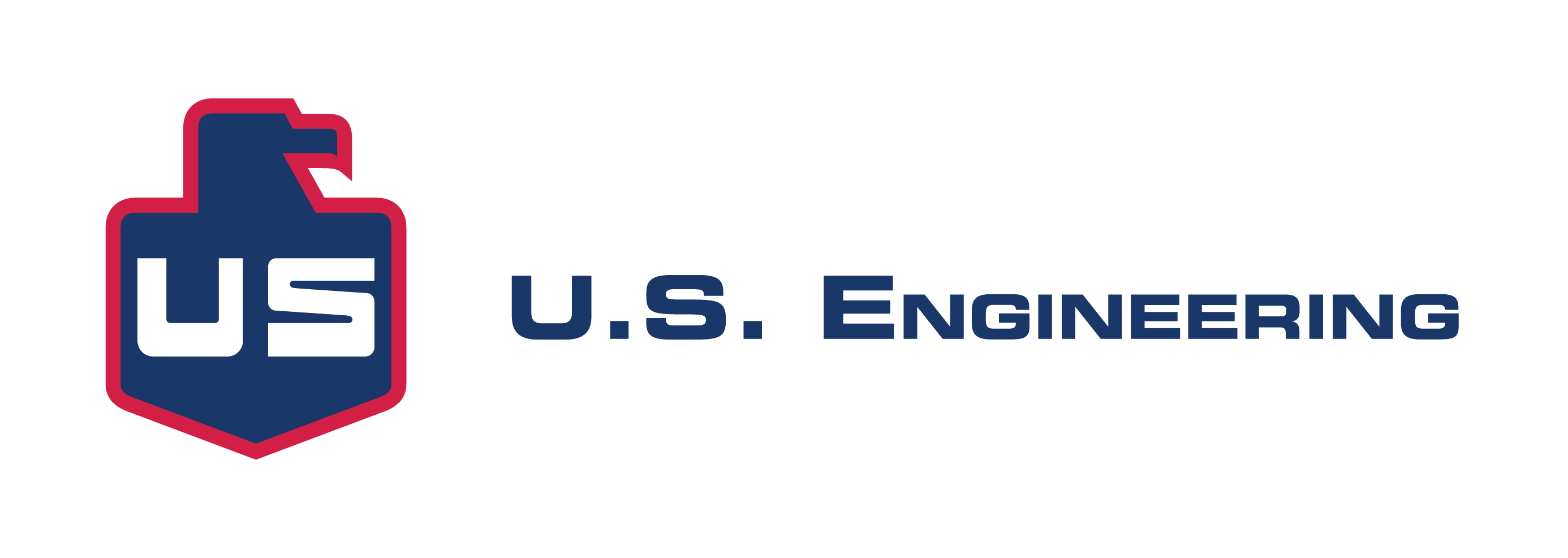
NEWS & INSIGHTS > Thought Leadership > A Case Study in Design for Manufacturing and Assembly
A Case Study in Design for Manufacturing and Assembly
Aug 06, 2021
U.S. Engineering
by Jeff Kiblen , Associate Vice President, U.S. Engineering Innovations
Design for Manufacturing and Assembly (DfMA) is one method U.S. Engineering Innovations (USEI) is implementing in our quest to reimagine ways to execute construction projects. I introduced DfMA and talked about how we’re using it in my first article in this series .
This article examines a recent project that used DfMA to produce a duct module component. Our design partners at Henderson Engineers worked with a client who was interested in using modular design and construction in their HVAC airside systems. Because of its potential for a repeatable floor plan, which could be mirrored for left and right applications, this project was a viable candidate for DfMA. We could design, manufacture and assemble the same duct modules for both configurations.
Design for Manufacturing and Assembly in Practice
Our process with Henderson began as an exercise to find a duct size that made the most effective use of USEI’s standard metal coil widths. The right size would drive out waste and maximize our machine capacities. Simultaneously, Henderson ran all the critical engineering calculations to establish the most flexible size module for their designs.
Once the basis of the design was established, our virtual construction teams consolidated the design content and coordinated with structure and ceiling to make everything fit within the envelope. They then converted that BIM content into buildable components for our shop floors.
Investment in Manufacturing Infrastructure
A key factor that enables us to work closely and seamlessly with our design partners on DfMA projects like this one is our commitment to improving our manufacturing infrastructure. For years we’ve invested in the machinery on the floors of our manufacturing facilities. We’ve invested in the software that communicates with that machinery. And we’ve invested in the teams that code the software and operate the machines.
Thanks to those investments, DfMA projects like this one are true joint efforts: we’re able to drive designs to work best within our machinery’s capabilities, all the while being completely attentive to meeting client needs.
As Henderson’s Sean Turner notes in his article about this case study, the owner’s goals in this case were to reduce costs and improve schedule. USEI helped achieve those goals by driving a common design and size for all of the owner’s store configurations and by performing 70+% of the mechanical work in our facility. As a result, we removed almost three weeks from the original build schedule.
A Sustainable Future in Construction
DfMA dramatically reduces the margin of error. From design to manufacturing to installation, the process is safer and more reliable than the traditional approach. But the process also improves sustainability, a topic USEI and Henderson take seriously. We work in a historically wasteful industry and are actively seeking out ways to minimize project excess. DfMA, in its effort to maximize efficiency, is a design-build method that reduces elements of the manufacturing process that end up in landfills.
Whether designing shipping frames that become the supplemental hanging steel on site after delivery, or repurposing modules like the ones we created on this project for completely different builds, we see DfMA as a method of sustainability. And we’ll continue to explore this approach on future builds.
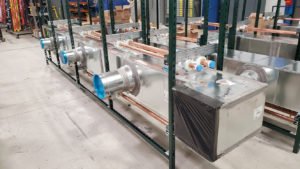
Jeff Kiblen is Associate Vice President of U.S. Engineering Innovations and K-Malt, a wholly owned subsidiary. Starting as a pipefitter apprentice in Kansas City, he spent a decade in the field working his way up to superintendent. From there, because of his passion for technology and problem solving, he pivoted to virtual construction and building information modeling. Today he and his family reside in Colorado.
Related Posts
See where our innovative thinkers and expert collaborators can take you..
Design for manufacture and assembly: Case studies in its implementation
- Published: May 1991
- Volume 6 , pages 131–140, ( 1991 )
Cite this article
- D. J. Gerhardt 1 ,
- W. R. Hutchinson 1 &
- D. K. Mistry 1
628 Accesses
7 Citations
3 Altmetric
Explore all metrics
This paper reviews the rapid and successful implementation of design for manufacture and assembly (DFMA) at Ingersoll-Rand. The relationship of DFMA to simultaneous engineering is discussed.
This is a preview of subscription content, log in via an institution to check access.
Access this article
Price includes VAT (Russian Federation)
Instant access to the full article PDF.
