

DMADV: A Complete Guide to Using the DMADV Method
- May 27, 2022
- February 18, 2024
- Lean Basics
No matter what industry you work in, you’ve likely experienced a situation where you need to create a new process or product in order to meet a customer’s requirements. Doing so is not an easy task so it can be helpful to use a framework such as DMADV.
What is DMADV?
Stage 1: define, step 1: convert requirements to ctqs, step 2: prioritize the ctqs, step 3: determine measurement methods for the ctqs, step 1: convert the ctqs to process/product features, step 2: prioritize the features, step 3: determine performance targets for each ctq, step 4: develop possible design concepts, step 5: evaluate each design concept, step 1: create a prototype, step 2: complete pilot runs, step 3: revise the design as needed, step 4: complete a risk assessment, step 5: create an implementation plan, step 1: complete trials with the standard process setup, step 2: make any necessary corrections to the design, step 3: prepare for implementation, step 4: go-live.
DMADV is a methodology used to provide structure to the task of designing a new product or process. The five stages of DMADV are Define, Measure, Analyze, Design, and Verify.
Specifically, DMADV falls within the principles of Six Sigma. Six Sigma is an improvement methodology that focuses on the reduction of variation or defects in a process in order to improve overall quality. DMADV is also referred to as a DFSS, or Design for Six Sigma, methodology.
It is often confused with the more commonly used DMAIC approach, but the goal of these processes is very different. DMADV is used when designing new processes or products while DMAIC is used to improve processes or products that already exist .
Therefore, DMADV is a proactive and preventative method whereas DMAIC is a reactive method.
DMADV should always be approached as a cross-functional team rather than one or two people/departments working alone. This ensures that all perspectives of an organization are captured in the design which will minimize potentials for failure after implementation.
What does DMADV Stand For?
DMADV is an acronym that stands for each of the five stages of the design process. Those stages are:
Throughout the rest of this article, we will take a deeper dive into each of these stages. We’ll discuss what typical steps are included in each stage as well as some useful tools to remember.

The primary goal of the Define stage is to clearly determine and understand your goal for the project.
You likely began using the DMADV approach because there was either a new customer request, a business problem, or a new market opening that requires you to design a new product or process.
Therefore, before you begin any further work, you must be sure to clearly understand the goal, scope, requirements, and expectations for the design. In particular, you will need to analyze the various voices that drive your business in order to determine what is most important to capture in your design.
These voices include the voice of the customer (VOC) , the voice of the employee (VOE) , and the voice of the business (VOB) .

Each of these voices is relatively straightforward in that they represent what each party cares most about.
For example, the customer wants a high quality product that functions for their application, the employee wants a safe process that they feel comfortable operating, and the business wants to generate a profit by creating a highly efficient process.
When defining your goals and expectations for the new product or process, you must take all of these voices into account in order to be successful.
Now, you may be wondering how you can figure out exactly what your VOC, VOE, and VOB are. A couple of tools you can use to do this include:
- Previous customer complaints
- Questionnaires
The primary point to remember in this stage is that you need to be extremely diligent in collecting all opinions regarding what is required for the new product or process. This will ensure you are not missing any vital parameters as you continue throughout the rest of the project.
STAGE 2: MEASURE
There are three steps involved in the Measure stage of the project. These include:
- Convert the requirements identified in the Define stage to CTQs
- Prioritize the CTQs
- Determine measurement methods for the CTQs
Let’s break down each of these steps:
In the measure stage of the project, you should start by converting all of the requirements that you identified from the VOC, VOE, and VOB in the Define stage to critical to quality parameters (CTQs) .
Some examples of common CTQs are:
Consistency
Customer service, affordability.
For example, if the VOC revealed that the customer wants a product that will not break easily, one of the CTQs will be durability.
Once you have the CTQs defined, you can then prioritize them.
The KANO model is a good tool to use to gain a deeper understanding of the customer’s requirements and to prioritize CTQs. The KANO model looks at each of the customer’s needs and analyzes how satisfied or unsatisfied a customer will be if the need is present or absent.
The model has two dimensions represented by x and y-axes.
- The x-axis is the supplier’s fulfillment of a particular need which ranges from “supplier did not fulfill at all” to “supplier fulfilled completely”.
- The y-axis is the customer’s satisfaction which ranges from “completely dissatisfied” to “completely satisfied”.

This model can be used to prioritize customer needs by ranking each within the following three categories:
Must-haves are needs that MUST be fully satisfied for the customer to even consider purchasing the product.
Satisfiers are needs that the customer expects to see in the product. These needs are essentially must-haves if you want to be competitive in the market.
Delighters are properties or features that would “wow” a customer. These allow you to become a market leader.
Now that you have defined and prioritized the CTQs, you should determine how you will measure their performance.
At this point, you won’t have anything to measure because you have not designed the process yet, but it is important to understand how you will gauge if you are achieving your CTQs.
Your measurement system will differ depending on what you are trying to measure (for example, you may want to use a thickness gauge if thickness is a CTQ for your product), but it is critical that the instrument you choose is both accurate and precise .
This can be achieved using a Gage Repeatability and Reproducibility (Gage R&R) test. The goal of a Gage R&R test is to determine how much of the variation present in your data can be attributed to the measurement system.
If the Gage R&R determines that your measurement system is accurate and precise, you can move forward with using it.
Also, as a part of this step, you should be sure to fully define your measurement process. You can do so by asking yourself the following questions:
- What am I measuring?
- How am I measuring it (what measurement system and procedure am I using)?
- When during the process should I measure this?
- How often should I measure it?
- Who is responsible for measuring this and communicating if the measurement data does not match our expectations for performance?
Depending on the business and your goals, the questions you need to consider may differ from this list, but it is critical to go through this exercise to ensure you are not leaving any gaps in your process that will result in future failures.
STAGE 3: ANALYZE
The next stage is Analyze which consists of five steps. These steps include:
- Convert the CTQs to process/product features
- Prioritize the features
- Determine performance targets for each CTQ
- Develop possible design concepts
- Evaluate each design concept
Let’s dig deeper into each of these steps:
The first step of the Analyze stage is very similar in concept to what you did in the Measure phase. In the Measure phase, you converted requirements from the VOC, VOE, and VOB to CTQs and now, in the Analyze phase, you will convert those CTQs to features.
The most important thing to remember here is that one CTQ can lead to multiple features.
For example, if you are designing a car, one of your CTQs will definitely be safety. This CTQ translates to many features, such as seatbelts, air bags, antilock brakes, and much more.
The next step is also similar to the Measure phase. In the Measure phase, you prioritized the CTQs. Now in the Analyze phase, you must prioritize the features.
There will be some features that are non-negotiable. This should include any features related to safety even if they weren’t explicitly stated in the VOC, VOE, or VOB.
A tool that you can use to help with this prioritization is QFD (Quality Function Deployment or House of Quality) . QFD shows the relationship between the customer’s wants and the product features and helps you to rate the importance level of each feature.
In this next step, you will determine targets for each CTQ based on the customer requirements as well as competitive products.
In general, your targets must at least meet the customer requirements and you should strive to exceed the targets set by your competitors in order to dominate the market.
The fourth step in the Analyze phase is when you begin actually creating design concepts. One useful tool you can use to do this is called TRIZ which is a Russian acronym for the Theory of Inventive Problem Solving.
The idea behind TRIZ is that every problem has previously been solved by someone, somewhere. Therefore, you can save yourself a lot of time by generalizing your specific problem to something that has already been solved rather than reinventing the wheel.
There is a TRIZ effects databases that is a compilation of resources that answers a wide variety of different queries.
By generalizing your specific problem to something that has already been solved by someone else, you can spend less time trying to uncover the basics of solving your problem and can instead get a jumpstart on determining exactly what your specific solution might look like.
Once you have some design solutions established, you will then need to evaluate each of these designs and land on a final decision. Some useful tools for this are the Pugh Matrix and the Six Thinking Hats .
The Pugh Matrix
The Pugh Matrix is a quantitative ranking system that allows you to compare alternative solutions to your baseline in order to determine which option best achieves your desired state. You can complete this using the following steps:
- Determine what the most important characteristics are for your solution. You can use the VOC, VOE, VOB, and QFD to do this.
- Weight each of these characteristics according to their relative importance.
- Rate how well your current process/business achieves these characteristics. You can do this using a numeric scale such as 1-5 where 1 is the worst and 5 is the best. This will be your baseline.
- Rate each of your alternative solutions based on how well they achieve each characteristic as compared to your baseline.
- Calculate the sum of the ratings for each possible solution and choose the best.
- Consider creating a hybrid design if it makes sense to do so.
The Six Thinking Hats
The Six Thinking Hats are a decision-making tool that forces you to consider all angles of a design. This will allow you to determine all the pros and cons that exist for the specific product. The six different aspects that you will need to consider are:
Information & Data
Process control, stage 4: design.
After you select the most optimal design in the Analyze phase, you will then need to create a prototype of this design and test it. Therefore, the steps involved in the design phase include:
- Create a prototype
- Complete pilot runs
- Revise the design as needed
- Complete a risk assessment
- Create an implementation plan
Overall, these steps are relatively straightforward to explain, but this will often be the stage that takes the longest to complete. Completing each of these steps thoroughly and accurately will ensure your success when you implement the final design.
The first step of the Design stage is to create a prototype for the design you selected during the Analyze phase. You will then be able to test this design through pilot runs or simulations.
Therefore, the next step is to complete these pilot runs. During these runs, you will want to complete the following:
- Gain a deep understanding of how every input and process setting affects your outputs
- Test whether or not your design is able to achieve the target CTQs
To do the first step, you should complete a design of experiments (DOE).
DOE will allow you to understand the relationships between different inputs, process settings, and outputs in your process. This is a critical piece if your process has many variables.
To complete the DOE, you should test different combinations of the inputs and process settings then analyze what effect they have on the outputs.

For the second step, you should use the measurement systems you chose and evaluated during the Measure stage to see if the design is achieving the target CTQs. If it is not, you will need to revise the design.
This is where the next step comes in.
This next step is where you will take your findings from the pilot runs and revise the design, if needed, to ensure you are achieving the target CTQ performance.
This will often be an iterative process. For example, once you revise your design you will need to redo steps 1-3 of this stage again and again until you have a final design that is fully functional and capable of achieving your target performance.
Once you have your final design defined, you need to complete a risk assessment for it. The most common form of risk assessment is a Failure Mode & Effects Analysis (FMEA).
The FMEA should be completed by a cross-functional team so that all perspectives are captured.
The goal of the FMEA is to identify anything that could potentially go wrong in the new process. These are referred to as your failure modes. Once you have identified these failure modes, you should go through them one-by-one and determine everything that can possibly happen if the failure were to occur.
This can be a very tedious process, but it is critical to ensuring you have a risk-free process.
If you do identify any high risk failure modes, you should alter your design to get rid of them.
Essentially, this step forces you to “foolproof” your design.
The final step of the Design phase involves creating an implementation plan. This should clearly define who, what, when, and how you are going to complete the final go-live for the design. For example, this can include:
- Target implementation date
- Process owner establishment
- Training plan
- Change management process plan
- Plan to communicate the change to affected employees
STAGE 5: VERIFY
The final stage of the DMADV method is the Verify stage. During this stage, you will need to complete the following four steps:
- Complete trials with the standard process setup
- Make any necessary corrections to the design
- Prepare for implementation
Let’s take a deeper look at each of these steps:
During the Design phase, you completed pilot run trials which are typically completed under controlled conditions that may not mirror standard working conditions. If this is the case, you should be sure to complete trials with the standard process setup before officially implementing the new design.
This includes using standard raw materials, working conditions, and staffing.
As you do these trials, you should use check sheets to confirm that each CTQ is fully achieved. You should also note any issues that arise and complete a root cause analysis. This will allow you to resolve the source of any remaining issues.
Now that you have completed trials with the standard process setup and identified any issues, you should make any necessary corrections to the design to resolve those issues.
You should add your findings from the root cause analysis to the FMEA and implement any necessary changes. This will give you the confidence that your design is fully operational and successful in achieving your goal.
The final step before implementation is to prepare. This is a critical step to ensure the go-live is smooth!
This includes actions such as:
- Writing standard operating procedures (SOP), work instructions, and/or standard work
- Updating any upstream or downstream processes to accommodate the new design
- Updating the process flow chart
- Training the employees
- Completing a change management process to communicate and track the change
- Creating a control plan
The final step is to officially go live with the new design!
At this point, the process will be handed over to the process owner and standard production will begin.
It is critical that you complete all of the previous steps thoroughly to ensure a smooth hand-off at this phase.
Once the process has gone live, you should continue to monitor it to confirm that the design is functioning as expected. You should always plan to look for potential areas for improvement to ensure you are maintaining a mentally of continuous improvement. This will allow you to stay on top of your competition.
🤿 DIVE DEEPER: Want to learn about how a continuous improvement mindset can benefit you? Read my article here to learn more!
The next time you need to design a new product or process, give the DMADV method a try! By using the DMADV approach, you will have a defined structure to follow which takes a lot of the overwhelm out of such a complicated process.
By using the DMADV approach you will ensure your final design is meeting the customer’s expectations and is robust enough to function smoothly. Overall, this approach is exactly what you need to stay ahead of the competition!
Would you consider using the DMADV approach? I’d love to hear your thoughts in the comments below!
Lindsay Jordan
Hi there! My name is Lindsay Jordan, and I am a full-time Chemical Process Engineer. That means I work with the principles of Lean methodology everyday. My goal is to help you develop the skills to use Lean methodology to improve every aspect of your daily life both in your career and at home!
Leave a Reply Cancel Reply
Your email address will not be published. Required fields are marked *
Name *
Email *
Add Comment *
Save my name, email, and website in this browser for the next time I comment.
I accept the Privacy Policy
Post Comment
This site uses Akismet to reduce spam. Learn how your comment data is processed .
Trending now


- Quality Management
Home » Free Resources » »
What is DMADV? Here’s Everything You Need to Know
- Written by Contributing Writer
- Updated on March 8, 2023
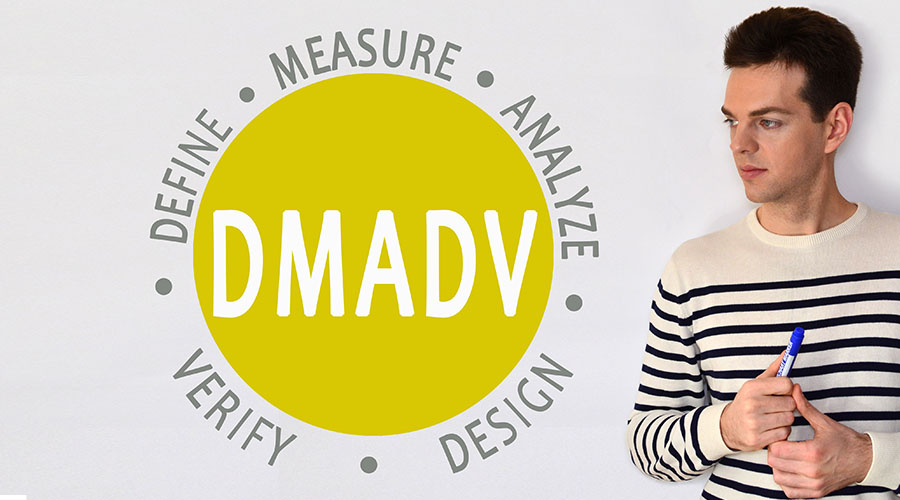
Every business should have a streamlined strategy before launching a new service or product line. All stakeholders involved in the latest project development must work in sync to deliver what will meet your customers’ requirements. DMADV is a framework that allows you to manage such development processes seamlessly.
DMADV is part of the Six Sigma methodology, which, when implemented correctly, ensures zero wastage of time and resources for businesses. With DMADV Six Sigma, you can deploy efficient production strategies and improve the working process within the organization.
Whether you are a project leader working for a client or planning a new product, service, or process for your business, knowledge of DMADV will give you an added advantage. This guide highlights the basics of DMADV for easy understanding of this methodology. It also shares a Lean Six Sigma program you can take to master this methodology.
Let’s dive in!
What is DMADV?
DMADV is a Six Sigma framework used in new product/service/process designing. It is also known as Design for Six Sigma (DFSS). It focuses on customers’ requirements and makes your team ideate the right strategies in the first development phase.
DMADV is the acronym for the five phases of product or service development: Define, Measure, Analyze, Design, and Verify.
You can rethink flawed processes, redesign problematic products, ensure all stakeholders are on the same page with an entirely new product or service, and more with DMADV.
Another similar Six Sigma process, DMAIC, is available to improve the quality of an existing product or service. DMAIC stands for Define-Measure-Analyze-Improve-Control. After creating a product or service with DMADV analysis, you can use the DMAIC framework for further improvement with an extensive customer-centric approach.
What is DMADV Used For?
DMADV Six Sigma is used for redesigning or creating a new product or service. You can optimize your production per client or customer requirements with DMADV tools. As mentioned, it involves five stages of a production process. We have explained the use of each stage in detail. Have a look.
In this phase, project managers discuss the goals and customer/client requirements for the product or service in this stage. The whole development process of the product depends on it. The team collects data from various sources like customer reviews, sales department, research information, and previously stored data to define the project details as accurately as possible. With all this information, the goal is to optimize the product design as the consumer wants and is willing to pay for it.
Once the project specifications are defined, the next step is to create nodes and collect data depending on them. That’s how you can construct a customer-defined specification list and ensure the product meets first-phase customer requirements. In this phase, a few characteristics are measured- customer-centric quality standards (CTQ), manufacturing capacity, risk assessments, and product capabilities. A DMADV-improved process or product will include all these measurements.
This step analyzes the projected product or service to find better strategies for attaining the objectives. You must detect the product and process flaws while analyzing and prototyping the improved one. All stakeholders perform in this stage. The production and testing teams evaluate the final product or service to provide a foundation for improvement. Then, the leaders use data to discover process adjustments that enhance product quality. Finally, the teams decide on the procedures and make modifications.
Once the analysis is ready, use the findings to design your product, service, or process. You may perform several revisions of the analytical data to compare the new design to the required criteria. The test members of your team should next evaluate new designs’ taking client satisfaction as the benchmark. All the internal testing for necessary design modifications should be performed per the client’s needs.
Verifying consumer satisfaction is the fifth phase of DMADV. It ensures the product is developed while maintaining the required standard. You should keep integrating customer inputs and updating the product or service after launch to imply this verification stage correctly. No matter how often you need to verify your production, the end goal will always be a product that satisfies all client needs.
The Advantages of DMADV
The structured problem-solving methodology of DMADV Six Sigma has several advantages. Here is a list of them:
- Customer-focused production : DMADV strongly emphasizes understanding and meeting customer needs throughout the design process. Hence, you can ensure your complete production process is consumer-focused.
- Systematic approac h: The DMADV methodology provides a step-by-step process for developing new products or processes, which reduces the risk of missing essential requirements. With such a systematic approach, all stakeholders can work together to produce results quickly.
- Data-driven solutions : This framework relies heavily on data to guide decision-making throughout the design process. It leads to more objective-oriented and informed decisions.
- Reduced waste and cost : DMADV tools can help you increase efficiency and profitability by focusing on critical requirements and identifying unnecessary resource wastage.
- Improved product quality : DMADV rigorously analyzes a product or service that helps you ensure the result is high quality and meets customer expectations.
- Competitive advantage : When you design a new product or service using DMADV, it gets automatically tested for customer satisfaction. This way, you gain an edge over your competitors.
- Continuous improvement : As DMADV allows you to rethink product designs, you can use it for continuous product/service improvement.
Examples of DMADV
DMADV is used widely for streamlined production across different industries. Here are a few examples of how the DMADV methodology shapes multiple sectors’ products, services, or process design. Let’s take a look.
When to Use the DMADV Methodology?
DMADV Six Sigma is most useful when designing a new product or process that meets specific customer/client needs while ensuring zero wastage and streamlined production.
Here are some instances of its application:
- New product development: While developing a new product that meets specific customer-defined requirements, DMADV can help you ensure the result is high quality and caters to all needs.
- Process redesign: DMADV can help you identify and redesign faulty processes according to consumer requirements. This will allow you to build a more effective and efficient product or service.
- Regulatory compliance: An organization must comply with specific regulatory requirements, like environmental regulations or safety standards. DMADV can help you structure and implement a new process that meets those needs.
- Competitive pressure: When you need to outperform your competitors, DMADV enables you to find out where they could be improved to serve the customers. You can integrate those processes into your business with a thorough DMADV analysis of consumers’ wants.
- Quality improvement: If an organization wants to improve its existing products or services, DMADV can help identify the ones of higher quality that better meet customer needs.
What’s the Difference Between DMADV and DMAIC?
Although DMADV and DMAIC are part of the Lean Six Sigma philosophy and share some similarities, they are markedly different. The chief difference between DMADV and DMAIC is that the former focuses on developing new processes, products, or services, while the latter is used to improve an existing process. Thus, DMADV measures customer needs and specifications, while DMAIC measures the process’s performance. DMAIC focuses on enhancing business processes to reduce and eliminate defects, and DMADV develops business models to meet customers’ requirements.
DMADV is a verification and design process for new projects, while DMAIC is an improvement and control process for preexisting models.
All About DMADV Best Practices
The following best practices are essential to the DMADV process.
- Engagement. At the start, identify who should be on the core and extended teams. Most DMADV projects need a wide array of engaged functions.
- Understand your customer’s requirements. Since you’re just starting, take the time to fully understand what the customer needs and how, based on your findings, you will be able to measure key metrics and CTQs.
- Divide the project into manageable pieces. Given the method’s intensity, allocate some time for the team to absorb and internalize all the process’s activities and outcomes. Expect profoundly serious diminishing returns if meetings are too long or frequent.
Get Online Six Sigma Training to Gain DMADV & Other Six Sigma Skills
Every detail mentioned above defines how DMADV methodology can help you redesign existing products or services and create a new one after deciding its market fit. But you must remember the use of DMADV will entirely depend on what industry you are serving and what product or service you want to develop. For example, the DMADV methodology benefits industries where innovation and quality are critical, such as healthcare, finance, and technology.
Whether you’re an aspiring Lean Six Sigma expert or want to improve organizational efficiency, you should know about DMADV. It’s a robust and specialized methodology, and mastering it can set you apart from other Lean Six Sigma professionals and enhance your career prospects.
Online Six Sigma training will help you use DMADV like a pro and efficiently build new products or services. A post graduate program in Lean Six Sigma is one such training offered by Simplilearn in collaboration with the University of Massachusetts. In this program, you’ll get an in-depth and comprehensive understanding of the principles, tools, and techniques of Lean Six Sigma and its applications in different industries. You will also acquire hands-on training and work on real-world projects, where you’ll learn to apply Lean Six Sigma concepts, tools, and techniques practically.
On completing the course, you’ll receive a certificate from the prestigious UMass Amherst, enhancing your CV and making you valuable to your current or future employers.
Indeed.com shows project managers in the United States earn a yearly average of $87,640, with a low range of $56,256 and a maximum range of $136,532.
Ready to become a Lean Six Sigma expert in six months? Enroll to get started!
Q: What is the DMADV process? A: The DMADV process is:
- Define the requirements or changes
- Measure the required resources
- Analyze the resources to ensure they are enough
- Design a plan of action to initiate the change
- Verify if the process and results are working in your favor
Q: What is the difference between DMAIC and DMADV? A: DMADV is a verification and design process targeted at new projects, while DMAIC is an improvement and control process for pre-existing models.
Q: What is an example of DMADV? A: A team could use DMADV to create new packaging for a product or change an existing package.
Q: What are the advantages of DMADV? A: The advantages are:
- It’s customer-driven
- It helps achieve maximum customer satisfaction while increasing profits
- It helps to reduce defects
- It focuses on the whole production and planning process
- It helps establish areas for improvement before it encounters defects
Leave a Comment Cancel Reply
Your email address will not be published. Required fields are marked *
Recommended Articles

What Is Lean Management? Principles & Everything You Need to Know
Discover the essence of lean management – a powerful approach to streamline processes and maximize efficiency. Explore its principles and benefits in our comprehensive guide.
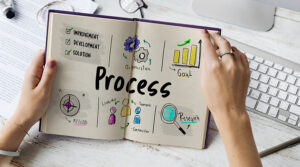
What is Process Mapping in Six Sigma? Here’s Everything You Need to Know
Demystifying Process Mapping in Six Sigma: Learn to optimize workflows and enhance quality. Dive into this essential quality management tool.
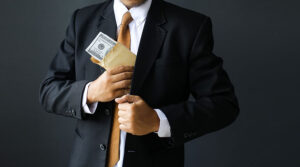
Six Sigma Black Belt Salaries in 2024: Everything You Need to Know!
Get to know about salaries and factors affecting six sigma black belt salary and the skills required to have an incremental effect on your pay scale.
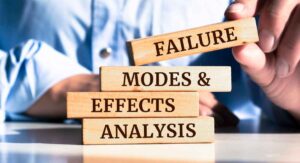
A Guide to Failure Mode and Effects Analysis
Explore Failure Mode and Effects Analysis with our easy-to-understand guide. Learn what it is, why it’s useful, how to use it, and its key applications.
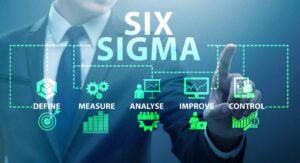
A Guide to Design of Experiments in Six Sigma
In today’s hypercompetitive world, organizations must streamline their operations and workflows to stay ahead of the game. Lean Six Sigma and the design of experiments are methodologies that can help them do this. Learn more in this article.
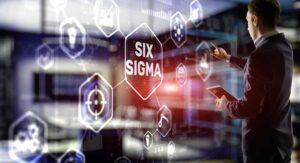
A Guide to Six Sigma Projects
Originally developed for manufacturing processes, the Six Sigma methodology is now leveraged by companies in nearly all industries. In this article, we will share information about successful Six Sigma projects, methods, and more.
Lean Six Sigma Certification
Learning Format
Online Bootcamp
Program benefits.
- Green and Black Belt exam training material included
- Aligned with IASSC-Lean Six Sigma
- Masterclasses from top faculty of UMass Amherst
- UMass Amherst Alumni Association membership

DMADV: The Methodology for Redesigning Broken Processes
Updated: July 17, 2023 by Ken Feldman

Lean Six Sigma is a set of tools used to improve organization processes. One tool, DMAIC, is used to improve existing processes. Define-Measure-Analyze-Design-Validate/Verify (DMADV) is a tool for designing new processes or improving processes that are too broken to fix.
This article will focus on how DMADV is used, its benefits and best practices, and an example of how it can be applied.
Overview: What is DMADV?
According to iSixSigma.com , DMAIC is defined as a data-driven process-improvement methodology that focuses on properly identifying the problem, utilizing data to determine the root cause, developing and implementing the solution, and verifying that the solution continues to be effective over time.
DMAIC is an acronym that stands for Define, Measure, Analyze, Improve, and Control. It is used to improve existing processes either incrementally or breakthrough.
But, what if the existing process is not able to be improved enough to meet expectations? Or, if you need to design a new process? Then, DMADV is the tool of choice.
The graphic below shows the steps of the DMADV process.

DMADV is a Design For Six Sigma (DFSS) method that focuses on customers. The DMADV (Define-Measure-Analyze-Design-Validate/Verify) method aims to design a new process or product, or to redesign a problematic process or product.
The approach initially follows the first three steps of DMAIC and then shifts to a different perspective in the Design/Redesign and Validate/Verify steps to achieve improvement.
Let’s explore the DMADV steps in more detail.
Define The goals here are to identify the purpose of the project and identify and set realistic and measurable goals based on the expectations of your customer, organization, and stakeholder(s). A clear definition of the project is established, and every strategy and goal aligned with the expectations of the organization and customers.
Measurement This step defines the factors that are critical to quality ( CTQs ). These need to be quantified and data collected.
Analyze In this step, you will:
- Develop design alternatives
- Identify the optimal combination of requirements to achieve value within any constraints
- Develop conceptual designs
- Evaluate them
- Select the best elements
- Develop alternatives for your design
Design This step includes both a detailed and high-level design for the selected alternative. The elements of the design are prioritized, and from there, a high-level design is developed. Then, a more detailed model will be prototyped in order to identify where errors may occur and to make necessary modifications.
Verify In this final step, the team validates and verifies whether the design is acceptable to all stakeholders. Is the design realistic? You may need to pilot the design and try some production runs to be sure the quality will meet expectations.
Lessons learned will be documented. You will also include a plan to transition the product or service to the process or product owner and to develop a control plan to sustain the change.
The graphic below compares DMAIC with DMADV.

3 benefits of DMADV
As a structured methodology for improvement, DMADV has several benefits.
1. Customer driven
DMAIC starts with the existing process or product and seeks to make an incremental change. DMADV starts with customer expectations and requirements and designs a new process or product to meet those.
2. Structured
The DMADV methodology is a sequential, structured set of activities and deliverables to allow a team to stay focused and on task.
3. Synergy
In addition to the members of a DMADV project team, many other parts of the organization are engaged in this process since considerations must be given to people, manufacturing, raw materials, engineering, and IT issues so that the final design is optimized for your organization.
Why is DMADV important to understand?
DMADV can be an intense process to execute. By understanding how it works, you will be able to complete your DMADV project without any serious problems.
Used for new processes
You can use DMAIC for improving existing processes. If you want or need to start with a fresh design, then the initial focus will be on the customer.
Requires an interactive approach to design
The process starts with a series of alternative designs before going to a preferred high-level design, and then cascading down to detailed designs and their components.
Prototyping is important
It is important to understand that you don’t jump from final design to execution. There are many unknowns in your new design, so it will be helpful to utilize prototypes and Design of Experiments (DOE) to confirm everything.
An industry example of DMADV
A company based in Germany produces and sells bicycles to a global marketplace. They had recently expanded production to the U.K. as well as Italy. Unfortunately, they started to experience some supply chain problems.
The decision was made to see if their current process can be redesigned to meet customer requirements using DMADV. In this case, the customer was really the leadership team since this was an internal issue. Here are some highlights of their project.
The goal was to redirect 100% of outsourced products from outside vendors to the U.K. and Italy. The project team consisted of team members from production, logistics, engineering, supply chain, and legal.
CTQs were identified based on leadership input. A current state, as-is process map was drawn. All suppliers and their products that were in scope were identified. Data was collected on delivery and inventory issues.
The team decided to focus on common parts based on volumes following the Pareto principle. The legal department contacted all suppliers and explained the new expectations for the shipping of bike components.
A new process was designed to consider the following:
- New contracts with component suppliers
- Supply chain calculated new expected order volumes
- Component prices were reviewed and repriced
- Logistics needed to contact transportation companies and negotiate prices, delivery times, and overall expectations
- Engineering reviewed drawings and documentation for components
To validate the new process, pilot components were transferred using the revised process. The team quickly realized they hadn’t considered the differences in customs requirements between the different countries. Revisions to the original design were made.
The new process worked well, and the company was able to improve its business results and local market competitiveness by 19% using this new sourcing strategy.
3 best practices when thinking about DMADV
This is a major team activity, so keep some of these things in mind.
1. Engagement
At the beginning, identify who should be on the team, both the core team as well as the extended team. Most DMADV projects require the engagement of a wide array of functions.
2. Understand the customer requirements
Since you are starting from scratch, take the opportunity to fully understand what the customer needs and how you will be able to measure the key metrics or CTQs.
3. Break the project into manageable pieces
Given the intensity of the method, allow some time for the team to absorb and internalize all the activities and outcomes of the process. There will be serious diminishing returns if meetings are too frequent or too long.
Frequently Asked Questions (FAQ) about DMADV
When should dmadv be used .
DMADV should be used when you want to improve a process or product that is too broken to fix with DMAIC or has reached its level of entitlement. This means the product or process won’t be able to fulfill customer requirements no matter how hard you try to improve the existing state.
What are the five stages of DMADV?
The five stages are: Define, Measure, Analyze, Design/Redesign, and Validate/Verify .
Is DMADV similar to DMAIC?
Yes, both are designed to improve a process or product. The first three steps of each, DMA, are similar, but then they diverge. The IC in DMAIC is to improve and develop a control plan. The DV in DMADV is the design of a new product or process and then to validate or verify it works.
Summing up DMADV
The steps of DMADV (Define, Measure, Analyze, Design, and Validate) are used to improve a product or process when the current process cannot be incrementally improved to a level that will satisfy customer requirements, or when there is no existing product or process.
About the Author
Ken Feldman

- Compliance Automation
- Blogs Benefits Realization Management Configuration Management Change Management Disaster and Recovery ( DR) Heatmap Meetings and Actions PMO Starter MS Project Templates Project Budget Project Closure Project Dashboards Project Implementation Project Initiation Project Management Concepts Project Risk Management Project Plans Project Status Reports Quality Management RAID Resource and Capacity Plans Stakeholder Management Task Management Testing Timeline and Roadmap
- All In One Pack

