- DSpace@MIT Home
- MIT Libraries
- Doctoral Theses

Low-frequency, low-amplitude MEMS vibration energy harvesting
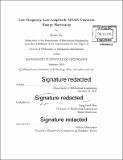
Alternative title
Other contributors, terms of use, description, date issued, collections.
Accessibility Links
- Skip to content
- Skip to search IOPscience
- Skip to Journals list
- Accessibility help
- Accessibility Help
Click here to close this panel.
Purpose-led Publishing is a coalition of three not-for-profit publishers in the field of physical sciences: AIP Publishing, the American Physical Society and IOP Publishing.
Together, as publishers that will always put purpose above profit, we have defined a set of industry standards that underpin high-quality, ethical scholarly communications.
We are proudly declaring that science is our only shareholder.
Research on Vibration of Mechanical System Based on MATLAB
Changying Feng 1 and Chen Pang 1
Published under licence by IOP Publishing Ltd Journal of Physics: Conference Series , Volume 2195 , 2021 International Conference on Smart Transportation, Energy and Power (STEP 2021) 03/12/2021 - 05/12/2021 Sanya City Citation Changying Feng and Chen Pang 2022 J. Phys.: Conf. Ser. 2195 012050 DOI 10.1088/1742-6596/2195/1/012050
Article metrics
1035 Total downloads
Share this article
Author e-mails.
Author affiliations
1 Wuhan University of Technology, Wuhan China
Buy this article in print
Mechanical vibration is the main factor affecting mechanical performance. This vibration will seriously affect the smoothness of the mechanical system and reduce the service life of mechanical system components. In addition, severe mechanical vibration may also affect the stability of the mechanical system and produce noise. Therefore, studying mechanical vibration and proposing control methods will be a significant task. This paper is mainly based on MATLAB to study the vibration of a typical mechanical system, namely the body and wheel dual-mass system, and obtain its amplitude-frequency characteristics, and focus on the influence of system parameters on the root mean square value of vibration. This research can provide a certain useful reference for reducing vehicle vibration and improving vehicle driving comfort.
Export citation and abstract BibTeX RIS
Content from this work may be used under the terms of the Creative Commons Attribution 3.0 licence . Any further distribution of this work must maintain attribution to the author(s) and the title of the work, journal citation and DOI.
Research Progress of Mechanical Vibration Sensors
Ieee account.
- Change Username/Password
- Update Address
Purchase Details
- Payment Options
- Order History
- View Purchased Documents
Profile Information
- Communications Preferences
- Profession and Education
- Technical Interests
- US & Canada: +1 800 678 4333
- Worldwide: +1 732 981 0060
- Contact & Support
- About IEEE Xplore
- Accessibility
- Terms of Use
- Nondiscrimination Policy
- Privacy & Opting Out of Cookies
A not-for-profit organization, IEEE is the world's largest technical professional organization dedicated to advancing technology for the benefit of humanity. © Copyright 2024 IEEE - All rights reserved. Use of this web site signifies your agreement to the terms and conditions.
ScholarWorks@UMass Amherst
Home > Engineering > MIE > ME_THESES

Mechanical Engineering Masters Theses Collection
Theses from 2024 2024.
TECHNICAL EVALUATION OF FLOATING OFFSHORE WIND PLANTS AND INSTALLATION OPERATIONS , CENGIZHAN CENGIZ, Mechanical Engineering
Heat Transfer Enhacement of Latent Heat Thermal Enery Storage , Joe Hatem T. Saba, Mechanical Engineering
Theses from 2023 2023
Device Design for Inducing Aneurysm-Susceptible Flow Conditions Onto Endothelial Cells , hans f. foelsche, Mechanical Engineering
Thermal Conductivity and Mechanical Properties of Interlayer-Bonded Graphene Bilayers , Afnan Mostafa, Mechanical Engineering
Wind-Wave Misalignment Effects on Multiline Anchor Systems for Floating Offshore Wind Turbines , Doron T. Rose, Mechanical Engineering
Theses from 2022 2022
A Simplified Fluid Dynamics Model of Ultrafiltration , Christopher Cardimino, Mechanical Engineering
Local Nanomechanical Variations of Cold-sprayed Tantalum Coatings , Dhrubajyoti Chowdhury, Mechanical Engineering
Aerodynamically Augmented Air-Hockey Pucks , Madhukar Prasad, Mechanical Engineering
Analysis of Low-Induction Rotors for Increased Power Production , Jack E. Rees, Mechanical Engineering
Application of the New IEC International Design Standard for Offshore Wind Turbines to a Reference Site in the Massachusetts Offshore Wind Energy Area , Samuel C. Roach, Mechanical Engineering
Applications of Thermal Energy Storage with Electrified Heating and Cooling , Erich Ryan, Mechanical Engineering
Theses from 2021 2021
Design and Testing of a Foundation Raised Oscillating Surge Wave Energy Converter , Jacob R. Davis, Mechanical Engineering
Wind Turbine Power Production Estimation for Better Financial Agreements , Shanon Fan, Mechanical Engineering
Finite Element Analysis of Impact and Cohesion of Cold Sprayed Particles onto Non-Planar Surfaces , Zhongkui Liu, Mechanical Engineering
Mechanical Design and Analysis: High-Precision Microcontact Printhead for Roll-to-Roll Printing of Flexible Electronics , Mehdi Riza, Mechanical Engineering
Jet Breakup Dynamics of Inkjet Printing Fluids , Kashyap Sundara Rajan, Mechanical Engineering
Ground Source Heat Pumps: Considerations for Large Facilities in Massachusetts , Eric Wagner, Mechanical Engineering
Theses from 2020 2020
Modeling of Electrical Grid Systems to Evaluate Sustainable Electricity Generation in Pakistan , Muhammad Mustafa Amjad, Mechanical Engineering
A Study on Latent Thermal Energy Storage (LTES) using Phase Change Materials (PCMs) 2020 , Ritvij Dixit, Mechanical Engineering
SunDown: Model-driven Per-Panel Solar Anomaly Detection for Residential Arrays , Menghong Feng, Mechanical Engineering
Nozzle Clogging Prevention and Analysis in Cold Spray , Alden Foelsche, Mechanical Engineering
Short Term Energy Forecasting for a Microgird Load using LSTM RNN , Akhil Soman, Mechanical Engineering
Optimization of Thermal Energy Storage Sizing Using Thermodynamic Analysis , Andrew Villanueva, Mechanical Engineering
Fabrication of Binder-Free Electrodes Based on Graphene Oxide with CNT for Decrease of Resistance , Di Zhang, Mechanical Engineering
Theses from 2019 2019
Computational Fluid Dynamics Models of Electromagnetic Levitation Experiments in Reduced Gravity , Gwendolyn Bracker, Mechanical Engineering
Forecasting the Cost of Electricity Generated by Offshore Wind Turbines , Timothy Costa, Mechanical Engineering
Optical-Fiber-Based Laser-Induced Cavitation for Dynamic Mechanical Characterization of Soft Materials , Qian Feng, Mechanical Engineering
On the Fuel Spray Applications of Multi-Phase Eulerian CFD Techniques , Gabriel Lev Jacobsohn, Mechanical Engineering
Topology Network Optimization of Facility Planning and Design Problems , Ravi Ratan Raj Monga, Mechanical Engineering
The Promise of VR Headsets: Validation of a Virtual Reality Headset-Based Driving Simulator for Measuring Drivers’ Hazard Anticipation Performance , Ganesh Pai Mangalore, Mechanical Engineering
Ammonia Production from a Non-Grid Connected Floating Offshore Wind-Farm: A System-Level Techno-Economic Review , Vismay V. Parmar, Mechanical Engineering
Calculation of Scalar Isosurface Area and Applications , Kedar Prashant Shete, Mechanical Engineering
Theses from 2018 2018
Electroplating of Copper on Tungsten Powder , Richard Berdos, Mechanical Engineering
A NUMERICAL FLUTTER PREDICTOR FOR 3D AIRFOILS USING THE ONERA DYNAMIC STALL MODEL , Pieter Boersma, Mechanical Engineering
Streamwise Flow-Induced Oscillations of Bluff Bodies - The Influence of Symmetry Breaking , Tyler Gurian, Mechanical Engineering
Thermal Radiation Measurement and Development of Tunable Plasmonic Thermal Emitter Using Strain-induced Buckling in Metallic Layers , Amir Kazemi-Moridani, Mechanical Engineering
Restructuring Controllers to Accommodate Plant Nonlinearities , Kushal Sahare, Mechanical Engineering
Application and Evaluation of Lighthouse Technology for Precision Motion Capture , Soumitra Sitole, Mechanical Engineering
High Strain Rate Dynamic Response of Aluminum 6061 Micro Particles at Elevated Temperatures and Varying Oxide Thicknesses of Substrate Surface , Carmine Taglienti, Mechanical Engineering
The Effects of Mechanical Loading and Tumor Factors on Osteocyte Dendrite Formation , Wenbo Wang, Mechanical Engineering
Microenvironment Regulates Fusion of Breast Cancer Cells , Peiran Zhu, Mechanical Engineering
Design for Sustainability through a Life Cycle Assessment Conceptual Framework Integrated within Product Lifecycle Management , Renpeng Zou, Mechanical Engineering
Theses from 2017 2017
Improving the Efficiency of Wind Farm Turbines using External Airfoils , Shujaut Bader, Mechanical Engineering
Evaluation Of Impedance Control On A Powered Hip Exoskeleton , Punith condoor, Mechanical Engineering
Experimental Study on Viscoelastic Fluid-Structure Interactions , Anita Anup Dey, Mechanical Engineering
BMI, Tumor Lesion and Probability of Femur Fracture: a Probabilistic Biomechanics Approach , Zhi Gao, Mechanical Engineering
A Magnetic Resonance Compatible Knee Extension Ergometer , Youssef Jaber, Mechanical Engineering
Non-Equispaced Fast Fourier Transforms in Turbulence Simulation , Aditya M. Kulkarni, Mechanical Engineering
INCORPORATING SEASONAL WIND RESOURCE AND ELECTRICITY PRICE DATA INTO WIND FARM MICROSITING , Timothy A. Pfeiffer, Mechanical Engineering
Effects of Malformed or Absent Valves to Lymphatic Fluid Transport and Lymphedema in Vivo in Mice , Akshay S. Pujari, Mechanical Engineering
Electroless Deposition & Electroplating of Nickel on Chromium-Nickel Carbide Powder , Jeffrey Rigali, Mechanical Engineering
Numerical Simulation of Multi-Phase Core-Shell Molten Metal Drop Oscillations , Kaushal Sumaria, Mechanical Engineering
Theses from 2016 2016
Cold Gas Dynamic Spray – Characterization of Polymeric Deposition , Trenton Bush, Mechanical Engineering
Intent Recognition Of Rotation Versus Translation Movements In Human-Robot Collaborative Manipulation Tasks , Vinh Q. Nguyen, Mechanical Engineering
A Soft Multiple-Degree of Freedom Load Cell Based on The Hall Effect , Qiandong Nie, Mechanical Engineering
A Haptic Surface Robot Interface for Large-Format Touchscreen Displays , Mark Price, Mechanical Engineering
Numerical Simulation of High Velocity Impact of a Single Polymer Particle during Cold Spray Deposition , Sagar P. Shah, Mechanical Engineering
