
- Career Blog

Maintenance Technician Resume: Winning Examples for 2024
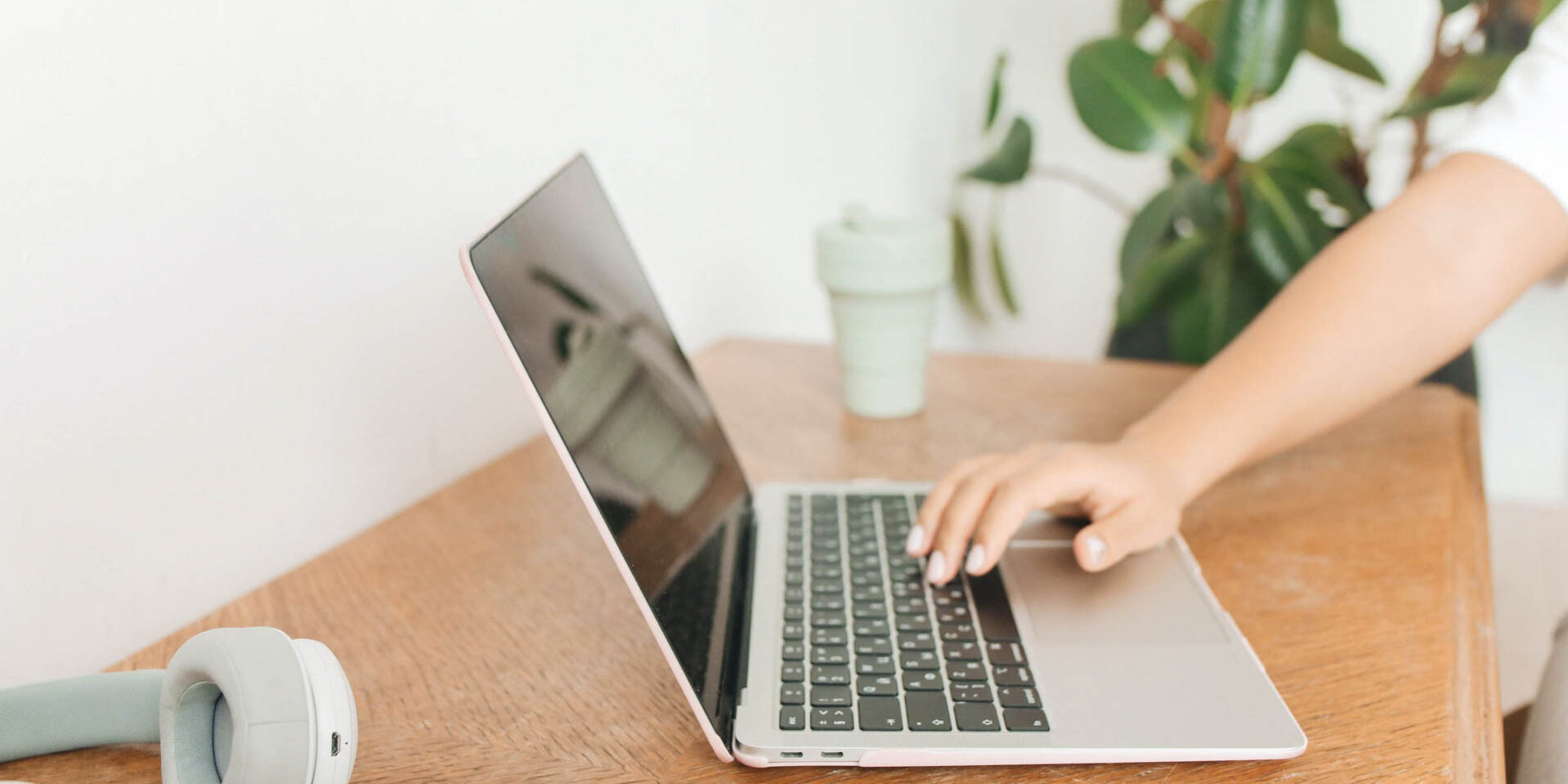
As a maintenance technician, your job is to ensure that equipment, machinery, and facilities are functioning properly. However, before you can even begin to showcase your skills, you need a winning resume to catch the attention of potential employers.
Overview of Maintenance Technician Resume
A maintenance technician resume is a document that showcases your relevant skills, experience, and achievements in a concise and organized manner. It should highlight your technical knowledge and ability to troubleshoot and repair machinery, as well as any certifications or training you have had.
Importance of having a winning resume
A winning maintenance technician resume is essential in standing out from the competition and securing an interview with potential employers. This document serves as your first impression, highlighting your unique qualities and demonstrating your ability to be successful in the role.
Key takeaways
In this article, you can expect to learn about:
- The key elements of a winning maintenance technician resume
- Tips for showcasing technical knowledge and experience
- Examples of successful maintenance technician resumes
- Common mistakes to avoid in a maintenance technician resume
- The importance of tailoring your resume to the specific job and company you’re applying to
By following the tips and examples provided in this article, you will have the tools needed to create a winning maintenance technician resume that will impress potential employers and help you land the job.
Understanding the role of a Maintenance Technician
When it comes to maintaining commercial, residential or industrial properties, the role of a maintenance technician is critical. Their primary responsibility involves ensuring that equipment, facilities, and infrastructure are in good working condition. In this section, we will delve into the job description and requirements, skills and qualifications needed, industry-specific knowledge, and scope of work of a maintenance technician.

A. Job description and requirements
The job description of a maintenance technician may vary depending on the specific industry or organization. However, in most cases, their duties include maintenance, repair, installation, and troubleshooting of various equipment and systems.
Additionally, they may be required to conduct regular inspections of equipment and identify potential issues that may affect performance or safety. They also need to maintain accurate records of maintenance activities and ensure that all tasks are performed in line with regulatory requirements.
To become a maintenance technician, one needs to have a high school diploma or its equivalent. Additionally, they should have a certification or diploma in maintenance, engineering or any related field. Some employers may also require relevant work experience.
B. Skills and qualifications needed
To be an effective maintenance technician, you need to have excellent mechanical, technical, and problem-solving skills. Additionally, you need to have a good understanding of electrical, hydraulic, and pneumatic systems.
Effective communication skills are also essential as you need to work collaboratively with other maintenance professionals, engineers, and management. Furthermore, your ability to prioritize tasks and work under pressure is critical.
C. Industry-specific knowledge
Maintenance technicians need to have industry-specific knowledge that relates to the nature of the equipment that they will be dealing with. For instance, a maintenance technician in an industrial facility may need to have knowledge of programmable logic controllers (PLCs).
In contrast, a maintenance technician involved in maintaining residential buildings requires a good understanding of electrical, plumbing, and HVAC systems. Additionally, they need to stay up to date with technological advancements and emerging trends that could impact their work.
D. Scope of work
The scope of work for maintenance technicians varies depending on the specific organization or industry. In general, their job responsibilities include routine inspections, repairs, and maintenance of equipment and systems.
They may also be required to undertake emergency repairs and troubleshoot issues affecting equipment and systems. Furthermore, they need to participate in the development of maintenance strategies, plans and ensure that all work is carried out in compliance with safety and environmental standards.
To stand out as a maintenance technician, you need to have the right mix of skills, qualifications, and industry-specific knowledge. Additionally, you need to demonstrate your ability to work in a fast-paced environment, prioritize tasks, and effectively communicate with other maintenance professionals and stakeholders.
Key Components of a Winning Maintenance Technician Resume
When crafting a maintenance technician resume, there are certain key components that can make all the difference in whether or not you get hired for your next job opportunity. The following sections should be included in any winning maintenance technician resume:
A. Contact Information
Your contact information should be listed at the top of the page, making it easy for potential employers to get in touch with you. Include your full name, phone number, email address, and physical address.

B. Professional Summary/Objective Statement
The professional summary or objective statement is your chance to make a strong first impression on potential employers. This section should be a brief statement that highlights your skills, experience, and why you are the ideal candidate for the job.
C. Skills Section
In the skills section, you should highlight your technical and soft skills that are relevant to the maintenance technician role. This might include experience with HVAC systems, proficiency with common maintenance tools, and strong communication and problem-solving abilities.
D. Work Experience
The work experience section is where you can showcase your relevant work history. List your previous job titles, employers, and the dates of employment. Be sure to use bullet points to describe your achievements in each role, highlighting any notable projects or accomplishments.
E. Education
In the education section, list any relevant degrees, certificates, or training programs you have completed. This might include vocational or technical training, as well as any college degrees or industry-specific certifications.
F. Certifications and Licenses
As a maintenance technician, there are a number of certifications and licenses that you may need to hold in order to perform your job duties safely and effectively. Be sure to list any relevant certifications or licenses you hold, including the date they were obtained and the organization that issued them.
G. Awards and Honors
If you have received any awards or honors in recognition of your work as a maintenance technician, be sure to list them in this section. This might include safety awards or recognition for excellence in customer service.
H. References
Finally, you may wish to include a list of professional references who can vouch for your skills and work ethic. Be sure to obtain permission before including someone as a reference, and provide their full name, job title, company name, and contact information.
By including these key components in your maintenance technician resume, you can create a winning document that showcases your skills and experience, and helps you stand out from other job seekers in your field.
Best Resume Format and Layout for Maintenance Technicians
When creating a resume for a maintenance technician position, it is important to choose the best format and layout to showcase your skills and experience. The following are some of the most popular formats for a maintenance technician resume:
A. Chronological Format
A chronological format lists your work history in reverse chronological order, with your most recent job at the top of the list. This format is ideal for those who have a strong, consistent work history with little to no gaps in employment. It highlights your career progression and shows potential employers how you have developed your skills over time.
B. Functional Format
A functional format focuses on your skills and abilities rather than your work history. This format is ideal for those who have gaps in their employment, are new to the industry, or are changing careers. It allows you to highlight your relevant skills and experience, regardless of when and where you acquired them.
C. Combination Format
A combination format combines elements of both the chronological and functional formats. This format allows you to showcase your work history and career progression while also highlighting your skills and abilities. It is ideal for those who have both a strong work history and relevant skills and experience.
D. Selecting the Right Layout
When selecting the layout for your maintenance technician resume, it is important to choose one that is easy to read and visually appealing. Use a clean and simple layout with clear headings and bullet points. Avoid using fancy fonts or colors that may distract from your content.
E. Tips for Formatting Your Resume
When formatting your maintenance technician resume, keep the following tips in mind:
Start with a strong opening summary or objective statement that highlights your key skills and experience.
Use bullet points to break up large chunks of text and make your content easy to read.
Use action verbs to describe your accomplishments and responsibilities in each job.
Quantify your achievements with specific numbers, percentages, or dollar amounts.
Use keywords from the job posting to show that you have the skills and experience employers are looking for.
Choosing the right format and layout for your maintenance technician resume is crucial in showcasing your skills and experience. Keep the layout simple and easy to read, and use bullet points and action verbs to highlight your accomplishments. Use keywords from the job posting and quantify your achievements to demonstrate your value to potential employers. With these tips in mind, your maintenance technician resume is sure to stand out from the crowd.
Writing the Professional Summary/Objective Statement
A well-crafted professional summary or objective statement can make all the difference in catching a hiring manager’s attention. This section will explore the purpose of the summary/objective statement and provide examples of winning formulas that could set your Maintenance Technician resume apart from the pack.
A. The purpose of the summary/objective statement
The summary/objective statement serves as an introduction to your resume, highlighting your key qualifications and career goals. It’s a brief but powerful summary of who you are, what you can achieve, and what you want to accomplish in your next role.
For Maintenance Technicians, the summary/objective statement needs to capture essential skills like troubleshooting, maintenance, and repair of electrical, mechanical, and hydraulic systems. Additionally, it should highlight relevant experience, certifications or training received, and a few specific achievements to grab the reader’s attention.
B. Examples of well-written professional summaries/objective statements
Here are some examples of winning professional summaries/objective statements:
“Detail-oriented Maintenance Technician with over 5 years of experience in repairing and maintaining complex machinery. Skilled in troubleshooting, electrical and mechanical repairs, and performing preventative and corrective maintenance. Certified in HVAC and OSHA, seeking to leverage my expertise and making a measurable impact in a challenging role as a senior Maintenance Technician.”
“Reliable Maintenance Technician with a successful track record of increasing machine uptime, maintaining accurate records, and exceeding production goals. Proficient in machinery inspections, electrical circuits and schematics, and mechanical systems. Experienced in managing a team of maintenance professionals and providing them with training and guidance. Seeking to utilize my technical and leadership skills to help your company achieve its operational objectives.”
“Hardworking and dedicated Maintenance Technician with over 7 years of experience in the maintenance and repair of heavy machinery in a manufacturing setting. Skilled in machine diagnostics, troubleshooting, and quality control. Consistently exceeded targets and minimized downtime by developing innovative solutions. Seeking a challenging role that leverages my problem-solving abilities and technical expertise.”
Each of these statements showcases the candidate’s unique value proposition, highlights their key qualifications, and speaks directly to the needs of the employer. Crafting a compelling professional summary or objective statement is an essential part of creating a Maintenance Technician resume that stands out from the competition.
Highlighting Relevant Maintenance Technician Skills
In order to create a winning Maintenance Technician Resume, it is crucial to highlight relevant skills that showcase your abilities as a technical professional. There are various types of skills that you can include on your resume, such as technical skills, soft skills, and industry-specific skills.
A. Technical Skills
Technical skills are the abilities that you have developed through your formal education, training, and work experience. These skills are essential for performing technical tasks related to maintenance work such as repairing, replacing, and installing equipment. Some examples of technical skills that you can include on your maintenance technician resume are:
- Electrical wiring and circuitry
- HVAC installation, maintenance, and repair
- Plumbing and piping systems
- Mechanical systems
- Industrial machinery and equipment
- Computerized maintenance management systems (CMMS)
- Blueprint reading and interpretation
- Diagnostic tools and equipment
- Preventive maintenance procedures
B. Soft Skills
Soft skills are personal attributes that help you interact effectively with others, perform well in a team, and make a good impression on your employer. Soft skills are essential for maintenance technician jobs that require communication skills, problem-solving skills, and critical thinking skills. Some examples of soft skills that you can include on your resume are:
- Communication skills
- Problem-solving skills
- Time management skills
- Customer service skills
- Attention to detail
- Collaboration skills
- Adaptability and flexibility
- Leadership skills
C. Industry-specific Skills
Industry-specific skills are the skills related to your industry or the company where you work. These skills are essential for performing the day-to-day tasks that are required for maintenance technician jobs. Some examples of industry-specific skills that you can include on your resume are:
- Safety regulations and procedures
- Knowledge of specific machinery and equipment
- Knowledge of the maintenance of specific building systems
- Knowledge of industry-specific materials and tools
- Knowledge of regulations in the maintenance industry
D. Examples of relevant skills to include on your resume
- Proficient in electrical wiring and circuitry
- Skilled in HVAC installation, maintenance, and repair
- Excellent problem-solving skills and ability to diagnose and repair mechanical issues
- Demonstrated ability to interpret building blueprints and schematics
- Strong knowledge of plumbing and piping systems, including installation, repair, and maintenance
- Proven ability to perform preventive maintenance on industrial machinery and equipment
- Knowledge of computerized maintenance management systems (CMMS)
- Experience guiding and training maintenance staff
- Ability to adhere to safety regulations and procedures
- Excellent communication skills and customer service skills
By highlighting these relevant skills, you can make a lasting impression on prospective employers and increase your chances of landing a maintenance technician job. Remember to tailor your resume to the specific job you are applying for, and use clear and concise language to showcase your abilities. ** Showcasing Work Experience**
Once you’ve listed your work experience on your maintenance technician resume, it’s important to make sure that the information you present effectively showcases your skills and abilities. To do this, you should:
A. Writing Bullet Points for Work Experience
Use bullet points to present your work experience in a clear and concise manner. Each bullet point should highlight a specific responsibility, achievement, or skill that you possess. Keep in mind that bullet points should not be too long – aim for no more than one or two sentences per point.
B. Quantifying Accomplishments and Achievements in Work Experience
When describing your work experience, try to include specific numbers or metrics whenever possible to quantify your accomplishments. This can help employers get a better idea of the impact you had in your previous positions. For example:
- “Increased production efficiency by 25% through implementation of new maintenance program”
- “Reduced equipment downtime by 30% by regularly performing preventative maintenance checks”
- “Managed a team of 5 technicians and successfully completed 30+ maintenance projects annually”
C. Examples of Well-Crafted Bullet Points for Work Experience
Here are some examples of effective bullet points for a maintenance technician resume:
- “Performed routine maintenance on HVAC systems, including replacing filters, checking thermostats, and cleaning ductwork”
- “Troubleshot and repaired electrical systems, including wiring, motors, and lighting fixtures”
- “Conducted regular inspections of machinery and equipment to identify and prevent potential problems”
- “Collaborated with other departments to ensure timely completion of maintenance projects”
- “Maintained detailed records of work performed and materials used to facilitate accurate inventory tracking”
Remember, the more specific and quantifiable your bullet points are, the more likely you are to catch the attention of potential employers. Make sure to proofread your resume carefully for errors and consistency, and tailor the language you use to the requirements of each job you apply for. With a well-crafted resume that showcases your experience and achievements, you’ll be well on your way to landing your dream maintenance technician job.
Emphasizing Education
As a maintenance technician, it’s important to highlight your educational background to distinguish yourself from other candidates. Hiring managers want to know that you are committed to staying up-to-date on the latest industry developments and that you have the necessary qualifications to perform the job.
When crafting your resume, consider emphasizing the following areas of education:
A. Relevant degrees and certifications
If you have a degree or certification in a field related to maintenance, be sure to mention it on your resume. This could include an associate’s or bachelor’s degree in engineering, HVAC certification, or a certification in a specialized area like plumbing or electrical work. These qualifications show that you have a solid foundation in the technical skills required for the job.
B. Technical courses and training programs
In addition to formal degrees and certifications, be sure to highlight any technical courses or training programs you have completed. For instance, if you have taken a course in industrial machinery repair or HVAC system maintenance, make sure to list it on your resume. These courses show that you are committed to staying current on emerging technologies and techniques.
C. Professional development and continuing education
As a maintenance technician, it’s essential to stay up-to-date on the latest industry developments, which is why continuing education is so important. Be sure to mention any professional development programs you’ve taken part in, such as seminars, workshops, or conferences. These activities show that you are committed to a lifelong learning mindset and are willing to go the extra mile to stay ahead of the curve.
D. Examples of educational achievements to highlight
When deciding which educational achievements to emphasize on your resume, consider those that align with the requirements of the specific job you’re applying for. For instance, if the job requires experience with HVAC systems, you should highlight any relevant coursework or certifications you have in this area. If the job requires experience with industrial machinery, emphasize any training you’ve received in this area.
Here are some examples of educational achievements that could be worth highlighting on your resume:
- Completion of a certified HVAC technician program
- Recognition for excellence in a plumbing apprenticeship
- Academic award for high achievement in electrical engineering coursework
- Completion of an OSHA-authorized safety training program
Highlighting your educational background is essential to creating a winning maintenance technician resume. With the right emphasis and attention to detail, you can distinguish yourself from other candidates and show potential employers that you have what it takes to excel in the job.
Certifications and Licenses Relevant to Maintenance Technicians
Maintenance technicians play a crucial role in ensuring that equipment and machinery are functioning properly. Obtaining relevant certifications and licenses in the industry can provide numerous benefits for these professionals.
A. Benefits of Obtaining a Certification or License
- Increased job opportunities : Employers often prioritize hiring candidates with certifications or licenses, as it shows that they possess the necessary skills and knowledge to perform the job effectively.
- Higher earning potential : Certified or licensed maintenance technicians may command higher salaries than their non-certified counterparts.
- Professional development : Obtaining a certification or license can provide technicians with an opportunity to enhance their skills and knowledge by attending training courses and workshops.
- Validation of skills and knowledge : Certifications and licenses demonstrate that maintenance technicians have met certain industry standards and possess a certain level of expertise.
B. Examples of Relevant Certifications and Licenses in the Industry
Maintenance technicians can obtain various certifications and licenses in the industry, depending on their area of expertise. Here are a few examples:
- Certified Maintenance and Reliability Professional (CMRP) : A certification that validates the skills and knowledge of maintenance and reliability professionals across various industries.
- National Institute for Certification in Engineering Technologies (NICET) : Offers certification in several areas, including industrial instrumentation and controls, fire protection engineering technology, and construction materials testing.
- Certified Welding Inspector (CWI) : A certification that demonstrates proficiency in welding inspection and testing.
- EPA 608 Certification : A license that allows maintenance technicians to handle and dispose of refrigerants in compliance with federal regulations.
C. How to Incorporate Certifications and Licenses on Your Resume
Including relevant certifications and licenses on a maintenance technician’s resume can improve their chances of getting hired. Here are a few tips on how to incorporate certifications and licenses into a resume:
- List certifications and licenses under a separate section : Create a separate section on the resume to list all relevant certifications and licenses. This will make it easier for hiring managers to identify the candidate’s qualifications quickly.
- Include the name of the certification or license : Write the full name of the certification or license, as well as any abbreviations or acronyms.
- Indicate the date obtained : List the date the certification or license was obtained. It’s important to keep in mind that some certifications may have an expiration date, so include the date of expiration if applicable.
- Add details about the certification or license : Provide additional information about the certification or license, such as the issuing organization or any notable achievements associated with it.
Incorporating certifications and licenses on a maintenance technician’s resume can demonstrate their level of expertise and validate their skills and knowledge. By following the tips outlined above, candidates can create a winning maintenance technician resume that showcases their qualifications to potential employers.
Writing a Winning Cover Letter for Maintenance Technician
A. the purpose of a cover letter.
A cover letter is a crucial component of any job application. It serves as an introduction to the employer and provides an opportunity for you to showcase your qualifications and skills that make you the perfect candidate for the job. The purpose of a cover letter is to grab the employer’s attention and persuade them to consider you for the position.
B. Essential Components of a Cover Letter
Introduction: Begin your cover letter by introducing yourself and stating your interest in the maintenance technician position.
Qualifications: Highlight your relevant job experience and education that make you the perfect candidate for the role. Mention any certifications or specialized training that you have received.
Skills: Emphasize your technical and soft skills that align with the job requirements. Include examples of how you have used these skills in previous roles.
Value Proposition: Explain how you can add value to the company by contributing to its goals and objectives.
Closing: End the cover letter by thanking the employer for considering your application and expressing your enthusiasm for the opportunity to join the team.
C. Tips and Tricks on Crafting an Effective Cover Letter
Tailor your cover letter to the job description and company culture. Highlight the skills and experiences that align with the specific role and showcase your knowledge of the company’s values and mission.
Keep it concise and focused on the most important details. Use bullet points to make the information easy to read and follow.
Use a professional tone and avoid using slang or overly casual language.
Proofread for any errors or typos. Have someone else review it for a fresh perspective.
Don’t simply restate your resume. Use the cover letter to provide additional context and details that may not be included in your resume.
Crafting an effective cover letter takes time and effort, but it is well worth it when it results in a job offer. Use these tips and tricks to ensure that your cover letter stands out from the rest and convinces the employer that you are the perfect maintenance technician for the job.
Common Resume Mistakes to Avoid
When it comes to creating a winning Maintenance Technician resume, there are several common mistakes that job seekers should avoid. These include:
A. Grammatical errors and typos
It’s essential to carefully proofread your resume to eliminate grammatical errors and typos. Simple mistakes like these can quickly turn off a potential employer and diminish the impact of an otherwise impressive resume.
B. Lack of focus on skills and achievements
A common mistake in writing a Maintenance Technician resume is failing to emphasize specific skills and achievements relevant to the job. Avoid taking a generic approach by tailoring your resume to highlight the skills and experiences that the particular job requires.
C. Length and formatting mistakes
Make sure that your resume is formatted clearly and cleanly, and avoid bloating it with unnecessary information. Keep it evenly spaced, using simple fonts and try to limit your resume to 1-2 pages to ensure that it is concise and easy to read.
D. Overusing technical jargon
While it is important to showcase your technical expertise, overusing technical jargon can backfire, especially if the individual reviewing your resume is not familiar with the jargon. Instead, focus on the key technical skills that are relevant to the position and use plain language to explain them.
By avoiding these common mistakes, you will ensure that your Maintenance Technician resume stands out for all the right reasons.
Related Articles
- Navigating Salary Expectation Questions in Job Interviews
- Top 30 Tips for a Communications Specialist Resume
- Agile Project Manager Resume: Samples and Writing Guide
- Learning and Development Specialist Resume: Best Examples
- Training Specialist Resume Writing Tips and Examples
Rate this article
0 / 5. Reviews: 0

More from ResumeHead
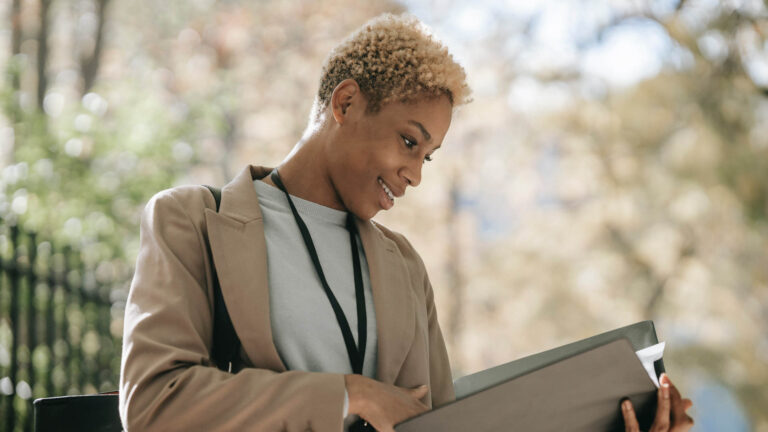
Resume Worded | Proven Resume Examples
- Resume Examples
- Engineering Resumes
4 Maintenance Technician Resume Examples - Here's What Works In 2024
Maintenance technicians keep everything up and running in a building, including hvac systems, structures, and equipment units. these professionals evaluate the conditions in the building to identify issues and troubleshoot them. in addition, they schedule maintenance operations and repairs. this is a profession that requires manual dexterity and technical knowledge of building maintenance. you don’t need a bachelor’s degree for this occupation, but technical training is surely important. if this sounds like your cup of tea read on. we’re about to show you how to create your maintenance technician resume..
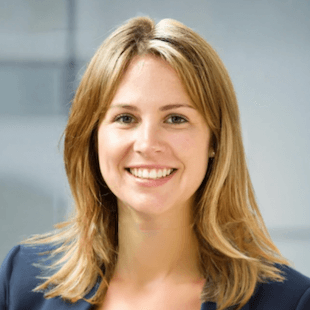
Maintenance technicians are responsible for maintaining an establishment, which could be an office building, an apartment, or any type of facility. Maintenance technicians perform various tasks, including inspection, plumbing, managing electrical systems, inventory, and HVAC systems. They must be proficient in multiple skills, such as carpentry, electrical repairs, painting, and landscaping.
Maintenance technicians must monitor the building and perform regular quality checks to identify failures or damages in the structure, systems, and equipment. This role requires excellent organizational skills and time management. It is important to demonstrate that in your resume by showcasing reliability.
As a maintenance technician, you must be familiar with security regulations and protocols since you’ll be dealing with highly dangerous tasks. Therefore, it is a good idea to mention your knowledge of security compliance on your resume. This way, your potential employer knows you are capable of delivering a good job without being prone to physical damage.
Even though you will be handling electrical and plumbing systems, there might be things that surpass your competencies. When you encounter highly complex issues, you must talk to the facility manager, and they’ll probably hire a qualified team of engineers or plumbers.
Maintenance Technician Resume Templates
Jump to a template:
- Maintenance Technician
- Industrial Maintenance Technician
- Maintenance Supervisor
- Maintenance Manager
Jump to a resource:
- Keywords for Maintenance Technician Resumes
Maintenance Technician Resume Tips
- Action Verbs to Use
- Related Engineering Resumes
Get advice on each section of your resume:
Template 1 of 4: Maintenance Technician Resume Example
A maintenance technician is an in-house employee that is responsible for repairs and maintenance in a particular facility. They inspect the building’s electrical systems, HVAC, and structure to see if there’s a need for troubleshooting or restoration. In addition, they estimate what materials and budget are needed for the repairs. That’s why mentioning your financial skills in your resume might be a plus. Some maintenance technicians work under the supervision of maintenance managers. You will need to let them know about complex issues in the building and comply with their orders. To become a maintenance technician, you can attend a trade school or get on-the-job training.
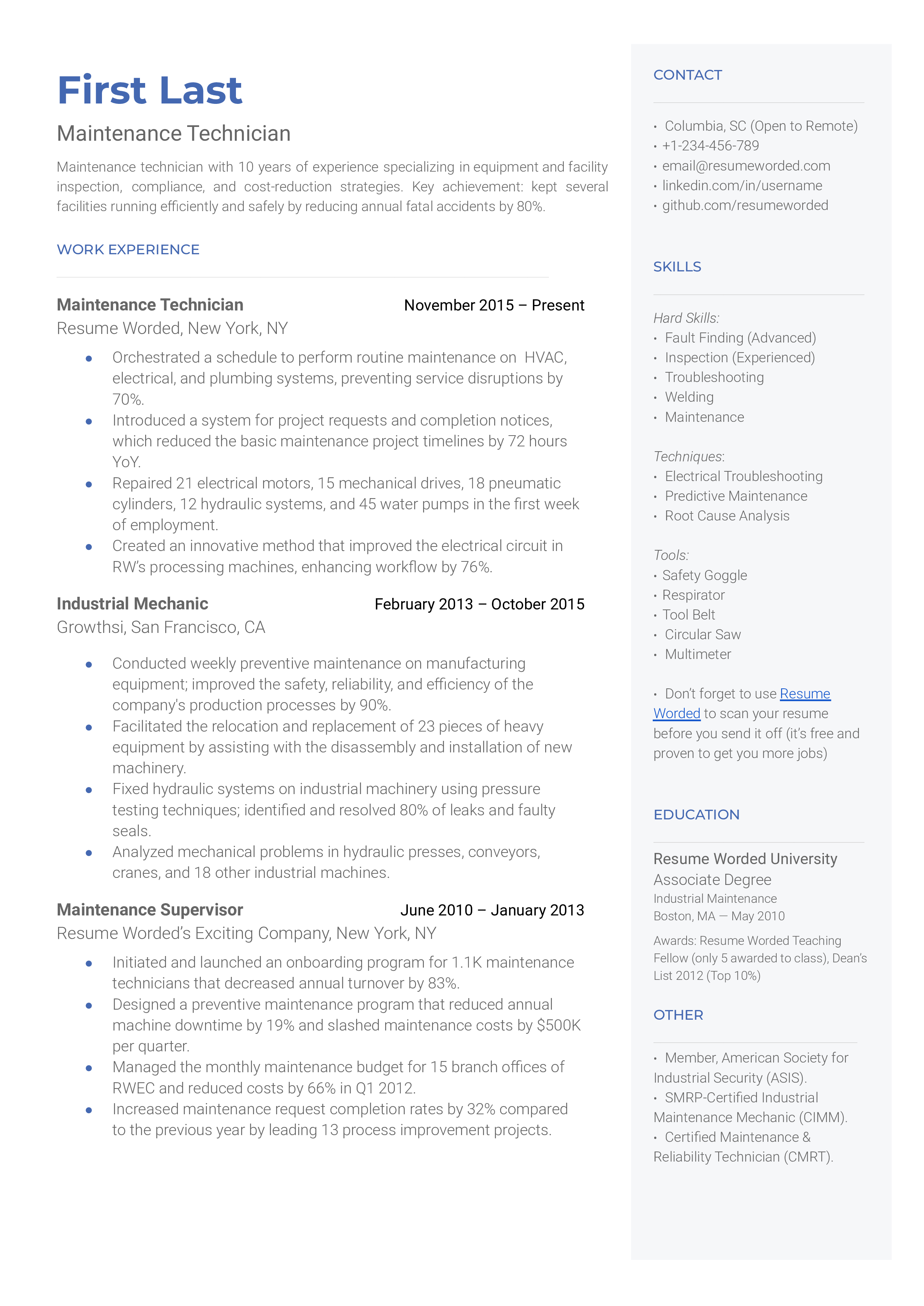
We're just getting the template ready for you, just a second left.
Tips to help you write your Maintenance Technician resume in 2024
include any relevant certification, such as an hvac certificate..
The Maintenance & Reliability Technician (CMRT) Certification helps you validate your skills for preventive maintenance and troubleshooting. Even though they are not required in most roles, it is definitely a plus in your resume. You can also add an HVAC certificate which is highly in demand for this role.
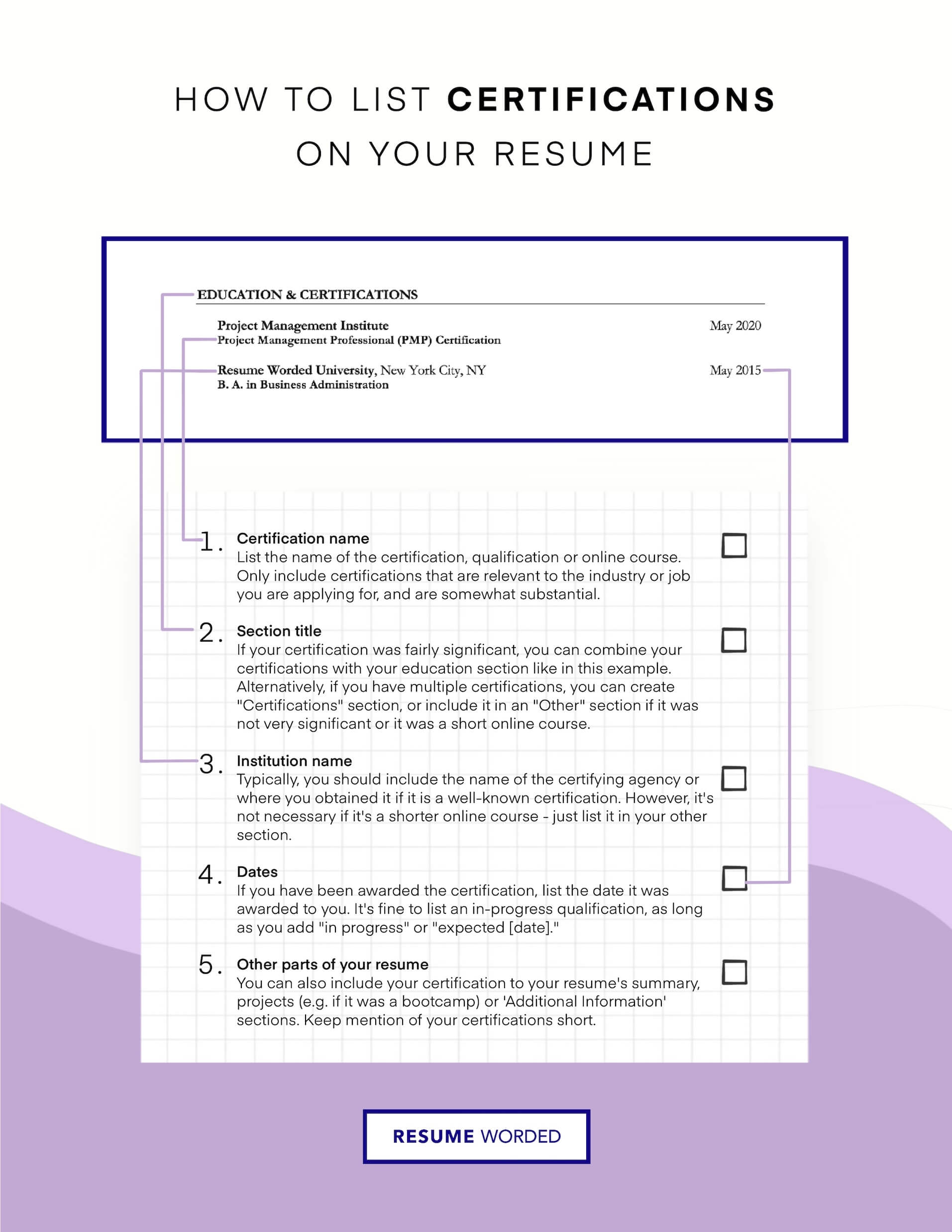
Highlight your technical skills.
This role requires you to be qualified in various technical areas, so it’s important to highlight your hard skills. Soft skills like communication, analytical thinking, and resilience are important in a maintenance technician role. Yet, it’s better to reserve your skills section for technical competencies.
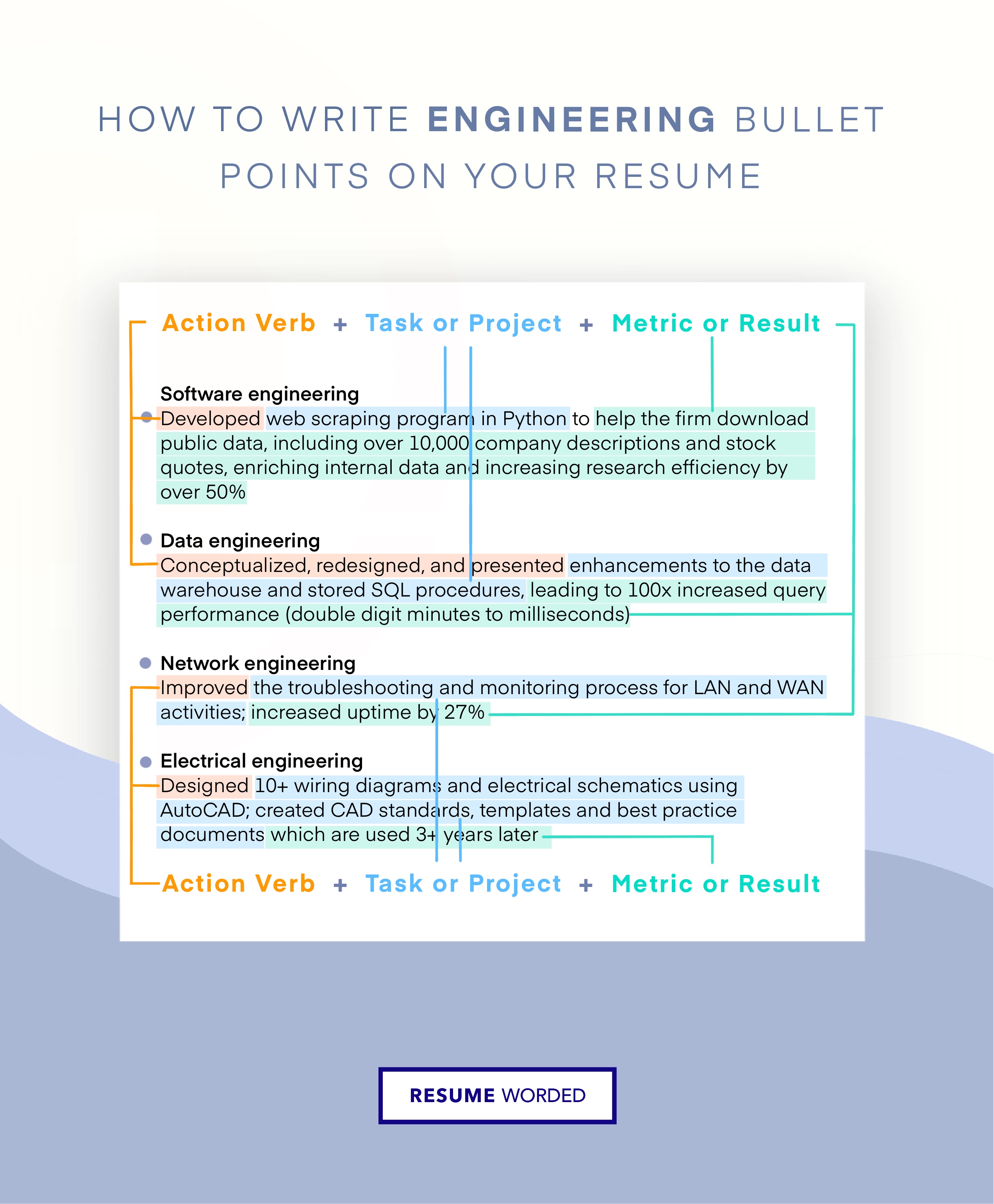
Skills you can include on your Maintenance Technician resume
Template 2 of 4: industrial maintenance technician resume example.
Industrial maintenance technicians work in manufacturing and industrial companies. They focus on the maintenance of industrial equipment and facilities. Industrial maintenance technicians perform hydraulic troubleshooting on equipment for issues that can delay production. You are also responsible for installing and maintaining industrial equipment. That’s why your resume should demonstrate that you have experience with industrial machinery. In addition, you must also monitor sensors and upkeep them.
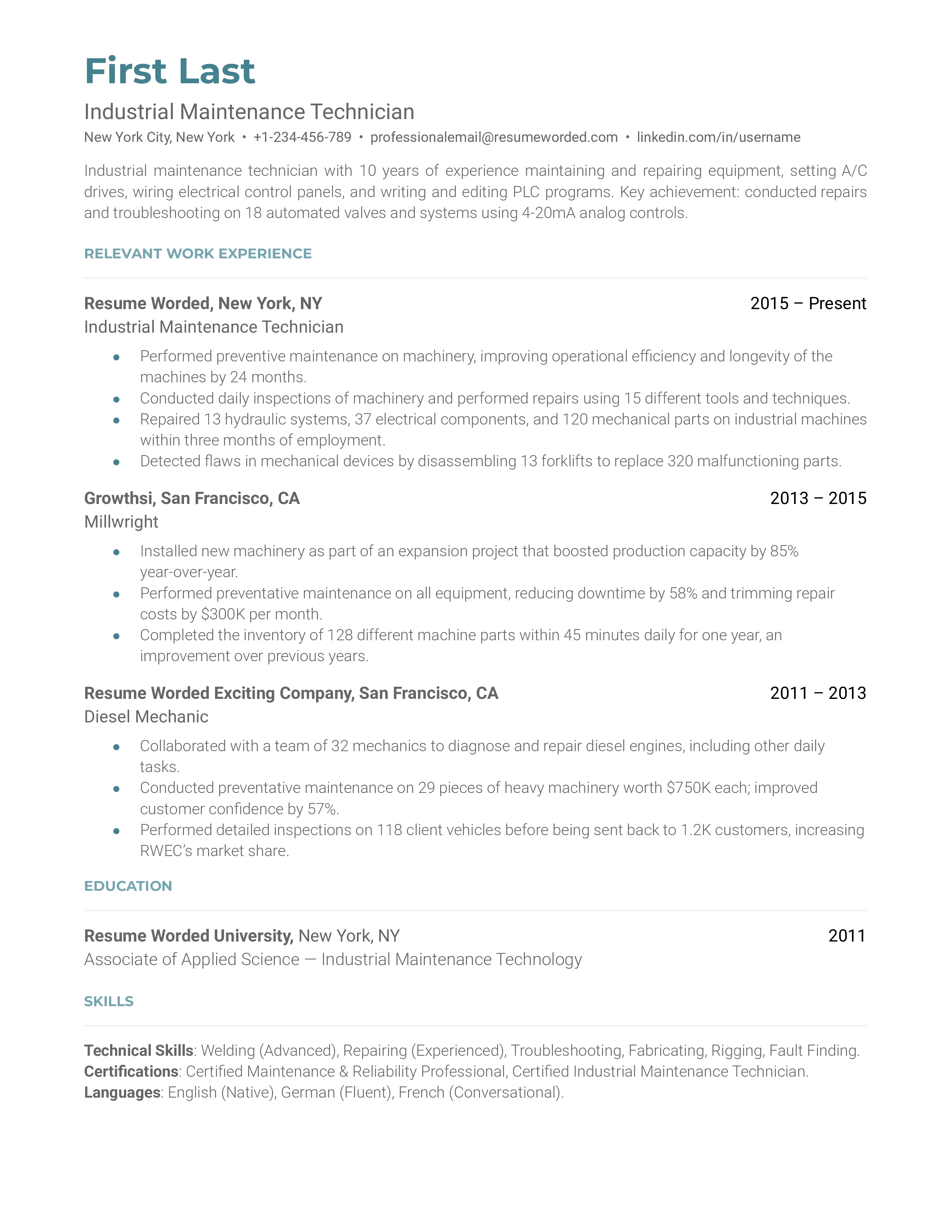
Tips to help you write your Industrial Maintenance Technician resume in 2024
highlight your ability to interpret technical documentation..
When working as an industrial maintenance technician, you will have to interpret technical procedures. That’s why you must be able to read and interpret schematics and blueprints. You must also understand service manuals to maintain machinery. That’s why it is important to mention this in your technical interpretation skills on your resume.
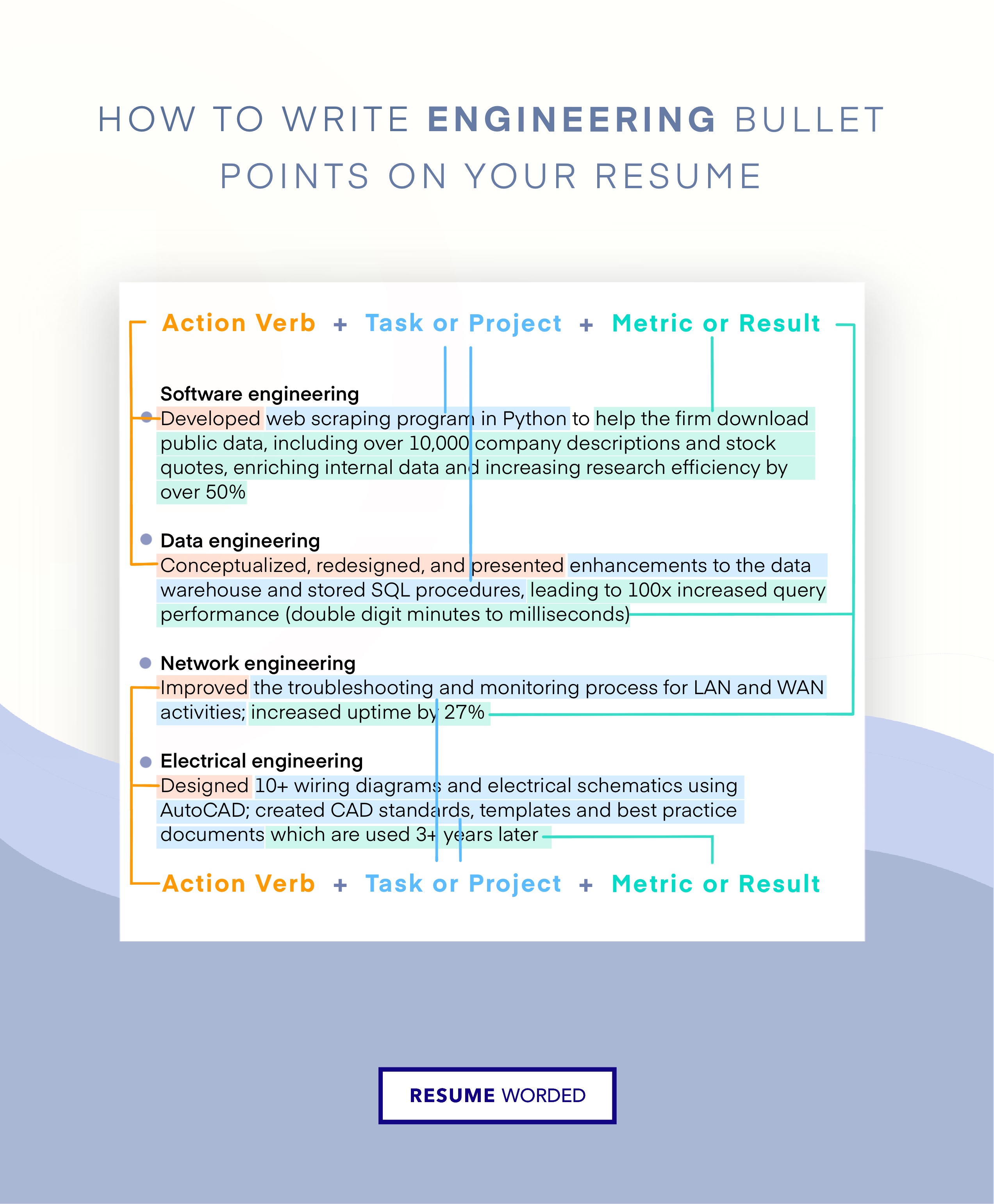
Emphasize your experience in the industrial field.
Your employer might be looking for someone with experience in the industrial field, a technician that can understand how machinery works and how to troubleshoot it. Hence, it’s a good idea to highlight your experience in the industrial field. Besides, your resume might go through ATS systems. They usually look for industry-relevant keywords, so tailoring your resume to the industrial field will give you more job opportunities.