- Home icon-chevron
- icon-chevron Software
- Compliance Automation icon-chevron
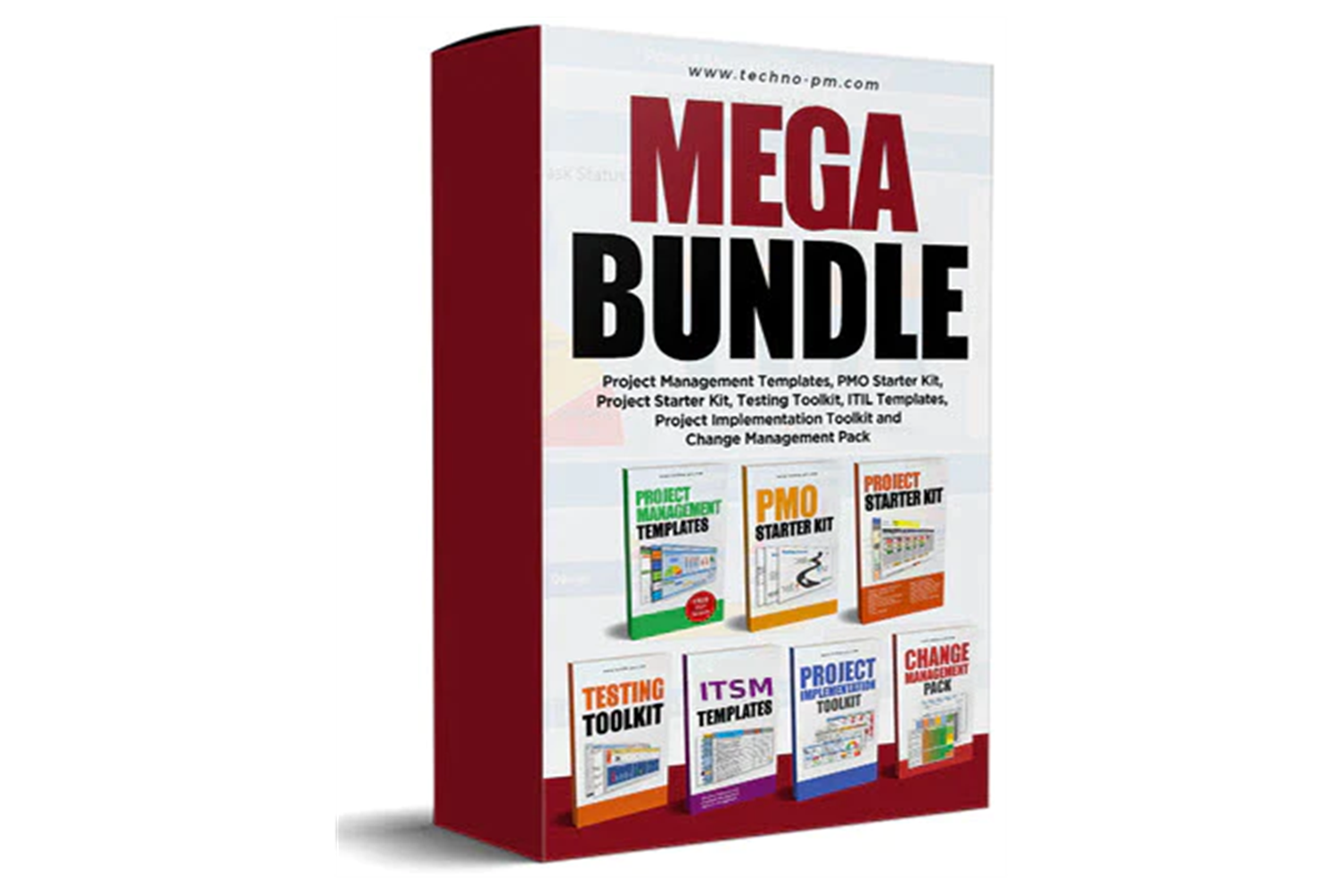
- icon-chevron Blogs
- icon-chevron Benefits Realization Management
- Configuration Management icon-chevron
- Change Management icon-chevron
- Disaster and Recovery ( DR) icon-chevron
- Heatmap icon-chevron
- Meetings and Actions icon-chevron
- icon-chevron PMO Starter
- MS Project Templates icon-chevron
- Project Budget icon-chevron
- Project Closure icon-chevron
- Project Dashboards icon-chevron
- Project Implementation icon-chevron
- icon-chevron Project Initiation
- Project Management Concepts icon-chevron
- Project Risk Management icon-chevron
- Project Plans icon-chevron
- Project Status Reports icon-chevron
- Quality Management icon-chevron
- RAID icon-chevron
- icon-chevron Resource and Capacity Plans
- Stakeholder Management icon-chevron
- Task Management icon-chevron
- Testing icon-chevron
- Timeline and Roadmap icon-chevron
- All In One Pack icon-chevron
The DMADV Methodology: What It Is And How It Works?
Six Sigma has been helping companies meet their project goals and deadlines since 1986, when Motorola was first introduced. Within Six Sigma, various methodologies can be used for problem-solving and process improvement. And one of them is DMADV, the other one being DMAIC.
Most people are familiar with DMAIC but not with DMADV. In this article, learn everything you need to know about the DMADV methodology.
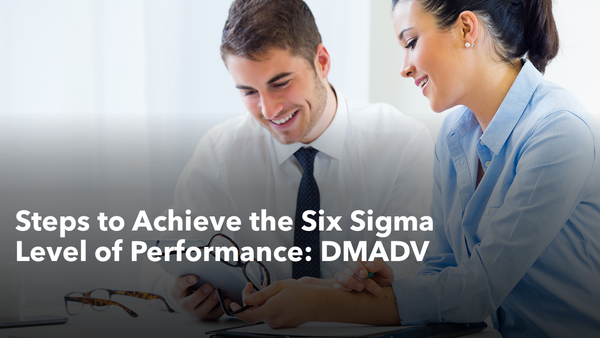
What Is DMADV?
DMADV is one of the two Six Sigma methodologies used to achieve the Six Sigma level of performance. It stands for Define-Measure-Analyze-Design-Verify, which are the five phases of this methodology.
As a project manager or six sigma practitioner, you will use this methodology when there's a need to create a new project or product. Implementing DMADV requires that the person managing the project have a Six Sigma Green, Black, and Master Belt certification. It also demands support from a Project Owner and/or Process Owner for successful execution.
The Phases In DMADV
As mentioned above, DMADV is made up of five steps, which are:
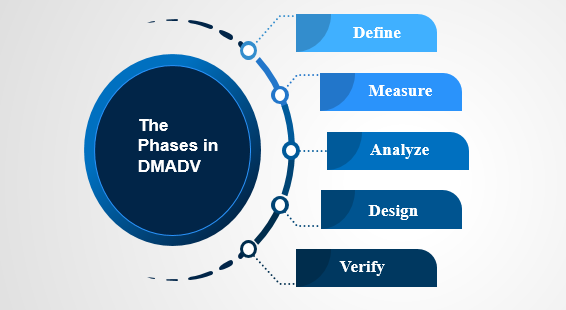
Let's explore each of the five phases in greater detail.
1. Define: The first phase is all about getting your vision right, because of which this phase is perhaps the most important. First, you're required to define the purpose and expectations of the project, process, or service. Based on that, you then set actionable and achievable goals. In the define phase, your goal is to define clear definitions that are understood by all the company stakeholders . Therefore, you should act from the organization's point of view rather than from a project manager's perspective. Along with that, you develop the policies, guidelines, and potential risks for the project.
2. Measure : Once the project or process is underway, the next phase is the measurement phase. Towards the end of phase one or the beginning of this phase, you should define CTQs or Critical to Quality metrics . These metrics will help you decide if your processes are up to the mark or need reassessment. In detail, here are the things you need to work on: Define requirements and market segments Define critical design parameters Design scorecards to evaluate different design components You should also define all project-specific factors that are important to the quality and production process.
3. Analyze : The next phase is about analyzing the process and recording the metrics/factors you've defined in the previous phase.
The analysis phase will include the following:
- To develop design alternatives.
- To figure out the best combination of requirements to deliver the best results.
- To develop conceptual designs.
- To evaluate each component and select the best ones
Unlike other phases, analysis is going to be a continuous phase. You’re likely going to run multiple analyses of a process. After the first few analysis, the project team can create the baseline for improvement. This will guide the entire team towards process optimization and help figure out the best process.
4. Design : Next comes the design phase. This is another critical phase that largely determines the success of your project. Therefore, don't be shy from devoting more time to this phase. The process expert should take the lead for this phase rather than a Six Sigma expert. That's because he is the one who is familiar with the minute details of the process. The process, along with the team, should look at the inputs from the analysis phase. Then cherrypick the components that they believe will have the best impact on the project or process. Based on the components, the team moves toward a high-level design.
5. Verify : The final phase of the DMADV Six Sigma methodology is the verification or verify phase. The team and all the stakeholders validate that the design is up to the mark. It's required that you run several pilot processes and production before approving a project or process for real-world applicability. Once the expectations are confirmed by the Six Sigma team and higher management, you can expand the deployment. In this phase, developing a plan that details transitioning the product to a routine operation is also recommended. Along with that, the plan should ensure that this transition is sustainable. So those were the five phases of DMADV methodology. Each phase is important in its own way. So devote adequate time to each phase for building a profitable product or service.
When Is DMADV Used?
There are various Six Sigma methodologies. Therefore, knowing when to adopt a particular method for your process is important. Generally, DMADV is used for new and nascent projects. For example, after identifying a problem or spotting a market opportunity, you'll feel the need to start a new project. Ideally, you'd want it to start delivering results from the very beginning. That's when you'd have to use the DMADV methodologies by following the five phases. At the core of DMADV is understanding customer's expectations. Then, you design CTQs to correlate to the quality parameters that would satisfy the customers' needs. Therefore, you can also use DMADV for redesigning an existing process or product.
Difference Between DMAIC & DMADV
DMAIC and DMADV are two common Six Sigma methodologies. Both of them share the same vision, which is to achieve Six-Sigma-level performance. They also share common phases, but they're used under different circumstances. Therefore, one cannot be used to replace the other.
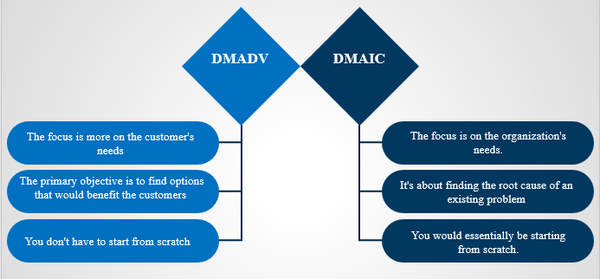
The main difference is that you would use DMAIC (Define-Measure-Analyze-Improve-Control) to improve an existing process. At the same time, you would employ the DMADV methodology for a completely new process or project. Besides that, here are some key differences:
- In DMADV, the focus is more on the customer's needs, while in DMAIC, the focus is on the organization's needs.
- In DMADV, the primary objective is to find options that would benefit the customers. In DMAIC, it's about finding the root cause of an existing problem.
- In DMADV, you don't have to start from scratch. However, in DMAIC, you would essentially be starting from scratch.
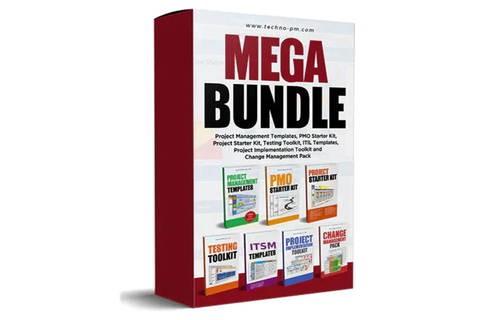
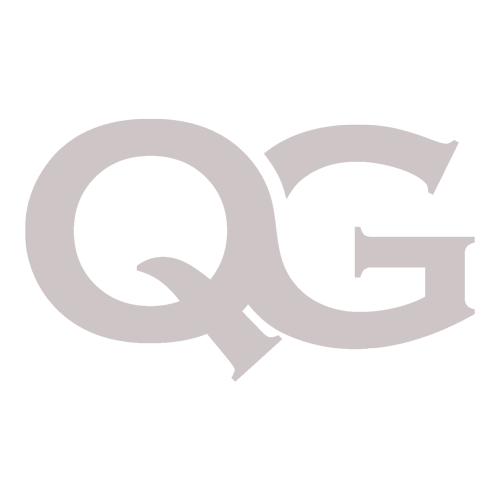
- ASQ® CQA Exam
- ASQ® CQE Exam
- ASQ® CSQP Exam
- ASQ® CSSYB Exam
- ASQ® CSSGB Exam
- ASQ® CSSBB Exam
- ASQ® CMQ/OE Exam
- ASQ® CQT Exam
- ASQ® CQPA Exam
- ASQ® CQIA Exam
- 7 Quality Tools
- Quality Gurus
- ISO 9001:2015
- Quality Cost
- Six Sigma Basics
- Risk Management
- Lean Manufacturing
- Design of Experiments
- Quality Acronyms
- Quality Awareness
- Quality Circles
- Acceptance Sampling
- Measurement System
- APQP + PPAP
- GD&T Symbols
- Project Quality (PMP)
- Full List of Quizzes >>
- Reliability Engineering
- Statistics with Excel
- Statistics with Minitab
- Multiple Regression
- Quality Function Deployment
- Benchmarking
- Statistical Process Control
- Quality Talks >> New
- Six Sigma White Belt
- Six Sigma Yellow Belt
- Six Sigma Green Belt
- Six Sigma Black Belt
- Minitab 17 for Six Sigma
- Casio fx-991MS Calculator
- CSSYB/LSSYB Mock Exam
- CSSGB/LSSGB Mock Exam
- CSSBB/LSSBB Mock Exam
- ASQ® CQA Preparation
- ASQ® CQE Preparation
- ASQ® CQPA Preparation
- ASQ® CQIA Preparation
- CQE Mock Exams
- CMQ/OE Mock Exams
- CQA Mock Exams
- CQIA Mock Exams
- CQPA Mock Exam
- CQT Mock Exam
- CQI Mock Exam
- CSQP Mock Exam
- Design of Experiments (DoE)
- Measurement System Analysis
- Statistics Using R
- Data Visualization with R
- Statistics Using Python
- Data Visualization with Python
- Regression with Minitab
- Logistic Regression
- Data Analysis Using Excel
- The Git Mindset
- Statistics Quiz
- Root Cause Analysis
- Kano Analysis
- Lean Management
- QMS Lead Auditor
- Quality Management
- ISO 9001:2015 Transition
- Project Quality Manager
- Practice Tests
- Summary Sheets
- गुणवत्ता.org
What is DMADV?
- What is DMADV ?
** Unlock Your Full Potential **
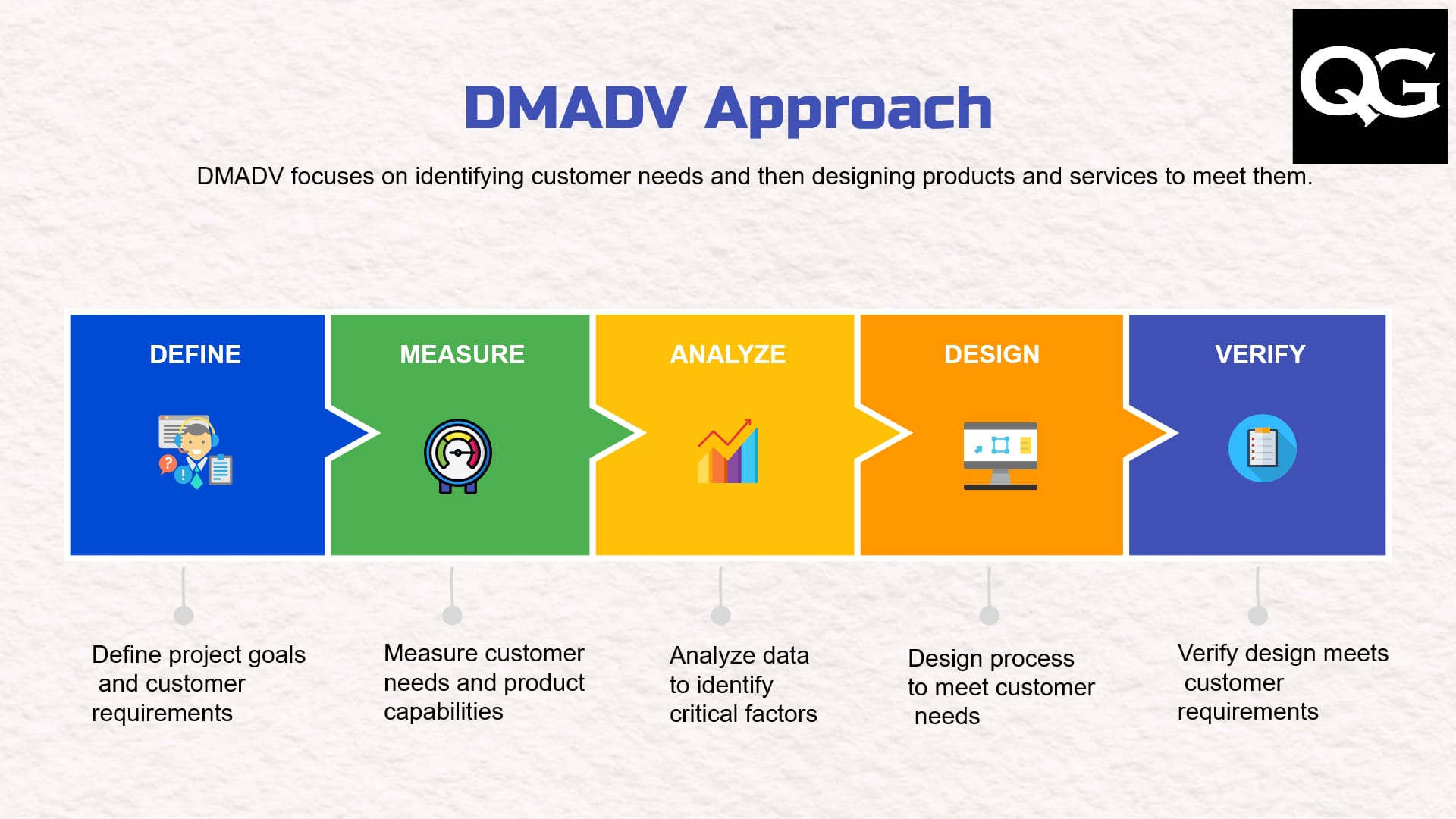
Six Sigma is a data-driven approach to improving business processes and reducing defects in products and services. It is based on statistical methods and is used by organizations to improve quality, reduce costs, and increase customer satisfaction. Six Sigma has two main approaches: DMAIC (Define, Measure, Analyze, Improve, and Control) and DMADV (Define, Measure, Analyze, Design, and Verify).
DMAIC is a process improvement methodology used to improve existing processes. DMAIC is typically used to improve processes already in place and require optimization. On the other hand, DMADV is a process improvement methodology used to create new products or processes. DMADV is typically used to develop new processes or products that meet or exceed customer expectations.
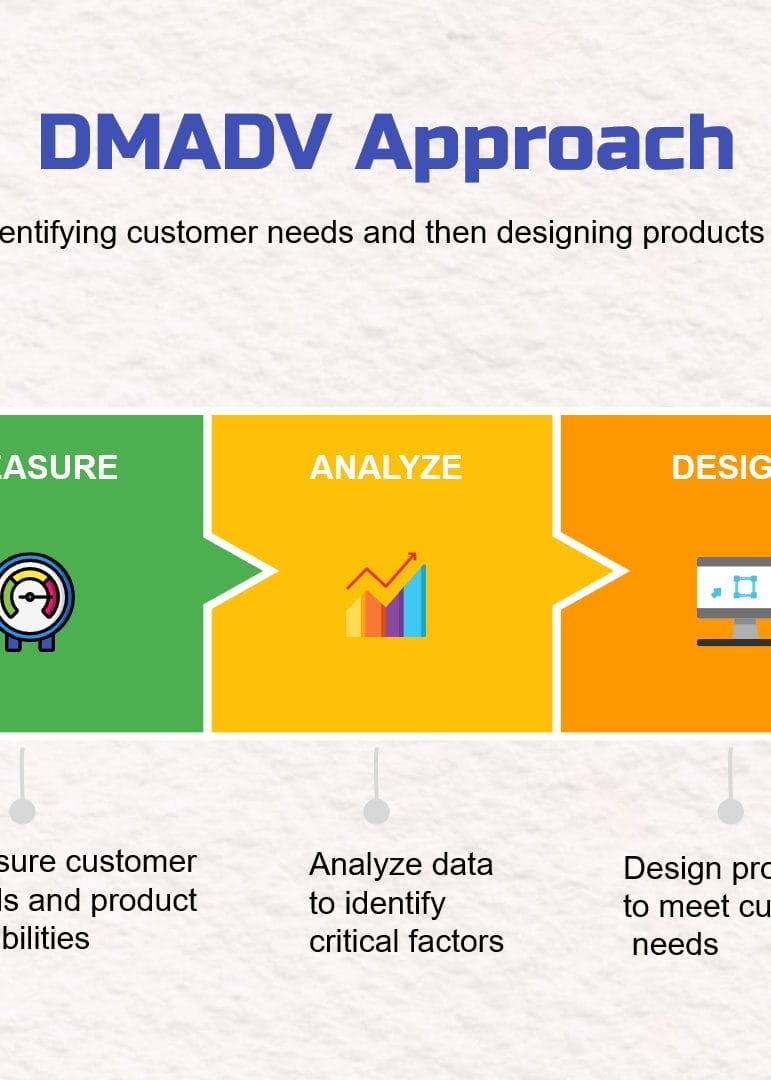
The DMADV process has five steps, which are explained in detail below:
The first step in DMADV is to define the problem or opportunity. In this step, the project team identifies the scope of the project, the stakeholders, and the goals and objectives. The team also identifies the voice of the customer ( VOC ) and the critical-to-quality ( CTQ ) characteristics important to the customer and establishes clear project goals.
The second step in DMADV is to measure the current performance of the process, product, or service. In this step, the team collects and analyzes data to establish a baseline and identify the gap between the current and desired performance.
The third step in DMADV is to analyze the data and identify the root cause of the problem using statistical tools. In this step, the team uses tools such as root cause analysis , regression analysis, and hypothesis testing to identify the factors causing the problem. Design alternatives are also explored in this step.
The fourth step in DMADV is to design a solution to the problem. In this step, the team develops a detailed design to address the root cause of the problem and improve the performance of the process, product, or service.
The fifth and final step in DMADV is to verify the solution's effectiveness. In this step, the team tests the solution in a pilot project or a controlled environment to ensure it meets the customer requirements and CTQ characteristics.
In conclusion, DMADV is a structured problem-solving methodology to improve processes, products, and services. The five steps of DMADV – Define, Measure, Analyze, Design, and Verify – provide a structured approach to problem-solving and help organizations deliver high-quality products and services that meet the needs of their customers. By following the DMADV process and using tools and techniques such as root cause analysis , DOE , and FMEA , organizations can improve their processes, products, and services and gain a competitive advantage in the marketplace.
Similar Posts:
October 24, 2022
The Best Lean Six Sigma Interview Questions: Guaranteed to Impress! (Part 1)
October 1, 2023
Attribute Agreement Analysis (AAA) in MSA
September 5, 2023
Gage Repeatability and Reproducibility (GR&R) – An Overview
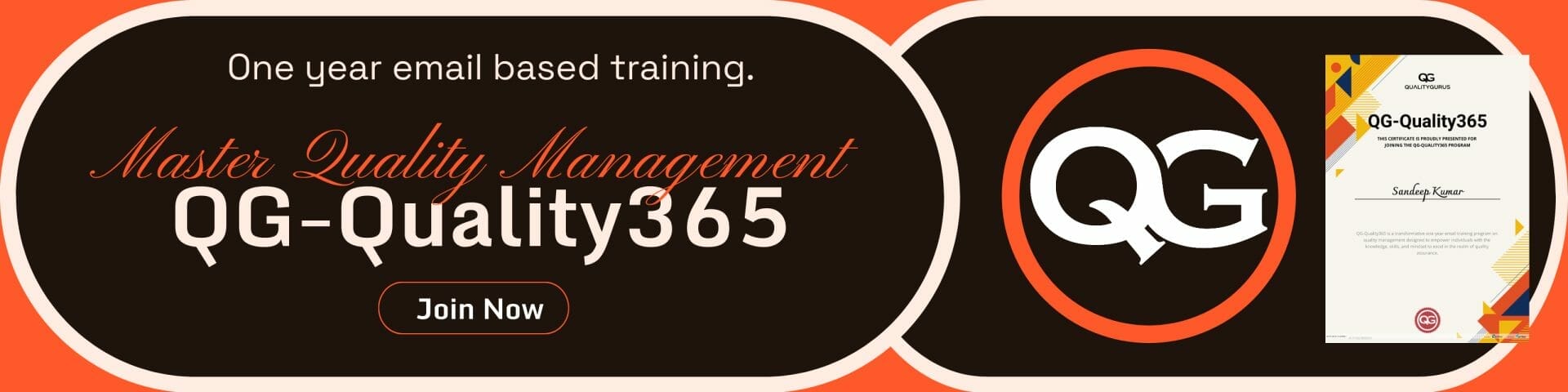
49 Courses on SALE!
Join us for an online Lean Six Sigma Live Webinar Date: May 7, 2024 Time: 12pm (ET)
DMAIC Vs. DMADV
28 May, 2021
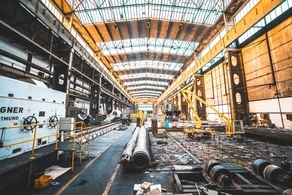
For developing a new product, service or process, there’s a modified version called DFSS ( Design for Six Sigma ). The process most often used in DFSS is called DMADV (Define—Measure—Analyze—Design—Verify).
DMAIC (Define—Measure—Analyze—Improve—Control)
DMAIC is the more well-known and most-used LSS project method. DMAIC focuses on improving an existing process by incorporating the following phases:
DMADV (Define—Measure—Analyze—Design—Verify)
DMADV is focused on the process of designing a new product, service or process, incorporating the following phases:
DMADVO is a lesser known DFSS method. The difference between DMADV and DMADVO is that “O” or “Optimize” has been added. Thus, DMADVO prioritizes the need for the organization to optimize the design after implementation.
Similarities of DMAIC and DMADV
Both DMAIC and DMADV :
- Use structured methods to reduce variation and solve problems
- Collect and analyze data to make informed decisions
- Use teams to solve problems
- Have a customer focus
- Use many of the same tools (brainstorming, FMEA, DOE)
Differences of DMAIC and DMADV
- DMAIC addresses the current process; DMADV addresses the design process.
- DMAIC reduces/eliminates defects (reactive); DMADV prevents defects (proactive).
- DMAIC includes specific solutions; DMADV is part of the solution design process.
- DMAIC includes controls to sustain the gains; DMADV includes verification and validation of the finished design.
DMAIC and DMADV provide a structured process for improvement. When applied properly with the applicable improvement tools, they can help ensure the success of your LSS projects, which can reduce costs and increase customer satisfaction.
About Purdue’s Online Lean Six Sigma (LSS) Certificate Program
Purdue University offers comprehensive online Lean Six Sigma (LSS) certificate programs designed for working professionals with varying levels of Lean Six Sigma experience. The online Lean Six Sigma certificate courses prepare professionals to satisfy the immense demand for Lean expertise, skills and certification.
Purdue offers the following courses 100% online:
- Six Sigma Green Belt
- Lean Principles
- Six Sigma Black Belt
- Six Sigma Green Belt Refresher
Request Information
To learn more about Purdue University’s online Lean Six Sigma Training and Certification program and download a free brochure , fill out this form. You can also email us at [email protected] or call us at (888) 390-0499 to speak to one of our program advisors.
Purdue University has engaged AllCampus to help support your educational journey. AllCampus will contact you shortly in response to your request for information. About AllCampus . Privacy Policy . You may opt out of receiving communications at any time.
* All Fields are Required. Your Privacy is Protected. Are you enrolling from outside the US? Click here.
Purdue Lean Six Sigma
Set yourself up for success with Lean Six Sigma Certification
Date: May 7, 2024 Time: 12pm (ET)
- [email protected]
- (888) 390-0499
Related Categories
- DMAIC Articles
- Lean Manufacturing Articles
- Six Sigma Articles
Latest News
- Six Sigma Belt Level Rankings
- Advance in Healthcare with Lean Six Sigma
- 4 Reasons to Become a Lean Six Sigma Black Belt
- Memberships
DMADV Process: the Basics and Steps

DMADV Process: this article describes the concept of the DMADV Process in a practical way. Next to what it is (including acronym), this article also highlights the phases and steps, the applications of this Process and DMAIC versus the DMADV Process. After reading you will understand the basics of this quality management tool. Enjoy reading!
What is the DMADV Process?
DMADV is a Six Sigma quality method that is used to design new processes, with the goal of delivering the final product to the client correctly. The goal of the DMADV Process is the creation of a high-quality product, whole keeping the customer and the customer’s need in mind during every phase of the project.
DMADV acronym
Each letter of the acronym DMADV is one of the five main phases of the project improvement initiative: Define, Measure, Analyse, Design en Verify.

Figure 1 – DMADV Process cycle
DMADV process is a Six Sigma method
Six Sigma is about process improvement as part of quality management. Existing products and/or services are improved using analytical techniques and statistics.
Six Sigma focuses on reducing variability in matters that are perceived as Critical to Quality (CTQ) by the customer. These CTQs are very important and vital to quality; it is about the internal critical quality parameters that relate to the customer’s wishes and needs. As such, CTQs are quality characteristics of the process or service that meet the requirements of the customer.
DMADV Process: phases and steps
DMADV is about the development of a new service, product or process. The DMADV Process is particularly useful for the implementing of new strategies and initiatives. Each phase is explained below.
In this first phase of the DMADV Process, it is about identifying the goal of the project, the process or the service.
Not just from the perspective of the organisation, but also from the perspective of other stakeholders , including customers. It should be clearly defined which guidelines are important for the development of a product or service, and if there are any potential risks and what the production schedule is.
During this first phase, the project manager determines what the most important customer needs are regarding the product or service to be newly developed. He determines this by using relevant, previously gathered customer information and customer feedback.
In the definition phase, a garden furniture manufacturer can decide to focus on the production of wooden sun loungers. Based on previously collected customer information, the manufacturer knows it is very important to customers that the wood being used comes from fair trade.
In addition, customers have indicated that the lounger should be adjustable in three positions, have a high back support and head support and have an environmentally friendly coating that allows the lounger to be left outside. During this definition phase, the manufacturer can also determine if it would be lucrative to design such a sun lounger.
This phase of the DMADV Process is aimed at the collecting and recording of data that are relevant to the CTQ measures that have been identified during the first phase. The data that is collected during the measuring phase are essential to the process, as it will be used to drive the rest of the process.
In the case of DMADV, there are no CTQs in the measuring phase yet. After all, there is no new product yet, let alone a production process. During this measuring phase, it is about determining what the customer thinks is important about a new product.
These factors are subsequently linked to quality, which leads to CTQs. If a value is assigned to all design components, this leads to an effective approach to start the production process. It is important to determine which components of the production process are critical to all stakeholders.
The customer requirements will eventually be translated to clear project objectives, in order to get a product that can distinguish itself from the competition. The garden furniture manufacturer now links what the customers think is important to the CTQs. If it is not possible to source fair trade wood, production cannot start.
The same goes for the environmentally-friendly coating and the design that needs to meet the minimum requirements; 3 positions, high back support and head support. During this measuring phase, the manufacturer checks whether the design costs, manufacturing costs and raw materials costs are worth the eventual selling prise.
The analysis phase of the DMADV Process is closely linked to the measuring phase, because the project team will analyse and test all the gathered data. This results in a good basis to measure improvements during the production process. During this analysis phase, design alternatives are developed and they determine the optimum combination of requirements.
An estimate of the total life cycle costs of the design is also made during this stage. After exploring the different design alternatives, a rough product design is created (functional specification) that meets the previously defined CTQ’s as much as possible.
In this phase, the garden furniture manufacturer will check out different importers from who they can purchase fair trade wood. They will determine the origin of the wood, so they can use it as background information for sales.
They also analyse different environmentally-friendly coatings, their advantages and disadvantages and the strengths of the different options. The analysis of different designs will receive close attention as well. Analysing is a time-consuming phase and the manufacturer would be wise to set a deadline to prevent cost-overruns.
The design phase of the DMADV Process consists of the design of the product or service that fully matches the customer requirements. During this phase, the project team uses data from the previous phases, leading to a product that is suitable for the customer with all possible additional adjustments that might be needed.
It is a detailed and high-quality design which will be made into a prototype. During production of this prototype, they also look at the production process. The goal is not just to develop a production process that creates good products, but one which is also logistically efficient.
Based on the earlier analysis, the garden furniture manufacturer has made certain choices. They have found a supplier for fair-trade wood, know which environmentally-friendly coating they will use and they have chosen a design in which adjusting the lounger is quickest, safest and easiest and in which the back support and neck support are connected in a good way.
In the manufacturing process, close attention will have to be paid to the layout of the woodworking machinery and what route the process will follow (routing), so no time is wasted and an x number of loungers will leave the factory every hour.
The verification phase of the DMADV Process might be the final phase, but it is not the end of the process. To safeguard quality, it is important to continue to verify and make adjustment to the product where necessary. In this last phase, the design is final and the product is ready to be sold.
During this phase, the project team receives feedback from the customers and user experiences, and they will make necessary adjustments to better meet the customers’ needs. The project team will also determine additional CTQ measures to be able to monitor customer feedback after delivery of the final product.
During this phase, the garden furniture manufacturer feels it is very important to find out what its customers/users think of the wooden sun lounger. Are they satisfied about the fair-trade wood that was used, do they have sufficient information about the origin of the wood, do they find the lounger comfortable and is it user-friendly?
Is the head support pleasant and in line with the back support and is the coating sufficiently water resistant? If after six months it turns out that there are some complaints about annoying spots in the wood damaged by weather, then the coating might need to be changed. In that case, the garden furniture manufacturer will use the data collected earlier during the analysis phase to find a proper alternative.
DMADV Process applications
DMADV is mainly used for products or services that do not exist yet and still have to be developed by a company. In addition, it is also used for existing products or services that not yet meet certain customer specifications. For each DMADV Process improvement project, additional emphasis can be put on certain components, even though the goal remains the same; addressing a problem that has been identified and achieve the desired results.
A DMADV Process improvement project can take several months or even years, but the final result is a product or service that fully meets the customers’ needs and wishes.
DMAIC versus the DMADV Process
The DMADV Process is very similar to the DMAIC Process , which stands for Define – Measure – Analyze – Improve – Control.
Both methods are used in Six Sigma methodologies and in many respects they match. Both are designed to make business processes more efficient and effective. However, the models are not interchangeable and are used for different business processes.
However, there are some important differences. The first three letters in the acronym match. The biggest difference is the way in which the last two steps of both models take shape; DMAIC is about improving and controlling a business process. It defines a business process and its applicability, while the DMADV Process defines the customer’s needs, as it relates to the service or product.
The DMAIC Process measures current processes of a process, while the DMADV Process measures customer needs.

It’s Your Turn
What do you think? What is your experience with the DMADV Process? Do you recognize the practical explanation or do you have more additions? What are your success factors for good problem solving?
Share your experience and knowledge in the comments box below.
More information
- Cronemyr, P. (2007). DMAIC and DMADV-differences, similarities and synergies. International Journal of Six Sigma and Competitive Advantage, 3(3), 193-209.
- Pyzdek, T., & Keller, P. A. (2003). The Six Sigma Handbook . McGraw-Hill .
- Jacobides, M. G., & Billinger, S. (2006). Designing the boundaries of the firm: From “make, buy, or ally” to the dynamic benefits of vertical architecture. Organization science, 17(2), 249-261.
- Johnson, J. A., Gitlow, H., Widener, S., & Popovich, E. (2006). Designing New Housing at the University of Miami: A “Six Sigma”© DMADV/DFSS Case Study. Quality Engineering, 18(3), 299-323.
How to cite this article: Mulder, P. (2017). DMADV Process . Retrieved [insert date] from Toolshero: https://www.toolshero.com/quality-management/dmadv-process/
Published on: 10/03/2017 | Last update: 04/16/2024
Add a link to this page on your website: <a href=”https://www.toolshero.com/quality-management/dmadv-process/”>Toolshero: DMADV Process</a>
Did you find this article interesting?
Your rating is more than welcome or share this article via Social media!
Average rating 4 / 5. Vote count: 5
No votes so far! Be the first to rate this post.
We are sorry that this post was not useful for you!
Let us improve this post!
Tell us how we can improve this post?

Patty Mulder
Patty Mulder is an Dutch expert on Management Skills, Personal Effectiveness and Business Communication. She is also a Content writer, Business Coach and Company Trainer and lives in the Netherlands (Europe). Note: all her articles are written in Dutch and we translated her articles to English!
Related ARTICLES

HACCP plan explained

Charles Kepner biography and books

Eight Dimensions of Quality by David Garvin

Measurement System Analysis (MSA)

Agile Crystal Method explained

Philip Crosby biography, quotes and books
Also interesting.

Day In the Life Of (DILO) Theory and Examples

Failure Mode and Effects Analysis (FMEA)

Scientific Management Theory and Taylorism
One response to “dmadv process: the basics and steps”.
Very very nice
Leave a Reply Cancel reply
You must be logged in to post a comment.
BOOST YOUR SKILLS
Toolshero supports people worldwide ( 10+ million visitors from 100+ countries ) to empower themselves through an easily accessible and high-quality learning platform for personal and professional development.
By making access to scientific knowledge simple and affordable, self-development becomes attainable for everyone, including you! Join our learning platform and boost your skills with Toolshero.