Rent this article via DeepDyve
Institutional subscriptions
Similar content being viewed by others
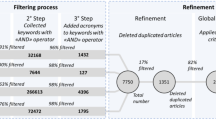
Design for manufacturing and assembly methods in the product development process of mechanical products: a systematic literature review
Redesign methodology for mechanical assembly.
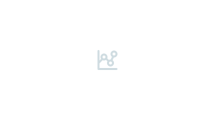
Integrated product-process design to suggest appropriate manufacturing technology: a review
S. Munro, MTS for Productivity, Troy, MI 48084.
G. Boothroyd and P. Dewhurst, “Product design for assembly”, Boothroyd Dewhurst Inc., Wakefield, RI 02879, 1987.
Google Scholar
“Design for improved manufacturability and productivity”, Society of Manufacturing Engineers, Dearborn, MI 48121, September 26–27, 1989.
W. Eureka and N. Ryan, “The customer-driven company, managerial perspectives on QFD”, American Supplier Institute, Dearborn, MI, 1988.
G. Boothroyd, C. Poli and L. Murch, Automatic Assembly , Marcel Dekker, New York, 1982.
M. Andreasen, S. Kahler, T. Lund and K. Swift, Design for Assembly , Springer-Verlag, New York, 1988.
D. Gerhardt and T. Sills, ‘Microprocessor control for diesel powered equipment”, Society of Automotive Engineers paper 87077, 1987.
Download references
Author information
Authors and affiliations.
Portable Compressor Division, Ingersoll-Rand Company, 501 Sanford Avenue, 27028-0868, Mocksville, North Carolina, USA
D. J. Gerhardt, W. R. Hutchinson & D. K. Mistry
You can also search for this author in PubMed Google Scholar
Rights and permissions
Reprints and permissions
About this article
Gerhardt, D.J., Hutchinson, W.R. & Mistry, D.K. Design for manufacture and assembly: Case studies in its implementation. Int J Adv Manuf Technol 6 , 131–140 (1991). https://doi.org/10.1007/BF02601436
Download citation
Accepted : 14 July 1990
Issue Date : May 1991
DOI : https://doi.org/10.1007/BF02601436
Share this article
Anyone you share the following link with will be able to read this content:
Sorry, a shareable link is not currently available for this article.
Provided by the Springer Nature SharedIt content-sharing initiative
- Manufacture
- Productivity
- Simultaneous engineering
- Development teams
- Find a journal
- Publish with us
- Track your research
- Deutsch (DE)
Design for Manufacturing Examples: Real-Life Engineering Case Studies

Key Takeaways:
- More than 70% of a part’s cost can be locked in during the early design phase
- Adopt a robust DFM process using digital manufacturing simulation tools to address cost, sustainability, and innovative design iterations simultaneously
The Full Article:
Typically, more than 70% of a part’s cost is locked in once its design is finalized. And at that point, manufacturing and sourcing teams have limited options to optimize part costs. That’s why cost modeling is exponentially more effective during the design phase. Product engineers need the ability to identify viable, cost-effective design alternatives while a project is still on the drawing board. This approach empowers design teams to innovate without sacrificing time to market or profit margins.
We explore this topic in greater detail by examining real-life examples to illustrate a key DFM principle in action. This includes why spreadsheets and other tools that rely on historical estimates provide a static, incomplete view of costing data – and how you can overcome this challenge with solutions that link design decisions to cost outcomes. Areas addressed include:
- The Design for Manufacturing (DFM) Imperative
- Overview of Important Cost Categories
- DFM Success Stories: Identifying Cost Inefficiencies
- Hidden Material Cost Drivers
- DFM Material Conversion Cost Example
- Other Methods for Cost-Effective Design for Manufacturability
- Learn More About the Power of Digital Manufacturing Insights
1) The Design for Manufacturing (DFM) Imperative
What if engineers had precise, design-level guidance on key cost drivers for their new product designs? And what if they had the insight to see how the cost is being affected by raw materials, conversion (i.e., the cost of turning raw material into a part), routing, and other manufacturability issues?
Having access to this capability would provide design and cost engineers with guidance to revise parts for added cost efficiency during the design phase. aPriori’s Manufacturing Insights Platform offers a solution that enables organizations to achieve this objective.
Unlike traditional spreadsheets, aPriori automatically evaluates the geometry of 3D CAD models whenever they are checked into a product lifecycle management (PLM) system. Through this software functionality, engineers gain real-time cost insights for parts and sub-assemblies, improving design and sourcing decisions.
Moreover, aPriori provides teams with a deeper understanding of the complex factors influencing part costs. The software is also equipped with cost and process modeling capabilities , enabling engineers to configure and run various scenarios. As a result, teams can seamlessly compare a part’s material, supplier, regional expenses, and more to make informed decisions.
To understand the impact of advanced manufacturing cost modeling, it’s helpful to consider the factors that contribute to a part’s final cost. Below, we break down a few key categories of part cost. The specifics may vary greatly, but these basic cost categories apply whether the part in question is sheet metal or plastic, cast or machined.
Watch this webinar to learn the best practices and digital tools to build a successful costing team.
2) Overview of Important Cost Categories
Direct + variable costs:.
The powerful interaction between each choice in the direct/variable cost category is significantly important. While engineering decisions may have an impact on period costs in the long run, we will focus on direct costs, as they often have the most substantial impact. The following categories describe the expenses associated with the marginal cost of producing each additional part.
Key Drivers of Material Costs
- Material type
- Material stock size (standard or non-standard)
- Material selection and utilization
- Special grain orientations (e.g., tight bends on a part may only allow manufacturing to orient the part in one direction when cutting it on the sheet)
Key Drivers of Overhead and Labor Costs
- Cycle time to make the part. Note: more than one machine may be used to make a part.
- Number of times that the part must be set up – whether in one machine or multiple machines
- Type and size of machine(s) that will be used to make the part
- Any secondary production processes such as paint, heat treatment, etc.
Indirect/Period Costs:
These costs matter for overall profitability but aren’t necessarily immediately impacted by marginal production changes. For instance, a factory will have some base level of maintenance costs regardless of the number of parts being made within a given period. These costs must be associated with specific supporting functions and spread across all parts produced.
Key Factory-Related Cost Drivers
- Energy costs
- Heating and cooling the plant
- Cleaning and maintenance
- Purchasing, manufacturing, engineering, shipping and receiving, and other supporting business functions
Key Administrative Cost Drivers
- General management costs
- Sales, marketing, and business development expenditures
- Technology support (e.g., IT staff or services)
Capital Expenditures (CapEx) and Non-Recurring Costs:
- Examples include initial investments in productive capital such as molds, stamping dies, machining fixtures, weld fixtures, and more.
- The cost impact of capital expenditures will vary depending on the complexity of the part, number of cavities, number of parts over the life of the tool, etc.
3) DFM Success Stories: Identifying Cost Inefficiencies
We developed both case studies using aPriori’s digital factory capabilities, which involve simulated production based on modeling a part’s digital twin .