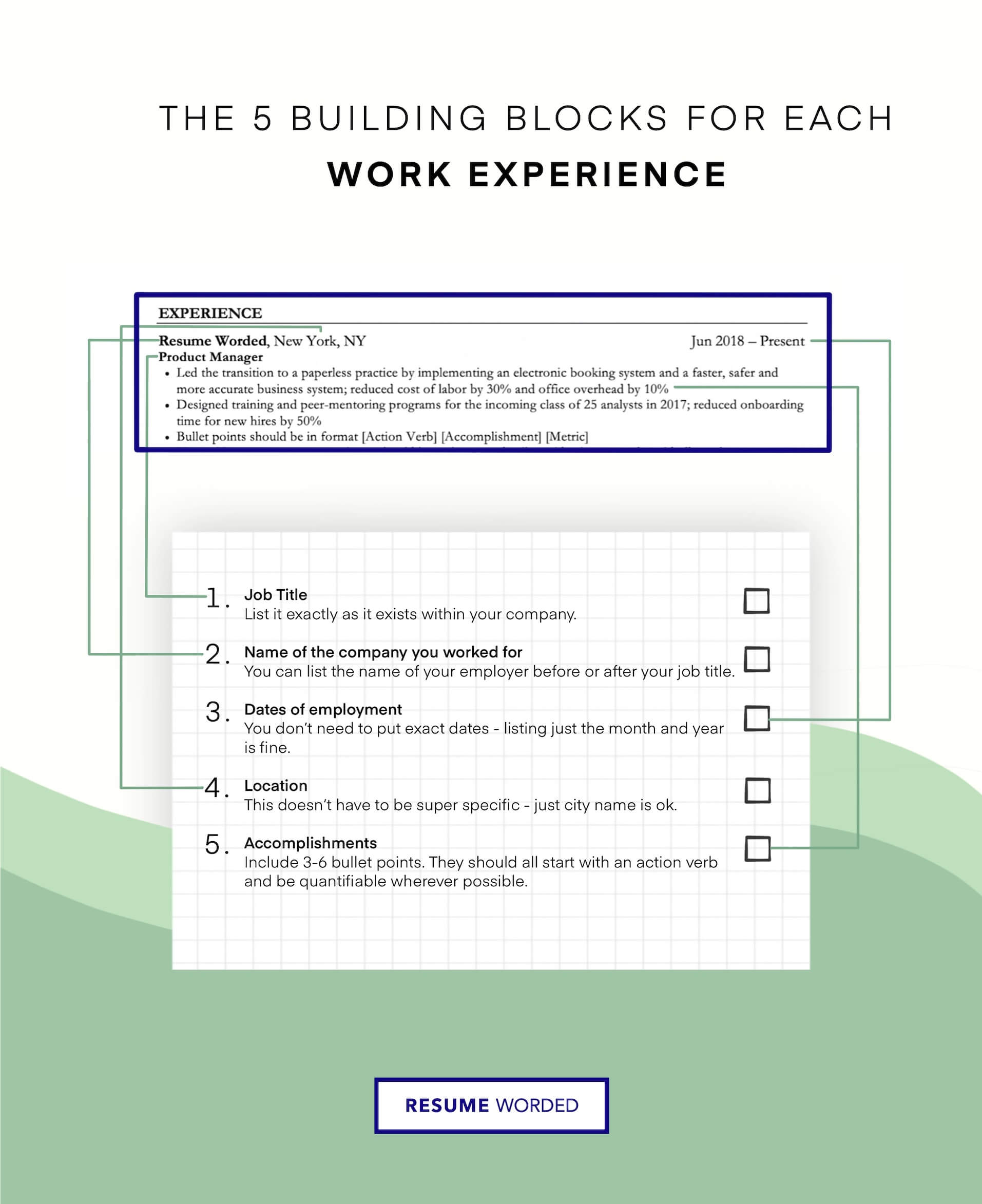
Skills you can include on your Industrial Maintenance Technician resume
Template 3 of 4: maintenance supervisor resume example.
The maintenance supervisor is responsible for ensuring that maintenance procedures and troubleshooting are taken care of adequately in the facility. They monitor other colleagues to evaluate whether they are following security compliance and budgetary standards. They must also keep track of their progress and make sure they stick to a schedule. A maintenance technician must have excellent organizational skills, so it’s important to illustrate that in your resume. You can talk about previous projects that you completed timely and efficient.
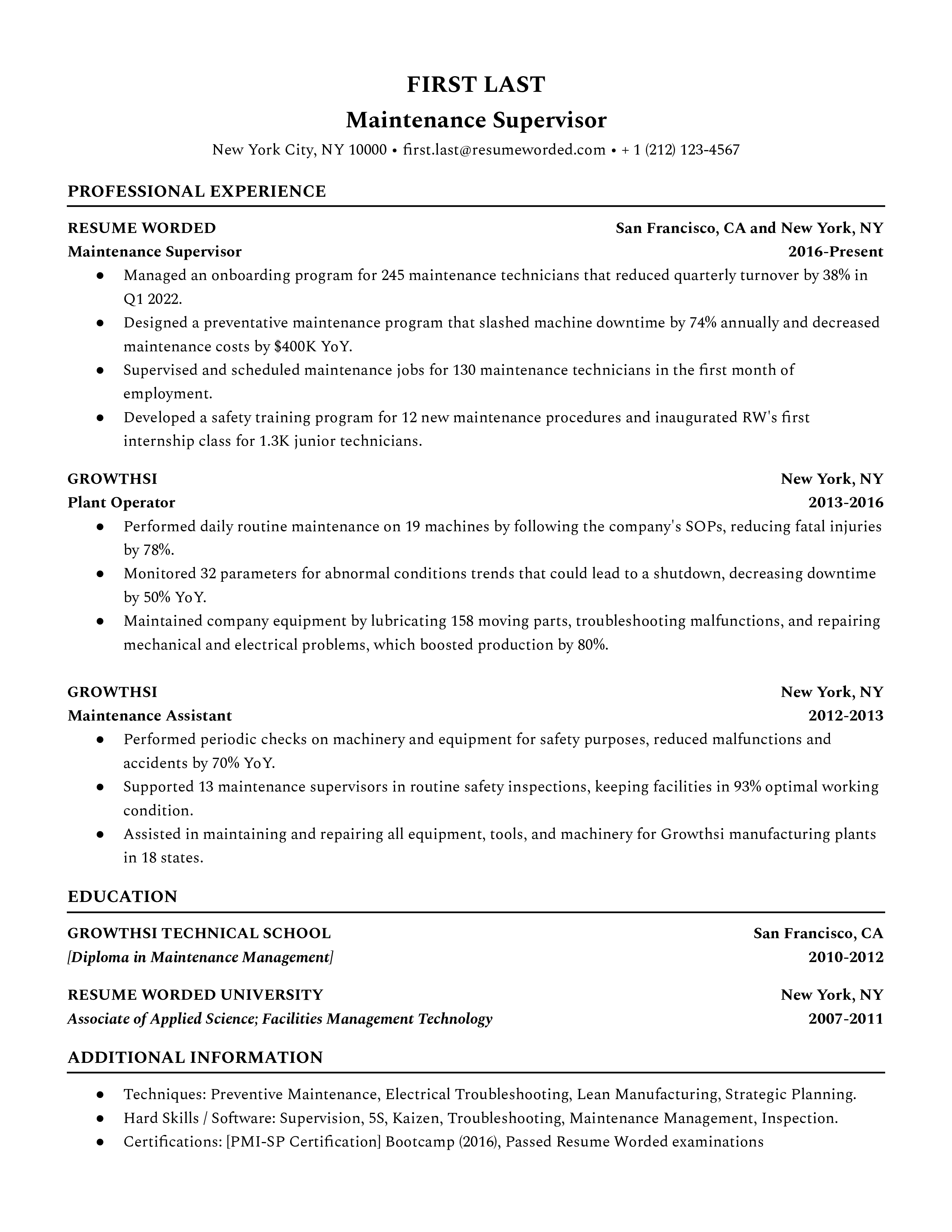
Tips to help you write your Maintenance Supervisor resume in 2024
indicate your ability to hire personnel..
Maintenance supervisors have usually experienced professionals with multiple years of experience in the field. That’s why some employers expect their help in the recruitment process. A good maintenance supervisor has an excellent eye for identifying other high-performing technicians.
Mention your knowledge of security compliance.
As a maintenance supervisor, you must ensure everyone is safe while doing their job. You must be knowledgeable of security compliance and train colleagues. You are responsible for teaching them how to be safe and ensuring they follow these procedures.
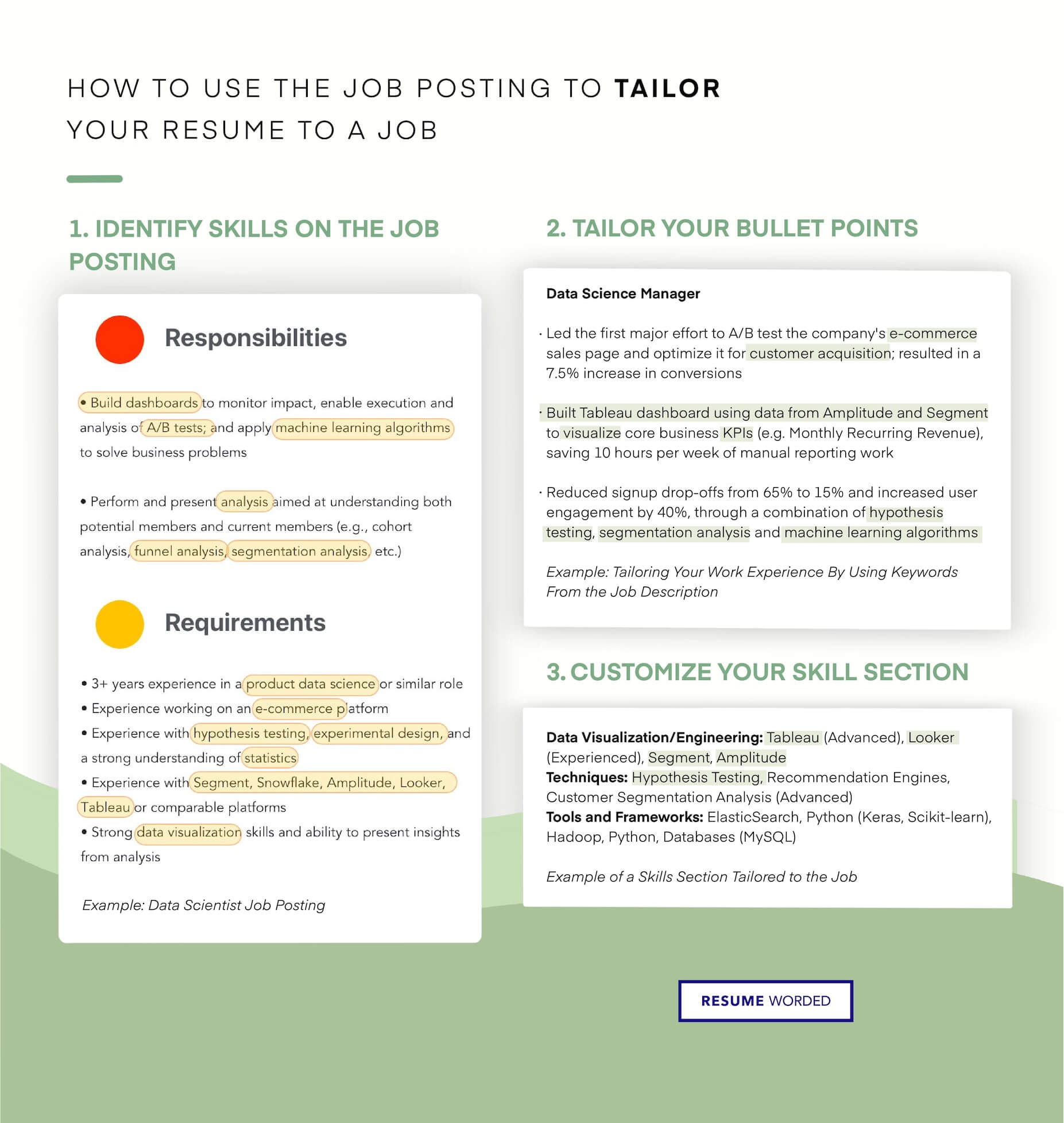
Skills you can include on your Maintenance Supervisor resume
Template 4 of 4: maintenance manager resume example.
A maintenance manager has a broader scope of responsibilities. They carry out inspections in the facility, oversee repair activities, delegate tasks, and coordinate with vendors. Once they’ve identified what they need for a particular facility, they will estimate the costs and negotiate with vendors to get fair deals. Maintenance managers keep track of the progress of the maintenance team and create reports to inform stakeholders about productivity and issues in the building. You must also monitor inventory and equipment. Therefore, adding inventory management skills to your resume might help you stand out.
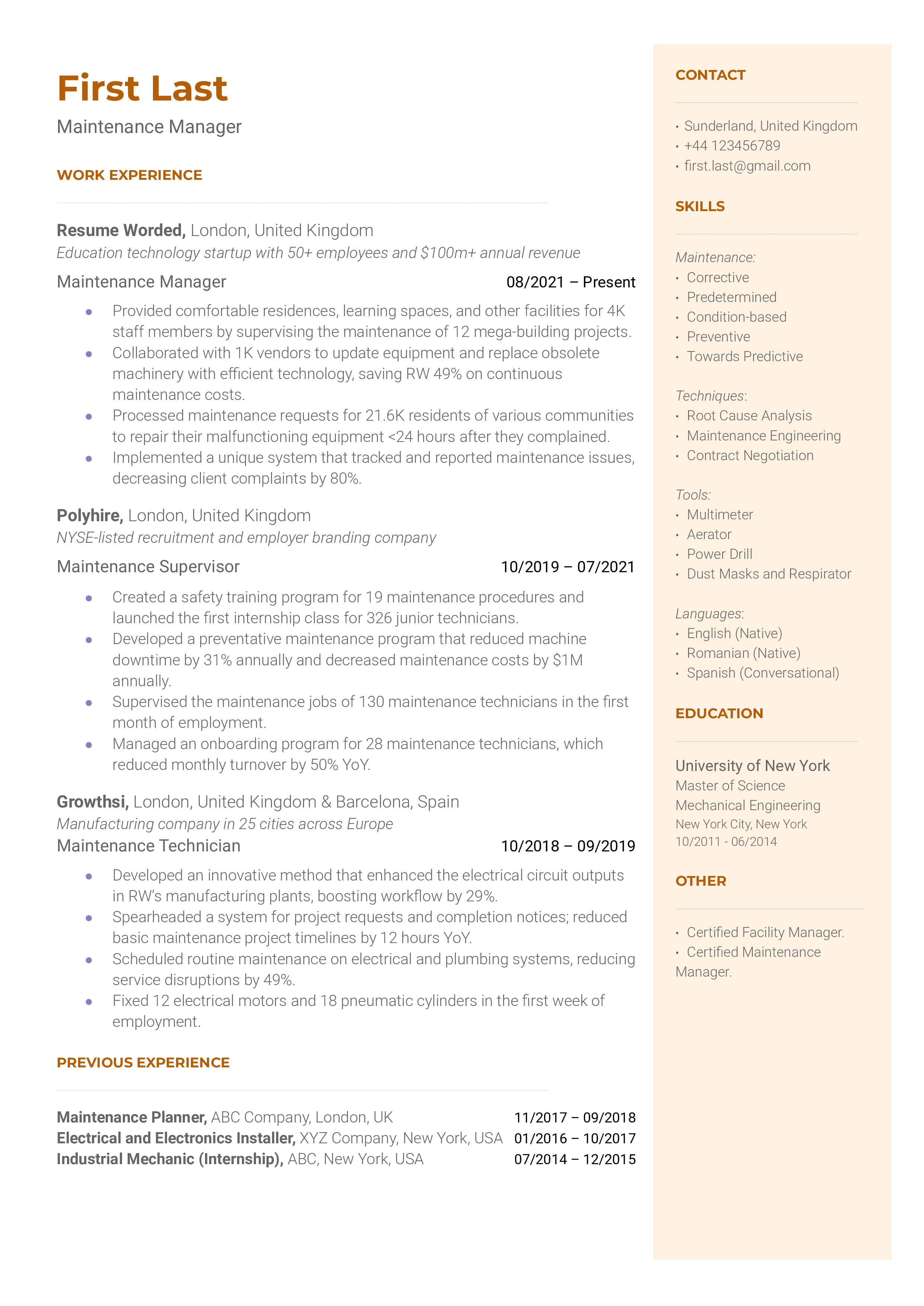
Tips to help you write your Maintenance Manager resume in 2024
demonstrate your ability to lead a technical team..
As a maintenance manager, you must have excellent managerial skills. You will be guiding the team to meet their goals and ensure everyone stays safe during repairs and installations. Your potential employer might be looking for someone with leadership skills, so this is something you can highlight on your resume.
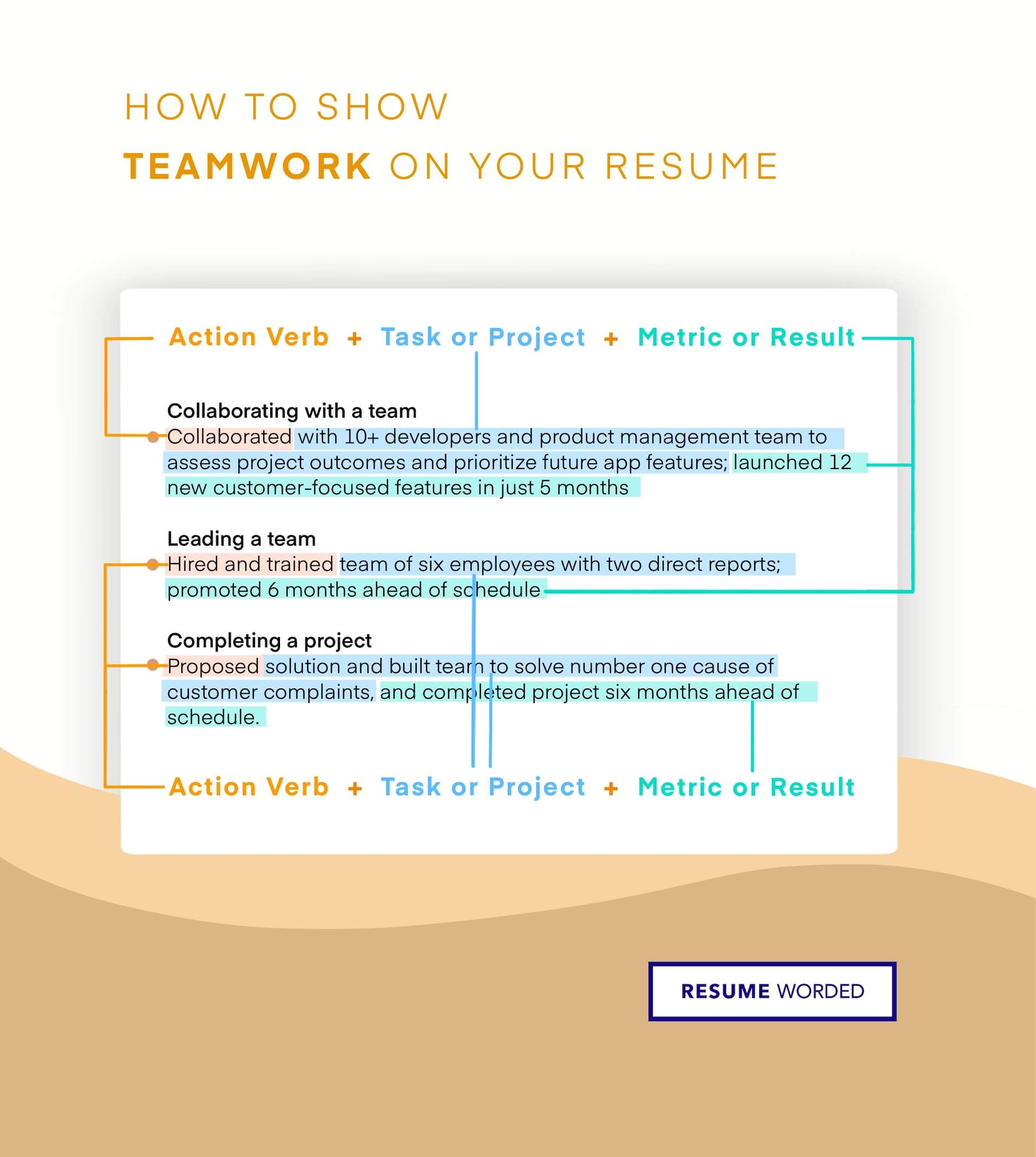
Mention your budgetary skills in your resume.
Maintenance managers estimate expenses and determine the best strategies to meet budgetary goals. That’s why having some basic financial skills is crucial for this role. You must be able to interpret data and come up with efficient solutions to maintain repairs under a budget. You should emphasize this skill in your resume.
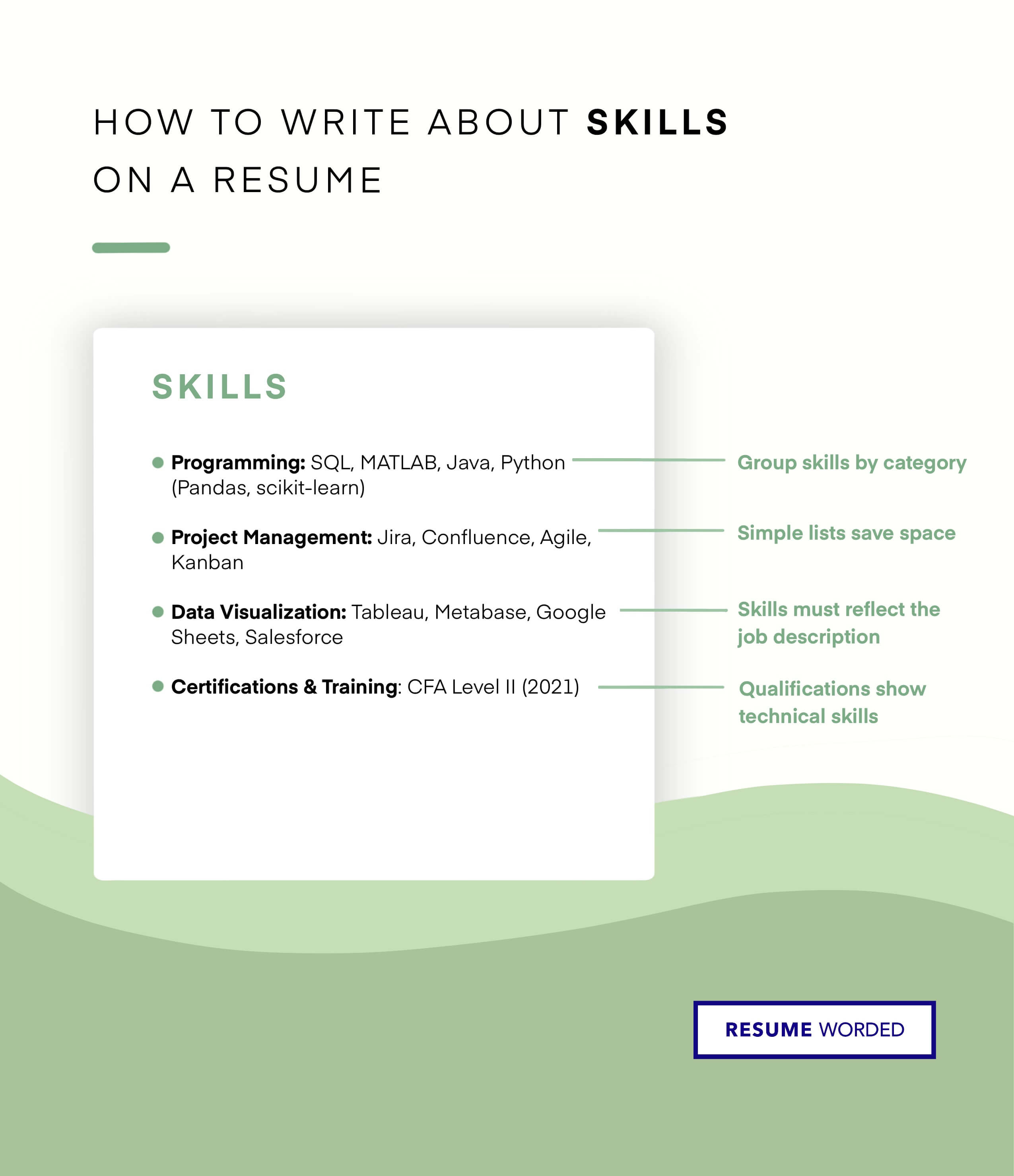
Skills you can include on your Maintenance Manager resume
As a hiring manager who has worked with top companies in the maintenance industry like Johnson Controls, Cushman & Wakefield, and CBRE, I've seen countless resumes for maintenance technician positions. In this article, I'll share insider tips on what makes a resume stand out and get noticed by employers. By following these tips, you can create a strong resume that showcases your skills, experience, and qualifications for the job.
Highlight your technical skills and certifications
Employers want to see that you have the technical skills and knowledge needed for the job. Make sure to:
- List any relevant certifications, such as HVAC, electrical, or plumbing licenses
- Mention specific equipment or systems you have experience with, like chillers, boilers, or building automation systems
- Highlight any specialized training or courses you've completed
Avoid simply listing generic skills without context, like this:
- Technical skills
- Problem-solving
- Good communication
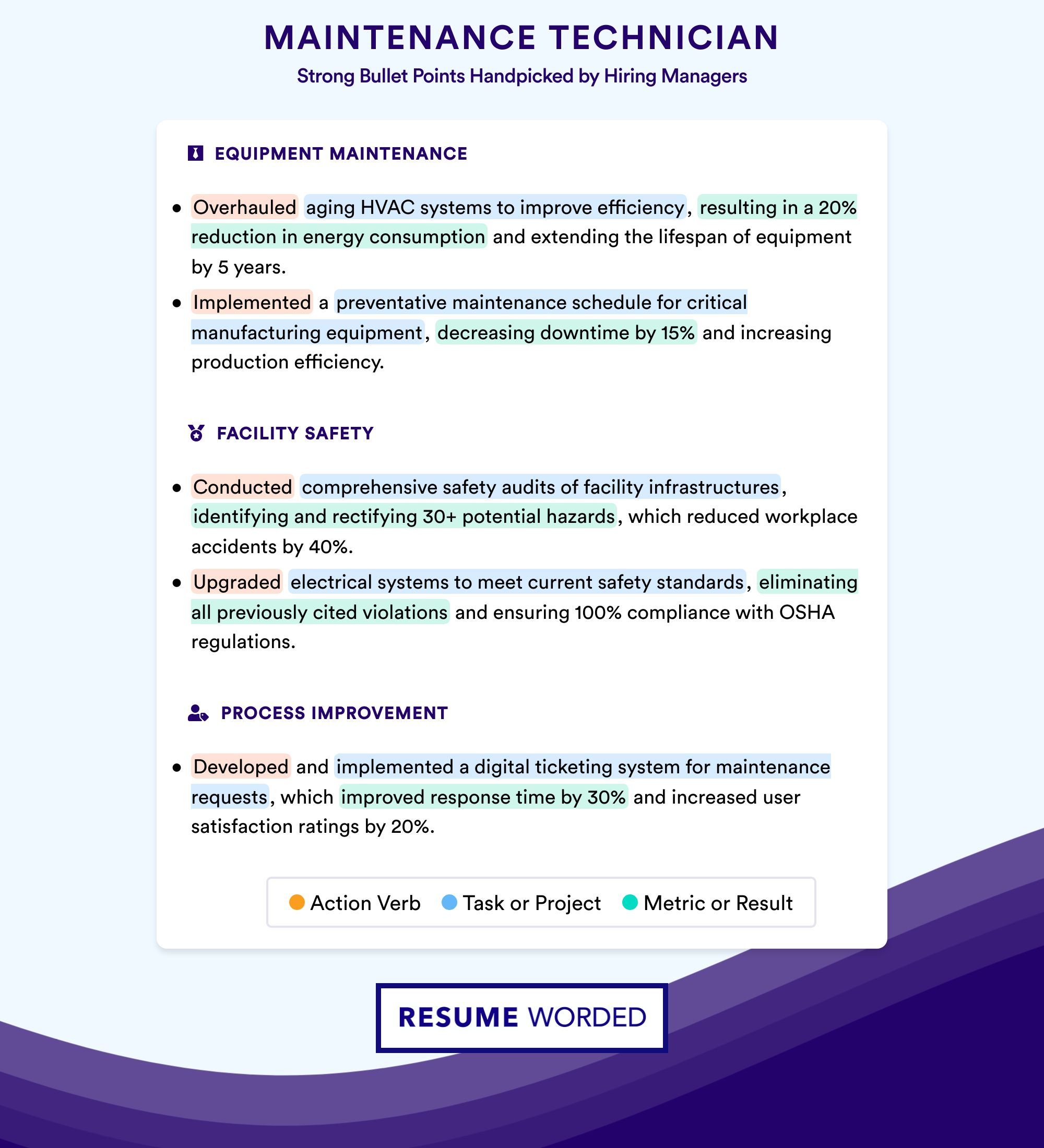
Quantify your accomplishments with metrics
Numbers and data help employers understand the impact you made in previous roles. Where possible, include metrics like:
- Maintained 95% equipment uptime for a 500,000 sq ft facility
- Completed 150+ work orders per month while meeting all SLAs
- Reduced energy costs by 20% through HVAC optimization project
Compare this to a resume statement without metrics:
- Responsible for equipment maintenance and repairs
The specific numbers make your contributions clear and impressive.
Tailor your resume to the job description
Customize your resume for each job you apply to. Carefully review the job posting and include relevant keywords:
- If the job emphasizes preventive maintenance, highlight your PM experience
- For a role that requires a lot of HVAC work, focus on your HVAC skills and certifications
Avoid using the exact same resume for every application. Hiring managers can tell when a resume is generic and hasn't been tailored to the position.
Show your progression and leadership experience
Hiring managers like to see career growth and increasing responsibilities. If you've advanced in your career or taken on leadership roles, make that clear:
- Promoted to Lead Maintenance Technician after two years, managing a team of 5
- Served as Project Manager for major renovation of commercial office space
Even if your job title didn't change, you can show progression in your bullet points:
- Took on additional responsibilities including training new hires and ordering supplies
- Chosen by management to lead special projects based on strong performance
Include relevant project or volunteer experience
Experience doesn't always have to come from paid jobs. If you have relevant project or volunteer experience, include it on your resume. For example:
- Helped rewire community theater's electrical systems during month-long volunteer project
- Completed home renovation project, including plumbing and drywall repairs
This kind of experience shows initiative and practical application of your skills. Just make sure it's related to maintenance work.
Emphasize your problem-solving abilities
Maintenance technicians need to be able to troubleshoot issues and find solutions quickly. Highlight examples of your problem-solving skills:
- Diagnosed and repaired malfunctioning industrial equipment, minimizing production downtime
- Responded to emergency maintenance requests and resolved issues within 2 hours on average
Show that you're someone who can handle the unexpected and keep things running smoothly. Avoid generic statements like:
- Good at fixing things
- Can solve problems
Instead, provide specific examples of how you've used your problem-solving abilities on the job.
Writing Your Maintenance Technician Resume: Section By Section
header, 1. put your name on its own line.
Your name should be the most prominent element in your header, so it's important to put it on its own line. Use a larger font size than the rest of your header to make it stand out.
Here's an example of a well-formatted name in a resume header:
Avoid formatting your name like this:
- JOHN SMITH | 123 Main St, Anytown, USA | 555-555-5555 | [email protected]
2. Include your job title if relevant
If you're an experienced maintenance technician, consider including your job title in your header. This can help quickly communicate your expertise to potential employers.
For example:
- John Smith Experienced Maintenance Technician
However, avoid using job titles that are too long or not directly relevant to the position you're applying for. Stick to a concise, targeted title.
John Smith Maintenance Technician with 5+ Years of Experience in HVAC, Plumbing, Electrical, and Carpentry
3. Use professional contact details
In addition to your name and job title, your header should include your professional contact details. This typically includes:
- Phone number
- Email address
- Location (City, State)
- LinkedIn profile URL (optional)
Make sure to use a professional email address (e.g. [email protected] ) rather than a casual one (e.g. [email protected] ). Also, there's no need to include your full mailing address - just your city and state are sufficient.
Here's an example of well-formatted contact details:
- John Smith Maintenance Technician Anytown, USA | 555-555-5555 | [email protected] | linkedin.com/in/johnsmith
Summary
A resume summary is an optional section that can help provide context about your career goals and highlight your most relevant qualifications. It's especially useful if you're changing careers or have a diverse background that may not be immediately obvious from the rest of your resume. However, it's important to avoid using an objective statement, as these are outdated and often too generic to be effective.
When writing a summary for a maintenance technician position, focus on your technical skills, experience with various equipment and systems, and any specializations or certifications you possess. Keep it concise and targeted to the specific job you're applying for.
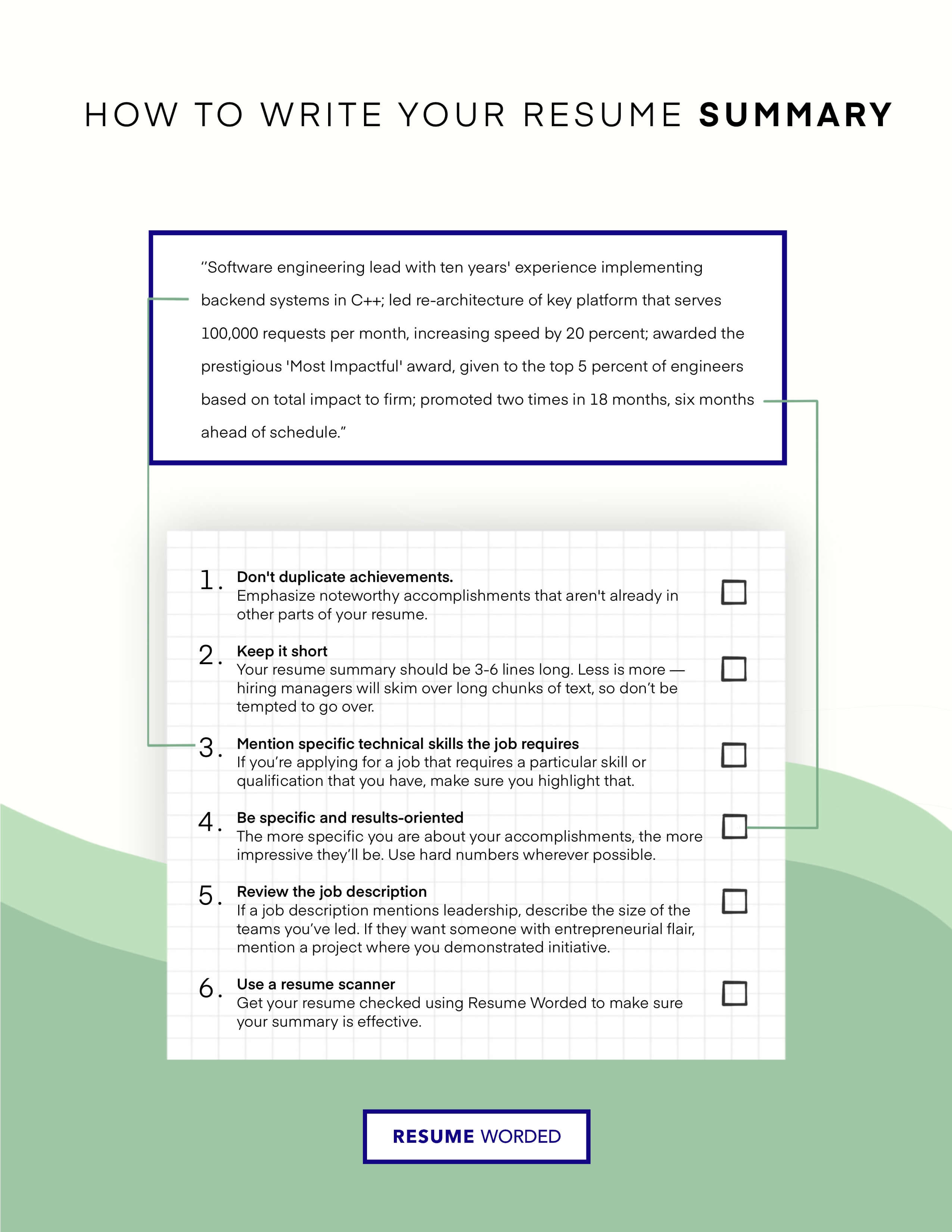
To learn how to write an effective resume summary for your Maintenance Technician resume, or figure out if you need one, please read Maintenance Technician Resume Summary Examples , or Maintenance Technician Resume Objective Examples .
1. Highlight your technical expertise
As a maintenance technician, your technical skills are your greatest asset. Use your summary to showcase your proficiency in areas such as:
- Electrical systems
- Mechanical repairs
- Preventive maintenance
Avoid generic statements like:
- Skilled in various maintenance tasks
- Experienced in repairing equipment
Instead, be specific about the systems and equipment you're familiar with:
- Proficient in troubleshooting and repairing industrial hydraulic systems
- Skilled in maintaining and servicing HVAC units, including chillers and boilers
2. Tailor your summary to the job
While it's tempting to use the same summary for every maintenance technician position, it's more effective to customize it for each job. Review the job description and identify the key skills and experience the employer is looking for. Then, incorporate those elements into your summary.
For example, if the job emphasizes experience with preventive maintenance, your summary might look like this:
Experienced maintenance technician with a strong background in preventive maintenance and a proven track record of reducing equipment downtime by 30%. Skilled in developing and implementing maintenance schedules, conducting inspections, and training junior technicians.
On the other hand, if the job focuses on a specific industry, such as healthcare, you might write:
Certified maintenance technician with 5+ years of experience in healthcare facilities. Proficient in maintaining and repairing medical equipment, ensuring compliance with safety regulations, and collaborating with healthcare professionals to minimize disruptions to patient care.

3. Demonstrate your problem-solving abilities
Maintenance technicians are often called upon to diagnose and solve complex problems. Use your summary to highlight your troubleshooting skills and ability to think critically under pressure.
Avoid vague statements like:
- Good problem-solver
- Able to work independently
Instead, provide specific examples of how you've used your problem-solving skills:
- Developed and implemented a new troubleshooting protocol that reduced average repair times by 25%
- Diagnosed and repaired a critical production line issue, saving the company $50,000 in potential lost revenue
By demonstrating your ability to analyze problems and find effective solutions, you'll show employers that you have the skills they need in a maintenance technician.
Experience
In your work experience section, you have the opportunity to showcase your relevant skills, accomplishments, and impact in previous roles. As a maintenance technician, it's crucial to highlight your technical expertise, problem-solving abilities, and the value you brought to your past employers. Let's break down the key elements to include in your work experience section.
1. Emphasize relevant technical skills
As a maintenance technician, you likely have a wide range of technical skills that are essential to your job. When writing your work experience section, make sure to showcase the specific skills that are most relevant to the position you're applying for.
For example, instead of simply listing your responsibilities, highlight the technical skills you utilized:
- Performed preventive maintenance on HVAC systems, including troubleshooting and repairing compressors, condensers, and evaporators
- Installed and maintained industrial equipment, such as conveyor systems, hydraulic lifts, and pneumatic tools
- Conducted electrical repairs on motors, switches, and control panels, ensuring compliance with NEC standards
2. Quantify your accomplishments
Whenever possible, use metrics to quantify your accomplishments and demonstrate the impact you had in your previous roles. This helps employers understand the scale and significance of your contributions.
Here are some examples:
- Implemented a preventive maintenance program that reduced equipment downtime by 30% and saved the company $50,000 in repair costs
- Completed an average of 25 work orders per week, consistently exceeding the department's target of 20 per week
- Trained and mentored a team of 5 junior technicians, improving overall department efficiency by 20%
In contrast, avoid using vague or generic descriptions:
- Responsible for maintaining equipment
- Worked on various projects
- Helped improve efficiency
3. Highlight promotions and career growth
If you've been promoted or taken on additional responsibilities in your previous roles, make sure to highlight this in your work experience section. This demonstrates your ability to learn, grow, and take on new challenges.
Maintenance Technician, ABC Manufacturing (2018-2022) - Promoted to Lead Maintenance Technician in 2020, overseeing a team of 8 technicians and managing maintenance projects across the facility - Implemented a new computerized maintenance management system (CMMS), streamlining work order processes and improving overall maintenance efficiency by 25% - Developed and delivered training programs on safety procedures and equipment operation, reducing accidents and injuries by 40%
4. Tailor your experience to the job description
When applying for a specific maintenance technician position, make sure to tailor your work experience section to the requirements and responsibilities listed in the job description. This shows employers that you have the relevant skills and experience they're looking for.
For example, if the job description emphasizes experience with preventive maintenance and HVAC systems, focus on highlighting your related experience:
- Developed and implemented a comprehensive preventive maintenance program for HVAC systems, reducing unexpected breakdowns by 50%
- Conducted regular inspections and maintenance on chillers, boilers, and air handling units, ensuring optimal performance and energy efficiency
Before finalizing your resume, consider using a tool like Targeted Resume to check if your resume has the right skills and keywords for the specific job you're applying for. This can help ensure that your resume is well-aligned with the job requirements and more likely to catch the attention of hiring managers.
Education
The education section is a critical part of your maintenance technician resume. It shows hiring managers you have the right training and knowledge. Follow these tips to make your education section stand out.
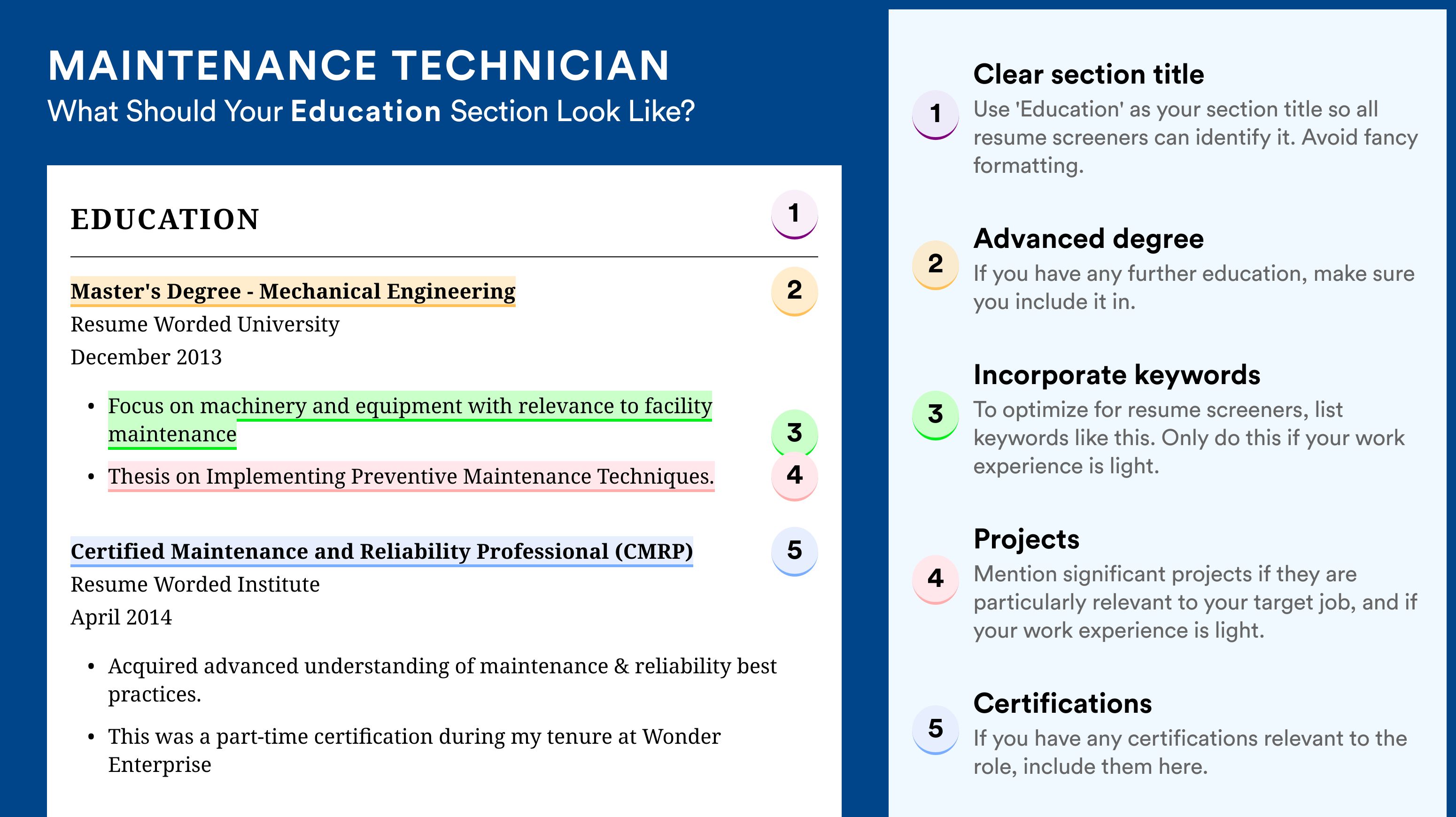
1. Show your highest level of education first
List your education in reverse chronological order, with your most recent or highest degree first. This quickly shows hiring managers your educational background.
Here's an example of how to format your education:
Bachelor of Science in Mechanical Engineering University of Texas, Austin, TX Graduated: May 2020
If you have multiple degrees, list them in order of highest to lowest level.
2. Include relevant coursework and projects
If you're a recent graduate or have limited work experience, highlight relevant coursework and projects. This shows you have hands-on experience with maintenance topics.
Bad example:
- Relevant coursework: Intro to Engineering, Calculus I, English Composition
Good example:
- Relevant coursework: Fluid Mechanics, Thermodynamics, Mechanical Design
- Senior Project: Designed and built a robotic arm using hydraulic systems
3. List certifications and licenses
Many maintenance technician roles require specific certifications or licenses. If you have them, include them in your education section to make them prominent.
Examples of certifications to list:
- EPA Section 608 Technician Certification
- OSHA 30-Hour General Industry Certification
- Certified Maintenance & Reliability Technician (CMRT)
4. Keep it concise for senior-level roles
If you're a senior maintenance technician with years of experience, your education section can be brief. Hiring managers will be more interested in your work history.
Here's what not to do:
Bachelor of Science in Mechanical Engineering University of Texas, Austin, TX Graduated: May 1995 Relevant coursework: Fluid Mechanics, Thermodynamics, Mechanical Design GPA: 3.5
Instead, keep it short and sweet:
BS, Mechanical Engineering, University of Texas
Action Verbs For Maintenance Technician Resumes
A good maintenance technician is diligent and proactive, so that’s the impression you should give in your resume. A great way to do that is by using an appropriate vocabulary that illustrates your accountability. Action verbs can help you achieve that, so use them when mentioning your accomplishments and duties in previous roles.
These are past-tensed words that can be used at the beginning of a phrase. By using the right action verbs you will elevate your readability and make a good impression. Remember to use always different verbs to enrich the vocabulary you use on your resume. It is important to avoid repetition.