POPULAR TOPICS
- Change Management
- Marketing Theories
- Problem Solving Theories
- Psychology Theories
ABOUT TOOLSHERO
- Free Toolshero e-book
- Memberships & Pricing

- Quality Improvement
- Talk To Minitab
DMAIC vs. DMADV vs. DFSS: A Guide on Six Sigma Terminology
Topics: Lean Six Sigma , Six Sigma , DMAIC , Minitab Engage
When you learn Six Sigma, familiarizing yourself with the alphabet soup of acronyms and abbreviations can be overwhelming. From FMEA and C&E Matrix to Gage R&R and SIPOC… the list goes on and on! DMAIC, DMADV, and DFSS can be some of the trickiest to keep straight because they sound so similar.
But it's OK. We're here to help with that!
DFSS, DMAIC and DMADV help quality improvement practitioners keep their projects focused with an established route to follow to completion. Each letter stands for a step of the processes.
Interested in Discussing Process Improvement with the Experts?
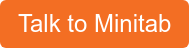
Starting with DFSS and DMADV
First off, DFSS stands for “ D esign F or S ix S igma” and it focuses on the idea of creating a new product or process or completely redesigning a product or process through a Six Sigma project. DMADV is a type of DFSS that is commonly used by many businesses and organizations.
DMADV stands for:
A Focus on DMAIC
DMAIC is a well-known Six Sigma project methodology that focuses on improving an existing process rather than creating a new pro
uct or process or a complete redesign like DFSS or DMADV. In general, DMAIC methodology can be included as a part of other process improvement initiatives, such as Lean, or enacted on its own.
DMAIC stands for:
Choosing Projects with DMAIC in Mind
One of the important components of good project selection is choosing a project most likely to benefit from the DMAIC approach, meani
ng it involves a defect or a process with changes that can be measured accurately. Without measurements, you would be unable to detect any improvement.
Once you have a project focus, you begin to identify and define the problem to solve. For more information on this journey, check out DMAIC Tools and Techniques: The Define Phase . Whether you are using DMAIC or DMADV, the real benefit of these methodologies is that they provide structured problem-solving to ensure success.
And when this information is available in a solution like Minitab Engage , sharing the learnings is easier than ever .
Customized roadmaps can be quickly and seamlessly created to include any additional steps needed from your quality team and transform into templates for future projects, saving time and the hassle of recreating the same roadmap again and again.
Put DMAIC or DMADV into Action Yourself
You might also like.
- Trust Center
© 2023 Minitab, LLC. All Rights Reserved.
- Terms of Use
- Privacy Policy
- Cookies Settings
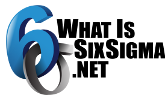
- Lean Six Sigma
DMADV – Another SIX SIGMA Methodology
By now, you would be familiar with DMAIC methodology and know when, where and how it is used and the benefits of it in problem solving and performance improvement. But DMAIC is not the only methodology that is used in Six Sigma . There is another common term DMADV which is equally important as DMAIC. To become a master in Six Sigma and use it for business purposes, it is essential to be familiar with all the other methodologies. For that, we need to first understand where, when and why we use DMADV.
Similar to DMAIC, DMADV is another methodology that is used in organizations to achieve Six Sigma level of performance. Let’s understand DMADV in little more detail with the help of the below table:
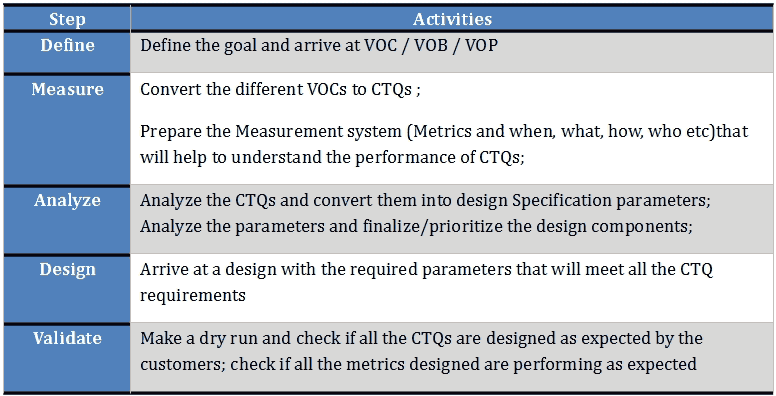
Table1: The Phases in DMADV and the activities in brief are described in the table.
VOC: Voice of Customer ; VOB: Voice of Business; VOP: Voice of Process; CTQ : Critical to Quality
The steps DMA (expands as Define, Measure, Analyze) – are similar to DMAIC, (remember similar but not the same). The activities in DEFINE (Define the problem, Set up the goal) – is evidently the same as DMAIC . But in Measure and Analyze, there is a slight difference in what you measure and what and how you analyze. Finally, D & V stand for Design and Validate/Verify, respectively, clearly indicating that a Process Design is undertaken to meet Six Sigma levels of Performance. Hence, DMADV is alternatively also called as DFSS (Design for Six Sigma).
Now that we know what DMADV is, we may have the following questions in our mind:
1. When should we use DMADV?
2. What is the difference between DMAIC and DMADV?
3. Does DMADV use the same tools like DMAIC?
When is DMADV used?
DMAIC is used, when the problem you want to solve is for a process that is already existing but not meeting the expected levels of performance. DMAIC is used when you want to correct an existing process that has not been performing up to the expectations.
Alternatively, DMADV is used when you want to set up/design a whole new process, that should be meeting the desired level of performance from the beginning. DMADV may also be used when there is a need to redesign an existing product or process, rather than constantly correcting the process. The soul of DMADV is in understanding the customer’s requirements and the CTQs which are mostly expressed qualitatively.
For example, a Telecom service provider who wants to introduce a new Customer service improvement team may use DMADV to design:
1. What are all the areas the Customer service improvement team will cover?
2. What would be the TAT (Turn-around time) that the team can fix up to respond to its customers?
3. What would be the working hours (window) required to maintain the TAT?
4. What skills are required by the team members processing the complaints?
5. How many staff is required to be present in each interval/day/time/shift?
The same service provider may take up DMAIC approach, when the already existing customer service team’s TAT Target fixed is 3 hours but majority of the complaints are resolved in 6-7 hours. The solution to the DMAIC project taken could be a change in one or more of the five points discussed above.
What is the difference between DMAIC & DMADV?
DMADV and DMAIC are two tools adopted for same mission/vision: Achieve Six Sigma Performance; Two different approaches and methodology used to attain a single goal under different circumstances and problem areas.
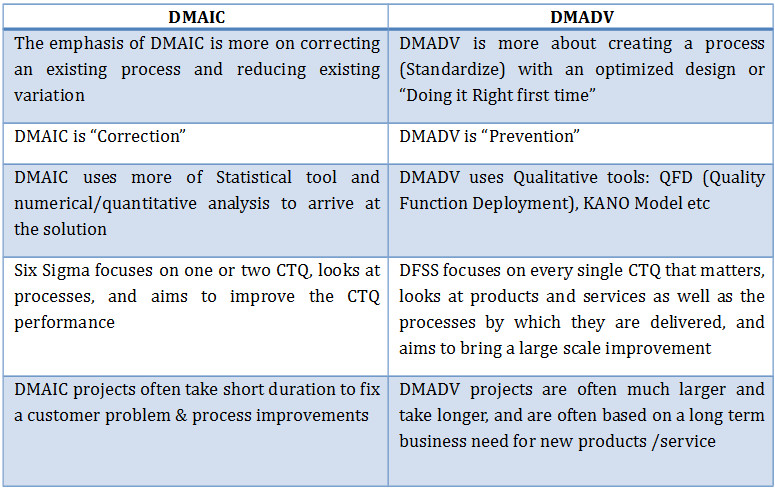
Table 2: DMAIC Vs DMADV
But the objective of both DMADV and DMAIC is the same: a) Variation reduction and b) Adherence to customer’s requirements.
Below is a table that provides an overview of the tools that are used in each phase of DMAV. (This table is just an indication/example and not an exhaustive list)
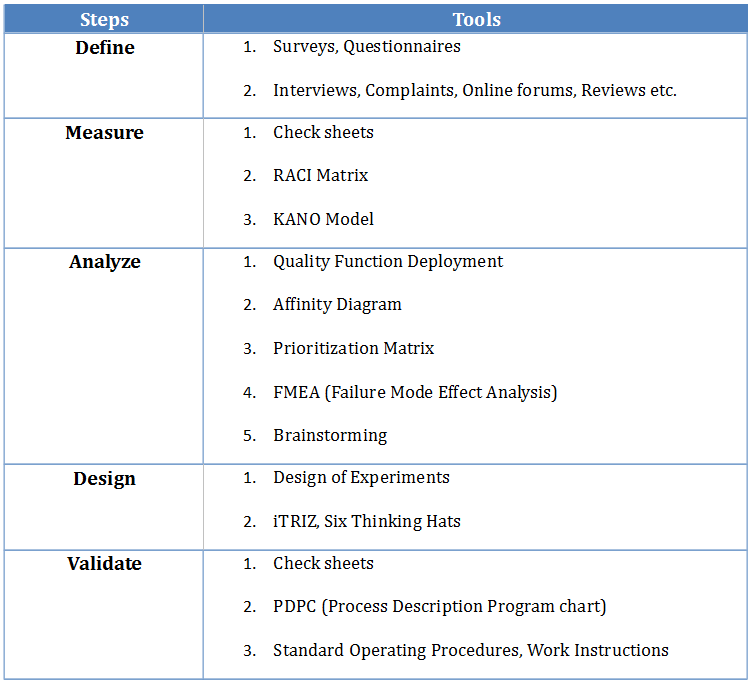
Table 3: DMADV – List of some Tools
There is no hard and fast rule that DMAIC should only use statistical tools and DMADV should only use Qualitative tools. It is based on the need and scenario that we choose the right tool to apply. (Example: Design of Experiments is a statistical tool to identify the significant variables from a list of ‘n’ variables; DOE is used both in DMAIC and DMADV)
Another important point to be remembered when using the DMADV approach is the effect of failure of design on the entire process. In DMAIC, when one of the solutions adopted does not prove to improve the result, there is always an alternative of returning to the AS-IS process; But in DMADV, since the process is quite new, there will not be any alternatives and the entire design should be revised and the failure might impact the cost and delay the project/forthcoming processes. Therefore care should be taken in designing the new process to the required accuracy.
Let us look at each step in detail with a case study in the forthcoming sections.
Previous post: Six Sigma Green Belt Certification
Next post: Six Sigma DMADV – Define Phase
- 10 Things You Should Know About Six Sigma
- Famous Six Sigma People
- Six Sigma Software
Recent Posts
- Control System Expansion
- Energy Audit Management
- Industrial Project Management
- Network Diagram
- Supply Chain and Logistics
- Visual Management
- Utilizing Pareto Charts in Business Analysis
- Privacy Policy
DMAIC vs. DMADV: Key Differences and Choosing the Right Six Sigma Methodology
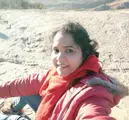
- 70 Comments
- Published on Nov 10 2023
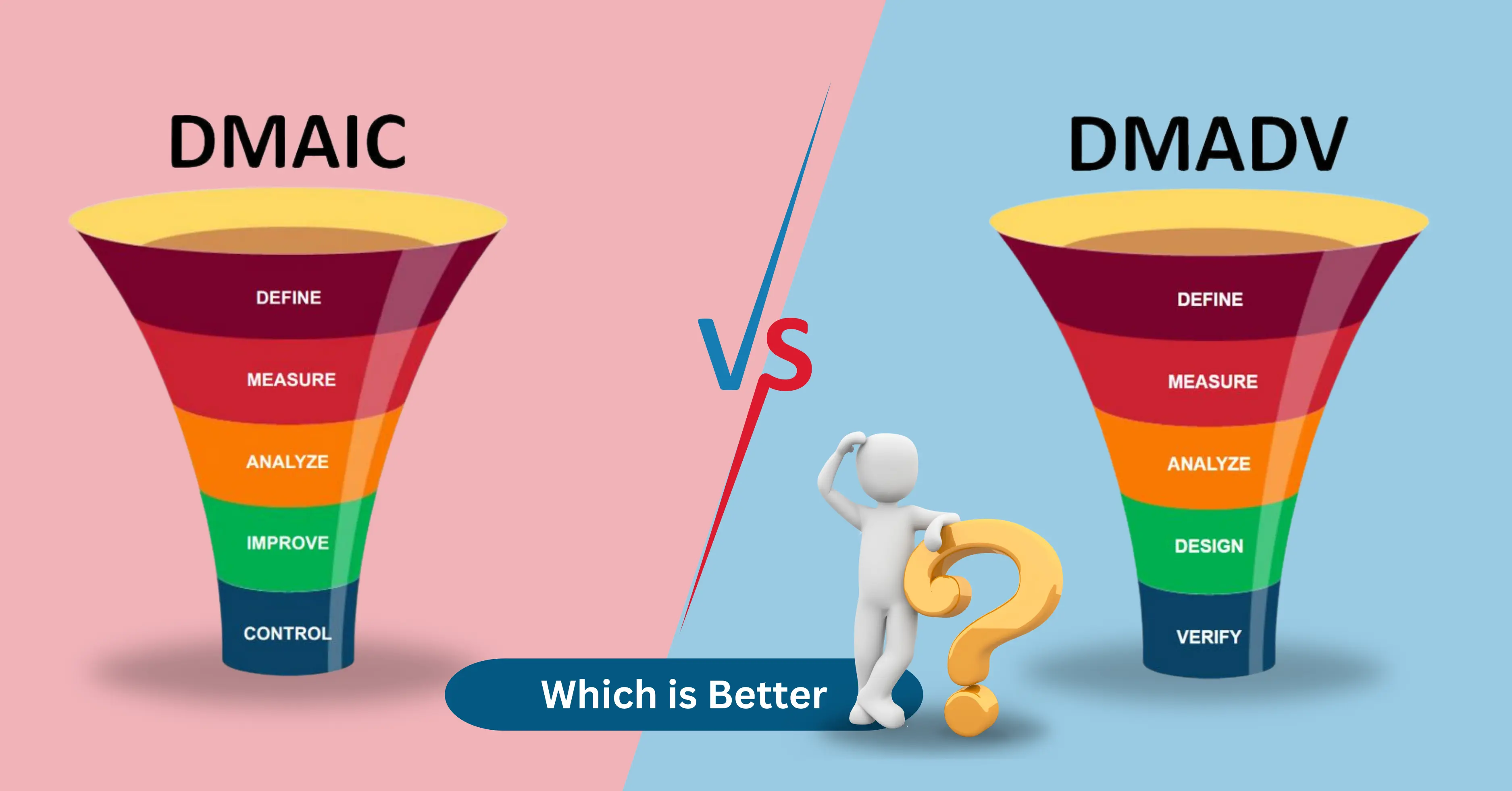
Table of Contents
Six sigma methodology, understanding dmaic, understanding dmadv, dmaic vs dmadv - what are the differences, pros and cons of each methodology, tools used by dmaic and dmadv, learn with sprintzeal.
In the world of improving how things work, there's a powerful tool called Six Sigma . It's like a super-skill for making processes better. Imagine it as your secret weapon for improving quality and efficiency in different tasks.
But here's the catch: Six Sigma has two main methods, like two sides of the same coin. These methods are called DMAIC and DMADV . Both DMAIC and DMADV share similarities, yet they also have distinct characteristics. The crucial question is determining when to employ each methodology. This is the aspect we will delve into in this blog.
Before we delve into contrasting DMAIC and DMADV, it's essential to understand the significance of Six Sigma.
Imagine you have a toolbox for making things work better, faster, and with fewer mistakes. In this world of striving for excellence, think of Six Sigma as your guide. It helps you discover and resolve issues, pointing you in the right direction. Now, consider DMAIC and DMADV as two distinct tools in that toolbox.
Both are useful, but it's essential to know when to apply each one. DMAIC is like a trusty wrench, perfect for fixing things that are a bit broken. On the other hand, DMADV is like a shiny new hammer, great for building something completely new and awesome.
In this blog post, we'll explain when to use DMAIC (the wrench) and when to go for DMADV (the hammer) to handle your projects effectively. Let's begin!
In the realm of Six Sigma, DMAIC is a potent method employed for enhancements. But what does it entail, and how does it function? Let's explore further.
DMAIC stands for five important steps: Define, Measure, Analyze, Improve, and Control. It's a roadmap that guides us to improve a process.
The first step, "Define," sets the stage. In this phase, we clearly describe the problem or goal. Think of it as the "what" and "why" part of the process. Now, let's look at the key components of DMAIC:
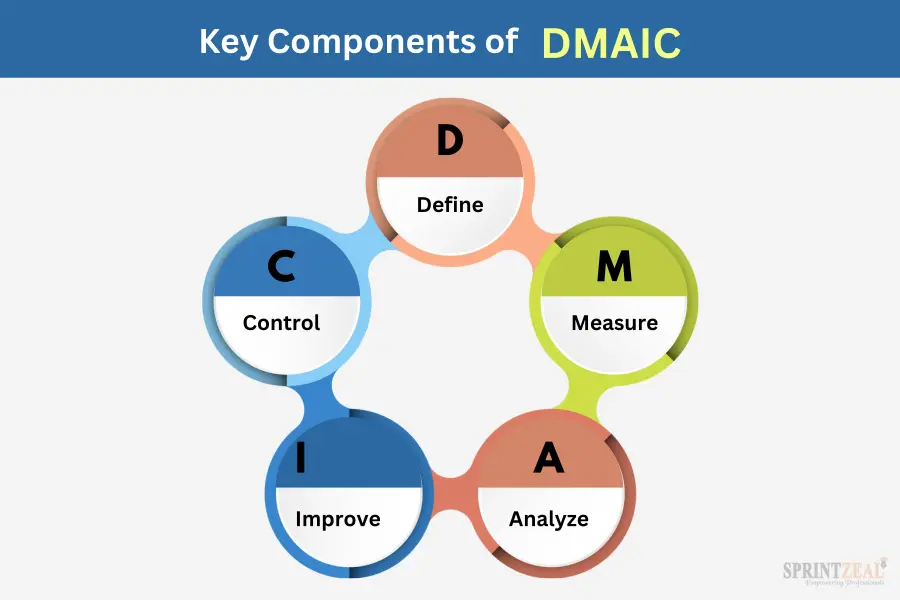
- Define: In this phase, you figure out what needs fixing or improving. You set specific goals and identify the people involved.
- Measure: Once you know what to improve, it's time to measure how things are currently working. This involves collecting data and understanding the process's current state.
- Analyze : After collecting data, you analyze it. This helps you find the root causes of any problems. It's like detective work for processes.
- Improve: With a good understanding of what's wrong, you can start making changes. This phase is all about finding solutions and putting them into action.
- Control: The last step ensures that the improvements stick around. You put measures in place to keep things on the right track.
When to Use DMAIC
Picture yourself working at a bakery, and you've observed that the cookies frequently turn out somewhat varied in size, color, and flavor. This lack of consistency is an issue, and you aim to resolve it. DMAIC can help.
You would define the issue (inconsistent cookies), measure how different they are, analyze the causes (like variations in the oven temperature), implement changes in your baking process, and control the new process to make sure the cookies come out consistently delicious. In this section, we'll explore the DMADV methodology within the Six Sigma framework. We'll break it down step by step and discuss what DMADV is all about.
DMADV stands for Define, Measure, Analyze, Design, and Verify. It's a structured approach used in Six Sigma for creating brand-new processes, products, or services. Unlike DMAIC, which focuses on improving existing processes, DMADV is all about starting from scratch to build something new and better.
Key components of DMADV:
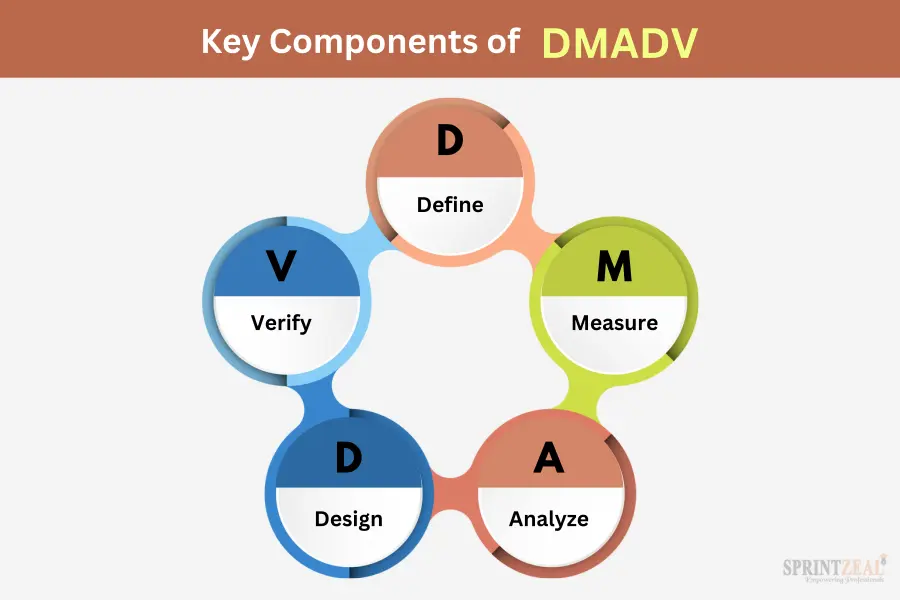
- Define : To begin, you should start by making a clear plan for what you want to make. This involves setting clear goals, knowing what your customers want, and recognizing any limits that could impact your project.
- Measure : After defining your project, you'll gather data to measure the current state. This helps you understand where you're starting from and what needs to be improved.
- Analyze : In the Analyze phase, you dig deeper into the data you've collected. You look for patterns, trends, and possible issues that might come up during the design phase. This step ensures you're well-prepared to tackle any challenges.
- Design : The heart of DMADV is the Design phase. This is where you create your new process, product, or service. It involves brainstorming, planning, and making decisions about how things will work in the future.
- Verify: Once your new design is ready, you need to make sure it meets the needs of your customers and works as intended. The Verify phase is like a final check to ensure your creation is up to the mark.
When to use DMADV
DMADV is ideal for projects where you need to invent something entirely new. Here are some examples:
New Product Development: If your company is designing a brand-new product that hasn't existed before, DMADV is the way to go. This could be anything from a new smartphone to a revolutionary medical device.
Process Innovation: When you're trying to create a more efficient process or a new way of doing things, DMADV can help. For instance, a car manufacturer might use DMADV to develop a more eco-friendly assembly line.
Service Improvement: Even in the service industry, DMADV can be applied. Let's say a hotel wants to completely overhaul its check-in process to make it faster and more customer-friendly. DMADV is the go-to choice.
In this section, we will explore the significant differences between the DMAIC and DMADV methodologies within the Six Sigma framework. Understanding DMAIC vs DMADV is crucial for making the right choice when improving your processes.
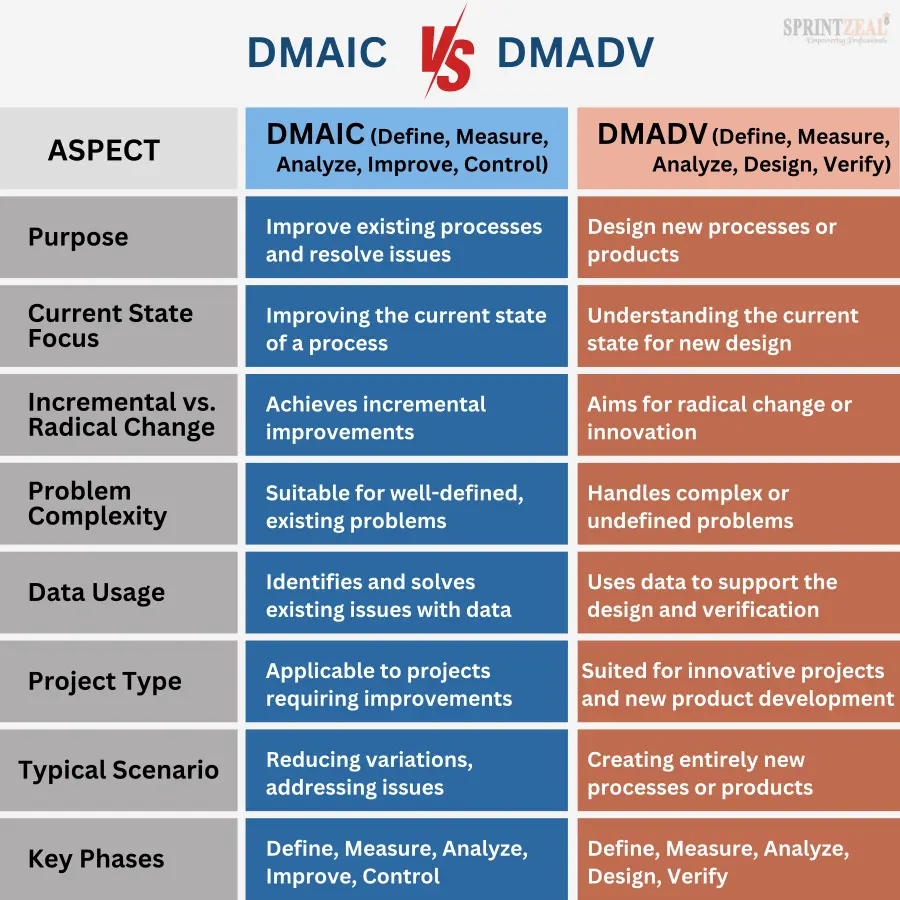
- Phases and Objectives
DMAIC: The DMAIC methodology, which stands for Define, Measure, Analyze, Improve, and Control, is primarily used for process improvement. Its main objective is to identify and address existing issues within a process. The phases in DMAIC are designed to help you understand, analyze, and improve the current state of a process, ultimately leading to better control and consistency.
DMADV: On the other hand, DMADV, short for Define, Measure, Analyze, Design, and Verify, is focused on creating something new or redesigning existing processes. Its primary objective is innovation and the development of entirely new processes or products. In DMADV, you start with the existing state but focus on designing a future state that is better, more efficient, and aligned with customer requirements.
- Project Types and Scenarios
DMAIC: DMAIC is the go-to methodology when you're dealing with well-defined problems or when the issues in a process are clear and measurable. It's best suited for situations where incremental improvements are sufficient to meet your project objectives. DMAIC works wonders in scenarios where you want to reduce variations in the process, making it more consistent and reliable.
DMADV: DMADV comes into play when you're dealing with complex or undefined problems. This is the top choice when you aim to be imaginative, create something entirely fresh, or bring substantial alterations to existing procedures or items. DMADV is your preferred method for projects that require imaginative solutions and thinking outside the box to fulfill customer needs.
- Approach to Data
DMAIC: In DMAIC, we use data to understand what's happening with our current process. It's similar to how we use a magnifying glass to investigate problems. We examine data to identify issues and come up with solutions.
DMADV : However, uses data in a distinct manner. It aids in crafting something fresh and intriguing. Think of it as using a compass to chart a new course. DMADV utilizes data to craft a roadmap for the future, making sure that the upcoming process or product aligns with what the customer wants.
- Focus on Innovation
DMAIC: This method is like a doctor who diagnoses and treats an illness. It's about finding and curing existing problems. DMAIC doesn't focus on creating new solutions or innovations; its goal is to restore health to the existing process.
DMADV: DMADV is like an artist who starts with a blank canvas and paints a masterpiece. It's all about innovation and creativity. When you use DMADV, you're aiming to design something entirely new and exciting. This could be a new product, service, or process that no one has seen before.
- Complexity of the Problem
DMAIC: If the problem you're facing is like a puzzle with missing pieces, DMAIC is your friend. It's great for dealing with issues that are well-defined and not too complex.
DMADV: If you're facing a complex problem that's as tricky as a maze, full of twists, turns, and many uncertainties, DMADV can be your guide. It's perfect for intricate problems where you must create a clear route from the beginning to the end.
- Resource Requirements
DMAIC: This method is generally less resource-intensive. Think of it as employing the tools you already possess in your toolkit to repair something. You might not require many extra resources or advanced gear.
DMADV: DMADV can be more resource-heavy. When you're making something brand-new, it can require extra time, funds, and specialized tools to turn your creative ideas into reality.
By grasping these extra distinctions, you'll be better prepared to pick the suitable method for the task, whether it's enhancing procedures or crafting innovative products.
In essence, DMAIC and DMADV are like two powerful tools in your process improvement toolbox. You can use them individually based on your project's needs, or you can use them sequentially to first fix what's broken and then innovate for the future.
Understanding DMAIC vs DMADV is crucial in making informed decisions when choosing the right Six Sigma methodology for your specific project.
- Well-suited for addressing known problems.
- Provides a structured approach to problem-solving.
- Enhances process stability and reduces variations.
- Easily integrated into existing processes.
- May not be suitable for complex, innovative projects.
- Less effective for creating entirely new processes or products.
- Ideal for innovative projects and new product development.
- Emphasizes customer requirements and innovation.
- Suitable for tackling complex, undefined issues.
- Allows for creative, out-of-the-box thinking.
- Time-consuming, as it involves designing new solutions.
- May require more resources and investment.
In the world of Six Sigma methodologies, both DMAIC and DMADV have a powerful arsenal of tools at their disposal. These tools are essential for collecting data, analyzing processes, and making informed decisions. Let's explore the key tools used by each methodology.
Tools Used by DMAIC:
Process Maps: Process maps are visual representations of a process that help in identifying inefficiencies and areas for improvement. They provide a clear picture of how a process works.
Cause-and-Effect Diagram (Ishikawa or Fishbone Diagram): This tool helps identify the root causes of problems. It's a visual representation that breaks down a problem into its potential causes, categorized into branches.
Data Collection and Analysis: DMAIC heavily relies on data collection and analysis. Tools such as histograms, control charts, and Pareto charts help in quantifying variations and making data-driven decisions.
Root Cause Analysis: Techniques like the 5 Whys and Failure Mode and Effects Analysis (FMEA) are used to delve deep into problems and find their underlying causes.
Process Capability Analysis: Tools like Cp, Cpk, Pp, and Ppk are employed to assess the capability of a process to meet customer requirements.
Statistical Process Control (SPC): SPC tools, including control charts and run charts, are vital for monitoring and maintaining process stability.
Design of Experiments (DOE): DOE helps optimize processes by systematically testing multiple variables to determine their impact on the final outcome.
Tools Used by DMADV:
Quality Function Deployment (QFD): QFD is a tool used to translate customer requirements into specific product or process features. It ensures that the design aligns with customer needs.
Failure Modes and Effects Analysis (FMEA): While also used in DMAIC, FMEA plays a crucial role in DMADV to identify potential failure modes in a new design and prioritize them.
TRIZ (Theory of Inventive Problem Solving): TRIZ is a systematic approach for creative problem-solving and innovation. It encourages innovative thinking and inventive solutions.
Pugh Matrix: This tool is used to compare and evaluate multiple design concepts and select the most promising one.
Simulation: Simulation software allows for the virtual testing of a new process or product design. It helps in understanding how the design will perform in real-world conditions.
Design for Six Sigma (DFSS) Scorecards: DFSS scorecards provide a structured approach to evaluating the success of a new design in meeting customer requirements.
Axiomatic Design: Axiomatic design principles help in ensuring that the design aligns with customer needs and minimizes the complexity of the design.
It's important to note that both DMAIC and DMADV methodologies can use common tools, such as statistical software, process flowcharts, and brainstorming sessions. However, the emphasis and application of these tools differ based on the methodology's objectives.
Sprintzeal is your go-to destination for mastering Six Sigma methodologies, including DMAIC and DMADV. If you're looking to enhance your process improvement skills and gain valuable certifications, Sprintzeal offers comprehensive courses designed to fit your learning needs.
- Six Sigma Green Belt : Ideal for those looking to play a key role in process improvement and problem-solving within an organization.
- Six Sigma Black Belt : For those aiming to become experts in Six Sigma methodologies and lead complex projects.
- Lean Six Sigma Green Belt : Combines the principles of Lean and Six Sigma to optimize processes and reduce waste.
- Lean Six Sigma Black Belt : A comprehensive program that covers Lean and Six Sigma tools for process improvement and innovation.
If you're ready to take your process improvement skills to the next level and become a certified Six Sigma professional, look no further. Explore our courses, gain valuable insights, and make a significant impact on your projects and organization's success.
Visit Sprintzeal's website and take the first step towards becoming a Six Sigma expert. Join our courses, gain certifications, and unlock exciting opportunities for process improvement in your career!
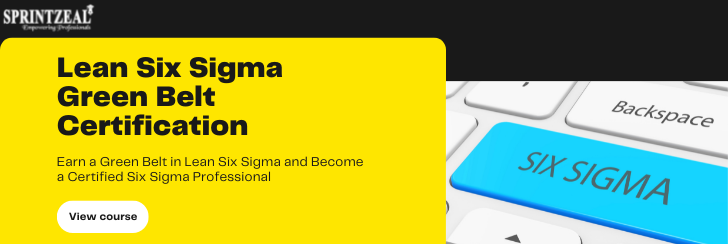
In conclusion, we've explored the world of Six Sigma methodologies, specifically focusing on DMAIC and DMADV. Understanding DMAIC vs DMADV play a vital role in process improvement, and choosing the right one for your project is a crucial decision.
The importance of selecting the right Six Sigma methodology cannot be overstated. Making the right choice can be the difference between success and stumbling. Take your project objectives, complexity, available resources, and the level of innovation required into careful consideration before deciding which methodology is the best fit.
If you're looking to further expand your knowledge in Six Sigma and its methodologies, we recommend exploring the courses offered by SprintZeal. They provide in-depth training and certification opportunities, equipping you with the skills and expertise needed for effective process improvement.
Don't hesitate to take the next step in your Six Sigma journey. Visit SprintZeal's website and discover the courses that can propel your career forward.
What is the difference in measure phase of DMAIC and DMADV?
The Measure phase in DMAIC focuses on collecting data to understand the current state of an existing process, while in DMADV, it is geared towards establishing a baseline for designing a new process or product.
What is DMADV methodology?
DMADV, which stands for Define, Measure, Analyze, Design, Verify, is a Six Sigma methodology primarily used for creating entirely new processes or products.
When should DMADV be used?
DMADV should be used when you're seeking to innovate, design new processes or products, and address complex, undefined issues.
What are the implications of DMAIC and DMADV?
The implications of DMAIC include improved process stability, waste reduction, and incremental enhancements, while DMADV leads to radical changes and innovations, potentially revolutionizing the way a process or product is designed or delivered.
Subscribe to our Newsletters
Explore program.