During the design stage, you don’t need the absolute value estimate to be exact; a good, reliable approximation will suffice. For instance, you may determine that 20% of the part cost is material and 65% is conversion cost. While these amounts may vary during final production, they can provide a useful guidepost for prioritizing cost optimization projects. This practice can help you save time by avoiding product design changes that will have minimal impact on cost.
Manufacturing insights can help engineers minimize time-consuming activities and work faster. This automation-driven platform can determine the most efficient manufacturing methodology through near-instant cost estimates for new design alternatives.
Learn more about how design for manufacturing (DFM) has a real impact on new product pipelines.
Material Cost Example One: Truck Sheet Metal Fan Cover Redesign
The following screenshot shows that 88% of the fan cover cost is material. To reduce material costs, you can:
- Select an alternative material that is cheaper (but still reflects functional load requirements and tolerances).
- Use less material by making the part thinner, adding ribbed forms to strengthen it, or improving material utilization to reduce waste.
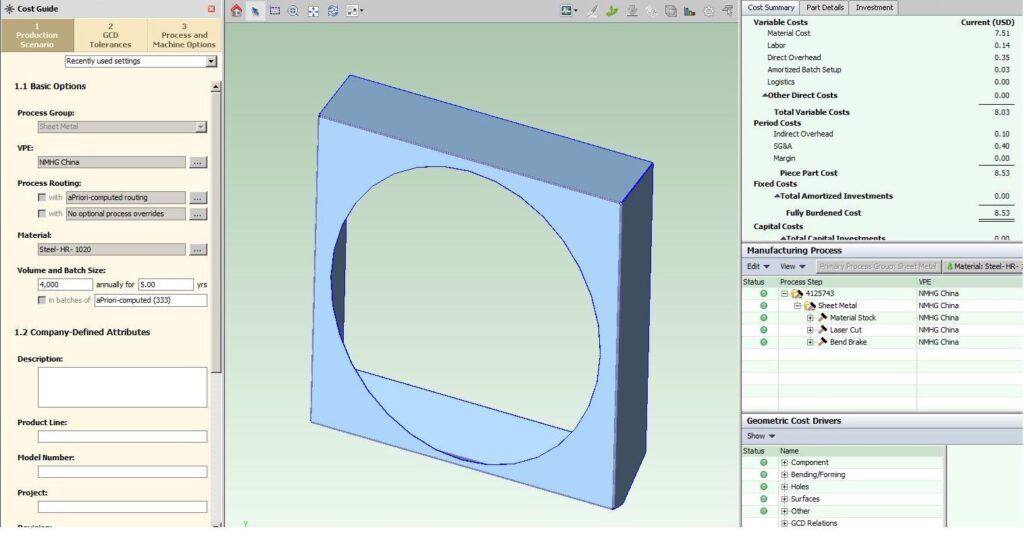
The product developer recognized that the material choice was the primary cost driver and reduced the part size without altering the size of the opening or component mating points. The following screenshot displays his final solution.
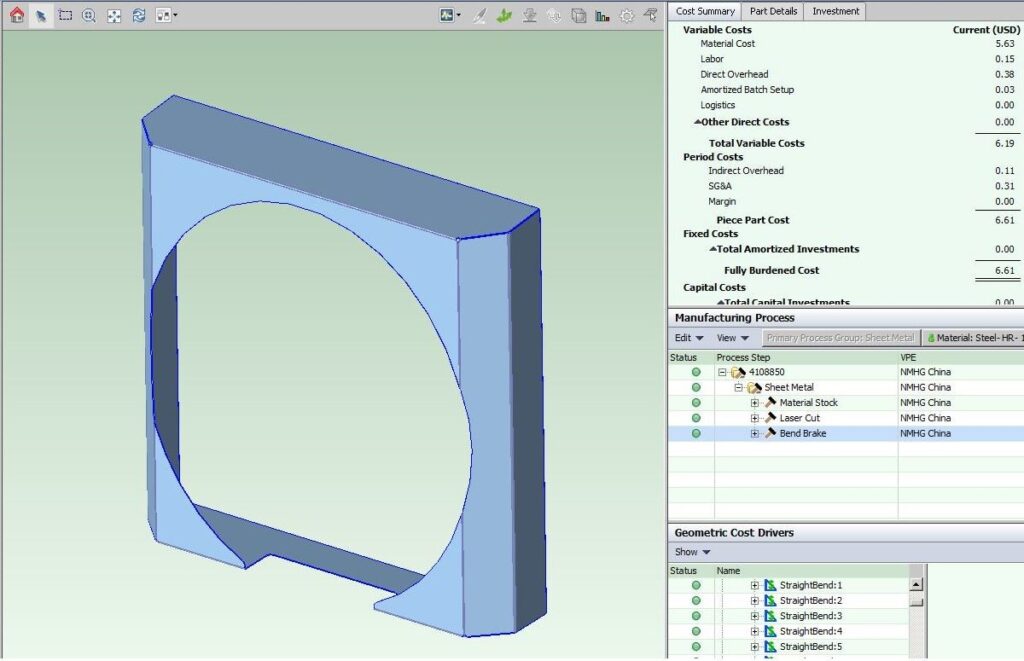
Note that while labor and overhead costs increased from $0.49 to $0.53, the material cost dropped from $7.51 to $5.63, saving $1.88 – which is a 25% savings. This improvement has paid for itself exponentially because the part is still used in tens of thousands of trucks.
This is a great example of how a reliable cost estimate is useful for prioritizing redesign work. A good cost vector (whether the cost is going up or down, by a little or a lot) is sufficient. For example, if the material cost dropped by only $1.50 instead of $1.88, the price reduction would still warrant a redesign.
Material Cost Example Two: Plastic Seat
A manufacturer produces approximately 200,000 seats annually. The digital manufacturing cost model revealed that material is 67% of the total cost.
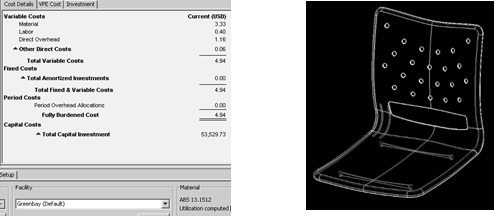
The engineer redesigning the seat has two options:
- Use lower-cost materials. Note: had the conversion cost been the most expensive, you may have wanted a material that cools faster, thereby decreasing the cycle time and production cost.
- Reduce the amount of material without compromising seat integrity.
The engineer tried several alternative designs, including:
She began by reducing the thickness of the plastic from the top edge of the back of the seat down to 2/3 of the way and from the edge of the bottom of the seat to approximately ½ of the way to the middle of the seat. This change decreased the average thickness from 0.18” to 0.15”. It is critical to note that the cost of materials, labor, and overhead was also reduced. That’s because the thinner part cools faster, leading to a double benefit: a reduction in material and manufacturing costs, totaling $0.95 on a $5 component – a nearly 20% reduction.