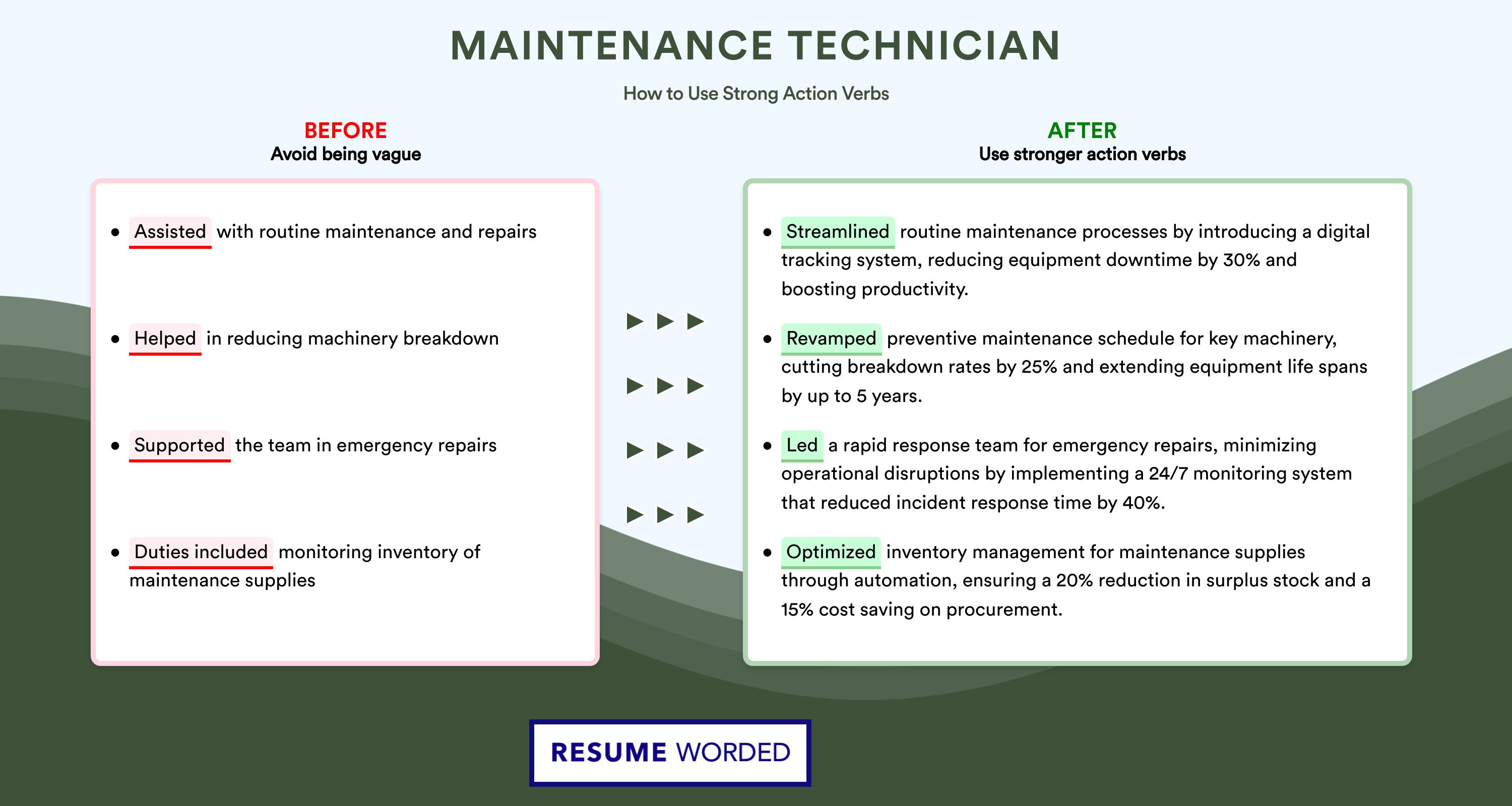
- Restructured
- Strengthened
- Troubleshooted
- Systematized
For a full list of effective resume action verbs, visit Resume Action Verbs .
Action Verbs for Maintenance Technician Resumes
Skills for maintenance technician resumes.
Your maintenance technician resume should demonstrate you have a qualified skillset in multiple disciplines such as carpentry, plumbing, structural repairs, etc. Maintenance technicians perform multiple tasks to upkeep a building, so your employer might want to know you are skillful in various areas. Use your skills section to showcase your value.
If you need some help with relevant skills to include in your resume, check out our list below. We have compiled some suitable maintenance technician skills you can use. Remember that you can also check your potential employer’s job post to discover more competencies they seek.
- Aircraft Maintenance
- Airworthiness
- Aircraft Systems
- Commercial Aviation
- Flight Safety
- Line Maintenance
- Maintenance & Repair
- Maintenance
- Aeronautics
- Aircraft Engines
How To Write Your Skills Section On a Maintenance Technician Resumes
You can include the above skills in a dedicated Skills section on your resume, or weave them in your experience. Here's how you might create your dedicated skills section:
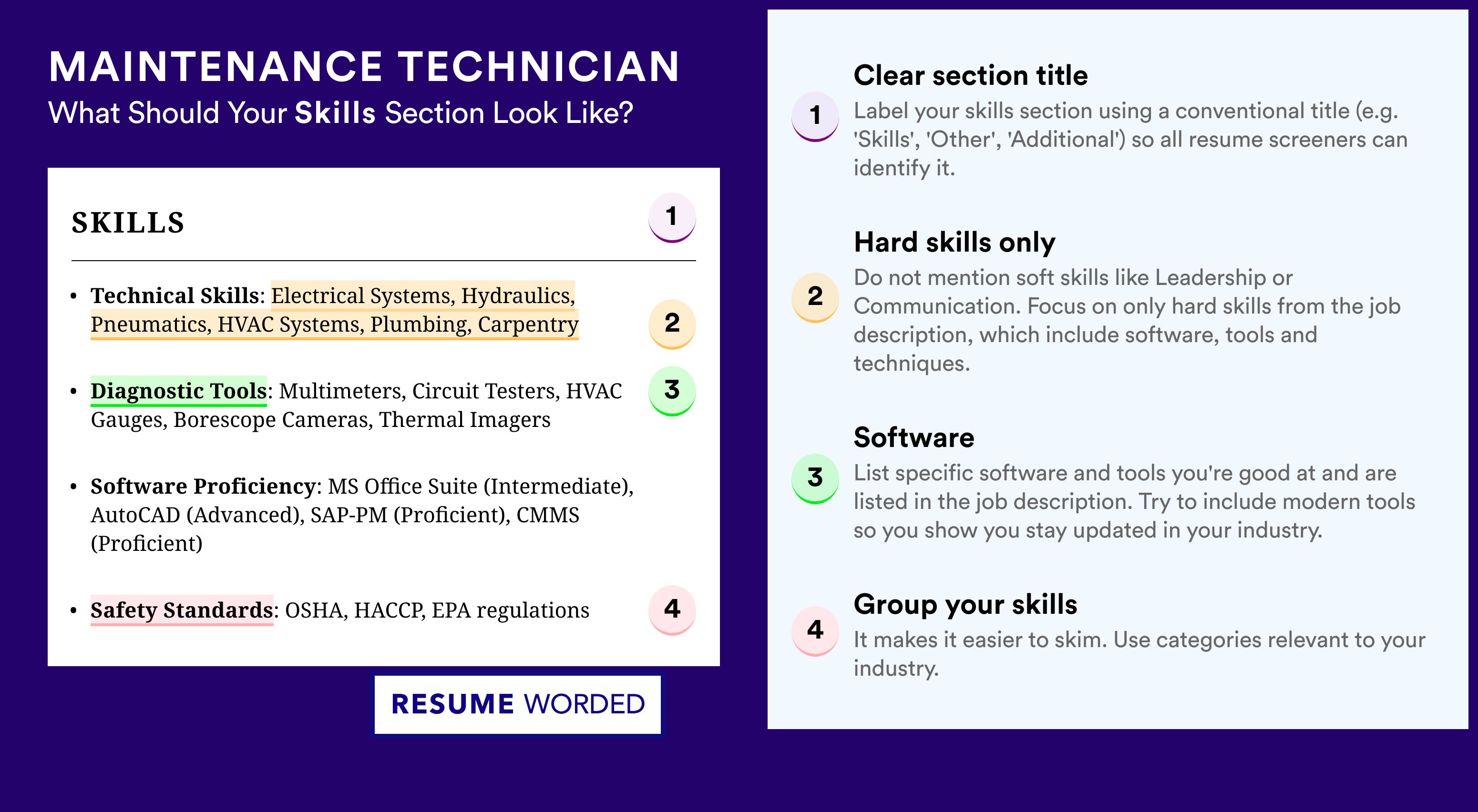
Skills Word Cloud For Maintenance Technician Resumes
This word cloud highlights the important keywords that appear on Maintenance Technician job descriptions and resumes. The bigger the word, the more frequently it appears on job postings, and the more 'important' it is.
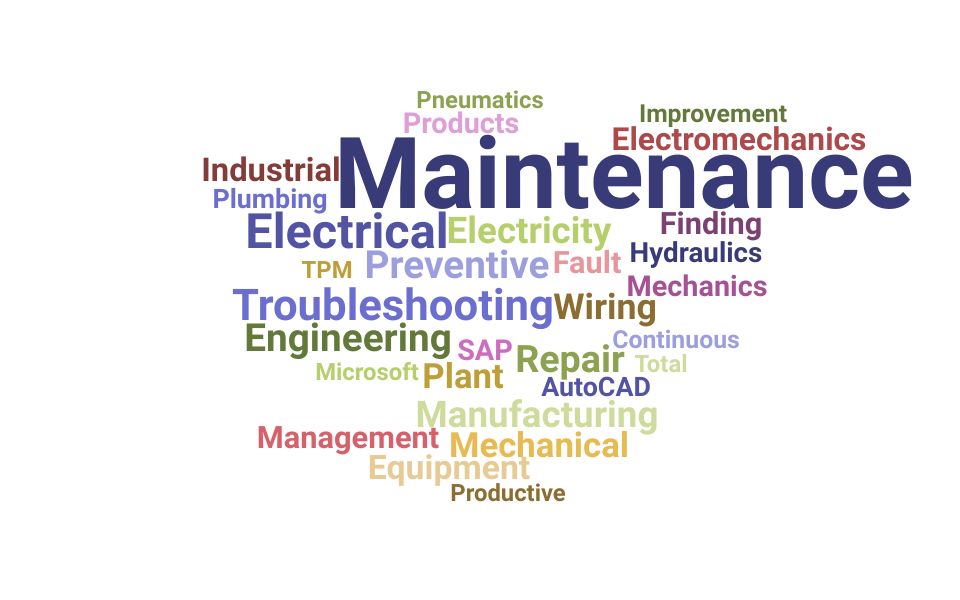
How to use these skills?
Other engineering resumes.
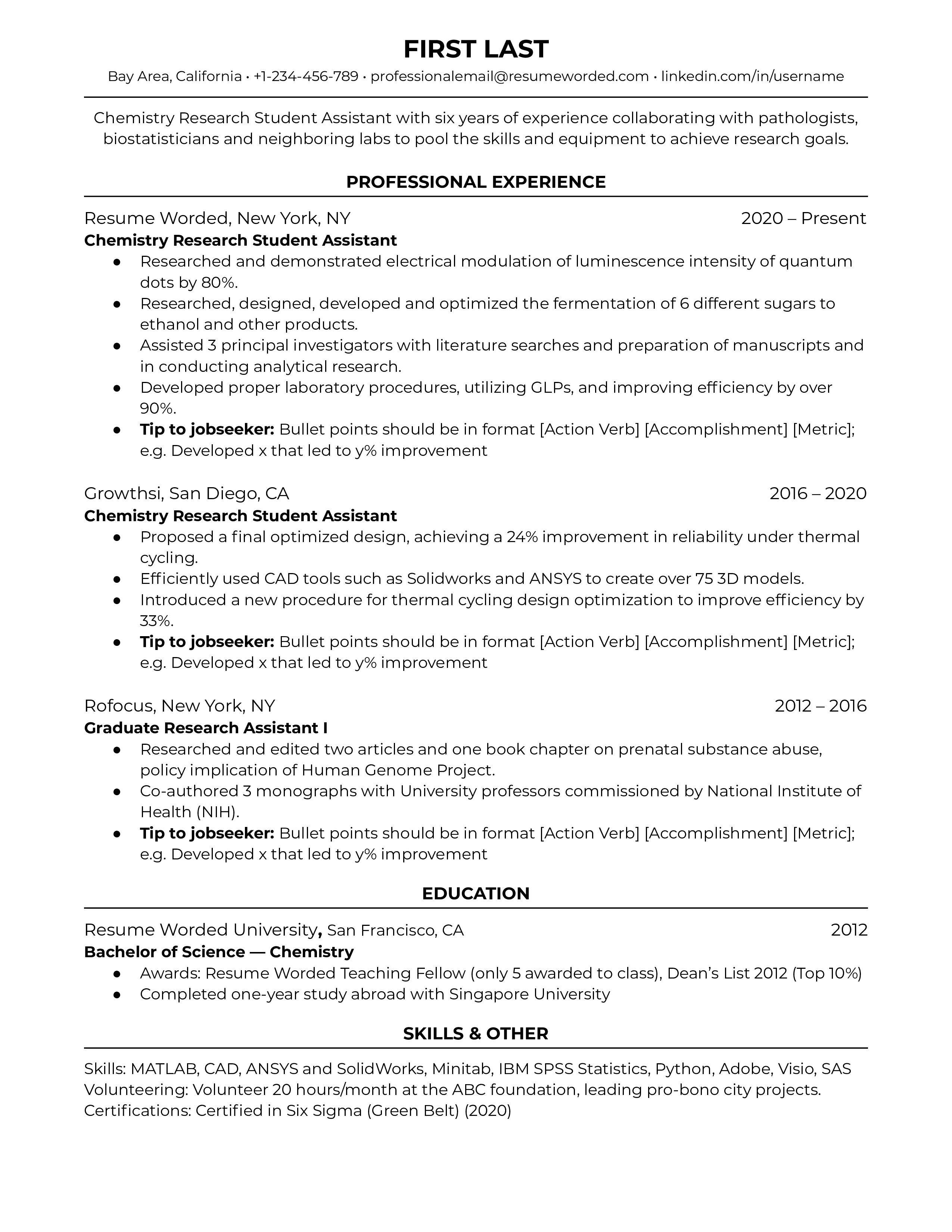
Quality Control
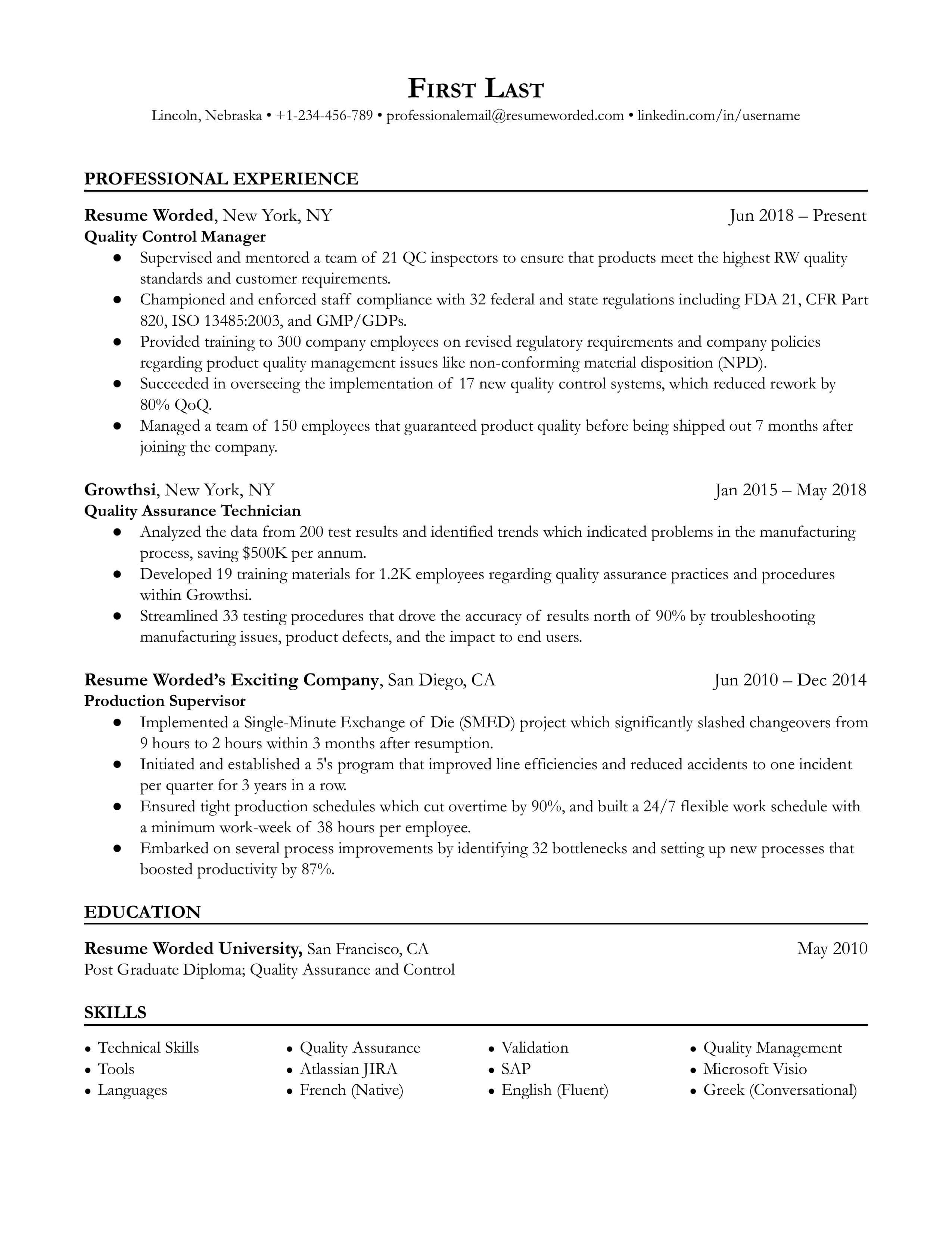
Service Desk
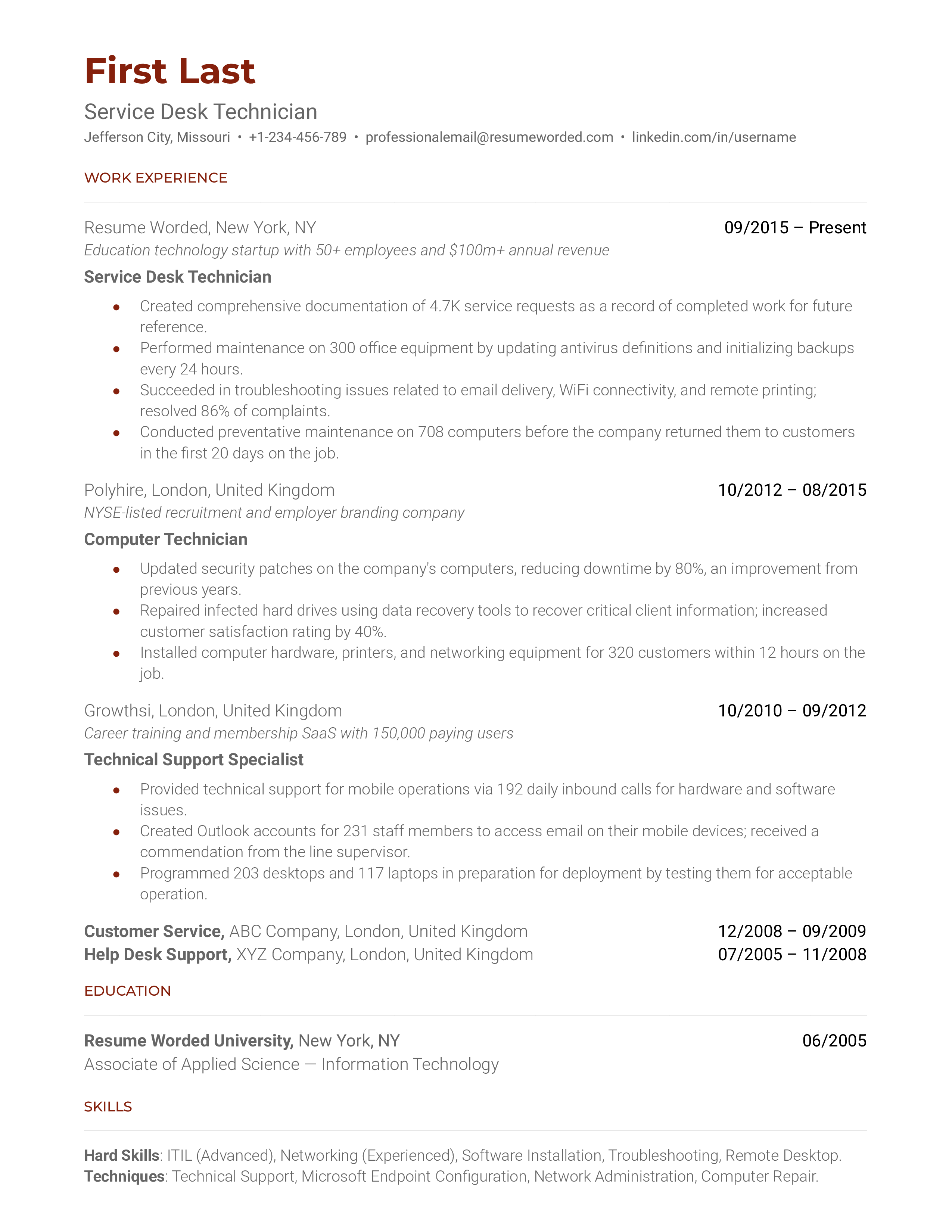
- Software Engineer Resume Guide
- Software Developer Resume Guide
- Web Developer Resume Guide
- Programmer Resume Guide
- Front End Developer Resume Guide
- DevOps Resume Guide
- Full Stack Developer Resume Guide
- Java Developer Resume Guide
- Python Developer Resume Guide
- IT Manager Resume Guide
- Cyber Security Resume Guide
- Salesforce Resume Guide
- Quality Assurance Resume Guide
- Quality Engineer Resume Guide
- Electrical Engineer Resume Guide
- System Administrator Resume Guide
- Scrum Master Resume Guide
- Civil Engineer Resume Guide
- Network Administrator Resume Guide
- Mechanical Engineer Resume Guide
- Manufacturing Engineer Resume Guide
- Network Engineer Resume Guide
- Node.js Resume Guide
- SQL Developer Resume Guide
- Integration Architect Resume Guide
- Engineering Manager Resume Guide
- Software Tester Resume Guide
- Service Technician Resume Guide
- Platform Engineer Resume Guide
- Automation Engineer Resume Guide
- C, C++, and C# Developer Resume Guide
- Technical Support Resume Guide
- Project Engineer Resume Guide
- Security Manager Resume Guide
- Electronic Technician Resume Guide
- System Engineer Resume Guide
- IT Specialist Resume Guide
- Packaging Engineer Resume Guide
- Oracle Resume Guide
- Planning Engineer Resume Guide
- Blockchain Resume Guide
- Cloud Developer Resume Guide
- ETL Developer Resume Guide
- SharePoint Developer Resume Guide
- Kafka Resume Guide
- Audio Engineer Resume Guide
- HVAC Resume Guide
- Industrial Engineer Resume Guide
Maintenance Technician Resume Guide
- Solutions Architect Resume Guide
- Implementation Specialist Resume Guide
- Software Architect Resume Guide
- PHP Developer Resume Guide
- Biomedical Engineer Resume Guide
- Robotics Resume Guide
- Chief Digital Officer Resume Guide
- Innovation Resume Guide
- Security Analyst Resume Guide
- IT Auditor Resume Guide
- Director of Software Engineering Resume Guide
- Environmental Engineer Resume Guide
- Technology Director Resume Guide
- Director of Information Technology Resume Guide
- AWS Resume Guide
- Director of Engineering Resume Guide
- Materials Engineer Resume Guide
- UAT Tester Resume Guide
- Maintenance Technician Resume Example
- Industrial Maintenance Technician Resume Example
- Maintenance Supervisor Resume Example
- Maintenance Manager Resume Example
- Tips for Maintenance Technician Resumes
- Skills and Keywords to Add
- All Resume Examples
- Maintenance Technician CV Examples
- Maintenance Technician Cover Letter
- Maintenance Technician Interview Guide
- Explore Alternative and Similar Careers
Download this PDF template.
Creating an account is free and takes five seconds. you'll get access to the pdf version of this resume template., choose an option..
- Have an account? Sign in
E-mail Please enter a valid email address This email address hasn't been signed up yet, or it has already been signed up with Facebook or Google login.
Password Show Your password needs to be between 6 and 50 characters long, and must contain at least 1 letter and 1 number. It looks like your password is incorrect.
Remember me
Forgot your password?
Sign up to get access to Resume Worded's Career Coaching platform in less than 2 minutes
Name Please enter your name correctly
E-mail Remember to use a real email address that you have access to. You will need to confirm your email address before you get access to our features, so please enter it correctly. Please enter a valid email address, or another email address to sign up. We unfortunately can't accept that email domain right now. This email address has already been taken, or you've already signed up via Google or Facebook login. We currently are experiencing a very high server load so Email signup is currently disabled for the next 24 hours. Please sign up with Google or Facebook to continue! We apologize for the inconvenience!
Password Show Your password needs to be between 6 and 50 characters long, and must contain at least 1 letter and 1 number.
Receive resume templates, real resume samples, and updates monthly via email
By continuing, you agree to our Terms and Conditions and Privacy Policy .
Lost your password? Please enter the email address you used when you signed up. We'll send you a link to create a new password.
E-mail This email address either hasn't been signed up yet, or you signed up with Facebook or Google. This email address doesn't look valid.
Back to log-in
These professional templates are optimized to beat resume screeners (i.e. the Applicant Tracking System). You can download the templates in Word, Google Docs, or PDF. For free (limited time).
access samples from top resumes, get inspired by real bullet points that helped candidates get into top companies., get a resume score., find out how effective your resume really is. you'll get access to our confidential resume review tool which will tell you how recruiters see your resume..
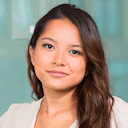
Writing an effective resume has never been easier .
Upgrade to resume worded pro to unlock your full resume review., get this resume template (+ 3 others), plus proven bullet points., for a small one-time fee, you'll get everything you need to write a winning resume in your industry., here's what you'll get:.
- 📄 Get the editable resume template in Google Docs + Word . Plus, you'll also get all 3 other templates .
- ✍️ Get sample bullet points that worked for others in your industry . Copy proven lines and tailor them to your resume.
- 🎯 Optimized to pass all resume screeners (i.e. ATS) . All templates have been professionally designed by recruiters and 100% readable by ATS.
Buy now. Instant delivery via email.
instant access. one-time only., what's your email address.

I had a clear uptick in responses after using your template. I got many compliments on it from senior hiring staff, and my resume scored way higher when I ran it through ATS resume scanners because it was more readable. Thank you!
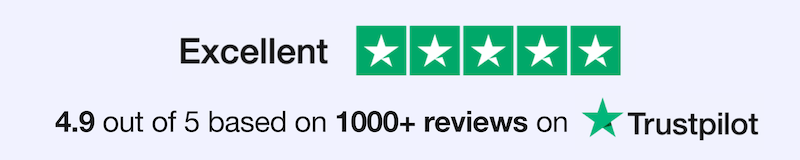
Thank you for the checklist! I realized I was making so many mistakes on my resume that I've now fixed. I'm much more confident in my resume now.
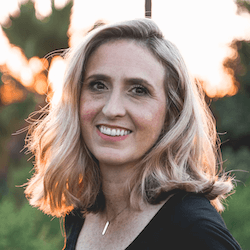
- • Led a team of 5 technicians in the preventive maintenance of electrical systems, improving plant reliability by 30% over one year
- • Implemented a predictive maintenance program that decreased equipment failure rates by 25% and enhanced operational efficiency
- • Conducted advanced troubleshooting and root cause analysis on complex control systems, reducing downtime by 20%
- • Developed and executed a specialized training program for plant operators, enhancing the team's technical skill set
- • Managed cross-functional initiatives to align electrical maintenance with environmental and safety standards, achieving a record of zero non-compliance incidents in two years
- • Spearheaded a project to retrofit existing equipment with updated instrumentation, resulting in a 15% reduction in energy consumption
- • Oversaw daily maintenance tasks and coordinated the workflow for a team of 10, improving operational throughput by 10%
- • Evaluated and optimized plant maintenance schedules, which increased the mean time between failure (MTBF) by 40%
- • Developed and maintained relationships with vendors, which led to a 15% cost reduction in maintenance supplies over two years
- • Updated the plant's environmental health and safety (EHS) program, leading to a 50% reduction in reportable incidents
- • Implemented a technology upgrade for the Distributed Control System (DCS), enhancing monitoring capabilities and operational control
- • Managed instrumentation calibration and maintenance, ensuring 98% accuracy across all measurements
- • Executed emergency repairs on critical instrumentation, limiting unplanned downtime to under 1%
- • Contributed to a company-wide initiative to standardize control systems, improving consistency in operations
- • Coordinated with the operations team to effectively manage plant upset events with a 100% success rate in emergency response
5 Maintenance Technician Resume Examples & Guide for 2024
Your maintenance technician resume needs to prominently feature your technical prowess. Be sure to include the range of machinery or systems you're adept at repairing. It's also essential to highlight your problem-solving skills. Employers value technicians who can quickly diagnose and rectify issues, minimizing downtime.
All resume examples in this guide
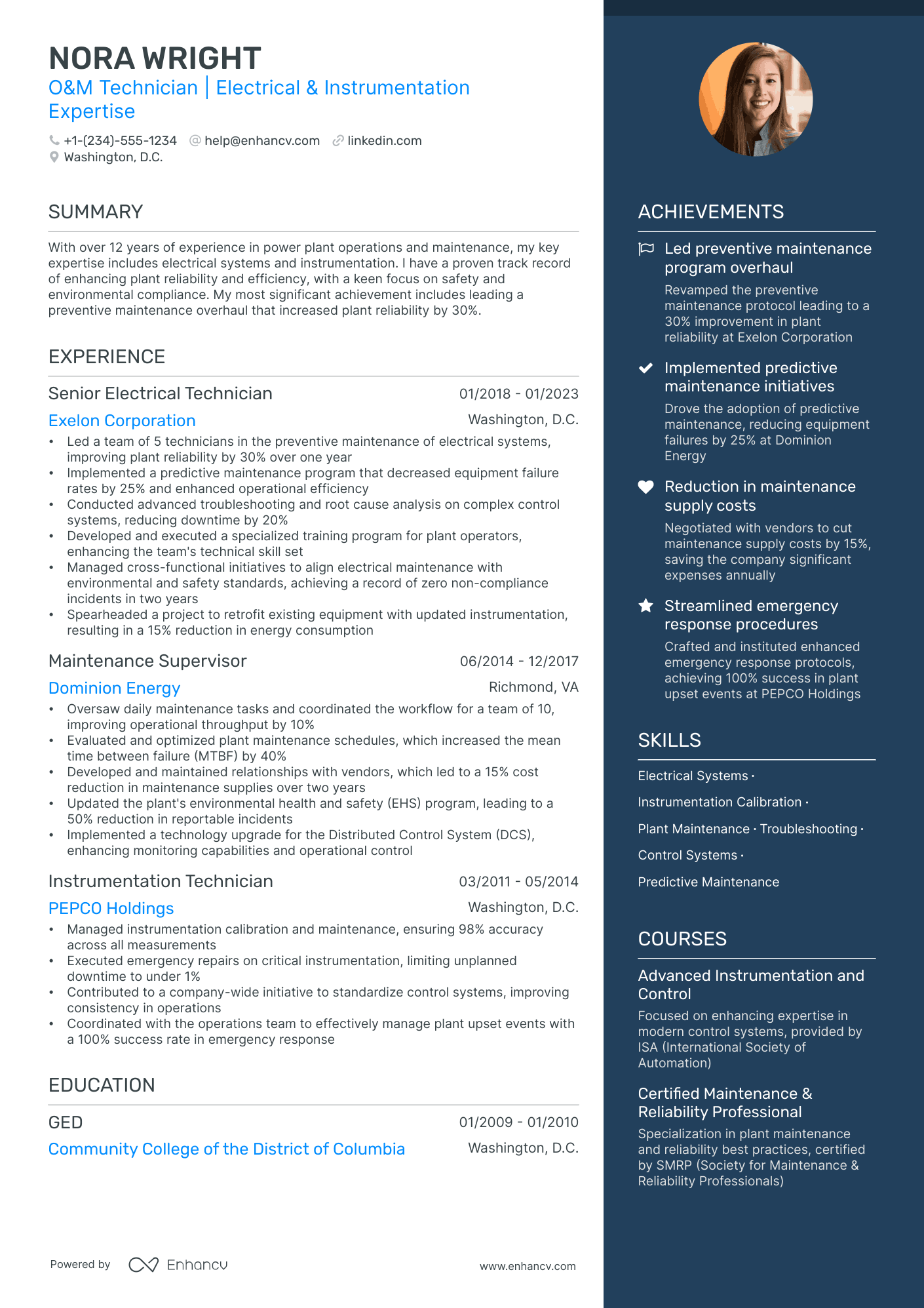
Traditional
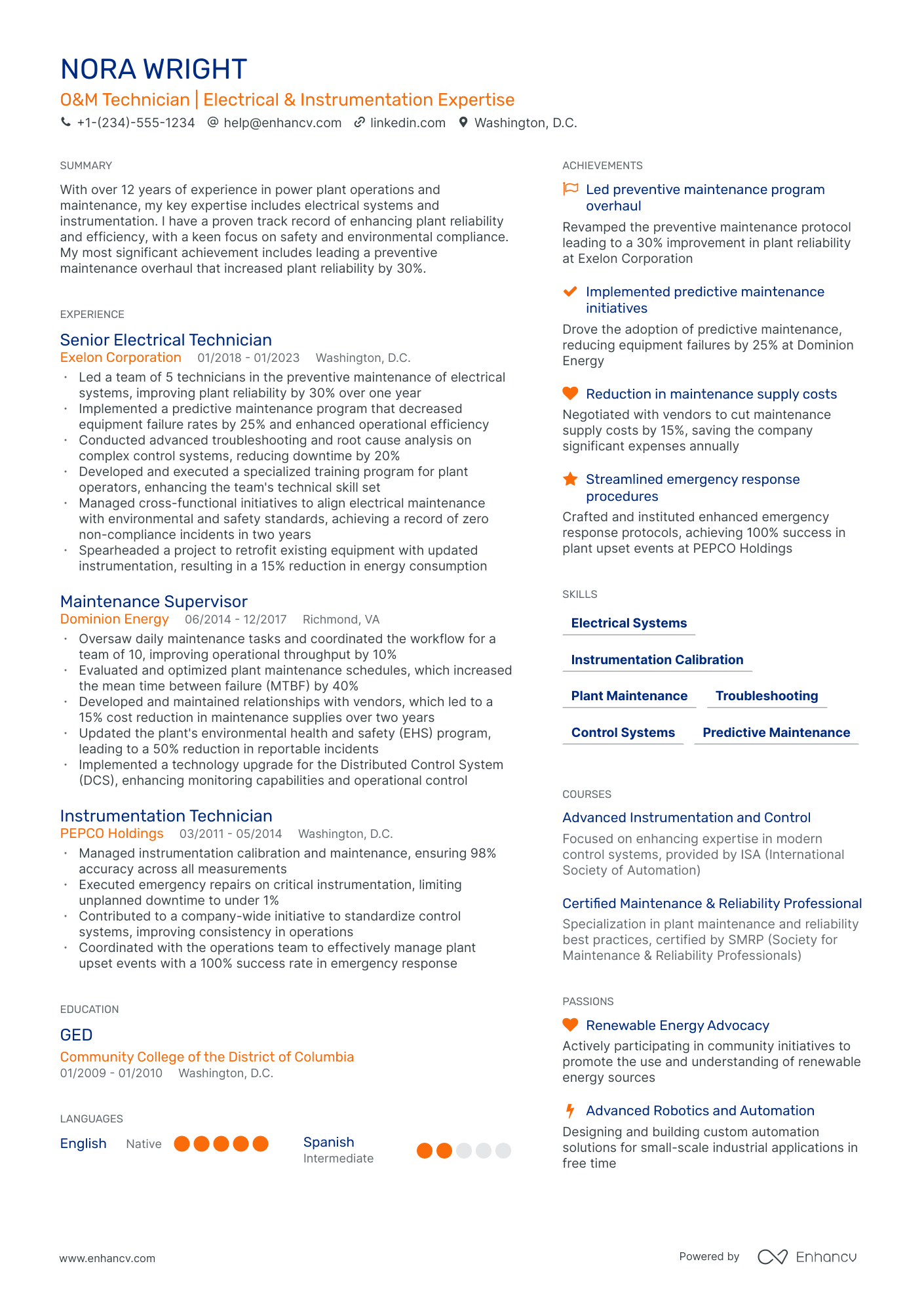
Resume Guide
Resume Format Tips
Resume Experience
Skills on Resume
Education & Certifications
Resume Summary Tips
Additional Resume Sections
Key Takeaways
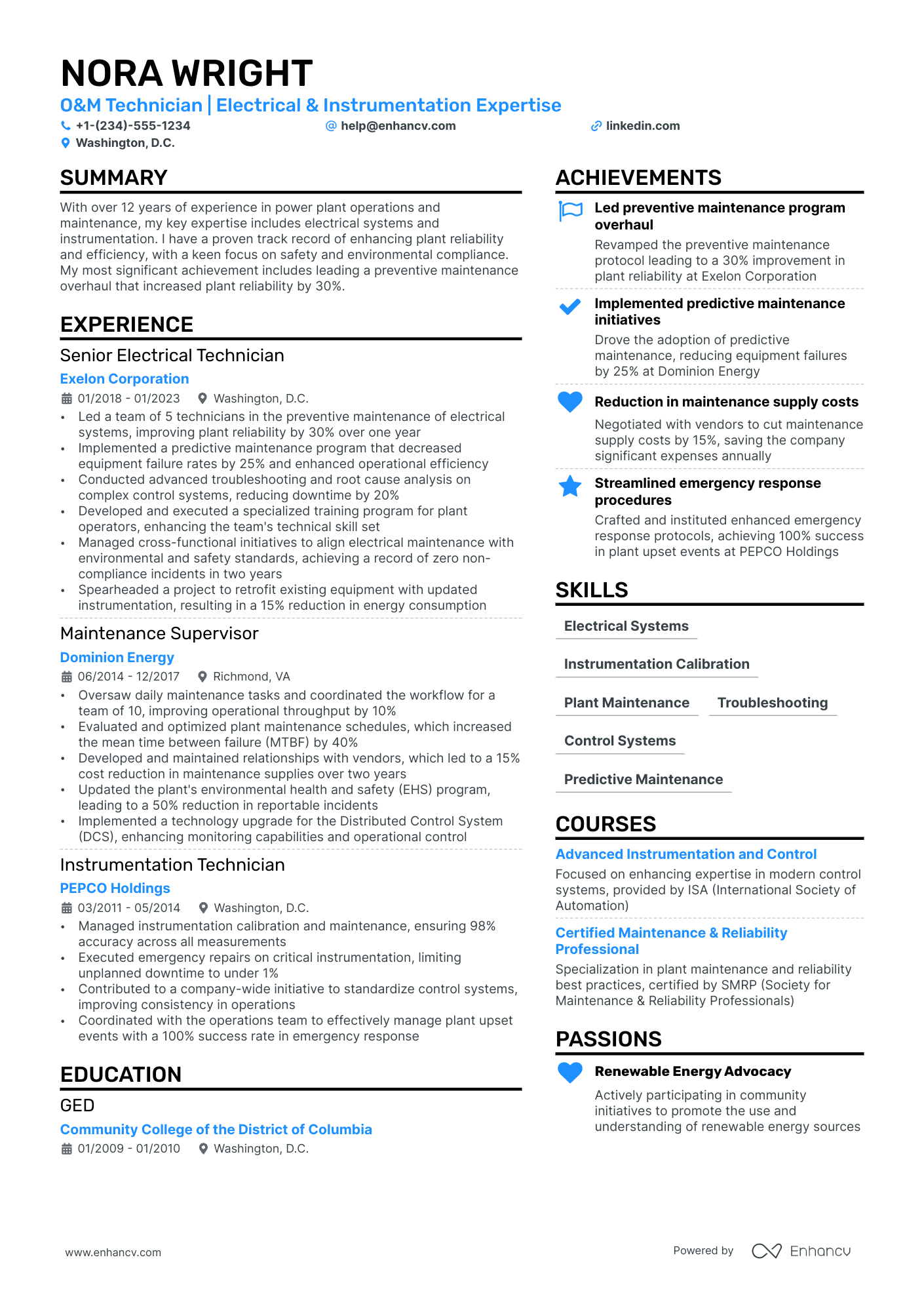
As a maintenance technician, differentiating your resume among others can be challenging, particularly when trying to showcase your unique skills and relevant experience in a concise way. Our guide offers targeted tips and strategies to help you craft a standout resume that highlights your expertise and catches the attention of potential employers.
- Get inspired from our maintenance technician resume samples with industry-leading skills, certifications, and more.
- Show how you can impact the organization with your resume summary and experience.
- Introducing your unique maintenance technician expertise with a focus on tangible results and achievements.
If the maintenance technician resume isn't the right one for you, take a look at other related guides we have:
- Custodian Resume Example
- Electronic Technician Resume Example
- Handyman Resume Example
- Cleaning Manager Resume Example
- Facilities Manager Resume Example
- Cable Technician Resume Example
- Regional Property Manager Resume Example
- Resident Assistant Resume Example
- Residential Property Manager Resume Example
- Pest Control Resume Example
Tips and tricks for your maintenance technician resume format
Before you start writing your resume, you must first consider its look-and-feel - or resume format . Your professional presentation hence should:
- Follow the reverse-chronological resume format , which incroporates the simple logic of listing your latest experience items first. The reverse-chronological format is the perfect choice for candidates who have plenty of relevant (and recent) experience.
- State your intention from the get-go with a clear and concise headline - making it easy for recruiters to allocate your contact details, check out your portfolio, or discover your latest job title.
- Be precise and simple - your resume should be no more than two pages long, representing your experience and skills that are applicable to the maintenance technician job.
- Ensure your layout is intact by submitting it as a PDF. Thus, your resume sections would stay in place, even when assessed by the Applicant Tracker System (ATS).
Upload & Check Your Resume
Drop your resume here or choose a file . PDF & DOCX only. Max 2MB file size.
If you happen to have plenty of certificates, select the ones that are most applicable and sought-after across the industry. Organize them by relevance to the role you're applying for.
Fundamental sections for your maintenance technician resume:
- The header with your name (if your degree or certification is impressive, you can add the title as a follow up to your name), contact details, portfolio link, and headline
- The summary or objective aligning your career and resume achievements with the role
- The experience section to curate neatly organized bullets with your tangible at-work-success
- Skills listed through various sections of your resume and within an exclusive sidebar
- The education and certifications for more credibility and industry-wide expertise
What recruiters want to see on your resume:
- Proven experience with troubleshooting and repairing mechanical, hydraulic, pneumatic, and electrical systems
- Familiarity with Computerized Maintenance Management Systems (CMMS) and preventive maintenance procedures
- Appropriate certifications or licensure (e.g., HVAC, Electrical, Plumbing, Welding, or other relevant technical certifications)
- Understanding of safety standards and regulations, such as OSHA guidelines and compliance
- Demonstrated ability to read and interpret equipment manuals, work orders, and blueprints
Quick formula for writing your maintenance technician resume experience section
Have you ever wondered why recruiters care about your maintenance technician expertise?
For starters, your past roles show that you've obtained the relevant on-the job training and expertise that'd be useful for the role.
What is more, the resume work experience section isn't just your work history , but:
- shows what you're capable of achieving based on your past success;
- proves your skills with (oftentimes, tangible) achievements;
- highlights the unique value of what it's like to work with you.
To ensure your resume work experience section is as effective as possible, follow this formula:
- start each bullet with a powerful, action verb , followed up by your responsibilities, and your workplace success.
The more details you can include - that are relevant to the job and linked with your skill set - the more likely you are to catch recruiters' attention.
Additionally, you can also scan the job advert for key requirements or buzzwords , which you can quantify across your experience section.
Not sure what we mean by this? Take inspiration from the maintenance technician resume experience sections below:
- Implemented a new preventive maintenance program for HVAC systems, reducing system downtime by 25% and extending equipment lifespan.
- Led a team of 5 in retrofitting lighting infrastructure with energy-efficient LED lights, saving the company approximately $10,000 annually in energy costs.
- Managed maintenance requests, consistently achieving a resolution rate of over 90% within the targeted 24-hour response period.
- Conducted daily inspections and maintenance on manufacturing equipment, reducing equipment failure rates by 30%.
- Collaborated on the installation of a new $2 million assembly line, ensuring optimal setup and contributing to a 15% increase in production efficiency.
- Developed a comprehensive maintenance training manual to onboard and continuously educate 20+ technicians within the facility.
- Managed routine and emergency repairs for a real estate portfolio encompassing 500 units, attaining a 95% tenant satisfaction score.
- Initiated a cost-saving initiative by in-sourcing painting and minor renovation work, saving the company $50,000 per annum.
- Negotiated vendor contracts for major repairs, including a $200,000 elevator overhaul, resulting in a 10% cost reduction through strategic sourcing.
- Streamlined maintenance processes using a modern CMMS, leading to a 20% improvement in maintenance task tracking and deployment.
- Executed critical electrical and plumbing repairs for multiple office complexes, maintaining a 99% operational uptime for building services.
- Actively participated in the greening of facilities, supporting the installation of solar panels that led to a 30% reduction in the building's carbon footprint.
- Overhauled and modernized 15-year-old conveyor systems, improving material handling speed by 40%.
- Provided technical expertise in upgrading the facility's fire suppression system, enhancing safety compliance.
- Performed meticulous machinery alignments using laser technology, ensuring equipment operated within specified tolerances and minimizing wear and tear.
- Developed and executed a successful maintenance strategy for a fleet of 100+ service vehicles, reducing downtime by 35%.
- Played a key role in the expansion project of the central warehouse, contributing to a 50% increase in inventory storage capacity.
- Established a cross-departmental maintenance committee to streamline communication and foster proactive equipment care practices.
- Instrumental in redesigning the manufacturing line layout for optimized maintenance access, reducing mean time to repair (MTTR) by 25%.
- Managed the implementation of a new waste water treatment system which increased processing capacity by 50%, while complying with stringent environmental regulations.
- Championed the update of the maintenance inventory system, thus ensuring a 98% availability of critical spare parts.
- Initiated a Total Productive Maintenance program, resulting in an impressive 20% increase in overall equipment effectiveness (OEE) across the production floor.
- Reduced annual maintenance costs by $40,000 by implementing a recycling program for machine oils and consumables.
- Spearheaded the upgrade of the company's security surveillance system, which led to a 50% reduction in workplace incidents.
Quantifying impact on your resume
- Detail the percentage reduction in machine downtime achieved through preventive maintenance programs.
- State the number of maintenance projects managed and their successful completion rates.
- Quantify the amount of money saved for the company through cost-efficient maintenance practices.
- Describe the scale of the facilities managed, including square footage and number of machines.
- List the number of maintenance technicians trained and upskilled under your supervision.
- Highlight the reduction in safety incidents as a result of your maintenance initiatives.
- Provide the number of technical diagnostic tools mastered and regularly used for troubleshooting.
- Mention the inventory cost reduction achieved through optimized spare parts management.
Action verbs for your maintenance technician resume
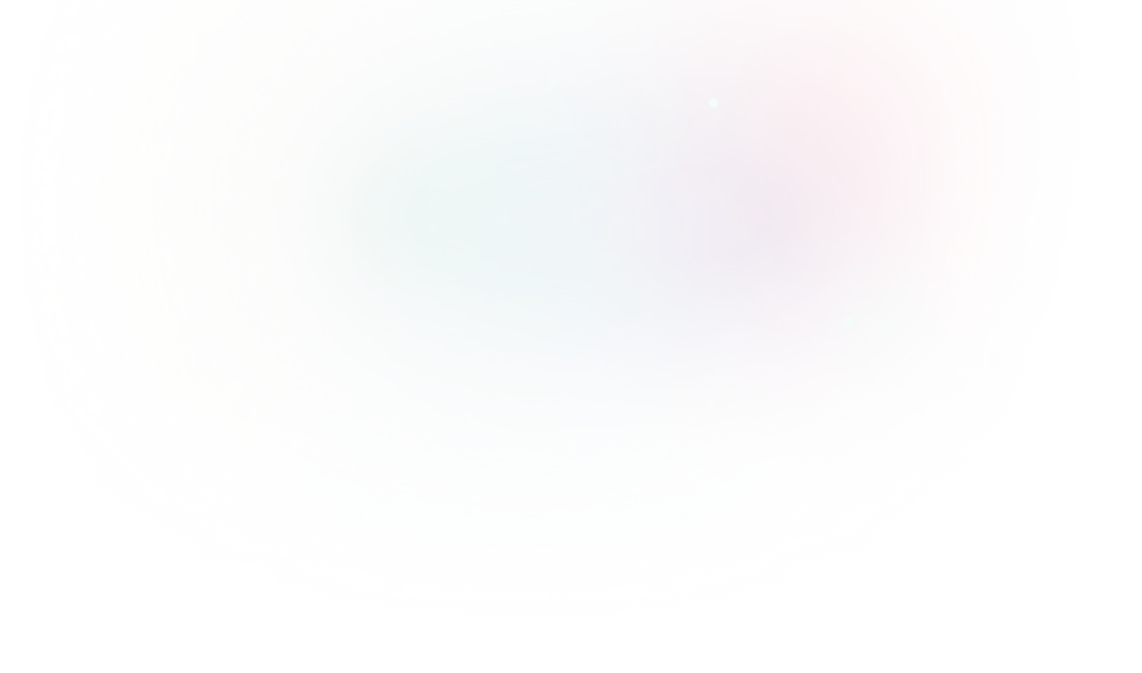
Lacking relevant maintenance technician resume experience?