Apply for Free Consultation
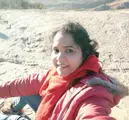
Niharika Chaurasia
Niharika is a technical content writer in the education niche with vast experience in creating content for certifications and training programs. She creates engaging, easy-to-understand, and valuable content for both beginners and professionals aspiring to enhance their careers.
Popular Programs

Six Sigma Yellow Belt
Live virtual training.
- 5 (3569 + Ratings)
- 46k + Learners
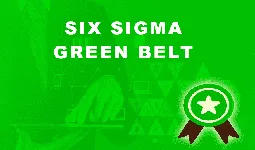
Six Sigma Green Belt
- 4.6 (1269 + Ratings)
- 35k + Learners
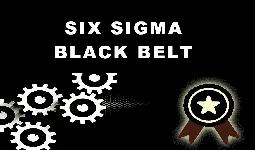
Six Sigma Black Belt
- 4 (412 + Ratings)
- 42k + Learners
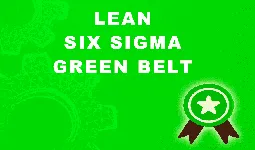
Lean Six Sigma Green Belt
- 5 (785 + Ratings)
- 70k + Learners
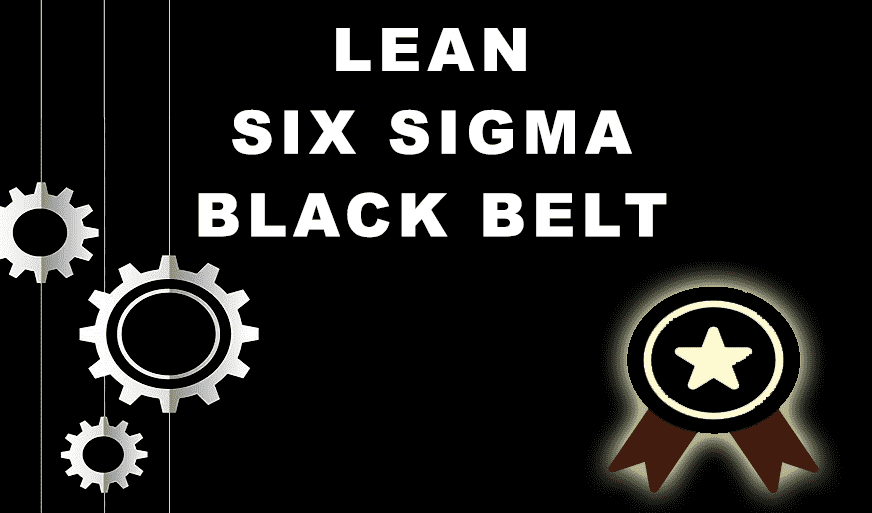
Lean Six Sigma Black Belt
- 4.2 (367 + Ratings)
Trending Now
Top Career benefits of Lean Six Sigma Green Belt
Lean methodology, Six Sigma methodology and Lean Six Sigma Explained
Six Sigma Black Belt Certification – Value and Career Benefits in 2024
Pareto Chart in Six Sigma - Explained
Six Sigma Certification Guide - A Professional's Guide
Six Sigma Yellow Belt Certification - Six Sigma for Beginners
Quality Control Explained – Six Sigma
Total Quality Management - A Complete Guide for Beginners
Quality Assurance in Six Sigma Explained
Quality Assurance vs Quality Control
Six Sigma Certification – Everything you Need to Know About Getting Certified
Lean Six Sigma on Resume for Rewarding Career Benefits
Quality Manager Interview Questions and Answers 2024(UPDATED)
Service Delivery Manager Interview Questions and Answers (With Examples)
Six Sigma Interview Questions and Answers 2024

How to become a Quality Analyst
A Supply Chain Management Guide to Mastering Logistics End to End
Senior Quality Manager Interview Questions and Answers 2024
Top 30 Quality Analyst Interview Questions and Answers 2024
Financial Analyst Interview Questions and Answers 2024
Risk Manager Interview Questions and Answers 2024
Compliance Manager Interview Questions and Answers 2024
Operation Manager Interview Questions and Answers
5 Lean Continuous Improvement Principles to Supercharge Your Operations
How to Become a Quality Manager - Career, Job Scope and Certifications
Six Sigma Certifications - Reasons Why you Should Get Them
Top Qualities of a Good Manager and a Leader
Learn about Statistical Process Control (SPC) and its top applications
Cost of Poor Quality - A Detailed Guide
Implementing 5S Methodology for Better Work Efficiency
What Is Lean Management?
Best Six Sigma Books in 2024
Leadership vs Management - The Ultimate Guide
Quality Assurance Plan - Six Steps To Quality Assurance Plan
Operational Planning Creation, Key Elements and its Benefits
A Complete Guide to Product Life Cycle Stages 2024
What Is Lean Manufacturing?- An Overview
The Lean Continuous Improvement Model: A Comprehensive Guide
A Deep Dive into the Power of Lean Continuous Improvement Process
Lean Continuous Improvement Methods for Business Excellence
Introduction to Lean Manufacturing- Definitions, Framework, and More
Understanding the Key Principles of Lean Manufacturing
Secret to Unlock Organizational Excellence: Stages of Continuous Improvement
Lean Continuous Improvement: A Detailed Guide to Mastering Organizational Quality
Lean Waste Management: The Ultimate Guide 2023
A Deep Dive into Lean Continuous Improvement Tools
8 Wastes of Lean - Strategies for Identification and Elimination
The Ultimate Guide to Lean Manufacturing
Understanding Lean Manufacturing's Pros and Cons
Lean Waste Reduction Strategies: Boost Efficiency and Cut Costs
Top 10 Lean Manufacturing Tools for Optimal Productivity
Beyond the Basics: Benefits of Lean Continuous Improvement
- Agile Management 59
- AI and Machine Learning 27
- Big Data 50
- Business Management 25
- Cloud Computing 37
- Digital Marketing 50
- IT Hardware and Networking 13
- IT Security 79
- IT Service Management 28
- Microsoft Program 2
- Programming Language 29
- Project Management 124
- Quality Management 53
Trending Posts
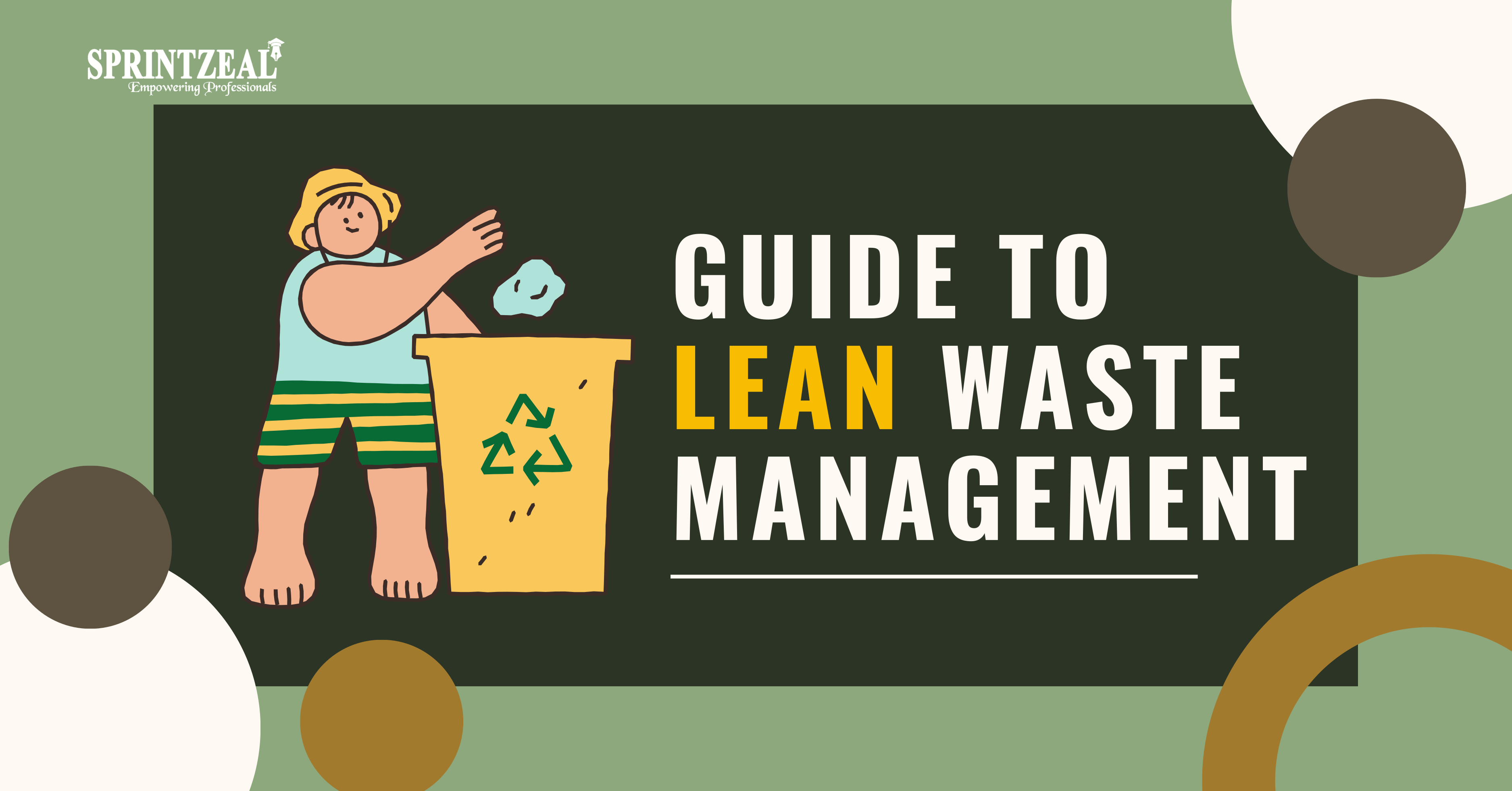
Last updated on Dec 13 2023
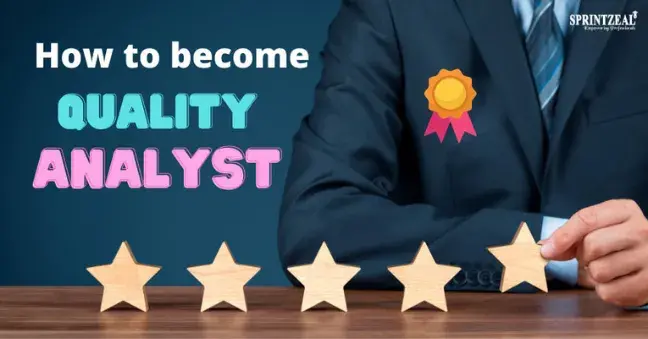
Last updated on Jan 11 2024
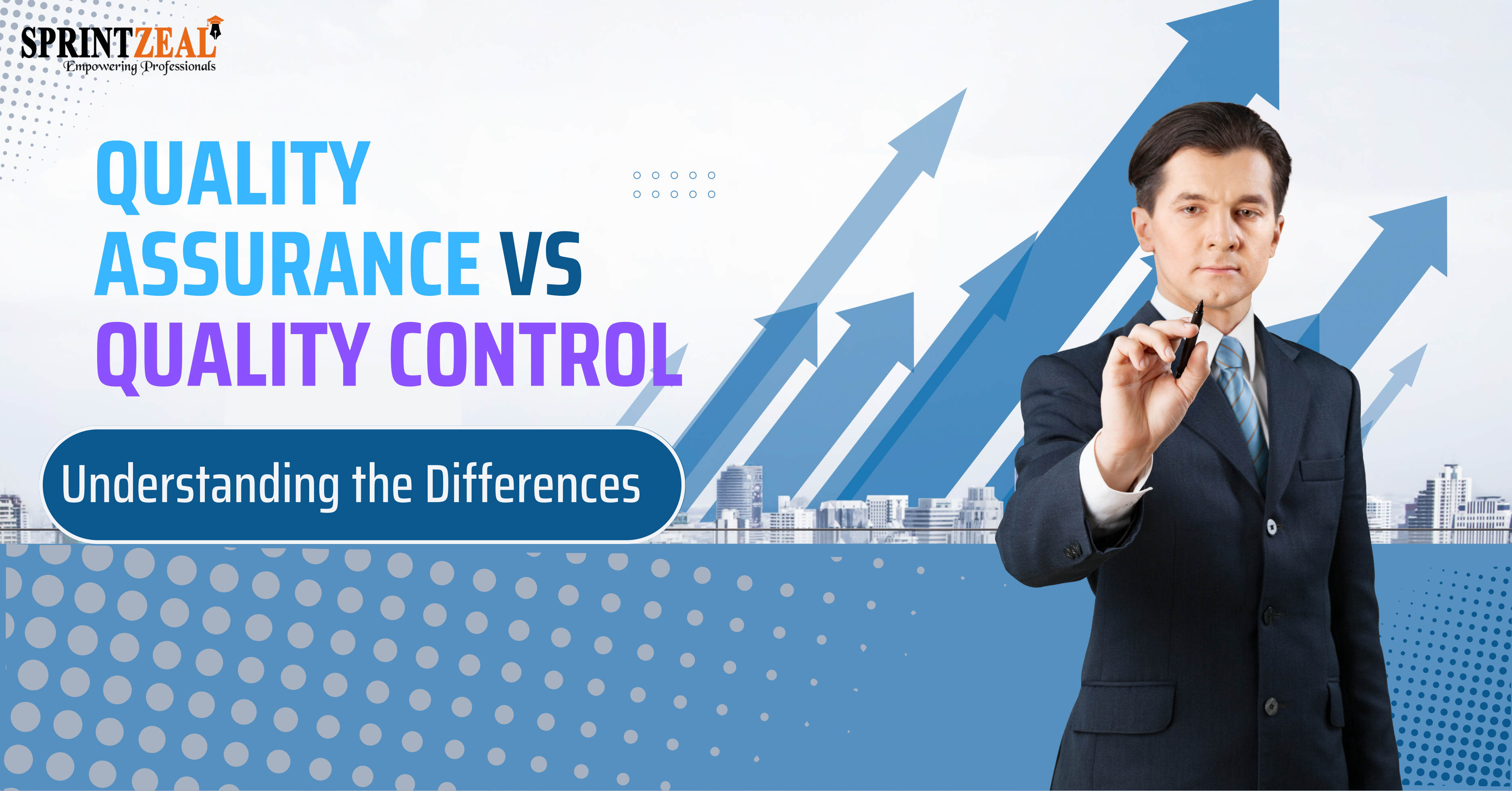
Last updated on Aug 2 2023
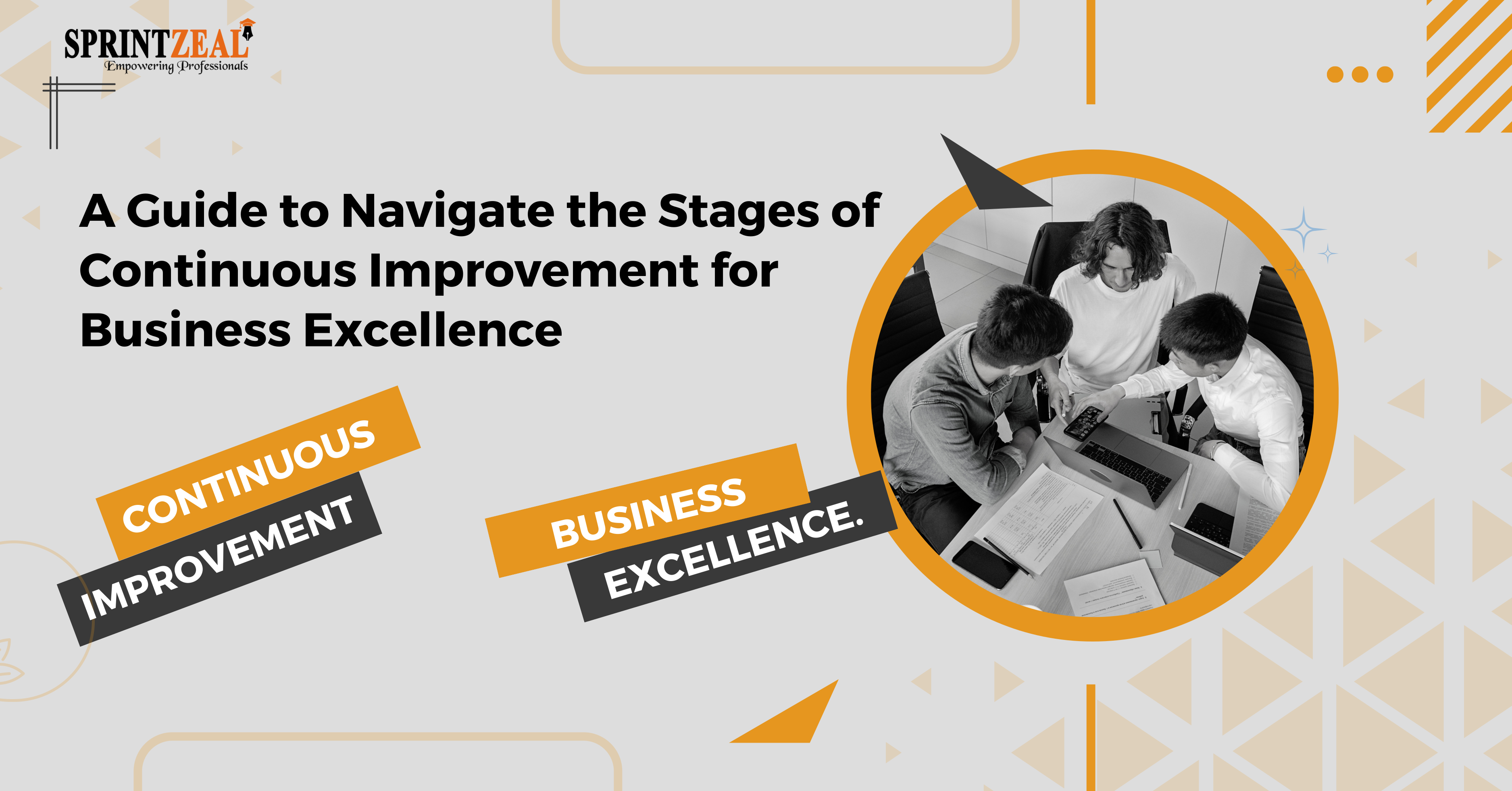
Last updated on Nov 27 2023
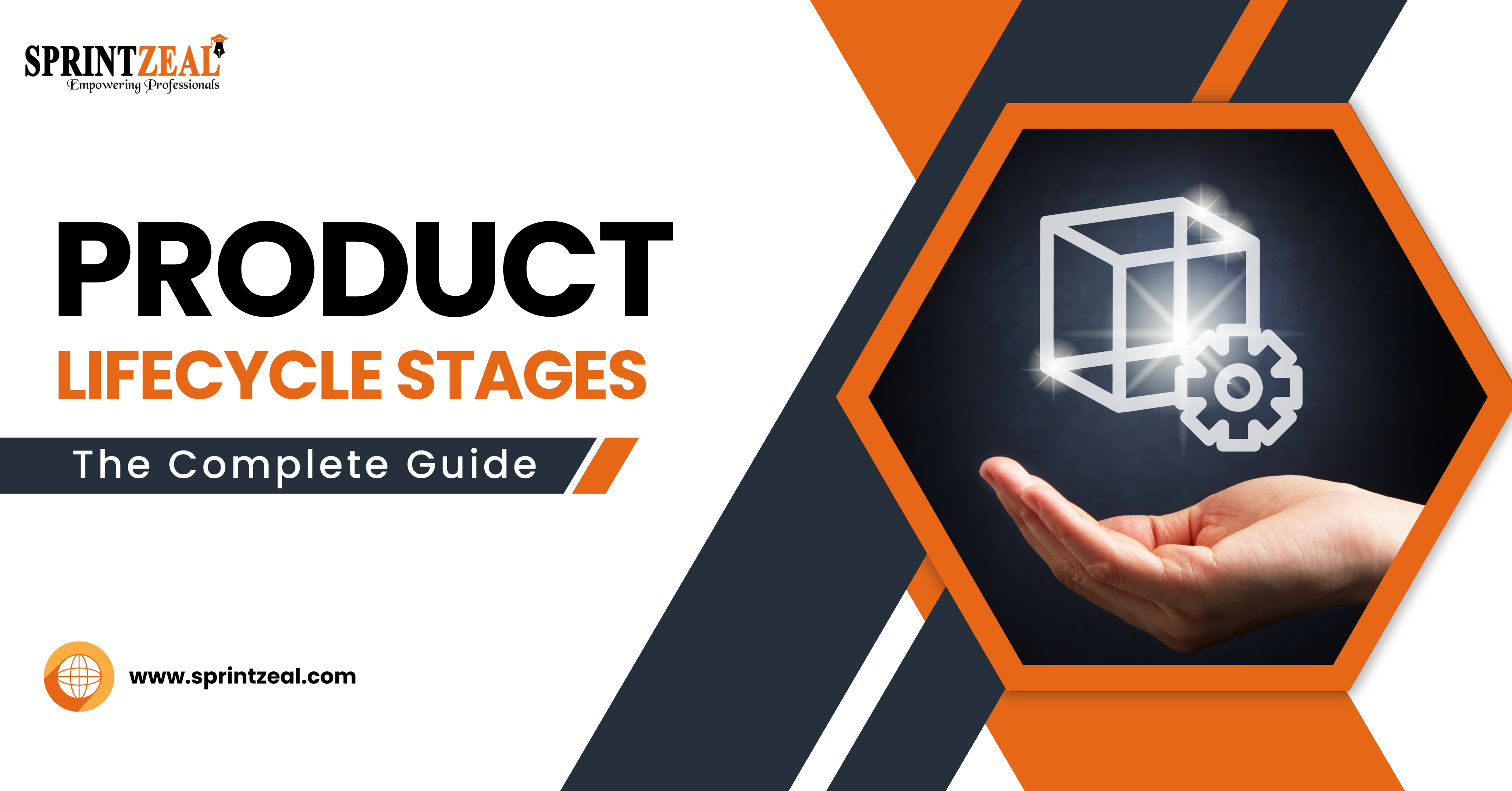
Last updated on Sep 19 2023
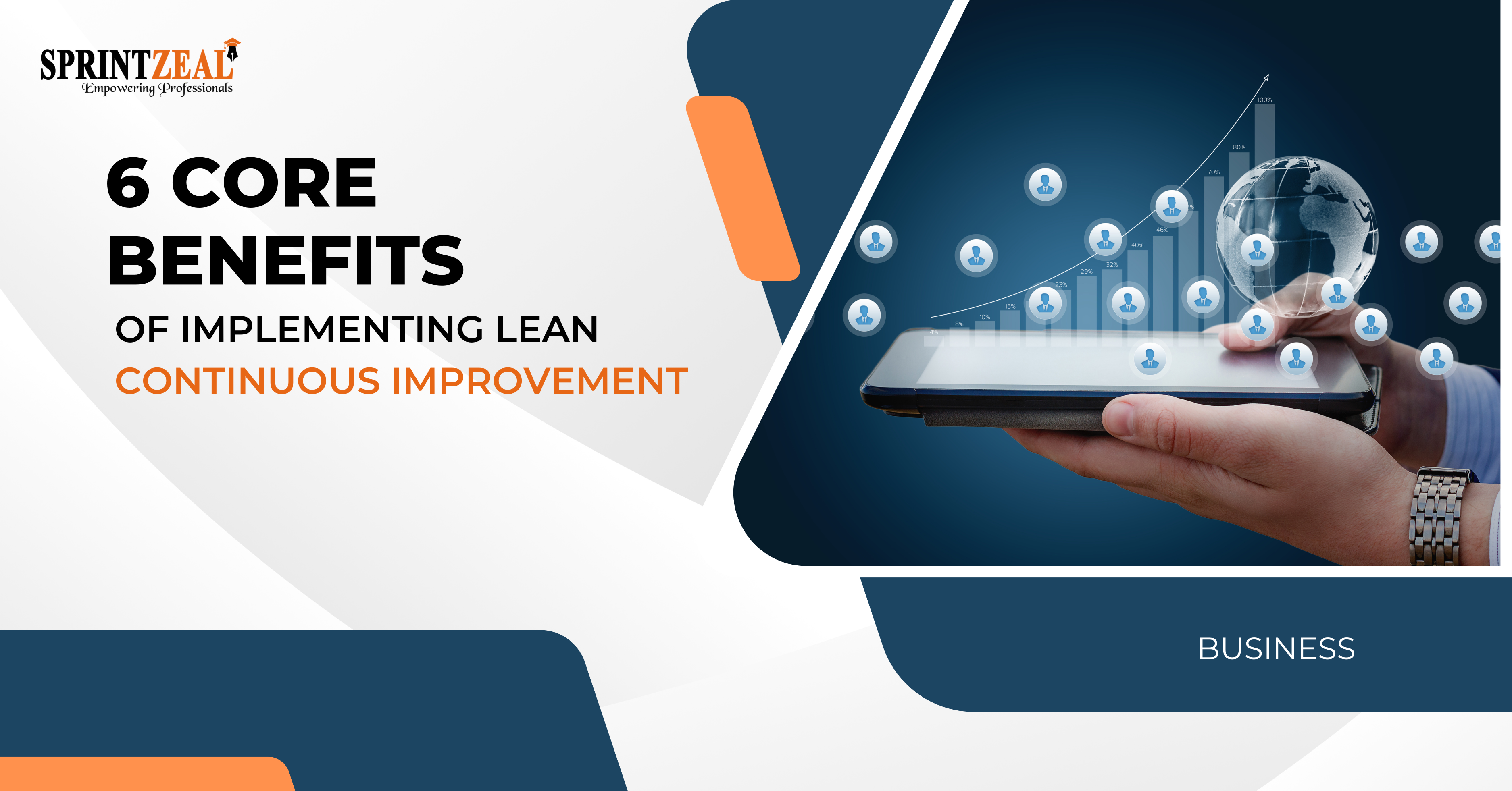
Last updated on Jan 16 2024

- Corporate Partners
- Affiliate Program
QUICK LINKS
- Terms & Conditions
- Privacy Policy
- Cookie Policy
- Become an Instructor
- Sprintzeal Reviews
SECURE PAYMENTS

Top Trending Courses
People also bought.
© 2024 Sprintzeal Americas Inc. - All Rights Reserved.
- PMP, PMI, PMBOK, CAPM, PgMP, PfMP, ACP, PBA, RMP and SP are registered marks of the Project Management Institute, Inc.
- CBAP® - Is a registered trade mark of IIBA.
- ITIL® is a registered trade mark of AXELOS Limited, used under permission of AXELOS Limited. The Swirl logoTM is a trademark of AXELOS Limited, used under permission of AXELOS Limited. All rights reserved
- PRINCE2® is a registered trade mark of AXELOS Limited, used under permission of AXELOS Limited. The Swirl logoTM is a trademark of AXELOS Limited, used under permission of AXELOS Limited. All rights reserved
- Certified ScrumMaster® (CSM) and Certified Scrum Trainer® (CST) are registered trademarks of SCRUM ALLIANCE®
- Professional Scrum Master is a registered trademark of Scrum.org
- The APMG-International Finance for Non-Financial Managers and Swirl Device logo is a trade mark of The APM Group Limited.
- The Open Group®, TOGAF® are trademarks of The Open Group.
- IIBA®, the IIBA® logo, BABOK® and Business Analysis Body of Knowledge® are registered trademarks owned by International Institute of Business Analysis.
- CBAP® is a registered certification mark owned by International Institute of Business Analysis. Certified Business Analysis Professional, EEP and the EEP logo are trademarks owned by International Institute of Business Analysis..
- COBIT® is a trademark of ISACA® registered in the United States and other countries.
- CISA® is a Registered Trade Mark of the Information Systems Audit and Control Association (ISACA) and the IT Governance Institute.
- CISSP® is a registered mark of The International Information Systems Security Certification Consortium ((ISC)2).
- CompTIA A+, CompTIA Network+, CompTIA Security+ are registered marks of CompTIA Inc
- CISCO®, CCNA®, and CCNP® are trademarks of Cisco and registered trademarks in the United States and certain other countries.
- CSM®, CSPO®, CSD®, CSP®, A-CSPO®, A-CSM® are registered trademarks of Scrum Alliance®
- TOGAF® is a registered trademark of The Open Group in the United States and other countries
- All the online courses are accredited by respective governing bodies and belong to their respective owners.
- Call us on +1 833 636 6366
- Request a callback
- Mail Your Queries
Enquire Now for Up to 30% Off!
WHO WILL BE FUNDING THE COURSE?
The Easy Guide to Solving Problems with Six Sigma DMAIC Method