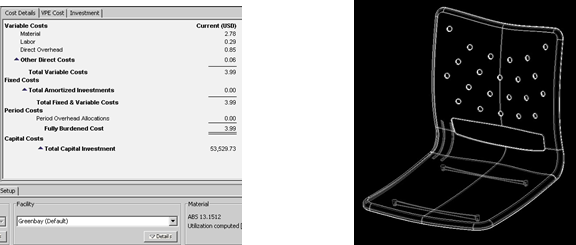
The second design change made the back hole slightly larger from its original 5”–6” in height. However, because this change only shaved a few cents off the original cost, it was not worth the risk of potential quality issues or increased customer discomfort. The value of having real-time cost feedback “at the speed of design” enables you to catch these false starts far earlier in the process and maintain quality control by adhering to the principles of DFM.
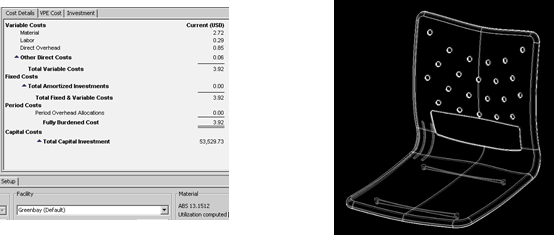
4) Hidden Material Cost Drivers
- This approach worked until their factory became overwhelmed and started buying parts or sending them to another internal factory across the country. The parts became much more expensive because they needed to orient the components perpendicular to the bend, which limits the nesting flexibility of the part and requires more material. Simulated production software like aPriori can automatically identify if a bend is too tight and recommend a minimum bend angle.
- The organization suspected an unscrupulous bid from a supplier. Still, upon review, it found that the supplier had to buy a special forging or start with the next size-up standard bar to meet the customer’s requirements. Either way, the cost would be disproportionately impacted. A diameter reduction of just a few millimeters fixed the issue, and the final design still had plenty of inertia margin.
5) DFM Material Conversion Cost Example
Let’s now move into conversion costs. Design engineers make choices that affect a large range of conversion costs, such as:
- Labor cost is proportional to cycle time. And the skill necessary to run the machine affects the wages of the operator. A 5-axis CNC machinist makes more than a 3-axis mill operator, for example.
- Set-up cost includes the number of machines to be set up and the number of times the part needs to be set up. Volume plays a large role in determining the per-product impact of set-up costs.
- Direct overhead cost is proportional to cycle time and the type and size of the machine.
An engineer was assigned to reduce the cost for a part like the one below. A quick design review revealed a 40/60 split between material cost and conversion cost. This implies that there may be opportunities to contain costs on both sides of this split without impacting lead times.
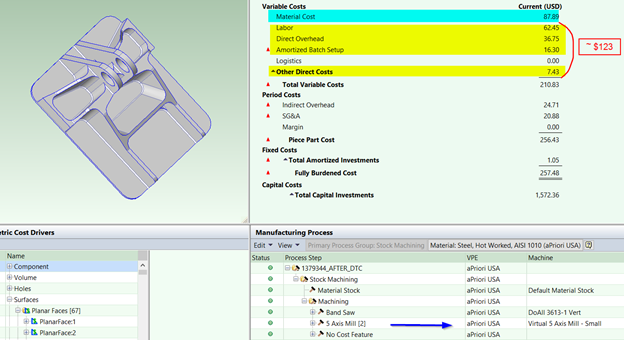
The engineer also noted that because this is a relatively low-volume part (300 units per year), it was being purchased as a machined part. While not very complex, the multiple slants on the surfaces were forcing this part to a 5-axis mill (rather than a comparatively cheap 3-axis mill).
The engineer had three choices to reduce costs:
- Redesign the part to reduce complexity for production on a cheaper machine
- Investigate machining costs further and address those issues in the design
- Identify alternative manufacturing processes for the part if they show promise
Using simulated manufacturing to analyze costs, the engineer discovered that the material utilization was only 11%, meaning that nearly 9 lbs. out of every 10 lbs. of material would be wasted. As expected, most of the cost of making the part was in machining, but from roughing operations, not finishing the part. This demonstrated that getting the part to near net shape was costing a lot in both material and manufacturing costs (see the figures below).
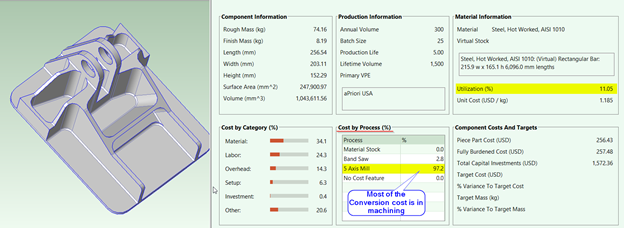
This part had been designated as a machined component because of the relatively low volume production of 300 units per year. However, based on this evidence, the engineer decided to investigate sand casting for the part. To see if it would be worth redoing the design and fatigue analysis to turn this into a casting, he created a cost estimate for sand casting the part.
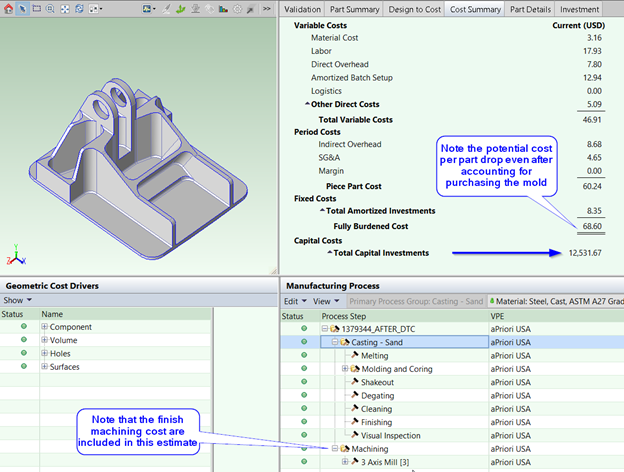
After analyzing the cost difference of approximately $190 per part on 300 parts, which amounted to a potential annual savings of $57,000, the component was redesigned and purchased as a casting, resulting in significant cost savings.
Alternatively, imagine that this part was not a candidate for a casting process due to load and fatigue requirements, as is the part below. The process for reducing costs for the part is similar, except that you need to explore machining costs (some parts may be extruded as well).
Consider how manufacturability issues may be costing you dearly. By evaluating the actual production methods intended for a part, manufacturing insights can identify design features that pose significant challenges. This could involve pinpointing a lack of draft angles, areas with excessive or insufficient thickness, or features that need a side action in plastic injection molding or die casting. For machined parts, issues like sharp corners, obstructed surfaces, or curved surfaces that require ball milling could be highlighted. Addressing these problems early can streamline production and reduce critical costs.