Tunable Plasmonic Thermal Emitter Using Metal-Coated Elastomeric Structures , Robert Zando, Mechanical Engineering
Theses from 2015 2015
Thermodynamic Analysis of the Application of Thermal Energy Storage to a Combined Heat and Power Plant , Benjamin McDaniel, Mechanical Engineering
Towards a Semantic Knowledge Management Framework for Laminated Composites , Vivek Premkumar, Mechanical Engineering
A CONTINOUS ROTARY ACTUATION MECHANISM FOR A POWERED HIP EXOSKELETON , Matthew C. Ryder, Mechanical Engineering
Optimal Topological Arrangement of Queues in Closed Finite Queueing Networks , Lening Wang, Mechanical Engineering
Creating a New Model to Predict Cooling Tower Performance and Determining Energy Saving Opportunities through Economizer Operation , Pranav Yedatore Venkatesh, Mechanical Engineering
Theses from 2014 2014
New Generator Control Algorithms for Smart-Bladed Wind Turbines to Improve Power Capture in Below Rated Conditions , Bryce B. Aquino, Mechanical Engineering
UBOT-7: THE DESIGN OF A COMPLIANT DEXTEROUS MOBILE MANIPULATOR , Jonathan Cummings, Mechanical Engineering
Design and Control of a Two-Wheeled Robotic Walker , Airton R. da Silva Jr., Mechanical Engineering
Free Wake Potential Flow Vortex Wind Turbine Modeling: Advances in Parallel Processing and Integration of Ground Effects , Nathaniel B. Develder, Mechanical Engineering
Buckling of Particle-Laden Interfaces , Theo Dias Kassuga, Mechanical Engineering
Modeling Dynamic Stall for a Free Vortex Wake Model of a Floating Offshore Wind Turbine , Evan M. Gaertner, Mechanical Engineering
An Experimental Study of the C-Start of a Mechanical Fish , Benjamin Kandaswamy Chinna Thambi, Mechanical Engineering
Measurement and Verification - Retro-Commissioning of a LEED Gold Rated Building Through Means of an Energy Model: Are Aggressive Energy Simulation Models Reliable? , Justin M. Marmaras, Mechanical Engineering
Development of a Support Structure for Multi-Rotor Wind Turbines , Gaurav Murlidhar Mate, Mechanical Engineering
Towards Accessible, Usable Knowledge Frameworks in Engineering , Jeffrey Mcpherson, Mechanical Engineering
A Consistent Algorithm for Implementing the Space Conservation Law , Venkata Pavan Pillalamarri Narasimha Rao, Mechanical Engineering
Kinetics of Aluminization and Homogenization in Wrought H-X750 Nickel-Base Superalloy , Sean Reilly, Mechanical Engineering
Single-Phase Turbulent Enthalpy Transport , Bradley J. Shields, Mechanical Engineering
CFD Simulation of the Flow around NREL Phase VI Wind Turbine , Yang Song, Mechanical Engineering
Selection of Outputs for Distributed Parameter Systems by Identifiability Analysis in the Time-scale Domain , Teergele, Mechanical Engineering
The Optimization of Offshore Wind Turbine Towers Using Passive Tuned Mass Dampers , Onur Can Yilmaz, Mechanical Engineering
Design of a Passive Exoskeleton Spine , Haohan Zhang, Mechanical Engineering
TURBULENT TRANSITION IN ELECTROMAGNETICALLY LEVITATED LIQUID METAL DROPLETS , Jie Zhao, Mechanical Engineering
Theses from 2013 2013
Optimization of Mixing in a Simulated Biomass Bed Reactor with a Center Feeding Tube , Michael T. Blatnik, Mechanical Engineering
Continued Development of a Chilled Water System Analysis Tool for Energy Conservation Measures Evaluation , Ghanshyam Gaudani, Mechanical Engineering
Application of Finite Element Method in Protein Normal Mode Analysis , Chiung-fang Hsu, Mechanical Engineering
Asymmetric Blade Spar for Passive Aerodynamic Load Control , Charles Mcclelland, Mechanical Engineering
Background and Available Potential Energy in Numerical Simulations of a Boussinesq Fluid , Shreyas S. Panse, Mechanical Engineering
Techno-Economic Analysis of Hydrogen Fuel Cell Systems Used as an Electricity Storage Technology in a Wind Farm with Large Amounts of Intermittent Energy , Yash Sanghai, Mechanical Engineering
Multi Rotor Wind Turbine Design And Cost Scaling , Preeti Verma, Mechanical Engineering
Activity Intent Recognition of the Torso Based on Surface Electromyography and Inertial Measurement Units , Zhe Zhang, Mechanical Engineering
Theses from 2012 2012
Simulations of Non-Contact Creep in Regimes of Mixed Dominance , Maija Benitz, Mechanical Engineering
Techniques for Industrial Implementation of Emerging Semantic Technologies , Jay T. Breindel, Mechanical Engineering
Environmental Impacts Due to Fixed and Floating Offshore Wind Turbines , Micah K. Brewer, Mechanical Engineering
Physical Model of the Feeding Strike of the Mantis Shrimp , Suzanne M. Cox, Mechanical Engineering
Investigating the Relationship Between Material Property Axes and Strain Orientations in Cebus Apella Crania , Christine M. Dzialo, Mechanical Engineering
A Multi-Level Hierarchical Finite Element Model for Capillary Failure in Soft Tissue , Lu Huang, Mechanical Engineering
Finite Element Analysis of a Femur to Deconstruct the Design Paradox of Bone Curvature , Sameer Jade, Mechanical Engineering
Vortex-Induced Vibrations of an Inclined Cylinder in Flow , Anil B. Jain, Mechanical Engineering
Experimental Study of Stability Limits for Slender Wind Turbine Blades , Shruti Ladge, Mechanical Engineering
Semi-Active Damping for an Intelligent Adaptive Ankle Prosthesis , Andrew K. Lapre, Mechanical Engineering
A Finite Volume Approach For Cure Kinetics Simulation , Wei Ma, Mechanical Engineering
Advanced Search
- Notify me via email or RSS
- Collections
- Disciplines
Author Corner
- Login for Faculty Authors
- Faculty Author Gallery
- Expert Gallery
- University Libraries
- Mechanical and Industrial Engineering Webpage
- UMass Amherst
This page is sponsored by the University Libraries.
© 2009 University of Massachusetts Amherst • Site Policies
Privacy Copyright
- Open access
- Published: 02 November 2020
Research on mechanical vibration monitoring based on wireless sensor network and sparse Bayes
- Xinjun Lei 1 , 4 &
- Yunxin Wu 1 , 2 , 3
EURASIP Journal on Wireless Communications and Networking volume 2020 , Article number: 225 ( 2020 ) Cite this article
4096 Accesses
11 Citations
Metrics details
Mechanical vibration monitoring for rotating mechanical equipment can improve the safety and reliability of the equipment. The traditional wired monitoring technology faces problems such as high-frequency signal pickup and high-precision data collection. Therefore, this paper proposes optimization techniques for mechanical vibration monitoring and signal processing based on wireless sensor networks. First, the hardware design uses high-performance STM32 as the control center and Si4463 as the wireless transceiver core. The monitoring node uses a high-precision MEMS acceleration sensor with a 16-bit resolution ADC acquisition chip to achieve high-frequency, high-precision acquisition of vibration signals. Then, the bearing vibration signal optimization method is studied, and the sparse Bayes algorithm is proposed as a compressed sensing reconstruction algorithm. Finally, the difference in reconstruction accuracy between this method and the traditional reconstruction algorithm is compared through experiments and the effect of this method on the reconstruction performance is analyzed when different parameters are selected.
1 Introduction
Vibration fault monitoring technology is to understand the state of the overall mechanical equipment or local mechanical parts during operation by analyzing the mechanical vibration signals collected by the sensors. This technology is a technology used to discover the early failure of mechanical equipment or predict the development trend of mechanical equipment failure [ 1 ]. Modern large-scale electromechanical equipment usually contains many rotating mechanical structures. Rolling bearings are the most commonly used components and play a very critical role in rotating machinery [ 2 ]. The health of rolling bearings greatly affects the operating state of the entire mechanical equipment [ 3 ]. When the rolling bearing fails, it will directly reduce the stability of the entire mechanical equipment and affect the working efficiency, and even a serious production accident occurs [ 4 ]. Therefore, it is very important to monitor the running status of bearings in real time through the mechanical equipment status monitoring system [ 5 ]. The mechanical equipment condition monitoring system performs feature extraction and pattern recognition by collecting physical quantity data during the operation of the equipment.
Common physical quantities include vibration signals, acoustic emission signals, temperature, and lubricant wear [ 6 ]. Vibration signals are easier to collect than other physical quantities and can better characterize the normal or faulty state of bearings during operation. Therefore, mechanical state detection systems based on vibration signal analysis are the most widely used [ 7 ]. The mechanical equipment condition monitoring system using wired connection is widely used in many large-scale equipment detection and process control [ 8 ]. However, the traditional wired connection method has some shortcomings. The wired connection system requires additional connection cables, so the signal is susceptible to interference during transmission. If the transmission distance is long, the lengthy cable will cause problems such as increased installation cost and maintenance cost [ 9 ]. In recent years, the development of wireless sensor networks has broken this wired connection model.
Faced with various problems of wired rotating machinery vibration monitoring system under some special environmental conditions, a new type of mechanical vibration monitoring method based on wireless sensor network has entered people’s research field [ 10 ]. The emergence of this new monitoring solution is due to the rapid development of embedded systems, wireless networks, and integrated hardware circuits in recent decades, which has reduced the cost and power consumption of wireless sensor networks and has broken through the barriers to the development of wireless sensor networks [ 11 ]. The wireless sensor network monitoring mode is a novel technical method for acquiring vibration signals. It uses a large number of distributed sensor nodes to self-network to construct a wireless data transmission method, thereby making up for the traditional wired monitoring system in some special insufficient circumstances [ 12 ]. Therefore, this paper proposes optimization techniques for mechanical vibration monitoring and signal processing based on wireless sensor networks. By combining the hardware design of the wireless sensor monitoring system and the signal processing optimization technology, the mechanical vibration monitoring technical solution is studied.