Learn how to write your maintenance technician resume experience in spite of having no real-world (or applicable) experience for the job.
You should:
- Feature relevant projects or publications that could impress recruiters or showcase that you have the basic skill set for the job
- Shift the focus towards your people (communication, organization, etc.) skills to demonstrate that you're a quick learner and can easily adapt to a new environment
- Use the resume objective to not only highlight your accomplishments but also map out how your career plans are perfectly aligned with the company's vision
- Select either the functional-skill-based resume format (that puts the focus on your skills) or the hybrid one (balancing expertise with skills).
Recommended reads:
- Perfecting the Education Section on Your Resume
- How to List Expected Graduation Date on Your Resume
The more trusted the organization you've attained your certificate (or degree) from, the more credible your skill set would be.
Shining a light on your maintenance technician hard skills and soft skills
To win recruiters over, you must really have a breadth of skill set presented and supported within your maintenance technician resume.
On hiring managers' checklists, you'd initially discover hard or technical skills. Those are the technology (and software) that help you perform on the job. Hard skills are easy to quantify via your education, certificates, and on-the-job success.
Another main criterion recruiters are always assessing your maintenance technician resume on is soft skills. That is your ability to communicate, adapt, and grow in new environments. Soft skills are a bit harder to measure, as they are gained both thanks to your personal and professional experience.
Showcase you have the ideal skill set for the role by:
- Dedicating both a skills box (for your technical capabilities) and an achievements or strengths section (to detail your personal skills).
- When listing your skills, be specific about your hard skills (name the precise technology you're able to use) and soft skills (aim to always demonstrate what the outcomes were).
- Avoid listing overused cliches in the skills section (e.g. Microsoft Office and Communication), unless they're otherwise specified as prominent for the role.
- Select up to ten skills which should be defined via various sections in your resume skills sidebar (e.g. a technical skills box, industry expertise box with sliders, strengths section with bullets).
Spice up your resume with leading technical and people skills, that'd help you get noticed by recruiters.
Top skills for your maintenance technician resume:
Electrical troubleshooting
Preventive maintenance
HVAC systems
Plumbing repair
Mechanical repair
Welding and fabrication
Blueprint reading
Computerized Maintenance Management Systems (CMMS)
Machinery alignment
Building automation systems
Problem-solving
Attention to detail
Communication
Time management
Adaptability
Customer service
Critical thinking
Stress management
Highlight any significant extracurricular activities that demonstrate valuable skills or leadership.
Showcase academic background with education and certifications' sections
Listing your education and certifications should be a rudimentary part of your resume writing.
Including your relevant academic background - in the form of your higher education degree and niche-specific certificates - will prove knowledge of the industry.
For your education section:
- Start by including your degree, followed by start and graduation dates, as well as the institution;
- You could include relevant coursework, major/minor , or GPA, only if your've just graduated from college or if this information would further support your application;
- If you have an "ongoing" degree, you can still list it in case you think your diploma can impress recruiters or it's required;
Follow a similar logic for your certifications section by listing the institution, alongside dates you've obtained the certificate. For some of the most recent and relevant industry certificates , check out the next part of our guide:
The top 5 certifications for your maintenance technician resume:
- Certified Maintenance & Reliability Technician (CMRT) - Society for Maintenance & Reliability Professionals (SMRP)
- Certified Maintenance & Reliability Professional (CMRP) - Society for Maintenance & Reliability Professionals (SMRP)
- Industrial Maintenance Electrical & Instrumentation Technician (IMEIT) - National Center for Construction Education and Research (NCCER)
- Heating, Ventilation, Air Conditioning and Refrigeration (HVAC/R) Certification - North American Technician Excellence (NATE)
- Electrical and Mechanical Technician Certificate - International Society of Automation (ISA)
If you happen to have some basic certificates, don't invest too much of your maintenance technician resume real estate in them. Instead, list them within the skills section or as part of your relevant experience. This way you'd ensure you meet all job requirements while dedicating your certificates to only the most in-demand certification across the industry.
- When You Should (And Not) Add Dean's List On Your Resume
- Should I Put In An Incomplete Degree On A Resume?
Should you write a resume summary or an objective?
No need to research social media or ask ChatGPT to find out if the summary or objective is right for your maintenance technician resume.
- Experienced candidates always tend to go for resume summaries. The summary is a three to five sentence long paragraph that narrates your career highlights and aligns your experience to the role. In it you can add your top skills and career achievements that are most impressive.
- Junior professionals or those making a career change, should write a resume objective. These shouldn't be longer than five sentences and should detail your career goals . Basically, how you see yourself growing in the current position and how would your experience or skill set could help out your potential employers.
Think of both the resume summary and objective as your opportunity to put your best foot forward - from the get go - answering job requirements with skills.
Use the below real-world maintenance technician professional statements as inspiration for writing your resume summary or objective.
Resume summaries for a maintenance technician job
- With over 8 years of expertise in industrial maintenance technology, this seasoned professional excels in maximizing machine uptime and improving systems efficiency for manufacturing giants. Broad experience encompasses PLC programming, HVAC systems, and welding, alongside a pivotal role in reducing machinery downtime by 30% through strategic preventive maintenance scheduling.
- Transitioning from automotive engineering to maintenance, this candidate brings a robust technical foundation with 4 years of experience. Key competencies include a strong grasp of electrical systems and diagnostics, plus accomplished project management skills, evidenced by leading a team to overhaul a major production line under budget and ahead of schedule.
- Former IT specialist seeking to leverage 5 years of problem-solving and technical troubleshooting experience into the maintenance sector. Proven track record in network administration and hardware repair, coupled with a passion for mechanical systems, promises to enrich a maintenance team with innovative solutions for operational efficiency.
- Adept at coordinating substantial maintenance tasks over the past 6 years for commercial facilities, this proactive technician boasts a wealth of knowledge in both electrical and mechanical systems. Recognizable achievement includes designing a customized inventory tracking tool that slashed part replacement times by 40%, contributing significantly to operational continuity.
- Eager to embark on a new journey as a maintenance technician, this enthusiastic individual is armed with a foundational certification in electrical systems and a genuine interest in machinery operations. Aimed at gaining hands-on experience, they are committed to applying their quick-learning abilities and attention to detail to excel in maintaining equipment and contributing to team success.
- Recent vocational school graduate with a specialization in HVAC and refrigeration systems, this fresh talent is poised to apply theoretical knowledge and practical training in a real-world setting. With an eye for detail and a dedication to safety and quality, the aim is to establish a solid career foundation while delivering high standards in equipment maintenance and reliability.
Recruiters' favorite additional maintenance technician resume sections
When writing your maintenance technician resume, you may be thinking to yourself, " Is there anything more I can add on to stand out? ".
Include any of the below four sections you deem relevant, to ensure your maintenance technician resume further builds up your professional and personal profile:
- Books - your favorite books can showcase that you have an excellent level of reading comprehension, creativity, and outside the box thinking;
- Languages - make sure you've included your proficiency level alongside a relevant certificate or a form of self-assessment;
- Website link - ensure you've curated your most relevant and recent projects in your professional portfolio (and that the link is a part of your resume header) to support your application;
- Passions - showing recruiters how you spend your time outside of work and what activities or causes you're invested in.
Key takeaways
Writing your maintenance technician resume can be a structured and simple experience, once you better understand the organization's requirements for the role you're applying to. To sum up, we'd like to remind you to:
- Always select which experiences, skills, and achievements to feature on your resume based on relevancy to the role;
- In your resume summary, ensure you've cherry-picked your top achievements and matched them with the job ad's skills;
- Submit your maintenance technician resume as a one or two-page long document at the most, in a PDF format;
- Select industry leading certifications and list your higher education to highlight you have the basis for technical know-how;
- Quantify your people's skills through various resume sections (e.g. Strengths, Hobbies and interests, etc.) to show recruiters how your profile aligns with the organizational culture.
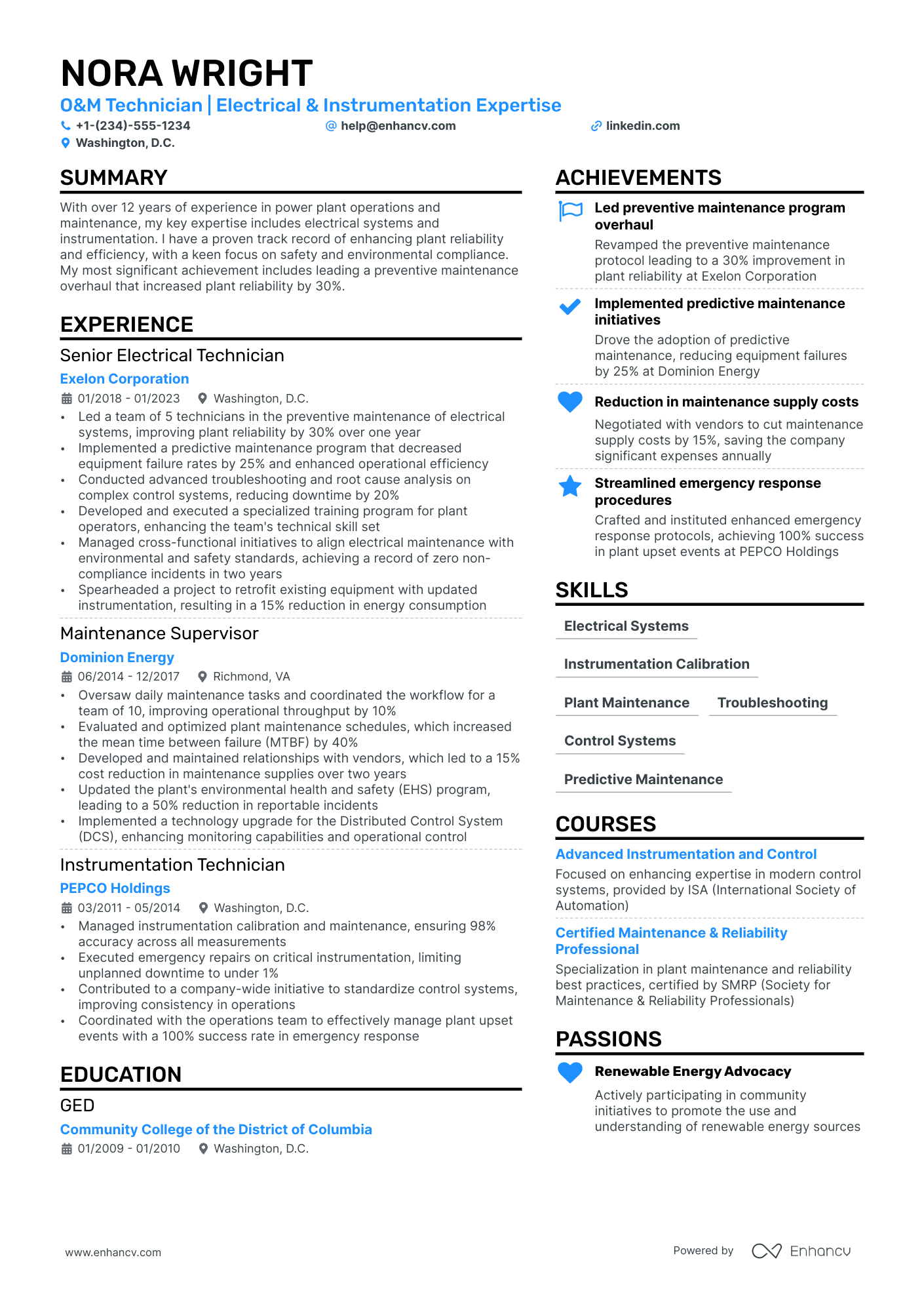
Looking to build your own Maintenance Technician resume?
- Resume Examples
Resume Bullet Points Or Paragraphs
Feeling passed over for a promotion here's what to do before you quit, what to do if you don't have any references for a job application, how to make resume margins the right size, what words do employers look for in a resume, negotiating a salary increase for a new job: what to expect and how to ask.
- Create Resume
- Terms of Service
- Privacy Policy
- Cookie Preferences
- Resume Templates
- AI Resume Builder
- Resume Summary Generator
- Resume Formats
- Resume Checker
- Resume Skills
- How to Write a Resume
- Modern Resume Templates
- Simple Resume Templates
- Cover Letter Builder
- Cover Letter Examples
- Cover Letter Templates
- Cover Letter Formats
- How to Write a Cover Letter
- Resume Guides
- Cover Letter Guides
- Job Interview Guides
- Job Interview Questions
- Career Resources
- Meet our customers
- Career resources
- English (UK)
- French (FR)
- German (DE)
- Spanish (ES)
- Swedish (SE)
© 2024 . All rights reserved.
Made with love by people who care.
Resume Builder
- Resume Experts
- Search Jobs
- Search for Talent
- Employer Branding
- Outplacement
- Resume Samples
Maintenance Technician Resume Samples
The guide to resume tailoring.
Guide the recruiter to the conclusion that you are the best candidate for the maintenance technician job. It’s actually very simple. Tailor your resume by picking relevant responsibilities from the examples below and then add your accomplishments. This way, you can position yourself in the best way to get hired.
Craft your perfect resume by picking job responsibilities written by professional recruiters
Pick from the thousands of curated job responsibilities used by the leading companies, tailor your resume & cover letter with wording that best fits for each job you apply.
Create a Resume in Minutes with Professional Resume Templates
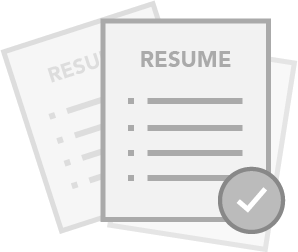
- Works with Maintenance Supervisor and Maintenance Planner to establish, review, improve and execute plant maintenance system standards
- Works with Maintenance Engineer and Maintenance Planner to establish, review, improve and execute plant maintenance system standards
- Conducts daily rounds as assigned, log equipment readings, makes indicated adjustments and/or creates work request for major repairs
- Assist in the development, revision, and updating of related SOPs or job plans/work plans for work related areas
- Work in a safe manner and follow safety policies. Make sure co-workers are working safely and following safety policies
- Works with conveyor, HVAC, and electrical systems as well as machinery such as forklifts and work assist vehicles. This work can be dirty or heavy at times
- Painting structures, performing masonry work, repairing plumbing fixtures and woodwork
- Create and execute performance objectives; meet performance commitments and work within the guidelines of the Milgard Performance System
- Actively participate in the Performance and Development Review process, ensuring alignment to the performance pillars - Perform, Grow, Develop and Innovate
- Performs all work in accordance with established safety and quality management procedures
- Provide improvement feedback for PM content and frequency. Record all performed work through the CMMS
- Assist with management of contractors performing work on KIPP facilities
- Perform work in a safe manner and insure that molding machines and auxiliary equipment are cleaned and in a safe working condition after all work is completed
- Provide guidance and assistance in work being performed by outside contractors
- Solid working knowledge and ability in all the mechanical, electrical, and plumbing trades, and a journeymen’s knowledge and skill level in one
- Good knowledge of Process Control and Instrumentation Systems as well as basic knowledge of office automation software
- Strong attention to detail, ability to multitask, good communications skills
- Strong written and verbal communication skills and basic knowledge of arithmetic; use of decimals, fractions, gauges or measuring instruments
- Proficient in use of hand and power tools necessary to perform plant maintenance and repair, and knowledgeable in the processes and procedures of the function
- Working knowledge of applied mathematics and basic computer knowledge
- Demonstrate basic building knowledge of construction means & methods and building systems knowledge
- Ability to problem solve and a thorough knowledge of basic repair and troubleshooting techniques
- Verifiable knowledge of and experience in application of cGMP's, validation, quality systems, document control and the impact of regulatory considerations
- -Strong attention to detail to display quality work
15 Maintenance Technician resume templates
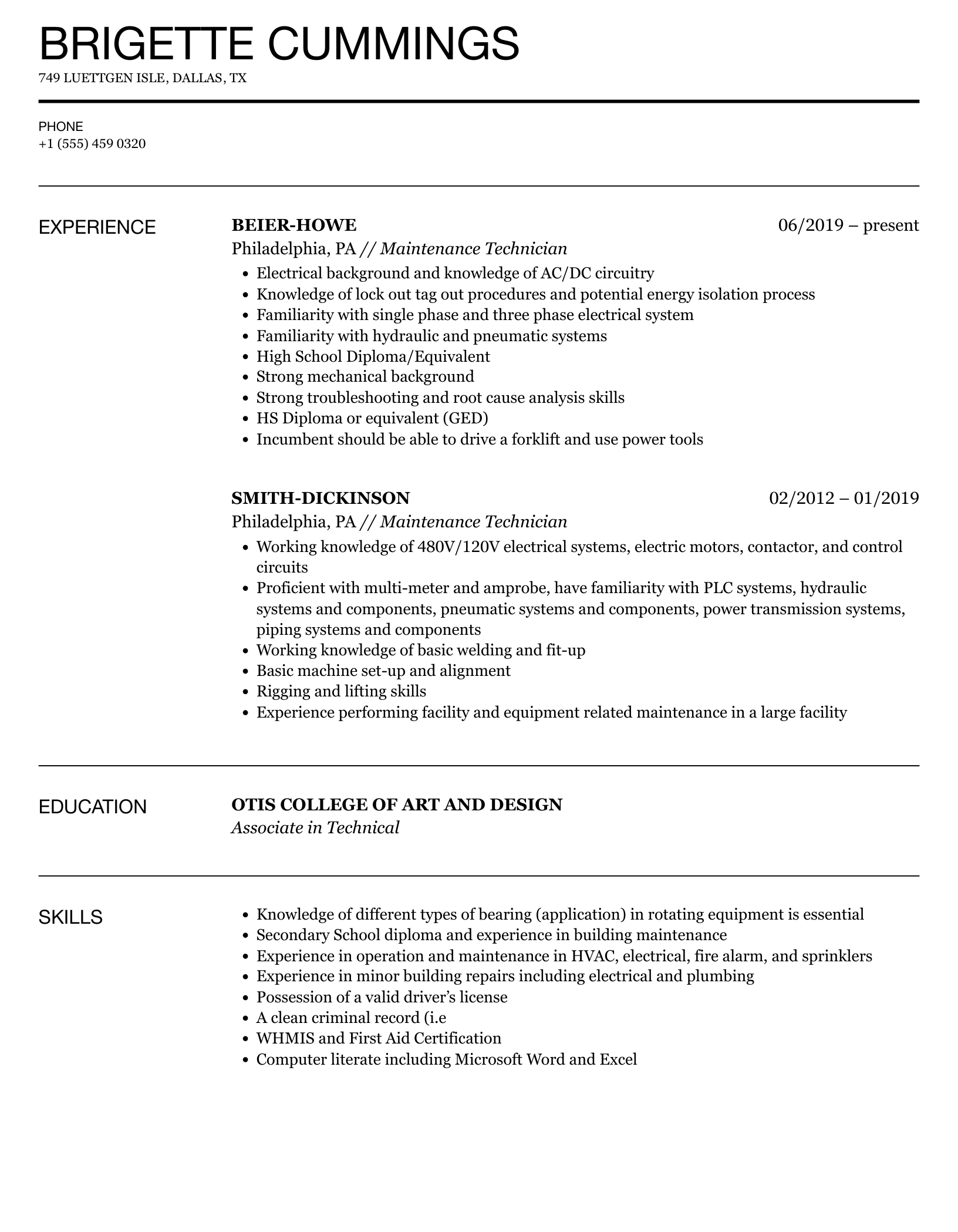
Read our complete resume writing guides
How to tailor your resume, how to make a resume, how to mention achievements, work experience in resume, 50+ skills to put on a resume, how and why put hobbies, top 22 fonts for your resume, 50 best resume tips, 200+ action words to use, internship resume, killer resume summary, write a resume objective, what to put on a resume, how long should a resume be, the best resume format, how to list education, cv vs. resume: the difference, include contact information, resume format pdf vs word, how to write a student resume, maintenance technician resume examples & samples.
- Must possess a high school diploma/GED
- Flexible to work odd hours, weekends and holidays
- Ability to lift 25 lbs or more
- Have own hand tools
- 1-3 years’ maintenance experience
- Ethernet networking administration skills including VPN, routers, managed switches
- Knowledge of IP-based audio-video routing/console mixing systems; IP audio-video delivery
- Knowledge of all Microsoft, Unix and Linux OS
- Ability to troubleshoot software problems including Audio-Video software, applications, and drivers
- Ability to troubleshoot computer hardware problems including workstations, servers, drives, cards,
- Familiar with SQL Server, mySQL, VB Script, VMWare, VOIP technology, streaming media encoding
- Knowledge of digital audio-video delivery systems, and storage systems
- Ability to read and produce technical drawings/documentation
- Strives to make improvements in all areas of responsibility
- Able to work with minimal supervision, work well under pressure and be solution-oriented
- Microsoft MSCE certification
- SBE certification
- Experience with Adobe Editing Suite
- Experience with Mac Editing systems
- Experience with Configuration of HP and Cisco switches/firewalls; Watchguard firewalls
- Knowledge of Broadcast STL, Microwave IP systems, audio-video processing
- Knowledge of satellite, fiber and IP transmission systems
- Complete ground work as directed by Property Manager which may include picking up trash, sweeping curb and dumpster areas and maintaining landscaping beds and other areas
- Responsible for alerting the Property Manager of any unusual occurrence and/or damage that have taken place or that may occur
- Maintain a professional courteous manner with all vendors, contractors, and fellow employees
- Ensure compliance of all work-related activities in a fair, ethical, and consistent manner
- Follow established company policies and those outlined in the Employee Guidebook
- This job requires exerting 10 to 100 pounds of force occasionally
- Responsible for the completion of all maintenance service requests as assigned
- Work within expense limits established
- Maintain inventory controls for cost effective operations
- Operates a variety of hand, power and shop tools used in the course of building construction, woodworking, and building maintenance such as power drills, saws, drill presses, joiners and planers
- High school diploma combined with professional training
- At least two years, less than five years experience
- Scheduling skills
- Proficient with Microsoft Office Suite
- Ability to work with minimal supervision and as part of a team
- Experience with scheduling and inventory management is a significant asset
- Previous experience supervising contractors is an asset
- Proficient time management skills and flexibility in adjusting between a variety of duties
- Bilingual French & English
- Perform repairs on equipment associated with warehouse distribution
- Department Safety – responsible for following all safety guidelines. With a strong emphasis on Lock-out Tag-outand Fall protection
- Obtain and maintain a PIV (powered industrial vehicle) license to operate all PIV equipment associated with your assigned location within 90 days of employment
- On Target performance of all tasks listed and other duties as assigned
- Advanced mechanical abilities. Perform routine technical and electrical repairs
- Perform equipment diagnostics/repairs of motor control systems, and forklifts
- Working knowledge of 600, 480, 277, 220, and 110 electrical powers. (single and three phase electric)
- Basic working knowledge of PLC’s
- Perform welding and fabrication assignments. Knowledge of ARC, MIG and gas welding. Able to perform fabrication from mechanical drawings
- Perform PM’s, repairs and overhauls on all associated equipment. Identify damaged or defective equipment and repair in a timely manner
- Working knowledge of the Energy Management System.*
- Detect safety hazards and plan/organize safe solutions
- Can work independently or as part of a team
- Lead projects and effectively direct the efforts of maintenance associates through the course of the project
- Provide training for subordinate Maintenance Associates as needed
- Maintain expected level of cleanliness in all assigned work areas
- Willingness to work any and all shifts, including weekends and overtime
- Promoting teamwork
- Advanced mechanical and electrical aptitude – proven skills through past experience,either formal or informal training
- 2 to 3 years of practical experience preferred as a maintenance mechanic or equivalent
- Experience with MS Office programs: Excel, Word and Outlook
- Minimum education level
- Must beable to lift 50 pounds
- Must present professional demeanor and appearance at all times. This will include, but not limited to facial hair being well trimmed, hair pulled back and combed and wearing attire that is in accordance with Gap Inc. dress codes and in a clean and well-maintained condition
- Perform major mechanical and advanced electrical repairs on equipment associated with warehouse distribution
- Lead and direct the work of other mechanics in the absence of Maintenance management
- Leadership responsibility for following all safety guidelines and departmental procedures
- Perform complex mechanical and electrical repairs on all DC related equipment
- Perform equipment diagnostics/repairs of motor control systems, forklifts and scanners
- Design and oversee installation of electrical circuits per applicable codes
- Proficient in the operation and utilization of various test & metering equipment
- Perform PLC modifications/troubleshooting
- Perform welding and fabrication assignments.Knowledge of ARC, MIG and gas welding.Able to perform fabrication from mechanical drawings
- Working knowledge of the Energy Management System
- Detect safety hazards and plan/organize smart solutions
- Can work independently, lead or work as part of a team
- Organize and lead projects
- Provide departmental Training and mentoring as needed
- Advanced mechanical and electrical aptitude – proven skills through past experience,either formal or informal training. Technical certifications are preferred
- 4 to 5 years of practical experience as a maintenance mechanic or equivalent
- Utilize standard office software programs
- Attire must include leather boots, long pants and shirts with sleeves
- Adhere to all safety codes and practices
- Oversees maintenance and housekeeping staff to ensure daily tasks are completed
- Assists in installation, preventative maintenance, repair of lift equipment, conveyor systems, building structures, electrical systems and mechanical systems in a highly automated production facility
- Assists with recommendations pertaining to equipment upgrades, analysis of operation parameters of equipment, and other requirements to support operations
- Able to coordinate work of outside vendors and contractors on capital projects or repairs. Obtain bids on labor, materials and schedules and communicate analysis to management
- Applies technical and maintenance experience to improve and maintain both short and long term facilities and/or production equipment
- Maintains safe validated parameters during the operation of equipment, thus permitting the timely release of product and meeting functional, cosmetic, and other quality control specifications
- Assists in equipment-related recommendations that will secure improvements in safety, productivity, efficiency, cost control, and product quality
- Helps implement methods that will maximize reliability of work production and facility equipment maximizing up-time operations
- Pro-actively identifies potential equipment failures which may affect performance and makes recommendations for corrective action
- Be available for emergency callbacks and flexible toward the daily start schedule and overtime requirements, including holidays and plant shutdowns
- Minimum H.S. diploma or equivalent, along with specialized coursework beyond high school education
- Minimum of 3 to 5 years related maintenance experience in a large highly automated distribution or production facility
- Trade skills in one or more of the following; welding, electrical, mechanical, HVAC, instrumentation, lift equipment repairs, light construction methods, PLC and conveyor systems
- Ability to interpret and understand maintenance manuals and electrical equipment schematics
- Ability to safely operate motorized heavy equipment
- Day to day maintenance and support of station’s core infrastructure, not limited to news editing systems, control room automation and components, master control systems, transmitter operations, studio equipment as well as field operations equipment and vehicles
- Install, upgrade, troubleshoot and repair electronic equipment to a component (hardware/software) level
- Work collaboratively in the design, construction and execution of station engineering projects and initiatives
- Perform station operations roles on an as-needed basis, including TOC, field and studio operations support, and master control operations
- Work with equipment manufacturers and vendors to resolve issues, including ordering parts/services
- Review discrepancy reports and address issues with minimal supervision
- Other duties, as assigned by Broadcast Operations & Engineering management
- College degree in Engineering or SBE Certification
- 3-5 years of experience in broadcast engineering or technical operations
- Must join the IBEW 1220 union if not a current member. Work rules, compensation and vacation time are dictated by the master agreement
- Knowledge and experience working with Sony automation, cameras and recording devices, Grass Valley non-linear editing systems, Telestream transcoding products, Harris routers and encoders and Harmonic video servers
- Knowledge of and understanding of FCC rules and regulations
- Experience in IT, including an understanding of networking, software, and operating systems
- Working knowledge of Microsoft Office Applications, Visio, and AutoCAD
- 5+ years of experience in building or apartment maintenance
- Work odd hours, weekends, and holidays
- Lift 25 lbs or more
- Strong carpentry, painting and general maintenance skills
- Maintain current EPA Certification minimum Type II
- Maintenance Electrical License a plus but not required
- Maintains general maintenance materials inventory and orders supplies with designated approved vendors
- Liaison with vendors in scheduling and completing outsourced general maintenance work or special projects
- Completes inter-departmental work orders and requests for general carpentry
- Performs regular routine maintenance on HVAC equipment to include changing filters and make VAV zone temperature adjustments
- Performs general plumbing maintenance, repairs and replacements
- Tests and regulates water softness in the buildings through maintenance of our water softeners per maintenance specifications and operations
- Creates duplicate keys of building locks
- Performs preventative and corrective maintenance on building mechanical systems
- Maintains work area, tools and equipment in safe and proper working conditions
- Sets up, operates, and troubleshoots videoconferencing and projection equipment
- Coaches and mentors less experienced maintenance technicians
- Monitors and inspects the work of others
- Assists in evaluating performance and providing appropriate feedback to department manager
- General plumbing knowledge sufficient to replace assembly, turn off water supplies, and unclog drains
- Knowledge of audio/visual equipment sufficient to setup and assist users, or ability to learn functions over a two-week training period
- General carpentry
- Patching drywall and painting
- Operating fork lift
- Time management skills and initiative sufficient to prioritize workload, handle multiple tasks and meet deadlines
- Learn safety training within 30 days
- Influence, motivate and persuade others to achieve desired results
- Read, comprehend and apply information from technical manuals and instructions
- Respond to emergency calls during scheduled "on-call" weekends and evenings
- Mobility sufficient to traverse on-site and off-site buildings, including rooftops, stairwells, and catwalk
- Establish and maintain effective working relationships with others
- Building Maintenance – Perform painting, sheetrock repairs, and general Tenant Improvement work as needed. Perform minor repairs on doors, dock plates, and plumbing to resolve problems and ensure successful operation
- Conveyor System Maintenance – Perform minor preventative maintenance tasks, with the goal of expanding hands-on knowledge and experience
- Equipment Maintenance -- Maintain equipment (i.e., scanners, photocells), battery room, and Maintenance shop in clean and good working order
- Facility Cleanliness / Safety – Ensure the maintenance shop area is organized, neat and clean. Adhere to 5S principles. Identify and act immediately regarding any safety hazards, spills, etc., to avoid the risk of accidents. Use safe lifting techniques and operate power equipment in a safe manner. Abide by all stated regulations while performing works, i.e., lockout/tag out procedures, etc. Maintain general cleanliness of building including collection of all recycled materials
- Fabrication – Utilize materials and tools to create custom equipment to support the operation (i.e., wood, metal, etc.)
- Ability to learn new trades
- Promoting and conduct good housekeeping practices
- Conveyor System Maintenance – Perform reactive repairs and preventative maintenance to maintain operation of conveyors and sorter equipment. Responsible for cleaning and lubricating machinery, performing basic diagnostic tests, checking performance, and testing damaged machine parts to determine whether major repairs are necessary; includes the assembly/disassembly of pneumatic sub-systems. Troubleshoot conveyor system controls and adjusts/calibrates or repairs as needed, both preventative and reactive. Work with vendor partners to determine the root cause of issues and appropriate corrections
- Equipment Maintenance – Perform preventative maintenance to production-related equipment, Powered Industrial Trucks, and building equipment as needed. Maintain complete inventory and cleaning of all equipment and work areas
- Electrical – Perform trouble-shooting and needed tasks involving low and high voltage electrical and control systems of 480 volt devices (AC and DC), including repair or replacement of system components
- Facility Cleanliness / Safety – Ensure the primary work areas are left in an organized, neat and clean manner. Identify and act immediately regarding any safety hazards, spills, etc., to avoid the risk of accidents. Use safe lifting techniques and operates power equipment in a safe manner. Abide by all stated regulations while performing works, i.e., lockout/tagout procedures, etc. Communicate with all peers, customers, and management regarding safety issues and training requirements
- Maintain records to ensure accountability of time, parts and repairs
- Building Maintenance – Perform general facility repairs such as minor plumbing, general electric, lighting, painting, and wall repair. Perform minor repairs on doors and dock plates to resolve problems and ensure successful operation. Communicate with all peers, customers, and management to accomplish assigned and critical tasks. Oversees Third Party project completion
- Conveyor System – Support and perform reactive repairs and preventative maintenance to maintain operation of conveyors and sorter equipment, including the assembly/disassembly of pneumatic sub-systems. Troubleshoot conveyor system controls and adjust/calibrate or repairs as needed. Work with vendor partners to determine the root cause of issues and appropriate corrections. Oversee production-related issues and make necessary corrections to sortation controls as needed
- Equipment Maintenance – Perform preventative maintenance to production-related equipment, Powered Industrial Trucks, and building equipment as needed. Maintain complete inventory and cleaning of all equipment and work areas. Identify and correct safety hazards and potential maintenance issues before they become critical. Supports the design and implementation of continuous improvement processes
- System Installation, Design, Construction and Repair – Recommend and performs installations of new or replacement facility equipment. Works with or oversees In-House and Third Party installation
- Problem Solving – Detect, diagnose, and resolve electrical, mechanical, plumbing, heating/cooling, and equipment problems before they impact the operation of the facility
- Facility Cleanliness / Safety – Oversee and ensure the maintenance shop area is organized, neat and clean. Identifie and act immediately regarding any safety hazards, spills, etc., to avoid the risk of accidents. Use safe lifting techniques and operates power equipment in a safe minor. Abide by all stated regulations while performing work, i.e., lockout/tag out procedures, etc. Oversee inventories, repairs and clean up of equipment and work areas daily. Communicate with all peers, customers, and management regarding safety issues and training requirements
- Fabrication – Utilize materials and tools to design/create/repair custom equipment to support the operation (i.e., wood, metal, etc.)
- Record Keeping -- Perform necessary data entry (i.e., work order tracking/filing) and keep current tools and documents updated as necessary (i.e., Material Safety Data Sheets). Maintain records to ensure accountability of time, parts and repairs
- Other Duties / Projects – Read blueprints, manuals and schematics and interpret technical manuals. Prioritize tasks to ensure all requests are completed in a timely manner. Train new associates in operational procedures, use of safety equipment and safety hazards. Communicate with and provide completed Work Orders or updates daily to management. Oversee small/medium-sized projects within the facility and provide oversight of Third Party vendors
- Supervise Maintenance Techs – Execute basic supervisory responsibilities for hiring, orienting & training, assigning work, evaluating performance and providing feedback to direct reports
- Industrial mechanic trade school courses or certificate (i.e., electrical, controls, plumbing, welding, etc.) or equivalent experience
- Minimum of five years experience with mechanical and electrical systems, including conveyor/sortation systems and related equipment, in a fast-paced production environment
- Minimum of two years supervisory experience with a technical team
- Possess strong prioritization skills and be able to make decisions independently
- Possess strong organizational skills and have the ability to oversee the timely completion of multiple tasks daily
- Ability to train new employees and mentor junior technicians
- Provides hands-on maintenance and repair for all in-house equipment, including conveyor and sortation systems, shipping and receiving dock equipment, HVAC systems, lighting, and interior office systems
- Coordinates equipment installation including coordinating and supporting specialized contractors during installation process
- Coordinates equipment repairs across shifts and responds to building maintenance needs
- Responds with a sense of urgency to repair requests which may delay shipment of goods to our customers
- Ensures that necessary repairs and improvements are made to the building, grounds and utility equipment
- Ensures optimum supplies of repair parts and other essentials are available for DC and equipment maintenance
- Utilizes interaction with warehouse personnel share and train others on the best and safest methods for equipment use, troubleshooting simple repairs, and preventative measures to avoid equipment down time
- Five or more years’ experience in an industrial maintenance role
- Strong experience in industrial facilities maintenance and repair, large conveyor and sortation systems, and general preventative maintenance responsibilities
- Electrical and welding skills are a plus
- Closely follows all preventative maintenance requirements
- Closely follows all safety requirements, actively engages in reducing safety risks, and advises management of any recognized safety concerns
- Carry out shop-fitting, general maintenance and repairs in night shifts
- Develop in-house crew standards and practices
- Ensure the provision of an excellent service to all stores
- Ensure all Health and Safety policies and procedures are being followed
- Assisting with window installations with Visual merchandisers
- Knowledge of Micro Main or other computerized maintenance program
- 2 years plumbing and electrical experience
- Basic carpentry experience
- Electrical experience
- Experience with painting/staining
- Experience with siding
- Must be able to read, write, speak and understand English fluently
- Able to communicate in a professional manner with guests and homeowners required
- Valid CO driver's license and satisfactory driving record required
- Experience in plumbing and HVAC required
- Ideal candidate must be able to work both independently, as part of a team, have strong communication skills and be a self starter
- Must be proficient with computers
- Must be able to work weekends, holidays and on-call evenings
- Resumes required
- In-person interviews preferred
- 2-4 years general experience required, building maintenance experience preferred
- Experience in electrical, painting, drywall and carpentry preferred
- Minimum 5 years of experience as a maintenance technician in a broadcast television station
- Ability to sit and stand for extended periods of time
- Ability to lift 20 lbs
- Must possess a valid drivers’ license
- Associate degree or equivalent technical and IT experience required
- Maintain and repair all store equipment, to include air conditioning, electrical, plumbing, all other building systems
- Support all other stores maintenance needs
- Maintain adequate repair parts inventories
- Manage assigned service calls and prioritize work based on departmental guidance
- Submit and complete work orders per Peruse CMMS system
- Provide written reports on stores as required
- There are no supervisory responsibilities for this position
- 2 or more years’ experience in HVAC, electrical, plumbing, and general building maintenance or documented formal training in at least one or more skill sets
- Must have a High School Diploma or equivalent is required
- Ability to work a flexible schedule based on company needs
- Must possess a valid Driver’s license in the state that you reside
- Freon Recovery Certificate is required
- THIS POSITION IS LOCATED IN THE ORLANDO MARKET*
- Repairs cable in emergency situations while working on stand-by for a one-week period. Must have the capability to be at outage sites in the 30 minute response time goal, at maximum 60 minutes response time
- Monitors Cheetah, Path Track and Unified tools on a daily basis to prevent plant outages and improve system reliability
- Demonstrates a strong commitment and dedication to delivering excellent customer service through executing by Time Warner Cable's Mission and Values
- Maintains a strong line of open communication with direct Supervisor and management team to address and resolve issues in a timely manner and drive productivity
- Must possess knowledge of basic electronic theory including Ohm's law formulas, voltage conversions, basic communication transmission fundamentals, cable TV fundamentals, complete knowledge of all company, FCC/City subscriber specifications, TWC, Federal and State OSHA regulations, and General Order 95 and 128 rules and regulations
- Must have knowledge of CLI leakage requirements, working strand and lashing wire and general construction and pole line transfers
- Must have knowledge of minor troubleshooting and repairs, signal level and other troubleshooting devices
- A minimum of six months experience as a Field Technician 4 or 5 or equivalent is preferred. Experience as FT3 may be considered on a case by case basis
- Associates in Electronics or Industrial Maintenance is preferred
- Experience with Rockwell Programming Software, ie. RS Logics 5000
- Ability to troubleshoot and repair Hydraulic and Pneumatic systems
- Perform repairs and maintenance in warehouse or office facilities, or on machines and equipment
- Typically performs work in one or more of the maintenance trades: carpentry, plumbing, painting, machine and equipment repair, electrical, sheet metal fabrication, and welding
- Conducts routine, periodic, or special inspections to determine repair and maintenance work necessary to prevent breakdowns of facilities, machinery, and equipment
- Tests, inspects, troubleshoots, and repairs machines and equipment
- Use blueprints, sketches, layouts, wiring diagrams, drawings, and specifications
- Assists maintenance team and supports all aspects of the maintenance department as needed, including general building and grounds maintenance
- Completes plant work orders, accurately and on time
- General industrial mechanical maintenance 2 years
- General industrial maintenance and electrical systems
- Ability to read, write and understand polices, guidelines, specifications and safety standards
- Maintaining equipment and using a computerized maintenance system
- Responding to equipment breakdowns and completing repairs to equipment
- Troubleshoot and correct malfunctions on industrial/assembly equipment, machinery and building as required
- Perform preventative maintenance as per schedules
- Request replacement parts
- Adhere to the company's Health and Safety policy and safe working practices
- Adhere to Caterpillar's Values in Action: Integrity, Commitment, Excellence, Teamwork
- Undertake training/further learning as required
- This position requires an experienced Maintenance Technician relevant to an industrial manufacturing environment
- Minimum of 3 years Industrial Maintenance experience and or training
- Be self-motivated and have the ability to work on your own initiative
- The ability to work closely with others is imperative, requiring team participation to achieve the agreed objectives
- Have a fully flexible approach to the job role and responsibilities
- The ability to read, comprehend and follow verbal and written instructions/procedures
- Good problem solving skills, necessary to get to the root cause of issues
- Willing to work a multi-shift system and overtime
- Experience in using PLC based systems would be an advantage
- Skilled in both Mechanical and Electrical
- Strong working knowledge of Microsoft Office Suite (Word, Excel, Publishers, Access)
- Ability to meet deadlines and be resourceful and have skill to solve technical issues
- A degree in Computer and/or Electrical Engineering preferred but not required
- SBE Certification preferred but not required
- Extended experience and training at a Broadcast Facility will also be considered
- Must be solution-oriented, proactive, and willing to dig to find a sound resolution
- Prepares and sets up machinery for scheduled production runs
- Performs emergency/unscheduled repairs on machines, equipment and plant facilities during production
- Performs regular preventive maintenance on machines, equipment and plant facilities
- Reads and interprets equipment manuals and work orders to perform required repairs, maintenance and service
- Diagnoses problems, replace or repair parts, test and make adjustments on machines and equipment
- Performs a variety of electrical, plumbing and carpentry functions
- Completes hot work permits
- Displays a positive attitude towards safety, works safely and follows all the Company's safety policies and procedures
- The mechanic must be capable of setting up all production lines and associated equipment independently
- Obtain and review all relevant documentation to ensure an efficient and top quality set-up
- Adjust programs and tooling as required to ensure the part fits to fixture
- Generate an approved sample and document the production run approval appropriately
- Troubleshoot problems with current production tools to ensure timely and appropriate repair
- Ensure that all production line programs are updated and documented appropriately
- Ensure that appropriate standard job procedures are in place, understood and followed
- Monitor and enhance the preventative maintenance programs for all production lines and associated equipment
- Ensure that preventative maintenance sheets are completed appropriately and on time
- Assist in the establishment of an appropriate inventory of all spare parts requirements
- Ensure that production training remains current and operate production equipment as required
- Work to ensure the most efficient machine utilization
- Ensure that appropriate channels of communication are maintained and enhanced between all employees
- Assist with the operation of production equipment as required
- Work as a team with other employees to ensure that objectives are completed efficiently and effectively
- Ensure that all safety requirements are being carried out when performing duties
- Comply with defined Business Management and Environmental Management Systems requirements
- Provide support for the continuous improvement initiatives
- Provide support in the attainment of key operating goals as outlined by established measurables
- Carry out all duties focusing on the goal of internal and external customer satisfaction
- Other duties as may be assigned by the supervisor or designate
- Post secondary education with full certification as an Electrician, Millwright or similar trade with the associated apprenticeship
- A minimum of three years in a related trade position is required
- The ability to interpret complex prints is required
- Knowledge of PLC programming principles is required
- Knowledge of CAD/CAM would be a definite asset
- Education or equivalent experience in hydraulics/pneumatics, electrical and/or welding is a definite asset
- Attention to detail is key
- An individual in this position must be capable of initiating and directing their work with minimum or no supervision
- Perform daily rounds-check boilers, pools, common areas, sprinkler systems, fire pump room, fire panels
- Will require lifting of 50 lbs. or more
- May require lifting arms above head and shoulders to work in ceiling
- Maintain tools and work area in safe, secure, and efficient manner
- Using CMMS-generated preventive maintenance worksheets to maintain production facilities machinery and equipment according to the manufacturer’s recommendation and good maintenance practices
- Monitoring maintenance upkeep checklists to ensure efficient equipment operation. May assign tasks to Level I Maintenance Technicians
- Operating, troubleshooting, and repairing electrical and mechanical assembly and material-handling equipment, including, but not limited to fork trucks, conveyors, robotic equipment, and related tools and equipment
- Working with Level III Maintenance Technician(s) to perform preventive, corrective, and predictive maintenance on high tech automated equipment
- Should be cross-trained on maintenance and repair of all production facilities systems and equipment
- Familiar with PM procedures, including performing PMs, logging completion, etc
- Able to troubleshoot and diagnose problems with mechanical, electrical, and electronic systems, such as Programmable Logic Controllers (PLCs), System Control Software (SCS), scanners, etc. Able to recommend and implement corrective action
- Performs routine and scheduled maintenance per PMCC’s and Work Standards on machines such as cleaning, lubricating parts, and daily repair
- Completes PM Check Sheets. Uses diagnostics test equipment to perform PM activities
- Understands function and operation of each station on a production line
- Runs each station on production line to verify work performed. Operates equipment to run samples to verify, test and confirm the equipment functionality
- Powers on and off production equipment. Performs and completes line start-up and shutdown to and from full auto
- Performs off-line measurements for verifications
- Creates, develops and updates PM check sheets according to established format
- Creates matrix tables and charts / graphs to show PM equipment activities and trends
- Tests damaged machine parts and determines if major repairs are necessary
- Learns and understands basic AC / DC theory, motor troubleshooting, circuits, machine shop tools, temperature controller, tool safety, Servo systems, and Keyence PLC training
- Position requires high school diploma or GED and 1-2 years of maintenance or related advanced manufacturing experience
- Completion of Canon Technical Training Academy Process Operator curriculum preferred
- Must be able to read and follow work standards and complete check sheets, forms and logs
- Shows demonstrated ability to understand and apply electrical and mechanical theory
- Position requires comprehensive knowledge of company policies and procedures
- Demonstrates ability to make appropriate decisions and work independently
- Take responsibility for completion of task. Projects and to do lists on that shift
- Provide superior service to our customers (internal and external) at all times. Follow The Resort’s etiquette guidelines
- Prepare estimates of cost of repairs
- Plan and carry out various maintenance and repair tasks in response to requests by guests
- High school diploma, plus 3-4 years of relevant work experience and/or trades training, or a combination of education and experience from which comparable knowledge and skills are acquired
- Operation, maintenance and repair of all natural and manufactured gas distribution lines, including all valves and control devices
- Operation, maintenance and repair of building automation systems for HVAC, including consoles, data gathering panels, remote sensors and indicating devices
- Operation, maintenance and repair of sump pumps
- Assist in the replacement of DDC control valves & associated systems
- Maintain the mechanics on all plant and machinery
- Carry out pneumatic control work on panels etc
- Responsible for the coordination of all work carried out by service engineers
- Deputise for Maintenance Supervisor in absence
- Responsible for Record Keeping in relation to plant/equipment and services to conform to all relevant legislation
- Ordering and stock maintenance of small items
- Be an interactive team member, promoting and being part of continual improvement departmental multi skilling and training in order to achieve world class function standards
- Ensure regular inspection and servicing that may be required on compressed air systems to ensure we comply with statutory regulations
- Ensure regular testing / servicing of all plant and equipment to ensure it conforms to current legislation
- Previous relevant work experience as multi skilled Maintenance Engineer
- Qualified 17th Edition
- Experience of fault finding on electrical / electronic, pneumatic and hydraulics circuits
- To work to a planned preventative maintenance schedule (PPM / TPM)
- CNC / PLC related machines experience
- Ability to work with limited supervision
- Works in a safe manner and consider other people around them
- Save money and costs
- Able to root cause a machine failure and implement corrective actions
- Be responsible for the ordering and stock maintenance of small items of equipment
- Ensure regular testing / Servicing of all plant and equipment to ensure it conforms to legislation
- Forklift and MEWP Licences an advantage
- Preventative Maintenance: * Document, analyze and recommend revisions to the IC Data Center Facilities Supervisor, as needed for all preventative maintenance programs on a continual basis for all building mechanical, electrical and life safety systems. Perform and track all preventative maintenance activities including mandatory inspection of life safety equipment; PRV valves and annual fire marshal inspections; HVAC systems to include bearing lubrication; belt change and adjustment; filter change; coil cleaning and oil changes; back-up power systems; Conduct water treatment and chemical analysis for efficient boiler operation as listed on the Preventative Maintenance schedule...25%
- Energy Conservation Plan: * Work with IC Data Center Facilities Supervisor to define operational parameters for energy conservation providing the proper balance of comforts vs. energy costs and verify that all systems are operational per the plan...5%
- General Maintenance: * Assist outside vendor staff with trouble shooting and problem resolution. Assemble, install, move and rearrange office furniture and equipment. Maintain and repair building finishes, hardware and furniture. Replace components of HVAC systems as required, including pumps, valves, relays, contacts, switches, compressors, fuses and motors. Perform roof maintenance to identify and stop water leaks. Troubleshoot and isolate electrical problems. Repair and paint damaged walls. Troubleshoot, isolate and repair minor electrical problems. Determine when outside contractors should be called to complete/assist with repairs...20%
- Contractor/vendor Coordination: * Attend vendor meetings as necessary to coordinate utility interruptions or modifications. Inspect contractor’s work to ensure that safe work practices and standard operating procedures are followed...10%
- Training: * Attend and successfully complete all training required of the Maintenance Technician position as required by IC Data Center Facilities Supervisor...10%
- Customer/contractor/vendor Interaction: * Continuous effort to improve operations, decrease turn around times, streamline work processes and work cooperatively and jointly to provide quality seamless customer service. Interacts professionally with internal and external customers, staff and contractors to maintain an effective working relationship and works in cooperation with the IC Data Center Facilities Supervisor to effectively meet departmental objectives...15%
- Maintenance On-Call Responsibilities: * Provides after hours maintenance and emergency support, on a rotational basis, for the assigned Pearson facilities. Provide emergency support to any assigned Pearson facility in the event of an emergency involving facility operations...5%