The most commonly used methodology in Six Sigma is the DMAIC process. Many use it to solve problems and identify and fix errors in business and manufacturing processes.
In this post, we will look at how to use the DMAIC process to solve problems. You will also find useful and editable templates that you can use right away when implementing DMAIC problem-solving in your organization.
- What are 5 the Steps of Six Sigma
DMAIC Process and Problem-Solving
Common mistakes to avoid when using six sigma dmaic methodology, how to use the dmaic methodology for problem solving in project management, what are the 5 steps of six sigma.
DMAIC is one of the core methodologies used within the Six Sigma framework. It is a data-driven method used to systematically improve the process. The approach aims to increase the quality of a product or service by focusing on optimizing the process that produces the output. This way DMAIC seeks to provide permanent solutions when it comes to process improvement.
It provides a structured problem-solving framework to identify, analyze, and improve existing processes. DMAIC guides practitioners through a series of steps to identify the root causes of process issues, implement solutions, and sustain the improvements over time.
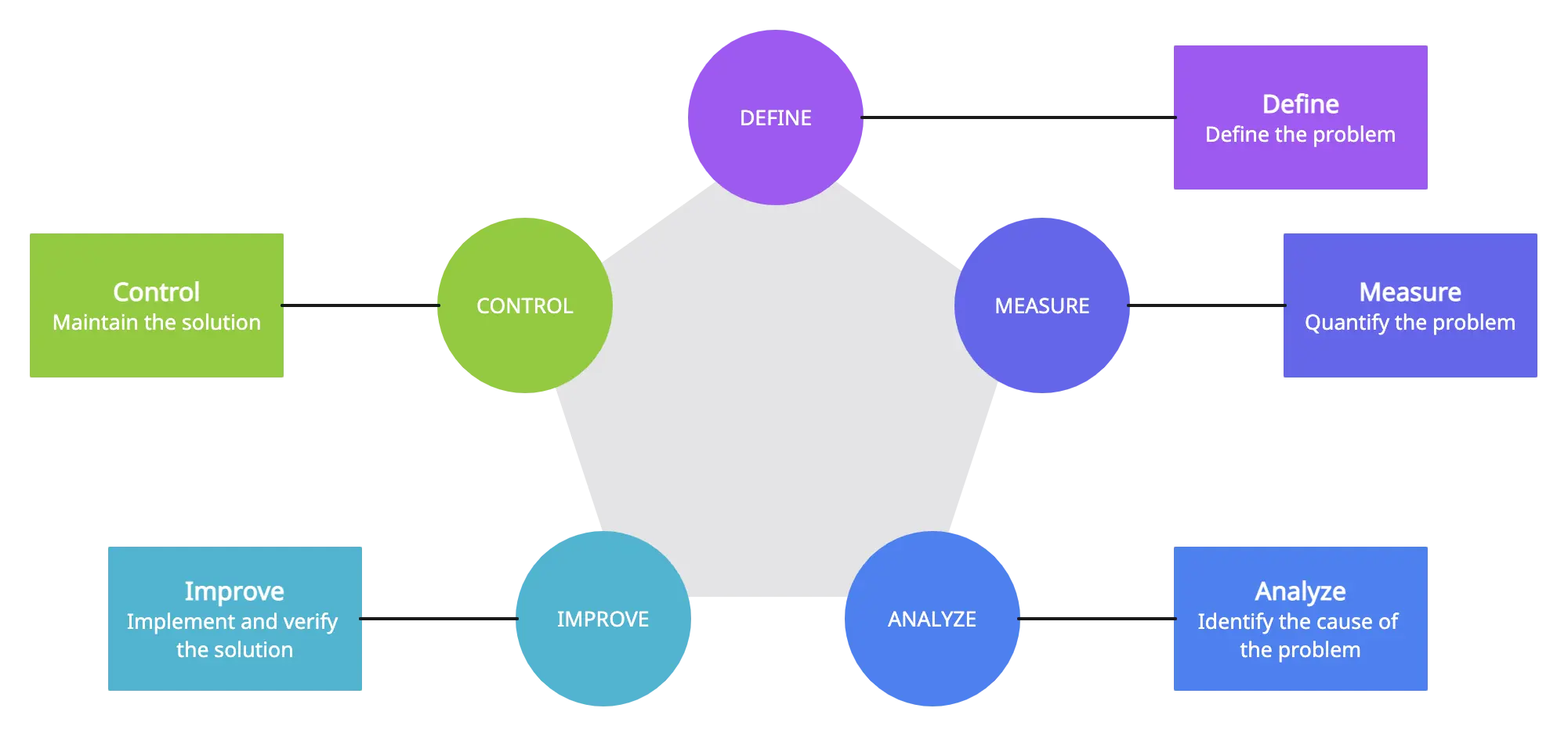
Following we have listed down the 5 phases of the DMAIC process along with the steps you need to take when using it to solve problems. Different tools for each phase is provided with editable templates.
Step 1: Define the Problem
So there’s a problem that affects your customer or your company processes. In this first step of the DMAIC problem solving method , you need to focus on what the problem is and how it has affected you as a company.
There are a few steps you need to follow in this phase.
• Create a problem statement which should include a definition of the problem in quantifiable terms and the severity of the problem.
• Make sure necessary resources such as a team leader and competent team members, and funds etc. are available at hand.
• Develop a goal statement based on your problem statement. It should be a measurable and time-bound target to achieve.
• Create a SIPOC diagram which will provide the team with a high-level overview of the process (along with its inputs, outputs, suppliers, and customers) that is being analyzed. You can also use a value stream map to do the same job.
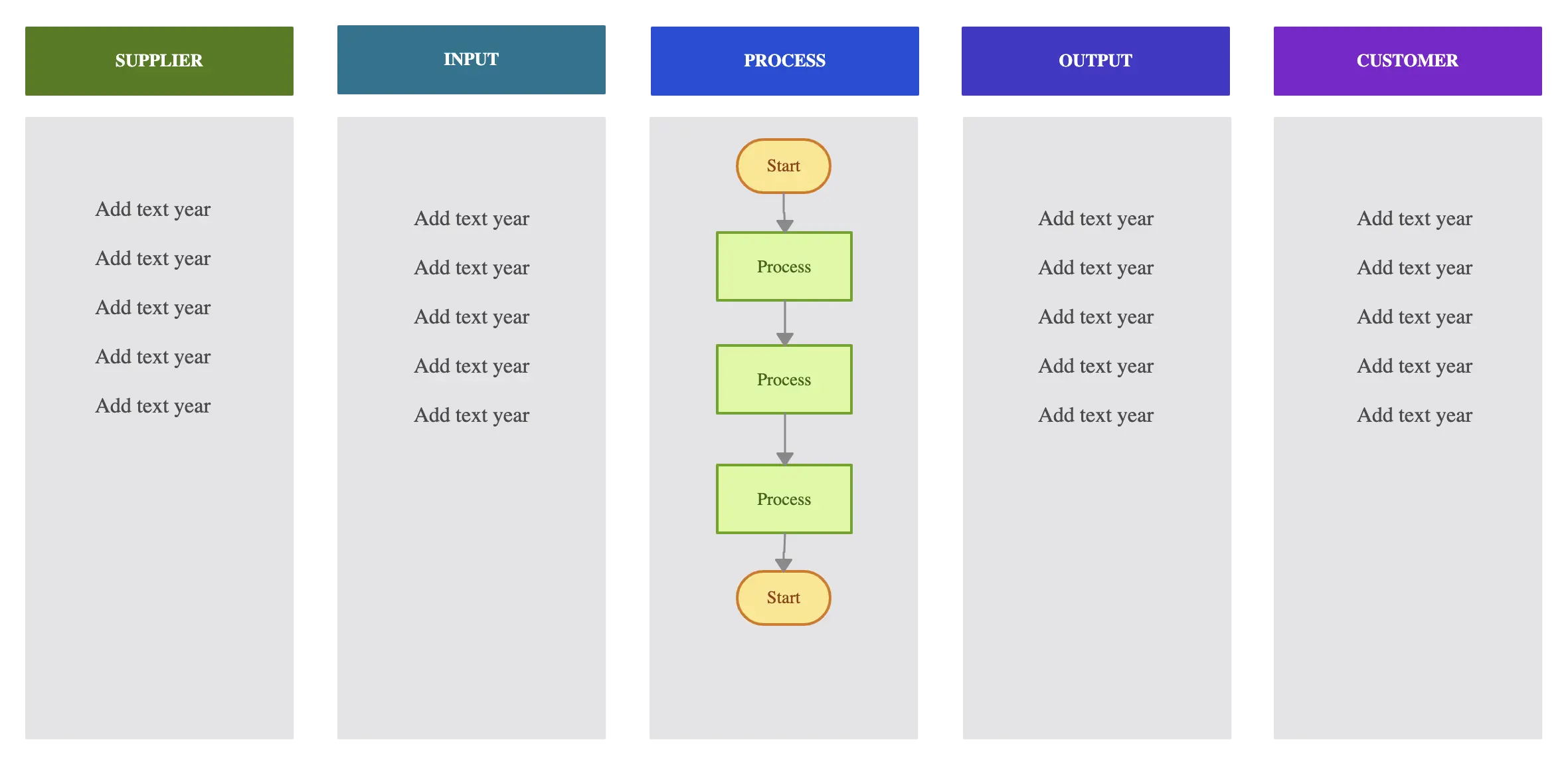
• Try to understand the process in more in-depth detail by creating a process map that outlines all process steps. Involve the process owners when identifying the process steps and developing the map. You can add swimlanes to represent different departments and actors responsible.
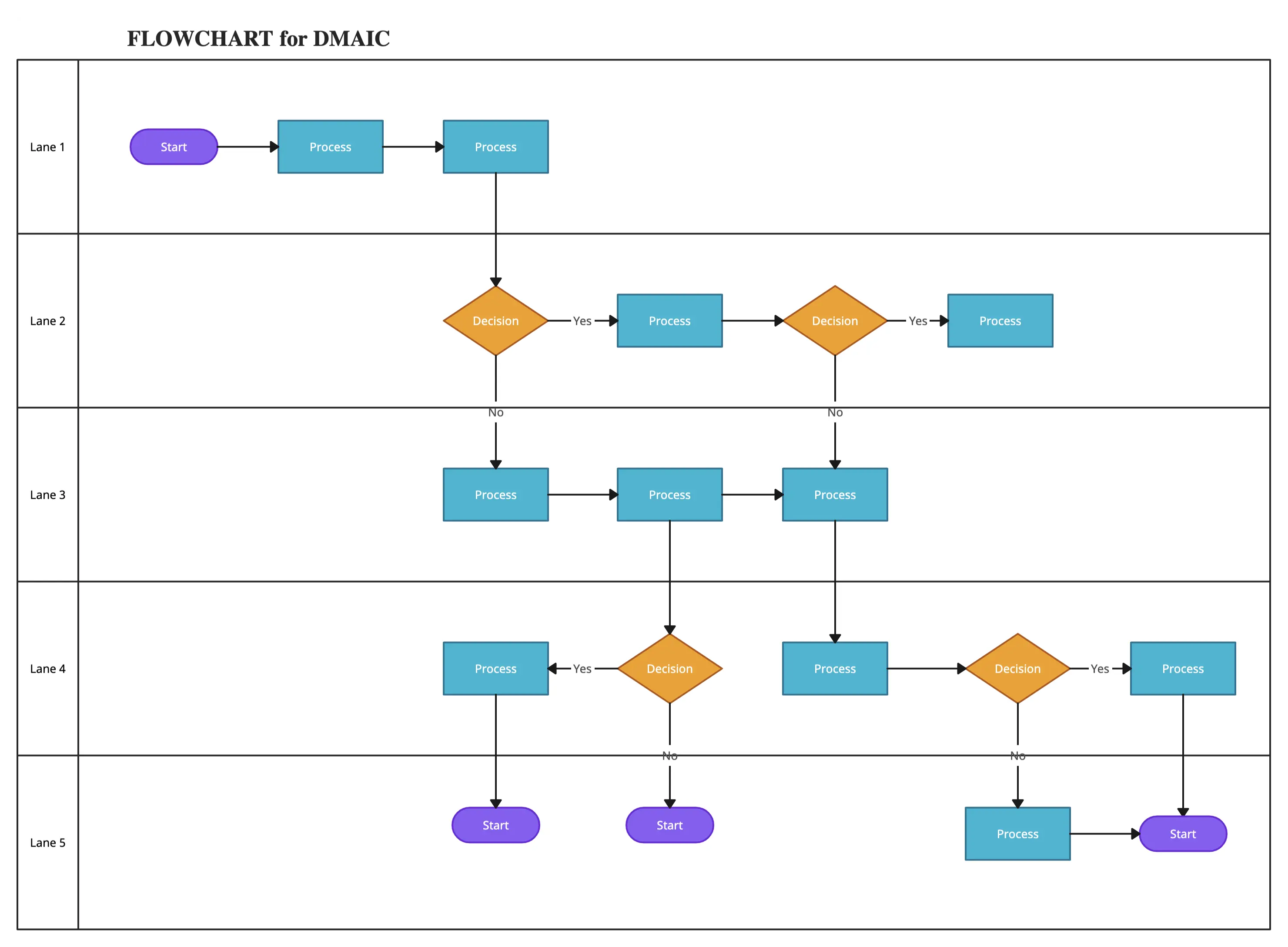
Step 2: Measure the Problem
In this step, you should measure the extent of the problem. To do so you need to examine the process in its current state to see how it performs. The detailed process map you created in the ‘Define’ phase can help you with this.
The baseline measurements you will need to look into in this phase, are process duration, the number of defects, costs and other relevant metrics.
These baseline measurements will be used as the standards against which the team will measure their success in the ‘Improve’ phase.
Step 3: Analyze the Problem
The analyze phase of the DMAIC process is about identifying the root cause that is causing the problem.
• Referring to the process maps and value stream maps you have created, further, analyze the process to identify the problem areas.
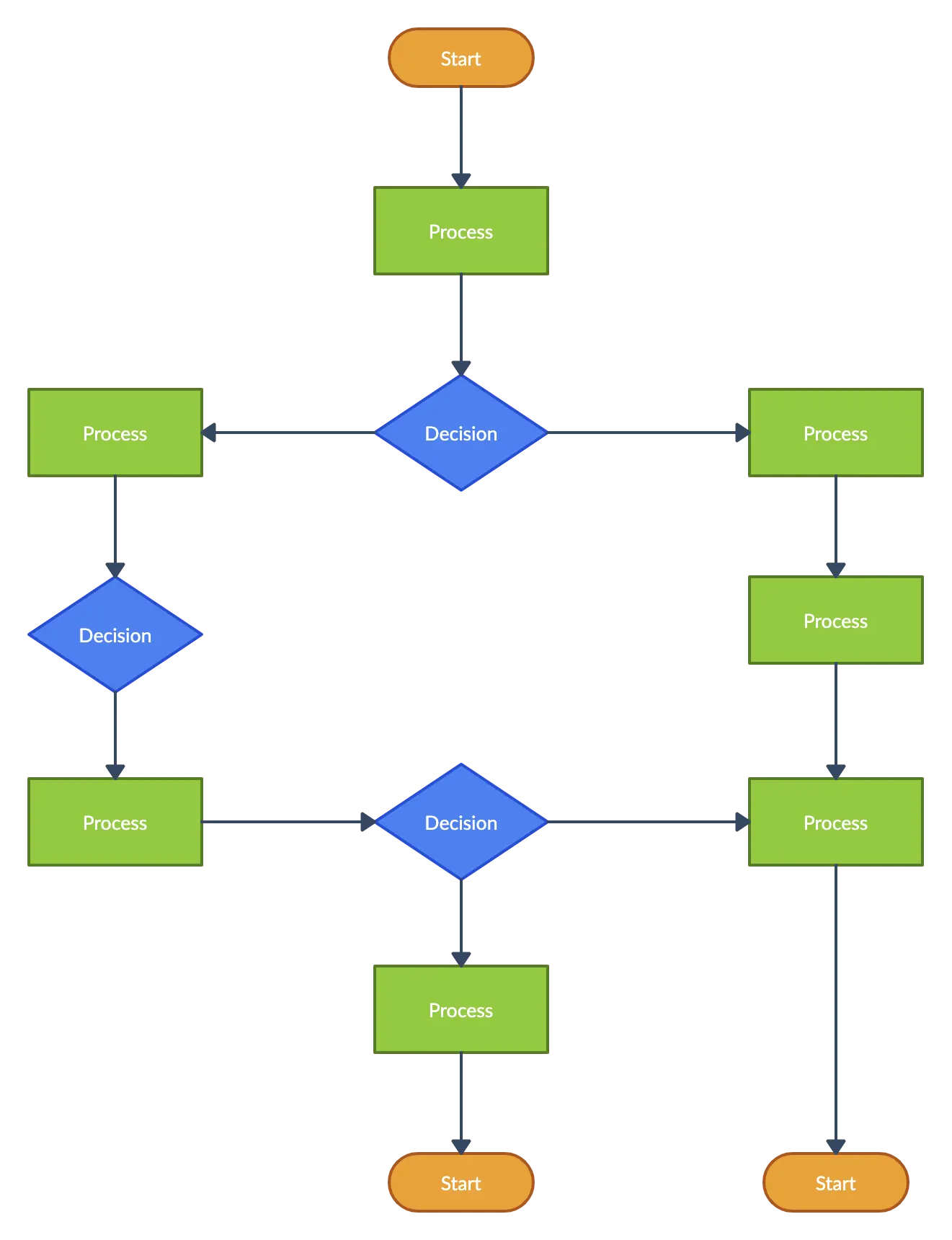
• Visualize the data you have collected (both in the ‘Measure’ phase and the analyze phase) to identify signs of problems in the processes.
• Use Pareto charts, histograms, run charts etc. to represent numerical data. Study them with team leaders and process owners to identify patterns.
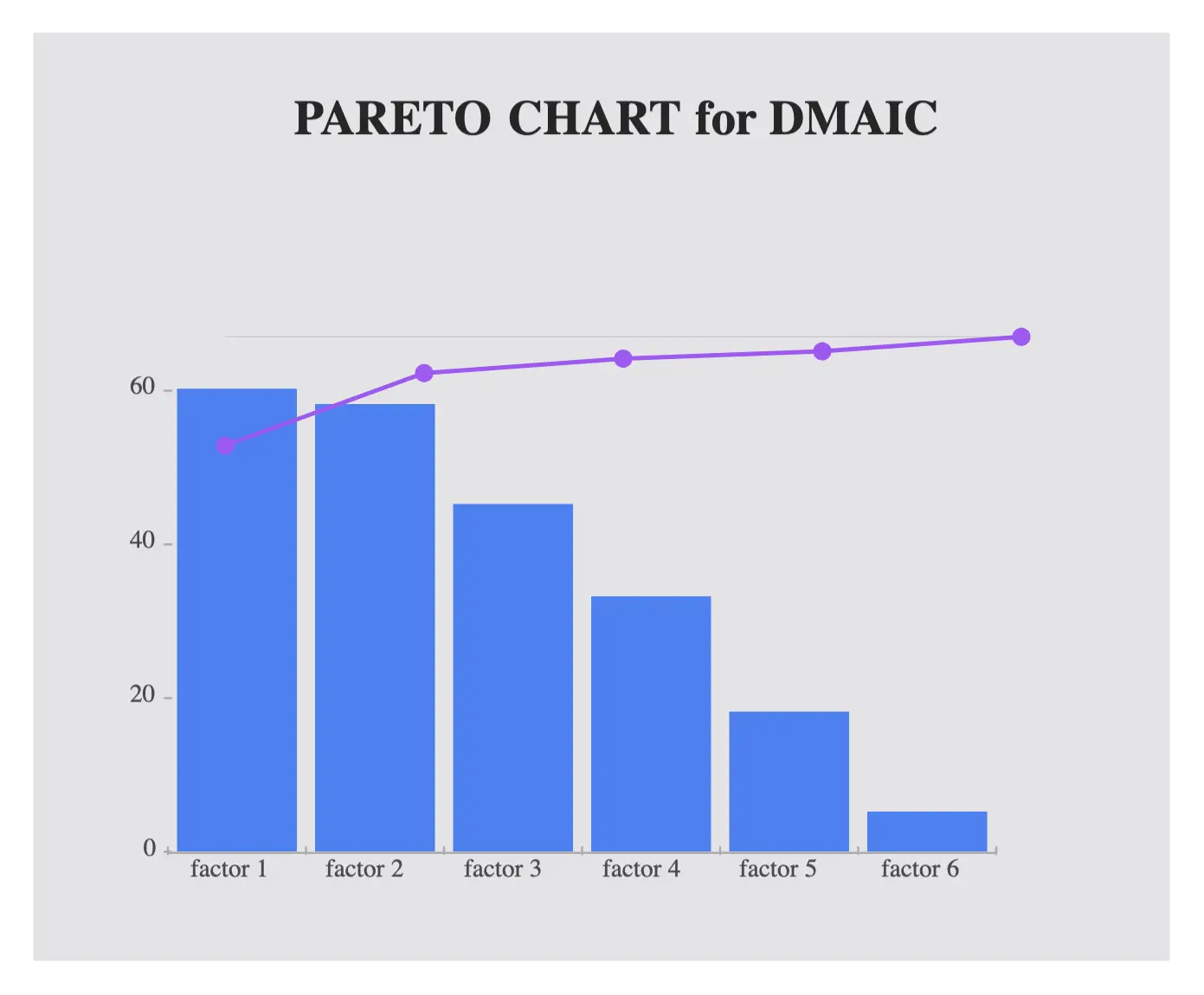
• With the results of your process analysis and your data analysis, start brainstorming the root causes of the problem. Use a cause and effect diagram/ fishbone diagram to capture the knowledge of the process participants during the session.
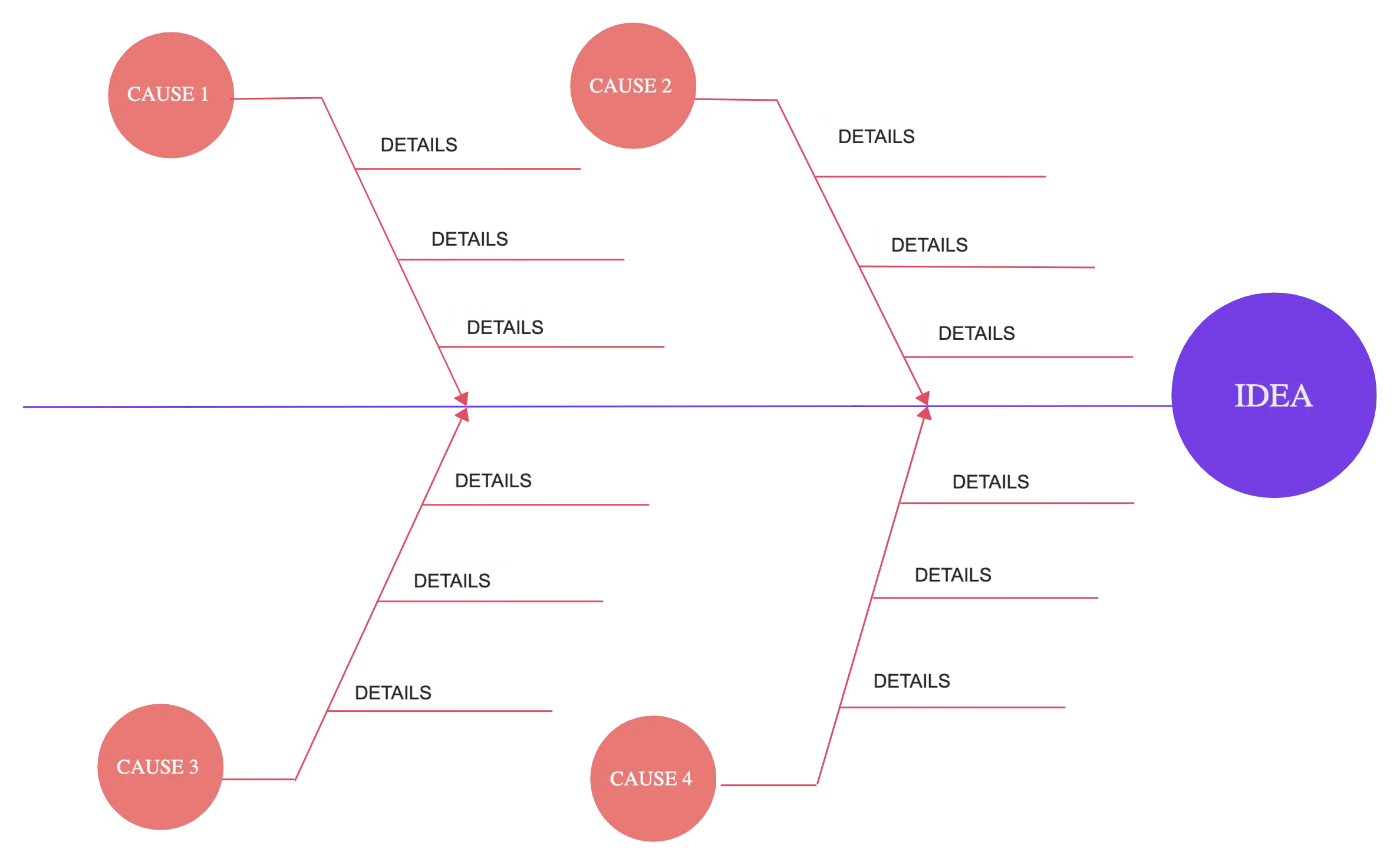
• Using a 5 whys diagram, narrow down your findings to the last few causes of the problem in your process.
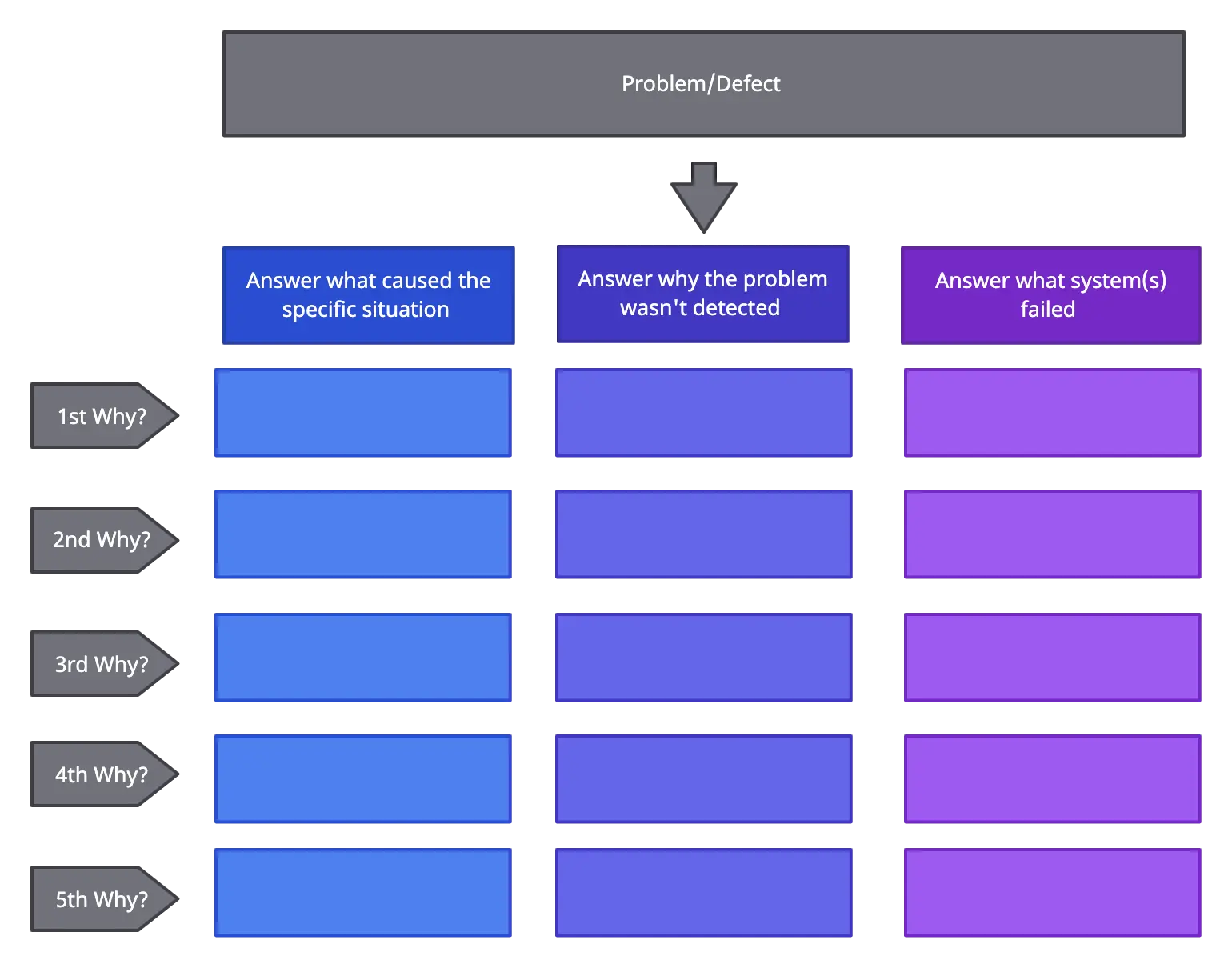
Step 4: Improve (Solve the Problem)
In this phase, the focus is on mitigating the root cause identified and brainstorming and implementing solutions. The team will also collect data to measure their improvement against the data collected during the ‘Measure’ phase.
• You may generate several effective solutions to the root cause, but implementing them all would not be practical. Therefore, you will have to select the most practical solutions.
To do this you can use an impact effort matrix . It will help you determine which solution has the best impact and the least effort/ cost.
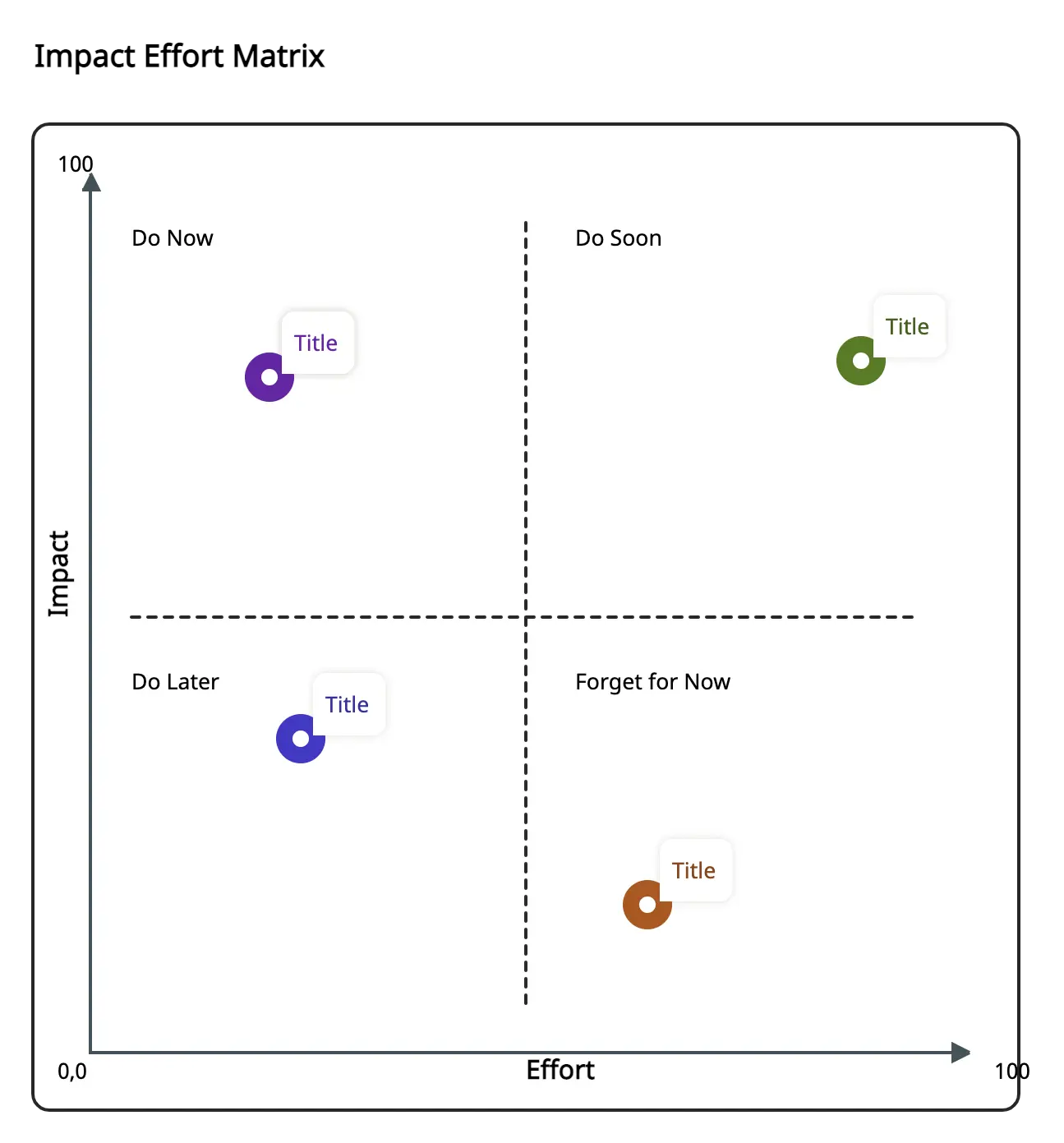
• Based on different solutions, you should develop new maps that will reflect the status of the process once the solution has been applied. This map is known as the to-be map or the future-state map. It will provide guidance for the team as they implement changes.
• Explore the different solutions using the PDCA cycle and select the best one to implement. The cycle allows you to systematically study the possible solutions, evaluate the results and select the ones that have a higher chance of success.
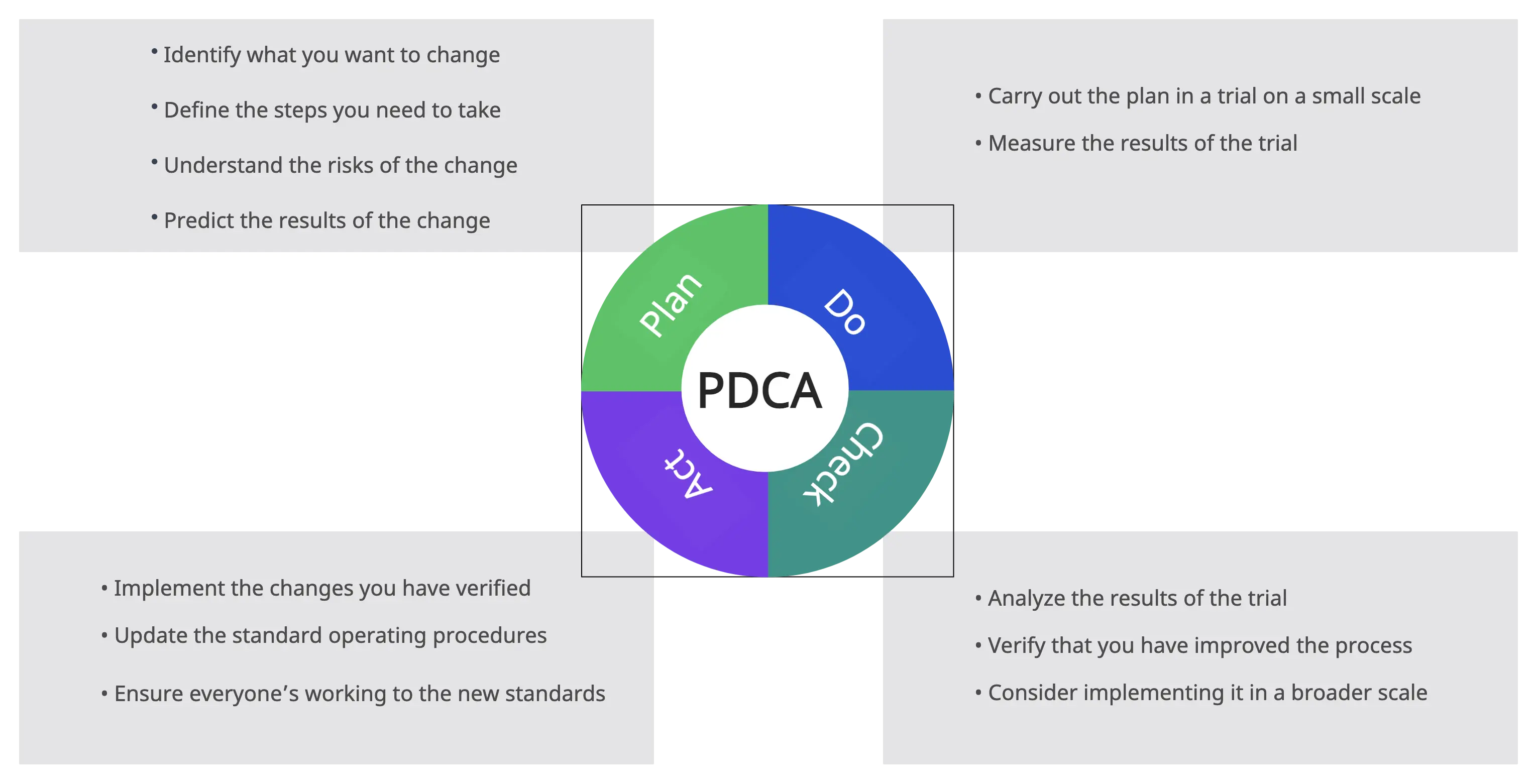
Step 5: Control (Sustain the Improvements)
In the final phase of the DMAIC method , the focus falls on maintaining the improvements you have gained by implementing the solutions. Here you should continue to measure the success and create a plan to monitor the improvements (a Monitoring plan).
You should also create a Response plan which includes steps to take if there’s a drop in the process performance. With new process maps and other documentation, you should then proceed to document the improved processes.
Hand these documents along with the Monitoring plan and the response plan to the process owners for their reference.
Insufficiently defining the problem can lead to a lack of clarity regarding the problem statement, objectives, and scope. Take the time to clearly define the problem, understand the desired outcomes, and align stakeholders' expectations.
Failing to engage key stakeholders throughout the DMAIC process can result in limited buy-in and resistance to change. Ensure that stakeholders are involved from the beginning, seeking their input, addressing concerns, and keeping them informed about progress and outcomes.
Collecting insufficient or inaccurate data can lead to flawed analysis and incorrect conclusions. Take the time to gather relevant data using appropriate measurement systems, ensure data accuracy and reliability, and apply appropriate statistical analysis techniques to derive meaningful insights.
Getting caught up in analysis paralysis without taking action is a common pitfall. While analysis is crucial, it’s equally important to translate insights into concrete improvement actions. Strive for a balance between analysis and implementation to drive real change.
Failing to test potential solutions before implementation can lead to unintended consequences. Utilize methods such as pilot studies, simulation, or small-scale experiments to validate and refine proposed solutions before full-scale implementation.
Successful process improvement is not just about making initial changes ; it’s about sustaining those improvements over the long term. Develop robust control plans, standard operating procedures, and monitoring mechanisms to ensure the gains achieved are maintained and deviations are identified and corrected.
Applying DMAIC in a one-size-fits-all manner without considering the organization’s unique culture, context, and capabilities can hinder success. Tailor the approach to fit the specific needs, capabilities, and culture of the organization to enhance acceptance and implementation.
In the project management context, the Define phase involves clearly defining the project objectives, scope, deliverables, and success criteria. It entails identifying project stakeholders, understanding their expectations, and establishing a project charter or a similar document that outlines the project’s purpose and key parameters.
The Measure phase focuses on collecting data and metrics to assess the project’s progress, performance, and adherence to schedule and budget. Key project metrics such as schedule variance, cost variance, and resource utilization are tracked and analyzed. This phase provides insights into the project’s current state and helps identify areas that require improvement.
The Analyze phase involves analyzing the project data and identifying root causes of any performance gaps or issues. It aims to understand why certain project aspects are not meeting expectations. Techniques such as root cause analysis, Pareto charts, or fishbone diagrams can be used to identify factors impacting project performance.
In the Improve phase, potential solutions and actions are developed and implemented to address the identified issues. This may involve making adjustments to the project plan, reallocating resources, refining processes, or implementing corrective measures. The goal is to optimize project performance and achieve desired outcomes.
The Control phase focuses on monitoring and controlling project activities to sustain the improvements made. It involves implementing project control mechanisms, establishing performance metrics, and conducting regular reviews to ensure that the project remains on track. Control measures help prevent deviations from the plan and enable timely corrective actions.
What are Your Thoughts on DMAIC Problem Solving Method?
Here we have covered the 5 phases of Six Sigma DMAIC and the tools that you can use in each stage. You can use them to identify problem areas in your organizational processes, generate practical solutions and implement them effectively.
Have you used DMAIC process to improve processes and solve problems in your organization? Share your experience with the tool with us in the comment section below.
Also, check our post on Process Improvement Methodologies to learn about more Six Sigma and Lean tools to streamline your processes.
Join over thousands of organizations that use Creately to brainstorm, plan, analyze, and execute their projects successfully.
FAQs about Six Sigma and DMAIC Approaches
DMAIC and DMADV are two methodologies used in Six Sigma. DMAIC is employed to enhance existing processes by addressing issues and improving efficiency, while DMADV is utilized for creating new processes or products that meet specific customer needs by following a structured design and verification process.
- Used for improving existing processes
- Define, Measure, Analyze, Improve, Control
- Identifies problem areas and implements solutions
- Focuses on reducing process variation and enhancing efficiency
- Used for developing new products, services, or processes
- Define, Measure, Analyze, Design, Verify
- Emphasizes meeting customer requirements and creating innovative solutions
- Involves detailed design and verification through testing
Problem identification : When a process is not meeting desired outcomes or experiencing defects, DMAIC can be used to identify and address the root causes of the problem.
Process optimization : DMAIC provides a systematic approach to analyze and make improvements to processes by reducing waste, improving cycle time, or enhancing overall efficiency.
Continuous improvement : DMAIC is often used as part of ongoing quality management efforts. It helps organizations maintain a culture of continuous improvement by systematically identifying and addressing process issues, reducing variation, and striving for better performance.
Data-driven decision making : DMAIC relies on data collection, measurement, and analysis. It is suitable when there is sufficient data available to evaluate process performance and identify areas for improvement.
Quality control and defect reduction : DMAIC is particularly useful when the primary objective is to reduce defects, minimize errors, and enhance product or service quality. By analyzing the root causes of defects, improvements can be made to prevent their occurrence.
More Related Articles
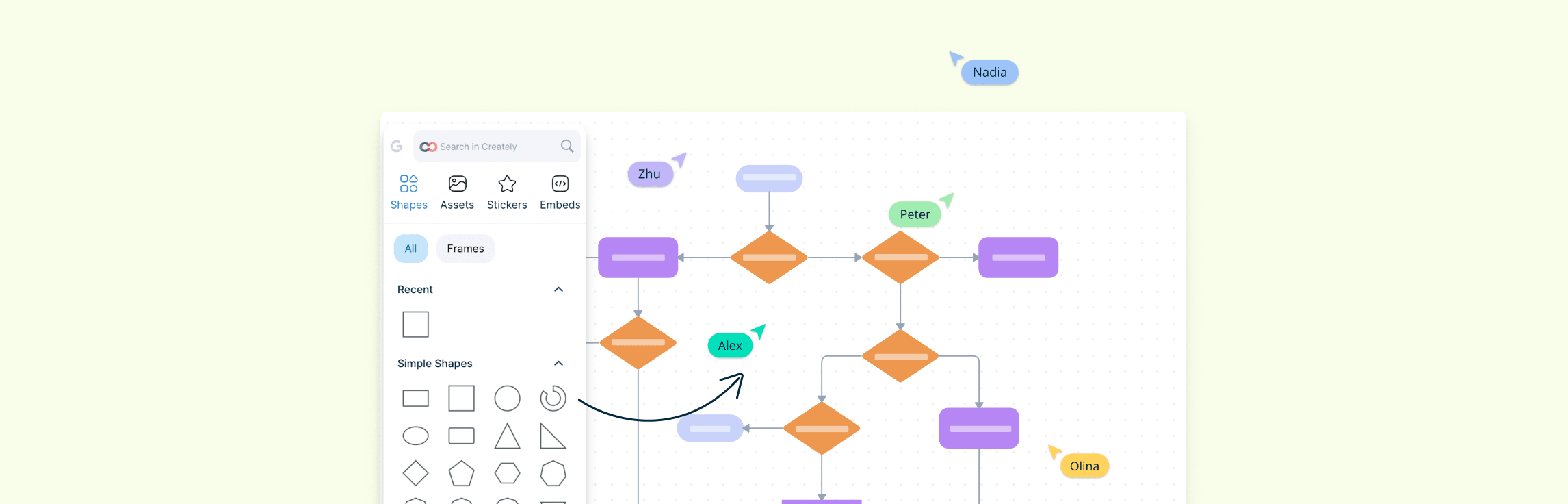
Amanda Athuraliya is the communication specialist/content writer at Creately, online diagramming and collaboration tool. She is an avid reader, a budding writer and a passionate researcher who loves to write about all kinds of topics.
- Professional Scrum Product Owner (PSPO)
- SAFe for Government
- Professional Scrum Master (PSM)
- Certified ScrumMaster
- PMI-ACP Exam Prep
- Leading SAFe® 6.0 Certification
- SAFe Scrum Master
- Certified Scrum Product Owner (CSPO)
- SAFe for Teams
- Agile Scrum Foundation
- AgilePM Foundation and Practitioner Certification
- Agile Scrum Master (ASM)
- Kanban Training
- Scrum Fundamentals
- PMP Certification
- Project Management Fundamentals
- CAPM Exam Prep
- Change Management Foundation and Practitioner Certification
- PRINCE2 Foundation & Practitioner Certification (7th Edition)
- PRINCE2 Agile Foundation & Practitioner Certification
- Business Analysis Foundation and Practitioner Certification
- Microsoft Project Training
- JIRA Certification Training
- Lean Project Management
- ITIL 4 Foundation
- VeriSM™ Foundation
- SIAM Foundation
- SIAM Professional
- 7 QC Tools Training
- Minitab Essentials
- Lean Six Sigma Yellow Belt
- Six Sigma Awareness
- Lean Six Sigma Green Belt
- Design for Six Sigma
- Lean Six Sigma Black Belt
- Lean Fundamentals
- Value Stream Mapping
- Quality by Design
- Quality Function Deployment
- BPM and Six Sigma
- RCA through Six Sigma
- DevOps Foundation
- DevOps Master
- DevOps Professional
- Continuous Delivery Architecture
- COBIT 5 Certification
- Corporate Group Training
- 1-to-1 Training
- Join as a Trainer
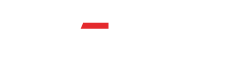
- Top Blogs on Quality Management
DMAIC Methodology: 5 Phases and the Tools used in Each Phases
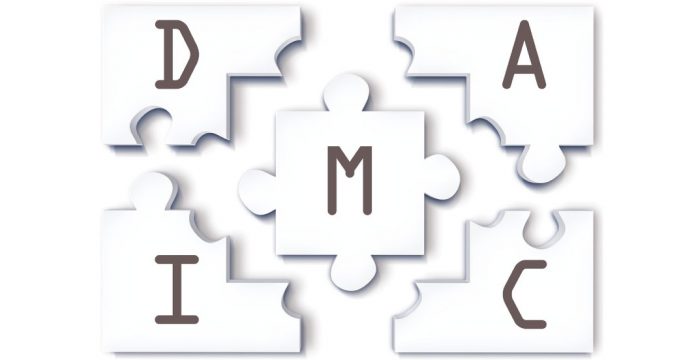
DMAIC is a widely utilized methodology that is the foundation of lean six sigma. Now, lean six sigma is a team-oriented management technique that aims to eliminate waste like physical resources, time, efforts, and defects in order to increase performance.
The appropriate application of DMAIC has benefited businesses in several ways, including lowering costs, improving quality, increasing revenue, and enhancing the overall company’s performance and efficiency. It also helps improve the faults and defects in your organization’s existing projects or processes. The Lean Six Sigma Yellow Belt certification is the entry-level certification credential that showcases a professional’s ability to successfully apply the fundamentals of six sigma methodology in an organization. So, if this sounds intriguing, read the article till the very end to understand everything about the DMAIC methodology. So we will start by understanding what the DMAIC methodology is.
What is DMAIC Methodology?
DMAIC is a data-driven problem-solving method for identifying and addressing inefficiencies in a process, improving its outputs, and making these improvements more predictable. The DMAIC methodology was founded by statistician Walter A. Shewhart and was created at Bell Laboratories in the 1930s and gets its roots from the PDSA (plan, do, study, act) cycle.
It is a five-phase approach for enhancing various organizational processes, including software development, manufacturing, and many others. This method is linked with six sigma and may also be used to lean and other process-improvement strategies. The acronym DMAIC stands for: Define- Measure-Analyze Improve Control . Now, the name itself gives out the five stages of this data-driven methodology. Now, let us talk about them one by one in detail.