The rest of this paper is organized as follows. Section 2 discusses methods, followed by the experiment discussed in Sect. 3 . The results are discussed in Sect. 4 . Section 5 concludes the paper with summary and future research directions.
The hardware of the vibration monitoring system for rotating machinery based on wireless sensor network mainly includes two parts: wireless sensor network monitoring node and wireless sensor network base station node. The wireless sensor network monitoring node is generally composed of five parts: control center, data collection, data storage, radio frequency transmission, and power supply [ 13 ]. The node is responsible for collecting and digitizing the vibration and other information of the rotating machinery and then transmitting the information to the base station node by wireless transmission. The base station node of the wireless sensor network is mainly composed of five parts: control center, data storage, radio frequency transmission, Ethernet communication, and power supply. The main function of the base station is to gather, classify, and package the information collected by the nodes joining the wireless sensor network and then transmit the data of each node to the host computer via Ethernet for data processing, display, and storage.
2.1 Overall design
The wireless monitoring system platform designed in this subject can be applied to the vibration monitoring of rotating machinery equipment and can even be widely applied to the vibration monitoring of other types of equipment through simple upgrades. The monitoring nodes in the system platform are used to obtain device status information. To intuitively understand the operating status of the device, the acquired device status information must also be read and displayed [ 14 ].
This requires the use of wireless networks to achieve data transmission and host computer software to display monitoring information. Through the design and analysis of the platform, the overall structure of the system is mainly composed of three parts: wireless sensor network monitoring node, wireless sensor network monitoring base station, and wireless sensor network host computer monitoring software. The structure diagram of a single wireless star network monitoring hardware platform is shown in Fig. 1 .
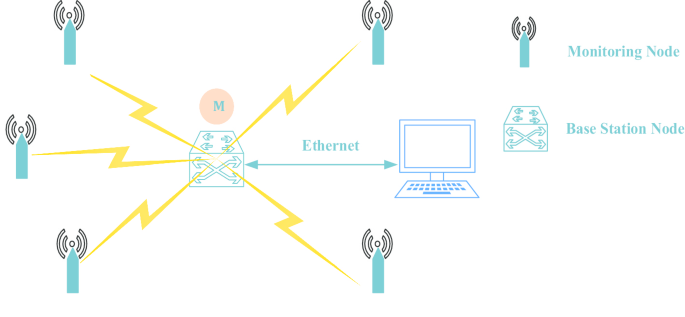
Structure diagram of a single wireless star network monitoring hardware platform
The monitoring node installed on the rotating machine obtains the operating information of the rotating machine and transmits it to the base station node using radio frequency communication. The base station node uses Ethernet to transmit the received operating information to the monitoring host for visual monitoring [ 15 ]. The upper computer in the upper computer monitoring software is the data center of the entire hardware system. The base station node can receive the control commands of the upper computer software and then send it to the target monitoring node through radio frequency communication. The user can also observe the entire monitoring area intuitively through the monitoring host monitoring data and analyze the data through the computer to understand the running status of rotating machinery [ 16 ].
The wireless vibration monitoring network uses a star network structure, which includes a network center and multiple network nodes. The wireless sensor network monitoring base station is the network center, and the wireless sensor network monitoring node is the network node to form the first-level wireless star network structure [ 17 ]. The second-level star network structure is networked by wire. It uses the monitoring host as the network center and the wireless sensor network monitoring base station as the node. The system transmits the monitoring data to the host computer through a two-level star network structure combining wireless and wired. The structure diagram of the improved wireless sensor network monitoring hardware is shown in Fig. 2 .
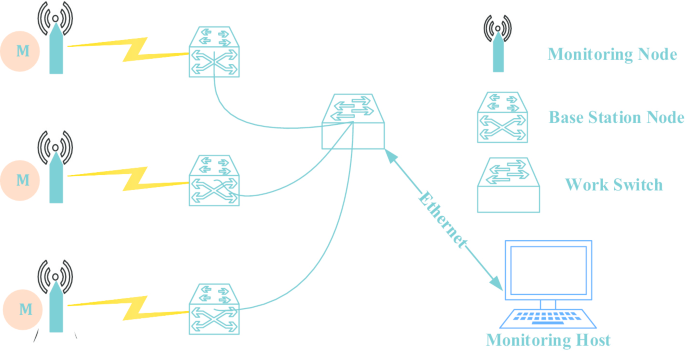
Improved wireless sensor network monitoring hardware structure diagram
2.2 Design of wireless vibration monitoring node
2.2.1 overall scheme design of monitoring node.
The wireless rotating machinery vibration monitoring node uses ST’s Cortex-M4 core 32-bit processor STM32F405RG as the core processor of the monitoring node. The wireless radio frequency takes Silicon Labs’ Si4463 as the core and is equipped with Analog Devices’ high-precision 16-bit A/D converter and MEMS acceleration sensor as the signal acquisition front end [ 17 ]. In addition, there are large-capacity flash storage modules and high-efficiency power supply modules as auxiliary.
Due to the higher accuracy and sampling rate required for vibration monitoring of rotating machinery, a large amount of data will be generated during the monitoring process. In response to the large power consumption problems of data storage, computing, and RF data transmission caused by large amounts of data, the monitoring nodes designed must have higher computing power, lower energy consumption, and superior storage capacity [ 18 ]. The overall design of the wireless rotating machinery vibration monitoring node is shown in Fig. 3 . The wireless monitoring node consists of five parts: control center, data collection, data storage, radio frequency transmission, and power supply [ 19 , 20 ]. The design adopts the concept of modularization, which is conducive to the addition and deletion of different functional modules, increases the flexibility of the equipment, and facilitates the upgrading and transformation of the equipment.
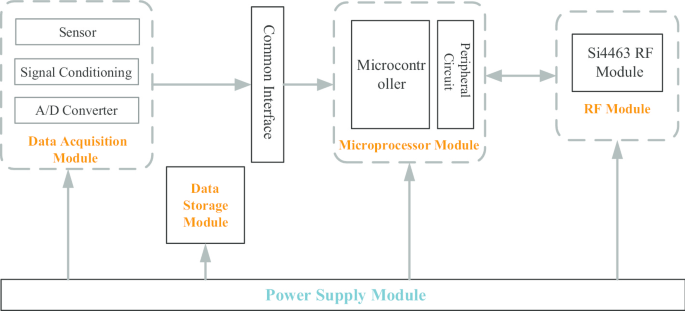
Wireless sensor network detection node design
2.2.2 Data acquisition module
The data acquisition module circuit designed in this paper includes two parts: the sensor part and the signal conditioning conversion part. The sensor is the source of monitoring data for the monitoring system and must meet the characteristics of large range, wide bandwidth, and low power consumption required by mechanical vibration monitoring [ 21 ]. Because only digital signals can be processed and analyzed in the microprocessor system, and the ADXL2203 5 acceleration sensor output is an analog voltage signal, the voltage signal output by the general sensor will not meet the requirements of the AD input signal and must go through the signal conditioning module. And input to the A/D converter for digitlization [ 22 ]. The internal structure of the acceleration sensor is shown in Fig. 4 .
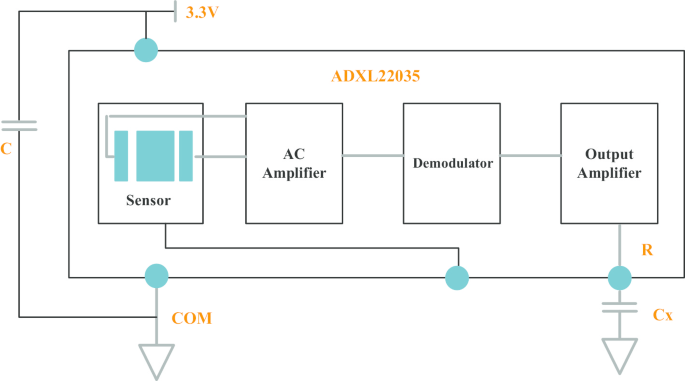
Internal structure of the acceleration sensor
The sensing part needs to measure the vibration parameters of the device, and the sensor module is required to have the characteristics of small size, low power consumption, and simple circuit [ 23 ]. The frequency component of mechanical vibration is related to the specific mechanical structure. The vibration signal of a typical mechanical structure often contains rich frequency components ranging from tens of hertz to several thousand hertz. Therefore, the vibration sensor needs to have a large bandwidth. The node in this paper adopts the high-performance 1VIEMS vibration acceleration sensor ADXL2203 5 from Analog Devices [ 17 ].
3 Experiment
The sampling process is a very important part of digital signal processing. In order to ensure that important information in the original signal is not lost, the sampling process must follow the Nyquist sampling theorem, that is, the sampling frequency must be twice the bandwidth of the original analog signal. If further compression of the original sampled data is required, the common method is to perform sparse transformation on the original signal, discard the smaller coefficients in the transform domain signal, only retain the larger coefficients with the most information, and then decode the signal at the decoding end to perform reconstruction [ 1 ].
This chapter studies the vibration characteristics of rotating machinery, improves the traditional reconstruction algorithm, and proposes a compressed sensing reconstruction method based on block sparse Bayesian learning [ 24 ]. This chapter first studies the block sparse structure model, and several typical reconstruction algorithms using the block sparse structure model, analyzes the characteristics of the mechanical vibration signal in the transform domain, and verifies the feasibility of the block sparse structure model by analyzing the actual signal waveform. Secondly, the theoretical framework and hyperparameter estimation method of block sparse Bayesian learning and reconstruction algorithm are studied, and the use of block sparse Bayesian learning for compressed sensing reconstruction of rotating machinery vibration signals is proposed [ 25 ]. The compression sensing method is used to process the bearing vibration signal, and the performance of different reconstruction algorithms is compared, which proves that the block sparse Bayesian learning method has better reconstruction accuracy than the traditional compression sensing reconstruction algorithm [ 26 , 27 ].