- Meetings: * Attend meetings as required by the IC Data Center Facilities Supervisor...5%
- Completing required paperwork/documentation: * Completed forms and reports required to document activities as required by the IC Data Center Facilities Supervisor...5%
- Five (5) years experience in building maintenance for medium to large size commercial or industrial buildings using commercial grade HVAC systems
- Relevant post high school vocational or technical skills training may be substituted for part two (2) years of the experience requirement
- Assisting in developing and implementing goals, objectives, policies, procedures and work standards for the department
- Planning, assigning, scheduling and reviewing the work of assigned vendors/contractors
- Interpreting and applying applicable codes regulations and work procedures
- Inventory and ordering equipment, supplies and materials
- Using tact, initiative and sound judgment within general procedural guidelines
- Safely using tools and operating equipment in the area of assignment
- Communication and effective interaction with co-workers, managers, and the general public
- Strong PC skills and specifically able to use Microsoft Office products plus the ability and aptitude to learn other departmental software (e.g. AutoCAD, CenterStone)
- Superior customer service and communication skills
- Individual must be physically capable of safely operating a vehicle, possess a valid Driver’s License and must have an acceptable driving record
- Self starter and be capable of functioning unsupervised
- Capable of reading blue prints and schematic drawings required for the job assignment
- Experienced in water treatment programs and use of chemicals
- Analytical ability to diagnose problems quickly and correctly for resolution
- Ability to work as a member or a team, often cross-functional
- Ability to work under tight deadlines, with some ambiguity and stressful situations
- Ability to implement Six Sigma and Lean techniques as they relate to the job assignment
- Understand safety practices and principles related to building maintenance activities
- Policies, procedures, equipment, materials and supplies related to the construction, operation, maintenance and repair of facilities and infrastructure found in an office, production and warehouse environments
- Applicable laws, ordinances, rules and regulations
- Standard computer applications related to routine work tasks
- Techniques for effectively dealing with a variety of individuals from various backgrounds, in person, over the phone and email
- Routine and emergency facility equipment maintenance requirements
- Chemical Handling and safety precautions
- Basic knowledge of instrumentation control and applications
- Basic knowledge of HVAC systems components including motors, relays, switches and system controls
- Basic knowledge of electrical, plumbing and pneumatic procedures and services
- Basic instrumentation control and applications to include boiler operations
- Paint and wall surfacing skills
- Knowledge of Life Safety codes and Fire Alarm Systems to include lock out/tag out; Material Safety Data Sheets; Personal Protective Equipment; air and water quality issues and Interim Life Safety measures
- At least 5 years experience in the maintenance of a Distribution center
- Must have conveyor maintenance and repair experience including Shoe sorters and Tilt tray sorters
- Must have electrical experience with Direct current and Alternating current up to 480 volts
- Must be flexible with schedule and available for weekend work and emergency situations
- Basic knowledge of Microsoft Office applications
- PLC troubleshooting experience necessary, programming experience a plus
- Forklift equipment maintenance and repair is a plus
- HVAC/CFC certification is a plus
- Associate’s degree in an electronics discipline highly preferred. Equivalent work experience would be considered
- Demonstrated analytical skills including the ability to use Microsoft Office tools
- Demonstrate good interpersonal and written/verbal communication skills to communicate with internal and external contacts and work in a team environment. Must be able to work independently and complete a high volume of work with little supervision
- Previous experience with robotics, controls, vision systems, lasers and/or SMT equipment strongly preferred
- Installs, repairs, rebuilds and maintains precision machine and production tools and equipment
- Diagnoses machine malfunctions and difficulties, then plans and implements actions necessary to return equipment to operation and prevent future breakdowns
- Rebuilds machines and overhauls troublesome components
- Reads and interprets blueprints, schematics and machine manuals in order to perform safe and effective repairs
- Fabricates parts with or without sketches and prints using lathe, mill, drill press and welder. Operates testing equipment, power tools, hand tools, torches, welders and precision measuring instruments
- Performs skilled operations such as fitting and aligning of bearings, spindles and shafts. Fits, aligns and calibrates measuring devices and feeding mechanisms
- Leads machine tool and processing equipment installation and relocation efforts. Performs erecting, leveling, fitting, and aligning actions necessary for safe and effective installation
- Troubleshoots basic electrical and PLC problems
- Routinely contacts suppliers or manufacturers on part information, repair issues, improvement needs and shipping instructions
- Assists other maintenance team members in meeting department requirements. Serves as a resource to production, engineering and other plant personnel
- Maintains and improves knowledge and skill requirements in all maintenance required trade areas
- Maintains user knowledge of tools, testing equipment, measuring instruments, conveyance and material handling equipment
- Uses PC to update data bases and retrieve information
- Operates company vehicles, conveyance and material handling equipment
- Completes appropriate paperwork, machine documentation and preventative maintenance records
- Maintains a clean, organized and safe work environment
- Trains and guides work of apprentices
- Adjust & repair automotive manufacturing equipment, repairs and services, and test equipment using hand tools and power tools
- May specialize in repairing specific manufacturing equipent, and equipment that is not specific to the manufacturing process
- Troubleshooting and modification to maintain uptime,make modifications to improve efficiency and reliability of equipment and its systems. Oversee modifications by internal and external resources for process changes, new models and expansion
- Use computerized or manual Maintenance Information Systems to document the details of equipment related issues, repairs made, Preventative and Predective Maintenance measures taken, etc
- Make necessary adjustments to parts and machinery to ensure proper production run
- Basic robotics troubleshooting on robots
- Basic electrical circuit troubleshooting
- Use computerized or manual systems to facilitate root cause analysis for failures resulting in major downtime (as defined by management). Once the root cause has been identified, put measures in place that will prevent reoccurance within the affected business unit as well as across the facility
- Ensure new parts get ordered or returned unused part back to the correct stock location
- Update verification forms when needed
- Practice good housekeeping on the shop floor and in assembly cells
- At least one year's experience in a similar position
- Basic knowledge of heating/air-conditioning technologies, plumbing, wiring, carpentry, sprinkler systems, and general building construction and grounds maintenance techniques
- Basic computer skills, to include Microsoft Word, Excel and Outlook
- Valid driver's license and a good driving record
- Must be able to lift/carry up to 50 lbs
- Must be able to understand, speak, read, and write English fluently
- Embrace a proactive attitude to providing best possible customer service to all clients and staff
- Report all issues, even if they are not pertaining to your area of control, anticipate problems and help ensure a clean, safe working environment
- Carpentry/joinery repairs and maintenance
- Identify potential maintenance issues and logging them for action accordingly
- General labouring
- Assisting other team members
- Maintaining a neat and tidy workshop
- Stock Control
- All functional KPIs met or exceeded
- Building or Technical Trade Skills
- Previous experience in General and commercial building maintenance
- Ability to repair equipment
- Hold a Class C Unrestricted Drivers License
- Trade certificate / licenses
- TECHNICAL SKILLS/JOB AND BUSINESS KNOWLEDGE:Keeps skills and knowledge up-to-date. Applies skills and technical knowledge to maintain a high level of accomplishment. Utilizes business systems and, when necessary, understands the business objectives and company operations as they relate to each other. Demonstrates the competency to work with an appropriate level of direction. Makes continuous efforts to learn and understand processes and procedures
- DELIVERS QUALITY RESULTS:Displays a commitment to achieve excellent results. Produces required job results with consistently high quality. Monitors own work to ensure quality; work is generally error free. Accepts responsibility for the results of his/her actions. Identifies problems and presents solutions. Consistently follows through on open projects and new initiatives, ensuring delivery dates are met and communicates progress/status to management in a timely manner
- TEAMWORK / TEAM PLAYER:Collaborates willingly as a team player with peers, customers and suppliers. Values and recognizes contributions made by others. Shares information freely and informs superiors and co-workers in a timely basis. Identifies and implements new ways to improve communication and cooperation between business units and other divisions. Treats all people with respect and dignity and fosters cooperation in a group effort
- COMMUNICATION:Prepares written documents that are concise, grammatically correct and appropriate for the intended audience. Communicates verbally in a clear, organized and articulate manner. Listens effectively and respects the views of others. Presents self professionally and can adapt to a variety of settings. Makes effective presentations. Appreciates the importance of interpersonal and group communications; consistently delivers crisp and intentional messages
- WORK HABITS / TIMELINESS / RELIABILITY:Establishes priorities and organizes work resources to complete objectives by established deadlines. Utilizes appropriate sources of information in making decisions or taking action. Utilizes effective time management skills. Reliably meets challenging goals and assignments, even during demanding or changing work periods. Self-motivates and produces required job results of consistent quality and levels of productivity
- CREATIVITY / INNOVATION / IDEAS:Identifies and develops new opportunities. Drives innovation at every level. Consistently suggests new ideas and new approaches and solutions to improve business. Explores new ways to improve and streamline processes and productivity. Energizes others to achieve exceptional results; gains commitment to new ideas and actions. Listens to and values the ideas of others as an important part of the creative process
- HONESTY / INTEGRITY / TRUST:Maintains confidences; knows when information is inappropriate to share. Acts consistently and ethically in doing their work. Consistently honors commitments. Trusted up, down and across the organization; balances the needs of others with personal goals; fosters a safe environment for sharing opinions. Maintains positive and respectful relationships with co-workers and communicates with all levels in the organization effectively and honestly
- FLEXIBLE / ADAPTABLE / RESOURCEFUL:Quickly grasps, interprets and effectively adjusts to new situations, methods and procedures. Exhibits flexibility in work habits and in addressing and improving processes. Responds positively to change and ambiguity. Can find effective solutions to goals that change regularly
- Learning ability for new tasks and technology
- Assists in training Maintenance Helpers to develop and expand their skills in maintenance and repair functions
- Reads basic blueprints and schematics
- Train employees to work safely, protect company assets and promote corporate safety policies
- Perform and record preventative maintenance on machines and systems
- Responds to service calls to address repairs and safety issues
- Exposure to working at heights and use of ladders, Man lifts, Forklifts, Carts while following safety guidelines when these conditions are present
- Exposure to moving mechanical parts, caustic chemicals, fumes, airborne particles, extreme heat or extreme cold, and outside weather conditions, and consistently follows safety guidelines when these conditions are present
- Repetitive body movement and the ability to stand for long periods of time and lift, push and pull a minimum of 50 lbs
- 5+ years building maintenance including but not limited to electrical, plumbing, carpentry and painting
- Must have strong knowledge or how to use hand tools
- Energetic, adaptable, self-motivated, and excellent organizational skills
- Attend training as required
- Handle confidential information on a regular basis
- Forklift License required
- Able to demonstrate understanding of how job performance affects product quality and customer satisfaction
- Able to manage and schedule multiple priorities and meet deadlines
- Able to use computer and software as required
- Must have good color vision to perform electronic and electrical maintenance and repairs
- Troubleshoot and repair problems on plant facilities and production equipment of electrical, mechanical, hydraulic or pneumatic in nature
- Assists in the implementations and improvement of effective preventive maintenance programs for all equipment, performing scheduled maintenance on facilities and production equipment as required
- Obtain and attend training for professional development and to stay current on maintenance and safety requirements and other training as required
- Complete all work in accordance with IOSHA, NEC, JIC and IDNR standards and regulations
- To work in a safe, quality minded, and productive manner with a sense of urgency to achieve maintenance dead lines and to attain production priorities as scheduled
- Attend daily pre-shift meetings and carry out assigned work loads as directed by shift/area leaders
- Communicates with maintenance manager and maintenance area/shift leaders, and other plant personnel about maintenance concerns, providing complete action plans and status reports as and when required
- Follows and supports Montezuma Manufacturing’s and Magna’s operating principles, including
- Must have high school diploma or GED
- Knowledge of hydraulic, pneumatic and basic electrical systems
- Computer proficiency, Microsoft Word, Excel etc
- Must exhibit high integrity and honesty
- Ability to read, write, analyze, and interpret technical procedures, blueprints, diagrams, schematics, equipment instructions, requirements and business correspondences
- Ability to effectively and appropriately present information and respond to questions from various groups
- Fabrication and mechanical skills
- Ability to obtain and hold a fork truck license
- Work is complex and difficult in character and requires strong technical and broad business knowledge. Requires independent problem solving and decision making with general direction given on project objectives and broad guidance from corporate strategy and goals
- Provides technical support by monitoring, troubleshooting, and repairing all complex electrical, electro-mechanical, automated systems, and robotics systems
- Updates equipment, solves mechanical problems, and gives direction for proper repairs in support of Maintenance Department
- Reviews engineering specifications and designs of new equipment and/or redesign of existing equipment. This includes safety requirements, electrical codes, and standardization of components, cost-effective design, and maintainability of equipment. Maintains machine, mechanical, and/or equipment documents as necessary
- Participates in continuous improvement processes. May work on projects involving cost reduction, up-time improvement, or evaluation of new equipment, etc. Establishes new preventative maintenance procedures and periodically audits/updates existing procedures
- Works independently on assigned projects that range from simple program modifications to major redesigns that may have a mechanical, pneumatic, or electronic scope
- Solves mechanical problems and gives direction for proper repairs. Assigns tasks and trains other staff as needed
- Be able to perform Customer Specific Recommendations
- Associate’s degree in a technical discipline plus significant amount of related work experience
- Or completion of apprenticeship as mechanic or electrician (i.e. journeyman card) and five years’ experience which includes advanced electronics/programming; or equivalent
- Demonstrated ability to troubleshoot, update, and work on all equipment in designated area of responsibility
- Must have current knowledge of electrical codes and electricity and be able to apply it to the job
- Machine rebuilding and mechanical knowledge including hydraulics required
- Demonstrated good interpersonal and written/verbal communication skills to communicate with internal and external contacts and work in a team environment. Must be able to lead, train, and support other staff
- ?At the direction of the Facility Supervisor(s), complete all work assigned through our electronic work order system in a timely, professional manner
- Candidate is expected to inspect all tenant floors, work spaces and Mechanical rooms as directed
- Candidate will be required to perform light painting (touch up’s/small office painting)
- Proactively and/or as directed, replace light bulbs, ceiling tiles and/or carpet tiles. Make small electrical repairs (replace switches and/or outlets) in a safe and compliant manner
- Ensure the successful completion of all work order, preventative maintenance orders, and production support tasks on a daily basis as directed
- Ensure repair parts inventories are organized and kept at sufficient levels (as determined by the Facilities Supervisor)
- Cover overtime projects to ensure contractors are completing work in a safe and professional manner to the high standards of the Ralph Lauren Corporate Facilities team
- Good communication skills. Good working knowledge of computers. Bilingual abilities are a plus but not a requirement
- Possess solid task and detail oriented work methods. The ability to ensure the successful completion of multiple jobs that are simultaneously in progress is critical
- Solid working knowledge and ability in all the mechanical, electrical, and plumbing trades, and a journeymen’s knowledge and skill level in one
- Candidate should have knowledge of light touchups and/or painting of offices and corridors, plastering, wall covering, vinyl repair, proper paint removal, caulking, grouting or other miscellaneous repairs
- Candidate should have basic concept of HVAC systems and use proper safety precautions, HVAC systems and thermostat replacement or repair. Bathroom exhausts repair, tenant space HVAC troubleshooting, and temperature controls
- Candidate must have knowledge of all pertinent electrical panels and wire management and must follow all lock out/tag out procedures
- Solid working knowledge of modular furniture systems
- Experienced in using hand and power tools
- Three years experience as an Maintenance Technician, Mechanic, HVAC mechanic (helper), electrical helper or Carpenter OR.
- Three years plant engineering/facilities Maintenance experience, or two years supervisory plant engineering/facilities management experience
- Associates degree in a relate field, or equivalent combination of education and work experience
- Minimum of 5 years maintenance experience in a manufacturing environment
- Extensive knowledge of programmable logic controls
- Experience with six axis robotics
- PC Training Problem Solving (e.g. 8D’s)
- Employee Charter Time Management
- Programmable Logic Controls Robotics
- Interpersonal Communication Current ISO/TS16949
- Hazardous Communication First Aid/CPR Training
- Personal Protective Equipment Ergonomics
- Bloodborne Pathogens Safety Signs
- Lockout/Tagout Confined Space
- Pedestrian Safety Emergency Evacuation
- 18001 Awareness 10-hour OSHA Training
- Repair and maintain all equipment and facilities expediently to ensure the safe and efficient operation of all equipment required to maintain uptime goals
- Inspect all machinery for defects and potential problems in accordance with the preventative maintenance program, repairing and replacing parts as required
- Order appropriate replacement parts and fluids through the Maintenance Manager
- Determine reasons for equipment failures and advise managers on corrective and preventive actions to eliminate future downtime
- Fabricate equipment components using welders, milling machines, lathes, and other machine tools as required
- Troubleshoot and repair all electrical, hydraulic, pneumatic, and mechanical systems in the molding department
- Assist in tooling and mode changes as required by the production schedule
- Execute lock out / tag out procedures as required on all molding department equipment and facilities
- Communicate detailed job related information utilizing written and verbal communication forms such as team meetings, work orders, and other related reports
- Assist in the implementation, development and maintenance of a computerized maintenance management system (CMMS)
- Maintain a high departmental standard of cleanliness in the Assembly Department areas
- Perform other duties as directed
- Minimum three years maintenance experience
- Minimum two years experience as an Industrial Electrician
- Maintain good tenant relations through prompt, courteous response to tenant requests
- Handles general maintenance and operations of the assigned property that includes but is not limited to HVAC, electrical, plumbing, lighting, painting, etc
- Handles all tenant repair calls and common area repairs including but not limited to, broken toilets, light/lamp replacements, leaking sinks, touch-up painting and normal maintenance and repair items, and/or the coordination of these repairs with outside contractors, if these items are a Landlord responsibility
- Acts to assure Cushman & Wakefield standards are maintained, but confers with Property Manager before spending unbudgeted funds in access of $200.00 or authorizing outside vendor work, not already approved by the Property Manager
- Assist with purchasing parts and supplies required within the area of responsibility under the guidance of the Property Manager and the Chief Engineer
- Assume additional authority as delegated by the Property Manager
- Assist and maintain an effective operation and maintenance program
- Maintain a productive preventive maintenance program with accurate up-to-date records
- Maintain a good working relationship with tenants, employees, and outside contractors
- Assist in maintaining an adequate stock of spare parts and supplies
- Assist in securing a broad spectrum of qualified outside contractors, and supervise same when they are working on the property
- Assist in maintaining emergency procedures for the property and total awareness of those procedures. Respond to all emergency calls and keep Property Manager advised of all issues
- Assume additional responsibilities as delegated by the Property Manager. Maintain all parking facilities including: car stops, signs, filling of pot holes, gates, arms, lights and systems associated with each. Communicates promptly to the Property Manager all issues and concerns relative to the operations of the building
- Constantly inspect physical plant of property and perform whatever maintenance tasks are necessary to maintain property in first-class condition, as well as those items which may be considered a hazard to safety
- Clean debris from roof on a quarterly basis. Be aware of the condition of each roof
- Install, maintain and repair television equipment, systems and installations, including but not limited to routing and switching systems, studio equipment, receivers and links, recorders and players, edit systems, live vehicles, RF and ENG/SNG equipment. A working knowledge of high powered TV transmitters is a plus
- Understand and use technical manuals to complete maintenance duties
- Use diagnostic equipment and test and measurement equipment, as required, to complete maintenance duties
- Work effectively and courteously with other departments to solve equipment and operational problems. Ascertain and satisfy other departments’ needs for service
- Order parts as required and approved for repair and maintenance of broadcast equipment
- Provide documentation, as required. Documentation may include, but is not limited to, technical drawings, databases, repair logs, procedures, purchase orders and parts account reconciliation
- Moves throughout the station and the department to ascertain and coordinate other departments’ needs
- Required to ensure timely repair of equipment
- Regularly set up, adjust, assemble, control, test and operate station equipment to meet engineering department requirements. Much of today’s technical equipment is computer based. Therefore all applicants must have a thorough knowledge of computer systems
- Required to keep skill sets and knowledge current in existing and emerging technologies
- Must be proficient with word processing software and job specific software such as databases, terminal and control programs. Most of the WGHP drawings are done on AutoCAD. The applicant must be proficient with this program
- Must be able to push a cart with equipment on it
- Must notify the Manager of Engineering or VP, Engineering and Operations of any accident involving personal injury or station vehicles, no matter how minor
- Must respond to all pages and phone calls as required by supervisor or schedule
- Attend and participate in department meetings, safety meetings and training
- Regularly bends, stoops and crouches to arrange, lift and transport engineering related equipment
- Occasionally drives automobile for long periods of time to perform job-related activities
- Regularly receives and gives information and instruction via telephone and e-mail to station personnel or outside vendors
- Mechanical/Electrical background
- Excellent troubleshooting
- Possess excellent PC computer skills
- Must possess strong analytical/problem solving skills
- Must be self-directed and goal oriented
- Must have knowledge of commercial power distribution
- Able to perform all tasks associated with the Maintenance Mechanic position
- Participates in the development, implementation, and maintenance of internal maintenance policies and procedures and ensures compliance with regulatory and manufacturers' maintenance policies and procedures
- Assists with the preparation of annual aircraft maintenance budget and responsible for maintenance budget expenditures. Reviews maintenance invoices for payments
- Prepares specifications for bids on outside repairs, maintenance and inspections. Reviews bids and makes recommendations to the Maintenance Manager
- Works with the Maintenance Manager to establish schedules for periodic inspections, general overhaul, repairs and modifications
- As directed, maintains records as required by FARS, manufacturers' and company policy, or monitoring these records if maintained by an outside agency
- Follows all maintenance safety rules and procedures as established by the Maintenance Manager
- Maintains spares and ground support equipment inventories
- Helps monitor security and environmental affairs, including completing material safety data sheets on all chemicals, fire drills and safety training
- Responsible for maintenance and upkeep of the aviation hangar and office facility
- Performs collateral duties as required
- FAA Airframe and Powerplant license required
- 6- 9 years business aviation experience required with a broad knowledge of the maintenance of class, category, and type of aircraft that Visa operates (G550 and Falcon 2000LX)
- Continuing education in aviation maintenance through accredited schools or manufacturer’s training programs required
- Expert skills in decision-making and building partnerships; internally and externally
- Excellent planning and organization skills and business judgment, including the ability to anticipate the impact of decisions/initiatives
- One to five years of maintenance experience
- Vocational diploma, or equivalent combination of education and experience is required
- Work experience in some of the following areas is preferred
- Building Maintenance - Perform general facility repairs such as minor plumbing, general electric, lighting, painting, and wall repair. Perform minor repairs on doors and dock plates to resolve problems and ensure successful operation. Communicate with all peers, customers, and management to accomplish assigned and critical tasks. Oversee 3rd party project completion
- Conveyor System - Support and perform reactive repairs and preventative maintenance to maintain operation of conveyors and sorter equipment, including the assembly / disassembly of pneumatic sub-systems. Troubleshoot conveyor system controls and adjust / calibrate or repair as needed. Work with vendor partners to determine the root cause of issues and appropriate corrections. Oversee production-related issues and make necessary corrections to sortation controls as needed
- Equipment Maintenance - Perform preventative maintenance to production-related equipment, Powered Industrial Trucks, and building equipment as needed. Maintain complete inventory and cleaning of all equipment and work areas. Identify and correct safety hazards and potential maintenance issues before they become critical. Support the design and implementation of continuous improvement processes
- Electrical - Perform troubleshooting and needed tasks involving low and high voltage electrical and control systems of 480 volt devices (AC & DC), including repair or replacement of system components
- Supervise Maintenance Techs - Execute basic supervisor responsibilities for hiring, orienting & training, assigning work, evaluating performance and providing feedback to direct reports
- Performs machine/equipment efficiency diagnostic and electronic repairs
- Trouble shoots electrical problems
- Assist with monitoring of contractor’s work and coordinate facility projects to ensure technical specifications and OSHA compliance
- Maintain boiler, chillers, air washers, air compressor, vacuum motors etc
- Plumbing, painting, wood working as necessary
- Follow safety rules and procedures at all times. Alert a supervisor or manager of any safety issues. Wear required PPE. Perform general housekeeping
- Basic computer skills required
- Effectively communicate both written and verbal
- Must be able to effectively communicate with all aspects of the business internally and externally including Golden Lady project and management teams
- Extremely organized and can prioritize multiple projects
- High school diploma required; some college preferred
- CPO (Certified Pool Operator) licensed or be able to complete class/test, is preferred
- Colorado Valid driver's license with an acceptable record is required
- Able to communicate in a professional manner with guests and homeowners
- Be able to stand for long periods of time of up to 6 hours
- A flexible schedule including weekends, holidays, etc is required
- Previous building maintenance experience - Preferred
- Assists in installation, preventative maintenance, emergency repairs, and modifications/upgrading of forklift, conveyor electrical, electronic, building and mechanical systems pertaining to facilities or production equipment
- Maintains validated parameters as well as cGMP's during the operation of equipment, thus permitting the timely release of product and meeting functional, cosmetic, and other quality control specifications
- Assists in equipment-related recommendations that will secure improvements in productivity, efficiency, cost control, and product quality
- Performs duties, per SOP and utilizes related documents of equipment during all job functions within assigned areas under the guidance of the Supervisor
- Helps implement methods that will maximize reliability of production and/or facilities equipment within its limitations
- Monitors and controls equipment in assigned areas to ensure the operation of equipment within written SOP/cGMP guidelines
- Assists in monitoring daily performance of production and/or facilities equipment
- Identifies equipment failures which may affect performance and makes recommendations for corrective action
- Helps compile weekly and/or monthly reports to identify results as they pertain to operational standards
- Ensures equipment operation, maintains cGMPs, and ensures required documentation is compiled and retained
- Adhere to all safety codes and practices for self and others throughout the plant
- Minimum of 2-5 years related maintenance experience
- Trade skills in one or more of the following: welding, electrical, mechanical, HVAC, instrumentation, forklifts, building construction, conveyor
- Ability to interpret and understand maintenance manuals and electrical equipment blueprints
- Knowledge and experience in industrial electrical and equipment mechanics
- Ability to lift up to 55 lbs. regularly
- Perform basic set-ups / changeovers for packaging and process equipment within focused work centers or line including cleaning / sanitizing equipment as required
- Maintain packaging equipment during production runs; clear jams, change labels, change over-wrap, reset coders / code blocks, initiate trouble shooting / corrective action investigation and quality checks as required, and perform basic operator responsibilities
- Move components and mass from staging area to Production floor as required
- Initiate trouble shooting; Assess and address failure modes of pneumatic and hydraulic systems as applicable
- Initiate trouble shooting of mechanical systems
- Execute assigned preventative maintenance work orders in accordance with identified schedules
- Perform other duties as assigned and required
- Education: Minimum college/technical diploma
- Experience: None required
- Testing: Candidates will be required to pass a written mechanical aptitude test, a personnel test and a practical mechanical test to be considered for the role
- Follow the Company health and safety objectives and support the company’s health and safety directives to provide a safe and healthful workplace for all employees, this includes
- Regulatory compliance with local, state and federal legislations
- Follow plant-wide measurable and goals that meet or exceed industry standards, and are monitored, tracked and audited on a regular basis and communicated to employees
- Follow instructions from supervisors for enforcing safety rules and attending the necessary training and follow corrective actions to ensure proper focus on established objectives
- Maintain records of work performed, as required
- Perform PM’s on molds, as scheduled
- Assist the Lead Maintenance Tooling Technician in troubleshooting of tooling issues
- Must be able to perform repairs to molds within capabilities of AIM’s tool room
- Demonstrate the ability to perform preventative and predictive maintenance on all equipment in the Mold Department repairing and replacing parts as necessary
- Must follow the company Lock Out/Tag Out Program
- Must demonstrate the ability to use required hand tools for the Mold Department and have all tools and equipment required to perform work prior to beginning AIM
- Fabricate new equipment or supplemental pieces when needed by using tooling machines such as milling machine or welder
- Assist Maintenance Technicians
- Assist Assembly Department
- Associates Degree in a related field; or equivalent combination of education and experience
- Working knowledge of hydraulics, pneumatics, and electrical
- Knowledge of manifold systems preferred
- Ability to modify or create blueprints to document any repairs
- Ability to operate: Surface grinder, milling machine, lathe, and welder
- Demonstrated oral and written communications skills
- Computer skills, including Microsoft software, a plus
- Minimum 5 years of experience in an automotive manufacturing environment preferred
- Minimum 3 years tool room experience preferred
- PC Training Problem Solving (e.g. 8D’s, etc.)
- Managing the Employee Charter Time Management
- Interpersonal Communication ISO/TS16949:2002
- Hazardous Communication Performance Management
- 18001 Awareness 10 Hour OSHA Training
- Normal amount of sitting
- May be required to stand in excess of 6 hours
- May be required to lift, push and/or pull 60 pounds
- Average mobility to move around a manufacturing environment
- Able to conduct normal amount of work at a computer
- Minimum of five years’ experience in building and facilities maintenance, including HVAC, electrical and basic plumbing and carpentry experience. Current HVAC and EPA certifications are preferred
- High school graduate or equivalency required; associate level degree is preferred
- Must be willing to work a rotating, on-call schedule including weeknight and weekend coverage
- Knowledge of general maintenance, the use of hand and power tools, the ability to understand mechanical systems
- Knowledge of current laws pertaining to facilities maintenance, including OSHA, ADA, and hazardous materials communication and the ability to follow all safety and health standards
- Ability to understand, devise and administer preventative maintenance plans
- Must be in good physical condition, including the ability to lift, carry or move 50-80 lbs. and to bend, stand or walk extensively
- Ability to manage emergency situations
- Sound judgment and effective decision-making skills
- Excellent organizational, customer service and communications skills
- Cultivating a spirit of cooperation and teamwork within the maintenance team and with all other departments
- Must be able to pass company drug test and criminal background check
- Comply with smoke free campus
- Help maintain all equipment, buildings, grounds and infrastructure in good working condition
- Perform general maintenance, repairs and upgrading of facilities and grounds, including HVAC, electrical, and basic plumbing and carpentry. Assures all work is completed safely, on-schedule and according to specification
- Complete all aspects of preventative maintenance, including inspections, repairs, written documentation and appropriate updating
- Provide maintenance services to guests and staff in a timely, courteous and efficient manner
- Provide weeknight and weekend “on-call” coverage according to a monthly rotating schedule
- Helps maintain and monitor the water system and fire protection systems
- Helps coordinate the maintenance and upkeep of all company vehicles
- Assists with the supervision of overnight security staff
- Assist in managing emergency situations
- Cultivate a spirit of cooperation, team work and problem-solving at all times
- Technical training in the following areas
- Hydraulic/pneumatic system maintenance and repair
- Mechanical power transmission maintenance and repair
- Combustion gas train maintenance and repair
- Industrial electronics
- Welding and fabrication
- Machine tool operation, maintenance and repair
- Automotive, forklift, work platforms operation
- Robot and PLC programming and trouble shooting
- Perform entry-level maintenance work in several of the following areas
- High School Diploma or Equivalent – required
- Trade School Diploma/Certificate – preferred
- Must be able to lift 50 pounds – required
- Must be able to stand or walk for up to 8 hours – required
- Must have flexible schedule to include working nights and weekends – required
- Previous maintenance experience – required
- Basic computer skills – required
- CPO Certified and experience with pool/tub operations – preferred
- Must be able to carry ladder up and down stairs with required tools – required
- Must be able to lift arms above head and shoulders to work in ceiling (i.e. small leaks, electrical shorts, replace motors) – required
- Performs repairs as required
- Performs preventive maintenance on equipment (building, conveyor, forklifts)
- Performs necessary modifications to the equipment, conveyor system, or building
- Proposes new methods and procedures for maintaining equipment
- Provides equipment status report
- Reports all unusual maintenance problems
- Performs daily clean up of work areas
- Follows safety guidelines established by manufacturer, Dick's Sporting Goods, or government agencies
- Ensures that supplies and tools are properly used and maintained to minimize cost
- Operates manual and mechanical equipment in a safe manner
- Must be a self-starter requiring minimal supervision
- Other duties as business needs require
- Preparing working papers and state & local tax returns (including analyzing and accruing any use tax due in all states)
- Replying to state inquires and working with external auditors as necessary
- Assisting in researching of nexus trigger and risk assessment of business operations performed within different states
- Preparing and reviewing various schedules for submission of VAT returns
- Researching and interpreting SALT and international tax jurisdictions issues i.e. EU VAT, Canada Goods & Services Tax (GST)
- Reviewing and preparing personal property tax returns and related working papers
- Reviewing and preparing unclaimed property tax returns
- Preparing and updating fixed asset reports for the tax department
- Coordinating with consultants on various domestic and international tax matters; and
- Proactively monitoring changes in federal tax and state & local tax regulations
- Performing other federal tax related job functions as directed by the Director
- Bachelor’s Degree in Finance, Accounting or related field or equivalent work experience required. Master’s Degree in Taxation or Accounting preferred
- CPA with an inclination towards learning state and local tax and international indirect taxes preferred
- Masters of Taxation or Accounting or closely related field i.e. CPA with an inclination towards learning domestic tax and international tax
- Possess an industry background including retail, financial services, manufacturing and telecommunications a plus
- Should be good with numbers and financial data reporting
- 1 -2 years of current or recent experience in accounting or tax department
- Strong computer technical skills required analyzing and manipulating data and spreadsheets - proficiency with Excel is required
- Detail oriented person with strong communication skills is required; and
- Familiarity with Vertex, Sabrix, Avatax or other automated tax collection and compliance software a plus
- Minimum of one year of experience in building and facilities maintenance, including basic electrical, plumbing, carpentry or HVAC experience. Current EPA certifications are desirable
- High school graduate or equivalency required; associate level degree or bachelor’s degree is preferred
- Mechanical aptitude, knowledge of general maintenance, the use of hand and power tools and the ability to understand mechanical systems
- Professional demeanor and the ability to work well with guests and staff
- Must be able to pass criminal background check
- Ability to live on-grounds in staff housing
- Provide weeknight and weekend “on-call” coverage according to a monthly rotating schedule. Requires on-grounds residency
- Perform general maintenance, repairs and upgrading of facilities and grounds, including basic electrical, plumbing, carpentry and HVAC. Assures all work is completed safely, on-schedule and according to specification
- If you are experienced in buildings and facilities maintenance, hardworking, and have a passion for non-profit service, send your resume, a cover letter explaining your interest in the Maintenance Technician position and three references to Jordan Domin, Director of Leadership Development. In lieu of a resume, you may also apply online at https://blueridgeassembly.org/index.php/join. Incomplete applications will not be accepted
- Forklift operations/inspections
- Ability to squat and bend over at the waist
- Ability to stand and walk for extended periods of time in temperature extremes on a daily basis up to 12 hours
- Minimum of 3 years Industrial Maintenance experience and/or training
- Experience reading mechanical or electrical blueprints
- The ability to work closely with others to accomplish team goals
- Experience in using PLC based systems
- Previous forklift and man-lift experience
- Perform necessary Carpentry (including minor construction) work in order to maintain the building as a First Class facility
- Maintain all interiors and exterior specialty finishes including paint, metal(s), and tile
- Respond to service calls from tenants including hanging pictures, assembly of office furniture, etc
- Support all theater events and work with event management to fulfill requirements
- Past involvement in restoration of Landmark facility preferred
- Knowledge of Art Deco construction materials and processes preferred
- Ability to excel in the execution of very detailed oriented work within a variety of trade areas
- Excellent organizational skills and ability to research, locate and work with vendors which deal in obscure materials necessary to maintain the architectural integrity of the building
- Although this is a non-union position, must be able to work with a variety of in-house union personnel and outside contractors
- Must be able to work off-hours when required
- Completes Work Orders, PM Sheets, Logs, and other written or computer-based documents according to established procedures
- Diagnose Mechanical and Electrical problems using technical drawings (e.g., blueprints, Electrical/Mechanical Schematics) and diagnostic tools (e.g., multi-meter, laptop)
- Three to Five years of related experience in Material Handling Equipment (Conveyors and Sortation), Mechanical Troubleshooting, Maintenance and /or Installation is required
- Ability to work independently in the absence of supervision
- This position will be scheduled to work Monday-Friday from 11pm-7:30am **
- Maintains, troubleshoots and repairs all presses, dryers, other equipment, electrical and mechanical
- Performs routine preventative maintenance on all building support systems
- Troubleshoots power distribution systems, branch circuits, lighting systems, transformers, and wiring methods and materials
- Assists in office-space build-outs, construction and remodeling projects
- Promotes and conducts good housekeeping practices
- Dedicated to supporting production by working in a safe, customer-focused manner
- Develops and maintains good working relationships across all levels in the organization
- Some Computer Skills (Windows Based Programs)
- Excellent attention to detail and ability to work unsupervised
- Experience with a Computerized Maintenance Management Solution(CMMS) platform.Working knowledge of Maintenance Connection is a plus
- Demonstrated leadership or supervisory experience
- Excellent proven safety record
- Additional Skills and Experience
- Able to operate and trained on all arial equipment, such as boom lift and scissor lift
- Forklift experience or the desire to be trained on Forklift
- Qualifications to be considered
- Must have High School Diploma/GED. Trade School completion preferred
- Must have at least 1 year of recent continuous employment
- Must be willing and able to be certified on motorized equipment
- Good record keeping of maintenance activities
- Report all unusual maintenance problems
- Must be able to interpret blueprints and schematics
- Must have a mechanical and electrical background and possess good troubleshooting skills
- Knowledge of MS Word and Excel
- 2 year technical degree or equivalent acquired skills
- Ability to diagnose and repair electronic equipment problems down to the component level
- Experience in the repair of television broadcast electronic, LCD monitors, and CRT monitors
- Associates degree in electronics technology
- Performing preventive and corrective maintenance on assembly equipment in production facilities building, in accordance with work orders and technical documentation as assigned in a timely manner
- Responding to service requests and work orders with limited supervision and direction without interrupting production facilities operations
- Within the guidelines of authorized Company policies, programs, procedures, budgets, laws, and good business ethics, coordinates the activities, plans, and programs of the designated areas of responsibility
- Using CMMS-generated preventive maintenance worksheets to maintain production facilities machinery and equipment according to the manufacturer’s recommendations and good maintenance practices
- Under limited supervision, performing assigned preventive maintenance tasks and minor mechanical repairs to production facilities equipment
- Performing general building maintenance as directed, such as lamp replacement, simple construction, overhead doors, and plumbing
- With direct supervision, performing basic electrical preventive maintenance, to motors, lights, and electrical panels
- Operating and maintaining production and material-handling equipment, including but not limited to fork trucks, conveyors, robotic equipment, and related tools and equipment
- Lubricating production and material handling equipment in accordance with preventive maintenance schedules
- Organizing lubrication equipment and recommending changes to lubrication schedules. Submitting tools / requisitions for lubrication equipment to the appropriate supervisor
- Organizing and cleaning maintenance shop areas
- Requesting direction from more senior technicians for unclear or advanced tasks
- Maintaining a strong mechanical fundamental knowledge
- Striving to acquire the skills and knowledge of a Level II Maintenance Technician
- Proper use of safety equipment, such as harnesses, electrical safety gloves, glasses, and shields
- Previous maintenance experience in manufacturing setting
- Experience in production facilities assembly and material-handling equipment
- General understanding of Robotics technology and related systems where applicable
- Understanding of lockout / tag out procedures
- Experience with basic hand and power tools in an industrial setting
- Understanding of mechanical theory, including the construction and operation of bearings, hydraulics, pneumatics, and conveyors
- Performs preventative maintenance on equipment as assigned
- Trouble shooting of electrical, hydraulic, pneumatic, PLC’s, robotics, resistance, mig welding and HVAC as needed
- Welding/fabricating and painting as required
- Assist in design and construction of special equipment
- Works in a safe manner and observes plant safety rules and regulations at all times. Aware of all Health, Safety & Environmental policies
- Recommends proposals for improving products, processes, systems, productivity and working environment
- Perform all other duties as required
- Solid background in electrical, hydraulic, pneumatic, PLC’s, and robotics
- Working knowledge of HVAC systems
- Knowledge of personal computers and software
- Capable of reading blue prints and schematic drawings
- Solid background in MIG and stick welding
- Knowledge in operating a fork lift or capable of passing a fork lift operators test
- Capable of working on their own with little supervision
- Be able to fault find on electrical, controls, pneumatic, hydraulic & mechanical systems
- Work to a planned preventative maintenance schedule
- Liaise with the Production & Engineering Depts. to ensure equipment availability
- Have experience in PLC / CNC related machines
- Experience of PLC, Electrical / Electronic & CNC systems, Fault finding & diagnostics
- Hydraulic & pneumatic machine control systems
- Experience of all Mechanical aspects of Machinery & Equipment
- Experience of Fanuc / ABB Robots an advantage
- Driving license, recognised forklift license, MEWP license, would also be an advantage
- Repair plumbing and mechanical systems, kitchen equipment, lighting, etc as assigned
- Track time and materials on specific work orders and turn in appropriate paperwork
- Identify and order parts required for maintenance systems
- Communicate with facility managers, employees, and department regarding work status
- Other duties as assigned by Manager, Maintenance Coordinator, or Lead Technicians
- High School Diploma or equivalent - required
- Previous Maintenance work experience - required
- Must be able to work unsupervised, as well as part of team
- Must be able to lift up to 100 lbs
- Must be comfortable woking outside in extreme weather conditions
- Job requires standing for long periods of time, frequent walking, reaching, climbing and good balance, kneeling crouching and crawling
- Knowledge of Beaver Creek - preferred
- Perform entry-level maintenance work in several of the following areas: electrical, plumbing, welding, carpentry, painting, mechanical, equipment operation, cabinet/countertop/trim/drywall installation, HVAC, etc
- Assist with pool and spa testing and maintenance
- Tend to any work orders, guest requests, housekeeping requests, front desk requests, room calls
- Maintain all Facilities and Operating Systems in a safe and efficient working order (i.e. Auto doors, exit doorways, required snow/ garbage removal)
- Will require lifting of 20lbs or more
- To carry ladder up and down stairs with required tools (may exceed 20 lbs.)