Looking at this part below, we notice a similar ratio of material to conversion cost. And we dig into the features that make it difficult to produce, as casting or extruding it is not an option.
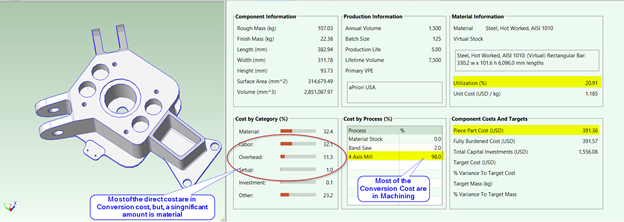
In the interest of time, we will limit ourselves to resolving as many of these L/D ratios as possible. The engineer realizes that the corner radius of those pockets is small, requiring a small tool diameter selection that violates customary L/D ratios and causes slower finishing times. He has the liberty to make those bigger, which won’t change the material consumed. See the figure below for the redesigned part.
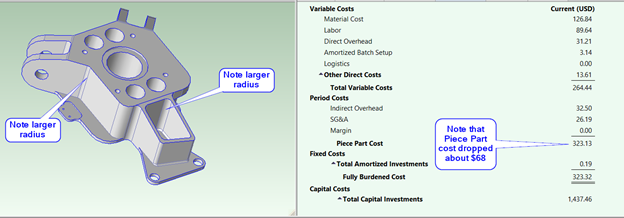
Larger corner radii allow for larger diameter selection, which increases the tool’s ability to reach further down without shaking. Cycle time drops, and cost goes down. A 17% cost reduction is certainly worth the effort of the redesign.
6) Other Methods for Cost-Effective Design for Manufacturability
It is possible to affect the size of a machine in manufacturing by considering the design of the part. For example, suppose a part is being produced in China, where labor costs are low, but overhead costs are high due to the use of large, expensive machines. In that case, it may be worth considering features that can influence machine selection.
The die-cast part below has a web in the middle that is not functionally necessary. This web is causing the part to require two-side cores, one on each side. If the web were removed, only one core would be needed, the mold base size would decrease, and the machine size (tonnage) would go down, causing a reduction in tooling and piece part cost with a smaller machine/lower overhead rate. Additionally, you may be able to have more cavities now, which is a big plus if this is a high-volume part.
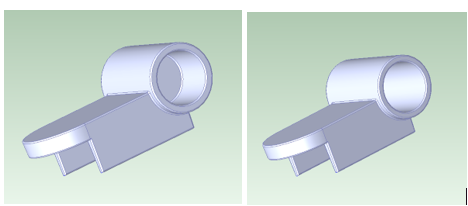
The number of set-ups can dramatically affect the cost of a low-volume part. A hole that can’t be accessed from an already available set-up direction (aPriori can show you those) can cause an extra set-up.
Too many of these will require a more expensive machine, for example, forcing a move from a 3-axis to a 4-axis or 5-axis. Did you know that if your sheet metal part has an acute angle bend and an obtuse angle bend on the same part, then two bend breaks will have to be set up to make it? This may have minimal cost impact if the part is produced in large volumes, but if this is a low-volume part, it could create serious cost inefficiencies.
7) Learn More About the Power of Digital Manufacturing Insights
DFM is pivotal to identifying cost savings from the initial product design through material selection and manufacturing. By integrating aPriori’s advanced manufacturing insights, product engineers gain a deeper understanding of how seemingly small variables can significantly impact cost and other factors.
This approach provides product design and cost engineers with clear visibility and automated guidance to make informed decisions that enhance both product quality and profitability. The adoption of DFM best practices, supported by aPriori’s insights, can ensure that products are designed for performance, profitability, sustainability, and market success.
This post was originally published on Aug. 12, 2020, and updated on April 18, 2024.

Ready to Unleash the Power of DFM?
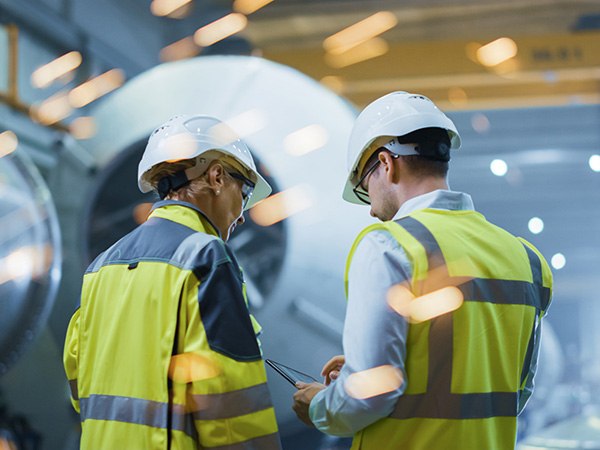
Subscribe to the aPriori Blog!
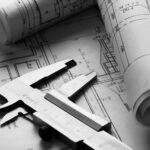
4 Manufacturing and Design Engineering Trends for 2024
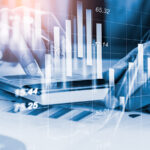
Global Manufacturing Cost and Carbon Updates: Spring 2024

6 Ways EU Automakers Can Outmaneuver Competitors in the Race Toward Net Zero
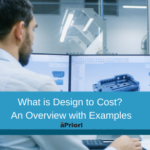
What Is Design to Cost? An Overview With Examples
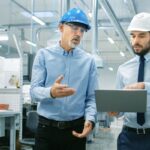
6 Metrics That Will Help Improve Your Engineering Productivity
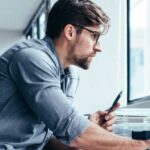
How to Conduct a Spend Analysis: Methodology in Detail
- Case Studies
- Customer Reviews
- Profitability
- Manufacturability
- Sustainability
- Design to Cost
- Design for Manufacturability
- Design for Sustainability
- Should Cost Analysis
- Quoting Professionals
- Design Engineering
- Cost Engineering
- Senior Leadership
- By Industry
- Aerospace & Defense
- Auto & Transportation
- High Tech Electronics
- Industrial Equipment
- Manufacturing Insights Platform
- Digital Factories
- Regional Data Libraries
- Manufacturing Process Models
- aP Workspace
- aP Generate
- aP Analytics
- News & Events
- Request a Demo
About the Author
Choose your region

Cutting & Bending
Cnc machining, finishing & assembly, knowledge base, about service, policies & terms, design for manufacturing and assembly.