3.1 Structural characteristics of the signal
The signal type studied in this paper is the vibration signal of rotating machinery, which is a typical one-dimensional signal. Generally, the actual one-dimensional engineering signals have obvious aggregation characteristics in the sparse signals in the transform domain, so it is reasonable to use the block sparse structure model to describe the vibration signals of rotating machinery [ 28 , 29 ]. The block structure of the signal can be expressed as a series of non-overlapping coefficient blocks. Different vibration signals were analyzed to verify the block sparse characteristics of the vibration signals, and a preliminary exploration was made for the combination of vibration signals and compression sensing of rotating machinery. In this section, the vibration signal with a load of 2hp, normal type, and three faults is selected at 800 points each [ 30 ]. The original signal has a very complex waveform in the time domain, but it has an obvious block sparse structure in the frequency domain, and when a fault exists, the larger coefficients are concentrated in the middle-frequency band. The signal has block sparse characteristics in the frequency domain and is related to the bearing vibration principle. 0 to 2000 Hz can be regarded as a low-frequency band. The low-frequency band mainly includes the ripple error of the bearing processing surface, the frequency of vibration caused by the assembly position error, and the characteristic frequency of the fault [ 31 , 32 ].
In the low-frequency band, the original vibration signal is particularly susceptible to noise interference, and the energy is very low. 2000 Hz to 4000 Hz can be regarded as an intermediate-frequency band. When the bearing fails, the signal energy in the mid-band is very high. This is mainly due to the existence of a bearing surface failure. When the bearing rotates past a failure point, it will cause an impact. The impulse signal is very short in time, and the spectrum range is particularly wide [ 33 , 34 ]. The inherent vibration frequency of the bearing is generally within the frequency range of the fault impact signal. Therefore, the impact signal will cause the resonance of the bearing, which is very strong. When the bearing is fault-free, the resonance will not be excited because there is no impact signal, so the normal signal has almost no energy in the middle-frequency band. High-frequency band above 4000 kHz usually contains the high-frequency band spectrum caused by fault impact and may also contain some high-frequency noise, usually the energy is the lowest [ 35 ].
3.2 Sparse Bayesian algorithm
Bayesian algorithm is one of the commonly used algorithms in machine learning, mainly used for classification problems [ 36 ]. It mainly refers to that under the given conditions of the training data set, first, based on the assumption of the conditional independence of the feature variables, the joint probability distribution of input and output is obtained [ 37 ]. Then, based on this model, the input instance features are used to find the maximum posterior probability output using Bayes’ theorem.
Let x be the input n-dimensional feature variable, and set \(y \in \{ c_{1} ,c_{2} , \ldots ,c_{n} \}\) as input, X is a random variable on the input space, and Y is a random variable on the output space. The joint probability distribution of X and Y is P ( X, Y ), and P ( X, Y ) independently and identically generates the training data set.
Then, from the Bayesian formula:
Naive Bayes has constructed conditional independence for conditional probability, namely:
The probability \(p (y = 1|x, \theta )\) represents the probability that y belongs to 1 given the characteristic variable x , and \(h_{\theta } \left( x \right) = p(y = 1|x,\theta )\) , then there are models:
in which \(\theta = \{ \theta_{0} ,\theta_{1} , \ldots \theta_{p} \}\) represents the coefficient value corresponding to each feature, θ value. It can be obtained by solving the maximum likelihood estimation function. Assuming that each sample in the data set is independent of each other, the likelihood function is:
The basic formula of the Naive Bayes algorithm is shown in Eq. ( 6 ), and its meaning is the probability of the output category A given the instance Y .
In practical applications, when classifying feature instances, we select the final category with the largest probability value, which can be formalized as Eq. ( 7 ).
In order to verify the high-precision reconstruction performance of the sparse Bayesian algorithm, experiments were carried out on the vibration signal processing method of rotating machinery based on compression sensing. The experimental data are a fault signal with a running load of 2hp, and the length of all experimental data is unified to 800. This section mainly conducts comparative experiments on reconstruction algorithms. Therefore, in order to avoid the influence of different forms of the sparse representation dictionary on the reconstruction accuracy, firstly perform sparse transformation on the time domain signal to obtain transform domain coefficients and then use Gaussian random matrix to transform domain coefficients for projection observation. Finally, a reconstruction algorithm is used to reconstruct transform domain coefficients from low-dimensional observation vectors, and finally an inverse transform method is used to reconstruct the original time domain signal. Projection observation using the observation matrix can reduce the length of the original data and use the signal frequency to evaluate the degree of data compression and optimization.
4.1 Technical performance test
In order to verify the reliability of the parameters of the mechanical vibration monitoring technology in actual use, we have organized various types of system tests. In the case that the function meets the business, the system also needs to meet the requirements of performance indicators such as response speed and server concurrent affordability. This system uses the Siege framework to perform performance tests and uses Noah to monitor various performance indicators. Figure 5 shows the response speed performance results of mechanical vibration monitoring technology. Figure 6 shows the results of server concurrency tolerance in mechanical vibration monitoring technology.
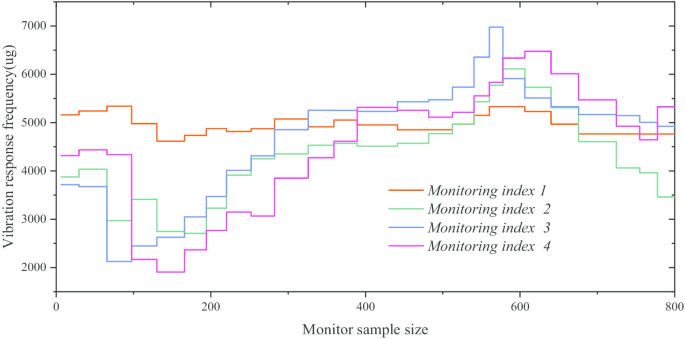
Response speed performance results of mechanical vibration monitoring technology
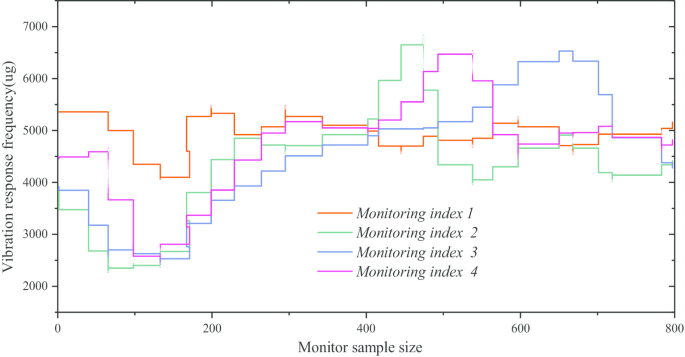
The results of server concurrency tolerance in mechanical vibration monitoring technology
In the process of system performance testing, the two indicators of system response time and packet loss rate are used to test the concurrent performance of the system and the performance of responding to customers. Limited to the network environment and server performance have a greater impact on performance indicators, the network environment during the test is selected as the internal network, and the server is a stand-alone server with a brand-new system and a cluster with two stand-alone servers.
4.2 Comparison of sparse Bayesian learning and other algorithms
In the previous chapter, in addition to introducing the concept of block sparse structure, several reconstruction algorithms using signal block structure were mentioned, including group LASSO, block OMP, group BP, etc. This group of experiments compares the reconstruction performance of sparse Bayes and other block-based sparse structure algorithms. The experimental signal is the bearing outer ring fault signal. During the experiment, except for the sparse Bayesian algorithm, other reconstruction algorithms need to set very complicated prior conditions, which will not be discussed in detail. Figure 7 shows a comparison of original signal and reconstructed signal quality with a compression rate of 30%, and Fig. 8 shows a comparison of original signal and reconstructed signal quality with a compression rate of 50%.
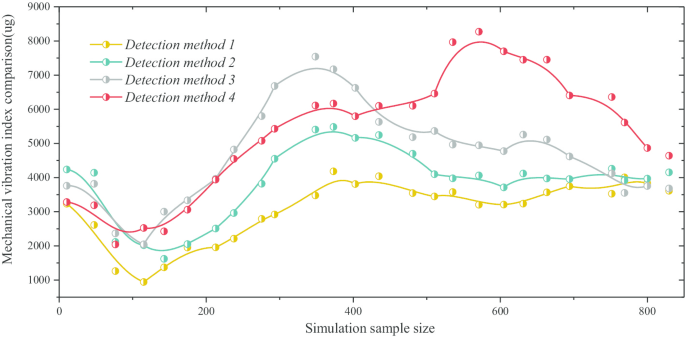
Comparison of the quality of the original signal and the reconstructed signal with a compression rate of 30%
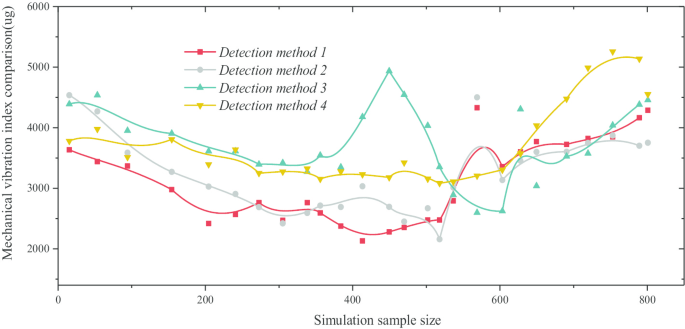
Comparison of the quality of the original signal and the reconstructed signal with a compression rate of 50%
It can be seen from Figs. 7 and 8 that the size of the original signal and the compression ratio has a very small impact on the reconstruction performance and can be ignored, and it can be considered that the sparse Bayesian algorithm is insensitive to the signal block structure. This is the advantage of this algorithm compared to other reconstruction algorithms based on block sparse structure. Before performing calculations, other types of algorithms must first set the block size that matches the signal type, otherwise the reconstruction error will be very large. However, the block structure information of the signal may be unknown in the actual signal processing, and only the sparse Bayesian algorithm can still reconstruct the signal with high accuracy without knowing the block structure of the signal.
Through the above experimental results, it can be observed that the four reconstruction algorithms based on fast sparse structure have no advantage, and even the reconstruction effect is even worse. This problem can be analyzed from two perspectives. First of all, although the energy of the signal has obvious concentration characteristics, it is not an ideal block structure, and there are still many small coefficients at other locations, and four reconstruction algorithms based on block sparse structure use simulation in a noise-free environment. Signal experiments are not good for actual complex signal processing. Secondly, these four kinds of block structure reconstruction algorithms require many prior conditions. Each reconstruction parameter setting needs to conform to the signal characteristics; obviously, the structure of the signal is different. This leads to a very large difference between the two transform domain reconstructed signals. In short, relying too much on the prior conditions will make the algorithm based on the sparse structure of the signal block inferior to the traditional algorithm in practical applications. Through a large number of experiments, the reconstruction performance of the block sparse Bayesian learning method and the existing reconstruction algorithm is compared. In addition, the denoising effect of block sparse Bayesian learning framework is studied. When studying the influence of the signal block structure on the reconstruction algorithm, an important conclusion is drawn through experiments, that is, the influence of the signal block structure on the block sparse Bayesian learning algorithm is negligible, which brings us new enlightenment.