- May require lifting arms above head and shoulders to work in ceiling (i.e. small leaks, electrical shorts, replace motors)
- Maintain tools and work area in safe, secure and efficient manner
- Trade School Diploma/Certificate - preferred
- Must be able to lift 50 pounds - required
- Previous maintenance experience - required
- General interior maintenance – hang pictures, install keyboard trays, repair office furniture systems
- Plumbing repairs
- Complete assigned system generated work requests for services on a daily basis and within established time frame
- Basic HVAC knowledge – maintain, troubleshoot, and repair to HVAC units in corporate settings and IT server rooms
- Maintains order in mechanical, electrical, work stations, and storage area
- Manage inventory for basic building supply needs such as light bulbs, paint, ceiling tiles, carpet tiles, etc
- Moves office furniture, machinery, equipment and other materials as requested
- Complies with all policies for the safe storage, usage and disposal of hazardous materials
- Participate in ongoing technical, safety, and operational process training programs
- Documents work performance and materials procurement as directed
- Evaluate and recommend areas of improvement within events team
- Conducts meeting room/classrooms inspections of assigned properties/facilities with special attention to flooring, lighting, décor, conferencing A/V and supplies, and other fixtures and equipment to detect deficiencies proactively. Places work orders within a Computerized Maintenance Management System (CMMS) as necessary to correct issues and improve overall event activities
- Completion of an applicable technical training program is desirable, have a minimum of one (1) year of applicable working experience in general building repair and maintenance, basic plumbing, and basic electrical
- Ability to multi-task, prioritize and complete multiple work assignments within time constraints on a regular basis
- Excellent interpersonal skills in person, by phone or by email
- Candidate must possess and maintain a valid state driver’s license
- Ability to work independently and accomplish tasks/projects with little supervision
- Exceptional customer service skills and attention to detail
- Must have ability to lift a minimum of 50 lbs
- Ability to use ladders up to 28 ft,
- Role requires occasional weekend work with advanced notice
- Mechanical and electrical aptitude
- Excellent communication skills in English, both oral and written
- Candidate must possess and provide own basic hand tools required to perform assigned work scope
- Performance of ongoing work orders on facility plumbing, lighting (bulb changes only), painting, temperature adjustments, and cleaning of equipment, rooms and other components within the building operations
- Maintain, operate, and repair all plumbing systems, building interior/exterior repair, and related grounds as it pertains to assigned buildings
- Must be willing and able to support any after-hours building related activity as required
- Attend periodic training seminars
- Interacts with external and internal customers with a positive demeanor
- Will be required to utilize e-mail, enter, query and change fields within a work order system (updating work orders)
- Required to understand and utilize Microsoft word and excel
- Evaluate vendors and suppliers on a regular basis with regard to quality and competitive pricing
- Verify the accuracy of deliveries for count, pricing, and description
- Safely operate a ladders
- Changing of light bulbs
- Able to carry 50 lbs
- Provide service for first response to hot and cold calls
- Works as a cohesive team member taking direction and training from engineering/management team
- High work order response time and closure percentages
- Client satisfaction
- Increased scope; with on-going training
- Willingness to learn and advance to an engineering role
- This position performs general maintenance on all facets of facility equipment and infrastructure
- Communicates with customers, management, colleagues, Planners/Schedulers and Operations Managers regarding issues, project completion timelines and workload priorities
- Candidate must be willing to work in a multi-skilled team environment
- This position performs general maintenance on all facets of facility equipment and infrastructure to include but not limited to the following: mechanical systems (HVAC, plumbing, controls), temperature control systems, critical environments, animal research support equipment, data center air conditioning units, fire/life safety alarm and suppression systems, elevator preventive and corrective maintenance oversight, clean steam generation, purified water systems, house vacuum systems, specialized lab equipment (incubators, autoclaves, bioreactors, ultra-low temperature freezers, refrigerators, liquid nitrogen freezers)
- Performs all work using proper safety equipment and in a safe manner
- Performs equipment calibration and repairs. Maintains tools, parts, equipment and supplies in clean and safe condition. Acts as a resource for all partners in equipment and service maintenance
- Willingness to work in a multi-skilled team environment
- Ensures all work orders are completed on and closed with all appropriate documentation within the time constraints of the request
- Ensures quality requirements for maintenance service(s) are met for equipment with a Level 1 classification. Work performed must be in compliance with all Client procedures and practices and is subject to inspection by Client maintenance or quality assurance staff
- May be required to work overtime to meet deadlines
- May be required to travel to alternate sites
- Works on-call, weekends, evenings, and holidays as needed
- A HS diploma or GED equivalent
- Minimum of five years of relevant work experience
- Operating Engineers license or equivalent
- Ability to lift 50 lbs. frequently
- Excellent English verbal and written communication skills
- Excellent computer skills, including a working knowledge of the CMMS, Word and Excel
- Proven record of excellent internal and external customer service
- Ability to work in a fast-paced, demanding environment and the ability to master new skill sets quickly
- Commitment to promote and support a collegial and supportive work environment for all staff
- Certification as a Universal Technician for CFC’s
- Experience in asceptic or GMP regulated manufacturing environment/
- Knowledge of Maximo
- Maintenance of a valid State Driver’s License and good driving record
- Safe installation and repair of equipment
- Passes on information, experience and knowledge to other maintenance
- 3 years of experience in a manufacturing environment in the automotive industry (preferably as an Electrician/Millwright) or a second year Apprentice currently enrolled in the Ontario Apprenticeship Program for 433A or 422A (at a minimum)
- Certificate of Qualification in 433A or 422A is preferred
- Must have strong electrical, mechanical and analytical aptitude
- Knowledge and experience working with hydraulics and pneumatics
- Must have experience with CNC Machines (Lathes, Mills and Grinders)
- Ability to bend frequently and lift heavy equipment as required
- Dual ticket is considered an asset
- Willingness to work as a team and get along well with others
- Must be able to work with minimum supervision and be reliable
- Must be flexible with working hours and breaks
- Willing to take responsibility for their work and respond to company needs; i.e. work overtime as required to meet deadline
- Perform Preventative maintenance on equipment and systems such as process and packaging, warehouse, electrical distribution, steam, compressed air, refrigeration, security and fire protection, treated water and waste water treatment facilities
- Utilize SAP-PM in the performance of daily tasks
- Install machinery and equipment as required
- Maintain technical literature regarding plant equipment
- Follow plant GMP procedures: maintain working areas in a clean and organized fashion
- Maintain tools, equipment and facilities are in good condition
- Perform purchase request for parts, services and supplies to carry out maintenance function
- Comply with all governmental and Coca-Cola requirements
- Other maintenance duties assigned as required
- This job is for 3rd shift, other shift may be required
- Strong knowledge and understanding of process safety, electrical safety and GMP
- Excellent skills, knowledge and experience in performing preventive maintenance
- Knowledge of maintenance, understand schematics, Auto CAD drawings and facilities purchasing
- Knowledge of electrical safety
- Knowledge of PLCs and ladder logic and controls
- Knowledge and use of Microsoft Office including MS Excel, Powerpoint and Word
- Knowledge and use of technical software applications including SAP
- Maintenance equipment troubleshooting skills
- Must be able to perform assigned work in a standing posture
- Must have manual dexterity to perform work that is repetitive
- Understand and adhere to policies, guidelines and procedures pertaining to the protection of Information Assets, integrity of customer transactions, proper and ethical utilization of access privileges and resources provided to perform the role. Fully comply with all provisions of the Company Code of Conduct, Use of Company Computer and Use of Communications Systems, and Telephone/Mobile Device Use Policy
- Diagnose Mechanical and Electrical problems using technical drawings (e.g., blueprints, Electrical/Mechanical Schematics) and diagnostic tools (e.g., multi-meter, laptop) Performs Preventative Maintenance and Repairs on equipment (Material Handling Equipment, Screen Printing Equipment, Heat Press Equipment, Forklifts, Dock Equipment, and Facility Equipment) according to safety and quality procedures
- Install, maintain, troubleshoot, or repair the following: o Facility Assets o Interior and Exterior Lighting o Dock Equipment o Plumbing and all related fixtures: urinals, toilets, sink, etc. o Light construction work: drywall, framing, paint, etc
- Adheres to all Department and Company Standards, Operating Procedures and Safety Requirements
- Three to Five years of related experience in Printing Equipment Mechanical Troubleshooting, Maintenance and /or Installation is required
- Performs preventative maintenance on equipment per assigned schedules
- Perform necessary basic repairs on equipment or structures
- Assists in the training of Maintenance Mechanics
- Requires high school diploma or equivalent
- Requires 6+ years of experience in the maintenance trades
- Trade knowledge and the ability to read, write and utilize complicated drawings/schematic reading
- Prior experience in Facilities or Property Maintenance capacity
- Familiarity of Haz Mat requirements
- Good communication skills, including completion of written reports, work requests, time logs
- Proficiency in utilizing job related computer software
- Ability to exercise independent judgment consistent with departmental guidelines
- Ability to work overtime required
- Acts as a lead to lower level staff
- Analyze, troubleshoot, install, rebuild, adjust, and replace commercial kitchen appliances, commercial refrigeration equipment andHVAC May include, but not limited to: Walk-ins, steamers, convection ovens, dishwashers, booster heaters, warmers, serving lines, ice machines, bearings, motors, heating elements, soup wells, steam wells, air conditioner compressors, exhaust systems, blast chillers and fryers
- Maintain room wiring systems and emergency exit signs; adjust timers; and test and replace smoke detectors and emergency lights. Secure electrical wires
- Prepare walls for painting, patch holes, replace dry wall, and paint. Stain and refinish wood work. Assist in roof repairs; repair or replace tiles; and perform caulking
- Maintain appliance part inventory. Fabricate cabinets, drawers, and screens and assemble furniture. Repair or replace closet doors, drawers, non-fire rated doors, door locks, closers, hinges, tiles, and bathroom fixtures
- Repair or replace various plumbing fixtures and hardware. Unclog sluggish or stopped drains
- Order, track, record, and maintain inventory parts for commercial kitchen appliances, commercial refrigeration equipment and allHVAC equipment as needed
- Perform other related duties as assigned or requested. The University reserves the right to add or change duties at any time
- Working with other Level III Maintenance Technician(s) to perform preventive, corrective, and predictive maintenance on high tech automated equipment
- Able to troubleshoot and diagnose problems with mechanical, electrical, and electronic systems, such as Programmable Logic Controllers (PLCs), System Control Software (SCS), scanners, etc
- Must demonstrate reasonable mastery of all production facilities systems, including conveyors, robotic equipment, and industrial trucks as applicable (ASRS, AKL, and Auto Guided Vehicles (AGVs) in new-generation production facilities)
- Knowledge of all phases of cutting and welding
- Experience with Microsoft Word and Excel and basic math skills
- Interpret, explain and enforce department policies and procedures
- Ability to read blueprints, spreadsheets, voltage meters and tape measure
- Establish and maintain effective working relationships with those contacted in the course of work
- Maintain mental capacity which allows for effective interaction and communication with others
- Maintain physical condition appropriate to the performance of assigned duties and responsibilities
- Maintain effective audio-visual discrimination and perception to the degree necessary for the successful performance of assigned duties
- Operational services and activities of a general maintenance program
- Computer skills: Microsoft Office tools and internet. Ability to use a computer, or smart phone to assist with work orders, BCS, and other duties required by supervisor
- Two (2) year general building operations
- Six months or more of related experience preferred
- Ability to read and interpret instructions, procedures, manuals, and other documents
- Ability to report and record maintenance requests
- Knowledge of cleaning methods and equipment
- Basic understanding of the upkeep and care of equipment
- Understanding of cleaning compounds and chemicals, and their safe, efficient use
- Must possess a valid Washington State Driver’s License
- Must pass a Washington State Patrol background check
- May implement, manage and oversee personnel and payroll administration
- Preform various maintenance duties that require a basic understanding and ability to work with power tools, plumbing, electrical, and general “do it yourself” (DIY) projects
- Serves as a member of the janitorial staff as needed; to include covering sick-days, vacation, personal days, etc
- May require on-call and/or weekend availability in an emergency or as dictated by projects and tasks to be completed
- Electrical repairs, install and maintenance
- General labouring as required
- Stock control
- Compliance of RCD and Emergency Light testing
- Carry out the implementation of the preventive maintenance program, including Electrical and Mechanical troubleshooting
- Electro-mechanical repairs to all milling and packaging equipment, including pneumatic systems
- Technical support for the site
- Closely monitor line and machine performance and intervene on line as soon as any deterioration in KPI occurs
- Work with equipment suppliers on new equipment installations and modifications
- Work with equipment suppliers on remote access using the web
- To be observant & work off your own initiative when a fault is detected and to take action based on your best judgment on whether to effect immediate repair or not
- Provide mentoring and coaching to operatives
- Co-operate and participate fully in training and development in cross-skilling and other job-related competencies
- Troubleshooting of PLC Programs and computer network with the support of the IT department
- Using all resources such as manuals, service contacts etc to aid in breakdown recovery
- Ensure all parts are ordered with the support of management
- All relevant information is passed to both management and operatives
- Work with project team on implementing new projects
- Be innovative with new ideas and initiatives for site improvements
- Maintain workshops to a high standard
- Ensure all electrical drawings and wiring is up to date with current practices
- Improve environmental awareness and optimise resource utilisation
- Further responsibilities may be added from time to time as the strategy evolve
- Time served electrician with City & Guilds qualification or equivalent
- 3-5+ years experience in a maintenance role
- Experience in programmable logic computer systems and programming skills essential
- Knowledge of/qualification in mechanical and pneumatic engineering systems
- Computer skills a must Excel, Word
- Knowledge of /Qualification in instrumentation such as noise, vibration and heat measurement an advantage
- Aptitude for manufacturing process, proven skills in diagnostic trouble shooting on busy production machinery ,gained in a FMCG environment. Examples included electrical or mechanical process or equipment such as milling equipment, electrical fault. Attention to detail and good problem solving skills essential
- Experience with grain milling and packaging equipment an advantage
- Multi-skilled / cross-skilled ethos
- A team player capable of using initiative and taking on new projects/challenges
- An understanding of food standards
- Ability to cover call-outs and breakdowns at evenings and weekends
- Is responsible for daily property inspections, prioritizing work orders, handling urgent requests, responding to client’s work order request for maintenance and facility/equipment repairs
- Performs and assigns resources to handle general repairs and services in all maintenance related disciplines, including but not limited to: carpentry, plumbing, piping, HVAC, low voltage electrical, finish work, painting, custodial, etc
- Coordinates with other technicians in the repair and service of building and central plant equipment
- Assists the completion of any and all assigned preventative maintenance work and procedures
- Supports the various trade personnel at the facility or complex in the performance and completion of their duties as needed and assigned
- Promptly responds and assign appropriate resources to handle non-technical tenant requests (e.g., hanging pictures, desk repairs, ceiling repairs, etc.)
- Ensures the cleanliness of the premises via inspection and light supervision and responds to restroom and janitorial service requests
- Performs facility mail, shipping and receiving duties as detailed on mail operations scope of work when required
- At least 1 to 3 years of mechanical experience preferably in a commercial or industrial facility with an emphasis in facility maintenance plus experience with electrical, plumbing, piping, HVAC, building equipment and building repairs
- Prior supervisory experience and computer knowledge is necessary. State Driver’s license required
- Must be physically capable of performing the duties of the position including bending, squatting, stretching and lifting up to 25 pounds on a regular basis. On occasion, may be required to lift items weighing 50 pounds
- Proficient with Microsoft Office, Excel and Word
- Ability to speak effectively before groups of customers, tenants, client representatives or employees of C&W
- Ability to positively deal with problems, resolve issues, address client and tenant needs as they relate to the maintenance of the facility, and handle multiple assignments and projects at the same time
- Inspect Boiler Chiller Room
- Verify Chemical Levels and that Chemical Pumps are stopped when Chillers are not running
- Perform Maintenance on Mechanical Systems
- Check and inspect Cooling Tower for debris and proper operation
- Replace bearings and seals on pumps and motors
- Oversee Building Facility Operation
- Verify Janitorial Service has been completed
- Verify Lawn Work has been completed
- General Maintenance Items
- Basic plumbing tasks – replace worn/failing bathroom fixtures, valves, seals, wax rings, etc
- Door maintenance tasks – adjust door closers, replace door strikes, make duplicate keys, replace hinges, etc
- 2 years Technical School and or Associates Degree or at least 2 years’ experience in the Facility Maintenance Industry
- Minimum 2 Years’ experience working with Building Mechanical Systems including Chillers, Boilers, HVAC Systems, UPS Systems and Facility Control Systems. Also experience in general upkeep and Maintenance of a Broadcast Facility
- Day to day coverage of equipment: respond to breakdowns, and Production requests quickly and efficiently to minimize downtime
- Diagnoses equipment failures, finds root cause and communicates actions taken to the rest of the team
- Perform major equipment repairs and rebuilds, (some weekends and holidays required)
- Uses manufacturing systems effectively (MES, Spares Inventory, Issue Tracking)
- Work with Maintenance Manager to resolve maintenance issues, improve equipment reliability, review procedures, and minimize equipment downtime
- Organizes and maintains a high degree of cleanliness in the maintenance area as well as performing spares inventory audits to ensure accuracy
- Participate in small improvement projects to assist in improving the facility
- Day to day coverage of production line equipment: respond to alarms, breakdowns, and Production requests quickly and efficiently to minimize downtime
- Takes initiative to improve PM documents and schedules, under the direction of the Equipment Engineers
- Participates in TPM team while taking on small improvement projects to assist in improving the factory
- Follows all aspects of Maintenance Safety protocol (LOTO, 5S, ESD protection, etc.), to ensure that the maintenance team operates safely at all times, always leading by example
- Maintain customer satisfaction when interacting with Production teams and other supporting group
- Strong sense of ownership and pride of the work performed
- Ability to sustain Tesla fast-paced growth
- Follows all aspects of Maintenance Safety protocol (LOTO, 5S, Arc Flash, etc.), to ensure that the maintenance team operates safely at all times, always leading by example
- AS/BS Degree on Industrial/Mechanical/Electrical Technology is preferred. 3+ years of experience maintaining industrial equipment and automation or technical military experience in lieu of Degree
- Areas of specialization may include one or more of the following: electrical/electronics, mechanical/machining or automation/PLC/robotics
- Experience creating & maintaining a positive atmosphere in a collaborative work team
- Ability to manage workload while contributing to a positive, team oriented work environment
- Skilled at troubleshooting automation, conveyance and electromechanical systems
- Skilled with the use of a variety of hand and portable tools, as well as general machining and welding
- Skilled with common workplace software (MS Word, Excel, PowerPoint, email etc)
- Able to read and interpret basic mechanical drawings and electrical schematics
- Willing to perform shift and overtime as required
- Customer driven to respond to request in a timely and supportive manner, going the extra mile to ensure the success of the OEM programs
- Ability to suggest and implement workable solutions for electrical, electro-mechanical, mechanical, hydraulic, pneumatic and electronic component and system problems
- Understanding and safe operation of gas delivery systems; safe troubleshooting at the installation level
- Working knowledge of building utilities, processes and components including DI water, process exhaust, vacuum, power and CDA
- Controller/systems programming; ability to manipulate software (where possible) for problem solving
- Fabrication, assembly and installation of tooling and fixturing from drawings
- Proficient at blueprint, electrical, circuit board drawings and schematics. Ability to conceptually develop ideas with standard language and symbols
- Basic/advanced shop skills including welding
- Project work in new installations, retrofit and upgrades. Ability to work closely and effectively with all company disciplines and vendors
- High vacuum system maintenance
- TECHNICAL SKILLS/JOB AND BUSINESS KNOWLEDGE: Keeps skills and knowledge up-to-date. Applies skills and technical knowledge to maintain a high level of accomplishment. Utilizes business systems and, when necessary, understands the business objectives and company operations as they relate to each other. Demonstrates the competency to work with an appropriate level of direction. Makes continuous efforts to learn and understand processes and procedures
- DELIVERS QUALITY RESULTS: Displays a commitment to achieve excellent results. Produces required job results with consistently high quality. Monitors own work to ensure quality; work is generally error free. Accepts responsibility for the results of his/her actions. Identifies problems and presents solutions. Consistently follows through on open projects and new initiatives, ensuring delivery dates are met and communicates progress/status to management in a timely manner
- TEAMWORK / TEAM PLAYER: Collaborates willingly as a team player with peers, customers and suppliers. Values and recognizes contributions made by others. Shares information freely and informs superiors and co-workers in a timely basis. Identifies and implements new ways to improve communication and cooperation between business units and other divisions. Treats all people with respect and dignity and fosters cooperation in a group effort
- COMMUNICATION: Prepares written documents that are concise, grammatically correct and appropriate for the intended audience. Communicates verbally in a clear, organized and articulate manner. Listens effectively and respects the views of others. Presents self professionally and can adapt to a variety of settings. Makes effective presentations. Appreciates the importance of interpersonal and group communications; consistently delivers crisp and intentional messages
- WORK HABITS / TIMELINESS / RELIABILITY: Establishes priorities and organizes work resources to complete objectives by established deadlines. Utilizes appropriate sources of information in making decisions or taking action. Utilizes effective time management skills. Reliably meets challenging goals and assignments, even during demanding or changing work periods. Self-motivates and produces required job results of consistent quality and levels of productivity
- CREATIVITY / INNOVATION / IDEAS: Identifies and develops new opportunities. Drives innovation at every level. Consistently suggests new ideas and new approaches and solutions to improve business. Explores new ways to improve and streamline processes and productivity. Energizes others to achieve exceptional results; gains commitment to new ideas and actions. Listens to and values the ideas of others as an important part of the creative process
- HONESTY / INTEGRITY / TRUST: Maintains confidences; knows when information is inappropriate to share. Acts consistently and ethically in doing their work. Consistently honors commitments. Trusted up, down and across the organization; balances the needs of others with personal goals; fosters a safe environment for sharing opinions. Maintains positive and respectful relationships with co-workers and communicates with all levels in the organization effectively and honestly
- FLEXIBLE / ADAPTABLE / RESOURCEFUL: Quickly grasps, interprets and effectively adjusts to new situations, methods and procedures. Exhibits flexibility in work habits and in addressing and improving processes. Responds positively to change and ambiguity. Can find effective solutions to goals that change regularly
- Maintain a positive and supportive relationship with the facility manager, site leader and key client contacts to insure customer needs are understood and met. Work closely with the facility manager and customers to ensure service delivery meets or exceeds expectations
- Support the Regional Facilities Manager in the implementation of short and long-term projects that apply to the MT position
- Performs all facility equipment repairs within the scope of experience the MT has
- Acts as a resource for all partners in equipment and service maintenance
- Recommends capital improvements to the Facility Manager
- Checks with the Facility Manager to ensure all on site work has an approved client Purchase Order in place before any work begins
- Follows the annual IPMP performance plan; accomplish Key Performance Indicators as agreed with client in the Objectives of the Performance Agreement for the position
- Ensure compliance with JLL minimum EHS standards
- Share innovations and best practices with the assigned owner of best practices for JLL Facilities Management
- Coordinates with contractors when on site ensuring each contractor is following all client and JLL polices and ensuring the delivery of the service is completed correctly
- Effectively participates in the JLL – 360 Facility & One View Service Center service ticket program by completing all assigned tickets from customers and the preventative maintenance program within the Service Level Agreement parameters
- When required assists with SMS (Service Management Suite) tickets with in the set time frame required for approvals. Understands that no work is to progress unless an approved SMS ticket is in place
- Must have good communication skills, both verbal and written
- Experience in the trades of electrical, plumbing, carpentry and building systems
- Good general computer skills with knowledge in email, Internet, Microsoft Word and Excel
- Must have a valid driver license
- 2 years field experience and trade school training OR 5 years total field experience
- Provide all necessary troubleshooting and maintenance (preventative and otherwise) including, but not limited to, the following Vera Bradley equipment: automated conveyor system, carton erector, tape machines, flexible conveyors, trim slitting machine, monogramming machine, sewing machines, tying machines, material slicer, Lectra cutting machines, turn buckle machine, fabric winder, auto spreader, and other cutting
- High School Graduate. Post high school technical education preferred
- 2+ years general facility and machine maintenance experience
- Experience troubleshooting and repairing industrial conveyor equipment
- Electrical experience preferred
- Machine operating experience in a manufacturing/light industrial environment preferred
- Mechanical aptitude to repair industrial conveyor equipment and general facilities maintenance
- Ability to work independently with little supervision
- Detail oriented with the ability to manage multiple tasks simultaneously
- Strong interpersonal, and communication skills
- Flexible, adaptable with the ability to work under pressure to meet deadlines in a fast paced environment
- Distribution environment – constant standing, walking and reaching; frequent stepping, bending and stooping
- Motivation and physical stamina required maintaining a quick work pace
- Ability to occasionally lift up to 70 lbs
- Ability to operate various mechanical machines
- Must have the basic proficiency of reading and writing of the English language
- Minimum 2 years full-time maintenance experience
- Must have mechanical experience
- Must have electrical experience
- Experience working on conveyors is a plus
- Willingness to perform all required tasks
- Demonstrated knowledge of work safety habits
- Ability to professionally represent the company
- Maintain a valid drivers’ license and reliable transportation
- Able to work on-call and extended hours (including after hours and weekends)
- Maintains good facility relations through prompt and courteous response to facility requests within the guidelines set forth by JLL and Client
- Performs general maintenance within the building including carpentry, painting and plumbing
- Insure that work performed in facility space is accomplished with a minimum of disruption and is followed by adequate clean-up
- Review monthly facility service request summaries to pinpoint and correct recurrent operational problems
- Communicate with the facility services coordinator to establish facility service request work priorities
- Ensure the availability of an adequate operating inventory of tools and supplies
- Monitor the quality and pricing of maintenance work performed by outside contractors
- Assist engineers in other work as assigned
- Learn all of the central plant machinery and equipment, as well as, all of the building operation functions (HVAC, plumbing and electrical)
- Comply with all written JLL and regional company policies
- Subject to on-call 24 hours per day
- Required to work in all weather conditions
- Perform general handyman tasks in maintaining buildings
- Hanging of art work, coat hooks and white boards as requested by facility
- Set-up desk hardware as per facility’s requests
- Set-ups and breakdowns of various cafeteria and/or conference rooms tables and chairs, for meetings, parties, and other functions, as requested by different departments
- Pick up and move engineering deliveries to final destination
- Support Audio/Video Services as needed
- Furniture relocation and repair throughout facility
- Deliver moving boxes; breakdown and set-up of said boxes
- Work closely with contractors. Assist in providing access to machinery rooms, electric closets and other restricted areas, as assigned by the Assistant Chief Engineer or other supervisor
- Perform basic electrical and plumbing repairs
- Associates degree or equivalent in a related field from an accredited two-year college or technical / trade school
- Minimum of two to four years in a general facilities environment or an equivalent combination of education and experience
- Good verbal and written communications skills are required
- Computer proficiency in e-mail and Microsoft Office Suite (Word, Excel, PowerPoint, Access, Project and Outlook) and Microsoft Windows
- Direct the performance of general maintenance work as needed
- Oversee the efficient operation of all building systems and to inform the Lead Engineer and Operations Supervisor(s) of any condition affecting building services and facility comfort or safety
- Conduct routine planned maintenance of the production equipment (filling lines, tanks, vial washers) as detailed by the Computerised Maintenance Management System (CMMS)
- Support production activities at all times by ensuring minimum response times to equipment breakdowns and achievement of equipment availability targets
- Ensure compliance to all aspects of the Company’s Health, Safety and Environmental procedures is maintained
- Ensure that all activities are carried out in accordance with the Good Manufacturing Practices requirements maintained by the company
- Work closely and interact with the other groups within the Engineering and Operations departments
- Proven years of experience in machine maintenance in a manufacturing environment
- Strong electrical and electronic repair and diagnostic skills
- General skills and expertise related to maintenance and facilities activities
- Demonstrate levels of theoretical knowledge with practical application
- Experience in pneumatic and hydraulic fault finding and repair
- Building/Maintenance certifications is a definite plus
- Three or more years of experience in maintenance/ housekeeping
- HVAC experience is required
- Strong supervisory and leadership skills must have been obtained and demonstrated through past job experiences
- Broad overview of the YMCA as it operates as a local, national, and international movement
- Provides routine maintenance
- Performs minor electrical repairs
- Able to perform carpentry and finish repair work
- Performs plumbing repairs
- Performs minor pool equipment maintenance and repair
- Performs routine inspections and maintenance checks of facilities as a means of preventive maintenance
- Notifies Property Director of any items needing immediate attention
- Completes equipment repair records and forms
- HVAC repairs
- Personal Development Oriented: Accurately assesses personal feelings, strengths and limitations; and how they impact relationships. Pursues self-development that enhances job performance. Demonstrates an openness to change, and seeks opportunities in the change process
- HVAC Certifications
- General interior maintenance: hang pictures, install keyboard trays, and repair office furniture systems
- Completes special tasks that include but are not limited to: painting, locksmith work, tenant services requests, and general maintenance as assigned
- Basic HVAC knowledge: maintain, troubleshoot, and repair to HVAC units in corporate settings and IT server rooms
- Maintain compliance of State, County, or City Ordinances, Codes, or Laws
- High School diploma or G.E.D. equivalent is required
- Completion of an applicable technical training program is desirable
- Have a minimum of one (1) year of applicable working experience in general building repair and maintenance, basic plumbing, and basic electrical
- Excellent interpersonal skills in person, by phone or by e-mail
- Ability to use ladders up to 28 ft
- Proficiency in computer use and knowledge of software such as Microsoft Office Suite (Word, Excel, PowerPoint, Access, Project and Outlook)and Microsoft Windows
- A high school diploma or GED is required
- A minimum two (2) years’ experience in the building maintenance industry and accredited trade school degree in HVAC, electronic, or other industry related trade
- Union training and certification is also acceptable
- Must have Universal CFC certification
- Should be knowledgeable in the safe and proper use of the following tools: ladders, lifts, basic hand tools, volt meter, manual drain auger, plumbers helper, safety goggles, ear protection, and fire extinguisher
- Have the ability to write routine reports and correspondence
- Ability to calculate figures and amounts such as load balancing, proportions, percentages, area, circumference, and volume
- Have the ability to apply concepts of basic algebra and geometry
- Have the ability to interpret a variety of instructions furnished in written, oral, diagram, or schedule format
- Performs all maintenance activities in a safe and efficient manner
- Trains production technicians in the proper set-up and copy troubleshooting techniques
- Performs activities to comprehend industrial computer controls and related I/O’s
- Replace and repair parts, rebuild equipment, and align; gears, shafts, pulleys and belts
- Utilizes illustrated parts breakdown manuals and operational manuals in the repair, modification and maintenance of equipment
- Performs inventory control of parts and equipment used from inventory
- Performs housekeeping duties required of maintenance staff, including work area clean-up, machine and equipment clean-up, sweeping production floor after clean-up, and various other general housekeeping duties as assigned
- Responds in a timely manner to all ANDON red lights on the production floor
- Performs activities to acquire detailed knowledge of equipment components, to diagnose causes of electrical or mechanical malfunctions or provide corrective maintenance
- Provides training and assistance to production technicians as needed, to help maximize production output and minimize downtime through the utilization of proper production techniques and handling practices
- Inspects machinery for potential problems on a daily basis. Documents problems and schedules work as appropriate
- Provides training and coaching to new maintenance technicians and inspects their work. Ensure proper operation of machines (Muller’s, Cheshire’s, Ink Jet Printers and Alpha liner)
- Ensure proper operation of machines (Mullers, Cheshire’s, Ink Jet Printers)
- Perform all maintenance activities in a safe and efficient manner
- Train production technicians in proper set-up and copy troubleshooting techniques
- Understanding of Industrial computer controls and related I/O’s
- Change and repair parts, rebuild equipment, and align; gears, shafts, pulleys and belts
- Use illustrated parts breakdown manuals and operational manuals in the repair, modification and maintenance of equipment
- Inform Supervisor of parts and equipment used from inventory
- Perform housekeeping duties required of maintenance staff, including work area clean-up, machine and equipment clean-up, sweeping production floor after clean-up and various other general housekeeping duties as assigned
- Respond in a timely manner to all red lights on the production floor
- Gain detailed knowledge of equipment components to diagnose causes of electrical or mechanical malfunctions or provides corrective maintenance
- Provide training and assistance to production technicians as needed to help maximize production output and minimize downtime through the utilization of proper production techniques and handling practices
- Inspect machinery for potential problems daily
- Documents problems and schedules work
- Provide training and coaching to new maintenance technicians and inspect their work
- Bilingual skills are preferred (English/Spanish) not required
- Production environment experience along with leadership experience is a requirement. Knowledge of LOTO (Lock Out Tag Out), PM’s (Preventative Maintenance), basic PLC (Programmable Logic Controller) and 3-Phase electrical work
- Prior electro-mechanical experience
- Be able to lift 40 pounds on a routine basis
- Ability to read and understand schematics and electrical blue prints
- Ability to learn and follow all safety regulations and job instructions to perform primary duties
- Mechanical and or electrical experience
- Technical degree and/or equivalent experience
- Extensive knowledge of OSHA requirements
- Ability to work in a team environment, striving to meet and exceed regional production, quality and safety goals
- Must demonstrate good time management skills
- Plans and organizes daily work flow
- Cost effective control of parts inventory in accordance with corporate operations policies and procedures
- Responsible for the planning and execution of a quality preventive maintenance program to maximize equipment life and operational efficiencies according to Valassis and manufacturer specifications
- Responsible for insuring that all equipment has the proper safety devices/protection is safe to operate and proper housekeeping practices are implemented
- Develops and leads a highly trained and motivated maintenance team to support all operations
- Assist the maintenance manager in controlling costs, fixed and variable
- Responsible for the coordination of schedules, plans, and training with department managers
- Accountable for the repair parts and equipment inventory and budget
- Responsible for maintaining the facility in compliance with local, state, and federal codes and Valassis policies
- Responsible for supporting safety initiatives and safe working conditions; (e.g. Hazcom, Hazardous energy standard, machine guarding, etc.)
- Develops and tests equipment improvements to continuously improve operational efficiencies and cost effectiveness of production
- Inspect machinery for potential problems daily. Documents problems and schedule work
- Responsible for preparing maintenance work order schedule for the shift and respond in a timely manner to all red lights on the production floor
- Responsible for performing B-level mechanic duties in accordance with preventive maintenance plan
- Performs any other tasks as assigned by management to achieve overall objectives of the organization
- Responsible for overseeing and performing A-level mechanic duties
- Coordinate with vendors and manage facility maintenance requirements
- 3-5 years in production maintenance leading mechanics
- Electrical, mechanical and HVAC Certification highly recommended
- Associate Degree in Facilities Management, technical certification or equivalent experience
- Ability to manage programs and systems which support the business
- Must demonstrate good time management skills. Plans and organizes daily work flow
- Must have experience with continuous improvement projects and requires making decisions on your own and explaining the decision and its advantages
- Participate in all safety and regulatory training needed to fulfill the duties of the position
- Follow all plant safety rules and regulations, wear PPE as required per procedures
- Performs all the duties of a Maintenance Mechanic in keeping equipment operational and processes going
- Troubleshoots difficult equipment issues using blueprints, equipment manuals and internet resources
- Directs the daily assignments of the Maintenance Mechanics
- Identifies training requirements of the Maintenance Mechanics. Trains as required or seeks proper training resources
- Assures that labor time is entered in maintenance work orders
- Perform other duties as assigned by the supervisor or designate
- As a skilled specialist, completes tasks in a creative and effective ways
- Receives directives from management and decides how to best carry out tasks and complete projects
- Substantial understanding of the job, and applies knowledge and skills to complete a wide range of tasks
- Receives little instruction on daily work, general instructions on newly introduced assignments
- Minimum five (5) years of maintenance experience including pneumatics, PLC, machinery, welding and electrical
- Minimum ten (10) years of experience in maintenance tasks including pneumatics, PLC, machinery, welding, and electrical
- Possess a two year technical degree in electronics AND minimum of five (5) years of maintenance experience including pneumatics, PLC, machinery, welding and electrical
- Good communication skills, both written and verbal in the English language
- Excellent math skills and complex blueprint reading, drawings, notes, and computer skills
- Highly skilled in pneumatics, PLC, machinery, welding, and electrical
- Maintain a safe work environment, maintain good personal safety record, report unsafe conditions or equipment
- Perform basic mechanical, electrical, building, grounds and preventative maintenance across the plant while maintaining a safe work environment
- Perform and/or assist in equipment installation, calibration and relocation
- Perform duties as required in the wood working area
- Minimum three (3) years in a manufacturing environment
- Minimum one (1) year of maintenance experience
- Possess a current and valid driver’s license
- Minimum five (5) years of maintenance experience
- Previous experience operating manual machines (lathe, mill, grinder)
- Possess an Electrical certification
- Functional and technical skills
- Basic computer skills; including experience in Excel, Word, and SAP
- Previous HVAC experience
- Knowledge and understanding of controls and instrumentation
- Attention to detail and have sound judgment
- Strong conceptual skills
- Ability to effectively plan daily activities
- Team oriented and possess interpersonal skills
- Perform required Maintenance and repairs on process equipment
- Perform required Maintenance and repairs on the facility and all related equipment
- Required to maintain work order documentation as well as data entry into the MP2 Maintenance Program
- Minimum three (3) years of industrial maintenance experience
- Proficiency in the application and programming of PLC controllers
- Organizational skills and PC literacy
- Capable of quickly coming up to speed and becoming fully competent in the diagnosis, troubleshooting, and repair of equipment such as, but not limited to, Conveyors, Dot matrix printers, pumps, mixers, dispensing units for fluids, air-vey units, presses, small ovens, hydraulic systems, Pneumatic systems, Electrical control systems and Extruder systems
- Ability to perform needed metal fabrication, repair, and welding for support of manufacturing as required
- Familiar with Power supply up to 480 v, electrical panels, circuitry, breakers, fuses, conduit, AC and DC drives, safety interlocks, relays, motor controls, motor starters and assorted electronic sensors
- Experience operating PIV and scissor lift
- Ability to work effectively with minimal supervision
- Perform the essential functions of the job within acceptable MSHA and safety/ environmental regulations, quality, productivity and performance standards as outlined in plant policies, procedures and applicable work instructions
- Maintain Pumps
- Possess a two (2) year technical degree OR minimum five (5) years of experience in heavy industry with emphasis on installation, troubleshooting and repair of machinery, pneumatic and hydraulic systems
- Possess a Welding Certification
- Perform full range of plant maintenance tasks and repairs on a proactive/planned and reactive basis
- Use predictive maintenance techniques such as thermo-graphic imaging and vibration analysis as well as experience, skill and judgement to make regular assessments of the plant condition
- Introduce a maintenance Management System to log faults and report potential problem areas, extract fault information, generate work orders and log completed work
- Implement equipment reliability improvements and develop new maintenance work-flow methods and techniques
- Process optimisation to ensure maximum efficiency
- Employ predictive maintenance techniques to achieve benchmark plant reliability
- Introduce safe system of work, PPE permits, risk assessment etc
- The role requires the skills of an experience maintenance person with a bias to mechanical engineering
- Diagnostic trouble shooting and problem analysis are essential skills
- Good knowledge of Maintenance process and activities gained within a plant environment
- Understanding of predictive maintenance techniques, vibration analysis, thermography and ultrasound
- Thorough understanding of EHS and a safety culture
- Demonstrated ability to build and maintain effective working relationships internally and externally
- Relevant qualification in mechanical engineering
- Perform scheduled inspections and develop follow-up work orders as needed
- Perform necessary repairs to equipment
- Maintain maintenance records and make necessary changes to schedule in conjunction with the Plant Manager
- On-site coordinator for contracted maintenance tasks
- Assist with future Maintenance & Reliability program execution at other locations within the Region
- Minimum 3 years of experience in the following areas
- Hydraulics & Pneumatics
- Plumbing & pipe fitting (including high pressure steam, ammonia, refrigeration)
- Mechanical assemblies (gearboxes, drives etc)
- Layout and fabrication – includes heli-arc, stick, and gas welding ability
- Preventive maintenance and repair of robot
- Basic electrical knowledge (3 phase, breakers, scematic reading, etc.)
- Coordinates prototype builds in the Pilot Factory while keeping an eye on design for manufacturability issues
- Ability to troubleshoot equipment and process issues
- Responsible for full support equipment on Pilot Factory Floor. Hardware and Software
- Handle setups and changeover of equipment for prototype product builds
- Define and Perform scheduled equipment maintenance and maintain equipment history and documentation using PM software system and logs
- Works closely with process engineering to develop Process Specifications for new processes, ensure that new products are designed for assembly and to initiates design changes for cost effectiveness
- Works with other engineering disciplines and manufacturing to identify cost reduction opportunities
- Supports new products launch activities in other Harman manufacturing locations as required
- Able to run simple designs of experiments to optimize processes or troubleshoot process variation
- Create and manage Visual Aid instructions
- Train pilot factory personal on equipment operation and setup
- Experience and programming knowledge of SMT and Electronics assembly equipment such as: MPM Screen Printer, Koh Young SPI, Fuji Pick and Place, Heller Reflow, Matrix X-ray, Soltec Select and Wave Solder, PVA Conformal Coat, Router
- Thorough knowledge of electronics assembly processes and Mechanical assembly processes
- Knowledge in Machine capability analysis
- Knowledge of personal computers and networks
- Familiar with Windows O.S
- Degree and/or Training
- Education Desired
- Will consider High School Diploma with proper experience
- Experience: 5+ years minimum related experience
- Certifications/ Licenses
- While performing the duties of this job, the employee is regularly required to sit; use hands to finger, handle, or feel; and talk or hear
- The employee frequently is required to reach with hands and arms
- The employee is occasionally required to stand and walk
- The employee must be able to lift up to 50 lbs
- Little to some exposure to hazards
- Knowledge of current manufacturing practices and procedures
- Knowledge of assembly processes
- Ability to conceptualize sequential mechanical motions
- Knowledge of troubleshooting equipment
- Experience with automated assembly lines
- Ability to work within time and budget constraints
- Ability to maintain positive attitude and remain focused on objective
- Must work well as part of a team and accept position responsibility
- Technical diploma or equivalent - advantage
- Basic PLC principles knowledge - advantage
- PC operative systems know how
- Experience and knowledge in pneumatic and sensor principles
- Mechanical machining know how ( ability to work with lathes or grindings to prepare spare mechanical components if needed)
- Basic English language knowledge - advantage
- Operate existing and new equipment, machinery and processes necessary to complete the maintenance and repair, both standard and preventative, on all facilities, buildings, equipment and machinery, to include but not limited to, pneumatic, hydraulic, electrical, and mechanical systems. Work on motor controls and building electrical systems up to 600 Volts (AC)
- Perform general maintenance of facilities, machinery and equipment
- Read and follow instructions, drawings, schematics, sketches, blueprints, specifications and instruction manuals. Works under general supervision
- Accurate reporting of shop floor data related to maintenance and quality, both manually and electronically. Communication of in process items with team members on other shifts. Report safety issues as they arise to the production supervisor
- Maintain a clean and safe work environment. Each technician is responsible for housekeeping within his or her assigned workstations, including the removal of waste and scrap on a daily basis
- Perform other related duties as assigned by management
- Responsible to report safety issues and work related accidents as they arise to the Supervisor
- Objectives and measures of the EH&S system are to be understood as follows: prevent pollution, injuries and hazards, to continual improve, and to follow legal requirements
- Perform normal daily maintenance that may require and include cleaning, greasing, lubricating
- Employees with specialized training or certifications may be required to perform specific aspects of production as assigned by the Supervisor
- Must receive a score of 70% or better on the Maintenance Skills Exam
- High school diploma (or GED equivalent)
- 2 years or more of industrial maintenance experience
- 1 year of PLC and National Electrical Code experience in a manufacturing environment
- Technical degree is preferred
- Fork lift experience is strongly preferred
- Ability to read, write and understand basic math
- Ability to understand basic computer skills
- Ability to follow written and verbal instruction
- Ability to interpret production documents that may include blueprints, schematics, sketches, specifications and instruction manuals
- Approaches all tasks and duties with the mindset that ensures safety is built in to every process so that ergonomic, environmental, and overall hazard reduction is achieved for themselves and their team members
- Examines machines and mechanical equipment to diagnose source of trouble
- Hydraulic; Sets-up and operates standard machine to make parts, tools in the machine shop
- Conducts scheduled preventative maintenance procedures
- 3 or more years of industrial maintenance experience
- Basic PLCs (Programmable Logic Controller) lay out and trouble shoot
- Dismantles machines and performs repairs
- Basic machine shop knowledge (using Lathes, End mills, Drill press machines)
- Performs maintenance of powered industrial trucks including mechanical, hydraulic and electrical systems
- Two year Associates Degree in Industrial Maintenance field perferred
- Knowledge of welding and pipe fitting techniques preferred
- Knowledge of gas control systems preferred
- Prior experience performing maintenance in an idustrial or similar environment
- AS Degree in Industrial Automation or Engineering preferred
- 5-Years minimum industrial maintenance, automation and control experience
- Demonstrated ability to read machinery documentation, blueprints and schematics
- Electrical and electronic troubleshooting skills including PLCs and VFDs
- Advanced Personal Computer (PC) skills
- Minimum 5 –Years Industrial maintenance, automation and control experience
- General Mechanical Aptitude required. Must have an understanding of maintenance shop tools and use of them
- Welding, drilling, tapping and other fabricating abilities required
- Must be able to read, comprehend and perform as directed
- Capable of lifting 100 lbs
- Must be able to climb and work at heights up to 120 ft
- Required to work in extreme climate conditions, Hot, Cold, Rain, Snow, Etc
- Two year maintenance industrial degree plus three years industrial experience; or five years documented experience in industrial maintenance including, electronic and electrical experience in a manufacturing facility
- Ability to read and interpret documents such as procedure manuals, safety rules and operating instructions
- Ability to work with mathematical concepts and apply these to practical situations
- Ability to troubleshoot equipment problems, logically and systematically analyze machine problems and correct
- Stand, walk, stoop, kneel, crouch, or crawl, use hands to finger, handle or feel objects, tools, or controls
- The employee must regularly lift and/or move up to 75 pounds
- Must be able to climb and work at heights up to 75 ft
- Work near moving mechanical parts
- Is regularly exposed to fumes or airborne particles and vibration
- Work in a normally loud / noisy environment
- Must be able to wear a respirator
- Hydraulic and pneumatic control and powered systems
- Machining, mill and lathe
- Thermal processing instruments and controls
- Food Manufacturing experience and knowledge of food safety
- Electrical/Electronics-install and repair (some explosion proof environments)
- Single and 3-phase powered equipment (troubleshoot, test, and repair)
- AC and DC control systems (troubleshoot, test, and repair)
- Fiber optic devices and cabling (repair, replace, set-up)
- Operate electronic test equipment (multi-meter, meg-ohm meter, amp probe, Hart Communicator, oscilloscope, power analyzer)
- 5+ years of experience maintaining mechanical systems on complex process and/or high-speed production equipment
- Demonstrated experience troubleshooting, testing, and repairing instrumentation devices
- Pressurized fluid systems
- Raw product material handling
- Mixers and vessels
- Flexible filling and sealing equipment
- Apply predictive maintenance technologies and condition based monitoring to equipment(oil analysis, vibration analysis, motor circuit analysis)
- Perform Root Cause Failure Analysis on major unplanned breakdowns and recurring problems
- Maintain equipment and assembly drawings and schematics, document maintenance activities, and maintain historic records
- Design, implementation and completion of reliability and cost reduction projects on equipment
- Provide equipment specific training to shift maintenance and operations associates to assure compliance with assembly, operating and safety procedures
- Rebuild and restock spare parts assemblies for equipment or systems
- Robotics operation, repair, and programmin
- Mechanical Maintenance
- Proper use of hand and power tools Food Manufacturing experience and knowledge of food safety
- Electrical/Electronics-install and repair (some explosion proof environments
- 5+ years experience maintaining mechanical systems on complex process and/or high-speed production equipment
- Safety Compliance
- Implement Continuous Improvements
- Equipment Maintenance and Sanitation
- Steady State/Changeover/Transition
- Recognized Expert for Maintenance
- Demonstrated ability to troubleshoot and problem solve
- Have a high school diploma, GED or equivalent education
- Two (2) plus years of work experience in maintenance/reliability
- Ability to travel 5% of the time
- Demonstrated competency in computer and pc software including Microsoft Office and email
- Successful completion of a substance screening and background check
- Three (3) plus years of experience in maintenance/reliability
- Associates degree or advanced training is considered a plus
- Knowledge of sensory evaluations
- PLC experience
- Experience using Wonderware and ControlLogix
- Responsible for plant reliability in designated area of the plant; equipment downtime, execution of permanent repairs and preventative maintenance, complicated changeovers, and significant improvement of area, backup for Reliability Leader and maximizes overall area and plant performance through reliability
- Perform all complex troubleshooting and repairs to minimize downtime in designated area of plant
- Ownership for all technical changeover procedures and effectiveness; completes complicated changeovers within scheduled timeframe
- Notifies Technical Manager of potential upgrades and modifications
- Fluent in CMMS – add and complete work orders through CMMS providing adequate detail, follow-up and parts sign-out
- Recommend and implement improvements for recurring reliability issues in Area
- Attend and participate in all maintenance planning and daily downtime meetings
- Provides training for operators in optimal changeover procedures, proper PM and work order completion
- Every associate at Mars has responsibility for the achievement of quality and food safety
- Manage spending to support overall maintenance budget as required
- Support minor projects as required
- Maintenance Team
- Minimum Secondary School diploma and Post-Secondary Education in a technical field
- Recognized trade certificate/license (mechanical or electrical)
- Safe work practices with equipment, materials, automation, etc
- Strong technical problem solving and troubleshooting skills
- Organizational and time management skills
- Knowledge of food safety, HACCP, ISO, materials conversion
- SAP PM working knowledge
- 5-10 years of manufacturing experience as licensed millwright or electrician with significant understanding manufacturing operations
- Demonstrated ability to continuously improve an area/equipment operation
- Performs all assigned activities & job tasks
- Ability to Operate equipment in a safe and efficient manner
- Able to assess equipment operating reliability and perform routine repairs, adjustments and
- Performs equipment & Building PM's as assigned
- Knowledge of how to maintain accurate records of QC checks, production numbers or waste
- Self-Development: Ability to learn additional skills and develop in role with additional
- Conflict Management: Can handle tough situations and equitably resolve conflict with colleagues
- Dealing w/ Ambiguity: Can effectively cope with change and comfortably handle risk & uncertainty
- Integrity & Trust: Is widely trusted by colleagues
- Demonstrated ability to work well in a team environment, taking initiative with team along with other team members to train, motivate and solve problems
- Shows initiative in self and team development, is reliable, uses time wisely and is willing to accept change
- Ability to complete root cause failure analysis on issues involving reliability, product/packaging
- Provide emergency/unscheduled repairs of production equipment during production and performs scheduled maintenance repairs of production equipment during machine service
- Perform mechanic skills including, but not limited to, mechanical, electrical, pneumatic, hydraulic, troubleshooting and repair of production machines
- Perform a variety of electrical, PLC, programming maintenance and functions
- Use a variety of hand and power tools, electric meters and material handling equipment in performing duties
- 4+ years of manufacturing experience; strong hydraulic, pneumatic, mechanical and industrial skills. PLC and HVAC experience desired
- Demonstrates Ability to Focus and Clearly Communicate Ideas, Issues or Problems and Communicates Results Of Work In an Impactful Way
- General Maintenance & Repair Skills and Record Keeping on Production Machines & Equipment, HVAC Systems, Chillers, Boilers, etc
- Basic Knowledge CNC Mills, Lathes, Drill Press, Sheers, Iron Worker, Punch Press, Grinders etc
- Basic Metal Fabrication & Assembly, Welding, Brazing, Soldering & Cutting
- Basic Plumbing Experience, Pipe Fitting, Treading, etc
- Basic Trouble Shooting & Problem Solving Skills
- Basic Electricity, Wiring & Controls
- Basic PLC & Programmable Controllers Experience
- Read Electrical & Mechanical Schematics/Drawings
- Use of Measuring & Testing Instruments: Calipers, Voltmeters, Ohmmeters Etc
- Provide Leadership to Safety and Sanitation Programs as Required
- Ensures Adherence To All Safety, AIB, and GMP Guidelines
- Maintains & Updates Attendance and Performance Records
- Participates & Supports Company Programs & Initiatives
- Perform Additional Duties as Assigned
- Associates Technical Degree With 5+ Years Experience or Bachelor's Technical Degree With 2+ Years Experience or High School Equivalent With 7 to 10 Years Maintenance & Mechanical Experience in Lieu of Degree
- Computer Literate (Word, Outlook, Internet, Web-Based Applications, AutoCAD is a Plus
- Basic Leadership Skills, Ability to Establish Priorities
- Good Communication Skills and Attention to Detail
- Experienced Working in a Food, Beverage or Manufacturing Environment
- Basic Knowledge in Facility Operations, Process, and Package Equipment
- Basic Understanding of Programmable Logic Computers and Facility & Process Software Programs
- Able to Lift up to 40 Pounds Repeatedly
- Willing to be Flexible With Work Hours and Also Work Overtime
- Exhibit troubleshooting skills in all aspects of distribution center maintenance including electrical, PLC, mechanical, breakdown, and analytical areas of the business. Apply training acquired both externally and internally to projects, assignments, and incidents to gain competence within the department
- Apply Safe Work practices learned from previous assignments and as a demonstration of understanding the organizational requirements for Safety. Recognize and communicate safety-related issues during troubleshooting assignments
- Demonstrate customer-focus by maintaining a neat and clean work area during both localized and shop-area projects
- Troubleshoot equipment-related problems and process performance related issues in order to determine the root cause(s) of a particular request or incident. Use systematic troubleshooting methods to determine the key root cause. Apply good judgment to choosing solutions
- Install electrical conduit, wiring, switching devices, controls, fixtures, motors, outlets, enclosures, and other such equipment in order to increase capacity, repair breakdowns, or improve efficiency
- Analyze and repair mechanical and operational problems on assigned equipment (i.e. conveyor/sortation, building/facility, fire/safety) and plans and takes corrective action
- Assist in testing and calibrating electrical, pneumatic, and HVAC controls
- Conduct routine preventative maintenance inspection of assigned equipment, report findings and take corrective actions if possible. Record findings in CMMS
- Notify maintenance department of recurring equipment malfunctions, reliability concerns, and corrective actions recommended or taken
- Use computerized maintenance management system to seek out similar issues for help with resolution and/or to build justification for replacement equipment. Lead the effort to apply the tools of the computerized maintenance management system to reduce failures and to increase the time between failures (or time between services). Enter feedback from field findings
- The ability to work in a constant state of alertness
- Mechanical maintenance, carpentry, plumbing, conveyors, and sortation: 2 years
- Perform routine and emergency repairs on plant processing equipment
- Complete plant work orders and work requests submitted by production and administrative personnel
- Support the overall facility maintenance as needed including general building and general grounds maintenance
- Perform diagnostic troubleshooting of machines and equipment used in an industrial high volume batch mixing and automated filling process
- Two (2) years of general industrial mechanical maintenance experience
- Experience in basic industrial electrical systems and control systems
- Ability to communicate with internal customers to ensure high level of service satisfaction
- Read, interpret, and understand technical literature/manuals
- Ability to work safely in environments that involve elevated work, machine lock out and other risk prevention best practices
- Able to work 2nd shift and overtime, including some weekends
- Able to lift 50 pounds
- Implement and maintain preventive maintenance on all equipment and machinery within the plant, as noted in the equipment manufacturer’s guidelines
- Visually inspect and test machinery to detect malfunction. Communicate equipment problems to operations staff as needed. Ensure safety procedures in use consistently. (Lock out, tag out, etc.)