The Five Phases of DMAIC Methodology
In this first step of DMAIC methodology, the team must clearly define the issues and the action plan necessary to attain the desired results in this initial step toward process improvement. The goal of this phase of DMAIC is to define the problem statement and develop a strategy for improvement. This phase is all about defining the issue and the improvement activity’s objectives. The most essential objectives are obtained from the clients because customer satisfaction is the primary objective of lean six sigma. So, project managers identify the issue to be addressed . To do so, one must first understand the problems as a whole and know the preferences of the customers.
Then they will need to define a problem statement for this and check if the issue reported is relevant by looking at the data available. As a result, they will be able to:
- Prioritize the issue into priorities
- Recognize the areas where it will influence
- Know the available resources
Once they figure out the problem statement and then outline the work process, they can start working on the project. The following stages ensure that the process is moving in the right direction.
The most commonly used DMAIC Tools in the “define” phase is Project Charter .
The project charter is the initial step in every six sigma project and one of the most crucial components. The document includes a summary of the project and serves as a contract between management and the six sigma team for the project’s projected outcome. Teams use the charter to define the process issue being addressed, the reason for doing so, and what “success” looks like for those working on it. Project Charter also helps to clarify what has not been discussed.
The goal of this phase is to gather data from the process and determine the current quality level. In this stage of DMAIC methodology, the team measures the existing system by defining valid and reliable metrics which will in turn help in tracking progress toward the goal. They must measure and monitor the project’s development and performance as soon as one begins working on it.
They must keep a close eye on the project and write down the “current stage” for the first assessment and use it as a baseline for the subsequent evaluations. It is a benchmark against which the project’s progress will be measured.
They may use this phase to figure out a means to collect as much measurable data as possible since it will be needed to analyze the core cause of the problems and their consequences. Constant updates from the team will be beneficial in this regard. One thing to keep in mind when gathering data is the source. Data must be accurate and come from a reputable source.
To make them more effective, they may make regular updates to the data in the workflow tools, such as a project charter.
The most commonly used DMAIC Tools in the “measure” phase are:
It is a type of bar chart that visualizes both attribute and variable data of a product or process and helps users show the different distribution of data and amount of variation within a process. So, it should be designed properly to easily utilize and understand those working in the operation process. Histograms can show the distribution of a process that is going smoothly over time. So, any fluctuation in that process can be immediately observed when histograms are produced on a regular basis. This is a significant benefit for businesses since it allows them to identify and address process variance immediately.
Pareto Chart
A Pareto Chart is a combination of a bar and line table that visually summarizes a set of data. The information might be related to things like cost, time, and mistakes. A Pareto chart helps to measure the cumulative impact of the defects. Now, the cumulative impact is the result of a defect occurring over a long time.
The pareto chart helps and offer a clearer understanding of the problems that must be addressed first, which helps to deliberate and arrange for the right and necessary procedures or actions to be performed in the event of a fault.
The major goal of this step in DMAIC methodology is to locate the source of the issue. Then, one may utilize the information gathered in the previous phases to figure out what’s causing it. The team manager keeps a close eye on the entire process along with the data. It is critical to assess the progress. So for this, make a list of the difficulties and concerns that arise from the data and observations. The team may contribute by expressing their perspectives and adding value to the process. Because lean six sigma focuses on removing waste from processes, the analysis includes analyzing the procedure in terms of:
1. Time: How efficiently project participants use their time. Are there any delays as a result of too extended breaks? Is there any factor that is causing the project to fall behind schedule?
2. Value: Is the project on track to meet the customer’s expectations? How does it provide value in terms of efficiency and product quality?
3. Value Stream Mapping: VSM is a technique for visualizing the flow. They may use the data to map the process and pinpoint the locations where waste processes are happening. It will allow the team to make better judgments about whether or not to add or remove a process step.
The most commonly used DMAIC Tools in the “analyze” phase are:
Fishbone- Diagram
During problem-solving, each team member has a different perspective on the root cause of the problem or question. The fishbone diagram collects all items and thoughts then uses brainstorming techniques to analyze and identify the most powerful underlying cause for that problem. It presents the possible causes using a graphic format. The core problem is placed at the head of the fish, then the different processes and sub-processes that may be responsible for the problem are noted in the bones of the fish.
This is a very interesting tool in the analysis phase . So to find the main cause of an issue, they should constantly ask the question “Why” (five is a decent rule of thumb). The actual cause of one problem will often lead to a new question. Despite the name “5 Whys,” one may discover that they need to ask the question fewer or more times than five times before they uncover the issue that is causing the problem.
In this phase of DMAIC methodology, after gathering the data and determining the root of the problem, the team member must devise a plan to address it. Using the data and the analysis report, the team at this stage seeks to improve the entire process. Now, the enhancements are introduced appropriately to get the intended benefits. As a result, they will need to put together a solid plan of action and assemble a team capable of coming up with creative answers. Proposing and choosing a solution to improve the system is the focus of this phase. This is the phase at which the team must become innovative in order to identify new methods to do things better, cheaper, or faster. The team addresses the root causes directly with an improvement based on the identified root causes.
One thing to keep in mind is that solutions must be feasible. They should be simple to execute and will not significantly increase the project’s expense. Other project restrictions, such as available workforce and technical assistance, must also be considered.
After figuring out the solutions, it’s time to put them into action and it is required to track and measure the progress. Now, to make things simpler, develop a list of the modifications that result in a better overall procedure.
The most commonly used DMAIC Tools in the “improve” phase are:
Countermeasures Matrix
A Countermeasures Matrix outlines the problems, identifies their causes, its fixes (countermeasures), and implementation priorities for an issue. Here, prioritization is determined by the team, ranking the recommended action items based on their importance or feasibility. This matrix acts as a source of information for creating an action plan.
Action Plan
Most improvements will need a strategy to ensure that they are implemented appropriately and that their effectiveness can be measured. So an action plan is very important. It is a strategy that helps improve the end products. An effective action plan will include questions like:
- What are the countermeasures?
- How to do them?
- Who will do them?
- When will they begin and end?
- How will they be measured?
The fifth stage of the DMAIC methodology is control, and it assures that the changes produced will last. It must be ensured that the problems do not occur again and the entire process adheres to the lean six sigma principles . Any deviations should be recorded and brought to the attention of the team. The team implements the solution and gives the ownership of the new, enhanced process to the responsible owner. They create a control strategy to monitor the ongoing performance and employ statistical methods to monitor the new process’s stability.
The team members can develop a monitoring algorithm that allows them to choose the various levels at which the process will function. They may also strategize the action plan to ensure that the gains are evident at these stages. They may also urge team members to keep the data up to date and add the progress at each level. This record is useful during the control phase. To find any issues with your DMAIC implementation, use this record.
The most commonly used DMAIC Tools in the “control” phase is:
Control Chart
In this phase, control charts are the most widely used tool. It helps in identifying the causes for variation in the new process, as well as the identification of corrective measures that must be taken before there are too many errors. This helps eliminate the requirement for product rework or additional product costs to repair an offering. So this was about the five phases of DMAIC methodology and the frequently used tools in these phases.
Initially, DMAIC was known as a method for reducing variation, but now the application of DMAIC can be considered a well-known mechanism for problem-solving and process improvement. Now, let us talk about some of the benefits of the DMAIC methodology.
Also read: The Top 7 Management Tools for Quality Control

Benefits of DMAIC Methodology
DMAIC methodology brings structure, helps in problem-solving, and is applied to complex processes and any type of organization. The data-driven approach helps identify the exact root causes and ensure that the applied enhancements outperform the previous strategy. It’s especially useful when dealing with complicated issues that involve many job functions or departments. Here are a few benefits of DMAIC methodology:
Structured Approach
DMAIC is a systematic technique that gives a road map for finding solutions. This enables us to solve problems from beginning to end while producing bottom-line results. DMAIC also offers an analytical approach, allowing the use of the data gathered. This helps the business ensure accurate baselines.
Faster Cycle Times
DMAIC software removes the friction from improvement, resulting in shorter improvement cycles and a quicker route to positive change. Because DMAIC improves communication, visibility, and responsibility, there is less downtime between phases in the improvement cycle. The faster each changes are implemented from beginning to end, the sooner the benefits are realized and move on to the next initiative.
Better Collaboration
DMAIC improves the collaboration of the entire team. One of the most difficult aspects of structured improvement is keeping everyone on the same page and informed about the cycle’s progress. This is especially challenging when the team consists of individuals from several functional areas who use distinct processes, terminology, and management styles.
More Impact From Improvement
With a knowledge repository in place, each DMAIC cycle may start with a review of what has previously worked successfully or failed. Teams get an advantage in terms of improvement by making more informed, data-driven decisions that result in more effective improvements. DMAIC software is useful because each improvement has the maximum, long-term impact.
Increased Productivity
Because the strategy is so systematic and requires comprehensive documentation, it helps to improve their problem-solving approach and efficiency constantly. DMAIC allows a business to quantify improvements and find answers to complex problems.
Improve the Overall Process
Then, it’s time to apply the DMAIC technique to improve the process. It aids in the identification of the problem’s fundamental cause and allows for the brainstorming of relevant solutions to the problems. The main goal of the DMAIC methodology is to improve the overall process. So these were just some of the benefits of the DMAIC methodology.
Now, sometimes DMAIC and DMADV can be confusing, because they share many similarities. So, let us talk about some differences between them.
Also read: Implementing DMAIC in Your Daily Life
DMAIC vs DMADV
Lean Six Sigma recommends an improvement process which is DMAIC. It is used to improve current processes. It is not concerned with the development of new goods, services, or processes. So, this is where DMADV comes into the picture. DMADV is a modified version for developing a new product, service or process. Now, let us see some differences between them to understand it better.
So these were just some of the differences between DMAIC and DMADV.

The DMAIC Methodology – Conclusion
DMAIC consists of five successive steps that produce the greatest outcomes when completed iteratively.
These stages are complementary to one another and, in some situations, iteratively operate together. When you acquire data in the measure phase, for example, you may need to evaluate and rectify it until your team can narrow down the problem’s main cause.
DMAIC is the foundation of the lean six sigma methodology. It is something you may use to improve existing initiatives in your business.
Implementing DMAIC requires a deep knowledge of lean and six sigma principles. This can be achieved by getting trained in globally-recognized six sigma and Quality Management Certification Courses from an accredited training organization.
Check out Invensis Learning popular quality management certification courses:
- Design For Six Sigma Training
- Lean Fundamentals Training
- Six Sigma Awareness Training
Lean Six Sigma Yellow Belt Certification Training
Lean Six Sigma Green Belt Certification Training
Lean Six Sigma Black Belt Certification Training
Lean Fundamentals Certification Training
Lean IT Certification Training
RCA Through Six Sigma Certification Training
7QC Tools Certification Training
Value Stream Mapping Certification Training
RELATED ARTICLES MORE FROM AUTHOR
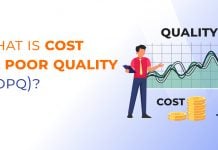
What is Cost of Poor Quality (COPQ)?
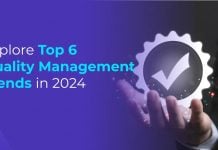
Top 6 Quality Management Trends to Follow in 2024
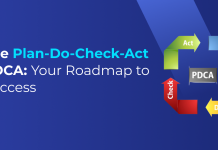
What is the Plan Do Check Act (PDCA) Cycle?
Leave a reply.
Save my name, email, and website in this browser for the next time I comment.
- 14,521 Likes
- 444 Followers
- 96,000 Subscribers
- 2,170 Followers
Related Articles
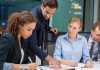
ITIL Access Management: Objectives, Process And Values
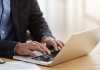
Top 10 Reasons To Get a Lean Six Sigma Certification
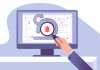
Agile Testing Methodology: Principles, Methods, and Advantages
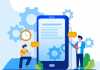
SAFe Agile Certification: What is SAFe for Teams?
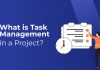
What is Task Management in a Project?
Popular posts.
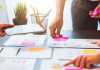
The Project Management Life Cycle Explained
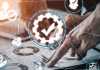
Roles and Responsibilities of a Quality Control Inspector
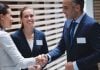
7 Cs of Effective Communication with Example
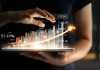
Top 5 Factors for Project Success
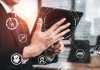
Quality Analyst Job Role and Responsibilities- Explained!
Suggested posts.
- 7 Cs of Effective Communication with Examples
- Project Management Lifecycle
- Project Success Factors
- Quality Control Inspector Job Description
- Risk Management Examples
- QA Manager Job Description
- Quality Management Team Roles and Responsibilities
- Risk Management Tools & Techniques
- Quality Analyst Job Description
- What is Business Value
- Who are Project Stakeholders
- Importance of Project Management
- What is Project Management
- Project Management Skills
- Project Manager Job Description
- Agile Project Manager Interview Questions
- Risk and Compliance Manager Job Description
- Risk Management Process
- Project Scope Management
- Healthcare Project Manager Job Description
- Six Sigma Project Examples
- Risk Analysis Methods
- ITIL Service Lifecycle
- Risk Manager Job Description
POPULAR CATEGORIES
- Best Project Management Blogs 254
- Top Agile Blog Posts 158
- Top Blogs on Quality Management 126
- Latest IT Service Management Blogs 108
- Trending Articles on DevOps 65
- Popular Blogs on IT Security and Governance 55
- Top Blogs on Professional Development 33
- Top Infographics Collection 8
Download E-book Blog
Thank You for submitting your enquiry. One of our training consultants will get in touch with you shortly.
50+ Training and Certification Programs - Upskill Today Learn more about our training programs.
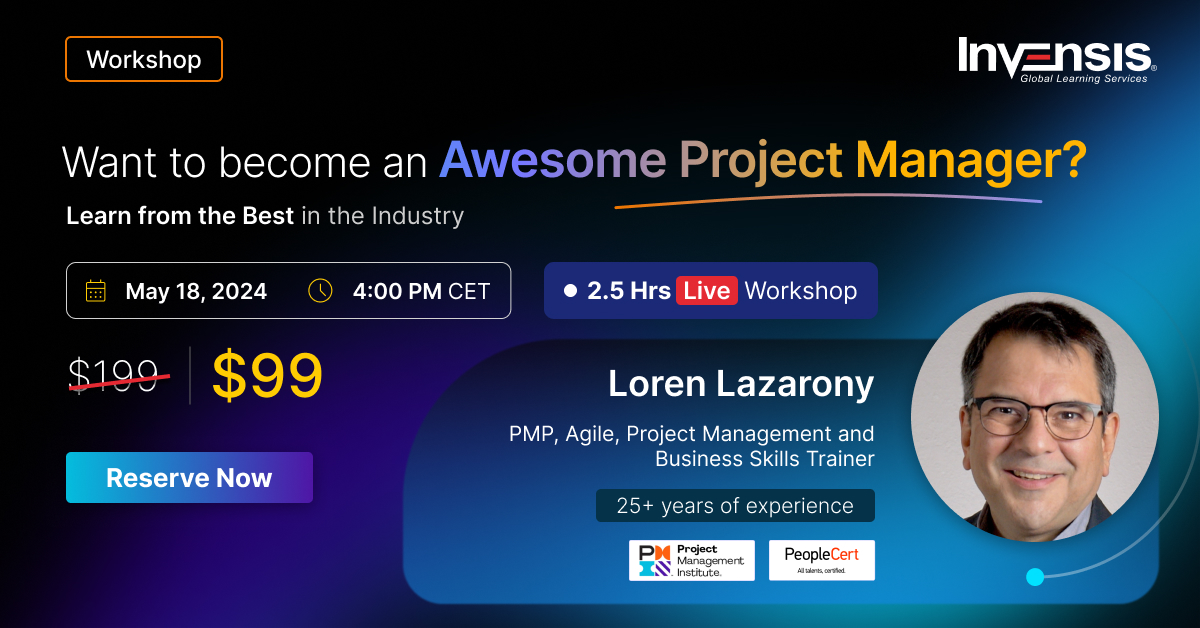
- Professional Services
- Creative & Design
- See all teams
- Project Management
- Workflow Management
- Task Management
- Resource Management
- See all use cases
Apps & Integrations
- Microsoft Teams
- See all integrations
Explore Wrike
- Book a Demo
- Take a Product Tour
- Start With Templates
- Customer Stories
- ROI Calculator
- Find a Reseller
- Mobile & Desktop Apps
- Cross-Tagging
- Kanban Boards
- Project Resource Planning
- Gantt Charts
- Custom Item Types
- Dynamic Request Forms
- Integrations
- See all features
Learn and connect
- Resource Hub
- Educational Guides
Become Wrike Pro
- Submit A Ticket
- Help Center
- Premium Support
- Community Topics
- Training Courses
- Facilitated Services
DMAIC vs DMADV: Choosing the Right Approach for Quality Improvement
August 28, 2023 - 10 min read

Quality improvement is a critical aspect of any organization's success. It allows businesses to identify and resolve issues, enhance operations, and meet customer demands effectively. Two commonly used methodologies for quality improvement are DMAIC and DMADV. In this article, we will explore the differences between these approaches and help you make an informed decision on which one to choose for your organization's quality improvement efforts.
Understanding the Basics of Quality Improvement
Quality improvement refers to the systematic approach that organizations adopt to enhance their products, processes, and services continuously. It focuses on identifying areas of improvement, analyzing root causes, implementing solutions, and evaluating results. Moreover, it function as a dynamic and ongoing process that businesses undertake to stay competitive in today's rapidly changing business landscape. By continuously striving for improvement, they can adapt to market demands, customer preferences, and technological advancements.
The Importance of Quality Improvement
Quality improvement is crucial because it:
- Optimizes business operations, leading to increased efficiency and reduced costs.
- Meets customer expectations by delivering high-quality products and services.
- Enhances the reputation and credibility of the organization. When customers perceive an organization as committed to quality, they are more likely to trust its products and services.
Key Concepts in Quality Improvement
There are several key concepts that underlie quality improvement efforts.
- Continuous improvement: Make incremental enhancements over time and be on the road to fostering innovation, creativity, and a commitment to excellence.
- Data-driven decision-making methods: Collect and analyze relevant data to make informed decisions based on facts and evidence rather than assumptions.
- Effective communication, collaboration, and teamwork: Foster open and transparent communication channels to ensure that all stakeholders are aligned and working towards a common goal.
An In-depth Look at DMAIC
DMAIC stands for Define, Measure, Analyze, Improve, and Control. It is a structured problem-solving methodology widely used in quality improvement projects. Let's delve into each phase of DMAIC:
- Define: Conduct thorough research to gain a deep understanding of the problem at hand. This includes analyzing customer feedback, conducting surveys, and studying industry best practices. By gathering as much information as possible, you gain a comprehensive understanding of the problem and can develop effective solutions. Also, create a project charter , which serves as a roadmap for the entire DMAIC process. The project charter outlines the project's objectives, scope, timeline, and key deliverables.
- Measure: Employ various data collection techniques such as surveys, interviews, and statistical analysis. This helps in gathering accurate and reliable data that reflects the current state of the process or product. By measuring key performance metrics, you can identify areas of improvement and set realistic goals for the subsequent phases of DMAIC.
- Analyze: Dive deep into the collected data to identify patterns, trends, and potential causes of the problem. Use various analytical tools and techniques to uncover the underlying issues and determine the root causes. This phase requires a meticulous examination of the data to ensure accurate and reliable findings.
- Improve: This is where creativity and innovation come into play. Brainstorm ideas and develop potential solutions to address the root causes identified in the Analyze phase. These solutions are then tested and refined through pilot projects or simulations to confirm their effectiveness. Once the most effective solution is identified, it is implemented on a larger scale to bring about the desired improvement.
- Control: Guarantee the long-term success of the improvement efforts. Establish control mechanisms such as standard operating procedures, performance metrics, and regular monitoring processes to verify that the improvements are sustained. Any deviations from the desired performance are identified and corrective actions are taken promptly to maintain the desired level of quality.
When to Use DMAIC
DMAIC is particularly well-suited for projects where a process already exists and needs improvement. It is effective for addressing ongoing issues, reducing variations, and optimizing existing processes. DMAIC is widely used in various industries, including manufacturing, healthcare, and service sectors.
Overall, companies often turn to DMAIC when they want to enhance the efficiency and effectiveness of their existing processes. By following the DMAIC methodology, businesses can systematically identify and address the root causes of problems, leading to improved quality, reduced costs, and increased customer satisfaction. DMAIC provides a structured approach that promotes continuous improvement and helps you stay competitive in today's rapidly changing business environment.
Unpacking DMADV
DMADV, which stands for Define, Measure, Analyze, Design, and Verify, is an alternative approach to quality improvement that is often used when there is a need to design and implement a new process or product. This methodology provides a structured framework for organizations to follow, ensuring that the end result meets customer requirements and delivers the desired outcomes. Let's explore each phase in detail:
- Define: Focus on defining the project goals, scope, and customer requirements. Establish a clear understanding of what the new process or product should deliver. This phase involves conducting thorough research, engaging with stakeholders, and gathering insights to lay a solid foundation for the rest of the DMADV process.
- Measure: Gather and analyze data related to the current state of affairs. This establishes a baseline and identifies areas for improvement in the new process or product. By collecting data from various sources, such as customer feedback, market research, and internal performance metrics, you gain valuable insights to make informed decisions throughout the DMADV journey.
- Analyze: Analyze the gathered data to identify potential design alternatives. This phase focuses on understanding customer needs, evaluating different design options, and selecting the most promising solution. Through techniques such as root cause analysis, process mapping, and statistical analysis, you gain a deeper understanding of the challenges and opportunities that lie ahead.
- Design: Develop a detailed design for the new process or product, by creating prototypes, conducting simulations, and refining the design based on feedback and analysis. This phase is where creativity and innovation come into play, as organizations explore different possibilities and strive to find the optimal solution that meets customer requirements. Collaboration between cross-functional teams, including designers, engineers, and subject matter experts, is crucial.
- Verify: Test and validate the designed process or product by conducting pilot runs, collecting feedback, and making necessary adjustments to verify that the final solution meets customer requirements. By engaging with end-users and stakeholders, you can identify any potential issues or areas for improvement before fully implementing the new process or product. This phase acts as a crucial checkpoint to ensure that the solution is robust and ready for implementation.
Ideal Situations for DMADV
DMADV is most appropriate when organizations need to create a new process or product from scratch or are introducing significant changes to an existing one. It is commonly used in industries such as product development, engineering, and research, where innovation and new designs are essential. By following the DMADV methodology, organizations can minimize risks, improve efficiency, and deliver high-quality results that meet or exceed customer expectations.
Also, implementing DMADV requires a dedicated team, strong leadership, and a commitment to continuous improvement. It is a comprehensive approach that ensures organizations consider all aspects of the process or product, from defining the goals to verifying the final solution. By embracing DMADV, companies can drive innovation, enhance customer satisfaction, and stay ahead in today's competitive business landscape.
DMAIC and DMADV: A Comparative Analysis
While DMAIC and DMADV share some similarities, they differ significantly in their application and goals. Let's explore the key similarities and differences between these two quality improvement methodologies:
- Both methodologies follow a structured approach to problem-solving and improvement.
- Both emphasize the importance of data-driven decision-making and continuous improvement.
- Both DMAIC and DMADV involve defining project goals and measuring the existing process or product performance.
- DMAIC is used for improving existing processes, while DMADV focuses on designing new processes or products.
- DMAIC is suitable for addressing ongoing issues, reducing variations, and optimizing existing processes. In contrast, DMADV is used when significant changes or innovations are required.
- DMAIC relies on existing data and information, while DMADV involves gathering new data and conducting extensive analysis during the design phase.
Making the Right Choice: DMAIC or DMADV?
Choosing the appropriate approach, DMAIC or DMADV, depends on various factors. Consider the following when making your decision:
- Project goals: Assess whether your project requires improvement of an existing process or the creation of a new one.
- Project scope: Evaluate the magnitude of change needed and the resources available to determine the feasibility of either approach.
- Industry and context: Consider the specific industry requirements, regulatory compliance, and the level of innovation required.
Ultimately, choosing the right approach, DMAIC or DMADV, can significantly impact the success of your quality improvement initiatives. Implementing the appropriate methodology ensures that your efforts are aligned with your project goals, delivering measurable improvements and enhancing overall organizational performance.
Choose the Right Quality Improvement Approach with Wrike
Choosing the right approach between DMAIC and DMADV is crucial for quality improvement. With Wrike, you can manage both DMAIC and DMADV initiatives effectively. Wrike allows you to create individual folders for each stage of DMAIC and DMADV, serving as a central hub for all relevant information and updates. Beyond just DMAIC and DMADV, Wrike offers a comprehensive suite of tools designed to streamline your workflows, foster collaboration, and drive productivity. From real-time communication to intuitive task management features, Wrike provides everything you need to choose the right approach for quality improvement. Ready to choose the right approach for quality improvement and boost your productivity? There's no better time to start than now. Get started with Wrike for free today.
Note: This article was created with the assistance of an AI engine. It has been reviewed and revised by our team of experts to ensure accuracy and quality.

Occasionally we write blog posts where multiple people contribute. Since our idea of having a gladiator arena where contributors would fight to the death to win total authorship wasn’t approved by HR, this was the compromise.
Related articles
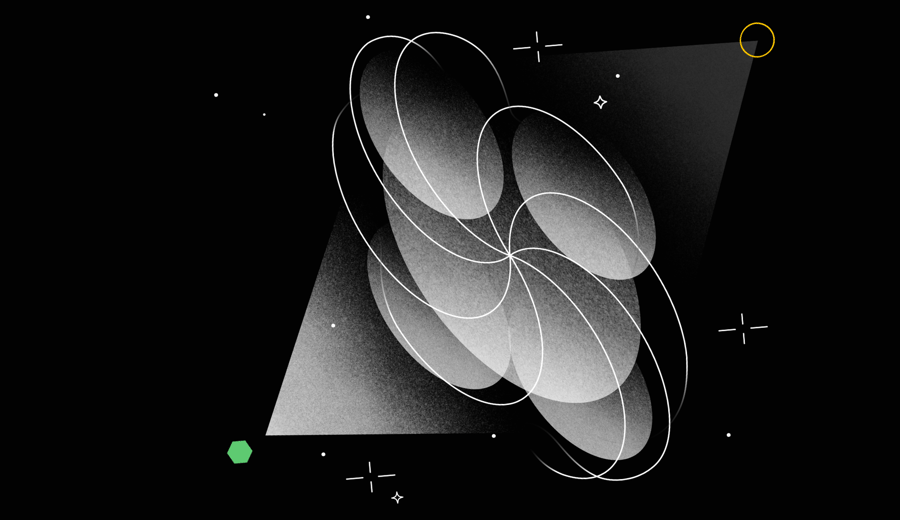
Dark Matter of Work: The Cost of Work Complexities in The PMO
Efficiency is everything for organizations – especially as we face a possible recession and mass layoffs continue. Plus, the way we work continues to evolve and become more complex, causing efficiency to suffer even more. Over the past few years, modern work complexities have been eating away at your bottom line through an invisible yet powerful presence in your organization — what we call the Dark Matter of Work. Just as CERN identified Dark Matter as the “invisible” content that makes up 95% of the mass of the universe, the Dark Matter of Work represents activity and details that we can’t immediately see but that have a significant influence on everything around it. From the tools we use to conduct our work to where and when we execute it, work complexities have truly exploded in recent years and will only become more complicated over time — making it increasingly difficult for employees and business leaders to get visibility into work and truly understand work in progress. Wrike is focused on shining a light on the Dark Matter of Work. That’s why we recently commissioned research to investigate its impact on PMO leaders, employees, and organizations as a whole. We wanted to understand to what extent Dark Matter exists and discover the financial cost of Dark Matter affecting us all. The results are staggering and can point PMOs towards key ways they can increase efficiency to endure the unknown economic future. Let’s explore the results. Impact on the PMO While we cannot “see” the Dark Matter of Work, we can identify where it exists. It lives in synchronous applications and unstructured work, such as instant message threads and video calls, as well as the gaps between systems and applications that aren’t integrated. Without a single work platform that is powerful and versatile enough to track, manage, action, and align all work to goals across an organization, there exists a dangerously low level of visibility amongst knowledge workers and leaders. At present, most project managers and PMO leaders generally have little visibility into the work their teams are doing and cannot track the progress of much of that work in real time. And if we ask knowledge workers, they say employer visibility into their work is even lower — suggesting there may be more Dark Matter of Work than we think. Wasted time Time wasted on activities such as repeating work that’s already been done, attending unproductive meetings, or following up on actions and statuses costs the average enterprise millions. The cost of the Dark Matter of Work The total cost of Dark Matter for PMOs and project managers is quite substantial and will continue to increase exponentially unless addressed. Low visibility For business and PMO leaders, visibility into work has only increased slightly since 2020 — from 48% to 51%. And other project managers are struggling to view their assignments and expectations. More human costs Amid the Great Resignation, the mass layoffs, and the continuing remote work environment, PMOs must work to address the human costs of the Dark Matter of Work, as well. Too many applications As hybrid work continues, PMOs rely more and more on applications to stay connected. But many of these tech tools do not integrate with each other, decreasing visibility, increasing wasted time, and resulting in duplicative work. Plus, app integration is also moving at a slow pace from 2020 (43%) to now (49%). Looking ahead If left unchecked, Dark Matter will increase by 42% in the next five years. According to the survey, the projected cost of Dark Matter in 2027 looks to be: How can you minimize these costs? A single source of truth is essential. PMOs need a solution that is robust enough to manage and orchestrate complex workflows and simple enough for team members to use. The organization with full visibility into these workflows and applications and the data they create at all levels will be best equipped to overcome the impacts of the Dark Matter of Work and come out on top. For more on the Dark Matter of Work, its costs, and the solutions, check out the full report here — and usher in a new age of digital collaboration. Or start a free two-week trial of Wrike today to see how our work management solution can centralize work and increase efficiency for your PMO!
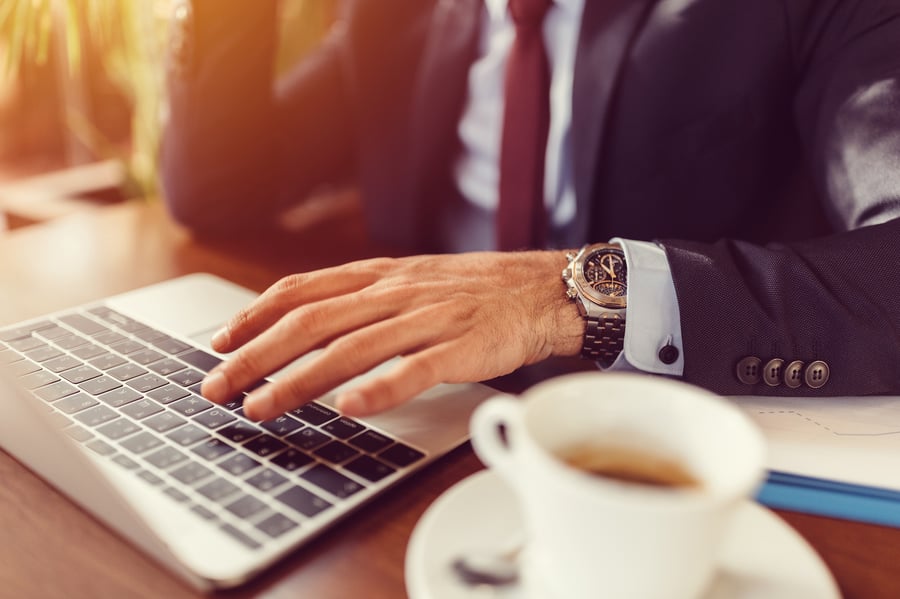
Scrum Master vs. Project Manager: Key Differences
When it comes to managing projects, Scrum and traditional project management are the two most commonly used approaches. Although both aim to deliver projects successfully, they differ in their processes and methodologies. In this article, we will explore the differences between a Scrum master vs. project manager and provide insights into their roles, responsibilities, and skill sets. Take your project management skills to the next level with Wrike’s advanced features, designed to support both Scrum and traditional project management methodologies. Claim a 14-day free trial of Wrike to explore the differences and similarities in practice. Try Wrike for free The difference between Scrum master and project manager Before we dive into the differences between the two, let’s first define Scrum and project management. Defining Scrum Scrum is an Agile project management methodology that enables teams to deliver high-quality products and involves regular reviews and feedback sessions. It is repetitive and focuses on delivering features in short sprints. Scrum teams typically consist of a Scrum master, product owner, and development team members. Defining project management On the other hand, traditional project management is a methodology that is more linear in nature. It aims to plan, control, and execute a project successfully, step by step. This involves defining goals, analyzing resources, developing timelines, and monitoring progress. Project managers are responsible for overseeing the project’s delivery and ensuring it meets the objectives. Roles and responsibilities of a Scrum master The Scrum master is a critical role in any Agile development team. They make sure the team follows the Scrum methodology and delivers high-quality work on time and within budget. Essentially, the Scrum master is a servant leader who collaborates with the development team. They also work with the product owner and other stakeholders to ensure that everyone is aligned and working toward achieving the project’s objectives. Facilitate Scrum events The Scrum master arranges and leads Scrum activities like sprint planning, daily standups, sprint reviews, and sprint retrospectives. During these events, the Scrum master ensures that the team stays focused and on track. Any issues or challenges that may be hindering progress are identified and addressed to boost the team’s overall productivity. Sprint planning requires collaborating with the product owner and development team to create a sprint backlog that outlines the work to be completed during the sprint. Scrum masters clarify the sprint goals for the team, so that everybody knows what must be accomplished. Daily standups involve ensuring that everyone on the team is following the Scrum framework and is aware of each teammate’s progress. Scrum masters identify any roadblocks and work with the team to remove them. Sprint reviews require communication with the team to review all completed tasks during the sprint. The work must meet the definition of ‘Completed,’ so that the Scrum master can assist the product owner in updating the product backlog based on the team’s progress. Lastly, sprint retrospectives involve identifying areas for improvement and assisting the team in developing a subsequent action plan. Scrum masters also ensure that the team is continuously learning and improving. Try Wrike for free Coach the team The Scrum master is responsible for coaching the development team on Scrum principles and practices. The team must understand and follow the Scrum framework and continuously improve their processes and practices. Areas for improvement are identified and addressed by the Scrum master alongside the team. They provide guidance and support to ensure that everyone is aligned and working toward achieving the project’s objectives. Remove roadblocks The Scrum master finds and removes obstacles that stop the team from delivering good features. They collaborate with the development team, product owner, and others to ensure the team has what it needs for success. Teams are aided by the Scrum master to identify and address any issues or challenges that may be hindering progress. They work with the team to remove roadblocks that slow down productivity. Ensure transparency and collaboration The Scrum master is responsible for fostering transparency and collaboration within the team and between the team and stakeholders. They ensure that everyone is aware of the project’s progress and that the team is working toward achieving its objectives. They also work with the product owner to ensure that the product backlog is transparent and that everyone understands the priorities and goals of the project. Roles and responsibilities of a project manager The project manager, in contrast to the Scrum master, oversees the entire project life cycle and works closely with stakeholders. Their key responsibilities include: Define project scope and objectives Defining the project scope means identifying the boundaries of the project and determining what is included and excluded. This step is important to make sure the project stays on track and the team members know what they have to do. Outlining the objectives requires identifying the specific outcomes that the project is expected to achieve. This ensures the project matches the organization’s goals and that everyone is working toward the same outcome. Identifying the resources required to deliver the project involves determining what people, equipment, and materials are needed. This makes sure the project has enough resources and avoids delays or bottlenecks caused by a lack of resources. Develop a project plan Developing a comprehensive project plan involves breaking down the project into smaller, more manageable tasks. This allows the team to keep track of tasks and deadlines. Creating timelines ensures that the project is completed on time and maintains a sense of organization. Identify and manage risks and issues This means anticipating potential problems that may arise during the project and developing strategies to address them. Doing this makes sure the project isn’t affected by surprises and the team is ready to deal with any problems. The project manager must also work with stakeholders to address these and ensure that the project remains on track. This means tracking the team’s progress against the project plan and crafting solutions. This could include adjusting the project plan or allocating additional resources to address the issue. Ensure quality Project managers must confirm that their team’s work meets project requirements and the tasks’ criteria. Additionally, they need to make sure that it follows relevant standards or regulations. This may involve developing quality standards and processes, conducting quality reviews, and providing feedback to the team. Comparing the skill sets of Scrum masters and project managers Although both roles focus on delivering projects, they require different skill sets. Some of the key differences include: Leadership styles Scrum masters typically follow a servant-leadership style, where they lead by example, empower the team, and prioritize the team’s needs. They believe in serving the team members rather than managing them. They act as a coach, mentor, and facilitator, allowing the team to self-organize and make its own decisions. Scrum masters also encourage collaboration, continuous improvement, and innovation. Project managers lead and make decisions for the team, using an authoritative leadership style. They are responsible for ensuring that the project is completed within the desired budget, scope, and timeline. Project managers have the power to give tasks, distribute resources, and make important choices. They also check task progress and update stakeholders. Communication skills Scrum masters need good communication skills to help teams work together and be open. They talk to team members, stakeholders, and customers every day. They also need to be good listeners, effectively understanding the needs and concerns of the team and addressing them promptly. Although project managers also need strong communication skills, they often focus more on communicating project progress to stakeholders and addressing all of their concerns. Therefore, project managers must be good negotiators, effectively resolving conflicts and reaching agreements. Problem solving abilities Scrum masters need to be skilled problem solvers, as they often address issues that arise during the development process. They must be able to identify the root cause of the problem, propose solutions, and implement them. They also encourage the team to come up with creative solutions and experiment with new ideas. As for project managers, they also need to have strong problem solving skills. However, they tend to focus more on risk management and identifying risks. They must be able to anticipate potential problems and develop contingency plans. They must evaluate the risks’ effect on the project and take suitable steps to reduce them. Adaptability and flexibility Scrum masters need to be adaptable and flexible to pivot their approach and adapt to changes as the project progresses. They must be able to embrace change and encourage the team to do the same. They also need to be able to adjust the scope, timeline, and budget of the project to accommodate changes. Project managers must do the same, even though they tend to develop and follow a more rigid plan. They must be able to adjust the plan as needed while ensuring that the project stays within the scope, timeline, and budget. Project managers also must balance the needs of the stakeholders with the needs of the team. Conclusion Both project managers and Scrum masters play critical roles in delivering projects successfully. However, they differ in their methodologies, responsibilities, and skill sets. If you’re looking to adopt an Agile methodology that focuses on iterative delivery, Scrum may be for you. But if you’re looking for a more structured approach to a project, traditional project management may be a better fit. Ultimately, it comes down to your team’s objectives, resources, and constraints. Get acquainted with the unique roles and responsibilities of Scrum masters and project managers, and then watch your projects thrive with Wrike’s collaboration-focused platform. Begin your free trial now and amplify efficiency across your Agile-oriented organization. Try Wrike for free Note: This article was created with the assistance of an AI engine. It has been reviewed and revised by our team of experts to ensure accuracy and quality.