5 Discussion
The wireless vibration fault monitoring technology is to analyze the mechanical vibration signal collected by the sensor to understand the status of the rotating mechanical equipment during operation, and then transmit the monitoring information through the wireless sensor network. This paper analyzes the problems that the wireless sensor network needs to solve in the application of mechanical vibration monitoring, and designs a set of wireless sensor network vibration monitoring system suitable for rotating machinery to initially realize the status monitoring of mechanical equipment. This paper designs a vibration monitoring platform for wireless sensor networks suitable for rotating machinery. According to the design requirements, the hardware circuit design of module units such as data collection, data storage, wireless communication, and power supply unit of the monitoring node is realized.
In addition, the sparse Bayesian algorithm is proposed as a compressed sensing reconstruction algorithm for vibration signal processing. The experiment compares the difference in reconstruction accuracy between this method and the traditional reconstruction algorithm, and the effect of this method on the reconstruction performance is analyzed when selecting different parameters. Although some research results of mechanical vibration monitoring optimization methods have been achieved in this paper, with the continuous expansion of the wireless sensing field and the expansion of new technologies, mechanical vibration monitoring methods still have many problems worth studying. We will further explore mechanical vibration principles and new technologies to provide a scientific reference for the development of modern industry.
Availability of data and materials
Data sharing is not applicable to this article as no data sets are generated or analyzed during the current study.
Abbreviations
Airborne digital computer
B. Zhang et al., Self-powered acceleration sensor based on liquid metal triboelectric nanogenerator for vibration monitoring. ACS Nano 11 , 7440–7446 (2017)
Article Google Scholar
Y. Duo et al., High-accuracy transient response fiber optic seismic accelerometer using a shock-absorbing ring as a mechanical ant resonator. Opt. Lett. 44 , 183–186 (2019)
D. Xia, Q. Qiu, Z. Zhang, S. Liu, Z. Xia, Magnetic field and characteristic analysis of the superconducting fault current limiter for DC applications. IEEE Trans. Appl. Superconduct. 28 , 1 (2018)
Google Scholar
S. Wu, W. Liang, X. Chen, B. Zhou, Flexible optical fiber Fabry–Perot interferometer based acoustic and mechanical vibration sensor. J. Lightwave Technol. 12 (9), 1 (2018)
P.R. Worsley et al., Monitoring contractile dermal lymphatic activity following uniaxial mechanical loading. Med. Eng. Phys. 38 , 895–903 (2016)
D. Wilmott, F. Alves, G. Karunasiri, High sensitive MEMS directional sound sensor with comb finger capacitor electronic readout. J. Acoust. Soc. Am. 138 (3), 1768 (2015)
Y. Wang, P. Jie, Comparison of mechanically and electrically excited vibration frequency responses of a small distribution transformer. IEEE Trans. Power Deliv. 32 (3), 1173–1180 (2017)
B. Phares, P. Lu, T. Wipf, L. Greimann, J. Seo, Evolution of a bridge damage-detection algorithm. Transp. Res. Rec. 2331 , 71–80 (2018)
S. Niu, D. Senk, J.L.L. Rezende, Numerical modeling of the effect of mechanical vibration on 10 kg C45 steel ingot solidification. Steel Res. Int. 90 , 1900081 (2019)
N. Ashwear, A. Eriksson, Influence of temperature on the vibration properties of tensegrity structures. Int. J. Mech. Sci. 15 (9), 237–250 (2015)
K. Mizuno, M. Tanaka, M. Ogata, T. Okamura, Mechanical vibration test of a REBCO coil designed for application to the Maglev. IEEE Trans. Appl. Supercond. 28 (4), 1–7 (2018)
W. Meng et al., Air flow-driven triboelectric nanogenerators for self-powered real-time respiratory monitoring. ACS Nano 12 (7), 562–569 (2018)
D. Maraval, R. Gabet, Y. Jaouen, V. Lamour, Dynamic optical fiber sensing with Brillouin optical time domain reflectometry: application to pipeline vibration monitoring. J. Lightwave Technol. 35 (16), 3296–3302 (2017)
M.T. Yarnold, F.L. Moon, Temperature-based structural health monitoring baseline for long-span bridges. Eng. Struct. 86 (mar.1), 157–167 (2015)
K. Law, H. Sohn, Bayesian probabilistic damage detection of a reinforced-concrete bridge column. Earthq. Eng. Struct. Dyn. 29 (8), 1131–1152 (2015)
G.V. Joseph, G. Hao, V. Pakrashi, Extreme value estimates using vibration energy harvesting. J. Sound Vib. 437 , 29–39 (2017)
J. Cao, X. Zhang, C. Lu, Y. Luo, X. Zhang, Self-healing sensors based on dual noncovalent network elastomer for human motion monitoring. Macromol. Rapid Commun. 38 , 1700406 (2017)
C.H. Hsu, M.F. Hsieh, C.M. Fu, Y.M. Huang, Effects of multicore structure on magnetic losses and magnetomechanical vibration at high frequencies. IEEE Trans. Magn. (2015). https://doi.org/10.1109/TMAG.2015.2443802
G. Shi et al., Highly sensitive, wearable, durable strain sensors and stretchable conductors using graphene/silicon rubber composites. Adv. Funct. Mater. (2016). https://doi.org/10.1002/adfm.201602619
F. Roberto, Simultaneous assessment of mechanical properties and boundary conditions based on digital image correlation. Exp. Mech. 55 (1), 139–153 (2015)
Article MathSciNet Google Scholar
H. Ehsani, J. Mohler, V. Marlinski, E. Rashedi, N. Toosizadeh, The influence of mechanical vibration on local and central balance control. J. Biomech. 71 , 59–66 (2018)
H.D.M. De Azevedo, A.M. Araújo, N. Bouchonneau, A review of wind turbine bearing condition monitoring: state of the art and challenges. Renew. Sustain. Energy Rev. 56 (4), 368–379 (2016)
Y.J. Chan, J.W. Huang, Multiple-point vibration testing with micro-electromechanical accelerometers and micro-controller unit. Mechatronics 44 (12), 84–93 (2017)
N. Ashwear, A. Eriksson, Influence of temperature on the vibration properties of tensegrity structures. Int. J. Mech. Sci. 99 , 237–250 (2015)
F. Andrey, S. Tarasov, S.V. Fortuna, O.A. Podgornykh, V.E. Rubtsov, Microstructural, mechanical and acoustic emission-assisted wear characterization of equal channel angular pressed (ECAP) low stacking fault energy brass. Tribol. Int. 123 (5), 273–285 (2018)
A. Alireza, T. Ahmadreza, R. Nasrin, Z.N. Abolghasem, B. Massimo, K.S. Ali, Vacuum packaged piezoelectric energy harvester for powering smart grid monitoring devices. IEEE Trans. Ind. Electron. 15 (14), 1 (2018)
A. Abasian, A. Tabesh, N. Rezaei-Hosseinabadi, A.Z. Nezhad, M. Bongiorno, S.A. Khajehoddin, Vacuum-packaged piezoelectric energy harvester for powering smart grid monitoring devices. IEEE Trans. Ind. Electron. 16 (6), 4447–4456 (2019)
F. Long, N. Xiong, A.V. Vasilakos, L.T. Yang, F. Sun, A sustainable heuristic QoS routing algorithm for pervasive multi-layered satellite wireless networks. Wirel. Netw. 16 (6), 1657–1673 (2010)
C. Lin, N. Xiong, J.H. Park, T. Kim, Dynamic power management in new architecture of wireless sensor networks. Int. J. Commun. Syst. 22 (6), 671–693 (2009)
H. Liang, J. Zou, K. Zuo, M.J. Khan, an improved genetic algorithm optimization fuzzy controller applied to the wellhead back pressure control system. Mech. Syst. Signal Process. 142 (1), 106–114 (2020)
H. Liang, J. Zou, Z. Li, M.J. Khan, Y. Lu, Dynamic evaluation of drilling leakage risk based on fuzzy theory and PSO-SVR algorithm. Future Gener. Comput. Syst. 95 (4), 454–466 (2019)
J. Li, N. Xiong, J.H. Park, C. Liu, M.A. Shihua, S. Cho, Intelligent model design of cluster supply chain with horizontal cooperation. J. Intell. Manuf. 23 (4), 917–931 (2012)
W. Guo, N. Xiong, A.V. Vasilakos, G. Chen, C. Yu, Distributed k-connected fault-tolerant topology control algorithms with PSO in future autonomic sensor systems. Int J. Sens. Netw. 12 (1), 53–62 (2012)
Z. Liu, B. Hu, Y. Zhao, L. Lang, H. Guo, K. Florence, S. Zhang, Research on Intelligent Decision Of Low Carbon Supply Chain Based On Carbon Tax Constraints In Human-Driven Edge Computing. IEEE Access 8 (3), 48264–48273 (2020)
C. Xu, A novel recommendation method based on social network using matrix factorization technique. Inf. Process. Manag. 54 (3), 463–474 (2018)
L. Dong, Q. Guo, W. Wu, Speech corpora subset selection based on time-continuous utterances features. J. Comb. Optim. 37 (4), 1237–1248 (2019)
Article MathSciNet MATH Google Scholar
Z. Liu, B. Hu, B. Huang, L. Lang, H. Guo, Y. Zhao, Decision optimization of low-carbon dual-channel supply chain of auto parts based on smart city architecture. Complexity 20 (05), 1–14 (2020)
Download references
Acknowledgements
This study was supported by the National Science and Technology Support Program of China (Grant No. 2015BAF07B03).
Author information
Authors and affiliations.
State Key Laboratory of High Performance Complex Manufacturing, Central South University, Changsha, 410083, People’s Republic of China
Xinjun Lei & Yunxin Wu
College of Mechanical and Electrical Engineering, Central South University, Changsha, 410083, People’s Republic of China
Light Alloy Research Institute, Central South University, Changsha, 410083, People’s Republic of China
Test Center, SANY Heavy Industry Co., Ltd, Changsha, 410100, People’s Republic of China
You can also search for this author in PubMed Google Scholar
Contributions
XL is responsible for the data collection and analysis of the experiment and writing of the paper, and YW is responsible for the guidance and revise of the writing of the paper. All authors read and approved the final manuscript.
Corresponding author
Correspondence to Xinjun Lei .