- Diagnose problems, dismantle defective machines and equipment, and install new or repaired parts, following the specifications set forth in blueprints, manuals, and schematic drawings
- Building maintenance and lighting (plumbing repair, changing lamps & ballasts, light remodeling, refrigeration systems, etc.)
- Source, quote, negotiate pricing for equipment and repairs
- Repair electrical and electronic components of machinery and equipment
- Maintain spare parts inventory
- Maintain open communication among the various departments. Communicate information pertaining to maintenance, equipment observations, problems and prevention
- Maintain costs, approve bills, and monitor credits and returns
- Complete other duties as assigned
- Ability to troubleshoot electrical, electronic, pneumatic, hydraulic circuits and machinery that incorporates one or all of these
- Ability to use precision measuring tools and use math
- Proficiency with electrical testing and measuring instruments (meters)
- Knowledge of PLC and servo controls and how they function
- Mechanical aptitude and ability to use a wide variety of tools, both hand and power
- Strong Communication: oral & written
- Analytical problem solving and decision making
- Negotiation/Persuasion skills
- Detail-Oriented. Strong focus on accuracy of work
- 1-3 years of industrial experience in maintenance
- Experience with PLCs, preventative maintenance programs, high-speed packing, and down-time analysis preferred
- Computer skills including Microsoft Word and Excel required
- General knowledge of OSHA regulations as they apply to industrial and facility maintenance
- Stand; walk; use hands to handle objects, or controls; reach with hands and arms; climb or balance; and stoop, kneel, crouch, climb or crawl
- The employee is occasionally required to sit and talk or hear
- The employee must be able to lift and/or move items up to 50-70 pounds
- Specific vision abilities required by this job include close vision, distance vision, peripheral vision, depth perception, and the ability to adjust focus
- Must be flexible to work all shifts which could be 8, 10 or 12 hour shifts (1st, 2nd and 3rd shift)
- Must be available to work weekends, holidays and overtime
- Must be able to achieve a passing score on both a written and practical NOCTI exam in the respective discipline (part of the selection process)
- Must have basic understanding of PCs and basic computer skills
- Food manufacturing experience is preferred
- Experience with Autonomous Maintenance (AM) is preferred
- Experience with Single-Minute Exchange of Die (SMED) is preferred
- 1-2 years hands on electrical or mechanical work in manufacturing systems maintenance
- Must be flexible to work all shifts - 1st (6am - 2pm), 2nd (2pm - 10pm) and 3rd shift (10pm - 6am)
- Must possess either a journeyman's card from a state approved apprenticeship program or a minimum of 5 - 7 years of hands on electrical and mechanical work in manufacturing systems maintenance. This should include experience as a qualified machine repair person, toolmaker, or machine tool builder in troubleshooting, machine repair, tool making, machine building, hydraulics, pneumatics, and mechanical systems
- Must be able to achieve a passing score on both a written and practical Electrical and Mechanical NOCTI exam
- Industrial electrical systems
- Process control & instrumentation
- Motors and controls (AC and DC)
- Analog and digital devices
- Schematics and electrical print reading
- Power supplies
- Electrical maintenance
- Hydraulic and pneumatic systems operational theory, troubleshooting and repair; including ability to read blueprints and schematics and systematically diagnose and repair problems
- Lubrication
- Mechanical drive systems including chains, belts, shaft, and gear drives
- Pump systems
- HVAC systems including controls for air, condensate, pressure and temperature
- Steam including boilers, temperature and pressure control, condensate control and system operation and performance
- Be able to troubleshoot and repair electrical devices such as fuses, motors, motor starters, proximity switches, circuit breakers, receptacles and plugs. Note: PLC experience is a plus
- Be able to troubleshoot and repair mechanical devices such as centrifugal and positive displacement pumps, roller conveyors, belt conveyors, palletizers, sanitary and non-sanitary valves, Fillers, check weighers, metal detectors, gearboxes, bearings, seals and etc
- Be able to use electrical equipment such as a volt meter and amp meter to determine electrical malfunctions on fuses, motors, motor starters and switches
- Use proper tools for aligning sprockets, sheaves and couplings on fans, motor drives, and pumps. Be able to track conveyor belts and align shafts
- Candidates should have some welding experience with Tig, Mig, Gas or stick
- Accountable for the QRMP (Quality Risk Management Process) standards as outlined in the plant’s QRMP accountability document, including the implementation, improvement and ongoing maintenance
- Install and maintain all plant manufacturing and packaging machinery and equipment to eliminate downtime and achieve maximum production efficiencies
- Perform preventative maintenance checks and repairs
- Record daily maintenance activities, PM’s, and work orders
- Ability to repair, rebuild or overhaul equipment
- Install or repair facilities lights, wiring, machinery motors, electrical panels, breakers, airlines, water lines, or gas lines as needed
- Relocate existing lights, plumbing, or electrical lines as needed
- Training and Safety – Provide a safe and healthful work environment for all personnel through consistent support of the company’s Heinz Safety Process
- Interprets company policies to workers and enforces policies and safety regulations
- Must be able to work flexible hours; days, afternoons, midnights, overtime and weekends as necessary
- Specific Duties
- Providing innovative solutions to resolve on-going breakdowns
- Troubleshoot and perform preventative maintenance (PM) on equipment. Make necessary repairs and adjustments on machines and equipment during production to minimize downtime and maximize equipment efficiency
- Provide training to associates and assist them so they can make minor adjustments to equipment
- Monitor equipment status and when necessary participate in equipment overhauls
- Utilize test equipment such as amp meter, fluke, and laptop computer to check electrical circuits, machine operations and process instrumentation
- Analyze equipment to improve efficiency, safety and quality
- Maintain legible, neat and accurate records, documentation, reports, etc
- Complete maintenance service request and perform routine preventative maintenance tasks as assigned
- Follow-up on current status of equipment modifications, work orders and preventative maintenance
- Meet with vendors and contractors as necessary to assure continued efficient and maintenance of equipment
- Upgrade skills as required due to improvements and /or changes in technology
- Insure good communication between different shifts
- Assist with new associate training
- Perform sanitation requirements as needed or required
- Productivity Responsibility
- Actively participate in team goal setting/implementation to insure that we are the low cost, high quality producer
- Strive to maximize the efficiency of the plant/department by submitting, & implementing process improvements
- Quality Responsibility
- Insure the quality of our products and our workplace by following all procedures and guidelines
- Comply with all established GMP's, HACCP guidelines, Housekeeping responsibilities and QCMS operating procedures
- Assist in the implementation of the QCMS program and training of new associates
- Safety Responsibility
- Actively participate in team safety efforts to achieve/exceed plant goals
- Involvement & supportive of KSRMP teams & processes
- Required to perform all duties safely & use discretion to prevent injuries to self and/or others
- Must presently reside in the maintenance department or have passed the qualification process for bidding into the maintenance department
- Previous maintenance experience and/or equivalent technical training
- Read and understand operating manuals
- Ability to interpret, analyze, and write electrical and electronic diagrams or schematics
- Ability to safely and effectively work on plant facilities and equipment
- Able to work well within a team environment as well as work effectively with all associates
- Planning/organizational skills and strong verbal communication skills
- Understanding of requirement and importance of documentation
- Understanding and knowledge of electronics and mechanics
- Works with all departments to meet or surpass the plant’s safety goals
- Follows all GMP’s (Good Manufacturing Practices)
- Ensures compliance with company policies and procedures
- Participates and provides input with the team during DDS (Daily Direction Setting) meetings
- Prioritizes and coordinates maintenance work to ensure maximum equipment uptime
- Performs troubleshooting as needed to minimize downtime
- Performs equipment repairs
- Installs/ repairs/ maintains all types of electrical and mechanical equipment including PLC’s, wiring, motor starters, switches, motors, gearboxes, pumps, filters, actuators, valves, etc
- Reads and understands all types of blueprints and CAD drawings
- Operates power tools, hand tools, and electrical and instrument test equipment to install, maintain, and troubleshoot plant equipment
- Operates welders and torches to perform repairs
- Operates trade specific tools including but not limited to micrometers, calipers, and verniers
- Operates all types of machine shop equipment including drills, lathes, milling machines, grinders, and cut-off saws
- Performs all necessary documentation of work performed and any unusual conditions, or defective equipment with the highest accuracy possible in SAP
- Executes ownership of tools and shop by maintaining good housekeeping and a clean and orderly work area
- Administers training as needed
- Filling of a specific position on the Line or Crew
- Adjustments to equipment, product or supplies through the natural process variation to promote maximum efficiency
- Aiding Supervision and other Line Employees in the building of capabilities and training new and existing employees to the line, department or plant
- Being thoroughly versed on all matters pertaining to Safety in the Job, Department and Plant
- Ability to perform calculations of process measurement (KPIs) to include but not be limited to yield, utilization, overfill, inject pick up or nonconformity rates
- Communication to all appropriate personnel regarding tasks that needs to be accomplished in order to maximize efficiency
- Filling in for line members for unplanned relief or to help troubleshoot a problem
- Plan for, prepare and install equipment and utilities
- Troubleshoot down equipment, find cause, and make necessary repairs
- Direct and assist apprentices and other crafts in completion of repairs and projects
- Perform prevantative and predictive maintenance on all facilities and equipment
- Read schematics and equipment drawings (electrical, hydraulic, pneumatic, etc.)
- Work with PLCs, VFDs, and other control components
- Prepare, complete and record work orders, PM data, equipment histories and other maintenance data
- Assist or fill in for other employees as directed
- Observe plant and safety rules at all times
- Maintain a neat and orderly work place
- Perform other miscellaneous duties as directed
- Must pass the maintenance assessment test with a 60% or greater score
- Must be willing and able to acquire knowledge and skills of ‘B’ level Craftsperson through successful completion of on-the-job training, computer-based learning and training classes. Timeline to be determined by supervisor
- Must have the demonstrated mechanical aptitude to work from all types of blueprints, maintenance manuals, and drawings
- Must have the demonstrated mechanical aptitude to the basic use of and measuring of instruments/precision tools (including Non Destructive Testing (NDT)) equipment), fasteners, piping/fittings & valves, cutting and welding, packing/sealing/gasket products, air/steam traps, rotating shaft components, filtering media and rigging
- Must be able to interpret equipment conditions using color scales on NDT instruments
- Must have a high degree of mechanical aptitude
- Demonstrated ability to perform basic mathematical functions including addition, subtraction, multiplication, division and percentages
- Must be willing and able to work rotating 8 or 12 hr shifts, including nights, overtime, weekends, holidays, and additional hours beyond regularly scheduled shift to cover vacancies, work jobs in progress and attend training
- Must be able to ascend and descend stairs, ladders, etc., to work in elevated areas of the plant, and must be able to work in confined spaces
- Must be willing and able to work in inclement conditions and extreme temperatures
- Must be able to frequently lift 10-25 pounds with occasional lifting up to 50 pounds
- Must be computer literate including being able to enter and retrieve data
- Must have very good time management skills with ability to prioritize tasks and work independently
- Must be willing to accept accountability
- Must have demonstrated high performance (work performance, attendance record, safety record.)
- Must have adequate transportation
- Must be able to travel
- Experience with Reliability Centered Maintenance including: vibration detection or analysis, infrared imaging, oil analysis, cause failure analysis and documentation
- Maintenance experience using precision instrumentation including: torque wrenches, micrometers, calipers, dial indicators, laser alignment tools, sheave alignment tools, etc
- Experience in cutting, welding, and metal fabrication
- Prior predictive and preventative maintenance experience
- Previous experience of manufacturing operations
- Knowledge of fasteners
- Experience maintaining and repairing rotating equipment (I.E. shafts, bearings, power transmission equipment)
- Experience aligning horizontal coupled and vertical coupled equipment using laser alignment
- Experience removing and replacing cartridge and component type mechanical seals
- Experience in maintaining and repairing fans, conveyors, pumps, drives
- Experience in pipefitting & tubing/fittings/valves & traps
- Experience in machine and equipment rigging
- Experience in data entry and SAP
- Experience repairing and troubleshooting Hydraulic and Pneumatic systems
- Experience in different types of Heat Exchangers
- Performance of ongoing preventive and repair response work orders on facility mechanical, electrical, plumbing and other installed systems, equipment, and other components
- General interior maintenance – hang pictures, install keyboard trays, repair office furniture systems and repair doors
- Assist the operations team in the maintenance and repair of building and equipment and/or as directed
- Replace lighting and ballasts
- Clean HVAC coils, change filters and belts
- Complete Hazard Assessments as necessary
- Must complete all required safety trainings as scheduled
- Practice Defensive Driving at all times
- Update work order status in real time
- Utilize CMMS systems such as 360 Facility for all work performed
- Perform Vehicle Safety Inspection
- Escalating problems or issues to Customer and Manager in a timely manner
- Attend work and safety meetings as required
- Other tasks as assigned
- High school diploma or GED equivalent required
- 1-3 years of experience in general building repair and maintenance, basic plumbing and basic electrical
- Demonstrated written/verbal communication skills
- Working knowledge of computer applications including Word and Excel preferred
- Conduct routine planned maintenance as detailed by the Computerised Maintenance Management System (CMMS) and directed
- Provide support to the Utilities function to ensure that production critical utility supply is maintained at all times
- Ensure compliance to all aspects of the Company’s Health, Safety and Environmental procedures are maintained
- Comply with EHS Regulations and Policies
- Associate’s Degree in Electrical or Mechanical discipline from an accredited University or college
- Successful completion of Electricity 1 and 2 coursework or equivalent
- Boiler Operator Certified or willing to obtain boiler license within 6 months of accepting position
- Good safety, attendance and performance record
- Possess mechanical aptitude
- Possess analytical troubleshooting ability
- Ability to perform work with minimum supervision
- Knowledge of plumbing, hydraulics, and welding
- Knowledge of electrical controls
- Possess strong leadership and administrative skills
- Possess production planning skills
- Knowledge of material control concepts
- Knowledge of PLC programming, troubleshooting and repair
- Possess high degree of safety knowledge in the area
- Master Electrician’s License
- Input into the plant maintainability reviews
- Input into the development of maintenance plans and procedures
- Input into the critical spares analysis process
- Integral part of the Commissioning team supporting cold and hot loop testing on Instrument, Control and Safety Instrumented systems
- Represent Operations in tri-party walk-downs and punch listing activities
- Sign-off & accept Inspection & Guidance on Certification (GOC) Check sheets
- Supervise/support Vendor/Contractor support personnel
- Attendance at Site Acceptance Tests
- Provide Operations day to day support for early works systems
- Input into the development of training plans for staff
- Fault finding of complex I&C systems and efficient resolution of technical issues that impact operability, safety and efficiency of the process units
- Detailed recording of maintenance activities and requisition of critical spare parts utilising the Maintenance Management System
- Active participation in safety briefings, safety talks and the Risk Assessment process
- NVQ, City and Guilds or equivalent qualification in a suitable Engineering discipline
- Experience in an Instrument maintenance role with an operating asset
- Experience of a gas, oil or petrochemical processing plant
- Experience with safety rules
- Experience in working as part of a multi-discipline maintenance team
- Full CompEx accreditation
- At least 7 experience in an Instrument maintenance role with an operating asset
- Experience with control of work processes and safety rules
- Experience of Commissioning on large Projects
- Experience of GOC, punch listing, tri-party walk downs and SIT’s
- Experience of fault analysis and maintenance on complex Instrument & Control systems
- Detailed understanding of Foundation Fieldbus field Instrumentation, ICSS interfaces and Compressor Controls
- Experience of developing equipment specific maintenance plans
- Experience of condition based monitoring techniques
- Experience of coaching and developing staff within competency management framework
- Must be able to work within a TEAM based environment. Must believe and be able to demonstrate “Team Before Me”
- Must be able to work unsupervised and possess a “Can Do” way of thinking
- Must have basic understanding of computer programs (i.e. E-mail, Data Entry, Document Review)
- Must have acceptable oral and written communication skills. Must have excellent interpersonal skills
- Must be able to work a flex work schedule as needed and able to manage well within a changing environment
- Must be multi-task oriented and able to understand the business needs
- Minimum of 5 years experience in the mechanical/electrical/instrumentation trade
- Must have capability to read blueprints, install electrical components, work closely with engineers, plan jobs and supervise jobs
- Journeyman Electrician license or Instrumentation certification
- Experience with preventive maintenance systems including upgrades to wiring, conduit and electrical control systems
- Ability to test or repair/troubleshoot electrical based equipment with test equipment like volt/ohmnmeters and oscilloscopes
- Familiarity with the NFPA 70 and NEC codes
- Mechanical skills, aptitude and the capabilities to perform mechanical work
- Experience in operating production equipment in a fast paced environment
- Working knowledge of boiler and pump maintenance
- Electrician/Instrumentation certification preferred
- Able to operate forklift, manlift, and other basic equipment
- Financial knowledge to assure compliance to the budget
- Professional certifications (electrical/welding, etc)
- Secondary education
- Professional certifications in Electrical/Welding
- Maintains all plant equipment (for example: blending and packaging equipment, valves, pumps, hot oil and steam systems)
- Executes and works within a shared leadership team environment
- Performs manual labor tasks in order to accomplish job duties (i.e. lifting, pushing, and pulling)
- Assesses projects, develops a bill of materials, obtains approval for purchase, and places orders for parts and equipment
- Performs all tasks in a skillful, controlled, safe and professional manner
- Reviews and completes work orders, preventative, and predictive maintenance assignments in a timely manner
- Assists in maintaining an adequate inventory of back up equipment, replacement parts and shop materials to ensure the proper operation of manufacturing and maintenance department
- Initiates corrective and preventive repairs
- Performs work in skilled areas of fabrication, assembly, welding, cutting and pipefitting
- Follows all applicable BP standards
- Maintains equipment, materials, and work areas to ensure they are clean, safe, and organized
- Takes action to identify and prevent problems related to HSSE, Quality. Recommends and initiates continuous improvement solutions to improve processes
- Troubleshooting and diagnosis of both mechanical and electrical equipment and system failures
- A minimum of 4 years of experience including welding, pipefitting, pump repair, basic instruments and mechanical equipment
- Must be qualified to safely operate a forklift and other motorized equipment
- Must have the ability to read and interpret mechanical drawings , blueprints
- Must have a basic understanding of computer programs (i.e. e-mail, data entry, document review)
- Must have the ability to work unsupervised and demonstrate Safety Leadership
- Should have knowledge of PLCs
- Should have experience with computer maintenance management systems (ex. Maximo)
- Should have TPM experience
- Should have Qualified Electrical worker certification
- Plans, carries out and evaluates preventive maintenance schedules for all designated mechanical equipment, either personally, or through outside vendors
- Inspect, diagnose and perform minor repair work on pumps, hydraulic equipment, compressors, controls, valves and related equipment
- Perform routine and preventative maintenance on pumps, and compressors. Operates a variety of diagnostic instruments and a variety of hand, electric, and air-driven tools
- Tests, troubleshoots, services and repairs mechanical equipment. Inspects, adjusts and replaces necessary units and related parts in the performance of repair and maintenance work
- Fabricate and modify parts and equipment as necessary. Evaluates status of mechanical equipment, and performs or schedules needed repairs
- Conducts various analyses and inspections of mechanical systems to determine the most cost-effective means of maintenance, repair or replacement
- Initiates and purchases equipment, parts, and supplies used for mechanical system maintenance in compliance with departmental and company policies
- Provides emergency field assistance to disabled equipment as needed and appropriate. Assists in the preparation of bid specifications for mechanical equipment
- Maintains records, prepares reports and other specialized maintenance records of equipment and mechanical equipment as requested by supervisor
- At least 1 year applicable work experience including experience with mechanical equipment, compressors, controls, valves, pumps and hydraulic equipment
- Must have a valid Driver’s License and acceptable Motor Vehicle Record
- No relocation assistance provided for this position
- Journeyman Elecrtrican
- I&E Technician
- Welding Certifications (Stick & Mig)
- Mechanical Certifications
- Develop and execute short and long-term Predictive (PdM) & Preventive (PM) maintenance programs for mechanical and electrical equipment, instrumentation and controls to ensure plant/equipment reliability, NERC, environmental and regulatory compliance
- Establish and maintain plant records for plant equipment maintenance using the Computerized Maintenance Management System (CMMS) SAP
- Coordinate maintenance activities between the Operations and Maintenance Departments
- Plan and coordinate on-site maintenance activities to address operational maintenance concerns reliability and availability. Develop complete work plans for repairs, modifications, preventive maintenance and overhauls
- Plan projects and activities by establishing correct benchmark times based upon work content analysis
- Provide support as needed to Maintenance and Operations Departments on emergency and urgent work
- Schedule and attend meetings with station supervision to refine schedules and make arrangements to accomplish the planned work
- Update supporting data and documents to maintain compliance with NERC standards that are related to load and energy forecast
- Specify, solicit and evaluate equipment and services from vendors for engineering and maintenance products and services for technical content and economic value
- Ensure compliance with Company environmental and safety policies as well as Federal, State and Local safety and environmental laws and regulations
- Promote productivity and teamwork in assigned area with open communication and timely decision making
- Ensure all Company resources are utilized in a cost effective manner, estimate resource requirements, monitor expenditures, and report on performance of assigned area
- Coordinate maintenance work plans with the Operations Department with respect to LOTO, Confined Space and Hot Work Permits as necessary for job execution
- Coordinate weekly planning meetings with Operations and Maintenance Departments
- Maintain a maintenance backlog tracking summary
- Knowledge of power plant systems and operations; and comprehensive knowledge in the area of responsibility
- Knowledge of SAP or other similar work management systems
- Demonstrated ability to operate effectively in a team environment
- Ability to effectively communicate (verbal and written) at all levels of the organization
- Ability to establish and maintain a positive and professional working relationship with all individuals
- Ability to read, create and follow written policies and procedures
- Ability to understand and use work management systems
- Attention to detail in development and delivery of work product
- High School Diploma or GED Equivalent
- Minimum of five (5) years of experience in Power Plant Operations or Mechanical/Electrical Maintenance activities
- Working knowledge of SAP or other similar work management systems
- Demonstrated leadership skills/experience
- Possesses excellent communication skills, is self-motivated and highly organized
- Has ability to interpret mechanical and electrical drawings
- Understands NERC regulations and associated electrical maintenance requirements as they apply to plant systems & equipment
- Working knowledge of safety, environmental and labor laws and regulations
- Experience working with the Microsoft Office Suite (Word, Excel, PowerPoint, Outlook…etc)
- Associate degree in Industrial Technology or an Engineering discipline
- Experience leading/ supervising employees
- Installs power supply wiring and conduit for newly installed machines and equipment such as extruders, conveyors, & programmable controllers
- Replaces faulty electrical components of machine such as relays, switches, and motors, and positions sensing devices
- Diagnoses and repairs or replaces faulty electronic components, such as printed circuit boards. Replaces electric motor bearings and rewires motors
- Plans layout of wiring and installs wiring, conduit and electrical apparatus in buildings
- Diagnoses and replaces faulty mechanical, hydraulic, and pneumatic components of machines and equipment
- Ability to read hydraulic and electrical schematics, comprehend complex drawings, specifications and procedures. Read and interpret safety documents, operating and maintenance instructions, procedure manuals
- Understanding of flushing and system fluid cleanliness installation
- Ability to assemble, disassemble and test various tools and assemblies for onshore and offshore surface and subsea applications
- Must have the ability to write routine reports and correspondence, speak effectively before groups of customers or employees of an organization
- Ability to be certified on forklift, scissor and man lift
- Physical ability to walk, stand, use hands to finger, handle or feel, reach with hands and arms and talk and hear. Frequently required to climb or balance; and stoop, kneel, crouch or crawl; occasionally lift and/or move up to 50 pounds
- Perform equipment troubleshooting and repairs by determining root causes of failures and implementing corrective actions
- Leverage theoretical training, equipment knowledge and computer skills to independently analyze OEE and tool performance data
- Ensure scheduled preventative maintenance (PM) is conducted on time and meeting all quality standards. Conduct maintenance with a strong safety commitment and mindset
- Collaborate with process tool owners, equipment engineers, internal cross-functional teams, and external vendors to improve equipment performance and cost of ownership
- Update or develop new and improved documentation for Equipment Maintenance under the direction of the Equipment Maintenance Manager or Engineers
- Responsible for training, mentoring, and developing other Maintenance Technicians
- Organize and monitor spare parts inventory to minimize unnecessary down time and cost of too much inventory
- Set up and maintain a high degree of cleanliness in the maintenance areas using 5S
- Support tool installations and tool modifications and maximize opportunities to learn from vendors when they are on site to reduce dependence on vendor support
- Maintain open and clear communication among team members Managers, Process Tool Owners and Equipment Engineers, internal cross-functional teams to resolve any issues, repairs, maintenance schedule, etc
- Drive other related responsibilities as assigned by management or as business needs change
- AA/AS Degree or equivalent
- Minimum 5 years of hands-on experience as an equipment maintenance technician in a high volume semiconductor, solar, or LCD manufacturing environment
- Detailed understanding of diagnostic, equipment test and evaluation, failure analysis, and debug techniques
- A leader in following all safety requirements and continuously working to improve workplace safety
- Advanced knowledge of control systems, electronics, mechanics and vacuum systems
- Experience with automation systems and robotics
- Proficient computer skills including Microsoft Office (Word, Excel, PowerPoint)
- Ability to work well with others in a collaborative team environment
- Performs preventative and corrective maintenance on electrical systems throughout the building - e.g. faulty wiring, power outages etc
- Performs preventative and corrective maintenance on buildings, structures, grounds, machinery and equipment - including air conditioning systems and plumbing amongst others
- Analyses equipment failures to determine causes and prevent recurrences
- Conducts other ad-hoc maintenance tasks such as desk moves, painting & decorating and other general plant maintenance tasks
- Assists in the keeping of maintenance records via Building Management System (BMS)
- Communicates effectively at all levels regarding recommended maintenance and repair procedures
- Supervises on-site specialist contractors
- Ensures compliance with Health & Safety regulations
- Troubleshoot, repair, maintain and calibrate equipment such as
- Grade level of job depends on prior experience as a skilled technician and industry related experience
- Able to read and understand electrical schematics and ladder diagrams, mechanical drawings, aerial strip maps and maintain as-built drawings for them
- Requires good communication skills, self-motivation and an assertive style
- Ability to be trained through both internal on the job training and external technical programs
- Experienced with installation, maintenance, and repair of refined petroleum products pipeline systems and equipment for station and terminal operations (experienced technicians)
- Knowledge of occupational hazards and required safety precautions, DOT requirements including those related to calibration and maintenance records, safety inspections and reports
- Strong verbal and written communications skills are required. Must be able to read and comprehend written documents, instructions and directions, as well as be able to accurately pass on information and instructions to co-workers
- Must be able to pass Operator Qualification requirements (OQ)
- Basic computer proficiency in Microsoft applications (i.e., Word, Excel, PowerPoint, and Outlook) is necessary in order to interface with company communication systems
- Must be self-motivated and capable of working with minimal supervision and/or direction
- Well-balanced interpersonal skills. Must be flexible and able to work effectively in a team environment and consistently maintain a professional and respectful demeanor/attitude with co-workers, clients, consultants, and representatives of various local, state and federal agencies
- In order to meet the various maintenance and general operational requirements, a mechanical aptitude is necessary
- Knowledge and experience working with construction contractors is preferred
- Experience in pipeline inspection is preferred
- Experience with petroleum storage and dispensing operations is preferred
- Pipeline hydraulics experience desired
- Basic knowledge of cathodic protection
- Knowledge of pipeline operations
- Experience with storage tank operations, including inspections, alarms and sampling
- Install, replace, or change machine parts and attachments, according to production specifications
- Dismantle machines and remove parts for repair using hand tools, chain falls, jacks, cranes, or hoists
- Record production, repair, and machine maintenance information
- Read work orders and specifications to determine machines and equipment requiring repair or maintenance
- Clean machines and machine parts, using cleaning solvents, cloths, air guns, hoses, vacuums, or other equipment
- Knowledge of measuring gauges such as tape measures
- Knowledge of various hand and power tools
- Ability to comprehend complex technical topics and specialized information
- Effective communication and problem solving skills
- Understanding of basic math, reading, and writing skills
- Perform needed maintenance on equipment and direct support of production operating needs. Evaluate equipment operation and suggest necessary action when malfunctions occur or improvements are needed
- Participate on various problem solving task groups; lead and direct other plant mechanics and provide input into training
- Participate in planning activities and manage various plant utilities including chiller, air compressor,
- Complete daily process work order data, initiate purchase requisitions, and utilize equipment and process documentation. plan & execute minor projects on an as needed basis
- Repair and maintain plant machinery and equipment such as mixers, conveyors, compressors, and pumps; repair or replace control devices such as switches, photo eyes, proximity sensors, pushbuttons, contactors, motor starters, etc. as needed; perform work order repairs, inspections and adjustments; able to set up and operate power tools, drill motor, circular saw, welders, drill press, bench grinder, band saw; hand tools and other metal working equipment; fabrication and modification of new and existing equipment; participate in plant safety, health and environmental programs; other duties as assigned
- Relative experience: bridge maintenance/ construction
- Experience with bridge maintenance/repair
- Good driving record is required
- This position typically involves a 40 hour work week but candidates must be willing to work additional hours as needed
- Candidates must be able to respond to emergency scenarios and work unususal/unscheduled work shifts that will or may require availability on days, nights, holidays, weekends, etc
- Provide emergency/unscheduled repairs of production equipment
- Diagnose, rebuild, and repair vehicles and equipment
- Perform inspections and preventative maintenance on vehicles and equipment
- Prepare and maintain records and reports
- Capable of troubleshooting electrical, hydraulic and pneumatic circuits
- Familiar with inverter or frequency drives
- Ability to utilize a variety of devices such as a multi-meter, oscilloscope, PLC controls, etc. to diagnose and repair machinery
- Capable of installing and or moving equipment using forklifts and other rigging techniques
- Ability to read and comprehend blue prints and other machine documentation
- Ability to use gauges, dials, and other machine indicators to troubleshoot or verify equipment operation
- Ability to perform routine preventative maintenance to ensure that machinery operates per specification, building systems operate efficiently, and that the overall condition of the building does not deteriorate
- Capable of inspecting machine drives, motors, belts, pulleys, bearings, sprockets, fluid levels, filters, and other associated components per a preventative maintenance checklist
- Capable of utilizing maintenance software to write work orders, document repairs, and book time
- Capable of aligning, fitting, and assembling components using hand tools, power tools, fixtures, and templates
- Repair or replace defective equipment parts using hand tools and power tools, and reassemble equipment
- Perform routine preventive maintenance to ensure that machines continue to run smoothly, building systems operate efficiently, and the physical condition of buildings does not deteriorate
- Use tools ranging from common hand and power tools, such as hammers, hoists, saws, drills, and wrenches, to precision measuring instruments and electrical and electronic testing devices
- Assemble, install and/or repair wiring, electrical and electronic components, pipe systems and plumbing, machinery, and equipment
- Diagnose mechanical problems and determine how to correct them, checking blueprints, repair manuals, and parts catalogs as necessary
- Inspect, operate, and test machinery and equipment in order to diagnose machine malfunctions
- Record maintenance and repair work performed and the costs of the work
- Dismantle devices to gain access to and remove defective parts, using hoists, cranes, hand tools, and power tools
- A high school diploma
- Technical training in industrial maintenance or an apprentice program preferred
- Minimum of three (3) years experience in maintaining and repairing production machinery
- Must be able to perform systematic preventive maintenance that incorporates industry best practices
- Safe use of hand tools, power tools, and electrical troubleshooting equipment to perform work safely
- Provide quick and effective conveyor repairs to support distribution functions including receiving, storage, and shipping activities
- Must be able to read and interpret schematics and drawings
- Must be experienced in PLC controllers and process instrumentation
- Must have experience in preventative maintenance and repair involving plumbing, carpentry, drywall repair, and high/low voltage electricity
- Must be a self starter with a dedicated focus on quality improvement
- Must be able to work in elevated areas of a distribution center involving heights of 32’ ceiling joists
- 5+ years of experience on the job in distribution building maintenance
- Operating knowledge of Microsoft office software and working proficiency with desktop/ laptop computers
- Proficient in electro mechanics, pneumatics, and hydraulics
- Flexible to work overtime and weekends as needed
- Ability to manage conflicts and reason, work well in team settings, and perform work independently with minimal supervision
- Maintain and repair conveyor and other warehouse equipment
- Assist the supervisor in maintaining a safe, injury-free work environment
- Maintain parts, usage and repair logs
- Generate and prepare maintenance files for all equipment in the facility
- Train employees on forklifts and safety
- Troubleshoots minor maintenance problems involving electrical ranging from 120 v single phase to 480 v three phase
- Performs preventive maintenance on equipment and buildings
- Performs routine plumbing repairs such as unstopping toilets, sinks or urinals, fixing of water leaks including leaking faucets, and water fountains
- Performs routine electrical repairs such as changing light bulbs or fluorescent lamps and the replacement of ballast and light fixtures
- Purchases supplies, and materials necessary to complete projects
- Assembles and moves furniture, hang pictures and bulletin boards, moves and sets up tables and chairs
- Repairs and replaces door knobs or locks, repairs door closures, patches holes in walls
- Paints interior and or exterior walls
- Knowledge of trades related to building maintenance and repair
- Knowledge of a variety of building maintenance procedures and techniques
- Knowledge of occupational hazards and safety precautions
- Skill in reading and following blueprints and assembly instructions
- Skills in following safety practices and recognizing hazards
- Skill in using hand and power tools
- Ability to perform moderate to heavy work in all types of weather
- There is frequent need to stand, stoop, walk, lift heavy objects (up to 100 pounds) and perform other similar actions during the course of the workday
- High school diploma or GED required and Four (4) years building maintenance experience, or any equivalent combination of training and experience
- A valid Illinois driver’s license is required
- 5 years of Maintenance Technician or Mechanic experience including fabrication using lathes, mills, and shop equipment
- 5 years of welding experience using Mig, Tig and stick welding
- 2 years of knowledge of PLC, electrical, and mechanical maintenance
- 5 years of an electrical background including troubleshooting low and high voltage circuits
- 5 years of power system knowledge, breakers panels, transformers, VFD’s and switch gears
- Associate’s degree or Technical certificate (HVAC, Electronics)
- 5 years of knowledge of PLC, electrical, and mechanical maintenance
- Ability to work in a hot and humid environment 15 – 20% of the time (dip room 105°F 40 % humidity
- Ability to lift and carry a 50lbs
- Must be able to pass a pulmonary function test (PFT)
- A H.S. Diploma with a minimum of 3 years of related industrial experience is required
- Completion of Trade School or Military Technical School is preferred
- Hands-on HVAC experience is preferred
- Ability to read and interpret documents such as SOP's, drawings, operating and maintenance manuals, and instructions
- Ability to write routine reports and correspondence and communicate effectively with supervisors, employees, and other internal customers
- Provides regular and routine updates to supervisor regarding work status
- Ability to use industrial control systems and standard office programs and computerized maintenance management systems such as SAP, GETS, and Documentum
- Needs to be mobile and able to independently transport themselves between various buildings on the Malvern campus, as dictated by the essential functions and responsibilities of the position
- Must be able to qualify for respiratory protective equipment use; and lift ergonomically, as required, a minimum of 25 pounds.Production
- To carry out both planned and reactive maintenance on complex elctro-mechanical systems and process equipment that includes Programmable Logic Controllers (PLC) and pneumatic controls
- Maintaining equipment and assets in a safe, compliant and reliable order
- Provide “hands on” Engineering support within the value streams
- Provide technical advice and solutions for equipment issues
- Complete and maintain GMP documentation in line with Current Good Manufacturing Practice
- Work as part of production team to ensure lines are safe, compliant and productive
- Be willing and able to coach others and develop understanding of others in equipment use and issues
- Support line change overs, continuous improvement activities and improvements to productivity
- BTEC ONC or C&G Technician or equivalent
- Apprentice trained (with applicable vocational qualifications)
- Appropriate engineering qualification (ideally HNC/ NVQ level 3 or equivalent)
- Performs day-to-day repair work on a variety of building physicalstructure
- Painting, carpentry, plumbing, electrical, masonry, cement work, heating, roofing, and related work
- Repairs structures; repairs and installs furniture and equipment; installs floor coverings, acoustical ceilings, and window glass; repairs roofs, floors, doors, locks, and related items
- Coordinate Conference room sets ups
- Performs electrical repairs such as replacing switches and minor wiring; repairs kitchen equipment; repairs faucets, sewers, plumbing, and minor HVAC equipment
- Monitors operation of the mechanical/electrical operating equipment
- Operate life safety/fires systems
- Respond to emergencies
- H.S. Diploma or GED
- Minimum of 1-year previous facilities maintenance janitorial/engineering experience
- Strong interpersonal skills and ability to function as a team member in a demanding service environment
- Some knowledge of computers preferred
- Maintain all Process Control Systems
- Responsible for troubleshooting and providing immediate preventable and corrective maintenance
- Ensuring all equipment throughout the industrial Plant is operating safely and at peak performance
- 10 to 12 hour rotational shifts 24/7 plant operation
- Generate parts request to ensure adequate Inventory
- Develop training and PM documentation
- Monitor, repair, and maintain a variety of television transmitters
- Maintain all types of broadcast equipment, including: Digital studio equipment, including routers and production related equipment
- Video cameras, production switchers, and routing switchers
- Digital audio and intercom systems
- Sony PMW350 recorders and camcorders
- Avid production editing and Leitch newsroom NLE editing systems
- ENG microwave equipment and accessories
- Satellite uplink and downlink equipment and accessories
- Computer based character generators and broadcast graphics systems
- Remote mobile microwave and satellite vehicles
- Ensure broadcast signal quality, for off air transmitters, cable and satellite companies
- Operate satellite truck uplink transmission systems and other equipment as needed
- Plan, document and install new broadcast systems
- Plan, document, modify and improve current systems
- Perform some I.T duties when required including desktop and printer support
- Recognized certificate in Electronic Technology
- Previous experience in maintaining video, audio, SDI, HD-SDI, AES and RF equipment
- Demonstrated knowledge of all types of digital and analogue broadcast equipment
- Knowledge of broadcast computer systems, operating systems, networking technology, applications, computer hardware etc
- Experience with CAD and Databases
- Ability to work independently and as part of a team, as projects dictate
- Ability to work under pressure and with limited supervision
- Must have and maintain valid documents required for travel to the United States
- Valid Class 5 or equivalent driver’s license
- Must have valid Passport
- Three to five years of mechanic experience
- Must have experience or knowledge of general maintenance tools, HVAC equipment/tools and electrical equipment/tools
- Must be willing and able to lift up to 50 pounds frequently with or without accommodation
- Must have excellent manual dexterity and visual acuity and be willing and able to stand, walk, stoop, bend, kneel, crawl, reach overhead, and climb stairs
- Must have the ability to interpret and apply instruction from blueprints and manuals to maintain existing equipment
- Must be willing and able to wear required PPE (personal protective equipment) such as a full face respirator, SCBA (self-contained breathing apparatus), safety glasses, steel toes, Tyvek, hearing protection and gloves
- Must have previous experience with manufacturing equipment, such as, pumps, valves, filters, conveyors, etc
- Must be willing and able to work a rotating shift schedule, including days, evenings, weekends, holidays and overtime according to business need
- Trade school certification, journeyman certification, Electrical Certification and/or HVAC Certification
- HMI experience
- Using basic electrical tools
- Experience in chemical plant
- Experience in a manufacturing environment
- Please include (paste or attach) an updated resume detailing your experiences and qualifications with your application for consideration
- Participate actively in department/plant safety programs. Promote safety rules and regulations
- Investigate and resolve equipment failures, determine root cause of failure, and recommend appropriate solutions to reduce reoccurrence of/or eliminate cause of failure
- Recommend and specify alterations and revisions to improve equipment requirement and/or system reliability/capacity
- Provide hands on support as required to resolve maintenance-related field problems as they occur
- Assist in the development, implementation, and periodic review of preventative/predictive maintenance programs to reduce unplanned shutdowns and improve overall plant on stream capability
- Maintain an error free execution. Pay very close attention to details and executes work to the highest possible standard. Apply a “Continuous Improvement” philosophy to daily work
- Four (4) years minimum maintenance experience in a petrochemical or manufacturing environment
- Accredited trade school graduate, military training or equivalent experience
- Pipe fitting skills, able to read and work from blueprints, good mechanical abilities
- Experienced in the troubleshooting and repair of centrifugal, diaphragm, and pneumatic pumps a plus
- Performs minor and major repair of all buildings and equipment. Frequent replacement of beams and uprights. Occasional use of hammer drill
- Acts as point of contact with outside and internal embedded contractors with general repair and special projects
- Coordinates / directly repairs or replaces broken windows, doors, and door locks
- Obtains estimates for supplies, repair parts; orders parts as needed
- Keeps work area clean and free of hazards – 5-S program
- Completes special projects as required – including design and repair work on material handling systems and other mechanical devices
- Completes projects as directed (machine moves, modifications, installations, material handling, remodeling, work area, etc.)