Workflow Diagram Examples for Process Management
If you’re looking to improve your business processes, one of the best tools to use is a workflow diagram. Not only do these diagrams provide a clear visual representation of how a process works, but they also help to identify areas for improvement and streamline operations. This article will discuss the key components of workflow diagrams and provide tips on creating effective diagrams to improve work management. Harness the power of effective workflow diagrams with Wrike and enhance your organization’s process management efforts. Unlock the efficiency of your business operations with a 14-day free trial of Wrike’s advanced project management software. Try Wrike for free Understanding workflow diagrams Let’s first gain a better grasp of what workflow diagrams are, how they will benefit you, and key components to remember when creating your diagram. What is a workflow diagram? A workflow diagram is a visual representation of a process that illustrates how tasks are completed from start to finish. The diagram outlines each step in the workflow, specifically the inputs, outputs, and connections between each step. Let’s say you work for a company that manufactures and sells products. Making and selling a product involves many steps, like designing, sourcing materials, manufacturing, marketing, and selling it. A workflow diagram can depict how all of these steps are connected in order. Benefits of using workflow diagrams The plethora of benefits to businesses taking advantage of the workflow diagram include: Improved efficiency: It is easier to identify areas for improvement and streamline operations. Steps that take too long or cause delays can quickly be identified and addressed. Reduced errors: Understanding how a process works can help reduce mistakes and increase efficiency. Clear communication: Workflow diagrams clearly communicate project steps to others and can be especially helpful when training new employees or working with outside vendors. Flexibility: If changes to the workflow must be made, diagrams assist the team in understanding how they will affect the overall project. If a new step is added or removed, the diagram can be updated to reflect these changes. Key components of a workflow diagram Workflow diagrams typically include the following elements: Start/end points: A clearly defined start and end point indicates where the process begins and ends. This is often represented by a circle or oval shape. Tasks or actions: Each step in the workflow serves as a specific task or action. This is often denoted by a rectangle shape. Decision points: Decision points reflect a choice that must be made in the process, such as whether to proceed to the next step or not. This often comes in the form of a diamond shape. Connectors: Connectors symbolize the flow of the process, showing how one task or action leads to the next. This is often represented by arrows or lines. Inputs and outputs: Input and output data or information should be included to show what is needed for each step and what is produced as a result. Use small rectangles connected to the task or action to mark them. Workflow process examples and types of diagrams While there are many types of workflow diagrams, some of the most common include: Flowchart diagrams Flowchart diagrams use symbols to represent each step in a workflow and the connections between them. These diagrams are often used to show the logic of a process. They help find ways to make a process better, especially when there are extra or unnecessary steps. Let’s take the example of a manufacturing operation. A flowchart shows the steps to make a product, from materials to finished goods. This tool can also show the different stages of the process, such as assembly, quality control, and packaging. Swimlane diagrams Swimlane diagrams, also known as cross-functional flowcharts, illustrate the steps in a process across multiple departments or functions. This type of diagram is particularly useful for identifying areas where communication and coordination between departments can be improved. Swimlane diagrams use horizontal or vertical lines to separate the different departments or functions involved in the workflow. A swimlane diagram can be used to depict the steps for hiring in a company. The diagram illustrates the different departments involved in the process, such as HR, hiring managers, and finance. Business process model and notation (BPMN) diagrams BPMN diagrams are a standardized form of workflow diagram used to portray complex processes. These diagrams use specific symbols to define the different types of tasks, decisions, and events that make up a process. BPMN diagrams are particularly useful for modeling business processes that involve multiple departments or functions. A BPMN diagram can be used to illustrate the order-to-cash process in a company. The diagram can show the different tasks involved in the workflow, such as order entry, invoicing, and payment processing. Data flow diagrams (DFDs) DFDs are used to represent how data flows through a system or process. These diagrams are particularly helpful when identifying data sources, storage, and transformations. Also, DFDs are quite useful for modeling complex systems that involve multiple data sources and transformations. For instance, a DFD can be used to explain the flow of data in a customer relationship management (CRM) system. The diagram can show how data flows from customer interactions to the CRM system, and how it is stored and used to inform business decisions. Try Wrike for free How to create effective workflow diagrams Creating an effective workflow diagram requires careful planning and attention to detail. In this section, we’ll explore some key steps to take when creating a workflow diagram that accurately reflects your process and is easy to understand. 1. Identify the scope Before you create a workflow diagram, determine the scope of the process you’re trying to document. This includes the boundaries of the process, what data is being used, and who the stakeholders are. By doing so, you’ll be able to create a diagram that accurately reflects the workflow and provides value to stakeholders. When diagramming a workflow for a customer service process, you’ll need to identify the different stages of the process. This involves initial contact, issue resolution, and follow-up. You’ll also need to determine the data that’s being used, such as customer information, issue details, and resolution status. Finally, you’ll need to identify the stakeholders involved, such as customers, customer service representatives, and managers. 2. Gather relevant information Once you’ve identified the scope, the next step is to gather relevant information about the process. This may involve speaking to stakeholders, gathering data, and documenting existing procedures. The goal is to create a more accurate and detailed workflow diagram. You may need to interview customer service representatives to understand how they handle different types of issues. You may also gather data on the average time it takes to resolve issues and the most common types of problems that arise, or document any existing procedures. 3. Choose the right diagram type When selecting a diagram type, it’s important to choose one that accurately reflects the process you’re documenting. Consider the level of detail required, who the audience is, and what the purpose of the diagram is when making your decision. If you’re creating a workflow diagram for a complex process with multiple decision points, you may want to use a BPMN diagram. This type of diagram uses standardized symbols and notations to represent different types of actions and decision points, making it easier to understand and analyze the process. 4. Use standard symbols and notations Standard symbols and notations make your diagram easily understandable and accessible for all team members and stakeholders. There are a number of established symbols and notations that are used in workflow diagrams, including those in BPMN diagrams. For example, while a rectangle is commonly used to represent a process step, a diamond typically stands for a decision point. 5. Ensure clarity and simplicity Finally, it’s important to make your diagram as clear and easy to understand as possible. Consider using a logical flow and avoiding too much detail or complexity. Focus on the key steps in the process and ensure that the connections between them are clear. You may want to use color coding or different line styles to symbolize different types of actions or decision points. Annotations or comments would also suffice to provide additional context or information about specific steps in the process. Whether you’re documenting a customer service process, manufacturing process, or any other type of process, it pays to create a well-designed workflow diagram that can help you identify inefficiencies and improve overall performance. How project management tools streamline workflow diagrams Project management tools assist teams in collaborating, sharing, and accessing visual representations of workflow diagrams. These tools provide a central platform for working together effectively. They enable real-time updates and version control, ensuring that everyone is on the same page and that changes to the workflow can be efficiently managed. Moreover, they often integrate task assignments, notifications, and progress tracking, simplifying the execution of each step in the workflow. Use Wrike as your workflow management software Wrike has proven to be an invaluable solution in the quest for efficient workflow management, particularly when it comes to implementing and visualizing workflow diagrams. Wrike helps users easily make, monitor, and enhance workflow diagrams with its user-friendly interface and numerous features. Its intuitive drag-and-drop functionality allows teams to design intricate diagrams with ease, ensuring that every step in their processes is clearly defined and organized. The real-time collaboration features enable teams to work seamlessly, whether they’re in the office or working remotely. Additionally, Wrike’s automation capabilities help streamline repetitive tasks, making workflows more efficient. Overall, Wrike can enhance workflow diagrams and drive productivity across the board. Conclusion Workflow diagrams are essential tools for effective process management, helping businesses streamline operations, reduce errors, and improve communication. Whichever diagram you choose, it’s important to select the right type for your needs and ensure that it accurately reflects the process you’re documenting. Empower your organization with intelligent workflow diagrams by harnessing the power of Wrike’s work management platform. Begin your free trial now and optimize workflows for elevated business performance. Try Wrike for free Note: This article was created with the assistance of an AI engine. It has been reviewed and revised by our team of experts to ensure accuracy and quality.

Get weekly updates in your inbox!
You are now subscribed to wrike news and updates.
Let us know what marketing emails you are interested in by updating your email preferences here .
Sorry, this content is unavailable due to your privacy settings. To view this content, click the “Cookie Preferences” button and accept Advertising Cookies there.

Lean Tools, Training, and Systems

Installation and Setup
Systems2win Training.
Lean Training
Microsoft Office Training
Scroll down to see the DFSS tools
What is Design for Six Sigma?
DFSS can be loosely defined as...
any systematic approach to design or re-design any product or service
While the target ratio of defects might be 6 sigma (or higher) ,
the design team can choose any other target quality ratio, (such as 1 defect per thousand opportunities, or 1 defect per 10,000 opportunities...)

Download free trial DFSS templates
Designing a product (or service) and a production process to produce such a high level of quality requires the design team to thoroughly understand:
- Customer desires (the spoken and unspoken Voice of the Customer)
- Features that fulfill (or conflict with) those desired (Critical To Quality CTQs)
- Design specifications for each feature (Target Performance Levels)
DFSS is the label used for just about any systematic attempt to understand those 3 things.
The most popular tools used for Design for Six Sigma are
the FMEA , and the House of Quality QFD
How does DFSS compare to DMAIC?
DMAIC is the acronym for the popular approach within the Six Sigma community
to apply the scientific method for process improvement (usually with an emphasis on quality improvement)
DFSS can be understood as an attempt to apply the DMAIC methodology to product and process design.
Unlike the rigidly structured 5 steps of DMAIC,
there are many (widely varying) approaches to product and process design, which all claim the label of DFSS.

Learn more about DMAIC , PDCA , and other ways to apply the scientific method .
Perhaps the most popular is DMAVD
(pronounced dah-mad-vee)
Define Measure Analyze Design Verify
In practice, the team will often add one more phase
to Optimize the design, which then becomes DMADOV
Your Systems2win templates come with an entire suite of DFSS templates
that your design team will find very useful when implementing any of the many popular approaches to Design for Six Sigma.
See packaging and pricing
To avoid confusing newcomers to lean six sigma,
the most complex DFSS tools have been split into an optional bundle of templates, but many of these tools are very simple to use,
and are therefore included among the Foundational Lean Toolkit (owned by every Systems2win user)
Design for Six Sigma tools
FMEA Failure Modes and Effects Analysis
This single FMEA template can be used for both:
DFMEA (during the Design phase)
PFMEA (to continuously improve the Process)
Use your FMEA template to anticipate problems, and to design processes and products to reduce risks
Download free trial FMEA template

FMEA template
Control Plan
To more carefully control the most severe or high-possibility risks
Learn more about the Control Plan template

Root Cause Analysis
also known as Cause and Effect Diagram, or Ishikawa Root Cause Analysis Fishbone Diagram
Your Systems2win templates give you the choice of several different types of Root Cause Analysis tools, to analyze different types of situations.
The fishbone template has a special feature that empowers you to click a button to import already-known causes from your FMEA so that your team has a helpful starting point to then brainstorm other potential risks and problems that should be included in your FMEA.
Download free trial Root Cause Analysis tools

Brainstorming & Affinity Group Tool
Six Sigma template to brainstorm ideas, then quickly organize them into affinity groups to stimulate even more ideas
Learn more about Brainstorming

Relations Diagram
also known as Thought Map Relations Diagram
To identify root causes of a complex, nonlinear problem.
(Use a Cause and Effect Fishbone Diagram to identify root causes of less complex, linear problems.)
Learn more about Relations Diagram

8D Problem Solving
also known as Corrective Action Report
To provide a systematic way for a team to resolve a problem that has uncertain root causes
in a way that systematically ensures that root causes have been identified and verified, and that permanent corrective actions are validated for effectiveness and instituted in a way that prevents the problem from ever recurring or escaping again.
It has been said that "an FMEA is an 8D waiting to happen". What if it does happen?

Corrective Action Request
also known as Supplier Corrective Action
The Supplier Corrective Action Report template does not pre-suppose that all of the rigid formality of the 8D process will be required. This simple Word template is structured as a one-page letter that simply requests the supplier to deal with a non-conformance issue.

Corrective Action
SIPOC Diagram
Use your SIPOC template to identify and eliminate wastes of any kind: hazardous wastes and emissions, scrap, energy, packaging...
Download free trial SIPOC template

Process Flow Diagram
Before creating a PFMEA — use the Process Flow Diagram to identify Sources of Variation, and desired Deliverables (ideal Functions) for each Process Step.

aka Parameter Diagram
Before creating an FMEA — use the p diagram to analyze Inputs and Outputs and Noise Factors and Control Factors that can affect performance of desired Ideal Functions, and minimize Error States.

P-Diagram template
Interface Matrix
Before creating a DFMEA — use the Interface Matrix to identify and clarify interfaces between environment, systems, sub-systems, and components that are beneficial or detrimental to functionality.
Also provides P-Diagram input/outputs and noise factors

Function/Requirements worksheet
aka Item/Function worksheet
Before completing the Function and Requirements columns of the FMEA form, use this Function/Requirements worksheet to identify and clarify Functions and corresponding Requirements.

Characteristic Matrix
aka Product Characteristics Matrix
When creating a PFMEA — identify process steps that can compromise characteristics of the product or service that are noticeable and important to the customer.

Design Verification Plan and Report
aka DVP&R, DDVPs, DVPR
Formalized testing of product or service to ensure compliance with all requirements.

House of Quality Quality Functional Deployment Matrix
One of the most sophisticated quality improvement tools to provide a guiding structure for a cross-functional product development team to rapidly design and deploy new products and services
Download free trial QFD template

House of Quality template
Cause and Effect Matrix
A simpler quality improvement tool than the QFD, with a similar objective:
To identify the few process input variables that provide the greatest opportunity to improve the key process outputs

Customer Segmentation Worksheet
Quality improvement template to identify and focus attention upon the sub-segments of customers that generate the most value from each product or service

Voice of the Customer Data Collection Worksheet
To plan and manage the collection of Six Sigma customer data from existing company data, listening posts, surveys, interviews, point-of-use observation, and more
Learn more about Voice of the Customer templates

Voice of the Customer Requirements Translation and Kano Analysis
Quality control template to translate potentially vague customer comments into measurable functional requirements, thereby strengthening your team's ability to design and deliver products and services that truly delight your customers

Tool Selection Matrix
Use your Tool Selection Matrix (1ToolSelection.xlsx) to choose the right tool,
and to see which tools are split into the DFSS Tools bundle, and which tools come with the Foundational Tools
Download free trial Tool Selection Matrix

These same DFSS tools are used for Design for Six Sigma, Design for Manufacturability, Design for Lean Manufacturing, and DMADV.

Your DFSS tools also come with many other useful tools for Lean Six Sigma
to empower every team member

Why re-invent?
One huge benefit of owning your Systems2win templates is Support when you need it
Consider Training and Coaching to support your teams to succeed
Schedule a conference to discuss your challenges with an experienced lean advisor

No, we're not going to buy you any tools...
but we don't want any excuses when those deadlines are due
If your organization has not yet provided a license, own yours now
Are you on your phone?
After you sign up for the newsletter , the first email that you receive will remind you to forward that email to your Windows computer, where you can then download and install your free trial and gift templates
Search results for
Affiliate links on Android Authority may earn us a commission. Learn more.
T-Mobile employees get AI superpowers to ‘predict’ and solve your problems
Published on April 29, 2024
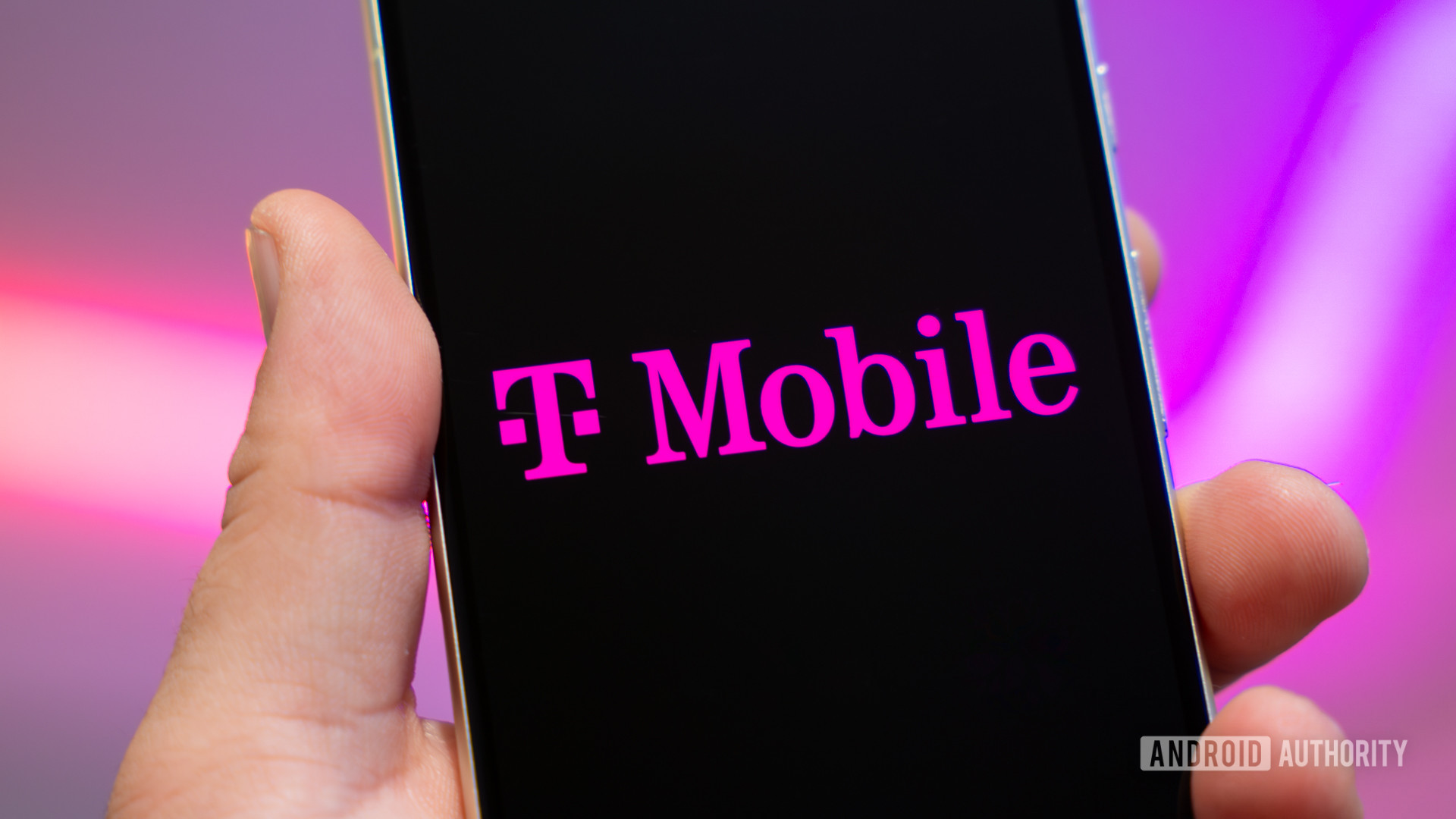
- T-Mobile is launching a set of AI-powered tools called Superpowers to improve customer-employee interactions.
- Tools like GenAI Chat act as an internal expert for employees, while Promo Genius helps find the most suitable promotions for customers.
- T-Mobile will also begin using predictive tools to anticipate customer needs and potential concerns.
T-Mobile is rolling out some impressive AI-powered tools, hoping to transform customer service within its retail and care channels. Internal documents obtained by The Mobile Report have revealed T-Mobile’s Superpowers project, which uses three core tools to streamline support for both retail stores and customer care channels.
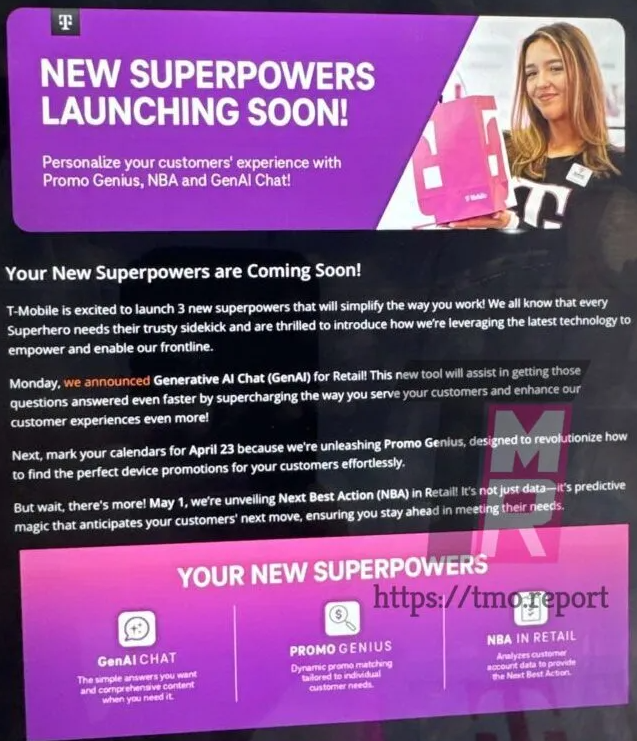
- GenAI Chat: Think of it as T-Mobile’s own ChatGPT, an always-available expert that can sift through T-Mobile’s vast internal knowledge base resources and help employees who need quick, accurate answers to complex questions and support them during difficult customer conversations.
- Promo Genius: This tool tackles the challenges of matching the perfect promotion to a customer’s needs. It uses dynamic filters to pinpoint the most relevant and value-focused promotions quickly.
- Next Best Action (NBA) in Retail: Probably the most impressive feature is the NBA, which is set to debut on May 1. As the name suggests, this system will provide real-time, personalized recommendations for the next best action during a customer interaction, fueled by vast amounts of data points about the customers.
The publication also came across a now-deleted Reddit thread that gave a glimpse into how some employees feel about these new AI tools. While some were excited about the potential to compare device specs easily, others bemoaned outdated information and clunky prompt requirements. Some users also raised concerns about AI being used for employee feedback, suggesting a distrust in whether the technology can replace the nuance of human leadership.
The future of customer service
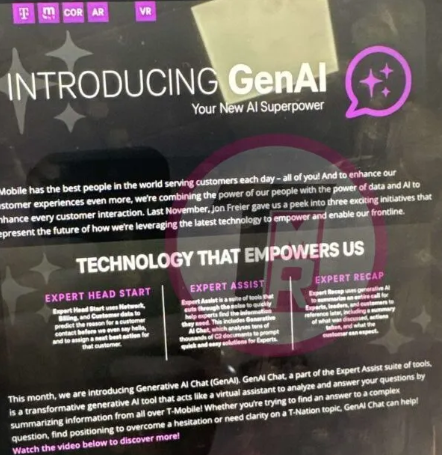
T-Mobile’s Superpowers project could be the foundation of a radically automated future for the company and the industry in general. The above image obtained by The Mobile Report reveals further automation initiatives by T-Mobile, such as Expert Head Start and Expert Recap.
Expert Head Start is the name of the company’s predictive system, which would tap into “network, billing, and customer data” ( possibly including data collected from T-Mobile’s controversial customer profiling feature ) to predict why someone is reaching out.
It would then proactively suggest the ‘next best action,’ arming employees before the conversation even begins. If executed without rigorous data anonymization, this could raise some privacy concerns as it blurs the boundaries between personalized service and potential data overreach.
Expert Recap would use the power of generative AI to summarize entire calls and chat conversations automatically. Employees, managers, and even customers would have an easily digestible reference point detailing the discussion, actions taken, and what to expect next.
These tools point to a future where AI isn’t just a support assistant for T-Mobile employees — it could become the driving force behind customer interactions. In the short term, customers may benefit from smoother interactions, better-matched promotions, and more informed support. As for the long-term impact of relying so heavily on AI, well, we’ll probably find out soon enough.
Is T-Mobile’s embrace of AI a step forward for customer service or a worrisome trend? Share your thoughts in the comments.
You might like
- Guide: DMAIC Tools
Daniel Croft
Daniel Croft is an experienced continuous improvement manager with a Lean Six Sigma Black Belt and a Bachelor's degree in Business Management. With more than ten years of experience applying his skills across various industries, Daniel specializes in optimizing processes and improving efficiency. His approach combines practical experience with a deep understanding of business fundamentals to drive meaningful change.
- Last Updated: February 29, 2024
- Learn Lean Sigma
Process improvement requires a structured, systematic approach to ensure success. DMAIC, standing for Define, Measure, Analyze, Improve, and Control, offers such a framework, integral to Six Sigma and widely applicable across various industries for enhancing operational efficiency and quality. This guide delves into the DMAIC methodology, explaining the tools and strategies pertinent to each phase. From initial problem identification to the sustainable implementation of solutions, the following sections will guide you through the path to achieving measurable, lasting improvements in your organization’s processes.
Table of Contents
What is dmaic.
The DMAIC methodology is a data-driven quality strategy used to improve processes. It is an integral part of Six Sigma but is also used independently in process improvement efforts. DMAIC stands for Define, Measure, Analyze, Improve, and Control. Each phase has specific objectives and tools designed to achieve these objectives. This guide will explore the tools used at each stage of the DMAIC process to provide a clear understanding of how to effectively implement process improvements.
Define Phase in DMAIC
The Define phase is the foundational pillar in the DMAIC methodology, setting the basis for all subsequent efforts in process improvement. This phase is important for aligning the project with business objectives and customer expectations. Let’s go deeper into the objective of the Define phase and examine the tools used to achieve its goals.
The objective of the Define phase is to establish a clear, comprehensive understanding of the project at hand. This involves identifying the specific problem or opportunity for improvement, understanding the needs and expectations of customers, and setting achievable goals that align with both customer expectations and business objectives. The Define phase ensures that the project team, stakeholders, and anyone else involved have a shared understanding of what the project aims to accomplish, thereby setting a clear direction for all subsequent phases of the DMAIC process.
To achieve the objectives laid out in the Define phase, several key tools are employed, each serving a specific purpose in laying the groundwork for successful project execution:
Project Charter
The Project Charter is akin to a project’s constitution. It is a document that formally outlines the project’s scope, objectives, and participants. The charter serves multiple purposes: it provides a high-level overview of the project for stakeholders , it acts as a contract between the project team and the organization’s leadership, and it serves as a constant reference point for the project’s goals and boundaries. By clearly defining what is in and out of scope, the Project Charter helps prevent project scope creep and ensures that all team members are aligned on the project’s objectives.
Take a look at our Project Charter template to help you get started.
SIPOC Diagrams
SIPOC Diagrams are a tool used to map out the high-level view of a process, illustrating the Suppliers, Inputs, Process, Outputs, and Customers involved. This visual tool is instrumental in the early stages of a project because it helps the team and stakeholders understand the current state of the process at a glance. By identifying these key components, SIPOC diagrams facilitate a common understanding among all project participants, ensuring that everyone has the same baseline knowledge of the process being improved. This tool is especially useful for identifying critical areas of focus and potential areas where problems may arise.
Voice of the Customer (VOC)
Voice of the Customer (VOC) techniques are used to capture and understand customer requirements, needs, and expectations. VOC can be gathered through various means, including surveys, interviews, focus groups, and feedback forms. The essence of VOC is to ensure that the project’s objectives are closely aligned with what the customers value most. It is a critical component in defining the problem because it shifts the perspective from internal process metrics to customer impact. Understanding the VOC helps the project team prioritize improvements based on what will have the most significant effect on customer satisfaction and loyalty.
Process map of the voice of the customer
Measure Phase in DMAIC
The Measure phase is a critical step in the DMAIC process that builds directly on the foundation established in the Define phase. It transitions the project from the conceptual understanding of problems and requirements to a quantitative analysis of the current process. This phase is where data takes center stage, offering insights into the process’s performance and laying the groundwork for targeted improvements. Let’s explore the objective of the Measure phase and the key tools used to achieve its goals.
The primary objective of the Measure phase is to accurately quantify the current state of the process being improved. This involves collecting data on key performance indicators (KPIs) to establish a baseline measurement. The aim is to measure the extent of the problem identified during the Define phase, using data to understand the current process capability. This quantitative understanding is crucial for identifying the gap between the current process performance and the desired state, setting the stage for focused analysis and improvement in subsequent phases. It ensures that any decisions made are data-driven and grounded in the reality of the process’s current state.
To achieve the objectives of the Measure phase, several specific tools are utilized, each facilitating a different aspect of the data collection and analysis process:
Data Collection Tools
Data collection tools such as check sheets, data capture forms, and software tools are essential for gathering accurate and relevant data efficiently. Check sheets are simple yet powerful tools for collecting data on the frequency of specific events or problems. Data capture forms are designed to gather more detailed information in a structured format, ensuring consistency and accuracy in data collection. Software tools can automate data collection processes, providing real-time data capture and storage capabilities. These tools are the backbone of the Measure phase, ensuring that the data collected is reliable, relevant, and sufficient for analysis.
Process Mapping
While SIPOC diagrams provide a high-level overview, detailed process mapping dives deeper into each step of the process. This tool visually represents every action, decision, and delay in the process, offering a comprehensive view of the current state. Detailed process maps are invaluable for identifying variations, inefficiencies, and bottlenecks within the process. They serve as a visual aid that enhances understanding among team members and stakeholders, facilitating a more targeted and effective approach to data collection and analysis.
Detailed sub process map
Statistical Software
Statistical software tools like Minitab , JMP, or R are employed to analyze the data collected. These tools offer powerful capabilities for understanding data patterns, variations, and the process’s initial capability. Through descriptive statistics, process capability analysis, and graphical representations, statistical software helps in identifying trends, outliers, and areas of concern. This analysis provides a quantitative foundation for the Analyze phase, where data-driven insights guide the identification of root causes.
As a free option we have developed some statistical analysis tools in our tools section of the website.
Analyze Phase in DMAIC
The Analyze phase is a critical juncture in the DMAIC methodology, marking the transition from understanding the problem to actively seeking its root causes. This phase is where the gathered data from the Measure phase is scrutinized to uncover the underlying reasons for process deficiencies. Let’s explore the objective of the Analyze phase and the tools that play pivotal roles in achieving its aims.
The primary objective of the Analyze phase is to identify the root causes of defects or inefficiencies within the process. This phase is dedicated to digging beneath the surface of observable symptoms to discover the fundamental reasons for process problems. By accurately identifying the root causes, organizations can ensure that the solutions they implement in the Improve phase are targeted and effective, rather than merely addressing symptoms. The Analyze phase is crucial for ensuring that efforts are focused on changes that will have a meaningful impact on process performance and customer satisfaction.
Several analytical tools are employed during the Analyze phase, each designed to facilitate a deeper understanding of the process problems. These tools help in systematically breaking down the data and issues to uncover the root causes:
Cause-and-Effect Diagrams (Ishikawa or Fishbone)
The Cause-and-Effect Diagram, also known as the Ishikawa or Fishbone diagram , is a visual tool used to systematically explore potential causes of a specific problem. The diagram resembles a fish’s skeleton, with the problem at the head and the potential causes branching off the spine into categories such as Materials, Methods, Machines, People, Environment, and Measurement. This tool is particularly useful for team brainstorming sessions, as it encourages the exploration of all possible sources of variation or defects, categorizing them in a manner that is easy to understand and analyze further.
The Five Whys technique is a straightforward but powerful tool for root cause analysis. It involves asking “Why?” repeatedly (typically five times) to peel away the layers of symptoms and get to the core of the problem. Each answer forms the basis of the next “Why?” question. This method is effective because it promotes a deeper investigation into the process issues and helps avoid the trap of addressing superficial symptoms instead of the underlying causes. The simplicity of the Five Whys makes it accessible for teams of all levels of expertise, fostering a culture of inquiry and continuous improvement.
Hypothesis Testing
Hypothesis Testing is a statistical approach used to determine the likelihood that a given hypothesis about a process or data set is true. This tool is invaluable in the Analyze phase for validating or disproving assumptions made about the root causes of problems. By applying statistical tests, such as t-tests, chi-square tests , or ANOVA , teams can objectively evaluate the evidence for or against potential root causes, based on the data collected. Hypothesis testing helps in making informed decisions about which factors are truly contributing to process variations or defects, ensuring that improvements are data-driven.
Improve Phase in DMAIC
The Improve phase is a critical stage in the DMAIC methodology, where the insights and root causes identified in the Analyze phase are translated into actionable solutions. The focus shifts from understanding the problem to implementing changes that lead to substantial improvements in process performance. This phase is about innovation, experimentation, and optimization, with the ultimate goal of enhancing quality, efficiency, and customer satisfaction. Let’s delve into the objective of the Improve phase and the strategic tools employed to achieve successful outcomes.
The main objective of the Improve phase is to develop and deploy solutions that address the root causes of deficiencies identified earlier in the DMAIC process. This involves designing innovative changes to the process, testing these changes to ensure they produce the desired outcomes, and then implementing the changes in a way that results in significant performance improvements. The challenge in this phase is not only to find solutions that solve the identified problems but also to ensure that these solutions are sustainable and do not introduce new issues into the process.
A variety of tools and techniques are used in the Improve phase to facilitate effective solution development and implementation:
Pilot Studies
Pilot studies are small-scale experiments or trials conducted to evaluate the feasibility, duration, cost, risk, and adverse effects of an improvement solution before it is rolled out on a larger scale. This approach allows teams to test the impact of changes in a controlled environment, minimizing risk and allowing for adjustments before full implementation. Pilot studies provide valuable insights into how a solution performs in the real world and can help identify potential issues or resistance that may not have been evident during the planning stages.
Design of Experiments (DOE)
Design of Experiments (DOE) is a statistical method that allows teams to systematically and efficiently explore the relationships between multiple input variables and their impact on output variables. This tool is invaluable for optimizing processes because it can identify the combination of factors that lead to the best possible outcome. DOE helps in understanding the interaction between variables, thereby enabling the development of solutions that are robust and optimized for performance. By using DOE, teams can ensure that improvements are based on empirical evidence and statistical rigor, leading to more effective and predictable process enhancements.
Lean tools, such as 5S (Sort, Set in order, Shine, Standardize, Sustain), Kanban (visual signal or card), and Value Stream Mapping (VSM) , are employed to streamline processes, eliminate waste, and enhance flow. These tools are grounded in the principles of Lean management, which focuses on maximizing value for the customer while minimizing waste. 5S is used to create organized workspaces that improve efficiency and quality. Kanban helps in managing workflow and inventory with visual cues, ensuring that work progresses smoothly without bottlenecks . Value Stream Mapping is a tool for visualizing the flow of materials and information as a product or service makes its way through the value stream, highlighting areas of waste and opportunities for improvement. By applying these Lean tools, teams can make significant strides in improving process performance, reducing cycle times, and increasing customer satisfaction.
Control Phase in DMAIC
The Control phase is the final, yet perpetually critical phase of the DMAIC methodology. It is where the improvements made in the previous phases are solidified into the standard operating procedure, ensuring the longevity and sustainability of these gains. The primary focus shifts to monitoring and controlling the process to prevent regression, maintaining the enhanced performance levels over time. Let’s delve into the objective of the Control phase and examine the tools that are essential for its successful execution.
The main objective of the Control phase is to ensure that the improvements and changes implemented during the Improve phase are maintained and that the process does not revert to its previous state. This phase is about embedding the new practices into the daily operations of the organization, ensuring that the process continues to operate at its new, improved level of performance. It involves close monitoring of the process to quickly identify and correct any deviations from the target performance. The Control phase is critical for realizing the long-term benefits of the DMAIC project, making the improvements truly sustainable.
To achieve the objective of the Control phase, several key tools are employed, each designed to facilitate effective monitoring, controlling, and documentation of process performance:
Statistical Process Control (SPC)
Statistical Process Control (SPC) is a method of using statistical tools and control charts to monitor and control a process. SPC charts are invaluable for identifying when a process is behaving as expected or when it has deviated from set parameters, signaling the need for intervention. These charts can monitor various aspects of process performance, such as mean, range, and defects, providing real-time data that helps in maintaining process stability. SPC is a cornerstone of the Control phase, enabling ongoing oversight of the process and ensuring that improvements are sustained over time.
Control Plans
Control Plans are comprehensive documents that outline the specific practices, metrics, and processes that need to be followed to maintain the improvements achieved. They detail the control points, specifications, and monitoring activities required to ensure that the process remains under control. Control Plans serve as a blueprint for process management post-improvement, guiding the daily activities of process operators and ensuring that everyone involved is aware of their roles in maintaining process performance. These plans are dynamic documents that may be updated as processes evolve or as new improvements are made.
Standard Operating Procedures (SOPs)
Standard Operating Procedures (SOPs) are updated to reflect the changes made during the Improve phase, ensuring that the new, more efficient processes are clearly documented. These documents provide step-by-step instructions on how to perform process tasks, ensuring consistency and quality in the execution of these tasks. By updating the SOPs, the organization ensures that the process changes are formally communicated to all stakeholders, embedding the improvements into the regular workflow. SOPs are essential for standardization, training new staff, and serving as a reference for process activities, contributing to the sustainability of improvements.
Example of Standard Work Instructions
By systematically applying these tools at each stage of the DMAIC process, organizations can effectively address and solve problems, leading to significant improvements in process quality, efficiency, and customer satisfaction. The key to successful DMAIC implementation is not just in using these tools but in understanding the interconnectivity between phases and how each tool contributes to a holistic improvement strategy.
- Berardinelli, C.F., 2012. TO DMAIC or not to DMAIC? . Quality Progress , 45 (11), p.72.
- De Mast, J. and Lokkerbol, J., 2012. An analysis of the Six Sigma DMAIC method from the perspective of problem solving. International Journal of Production Economics , 139 (2), pp.604-614.
Q: What is DMAIC and why is it important in process improvement?
A: DMAIC stands for Define, Measure, Analyze, Improve, and Control. It is a data-driven quality strategy used for improving, optimizing, and stabilizing business processes and designs. DMAIC is important because it provides a structured, systematic approach to problem-solving, which helps organizations identify and address inefficiencies, reduce defects, and improve overall quality, leading to enhanced customer satisfaction and operational excellence.
Q: Can DMAIC be used outside of manufacturing environments?
A: Yes, DMAIC can be applied in various sectors beyond manufacturing, including services, healthcare, finance, and IT. The methodology is versatile and can be adapted to any process or industry where there is a need to improve efficiency, reduce waste, or solve problems related to quality and process performance.
Q: How does the Define phase set the stage for the rest of the DMAIC process?
A: The Define phase sets the foundation for a DMAIC project by clearly identifying the problem, project goals, and scope. It involves understanding customer requirements and establishing clear objectives for the improvement effort. This phase ensures that all team members and stakeholders have a shared understanding of the project’s purpose and scope, which is crucial for guiding the project’s direction and focus throughout the subsequent phases.
Q: In the Measure phase, how do you ensure data collected is reliable and accurate?
A: To ensure data reliability and accuracy in the Measure phase, it’s important to define data collection methods and tools clearly, train team members on these methods, and use standardized procedures for data collection. Validating the measurement system itself through techniques like gauge R&R (Repeatability and Reproducibility) can also help ensure that the data collected reflects the true performance of the process being analyzed.
Q: What makes the Control phase critical to the DMAIC process?
A: The Control phase is critical because it ensures that the improvements made during the Improve phase are sustained over time. Without effective control measures, processes may drift back to their original state, negating the improvements achieved. By implementing tools like SPC charts, Control Plans, and updated SOPs, organizations can monitor process performance, make adjustments as necessary, and embed the improvements into daily operations, ensuring lasting benefits from the DMAIC project.
Daniel Croft is a seasoned continuous improvement manager with a Black Belt in Lean Six Sigma. With over 10 years of real-world application experience across diverse sectors, Daniel has a passion for optimizing processes and fostering a culture of efficiency. He's not just a practitioner but also an avid learner, constantly seeking to expand his knowledge. Outside of his professional life, Daniel has a keen Investing, statistics and knowledge-sharing, which led him to create the website learnleansigma.com, a platform dedicated to Lean Six Sigma and process improvement insights.
Free Lean Six Sigma Templates
Improve your Lean Six Sigma projects with our free templates. They're designed to make implementation and management easier, helping you achieve better results.
Other Guides