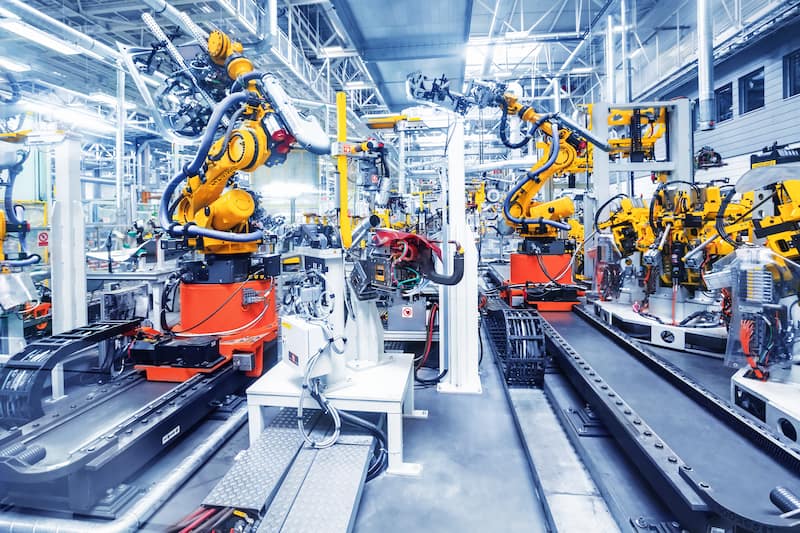
In the past few decades, research into design thinking has engendered a new wave of methodologies in product design and manufacturing processes. These methodologies have saved billions in product development and ensured lower cost, higher competition and greater product reliability.
Among these methodologies, one of the most prominent ones, Design for Excellence (DFX) , has since fragmented into smaller focus areas such as Design for Manufacturing (DFM), Design for Assembly (DFA), Design for Manufacturing and Assembly (DFMA), Design for Supply Chain (DFSC) and so on. In DFX, a focus such as cost, quality or ease of manufacturing is chosen and the product’s design is improved in regards to that aspect.
This article will explore the role of Design for Manufacturing and Assembly (DFMA or DFM/A) in product design. DFMA represents a harmonious combination of Design for Manufacturing (DFM) and Design for Assembly (DFA) , both of which we have discussed in separate articles previously.
What Is Design for Manufacturing and Assembly?
DFMA stands for Design for Manufacturing and Assembly. It is an engineering methodology that focuses on optimising the manufacturing and assembly aspects of a product. Both of these aspects have a high impact on the final product’s quality and cost.
Factors such as raw materials, manufacturing processes, volume, machinery, tooling, precision, number of parts and their complexity, labour and skills, automation potential, etc, are all very influential in product development. By optimising these factors alone, companies can drop the initial cost estimates by over 50%. This is the main intention of implementing DFMA principles.
In DFMA, the product design is continuously modified while keeping certain end goals in mind to arrive at a product that requires less time, money and effort to produce.
The Need for DFMA Methodology
Why do we need DFMA when we already have DFM and DFA? Let us start by reviewing our understanding of each.
Design for Manufacturing is concerned with maximising the manufacturing ease of a product. It employs techniques that make manufacturing faster, cheaper, and easier by improving the design and the manufacturing process.
On the other hand, Design for Assembly works to simplify, shorten and mistake-proof the assembly process. Principles such as poka-yoke, combining and standardising parts are all examples of DFA application.
Both DFM and DFA have similar objectives. They both aim to reduce material requirements, cost and time-to-market. But there are times when the two may work against each other. A net gain from DFM could lead to a net loss in DFA, essentially making the gain worthless.
Let’s take the example of combining parts from DFA “guidebook”. If fewer individual parts lead to a part that is expensive or difficult to manufacture, we gain little benefit from this DFA technique as DFM is affected negatively. Similarly, many DFM guidelines can reduce the effectiveness of a DFA technique.
To avoid such occurrences, it was prudent to look at the two methodologies of DFM and DFA together. This is how DFMA came to be. It uses DFA and DFM in tandem to arrive at an optimum product design. DFMA can help us leverage the advantages of both these methodologies without the disadvantages of either.
Benefits of DFMA
A well-structured DFMA application provides both short-term and long-term advantages. These advantages are indispensable to the creation of a sound product that can beat modern-day competitors. Some of the amazing benefits of DFMA are:
Shorter time to market
Time to market is defined as the duration between the idea generation phase and the introduction of a product to the market. Ideally, you’d want this time to be as short as possible. DFMA significantly reduces the time to market by simplifying the manufacturing processes and the assembly steps.
Lower product development cost
An efficient DFMA at the initial phase reduces the development costs by thinking ahead of time and resolving possible issues that may crop up later.
One of the leading experts on concurrent engineering and Design for Manufacturing, Dr. David Anderson explains that in DFM there is a “Rule of 10” which states that it costs 10 times more to fix defects at every successive stage of assembly. Thus, if rectifying a part defect costs x prior to assembly, it will cost 10x at sub-assembly, 100x at final assembly, 1000x at the distributor stage and 10.000x if the part has reached the customer.
DFMA removes the need for downstream design changes. It also recommends adding provisions for features that the manufacturer may want to add to a product at a later point in time.
Reduced wastage
DFMA aims to eliminate waste from the product and assembly design. It reduces the wastage of materials, motion, inventory and overprocessing. It also minimises defect risks and wait time by eliminating redundant manufacturing and assembly steps and unnecessary features.
Greater product reliability
Due to the high focus on preventing defects and increasing the benefit-cost ratio (BCR) , DFMA products naturally become highly reliable and durable. The fewer number of parts in a DFMA-conscious product also helps to reduce the failure rate.
Quality control
DFMA improves communication and teamwork between different teams in a manufacturing setup. A well-coordinated product development effort between designers and manufacturing engineers, for instance, informs both teams about the best practices of each department to reach a certain end goal. This ensures a higher quality product within the allotted budget.
- Personal account manager
- Quality assurance
- Payment terms for companies
- On-time delivery by Fractory
DFMA Principles
DFMA is a vast methodology and many books have been written on this subject. It consists of a variety of principles. The application at hand is evaluated in light of these principles to create a DFMA-conscious product.
It is crucial that DFMA starts at the concept creation phase. The design stage is the most influential in determining many aspects of the product such as the quality, reliability and final price. Any decisions taken at this stage have far-reaching effects. Some of the common principles in DFMA that can be applied to a wide variety of products are as follows:
Simple design
Keeping the design simple is one of the tenets of design for manufacture and assembly (DFMA). A designer must strive for a clear and efficient product design. Removal of unnecessary features and components must be a priority.
Such a design is usually easier to manufacture and assemble. It also requires lower investment costs and relatively less time to manufacture and repair, if the necessity arises.
A complicated product geometry is unattractive besides being uncomfortable to use. You will find that it is actually more complex to create a simple design than a complex one. Remember the adage “Simplicity is the ultimate sophistication.”
Opt for a modular design
A modular design breaks a product down into various modules, each of which performs a certain function. Such modules reduce the number of parts present in a family of products. For instance, a single laptop battery may be used in a number of different laptops. Same goes for other components such as a smartphone camera module. This type of design process has a positive effect on time to market, inventory, cost, customisation, sustainability and the possibility of future upgrades.