Ethics declarations
Competing interests.
The authors declare that they have no competing interests.
Additional information
Publisher's note.
Springer Nature remains neutral with regard to jurisdictional claims in published maps and institutional affiliations.
Rights and permissions
Open Access This article is licensed under a Creative Commons Attribution 4.0 International License, which permits use, sharing, adaptation, distribution and reproduction in any medium or format, as long as you give appropriate credit to the original author(s) and the source, provide a link to the Creative Commons licence, and indicate if changes were made. The images or other third party material in this article are included in the article's Creative Commons licence, unless indicated otherwise in a credit line to the material. If material is not included in the article's Creative Commons licence and your intended use is not permitted by statutory regulation or exceeds the permitted use, you will need to obtain permission directly from the copyright holder. To view a copy of this licence, visit http://creativecommons.org/licenses/by/4.0/ .
Reprints and permissions
About this article
Cite this article.
Lei, X., Wu, Y. Research on mechanical vibration monitoring based on wireless sensor network and sparse Bayes. J Wireless Com Network 2020 , 225 (2020). https://doi.org/10.1186/s13638-020-01836-9
Download citation
Received : 07 July 2020
Accepted : 19 October 2020
Published : 02 November 2020
DOI : https://doi.org/10.1186/s13638-020-01836-9
Share this article
Anyone you share the following link with will be able to read this content:
Sorry, a shareable link is not currently available for this article.
Provided by the Springer Nature SharedIt content-sharing initiative
- Mechanical vibration monitoring
- Wireless sensor networks
- Sparse Bayes
- Monitoring nodes
- Bibliography
- More Referencing guides Blog Automated transliteration Relevant bibliographies by topics
- Automated transliteration
- Relevant bibliographies by topics
- Referencing guides
Dissertations / Theses on the topic 'Mechanical Vibration'
Create a spot-on reference in apa, mla, chicago, harvard, and other styles.
Consult the top 50 dissertations / theses for your research on the topic 'Mechanical Vibration.'
Next to every source in the list of references, there is an 'Add to bibliography' button. Press on it, and we will generate automatically the bibliographic reference to the chosen work in the citation style you need: APA, MLA, Harvard, Chicago, Vancouver, etc.
You can also download the full text of the academic publication as pdf and read online its abstract whenever available in the metadata.
Browse dissertations / theses on a wide variety of disciplines and organise your bibliography correctly.
Trimble, A. Zachary. "Downhole vibration sensing by vibration energy harvesting." Thesis, Massachusetts Institute of Technology, 2007. http://hdl.handle.net/1721.1/39891.
Donarski, Robert J. "Bone fracture measurement using mechanical vibration." Thesis, University of Kent, 1989. http://ethos.bl.uk/OrderDetails.do?uin=uk.bl.ethos.256998.
LIMA, ROBERTA DE QUEIROZ. "RAMDOM VIBRATION ANALYSIS OF MECHANICAL SYSTEMS." PONTIFÍCIA UNIVERSIDADE CATÓLICA DO RIO DE JANEIRO, 2011. http://www.maxwell.vrac.puc-rio.br/Busca_etds.php?strSecao=resultado&nrSeq=19543@1.
Petri, Patrick Andreas 1979. "Vibration-induced rotation." Thesis, Massachusetts Institute of Technology, 2001. http://hdl.handle.net/1721.1/36110.
Nauclér, Peter. "Modeling and control of vibration in mechanical structures /." Uppsala : Univ. : Dept. of Information Technology, Univ, 2005. http://www.it.uu.se/research/publications/lic/2005-005/.
Kitazaki, Satoshi. "Modelling mechanical responses to human whole-body vibration." Thesis, University of Southampton, 1994. https://eprints.soton.ac.uk/173255/.
Niknam, Alborz. "VIBRATION INSTABILITY IN FRICTIONALLY DRIVEN ELASTIC MECHANICAL SYSTEM." OpenSIUC, 2018. https://opensiuc.lib.siu.edu/dissertations/1579.
Nauclér, Peter. "Modeling and control of vibration in mechanical structures." Licentiate thesis, Uppsala universitet, Avdelningen för systemteknik, 2005. http://urn.kb.se/resolve?urn=urn:nbn:se:uu:diva-85824.
Baker, R. T. "Vibration in electromagnetically heated steel." Thesis, Aston University, 1995. http://publications.aston.ac.uk/15272/.
McCarthy, Daniel Joseph. "Vibration-based diagnostics of reciprocating machinery." Thesis, Massachusetts Institute of Technology, 1994. http://hdl.handle.net/1721.1/10823.
Lee, Evan J. (Evan Joseph). "Airfoil Vortex Induced Vibration suppression devices." Thesis, Massachusetts Institute of Technology, 2007. http://hdl.handle.net/1721.1/39874.
Lavallée, Jean G. 1960. "The effect of vibration mount aging on machinery raft displacement and vibration isolation performance." Thesis, Massachusetts Institute of Technology, 2000. http://hdl.handle.net/1721.1/88351.
Thomas, Rohan J. "Prediction of aircraft fuselage vibration." Thesis, The University of North Dakota, 2015. http://pqdtopen.proquest.com/#viewpdf?dispub=1594387.
Modern unmanned aerial vehicles (UAV) are made of lightweight structures, owing to the demand for longer ranges and heavier payloads. These lightweight aircraft are more susceptible to vibrations caused by atmospheric turbulence transmitted to the fuselage from the wings. These vibrations, which can cause damage to the payload or on board avionics present a serious problem, since air turbulence is expected to increase over the next few decades, due to climate change.
The objective of this thesis is to predict the vibration of an aircraft fuselage by establishing a relationship between wing and fuselage vibration. A combination of ANSYS ® and MATLAB ® modeling are used to simulate aircraft vibrations. First, the displacement of a lumped mass aircraft model to step and sinusoidal forces acting on the wings are compared to displacements calculated using modal superposition equations. Next, a state space representation of this system is found using system identification techniques, which uses wing displacement as input, and provides fuselage displacement as output. This state space model is compared to a derived state space model for validation. Finally, a three dimensional aircraft with distributed displacement sensors on its wings is modeled. A state space representation is established using the wing displacement output from the sensors as its input and the motion and rotation of the fuselage along the X, Y and Z axes as the output.
It is seen that the displacement results of the lumped mass system match with those calculated using modal superposition equations. The state space model can also accurately predict the fuselage vibration of the lumped mass system, when provided with wing displacement as input. More importantly, results have shown that the distributed vibration sensors on the three dimensional plane model are able to measure the wing displacements. Using the output from these distributed sensors, the motion and rotation of the fuselage about all three axes can be effectively predicted.
Issa, Jimmy. "Vibration suppression through stiffness variation and modal disparity." Diss., Connect to online resource - MSU authorized users, 2008.
Reynolds, George Alexander. "REDUCTION OF VIBRATION BY OSCILLATING BOUNDARIES AND ITS APPLICATION IN ROTORDYNAMICS." Miami University / OhioLINK, 2016. http://rave.ohiolink.edu/etdc/view?acc_num=miami1470319955.
Lau, M. W. S. "Active vibration control at machinery feet." Thesis, Aston University, 2000. http://publications.aston.ac.uk/15340/.
Gonsalves, Diane Helen. "Chaos concepts in mechanical systems with clearances." Thesis, University of Aberdeen, 1992. http://ethos.bl.uk/OrderDetails.do?uin=uk.bl.ethos.387216.
Yang, Heng S. M. Massachusetts Institute of Technology. "Ultrasound shear wave elastography imaging with external mechanical vibration." Thesis, Massachusetts Institute of Technology, 2017. http://hdl.handle.net/1721.1/113749.
Xu, Bo. "Vibration and stability analysis of toroidal shells." Thesis, National Library of Canada = Bibliothèque nationale du Canada, 1999. http://www.collectionscanada.ca/obj/s4/f2/dsk1/tape8/PQDD_0006/MQ45257.pdf.
Krull, Alexander G. (Alexander Gerhard). "Experimental testing of LIGO vibration isolation system." Thesis, Massachusetts Institute of Technology, 2007. http://hdl.handle.net/1721.1/40439.
Fitch, Eric E. "Durability analysis method for nonstationary random vibration." Thesis, Massachusetts Institute of Technology, 1996. http://hdl.handle.net/1721.1/40004.
Singer, Neil C. "Residual vibration reduction in computer controlled machines." Thesis, Massachusetts Institute of Technology, 1988. http://hdl.handle.net/1721.1/14435.
Funnell, M. E. (Marc Edwin). "Helicopter tail boom vibration analysis and suppression." Thesis, Stellenbosch : Stellenbosch University, 2002. http://hdl.handle.net/10019.1/52873.
Triplett, Angela L. "Vibration-Based Energy Harvesting." University of Akron / OhioLINK, 2008. http://rave.ohiolink.edu/etdc/view?acc_num=akron1226614650.
Lim, Geok H. "Vibration analysis of a printed circuit board." Thesis, Aston University, 2000. http://publications.aston.ac.uk/15341/.
Min, Byung No 1967. "Non-linear free vibration of a spinning tether." Thesis, McGill University, 1996. http://digitool.Library.McGill.CA:80/R/?func=dbin-jump-full&object_id=27243.
Chan, Alfred. "Vocal fold vibration measurements using laser Doppler vibrometry." Thesis, McGill University, 2012. http://digitool.Library.McGill.CA:80/R/?func=dbin-jump-full&object_id=106574.
Xu, Ruize Ph D. Massachusetts Institute of Technology. "Low-frequency, low-amplitude MEMS vibration energy harvesting." Thesis, Massachusetts Institute of Technology, 2018. http://hdl.handle.net/1721.1/115673.
Miller, Scott E. (Scott Edward). "Distributed parameter active vibration control of smart structures." Thesis, Massachusetts Institute of Technology, 1988. http://hdl.handle.net/1721.1/33473.
Miskel, James F. (James Francis). "Fatigue-based random vibration and acoustic test specification." Thesis, Massachusetts Institute of Technology, 1994. http://hdl.handle.net/1721.1/12069.
Kim, Jeung Tae. "Source and path recovery from vibration response monitoring." Thesis, Massachusetts Institute of Technology, 1987. http://hdl.handle.net/1721.1/14806.
Li, Nong. "Vibration of laminated orthotropic composite plates and shells." Thesis, University of Ottawa (Canada), 1994. http://hdl.handle.net/10393/6946.
Alizadeh, Y. "Free vibration of partially supported plates and shells." Thesis, University of Ottawa (Canada), 1992. http://hdl.handle.net/10393/10751.