- About Amazon (English)
- About Amazon (日本語)
- About Amazon (Français)
- About Amazon (Deutsch)
- Newsroom (Deutsch)
- About Amazon (Italiano)
- About Amazon (Polski)
- About Amazon (Español)
- Press Center (English)
- About Amazon (Português)
I’m an AWS developer. Here are 3 ways I’m using Amazon Q, a generative AI-powered assistant, to work more efficiently.
- Facebook Share
- Twitter Share
- LinkedIn Share
- Email Share
- Copy Link copied
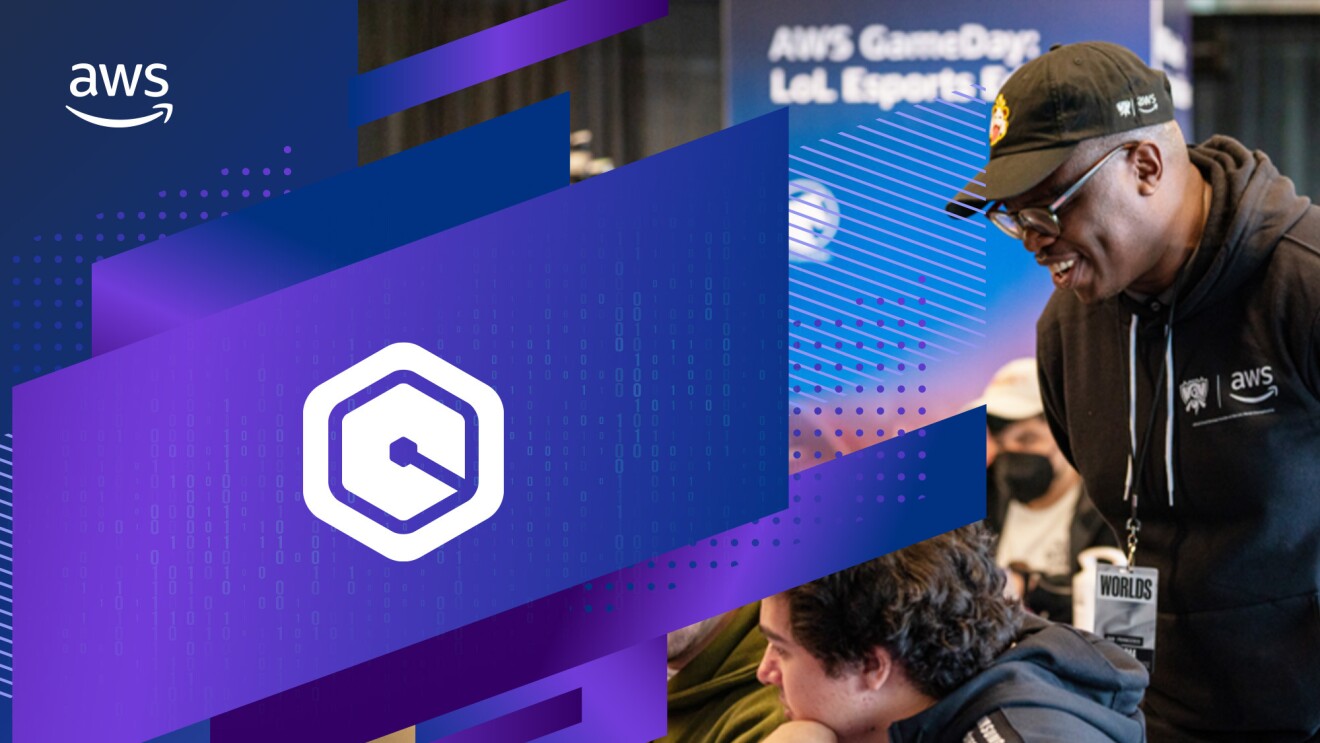
I’ve been interested in software engineering ever since I got hooked on video games as a kid. I studied computer science in college at the University of Maryland, which was hard work. I didn’t really get it at first—until I built first my first app and saw how much creativity was involved in the process.
I went on to work for more than 10 years as a software engineer, initially coding for government contractors and later running cloud infrastructure and data analytics platforms for technology companies.
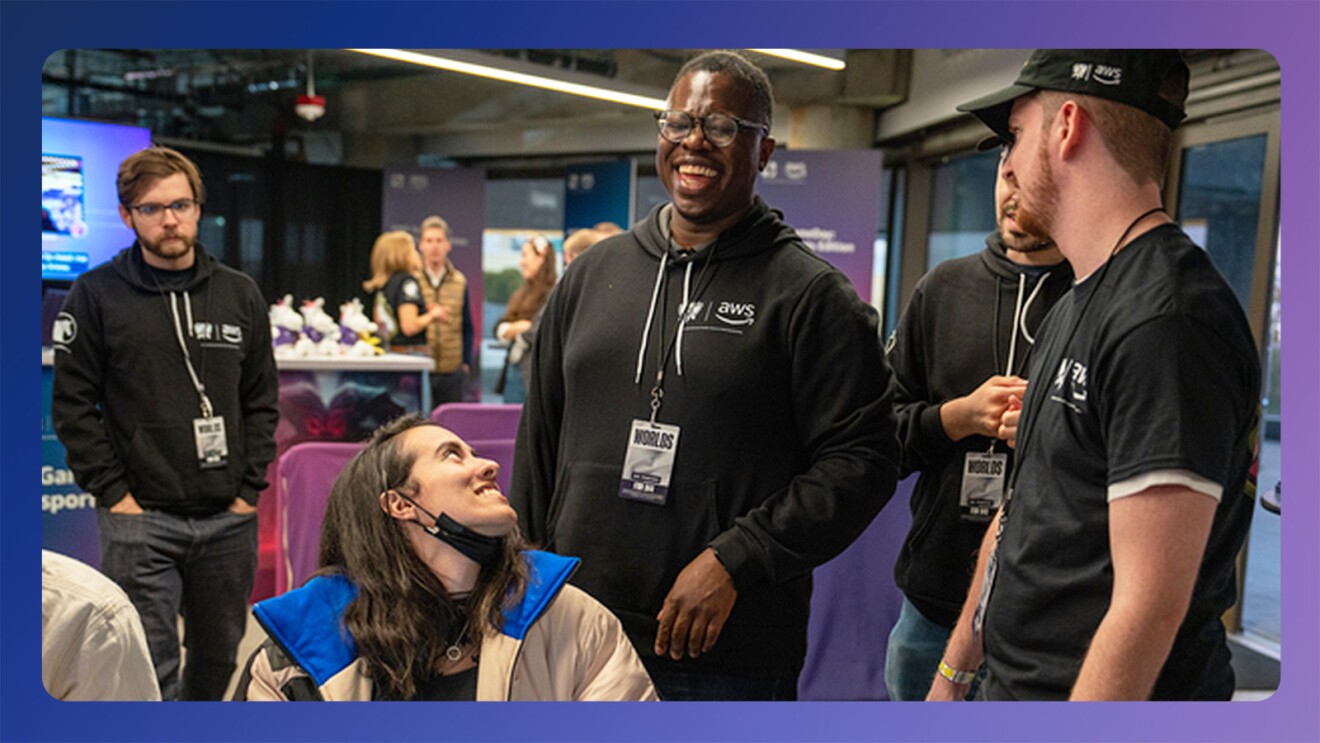
These days, I work at Amazon Web Services (AWS) as what’s known as a developer advocate—it’s a role that allows me to connect with other engineers help them learn about AWS tools. I spend much of my time sharing my knowledge at workshops , meetups , and AWS Community Day events .
Additionally, I do a lot of my own experimenting, building with AWS’s latest tools and creating real-world applications for the newest generative AI tools that we are building on AWS.
One tool I’ve been using recently is Amazon Q , which AWS just announced is now generally available. It’s a generative artificial intelligence-powered assistant that’s designed to revolutionize the future of work for employees across every organization and department.
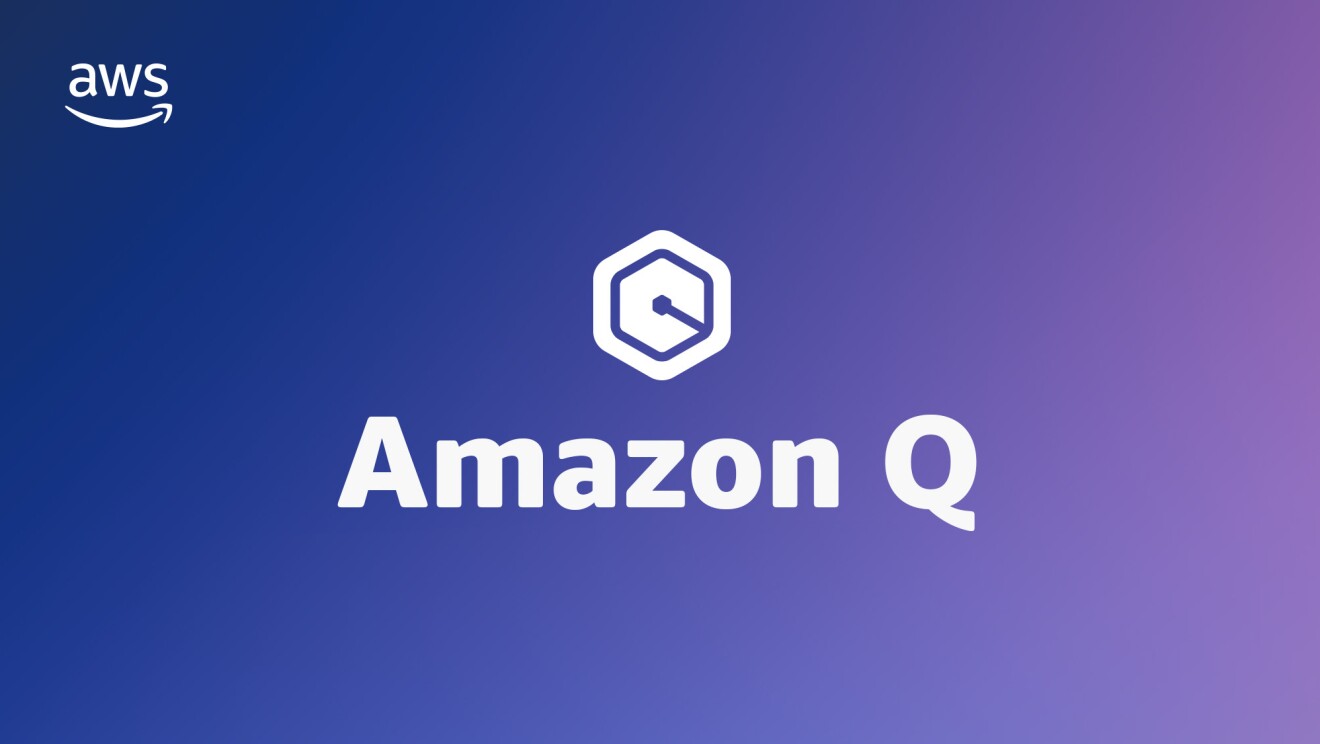
When Amazon Q was first previewed at re:Invent last year, I knew I needed to give it a try. Using generative AI, it can give you fast answers to questions, solve problems, and generate content.
It’s useful for more than just developers like me, of course. IT professionals and business users of all kinds use Amazon Q to extract relevant information to streamline tasks and speed up decision-making.
I think this is one of the best generative AI tools that can help to spark creativity and innovation at work.
Here are three ways I’ve been using Amazon Q to do just that:
I’m a big fan of the Slay the Spire video game, where the goal is to ascend a spire of multiple floors while battling enemies. Recently, I decided I wanted to build a large language model (LLM) bot that would be able to play the game by itself.
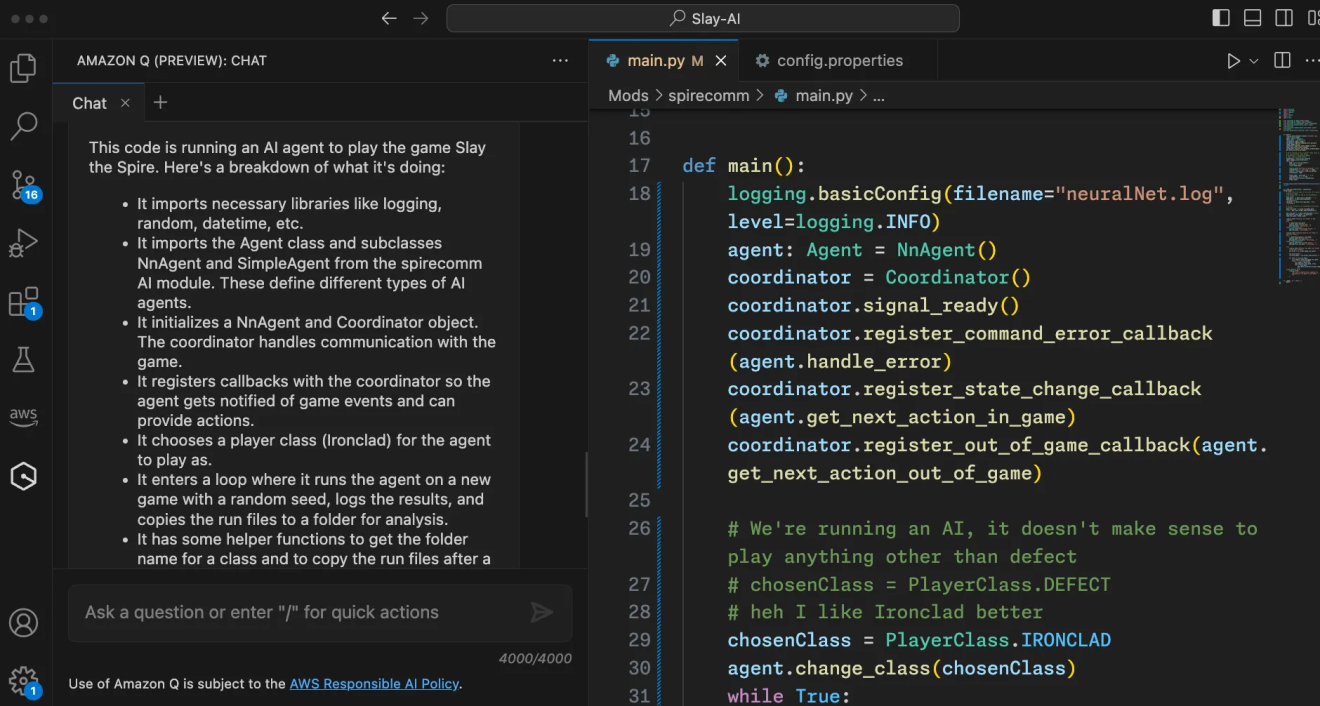
I was able to find a five-year-old codebase (the body of source code for a given game or application) that could help me do this, but it was lacking documentation and it had bugs.
In just three hours I was able to use Amazon Q to help me understand code, allowing me to generate my own code and debug issues as they arose to build my bot. Without the help of this assistant, it would have taken me a day or two to do this work, not just a few hours. Here's the play-by-play of how I did that.
If you code as often as I do, it’s inevitable that you’ll make a mistake or encounter an error as you build.
When you’re building applications, you may not know how to use all the capabilities that are available to you. If I have a question on how to do something, I use Amazon Q to guide me on how to do a specific task.
Sometimes I talk to engineers who don’t know where to begin, or are afraid to touch things because there are so many possibilities. Amazon Q can provide assistance and guide you on how to take advantage of all the capabilities of the console, using something as simple as a natural language prompt.
When building workshops, it's common to include exercises that involve querying data. SQL (a language for database creation and calculations) is often used for this purpose. While SQL is powerful, it can be challenging for developers to remember the correct syntax, keywords, and database names.
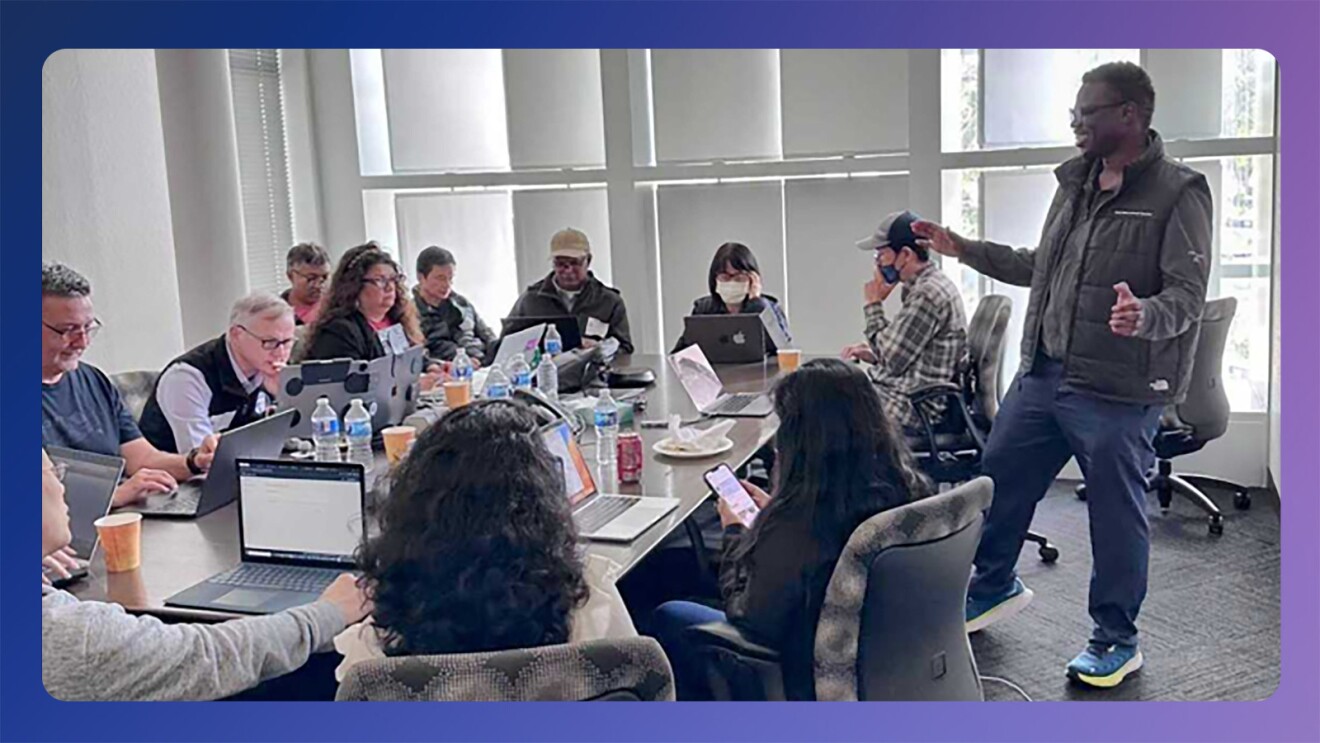
When I was building a workshop recently, one of the modules focused on writing SQL queries to analyze user engagement with different products. I wanted to show developers how much easier it is to use Amazon Q for this task instead of writing the queries from scratch.
If you're a seasoned SQL developer, you could write that query easily. But with Q, developers could ask that question in simple, natural language, and see it return the answer they needed.
I’m excited to see how Amazon Q will continue to evolve. I know it has many capabilities that can be used in helping build solutions, and I’m looking forward to using it in more parts of the software development life cycle—from feature development to code transformation.
Learn more about how to build with Amazon Q and how to engage with the AWS Community:
- AWS Workshops
- AWS Developers YouTube
- AWS User Groups
- AWS Community Days discussions
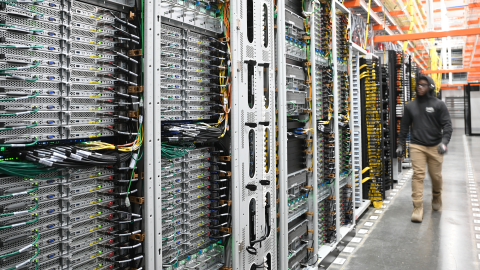
AWS plans to invest $11 billion in Indiana, the largest capital investment in the state's history
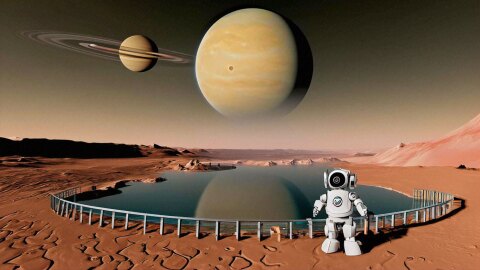
New additions to Amazon Bedrock make it easier and faster than ever to build generative AI applications securely
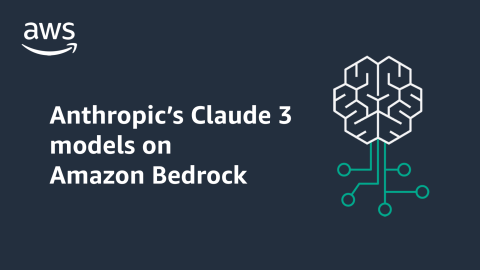
Access to the most powerful Anthropic AI models begins today on Amazon Bedrock
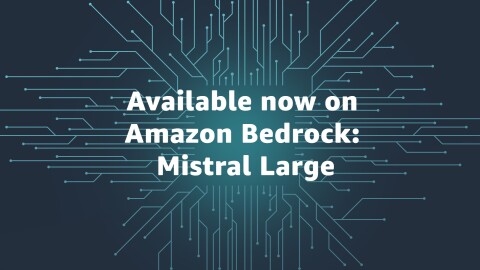
Amazon Bedrock customers have more choice in AI models with Mistral Large now available
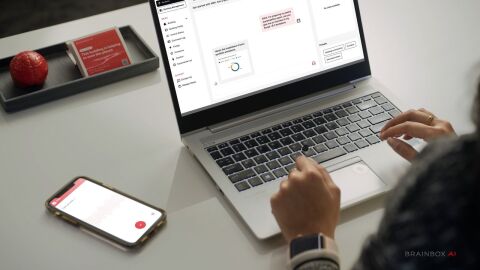
A new virtual AI assistant built on Amazon Bedrock can reduce the carbon footprint of commercial buildings. Here’s how.
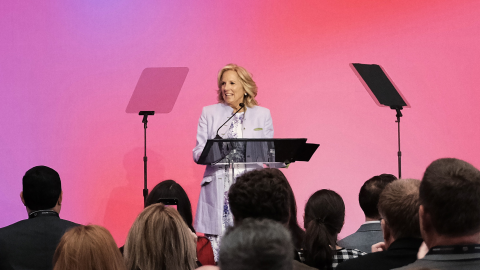
First Lady Jill Biden discusses health and innovation at AWS IMAGINE: Nonprofit conference
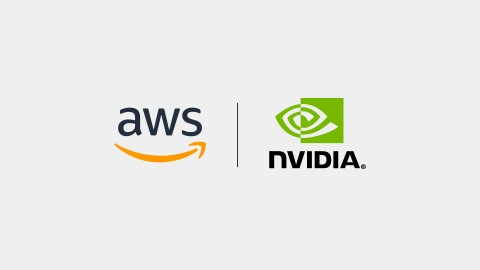
AWS and NVIDIA extend their collaboration to advance generative AI
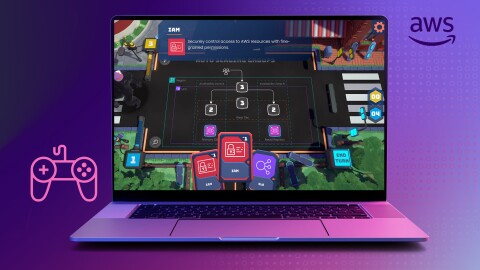
AWS offers 5 game-based training experiences to power up your cloud skills
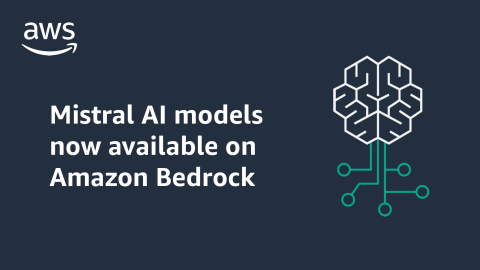
Amazon Bedrock adds Mistral AI models, giving customers more choice

IMAGES
VIDEO
COMMENTS
Whether you're a seasoned Six Sigma Black Belt or new to the world of continuous improvement, this guide will equip you with the knowledge and tools to make data-driven decisions confidently. So, let's embark on this journey to master DMADV and elevate your approach to problem-solving and design.
The key difference between DMADV and DMAIC (Define, Measure, Analyze, Improve, Control) lies in their application: DMADV is used for creating new solutions or making major redesigns, focusing on innovation and design from scratch, while DMAIC is applied to existing processes, focusing on incremental improvements and problem-solving.
The DMADV methodology (Define, Measure, Analyze, Design, Verify) is a crucial component of the Design for Six Sigma framework.DMADV helps organizations create new processes, products, or services that meet customer requirements and performance expectations. In this post, we will explore five key tools for each stage of the DMADV approach, providing a comprehensive toolkit to guide you through ...
STAGE 1: DEFINE. The primary goal of the Define stage is to clearly determine and understand your goal for the project. You likely began using the DMADV approach because there was either a new customer request, a business problem, or a new market opening that requires you to design a new product or process.
Overview of DMADV Methodology. Another problem-solving methodology used in Six Sigma and other process improvement initiatives is DMADV. DMADV is an acronym that stands for Define, Measure, Analyze, Design, and Verify. DMADV is a methodical approach to developing a new process, product, or service that meets or exceeds customer expectations.
DMADV stands for Define, Measure, Analyze, Design, and Verify, which are the five phases that make up this framework. It is primarily used for designing and implementing new processes or products that meet customer requirements and achieve the highest level of quality. Unlike other improvement methodologies like DMAIC (Define, Measure, Analyze ...
The structured problem-solving methodology of DMADV Six Sigma has several advantages. Here is a list of them: ... Using DMADV tools, retailers can determine the actual requirements for the inventory management system, measure its current state, analyze alternative system designs, develop the new system, and verify its performance through ...
Then, DMADV is the tool of choice. The graphic below shows the steps of the DMADV process. DMADV. DMADV is a Design For Six Sigma (DFSS) method that focuses on customers. The DMADV (Define-Measure-Analyze-Design-Validate/Verify) method aims to design a new process or product, or to redesign a problematic process or product.
Six Sigma has been helping companies meet their project goals and deadlines since 1986, when Motorola was first introduced. Within Six Sigma, various methodologies can be used for problem-solving and process improvement. And one of them is DMADV, the other one being DMAIC. Most people are familiar with DMAIC but not with DMADV. In this article, learn everything you need to know about the DMADV ...
In conclusion, DMADV is a structured problem-solving methodology to improve processes, products, and services. The five steps of DMADV - Define, Measure, Analyze, Design, and Verify - provide a structured approach to problem-solving and help organizations deliver high-quality products and services that meet the needs of their customers.
Similarities of DMAIC and DMADV. Both DMAIC and DMADV: Use structured methods to reduce variation and solve problems; Collect and analyze data to make informed decisions; Use teams to solve problems; Have a customer focus; Use many of the same tools (brainstorming, FMEA, DOE)
DMADV process is a Six Sigma method. Six Sigma is about process improvement as part of quality management. Existing products and/or services are improved using analytical techniques and statistics. Six Sigma focuses on reducing variability in matters that are perceived as Critical to Quality (CTQ) by the customer. These CTQs are very important and vital to quality; it is about the internal ...
Once you have a project focus, you begin to identify and define the problem to solve. For more information on this journey, check out DMAIC Tools and Techniques: The Define Phase. Whether you are using DMAIC or DMADV, the real benefit of these methodologies is that they provide structured problem-solving to ensure success.
DMADV and DMAIC are two tools adopted for same mission/vision: Achieve Six Sigma Performance; Two different approaches and methodology used to attain a single goal under different circumstances and problem areas. Table 2: DMAIC Vs DMADV. But the objective of both DMADV and DMAIC is the same: a) Variation reduction and b) Adherence to customer ...
Tools Used by DMADV: Quality Function Deployment (QFD): QFD is a tool used to translate customer requirements into specific product or process features. It ensures that the design aligns with customer needs. ... TRIZ (Theory of Inventive Problem Solving): TRIZ is a systematic approach for creative problem-solving and innovation. It encourages ...
DMAIC is an acronym that stands for Define, Measure, Analyze, Improve, and Control. It represents the five phases that make up the process: Define the problem, improvement activity, opportunity for improvement, the project goals, and customer (internal and external) requirements. Project charter to define the focus, scope, direction, and ...
The DMADV procedure entails five phases: define, measure, analyze, design, and verify. Because it is systematic and structured, the framework can be applied to any problem, making it a useful tool for business improvement. On top of all that, the DMADV procedure is adaptable and can be modified to meet the requirements of every business.
DMAIC Process and Problem-Solving. Following we have listed down the 5 phases of the DMAIC process along with the steps you need to take when using it to solve problems. Different tools for each phase is provided with editable templates. Step 1: Define the Problem. So there's a problem that affects your customer or your company processes.
DMAIC is a data-driven problem-solving method for identifying and addressing inefficiencies in a process, improving its outputs, and making these improvements more predictable. The DMAIC methodology was founded by statistician Walter A. Shewhart and was created at Bell Laboratories in the 1930s and gets its roots from the PDSA (plan, do, study ...
Compare the DMAIC and DMADV methods in the context of Lean Six Sigma, guiding readers on when to use which approach. ... Improve, and Control. It is a structured problem-solving methodology widely used in quality improvement projects. ... and potential causes of the problem. Use various analytical tools and techniques to uncover the underlying ...
Designing a product (or service) and a production process to produce such a high level of quality requires the design team to thoroughly understand: DFSS is the label used for just about any systematic attempt to understand those 3 things. The most popular tools used for Design for Six Sigma are. the FMEA, and the House of Quality QFD.
Essential skills for an excellent career
The DMAIC methodology is a popular problem-solving framework that is used to drive process improvements and achieve measurable results. Businesses can improve efficiency, quality, and customer satisfaction by using a structured and data-driven approach to identify, analyze, and address issues.
An informational tool provided as part of a toolkit for researchers and practitioners with an interest in coproducing actionable science to support public land management ... Tool 5: A Problem-solving checklist for coproduction: Authors: Lea B. Selby, Sarah K. Carter, Travis Haby, D. J. A. Wood, Aparna Bamzai-Dodson, Patrick J. Anderson ...
Promo Genius: This tool tackles the challenges of matching the perfect promotion to a customer's needs. It uses dynamic filters to pinpoint the most relevant and value-focused promotions quickly.
The DMAIC methodology is a data-driven quality strategy used to improve processes. It is an integral part of Six Sigma but is also used independently in process improvement efforts. DMAIC stands for Define, Measure, Analyze, Improve, and Control. Each phase has specific objectives and tools designed to achieve these objectives.
AWS developer Banjo Obayomi harnesses Amazon's generative AI tools to get answers and solve problems, while helping other engineers learn and build on Amazon Web Services. I've been interested in software engineering ever since I got hooked on video games as a kid. I studied computer science in college at the University of Maryland, which ...