Easy and efficient fasteners
Most products require the use of some kind of fasteners and there’s a variety of options available on the market. Many fasteners may appear cheap on paper but their installation can be expensive and time-consuming. Moreover, fasteners can create a bottleneck in a factory’s manufacturing setup, often restricting production volume.
DFMA optimises the fastening process by recommending affordable fasteners that are also easy and cheap to install. Wherever possible, it prefers the use of snap-fit fastening methods. For a stronger bond, rivets can be chosen over screws. Due consideration to fastening methods can reduce manufacturing costs , waste, product weight and space requirements.
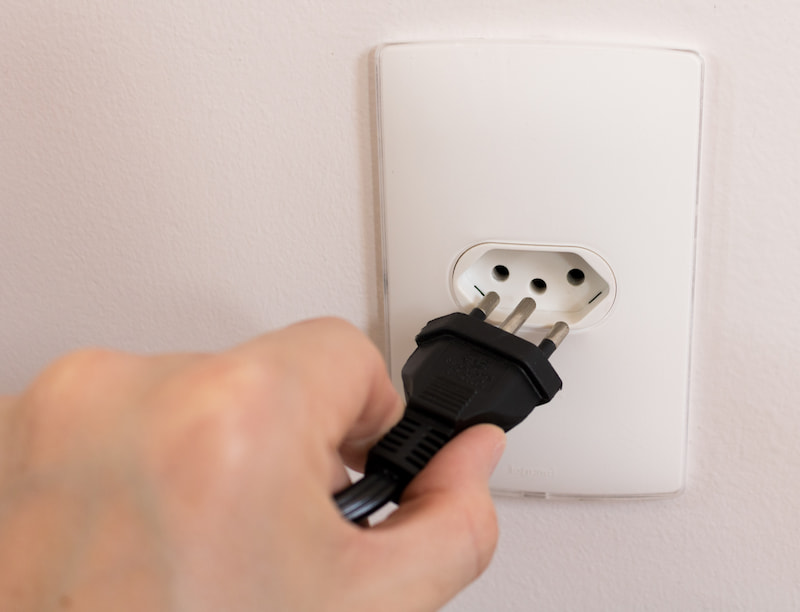
Poka-yoke refers to the use of mistake-proofing techniques to improve the accuracy rates of assembly and manufacturing operations. The intention is to correct errors and defects as close to the source as possible by installing automatic/manual interlocks that prevent incorrect manufacturing and assembly of product parts. These interlocks ensure that a component can only be assembled in the correct orientation. Using asymmetry in product structure is one of the ways to ensure this. However, it must be noted that symmetrical products are easier to manufacture and assemble.
Reduce the number of parts
Reducing the number of parts is one of the most popular techniques in DFMA as in DFM and DFA. There are many advantages to this.
Each part draws from your team’s bandwidth logistically and financially. It will require specific tooling and fixtures. More parts will require more prototypes, manufacturing, individual analysis and assembly steps. It is always a good practice to consolidate part functions wherever possible.
Fewer parts reduce the amount of time required in manufacturing and fastening processes. It also reduces the assembly time and the chances of incorrect assembly.
Use standard parts
Standard parts are readily available, they’re also cheaper and have greater reliability than custom-made parts. DFMA advises preferring the use of standardised components wherever possible.
Be aware of process limitations
Many designers are unaware of suitable manufacturing processes and their capabilities when designing a product. By improving communication between different teams, DFMA ensures that designers make decisions that suit more economical manufacturing methods.
Use suitable tolerances
Tight tolerances can be very difficult to achieve. They require expensive production and measurement methods. Furthermore, parts with tighter tolerances are difficult to assemble. This increases the assembly costs through increased labour costs and scrap rates.
Wherever possible, the tolerances should be as loose as possible to keep the price down while maintaining functionality.
Other DFMA techniques
In addition to the above principles, some other DFMA techniques that improve the manufacturing and assembly ease are:
Remove flexible parts
Implement automation into the production process or make provisions for future automation potential
Make modifications for an easy assembly
Give due consideration to how the part will be handled and oriented during assembly and manufacturing operations
Design multi-functional parts
Related Posts:
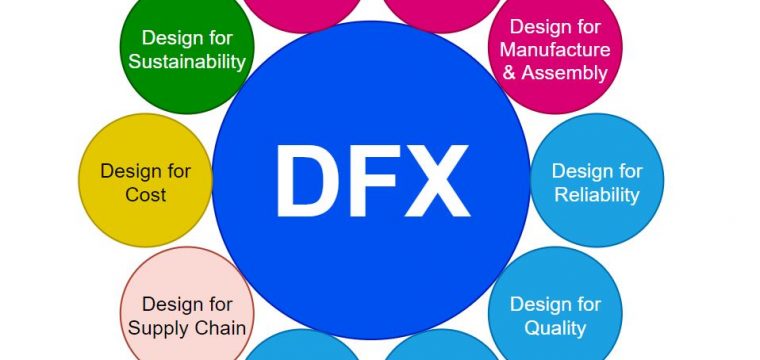
Would you like to read more of our content?
Receive engineering articles to your inbox monthly .
- Phone This field is for validation purposes and should be left unchanged.
- Machine Components
- Product Updates
- Project Management
- Learn from Engineers
- Fabrication Methods
- Engineering Materials
- Product design
- Company News
- Procurement
Fractory’s bending calculator helps you to get your sheet metal designs right from the start.
- Sign me up for a newsletter too
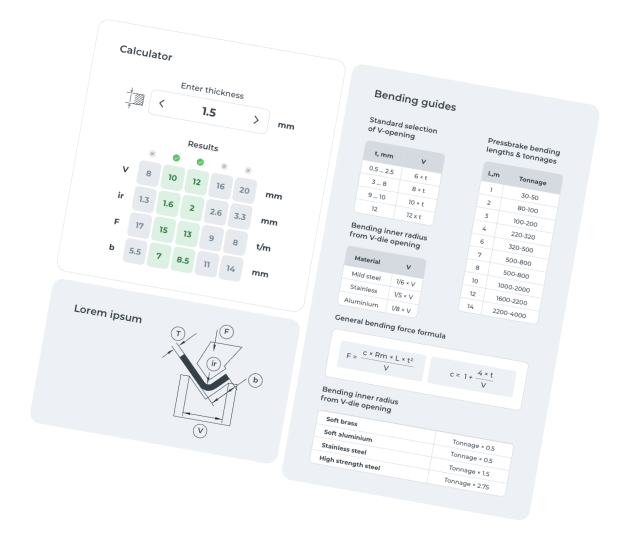

IMAGES
VIDEO
COMMENTS
Design for Manufacture and Assembly (DFMA) is an engineering methodology which focuses on reducing time-to-market and total production costs by prioritizing the following during the early design phases of the product life cycle. Ease of manufacture for the product's parts. DFMA is comprised of two components: Design for Manufacturing (DFM ...