Bhaskar, Atul. "Damping in mechanical vibration : new methods of analysis and estimation." Thesis, University of Cambridge, 1992. http://ethos.bl.uk/OrderDetails.do?uin=uk.bl.ethos.314853.
Herder, Erik, and Erik Jenåker. "Vibration Isolation for Electronics on an Autonomous Truck." Thesis, Högskolan i Skövde, Institutionen för ingenjörsvetenskap, 2020. http://urn.kb.se/resolve?urn=urn:nbn:se:his:diva-19367.
Bonsi, Adime. "Fatigue of piezoelectric beams used in vibration energy harvesting." Thesis, McGill University, 2010. http://digitool.Library.McGill.CA:80/R/?func=dbin-jump-full&object_id=92374.
Jian, Ming. "Theoretical and experimental studies of ITH percussive drill vibration." Thesis, McGill University, 1994. http://digitool.Library.McGill.CA:80/R/?func=dbin-jump-full&object_id=68030.
Negishi, Nobuhiko. "Elliptical Vibration Assisted Machining with Single Crystal Diamond Tools." NCSU, 2003. http://www.lib.ncsu.edu/theses/available/etd-08292003-175201/.
Nickerson, Mark David. "Coupled thermal and vibration numerical analysis of solder joints." Diss., The University of Arizona, 2002. http://hdl.handle.net/10150/280238.
Verdirame, Justin Matthew 1978. "Structural vibration damping using lightweight, low-wave-speed media." Thesis, Massachusetts Institute of Technology, 2007. http://hdl.handle.net/1721.1/40360.
Kluger, Jocelyn Maxine. "Nonlinear beam-based vibration energy harvesters and load cells." Thesis, Massachusetts Institute of Technology, 2014. http://hdl.handle.net/1721.1/87958.
Thekkoodan, Dilip Joy. "Interaction of cylinders In proximity under flow-induced vibration." Thesis, Massachusetts Institute of Technology, 2014. http://hdl.handle.net/1721.1/92126.
Miu, Kevin Kar-Leung. "A low cost, DC-coupled active vibration isolation system." Thesis, Massachusetts Institute of Technology, 2008. http://hdl.handle.net/1721.1/46061.
Ustundag, Burak. "On the free vibration behavior of cylindrical shell structures." Thesis, Massachusetts Institute of Technology, 2011. http://hdl.handle.net/1721.1/67717.
Gomez, Nicasio. "PCV valve flutter : vibration characterization through pressure and flow." Thesis, Massachusetts Institute of Technology, 2005. http://hdl.handle.net/1721.1/32895.
Tratch, Jorge. "Vibration transmission through machinery foundation and ship bottom structure." Thesis, Massachusetts Institute of Technology, 1985. http://hdl.handle.net/1721.1/15216.
Liao, Jung-Chi 1971. "Vortex-induced vibration of slender structures in unsteady flow." Thesis, Massachusetts Institute of Technology, 2001. http://hdl.handle.net/1721.1/8331.
Inoue, Akira. "Quantification of parallel vibration transmission paths in discretized systens." The Ohio State University, 2007. http://rave.ohiolink.edu/etdc/view?acc_num=osu1167412835.
Arunyanart, Pirapat. "Fault Identification In Drivetrain Components Using Vibration Signature Analysis." University of Akron / OhioLINK, 2015. http://rave.ohiolink.edu/etdc/view?acc_num=akron1428351973.
Raubenheimer, Gert. "Vibration excitation of axial compressor rotor blades." Thesis, Stellenbosch : Stellenbosch University, 2011. http://hdl.handle.net/10019.1/17987.
Variation of the vibrational treatment on mechanical properties and weld residual stress
- ORIGINAL ARTICLE
- Published: 01 March 2024
- Volume 131 , pages 5037–5046, ( 2024 )
Cite this article
- Douglas Silva Marques Serrati ORCID: orcid.org/0000-0002-1020-8388 1 ,
- Ricardo Martins Silva 1 ,
- Daniel Dominices Baía Gomes de Souza 1 ,
- Jonas Guilherme Gomes Wiezel 2 ,
- Danilo Batista da Cunha 2 ,
- Douglas Bezerra de Araújo 1 &
- Louriel Oliveira Vilarinho 1
163 Accesses
Explore all metrics
There are several ways to relieve welding residual stresses. The most commonly used and the only standardized method is the post-weld heat treatment. However, this method is time-consuming and costly, which necessitates exploring other approaches that can ensure satisfactory results in a faster and more economical manner. In this context, the industry has gradually adopted relief of residual stresses through vibration. Therefore, this study aims to relieve welding residual stresses in thick plates to evaluate whether the position of the excitation source, whether parallel or coincident with the welded plates, influences the expected results. Additionally, it seeks to determine whether the best results are obtained when vibration stress relief is performed simultaneously with welding or after the completion of the process. It was verified that the parallel position presented a maximum reduction of 63.7% in residual stresses when performed after welding, while the parallel and coincident position during the welding reduced a maximum of 2.5% and 56.0% of residual stresses, respectively. Furthermore, mechanical tests are conducted to determine the influence of these processes on mechanical properties. The results indicated that performed vibration after welding is more efficient, and the vibration motor’s position significantly influences the results. Furthermore, it was observed that the only impacted toughness without altering significant other mechanical properties.
This is a preview of subscription content, log in via an institution to check access.
Access this article
Price includes VAT (Russian Federation)
Instant access to the full article PDF.
Rent this article via DeepDyve
Institutional subscriptions
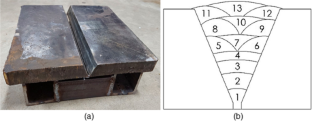
Similar content being viewed by others
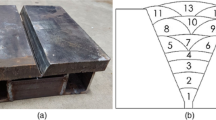
Effects of heat and vibration treatments for welding on residual stresses and mechanical properties
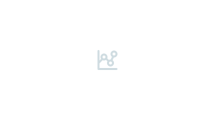
Analysis of the Vibrational Stress Relief for Reducing the Residual Stresses Caused by Machining
The influences of the cyclic force magnitude and frequency on the effectiveness of the vibratory stress relief process on a butt welded connection, data availability.
The data that support the findings of this study are available from the corresponding author, upon reasonable request.
Samardžić I et al (2015) Influence of vibrations on residual stresses stress relief by vibrations. Metalurgija 54(3):527–530
Google Scholar
Walker CA, Waddell AJ, Johnston DJ (1995) Vibratory stress relief—an investigation of the underlying processes. Proc Inst Mech Eng E: J Process Mech Eng 209(1):51–58
Munsi ASMY, Waddell AJ, Walker CA (2001) The influence of vibratory treatment on the fatigue life of welds: a comparison with thermal stress relief. Strain 37(4):141–149. https://doi.org/10.1111/j.1475-1305.2001.tb01250.x
Article Google Scholar
Dawson R, Moffat DG (1980) Vibratory stress relief: a fundamental study of its effectiveness. J Eng Mater Technol Trans ASME 102(2):169–176. https://doi.org/10.1115/1.3224793
Jurčius A et al (2010) Influence of vibratory stress relief on residual stresses in weldments and mechanical properties of structural steel joint. J Vibroeng 12(1):133–141
Sun MC, Sun YH, Wang RK (2004) Vibratory stress relieving of welded sheet steels of low alloy high strength steel. Mater Lett 58(7–8):1396–1399. https://doi.org/10.1016/j.matlet.2003.10.002
Martins CAP et al (2018) Alívio de tensões por vibrações sub-ressonantes: análise e parametrização. Material (Rio de Janeiro) 23(1). https://doi.org/10.1590/s1517-707620170001.0309
Rao D et al (2007) The effectiveness evaluation of 314L stainless steel vibratory stress relief by dynamic stress. Int J Fatigue 29(1):192–196. https://doi.org/10.1016/j.ijfatigue.2006.02.047
Wong TE, Johnson GC (1988) Ultrasonic evaluation of the nonlinearity of metals from a design perspective. Rev Prog Quantitative Nondestruct Eval 7B:1203–1210. https://doi.org/10.1007/978-1-4613-0979-6_39
Bolina CC, Palechor EUL, Vásquez MPR (2015) Vibrações: As Frequências Naturais Estimada E Experimental De Uma Estrutura. p. 186–194. https://doi.org/10.5151/mathpro-cnmai-0038
Ingram E et al (2019) The effect of localized vibration during welding on the microstructure and mechanical behavior of steel welds. Materials 12(16). https://doi.org/10.3390/ma12162553
Munsi ASMY (1999) Investigation and validation of vibratory methods for stress relieving and weld conditioning. PhD Thesis - Mechanical Engineering. University of Strathclyde, Glasgow, UK, p 535
Callister W, Rethwisch D (2007) Materials science and engineering: an introduction. York, PA: John Wylen & Sons, Inc, v. 94
Hassan AH (2014) Fundamentals of vibratory stress relief. Asian J Appl Sci 7(5):317–324. https://doi.org/10.3923/ajaps.2014.317.324
Walker C (2011) A theoretical review of the operation of vibratory stress relief with particular reference to the stabilization of large-scale fabrications. Proc Inst Mecha Eng Part L: J Mater: Design Appl 225(3):195–204. https://doi.org/10.1177/0954420711402877
Shankar S (1982) Vibratory stress relief of mild steel weldments. PhD Thesis - Materials Science. Bangalore University, Bangalore, India, p 128
Prohaszka J, Hidasi B, Varga L (1975) Vibration-induced internal stress relief. Period Polytech Mech Eng 19(1):69–78
Shalvandi M et al (2013) Influence of ultrasonic stress relief on stainless steel 316 specimens: a comparison with thermal stress relief. Mater Design 46:713–723. https://doi.org/10.1016/j.matdes.2012.11.023
Modenesi Paulo, Marques Paulo, Santos Dagoberto (2012) Introdução à metalurgia da soldagem. Federal University of Minas Gerais, Belo Horizonte, Brazil, p 21
Li S et al (2016) Inter-pass thermal-vibration stress relief on multi-pass welded joints of DH 36 steel. Adv Mater Sci Eng (AMSE2016) Anais World Scientific. https://doi.org/10.1142/9789813141612_0073
ASTM A370 (2020) A370: standard test methods and definitions for mechanical testing of steel products. ASTM International, pp 1–50
Stress Relief Engineering Company (1990) Resonant vibration method for reducing residual stresses in welded or machined fabrication. Costa Mesa, California, USA
Rao PG, Rao PS, Krishna AG (2014) Impact strength improvement of butt welded joints prepared by vibratory welding process. J Manuf Technol Manag 6(3/4):143
Serrati DSM (2019) Thermal Analysis of Multipass Welding via Finite Elements. Graduation Project, vol 40. Federal University of Uberlandia, Brazil
Serrati DSM, Araújo Douglas B, Vilarinho Louriel O (2023) Thermal-Structural Plasma Gouging Simulation for Welding Repair. Soldagem & Inspeção 28:e2807. https://doi.org/10.1590/0104-9224/SI28.07
Xu JJ, Chen LG, Ni CZ (2006) Effects of vibratory weld conditioning on residual stresses and transverse contraction distortions in multipass welding. Sci Technol Weld Join 11(4):374–378. https://doi.org/10.1179/174329306X113325
Zhao X, Zhang Y, Ma Y (2011) Finite element analysis of vibratory stress relief process. In: Applied Mechanics and Materials. Trans Tech Publications Ltd, pp 623–627. https://doi.org/10.4028/www.scientific.net/AMM.88-89.623
Chapter Google Scholar
Serrati DS, Silva RM, Wiezel JG, Cunha DB, de Araújo DB, Vilarinho LO (2023) Effects of heat and vibration treatments for welding on residual stresses and mechanical properties. Int J Adv Manuf Technol 128:1473–1481. https://doi.org/10.1007/s00170-023-12011-x
IOGP(S-705) (2020) Supplementary specification to API recommended practice 582 for welding of pressure containing equipment and piping. Joint Ind Programe 33 (JIP33) 33(S-705):55
AWS D1.1, D1.1M (2020) Structural Welding Code - Steel, 24th edn. American Welding Society Inc, Danvers, MA, p 2020
Viii ASME, - DIV1 (2019) Rules for Construction of Pressure Vessels, 2019th edn. ASME International, New York, NY, p 2019
Download references
This research is supported by Petrobras, ANP, CAPES, CNPq, and FAPEMIG.