The Design for Manufacturing and Assembly (DfMA) approach has been extensively used for decades in the automobile, aerospace, general mechanical and other manufacturing industries for the development of products [15, 16]. ... For the experimental case study we then analyse the design, manufacture and installation of a prefabrication prototype ...
A Case Study in Design for Manufacturing and Assembly. Aug 06, 2021. U.S. Engineering. by Jeff Kiblen, Associate Vice President, U.S. Engineering Innovations. Design for Manufacturing and Assembly (DfMA) is one method U.S. Engineering Innovations (USEI) is implementing in our quest to reimagine ways to execute construction projects.
The design for manufacturing and assembly (DFMA) is a family of methods belonging to the design for X (DfX) category which goal is to optimize the manufacturing and assembly phase of products. DFMA methods have been developed at the beginning of the 1980s and widely used in both academia and industries since then. However, to the best of the authors' knowledge, no systematic literature ...
CASE STUDY The methodology of this research draws on Flyvbjerg's viewpoint of advancing the existing knowledge from case study (Flyvbjerg, 2006). An actual prefabricated bamboo building was selected as the case study project. Using a single case for case study might lack generalizability, but still has advantages in offering the "force of
Design for Manufacturing, Design for Assembly, Knowledge-Based Engineering . 1. Introduction ... Then, using a case study, the philosophy of the Design for Manufacture and Assembly (DFMA ...
The design efficiency of the seat recliner subassembly for this design is 68.18%. The total material cost is $0.6329, and the total manufacturing index cost is 287.15. Table 6.39 Design for assembly analysis - Design Option 3. Full size table. Table 6.40 Relative costs (R c) - Design Option 3.
Design for manufacture and assembly (DfMA) has become a buzzword amid the global resurgence of prefabrication and construction industrialization. Some argued that DfMA is hardly new, as there are concepts such as buildability, lean construction, value management, and integrated project delivery in place already.
Arashpour, M. 2019. "Design for manufacture and assembly in offsite construction and relationship with concurrent engineering." In Offsite production and manufacturing for innovative construction: People, process and technology, edited by J. S. Goulding and F. P. Rahimian. London: Routledge.
BIM for DfMA (Design for Manufacturing and Assembly) essential guide, Building and Construction Authority, Singapore. Google Scholar. ... Case study research and applications: Design and methods, Sage publications. Google Scholar. Yuan, Z., Sun, C., and Wang, Y. (2018). "Design for Manufacture and Assembly-oriented parametric design of ...
This paper reviews the rapid and successful implementation of design for manufacture and assembly (DFMA) at Ingersoll-Rand. ... Society of Manufacturing Engineers, Dearborn, MI 48121, September 26-27, 1989. ... W.R. & Mistry, D.K. Design for manufacture and assembly: Case studies in its implementation. Int J Adv Manuf Technol 6, 131-140 ...
Design for manufacturing and assembly is an engineering methodology that focuses on reducing time-to-market and total production costs by prioritizing both the ease of manufacture for the product's parts and the simplified assembly of those parts into the final product - all during the early design phases of the product lifecycle. ...
That's because the thinner part cools faster, leading to a double benefit: a reduction in material and manufacturing costs, totaling $0.95 on a $5 component - a nearly 20% reduction. The second design change made the back hole slightly larger from its original 5"-6" in height.
In Section 2, previous research regarding design for manufacturing and assembly, design optimization, and selection of the OSC system is reviewed to clarify the research gap. Subsequently, the proposed methodology is illustrated in Section 3 in detail. Sections 4, 5 and 6 presents the prototype development and case study, as well as their ...
However, many studies of DfMA in construction are still simply following the DfMA guidelines developed from manufacturing without adequately considering important differences between the two sectors of construction and manufacturing. This study aims to develop a series of construction-oriented DfMA guidelines by adopting a mixed-method approach.
A case study is used to evaluate the proposed method. ... To address this challenge, this paper introduces a novel approach involving the integration of the design for manufacturing and assembly (DfMA) principles and parametric building information modeling (BIM) to develop a preassembly analysis system (PAS). The DfMA methodology enables a ...
DFMA stands for Design for Manufacturing and Assembly. It is an engineering methodology that focuses on optimising the manufacturing and assembly aspects of a product. Both of these aspects have a high impact on the final product's quality and cost. Factors such as raw materials, manufacturing processes, volume, machinery, tooling, precision ...
Design for Manufacturing and Assembly (DFMA) Influence on Cost / Quality / Time: 2. Design for Assembly aims to reduce the number of parts, easing handling and assembly operations 3. Design for Manufacturing aims to select the most cost effective material and process to ease manufacturing operations 4. DFMA utilises cross-functional
In this regard, design for manufacturing and assembly (DfMA) and design for deconstruction (DfD) have gained prominence, as studies have elucidated the methods' unprecedented potential to wholly transform the construction process and mitigate the unwanted impacts brought about by the industry. ... Zamani, E.; Dounas, T. A generative design ...
A product redesign strategy can effectively shorten design lead time and reduce the manufacturing cost of innovative development for the manufacturing industry to stay competitive. Identification of function components is the basis of product redesign. Existing practices to identify the critical component and customer requirements are considered while complaint and historical failure data ...
Abstract: Design for manufacturing and assembly is widely used in industry, especially in product design and development. process in order to meet customer needs, companies are stru ggling with co ...
Design for Manufacturing, Assembly, and Disassembly is important in today's production systems because if this aspect is not considered, it could lead to inefficient operations and excessive material usage, both of which have a significant impact ... Two case studies are used to present the calculations involved in the metrics (Mesa ...
4. Design For Manufacturing and Assembly (DFMA) 4 After final selection of material and process carry out a thorough analysis of DFM. Figure 2 depicts the flow diagram of various steps undertaken in a DFMA study using DFMA software. Advantages of applying DFMA during product Design: Today products are Tending to becoming more complex Made/required in increasingly large number Intended to ...
AM, and FLM in particular, enable the manufacturing of these fully functional non-assembly components within a single production step, making previously required assembly steps dispensable (Chen and Zhezheng Citation 2011; Mavroidis et al. Citation 2001; Schaechtl, Schleich, and Wartzack Citation 2021).AM therefore offers opportunities as no trade-offs need to be made to simplify components ...
PDF Design for Manufacturing and Assembly: Concepts, architectures and implementation O. Molloy, S. Tilley, E. Warman (auth.) digsell https://lnkd.in/e55mfMRS In order to compete in the current ...
Case Studies: AM in Action Several transportation sectors have already begun to harness the potential of AM for producing end-use parts. In the automotive industry , companies like BMW and General Motors have adopted 3D printing for both prototype and production parts, including components for high-performance vehicles that require a blend of ...
Printed version: PDF Publication Date: 05/01/2024 Agency: Department of Energy Dates: The effective date of this rule is July 15, 2024. Compliance with revised performance standards established in this rule is required for the construction of new and major renovation of Federal buildings, including commercial buildings, multi-family high-rise residential buildings, and low-rise residential ...