Author information
Authors and affiliations.
Faculty of Mechanical Engineering, Federal University of Uberlândia, Uberlândia, Minas Gerais, Brazil
Douglas Silva Marques Serrati, Ricardo Martins Silva, Daniel Dominices Baía Gomes de Souza, Douglas Bezerra de Araújo & Louriel Oliveira Vilarinho
Petrobras, Rio de Janeiro, Rio de Janeiro, Brazil
Jonas Guilherme Gomes Wiezel & Danilo Batista da Cunha
You can also search for this author in PubMed Google Scholar
Contributions
All authors contributed at all stages of the article. All authors have read and agreed to the published version of the manuscript.
Corresponding authors
Correspondence to Douglas Silva Marques Serrati or Ricardo Martins Silva .
Ethics declarations
Conflict of interest.
The authors declare no competing interests.
Additional information
Publisher's note.
Springer Nature remains neutral with regard to jurisdictional claims in published maps and institutional affiliations.
Rights and permissions
Springer Nature or its licensor (e.g. a society or other partner) holds exclusive rights to this article under a publishing agreement with the author(s) or other rightsholder(s); author self-archiving of the accepted manuscript version of this article is solely governed by the terms of such publishing agreement and applicable law.
Reprints and permissions
About this article
Serrati, D.S.M., Silva, R.M., de Souza, D.D.B.G. et al. Variation of the vibrational treatment on mechanical properties and weld residual stress. Int J Adv Manuf Technol 131 , 5037–5046 (2024). https://doi.org/10.1007/s00170-024-13318-z
Download citation
Received : 07 November 2023
Accepted : 19 February 2024
Published : 01 March 2024
Issue Date : April 2024
DOI : https://doi.org/10.1007/s00170-024-13318-z
Share this article
Anyone you share the following link with will be able to read this content:
Sorry, a shareable link is not currently available for this article.
Provided by the Springer Nature SharedIt content-sharing initiative
- Residual stress
- Vibration treatment
- Stress relief
- Mechanical tests
- Find a journal
- Publish with us
- Track your research

IMAGES
VIDEO
COMMENTS
up-to-date vibration analysis for machine monitoring and diagnosis. It involves data acquisition (instrument applied such as. analyzer and sensors), feature extraction, and fault recognition ...
1.3 Thesis format In order to carry out this thesis, a lot of preparatory work was done. Specifically the preparation of the author's own knowledge in the field of vibrations and FEM theory was required. Additionally it was necessary to do some analysis exercises to get along with both software, particularly with ANSYS. A good understanding
Thesis similar to an earthquake where the earth shock is transmitted to infrastructures without any control to its. ... Mechanical Vibrations and the Balance of Multi-Cylinder Engines.
In this thesis, feedback and feedforward control of active structures are ad-dressed. The thesis is divided into four parts. The first part contains a general introduction to the subject of active vibration control and also pro-vides an outline of the thesis. The second part of the thesis treats modeling and feedback control of a beam
The adverse effect of mechanical vibration is inevitable and can be observed in machine components either on the long- or short-term of machine life-span based on the severity of oscillation. ... Elmadih W. Additively manufactured lattice structures for vibration attenuation. Waiel Elmadih Thesis, University of Nottingham for the degree of ...
Abstract. Mechanical Vibrations and Control: Dynamic System Analysis presents a comprehensive exploration of mechanical vibrations and their control within dynamic systems. The study delves into ...
Beijing University of Chemical Technology Master Degree Thesis, 11. Li MG, Sun RX, Li Y (2008) Research on vibration sensor of ultra low frequency. Colliery Mech Electr Technol 3:012. Google Scholar Bruel and Kjaer (1984) Mechanical vibration and shock measurements. Bruel and Kjaer, Denmark, pp 97-120. Google Scholar
Thesis: Ph. D., Massachusetts Institute of Technology, Department of Mechanical Engineering, 2018. Cataloged from PDF version of thesis. Includes bibliographical references (pages 187-195). ... Vibration energy harvesters work effectively only when the operating conditions match with the available vibration source. Typical resonating MEMS ...
SIMULATION AND EXPERIMENTAL STUDY. FOR VIBRATION ANALYSIS ON ROTATING. MACHINERY. Msc in Mechanical Engineering with Emphas is on. Structural Mechanic. MOHD SHAFIQ SHARHAN BIN ZAINAL. Supervisor ...
The prediction of dynamic stress and strain in randomly vibrating structures using vibration velocity measurements, PhD thesis, University of Western Australia Fuller , C. R. 1981 . ' The effects of wall discontinuities on the propagation of flexural waves in cylindrical shells ', Journal of Sound and Vibration 75 (2), 207-28 CrossRef ...
The thesis was titled 'Vibrations and Stability of Heterogeneous Curved Beams'. Currently, he is a Senior Lecturer at the Institute of Applied Mechanics. He has been teaching Dynamics since 2012 and Mechanical Vibrations to foreign students since 2015. His research interests and activities include applied mechanics, stability theory, vibration ...
In addition, severe mechanical vibration may also affect the stability of the mechanical system and produce noise. Therefore, studying mechanical vibration and proposing control methods will be a significant task. This paper is mainly based on MATLAB to study the vibration of a typical mechanical system, namely the body and wheel dual-mass ...
theory of mechanical vibrations and its applications (Table1), which has been published in prestigious international Journals within last five years. The data is taken from the Web of Sci-ence Core Collection database and indicated 14,890 papers on mechanical vibrations related to wide variety of scientific cate-
Mechanical systems with n degrees of freedom are discussed and the concepts of mechanical impedance, vibration absorption and impedance matching are studied. The sources of nonli-nearities in structural vibrations are examined and an appropriate solution technique is explored. ... Doctoral Thesis, ETH Zürich, Switzerland, Diss. ETH 7322, 1983 ...
Mechanical vibration is a very common phenomenon in industrial production, and also an important cause of mechanical equipment failure. Monitoring mechanical vibration signal can know the operation status of mechanical equipment, so as to effectively prevent mechanical failure and sudden accidents. Therefore, the acquisition of vibration signal becomes a necessary link in the condition ...
Theses from 2021 PDF. Design and Testing of a Foundation Raised Oscillating Surge Wave Energy Converter, Jacob R. Davis, Mechanical Engineering. PDF. Wind Turbine Power Production Estimation for Better Financial Agreements, Shanon Fan, Mechanical Engineering. PDF
Mechanical vibration monitoring for rotating mechanical equipment can improve the safety and reliability of the equipment. The traditional wired monitoring technology faces problems such as high-frequency signal pickup and high-precision data collection. Therefore, this paper proposes optimization techniques for mechanical vibration monitoring and signal processing based on wireless sensor ...
University of New Mexico
ABSTRACT. Mechanical Vibration: Analysis, Uncertainties, and Control simply and comprehensively addresses the fundamental principles of vibration theory, emphasizing its application in solving practical engineering problems. The authors focus on strengthening engineers' command of mathematics as a cornerstone for understanding vibration ...
The purpose of this study was to investigate the effect of mechanical vibration on. acute power output in the bench press. A total of 10 male subjects performed 3 sets of 3. reps of bench presses using a load equal to 70% one repetition maximum (IRM) on two. occasions separated by 3 days.
International Journal of Mechanical System Dynamics showcases the importance of mechanical system dynamics within modern industrial equipment and product. Abstract Axle-box bearings are crucial components of high-speed trains and operate in challenging conditions. ... Composite fault mechanism and vibration characteristics of high-speed train ...
Thesis (S.M.)--Massachusetts Institute of Technology, Dept. of Mechanical Engineering, 2007. Includes bibliographical references (p. 117). This thesis outlines the design of a prototype electromagnetic induction vibration energy harvesting device for use in a downhole environment.
Vibrations make the weld metal take longer to solidify, favoring the movement of dislocations . A study comparing PWHT, VSR, and VWC, using ASTM A572 G50 carbon steel plates with a thickness of 30 mm, concluded that mechanical vibration, both after and during welding, is effective in reducing stresses to safe levels. VSR reduced stresses by ...
Mechanical Vibrations Singiresu S. Rao. Mechanical Vibration, Pearson sixth edition Brief history • People became interested in vibration when they created the first musical instruments ( as long as 4000 B.C.). • Pythagoras ( 582 -507 B.C) is considered the fisrt person to investigate musical sounds.
mechanical damping systems, springs and dampers. With traditional method, the vibration energy will be dissipated by the damping system as heat, released to the environment. In the damping systems, by replacing dampers with electrical generators (Fig. 5 & Fig. 6), the vibration energy could be collected and fed back to the power system of vehicles.
The thesis also studies about new type of system with switching mechanism, in which other papers do not talk too much and possible control research direction to deal with such complicated system in vibration control. The state-space modeling for both systems are provided in the thesis with detailed model of the MMR gearbox.