- Performs basic plumbing tasks
- Performs outside custodial duties as required
- Replaces / repairs site light fixtures
- High School diploma or GED from an accredited institution is required
- Minimum 5 years of experience performing maintenance duties
- Must live within a 50 mile radius of work location; no relocation is offered
- Demonstrated problem solving and team building skills
- Ability to meet assigned goals and objectives in a timely manner
- Ability to communicate effectively across job functions
- Maintenance experience in an industrial or warehouse environment is preferred
- Experience using industrial power trucks (I.e forklift, reach truck, order pickers) is preferred
- Experience working with and managing outside contractors and vendors is preferred
- Troubleshoot, design and install electrical, electronic, pneumatic, hydraulic, and electromechanical equipment
- Read, interpret, and troubleshoot PLC languages
- Determine root cause of equipment failures and develop preventive measures
- Perform electrical and mechanical design, fabrication, and alteration
- Solve complex electrical and mechanical problems including hydraulic, pneumatic, and electronics
- Diagnose machine operation failures and downtime using PLC controls and PC troubleshooting
- Inspect, operate, or test machinery or equipment to diagnose machine malfunctions
- Inspect drives, motors, and belts, check fluid levels, replace filters, or perform other maintenance actions,
- Repair or replace defective equipment parts, using hand tools and power tools, and reassemble equipment
- Order parts, supplies, and equipment
- Dismantle devices to access and remove defective parts, using hoists, cranes, hand tools, and power tools
- Operate cutting torches or welding equipment
- Other maintenance tasks as assigned
- Minimum 2 years of maintenance technician experience in a manufacturing environment
- Minimum High School diploma or GED from an accredited institution
- Must be authorized to work in the United States without company sponsorship
- No relocation offered. Must reside within the 50 miles of Pinckneyville, IL in order to be considered
- Demonstrated knowledge of PLC electronic controls
- Previous electrical experience
- 2 - 5 years of direct mechanical experience in a manufacturing environment
- Basic industrial electrical skills
- Basic computer skills; e-mail, Microsoft Word and Excel
- Basic PLC skills preferred
- Troubleshoots mechanical devices in operation. Dismantles and examines devices to gain access to and remove defective parts. Adjusts repairs or replaces defective parts
- Sets up and operates shop machinery such as lathe, drill press, grinders, band saws, cutting torch, welder. etc. Uses hand tools and pneumatic tools to modify or repair parts and equipment. - Installs new or repairs/modifies hydraulic and pneumatic equipment as needed. * Improves reliability and uptime of all equipment. Takes a proactive approach to equipment issues with a preventive maintenance mentality
- Contributes to upkeep and updating of required paperwork such as records, maintenance logs, documents, manuals, drawings, PM logs, etc
- Technical School Degree a plus
- 5+ years in the following areas
- Adhere to all plant safety policies, environmental guidelines, and procedures
- Troubleshoot mechanical equipment and systems in order to maintain machine performance expectations, maximizing uptime and throughput
- Inspect and perform predictive maintenance on equipment and machinery
- Completes projects with minimal guidance showing a proactive attitude
- Installs new or repairs / modify mechanical, hydraulic and pneumatic equipment as necessary
- Improves reliability and uptime of all equipment. Takes a proactive approach to equipment issues with a preventative maintenance mentality
- Employee is expected to employ some skills of the electric, plumbing, welding and machine shop trades
- Ability to positively communicate with all team members both verbally and in writing
- Participate in the Maintenance department meetings with an open mind and a candid attitude following the principles of TPM. Work well in a team environment
- Perform root cause analysis for safety, quality and process issues
- Participate in assigned areas of responsibility, in the shop and production areas
- Technical school or at least 10 years of industrial maintenance experience and capable to pass the Maintenance theory and hands on test
- Requires the ability to operate a wide variety of tools such as hand tools, power tools, drill press, band saw, welder, cutting torch, etc
- Must have knowledge of mechanical systems including gear boxes, motors, air compressors, pumps, power transmission, couplings, drive train troubleshooting, etc
- Must be able to read, communicate and comprehend written and oral instructions in English; read and comprehend safety rules, operating and maintenance instructions, procedure manuals, equipment files, etc. Ability to follow instructions from maintenance management. Ability to use pc computer to complete work orders
- Ability to handle multiple tasks in a fast-paced team environment. Strong organization skills and self-starter motivation. Prioritization skills in alignment with Plant priorities. Continuous Improvement mindset and results oriented
- Must have trade mathematical skills to add, subtract, multiply and divide and the ability to perform these operations using units of weight measurement, volume, and distance
- Must have ability to sketch and dimension any part that can require fabrication
- Must have physical ability to lift 65lbs occasionally
- Must be willing to work overtime when needed, off shift work and / or on-call rotation
- Electrical experience and Steam Boiler experience is a plus
- Minimum 10 years of hands on experience in industrial maintenance
- Repair of Industrial Mechanical Equipment
- Machine shop skills
- Electrical is a plus, but a combination of electrical and mechanical is preferred
- Completes projects with minimal guidance showing a proactive attitude toward minimizing equipment down time and lost production capability
- Troubleshoots electrical devices and circuits in operation. Dismantles and examines devices to gain access and to replace defective parts. Adjusts, tests, repairs, or replaces defective parts
- Must be able to read and understand wiring diagrams
- Be able to rewire existing equipment and new machinery
- Be able to utilize all maintenance equipment in a safe fashion, including forklifts and scissor lifts
- Must be able to diagnose electrical problems on machinery, and repair with minimum supervision
- Must be able to design and fabricate, with certain limitations, necessary equipment for operation of the plant
- Contributes to upkeep and updating of required records, such as maintenance logs, documents, manuals, drawings, electronic CMMS entries, etc
- Electrician Qualification Exam
- Technical Degree preferred
- 5 years experience in
- High School Graduate or General education degree (GED); or equivalent combination of education and experience
- Preferred documented manufacturing working experience with 1-5 years’ experience
- Experience with Composite material would be beneficial
- Have the skill and ability to learn all Treaters operations
- Ability to read and interpret documents such as safety rules, WIs, QPs, Customer Specifications
- Ability to work Night Shift, 6PM to 6AM
- Ability to work in Quick-Paced Production Environment
- Ability to work 12 Hour Shifts
- Ability to work extended hours and weekend when necessary to complete all tasks
- 60% - Perform general maintenance duties as needed
- 20% - Training and development
- 10% - Safety and Housekeeping
- 5% - Work Order Management Process
- 5% - Engagement and collateral duty ability
- Ability to lift 50 lbs, climb ladders, work at elevated heights and confined spaces
- Basic knowledge of all industry safety and environmental regulations and requirements
- Willingness to work in an outside environment
- Ability to read, interpret, and communicate from detailed job plans
- Ability to use precision maintenance tools (i.e. torque wrench, calipers, alignment instruments such as dial indicators)
- Ability to read and interpret original equipment manufacturer manuals and drawings
- Available to work week-ends, nights and holidays as requested for occasional emergency or planned maintenance
- General knowledge of power transmission equipment (i.e. belts, sheaves, pulleys, bearings, gear boxes)
- General knowledge of conveyance and storage equipment
- Cutting and Welding, pipe fitting and metal fabrication skills
- Must have strong written communication skills
- Must have strong analytical troubleshooting skills
- Must have good time management, priority and follow-up skills
- Must be willing and able to respond to Maintenance Call-ins on nights, week-ends and holidays
- Must have a full understanding of rotating equipment
- Good attitude toward safety, Cargill's interest, other employees, supervisors and desire/dedication to do a good job
- Good communication skills with others, both co-workers and supervisors
- Solid work performance record
- Ability to troubleshoot electronic and electrical systems, including motors, drives, and controls
- Working knowledge of programmable logic controllers (plc’s)
- Intermediate skill level with personal computer operation (word processing, spreadsheets, e-mail)
- Working knowledge of networks
- Certification, apprenticeship, military or vocational education in mechanical/electrical/electronic field or combination of education and experience equivalent to 3-5 years
- Experience in printing or industrial production environment is preferred
- AA Degree preferred
- The successful candidate must have a minimum of five (5) years of “hand-on” experience in troubleshooting microprocessor controlled equipment as well as all ancillary equipment
- Allen Bradley troubleshooting experience preferred
- Ability to troubleshoot electrical control systems
- Ability to use electrical test equipment; e.g., volt-ohm meter, ammeter, megohmmeter
- Ability to perform pipe fitting and welding
- Must be inquisitive in nature and able to formulate plans to solve problems
- Must be safety oriented
- Must have low absenteeism
- Must be willing to work a flexible schedule in order to support the operation
- Ability to meet confined space entry requirements
- Meet visual acuity requirements as documented in the Baxter Cleveland visual acuity procedure CL-01-01-037
- Must be able to lift, push, and pull up to 75 pounds
- Ability to lift above the shoulder up to 30 pounds
- Must be able to climb on ladders and catwalks to work on equipment
- Audiometric testing and hearing protection required
- Ability to work in unfavorable conditions (hot/cold temperatures)
- Ability to reach above shoulder
- Ability to bend/stoop
- Must be willing to work flexible schedules, if necessary
- Must have completed the CRC test thru the local Win Job Center
- Monitor controlled environment areas and rooms. Includes performing routine, regular daily checks for temperature, humidity, and static pressure, verifying HVAC, plumbing and electrical systems are working properly
- Oversee and maintain critical HVAC systems to ensure that indoor environments are comfortable and in compliance with production requirements
- Coordinate outside service providers as needed. Coordinate the installation of all types of equipment. Includes planning and installing services and equipment
- Manage utility systems including assistance in performing regular maintenance monitoring usage and upgrading equipment
- Assist to ensure facility compliance with all required SOP
- Assist developing and maintaining facility related written SOP processes, procedures, and forms
- Attend meetings and facilitate special projects as required by manager
- Lead and develop facilities technicians
- Proven expertise in preventive and predictive maintenance methods
- Ability to identify root cause of problems and effectively initiate immediate corrective action to prevent reoccurrence
- Excellent interpersonal, written, verbal and electronic communication skills
- Strong work ethic, good judgment and decision-making skills
- AS degree or higher in trades or proven experience equivalency
- Minimum 5 years direct experience in a an industrial environment with manufacturing equipment and/or facilities in a production environment
- Work related experience in ensuring compliance with safety initiatives
- Knowledgeable in the areas of hydraulics, air systems, mechanical drives, mechanical components, installation methods, troubleshooting and repair techniques and methods, welding, and basic industrial electrical
- Demonstrated basic computer skills and proficiency in MS Office and other Windows based programs and internet skills
- Perform turn-key work as required to ensure vacant apartment homes are rent-ready in a timely manner
- Apply all applicable Atria Policies and Procedures such as, but not limited to, company operating and safety standards. Promote safe work practices among on-site staff
- Ensure compliance with all federal, state and local laws, specifically Fair Housing regulations, building codes and environmental laws and regulations
- May drive company vehicle from community to social and other various destinations (only if required by community)
- May supervise the work of other associates and outside contractors
- High School diploma or equivalent (GED) preferred
- 1 year experience in property management maintenance performing the duties associated with a Maintenance Technician
- Able to perform basic arithmetic skills such as measurement, addition, subtraction, multiplication and division in order to do basic calculations and analysis such as estimating, determining averages and percentages, and totals
- Able to occasionally operate general office equipment such as, but not limited to, personal computer, telephone, photocopying machine, facsimile machine and postage machine
- Able to frequently use general maintenance tools, supplies and equipment such as, but not limited to, hand tools, pressure washers, blowers, paint equipment, pool chemicals, ice removal equipment, ladders, landscaping equipment, sanders and safety equipment
- Able to frequently handle and use chemicals and general cleaning supplies
- Must possess basic hand tools necessary for performing maintenance related duties
- Position requires driving responsibilities (may use Company provided vehicle and/or personal vehicle)
- 40% - Perform routine plant maintenance
- 30% - Perform preventive maintenance
- 20% - Maintain maintenance records and assist in plant production as needed
- 20% - Safety- Responsible for safety of self and teammates
- Excellent Math Skills
- Proficient in the following areas as defined by maintenance exam: Mechanical Aptitude, Mechanical Repair, Welding, Electrical
- Ability to obtain boiler certification within one year
- Ability to lift 50 Lbs
- Agricultural background/experience
- Outlook for email
- Perform daily/weekly preventative maintenance on all equipment, recognize unsafe conditions and take proper measures to correct any unsafe situations
- Maintain critical parts inventory including supply and replenishment as needed
- Order proper parts for completion of projects and general tasks
- Work with multiple departments and communicate effectively to all levels of the organization on a daily basis
- Work overtime as required. Provide good crossover report to next shift
- Document and troubleshoot activities on a daily basis
- A minimum of 3 year’s experience in mechanical and electrical field or combination of trade school
- 2 years on the job experience in a similar position
- Technician must be able to lift 50 pounds on regular bases
- Able to read schematics, architectural and electrical drawings
- Must be able to troubleshoot and repair plant and production equipment without direct supervision. This includes Electrical, Mechanical, Hydraulic and temperature control equipment. Any additional equipment knowledge a plus
- Must be a self-starter, organized and willing to grow with the company
- Welding, plumbing, low voltage and PLC experience a plus
- Certification or training in HVAC, Electrical, forklift and LOTO, all a plus
- Maintain facility systems such as HVAC, electrical, plumbing: Monitor and repair HVAC system for the entire facility. Perform plumbing maintenance such as pipes, drains, faucets, disposals, showers and Jacuzzi tubs using methods that include soldering, brazing silver, PVC, CPVC and fittings. Reset/replace breakers, ballast and other electrical fixtures including switches and sockets; prevent and trouble shoot possible electric hazards. Monitor and repair the water (boiler) system in living units and facilities to ensure adequate hot water supply for guests, customers and employees. (50% time)
- Assist the Maintenance Department and performs other duties as needed: (10% time)
- Certified HVAC, plumbing or electrical skill required
- Apply intermediate working knowledge of facilities maintenance such as HVAC, electrical, plumbing and repairs as needed. (25% time)
- Completes preventative programs on all systems such as HVAC, boilers, pool certification etc. Competencies in plumbing, electric and HVAC repairs with minimal assistance or supervision. (20% time)
- Assist with unit inspections. (5% time)
- 2-4 year in role or similar role is preferred
- Basic knowledge of plumbing, A/C repair, drywall repair, painting and minor electrical preferred
- Ability to read and comprehend routine instructions
- Basic Plumbing preferred
- Six months related maintenance experience preferred
- 3 years HVAC, plumbing, appliance repair and general maintenance experience
- EPA certification
- Able to lift/carry supplies or equipment of 50 lbs or more with frequent reaching, stooping, bending and kneeling
- Extensive walking and standing
- Manual dexterity and mobility required
- 2-4 years in role or similar role is preferred
- Valid Drivers License required
- Available to work a flexible schedule including weekends and holidays
- High School diploma or equivalent and/or experience in a hotel or a related field required
- At least three years progressive experience in a hotel or related field preferred
- Trade school and/or College course work in related field helpful
- Previous supervisory skills preferred
- Stationary Engineer License from ( Chicago or Elgin) Required
- Experience in replacing circulating pumps motors, difference between volt electrical systems, using basic functions of building automation systems and pipe HVAC loops
- Assist with preventative maintenance and complete report work orders such as replacing ceiling tiles, light bulbs, patching vinyl, etc., to maintain the hotel and keep the product quality standard
- Perform preventative maintenance assignments on a scheduled basis (e.g., “room care”)
- Assist in checking and making routine repairs and assist on major repairs of all hotel equipment including small appliances, kitchen equipment, laundry equipment, boilers, pool equipment, HVAC, hand and power tools and general plumbing systems and fixtures such as pipe lines, toilets and sinks, kitchen and laundry equipment
- Service the hotel’s pool, including adjusting chemicals and cleaning filters; completing maintenance request forms and record logs
- Maintain the building exterior and “curb appeal” (e.g., snow removal, lawn care, painting, gardening)
- Exposure to extreme temperatures
- Operation of heavy machinery
- Comply with attendance rules and be available to work on a regular basis
- Perform any other job related duties as assigned
- 401(k) Retirement Plan
- Paid Holidays
- Newborn & Adopted Child Leave
- Complete work orders such as replacing ceiling titles, filters, light bulbs, patching vinyl, painting, repairs to pipe lines, toilets, sinks, kitchen and laundry equipment, etc. Perform preventative maintenance duties as assigned
- Refurbish furniture and fixtures such as cabinets, tables, chairs, doors, windows, counters. Paint and finish furniture and fixtures in guest rooms, if needed
- Maintain front entrance area, parking lot, and street entrance in a clean and presentable manner
- Perform maintenance and repair work on the interior and exterior of buildings, hotels rooms and contents, laundry and kitchen/refrigeration equipment, lighting, heating, air conditioning (HVAC), ventilation, and water treatment systems, and swimming pool (if applicable), etc
- Comply with federal, state and local laws regarding health, and safety services
- Advanced vocational training plus two years of experience in general building maintenance or construction, or equivalent combination of education and experience
- Previous background from the extended stay industry or apartment building maintenance preferred
- Knowledge of basic plumbing, carpentry, electricity, and equipment mechanics
- Ability to speak, read, and write fluent English; other languages beneficial
- Reading and writing abilities are required in order to receive instructions for the day and/or to read equipment manuals including safety information
- Problem solving, reasoning, motivating, organizational and training abilities
- Valid driver’s license required
- Frequently handling objects and equipment to maintain the facility
- Carrying, lifting or pulling items weighing up to 75 pounds
- Ability to understand and follow guidelines, procedures and company standards
- Demonstrates and promotes a 100% commitment to providing the best possible experience for our guests and associates
- Job functions to include maintaining all records as outlined within the Green Shield Binder to include but not limited to Guest Room PM deficiencies, PM Room Inspections, Life Safety Inspections, Elevator Inspections and Non-Guest Room Deficiency Log
- Job functions to include maintenance engineer to respond to all emergencies at the property or sister location when asked to be dispatched by a manager
- While performing the duties of this job, the employee is regularly required to stand; walk; use hands to finger, handle, or feel objects, tools, or controls; talk or hear; and taste or smell. The employee frequently is required to reach with hands and arms. The employee is occasionally required to sit; climb or balance; and stoop, kneel, crouch, or crawl
- The employee must occasionally lift and/or move up to 50 pounds. Specific vision abilities required by this job include close vision, distance vision, color vision, peripheral vision, depth perception, and the ability to adjust focus
- While performing the duties of this job, the employee frequently works in outside weather conditions and is frequently exposed to wet and/or humid conditions. The employee occasionally works near moving mechanical parts and is occasionally exposed to fumes or airborne particles and toxic or caustic chemicals
- Assisting to clean any areas of the hotel as assigned by the manager when needed to include but not limited to font desk, associate breakroom, guest laundry, fitness room, vending areas, stairwells and common areas
- Responsible for maintaining overall hotel cleanliness
- And any other duties as requested by the management team
- Must be able to obtain and maintain valid gaming license
- General maintenance or environmental services experience
- Must have basic computer skills and are familiar with Microsoft Office programs
- Maintenance of site mission and support equipment to include basic vehicle maintenance activities; facility janitorial functions; supply materials acquisition and electronic equipment cleaning, installation, and removal in harsh environments
- Determines maintenance priorities for the site and the seismic array in coordination with senior personnel at the facility and executes such priorities in order to maintain equipment functionality
- Provides site-specific training, briefings, and administrative support for Chugach staff; foreign national staff, and other visiting personnel
- Effectively supports Air Force and other contractor maintenance teams when on site
- Provides technical, administrative, and logistical support in the technical evaluation of services provided by modification teams and other contractors to the site supervisor
- Support the Facilities Manager in the implementation of short and long-term projects that apply to the MT position
- Performs all facility equipment repairs within the scope of the contract
- Actively share innovations and best practices with the best practice owner or facilities management leadership
- Provide oversight of contractors when on site ensuring each contractor is following all client’ and JLL polices and ensuring the delivery of the service is completed correctly
- Ensures completion of the preventative maintenance program for the building(s)
- Ability to work long hours occasionally, some weekends and responds onsite to support emergencies
- Actively participates in emergency response procedures, technical and safety training programs
- Experience in the trades of HVAC, electrical, plumbing, carpentry or relevant building systems
- Good interpersonal skills and a positive team attitude
- Excellent English language verbal and written communication skills
- While performing the duties of this job, the employee is regularly required to walk long distances and climb ladders to cover property portfolio
- Perform repairs and maintenance in plant or office facilities, or on machines and equipment
- Perform work in one or more of the maintenance trades including HVAC, carpentry, plumbing, painting, machine and equipment repair, electrical, sheet metal fabrication, and welding
- Conduct routine, periodic, or special inspections to determine repair and maintenance work necessary to prevent breakdowns of facilities, machinery, and equipment
- Test, inspect, troubleshoot, and repair machines and equipment using blueprints, sketches, layouts, wiring diagrams, drawings, and specifications
- Two year technical degree is required
- Three to five years maintenance experience in a manufacturing environment
- Possess basic electrical skills including motor control, electrical distribution, and machinery installation
- Possess basic mechanical skills repairing and maintaining manufacturing machinery and equipment
- Ability to use a ladder, work in elevated work areas, and frequently lift up to 45 pounds
- Experience in servicing and maintaining HVAC equipment is a plus
- The incumbent receives and evaluates work orders and requests, investigates the requests or problems and completes the necessary repairs where appropriate. The incumbent performs preventative maintenance and daily inspections as prescribed through a developed work flow plan and meets company standards. Is able to inspect and diagnose problems and determine corrective repairs. Completes repairs, and preparation of common facilities and buildings. Perform on call and preventive maintenance duties as necessary
- Respond to emergency site maintenance as required
- Performs maintenance and repair work to include: interior walls, painting, all types of floor covering, raised-floors, structural members, and all other building components as necessary
- Operate, maintain, repair, and install equipment, components, and systems that support the facility and infrastructure
- Performs general carpentry to maintain, repair, or upgrade facilities, structures, equipment and utilities
- Conduct random inspections to review work while in progress. Ensure procedures are being followed while making certain the highest quality standards are met. Review completed site work to verify compliance in accordance with applicable plans, procedures and all governing codes
- Confer with and advise other management personnel regarding maintenance projects and priorities
- Help perform periodic stock inventories and prepare material requisitions for replacement items as required
- Maintain accurate records of building/common areas serviced, and assist with special projects as required
- Respond in a courteous manner to all questions, complaints, or requests, referring to Management as required
- Perform any other duties within the assigned areas as deemed necessary by Facilities Manager to include but not limited to file maintenance, facilities site cleanup, maintain warehouse space and oversee janitorial contract
- This job description in no way states or implies that these are the only duties to be performed by the employee in this position. It is not intended to give all details or a step-by-step account of the way each procedure or task is performed. The incumbent is expected to perform other duties necessary for the effective operation of the department
- Must have the experience in all aspects of facility maintenance and ability to perform skilled work in general maintenance
- Must have high quality skills in painting, caulking, tile repair, carpentry, plumbing, general electrical and general HVAC skills with the knowledge necessary to troubleshoot issues to determine the need for licensed contractor
- Must have extensive knowledge and experience in the use of hand and power tools as well as a strong mechanical aptitude
- Must be able to follow written instruction and complete documentation associated with facility maintenance
- Must be proficient in Microsoft Office programs to include Word, Excel, Outlook and the ability to learn other specific programs and databases specific to the organization
- Must be able to independently lift a minimum of 50 pounds. Must be able to group lift a minimum of 100 pounds
- Must be able to climb ladders
- Must have good customer service skills
- Must have a valid driver’s license
- Must be able to obtain a Security Clearance: TS/SCI with life-style polygraph
- Provide constructive feedback on maintenance tasks and the manner in which they are executed
- Receive feedback and be accountable for own actions
- Communicate clearly (verbal and written) with customers and inter-department teammates
- Proficient with PCs and common software, e.g. Microsoft Excel® and PowerPoint®, Lotus Notes, and Adobe Acrobat
- Experience with CMMS software: SAP, Maximo, CWorks, Manager Plus, etc
- Possess PLC, VFD, and system/facilities controls knowledge accompanied by experience with software and hardware/instrumentation required for facility integration
- Monitor and adjust all mechanical/pneumatic equipment, control gauges, distributor panels, valves, thermostats, diffusers, and other equipment necessary to provide a comfortable environment for the buildings
- Monitor Energy Management
- Perform preventive maintenance duties, including changing filters, oiling motors, replacing light fixtures, inspecting and adjusting belts, replacing motor bearings, aligning shafts and annual inspections as directed by manufacturers
- Document and report activities to supervisor
- Comply with all applicable codes, regulations, and governmental agency
- Must safely operate all hand and power tools common to the construction industry
- Must know and use all personal protective equipment necessary to safely do assigned work
- Must work from ladders and scaffolding, on roofs, in crawl spaces, and in attics
- Must work while standing all day. Must bend over frequently. Must work with arms extended overhead frequently
- Experience with plumbing, heating, and electrical repairs
- Maintain, Troubleshoot and repair plumbing, heating and electrical equipment
- Working knowledge of commercial HVAC, kitchen equipment, and utilities
- Working knowledge of residential type HVAC (forced air, boiler systems)
- Knowledge of residential appliances it preferred
- Ensure quality products and timely completions of projects are achieved
- Communicate with supervisor and co-workers concerning projects
- Complete assigned tasks in a safe, clean and professional manner and communicate that completion with those necessary to get the accommodation or facility open and operational
- Clean and organize the carpenter's workshop
- Uphold the YMCA of the Rockies Mission, policies, and programs
- Uphold and reflect the YMCA core values of Caring, Honesty, Respect, Responsibility and Faith in all functions
- Ability to work cooperatively with others in a diverse environment
- Service and repair duties of drywall, painting, wallpapering and grouting
- Maintain a positive working relationship with suppliers
- Maintain Standard Operating Procedures for the area and ensure appropriate parts are in stock
- To actively participate in the Fairmont Pacific Rim’s environmental program and department specific initiatives in working towards sustainable operations
- To be Health & Safety conscious and actively involved in maintaining a safe work environment
- Painting and drywall experience necessary
- Must have an eye for detail and experience in Customer Service
- Highly organized, results oriented
- Able to maintain a positive and objective outlook in challenging situations and have the ability to work unsupervised
- May require working weekends or shifts other than dayshift
- Must be physically fit
- Profession aspect drywall repair, insulation drywall, patching and painting
- Tile, grouting and woodwork, is an asset
- Ability to complete work within set timeframes
- To ensure the continuity of production process-current repair of machinery and production equipment, diagnosing faults and implementation of preventive actions
- Maintenance of machinery in good condition,
- Participate in the planning and maintenance and their implementation in accordance with the timetable,
- Carrying out a repair documentation (technical drawing, material specification manual repair),
- Implementation of new technical solutions and modifications
- Patient and organized
- Able to think analytically
- Systematic and focused on deadlines
- Stress tolerant
- Normally receives general to no instructions on routine work, or new assignments
- Follows group standards and procedures
- Participates in testing, process improvement projects
- Adheres to policies and procedures Role expectations
- Perform Preventive Maintenance and breakdown repairs to CNC lathes, milling machines, and related equipment
- Proficient in electrical & mechanical preventive maintenance of metal cutting equipment
- Analyses to prioritize work and make decisions
- Responsible for cleaning and lubricating machinery
- Performs or coordinates maintaining the working areas in a clean and orderly condition
- Understands and practices safe working practices including proper application of chemicals
- The incumbent may be responsible for the transport of hazardous waste from work areas to designated hazardous waste storage areas
- Contributes to customer satisfaction
- Performs a variety of work in the maintenance and repair of building and grounds including carpentry, electrical, plumbing, and painting tasks; repairs and treats structures such as floors, sinks, walls, roofs, and carpets
- Responsible for the management of recyclable materials at the satellite accumulation areas and ensuring these materials are prepared for shipment to designated recycling facility. Capable of operating equipment necessary to prepare these shipments
- Completes required facility inspections including: Air Compressors, Rodent Control, Housekeeping, Fire Suppression System, and Balers
- Manages obtaining quotes and arranging for services of outside vendors as needed
- Performs Preventative Maintenance (PM) activities on the following equipment: Emergency Stations, Waste Balers, Spill Kits, Fire Suppression System and Exhaust fans
- Manages the storage and labeling of universal and hazardous waste and prepares waste for removal by contracted services
- Moves furniture, equipment, and supplies, either manually or by using hand trucks. Sets up, arranges, and removes decorations, tables, chairs, ladders, and scaffolding to prepare facilities for events such as banquets and meetings
- Maintains up-to-date knowledge of lockout/tagout procedures and OSHA safe operating guidelines
- Provides support to the maintenance department by assisting Maintenance Supervisor in the completion of assigned tasks in a timely manner
- Completes required Environmental, Health & Safety inspections including: Ladders, Fire Extinguishers, Compressed Gas Cylinders, Safety Harness, Hydraulic and Acid Spill Kits
- Must interface effectively with all levels of management in many diverse departments
- Respond to tenant service requests-must be able to prioritize these requests and respond accordingly as dispatched by the Service Center
- Painting of equipment and common areas
- Drywall repair and finishing
- Minor carpentry repairs
- Replacement of damaged ceiling tiles
- Roof maintenance including inspection and cleaning of drains and gutters
- Plumbing fixture repair and replacement
- Repair and maintenance of light fixtures and lamp replacement
- Perform on call duties
- Coordinate and supervise repairs provided by vendors and contractors
- Carry out daily equipment inspection logs
- Provide adjustments to HVAC System and replacement of HVAC filters
- Conduct periodic testing of fire and life safety systems per governing regulations and codes (Ex.-emergency generator, fire alarm, boilers, chillers)
- Communicate with tenants, owners, property managers, leasing agents, service providers and contractors
- Some experience preferred
- Professional appearance and attitude are essential
- Valid Driver’s License and State-minimum insurance coverage required
- Reliable transportation
- Pleasant, cooperative attitude
- Ability to work flexible hours and work well under pressure
- Must be available after hours to coordinate and, when necessary, respond to emergencies
- Efficient with computer and smart phone
- Works as a part of the property management team to deliver departmental goals, objectives and systems
- Maintains regular contact and builds solid working relationships with Property Managers and department leaders to ensure the highest level of customer service
- Responsible for all preventative maintenance, necessary maintenance and repairs to the buildings mechanical, electrical, HVAC and plumbing systems. Must be familiar with the location and have working knowledge of all building mechanical, electrical, HVAC, plumbing, life safety, fire protection and security systems to ensure proper operations and be able to act upon any conditions that are out of the ordinary
- Conducts periodic general preventative maintenance on the mechanical, electrical, HVAC, and plumbing systems, which involves normal lubrication, adjustment, cleaning, replacement of consumable parts (such as filters, indicator lights), and periodic testing of the equipment. These systems include, but are not limited to; air handling units (including both rooftop and built-up units), re-circulating air systems, water pumping systems, cooling plant and all plumbing system components. Also conducts general building maintenance, as needed
- Responds to tenant requests in the areas of safety, plumbing, mechanical, electrical and environmental needs
- Prepares and maintains maintenance logs and records
- Coordinates contractor, tenant and management approvals for work orders that require the use of an outside contractor. Maintains log of work order details
- Performs all assigned work so as to ensure the safety of the building’s tenants and the continuous operation of the property
- Familiarity with and conforms to all written operating procedures associated with the property
- Assists in snow and ice clearing operations, including the coordination of plowing and salting activities by outside vendors
- Other duties as assigned by Chief Engineer, Assistant Chief Engineer and Property Manager
- A minimum of five years previous building operations engineering experience
- Must be CFC certified in high pressure discipline and hold any other necessary/required licenses
- Proficiency with computer applications required, including Microsoft, Windows, and Outlook
- Familiarity with preventative maintenance and work order software systems
- Excellent communication, analytical and problem solving skills
- Demonstrates organization skills with the ability to successfully handle multiple priorities in a dynamic environment
- Team oriented, with the ability to build consensus and effective relationships in a cohesive business environment
- May be on call as necessary
- Valid Driver’s License may be required
- Maintains regular contact and builds solid working relationships with the Engineers, administrative staff, Property Managers and tenants to ensure the highest level of customer service
- Reviews maintenance invoices for accuracy
- Assists the Engineers or Property Managers in designing specs for a particular job and is able to discuss the bids and make recommendations
- Complete knowledge and understanding of the fire protection system including pumphouses, risers and monitoring system. Performs inspections required by code and/or insurance company
- Develops and maintains logs (with the assistance of the Administrative Assistant) on the maintenance history of each building and units as needed
- Communicates all issues/concerns relating to the properties with the Engineers, administrative staff and Property Managers
- Provides back up for the Engineers, if needed, and is available for after-hours emergency coverage
- Ensures compliance with Energy Star, Sustainability Program, Preferred Provider Program, Quality Assurance Program, Disaster Program, and Customer Service/Tenant Retention Program
- A minimum of three years of progressively responsible building maintenance, janitorial and engineering experience
- Effectively multi-task and recognize and address important and time-sensitive tasks and matters
- Demonstrates organization skills with the ability to successfully manage multiple priorities in a dynamic environment
- Experience with Sterile Production equipment, such as Powder Filler, Tank, Syringe Filler, Autoclave, Parts Washer is preferred
- Good industrial maintenance skills
- Good knowledge of rotating machinery (pumps, fans, blowers)
- Good knowledge of electrical systems, controls and electronics
- General understanding of automation systems
- Basic understanding of engineering principles as they apply to facility and production equipment
- Ability to read P&ID’s and other engineering documents
- Hands-on ability to isolate problems and identify root cause of issues
- Ability to assist others with troubleshooting direction
- Ability to manage multiple problems with supervisory direction
- Able to lift/move 40 lbs overhead
- Facility Maintenance and Operation
- Experience with general facility systems and equipment
- Ability to clearly describe technical issues
- Writing Skills
- Ability to clearly and neatly document work performed
- Ability to revise maintenance procedures that clearly define required tasks
- Ability to proofread other’s work for accuracy
- Good knowledge of OSHA safe work practices
- Good understanding of cGMP, GDP, and FDA requirements as they apply to maintenance
- Pharmaceutical Operations
- Knowledge of basic pharmaceutical manufacturing technology including washers, HEPA filters, etc
- Knowledge of Clean Utility technology
- Sanitary piping principles including the ability to understand pipe specifications, valve configuration, pump setup, etc
- Ability to gown in an aseptic manner
- Computer Systems
- Good knowledge of Process Control and Instrumentation Systems
- Basic knowledge of typical office automation software suite
- Two year technical degree or trade school a plus
- Five to Ten years of maintenance experience
- Three to seven years of experience in pharmaceutical industry
- Must be able to pass a DEA background check
- 3-7 years experience in a pharmaceutical/GMP environment
- Strong mechanical aptitude; pipe fitting, plumbing, and industrial maintenance skills.; knowledge of rotating machinery (pumps, fans, blowers). and electrical systems and electronics; general understanding of automation systems
- Basic understanding of engineering principles as they apply to facility and production equipment with ability to read P&ID’s and other engineering documents
- Troubleshooting; hands-on ability to isolate problems and identify root cause of issues
- Experience with general facility systems and equipment such as cooling towers, chillers, boilers, air handlers, vacuum pumps, compressors, etc. as well as refrigeration systems
- Pharmaceutical manufacturing technology (preferably aseptic) including fillers, washers, autoclaves, HEPA filters, etc
- Knowledge of Pure Utility technology such as ROEDI, Multi-effect distillation, clean steam generators, etc.; Sanitary piping principles including pipe specification, valve configuration, pump setup, etc.; ability to gown in an aseptic manner
- Experience with OSD equipment, such as Tablet Press, Coating, Blender, Mill, is preferred
- Good pipe fitting, plumbing, and industrial maintenance skills
- Good knowledge of electrical systems and electronics
- Sanitary piping principles including pipe specification, valve configuration, pump setup, etc
- Three to seven years experience in pharmaceutical industry
- Responsible to support Sheboygan Site
- Corrective and Preventive Maintenance of equipment, facilities, utility systems
- Independently complete assigned work orders
- Participation in the call-in program
- Successful completion of required training curriculum
- Must have a valid driver’s license for work related travel
- Required work related travel
- Required to be available for weekend and holiday on-call and after hours duty. Must be able to work independently on a variety of shifts
- Miscellaneous duties and tasks as assigned
- Exemplary attendance and adherence to schedule
- Lockout Tag out trained
- Contributes to department goals
- Shows dignity and respect while performing duties
- Identifies unsafe work conditions and reports them
- Must be able to follow all safety rules and regulations
- Ability to work independently on P.M. tasks
- Basic math, English grammar, reading comprehension
- Excellent organizational skills and 5S skills and follows good documentation practices
- Express ideas for process improvement
- Proficient in use of Management of Change Process knowledge
- Ability to read blueprints and other schematics
- Perform Corrective and Preventive Maintenance of equipment, facilities, utility systems
- Complete assigned work orders
- Provides direction and expertise to others in the department
- Ability to understand electrical safety (grounding, arc flash, etc.)
- Ability to use electrical testing equipment
- Ability to use calibration equipment to calibrate or test all types of instrumentation
- Ability to troubleshoot and repair ventilation equipment (air handlers, exhaust systems)
- Ability to solder and braze
- Ability to understand and use building management systems
- Ability to perform corrective maintenance on boilers
- Ability to troubleshoot and repair fluid and vacuum pumps
- Ability to diagnose steam trap problems
- Ability to operate, repair, and troubleshoot of high purity water equipment
- Ability to troubleshoot and replace mechanical seals and bearings on rotating shaft equipment
- Ability to use hoists and rigging equipment
- Uses machines or other tools as needed to clean, renovate and renew floor surface finishes; to sweep, dry mop, wet mop or machine scrub and wax floor; to sweep and shovel snow or remove debris from steps and walks; to vacuum rugs and carpets; to move furniture, office equipment, supplies, etc
- Physical ability to perform assigned tasks
- Possess work history of reliability and integrity
- Fork / lift Material Handling is the primary task
- Assist the operations team in the maintenance and repair of building and equipment when needed
- Performs all work using the proper safety equipment and in a safe manner
- General office maintenance – hang pictures, install keyboard trays, repair office furniture systems
- Perform additional job duties as requested by direct manager
- Position requires OT as needed
- Ability to lift at least 50 lbs. and use ladders up to 26'
- Team player, hard worker, good interpersonal skills, and ability to communicate well in both oral and written reports
- Speak fluent English
- Demonstrated good verbal/written communication skills
- To be familiar with all relevant S.O.P.'s (Standard Operating Procedures), Equipment Validation and controls for the operation and safe running of equipment
- To assist with training of Machine operators on machine set up, operations, fault correction and adjustment
- Communicate relevant information to management and staff in Engineering and other departments. This may include notifying current or potential problems, status of problems (e.g. expected repair time for a breakdown) etc. Communication may be verbal, written records or routine Team Meetings, etc
- Continuous improvement of production process equipment, by identifying and implementing improvement projects that will improve the operating effectiveness of equipment
- Coordination and liaison with vendors, site contractors and external specialist contractors, engaged in work on site
- Responsibility for one or more specific areas as and when assigned, e.g. specific production line(s) or area(s), Engineering Workshop, spares stocks etc
- Experience and knowledge of Plant maintenance and calibration Systems. Including software management systems. SAP, PEMAC, BMS, One World etc
- To maintain a high standard of cleanliness, hygiene and GMP during maintenance work, including maintaining the workshops and engineering storage areas in an organised and tidy condition at all times and ensures the correct storage of tools, spares and parts
- To participate in all training and assessment activities related to the position, e.g. GMP training, equipment technical training, Health & Safety requirements etc, and undertake additional tasks as assigned by the Engineering Supervisor/Manager/ Director
- Minimum of Senior Trade Qualification or National Diploma/Degree and at least 2 years post qualification experience. However, a combination of experience and/or education will be taken into consideration
- Experience of hands-on of mechanical and electrical maintenance and troubleshooting of Pharmaceutical Manufacture, Packaging, Laboratory, Containment and Plant equipment desirable
- Pharmaceutical and or Food experience desirable but not essential
- Must possess good computer skills, mainly to maintain databases and work with numbers
- Must possess superior written and verbal communication skills, excellent interpersonal skills, and the ability to multitask
- Setup and fault find Vial Line/Syringe Line and Packaging Line
- Carry out scheduled service on plant equipment
- To prepare plant equipment for external contractors and inspectors
- To assist external contractors when required
- Responsible for adhering to Standard Operating Procedures and Work Instructions pertaining to the Work-In-Process area
- Responsible for adhering to regulatory quality standards and for working within Health and Safety Guidelines and Procedures
- When required, you will be responsible for training and supervision of other staff
- Minimum of a Certification in Electrical/Mechanical Engineering and a minimum of 2 years relevant experience. However, a combination of experience and/or education will be taken into consideration
- Knowledge of working in a highly regulated pharmaceutical/ medical device company
- Ability to effectively communicate issues and status of tasks in a timely manner
- Experience of working in a regulated industry, FDA, IMB, ISO etc
- Clean room experience a distinct advantage
- You will be required to work on call for 1 week (7 days – Monday to Sunday) on a rotational basis
- You will also be required to be flexible within this role in relation to working overtime outside of your normal 39 hour week
- Performs calibration, calibration record keeping, scheduling, PM's, repairs and support utility
- Uses a variety of tools and equipment associated with maintenance work
- Troubleshoots and performs various repairs on utilities, laboratory instruments and equipment
- May determine methods and procedures on new assignments and may provide guidance to other nonexempt personnel
- Perform daily operations, maintenance and repairs on utility systems, manufacturing equipment and building systems in a cGMP environment with minimal supervision
- Identify any off-nominal conditions with mechanical equipment and mechanical troubleshooting of manufacturing/utility equipment in a clean room environment
- Troubleshoot the electrical equipment during off-nominal conditions; locate the source of trouble and make/arrange for all necessary repairs; this includes generating and completing critical systems change control and interact with and oversee contractor/vendor work
- Adhere to and remain current in assigned IOPS plant and department SOPs and required trainings as related to positional and department responsibilities; maintain an up-to-date training file to ensure compliance
- Follow safety rules and ensure compliance with NY state and federal EPA regulation and law; specifically responsible system repairs, upkeep, maintenance and operations managed within regulating agencies such as OSHA
- Interpret P&IDs, equipment/system layouts, wiring diagrams and specifications in planning and performing maintenance and repairs
- Ensure a safe work environment is maintained through adherence to safety guidelines and policies
- AAS in Engineering or Construction technologies with 2+ years of relevant experience in a similar position preferred; will substitute additional relevant experience for educational requirement
- Performs work tasks expected to be accomplished by a Technician as needed
- Schedule, complete, and assign Work Orders in a timely manner
- Schedule, assign, and complete incursions
- Attend Facilities Informational Meetings
- Communicate and coordinate with each Department and with Facilities Managers when planned and unplanned work events occur
- Schedule outside contractors/vendors to perform scheduled and non-scheduled PM work
- Follow current good manufacturing practices (cGMP)
- Maintain up to date training records
- Prepare management of change documentation as necessary
- Perform OJT as required for technicians
- Responds to corrective breakdown work and troubleshoots route cause analysis with Manufacturing
- Solid working knowledge of process controls, VFD drives, and pumps
- Working knowledge of functional area discipline (calibration, process equipment) and automated control systems
- Knowledge and ability to operate, analyze problems, and repair process PLC controllers
- Experience with instrument calibration
- Working knowledge and repair experience with pneumatic and electronic controls & systems
- Electrical background and the ability to work with low voltages
- Qualified to National Craft Standard, Minimum of 3+ years’ experience in Biopharmaceutical process Equipment operation and Maintenance. Will substitute Biopharma experience for similar manufacturing experience in a highly regulated industry
- Experienced equipment reliability methods including preventive & predictive maintenance, TPM, FMEA/RCM
- Hands on experience with automated equipment and controls
- Assist with the installation of pharmaceutical equipment
- Perform changeovers and setup of equipment
- Comply with company policies, SOPs, cGMP and OSHA requirements. Ability to communicate and work constructively with other departments and teams
- Demonstrate sound organizational, written and oral communications skills
- Participate in deviation and root cause investigations as required
- Utilize a CMMS to accurately document the completion of all maintenance activities
- Experience with mechanical, electrical and automated packaging equipment
- Must be able to work as part of a team and work with minimal supervision
- Clearly communicate issues and resolutions to management, peers and first shift maintenance team
- Be knowledgeable in LOTO, PPE, Confined Space Entry and Electrical Safety programs
- Knowledge of change control, Infor EAM CMMS, E-Beam, PLC, calibration
- Be able to learn electrical drawings, schematics and P&IDs
- Monitor, operate, adjust and repair the facility’s process critical equipment, systems and utilities in a safe, compliant, and efficient manner
- Report alarm or “out of specification” conditions to required personnel as per SOP’s and take the appropriate actions required to correct the condition
- Perform preventative/predictive maintenance, troubleshooting, and repairs on process critical utility equipment and systems including but not limited to; WFI/RO systems, clean steam systems, HVAC-R systems, boilers and high pressure steam systems, chilled water systems, air handling systems and water treatment systems
- Perform daily equipment readings on all process and non-process equipment
- Maintain high housekeeping standards for assigned areas
- Maintain detailed verbal/written communication throughout assigned shift and at shift turnover
- Communicate in detail verbally and via written shift logs, maintenance logs, process checklists and information systems (Infor EAM, E-mail, etc.)
- Adhere to safe operating procedures and work instructions
- Gather operating data and assist with preparing reports as required
- Sample and test process and utility system fluids as required
- Safely handle, use, and maintain the proper inventory levels, of all process chemicals and consumables required in the process utilities area
- Support the shutdown and isolation of process critical equipment for all maintenance activities
- Maintain a thorough understanding of and adherence to all company, cGMP, safety and environmental policies and procedures
- Current State of New Jersey Black Seal High Pressure Boiler Operator License
- 2 - 5 years experience working in a cGMP pharmaceutical manufacturing environment or other regulated environment
- 2 - 5 years experience operating, maintaining, troubleshooting and repair WFI, RO and clean steam systems
- 2 - 5 years experience in the operation, maintenance, troubleshooting and repair of high pressure boilers, chilled water systems and emergency generators
- 2 - 5 years experience monitoring and operating a BMS in a pharmaceutical manufacturing facility
- Work as part of a team but also able to work independently with minimal supervision
- Knowledge of LOTO, PPE, Confined Space, Hazmat and Electrical Safety programs
- Blue Seal Boiler Engineer License
- Refrigeration Blue Seal Engineer License
- Build and rebuild machine assemblies
- Ability to read & understand electrical, mechanical and pneumatic drawings
- Develop strong troubleshooting skills
- Responsible for the operation and maintenance of plant equipment, including but not limited to, high pressure steam boilers; chillers; heating/cooling air handling units; process waste treatment systems; CIP equipment; water purification system (water softening and carbon bed filtration, reverse osmosis equipment, continuous deionization equipment, sanitary pumps, multi-effect distillation equipment); tank mixers; air compressors and dryers; and chilled water distribution systems
- Responds to service calls and conducts repairs throughout the facility
- This position will operate independently while performing routine maintenance and receive minimal instruction on new assignments
- Will be assigned to a shift rotation in support of 24/7 plant operations that may require day, evening, or night shifts that will include weekend work
- Primarily interacts with Facility Department personnel. Moderate interaction with other departments. May act as a team leader when multiple technicians are providing maintenance services to another group
- Ability to read and understand technical manuals and wiring schematics
- Ability to troubleshoot control circuits and must possess basic pipe fitting skills
- Must have the ability to work on projects or assignments that are moderately complex in nature where judgement is required in resolving problems
- May provide guidance on routine tasks and offer troubleshooting assistance to other less experienced maintenance technicians. May utilize experience to suggest new methods to management. Expected to lead by example by exhibiting professional behaviour when conducting daily business
- 5 to 7 years of maintenance experience
- This position will receive minimal instruction on routine work but will receive general instruction on new assignments
- Primarily interacts with Facility Department personnel. Moderate interaction with other departments
- Must have the ability to work on projects or assignments that are moderately complex in nature where judgement is required in resolving problems and will provide recommendations to Facilities Management
- 2-5 years of maintenance experience
- Responds to service calls and conducts repairs throughout the facility. May be assigned to escort a contractor performing wok on the premises
- This position will receive general instruction on routine work with detailed instruction on new assignments. Will be closely supervised and often is assigned to work with more experienced, senior level maintenance technician
- 0-2 years of experience in the maintenance trades
- Repair, replace, install, and maintain plant equipment and facilities
- Read, understand, and complete with SOPs and cGMP’s
- Conduct daily, weekly, monthly, and yearly preventative maintenance on equipment – which includes: pumps, fans, blowers, gearboxes, rotary valves, compressors, air dryers, electrical systems, blenders, stretch wrappers, and robot
- Perform work with metal fabrication, piping, mechanical and electrical troubleshooting, and equipment repair as required
- Maintains replacement parts inventory and maintenance supplies
- Maintains files of vendors, suppliers and equipment service records
- Assists blend plant manager in assuring plant meets OSHA standards, while also responsible for conformity to safety procedures
- Oversee and maintain facility buildings and grounds
- Actively participate in all capital projects
- Maintain flexibility to work the necessary hours to keep the facility running, including night and weekend shifts as necessary
- High School education or equivalent and minimum 3 years related experience; five years preferred. Trade school education desirable
- Working experience in a Dust Hazard environment
- Experience working in an FDA regulated facility is preferred
- Knowledge and ability to read / understand P&ID drawings and schematics
- Demonstrated troubleshooting skills; ability to troubleshoot equipment when inoperable
- Demonstrated PLC programming and troubleshooting skills, including ladder logic
- Experience with pneumatics, hydraulics, and scaling equipment
- Working knowledge of electrical, both electronics and electrical systems
- Working knowledge and experience with weigh hoppers, bag houses, dust collection systems
- Working knowledge of Robotics and Dust Collection systems is a plus
- Experience with developing Preventative maintenance plan for plant equipment
- Ability to manage multiple tasks effectively
- Strong interpersonal and communication skills; ability to communicate well with other employees relative to production issues
- Excellent attention to detail and recordkeeping skills
- Perform departmental activities per standard operating procedures, MPS, and Philosophy
- Work with Production personnel to maintain and improve quality
- Create and execute MPS plans, meet MPS commitments and work with in the guidelines of MPS; reflect Milgard's business values and the Milgard philosophy in all business interactions
- Incorporate Milgard's vision and values into day-to-day activities and behaviors; guides and motivates others to remain committed to the Milgard philosophy
- Adhere to all facets of safety policies and procedures
- At least one (1) year of maintenance experience or equivalent
- Sense of urgency and self-motivation; ability to work independently
- Preventive maintenance repairs including performing safety related inspections
- Diagnose trouble shoot, plan and perform all mechanical operations required to modify, dismantle, repair overhaul and rebuild all types plant process machinery and equipment (electrical, PLC/Electronics, hydraulic, pneumatic, and mechanical, etc.)
- Building facility and grounds maintenance
- Record maintenance issues in the maintenance job tracking system, and update required equipment logs
- Insures repairs done to equipment are completed correctly and are verified by testing the equipment for proper operation and functionality
- Works in cooperation with engineering, manufacturing and/or outside contractors as directed
- Planning work time to meet all needs of the plant
- Previous experience troubleshooting mechanical or electronic systems
- Team player who can work effectively in a team environment and demonstrate a positive work attitude
- Demonstrated ability to work with minimal guidance, to troubleshoot and resolve problems, prioritize and organize workloads
- Ability to obtain a forklift license
- Safely repairs and maintains equipment and site
- Ability to react timely and safely to emergency repairs
- Ability to install equipment both mechanically and electrically
- Ability to read and trace schematics both electrical and mechanical
- Degree of expertise is determined by various mechanical / electrical skills (Troubleshooting, PLC knowledge, welding, machining skills, etc.)
- Ability to assist in design and construction of various mechanical or electrical projects
- Completes maintenance documentation in SAP. This includes job time confirmation and parts consumption
- Responsible for the instrumentation and electrical repair and maintenance of the plant equipment and production processes
- PLC fault finding experience preferred
- Responsible for stores management (Parts, Max/Min levels, etc.)
- Responsible for general housekeeping in the department and other maintenance areas throughout plant (Boiler rooms, Water recovery room)
- Responsible for helping operators/mechanics in other areas, as assigned by supervision
- Responsible for participating in safety activities
- Attend and participate in Powder Plant Programs/Committees/Training as required, such as Department Safety, Plant Safety, Behavioral Safety, Housekeeping Audit Teams, ISO, Life Saving Rules or any other safety programs
- Participate in the Powder Safety Journey. Adhere to the Golden Principle which is Simply to intervene to stop work if conditions or behavior are unsafe
- Minimum of 5 years experience performing a trade in a manufacturing environment
- Strong knowledge of electrical repair and maintenance
- Working knowledge of SAP R/3
- Strong interpersonal skills and ability to work well with others
- Strong verbal and written communication skills; communicates effectively with various employee groups, contractors and management
- Knowledge of Company policies and procedures
- Ability to organize priorities and perform at a fast pace
- Ability to multi-task
- Knowledge of process equipment
- Requires daily contact with employees in other departments
- Ability to work with contractors
- Ability to work Shifts
- Overtime coverage is required, particularly for short-notice absences of other Shift FLL
- May work in seated or standing positions for prolonged periods of time, performs sustained manual activities at moderate to heavy levels of exertion
- Works and travels throughout the plant environments of varied temperatures and humidity
- Climbs ladders and stairs and works on elevated platforms
- May work in confined spaces
- May use hand tools and operate fixed and mobile plant equipment
- May be required to lift up to 55 lbs
- Fabricate tools and equipment as part of the kaizen program
- Install new equipment and equipment add-ons per engineering specifications
- Assist operators and shift management with trouble shooting on equipment
- Inspects equipment and performs preventative maintenance activities to keep the facility operating efficiently, avoiding downtime
- Operates simple machines such as power saws, drills and grinders to maintain or repair facility equipment
- Strictly follow all 5S programs regarding use and placement of all tools, supplies and equipment
- Follow all standard practices are being followed with a high level of discipline, especially for safety related items
- Minimum of a High School Diploma
- 5 years experience with equipment maintenance, fabrication, electrical equipment required
- Experience with 5S, kaizen, and lean manufacturing preferred
- High level of time-on-task and independent thinking/reasoning skills preferred
- Must be able to lift 65 pounds and stand for long periods of time
- Also requires extensive bending and stooping
- Candidate must be able to work in a manufacturing & laboratory environment and be capable of wearing an air purifying respirator. To wear a respirator per OSHA regulations, candidate must pass medical evaluation and fit testing to qualify as a respirator user
- Two (2) years' Maintenance experience in a manufacturing environment
- Must be able to perform electrical and mechanical repairs to processing machinery and associated equipment
- Must be able to repair and install equipment from schematics
- Must be able to plan, prioritize and coordinate multiple activities
- Must be able to properly document maintenance information in a neat and legible manner when required
- Ability to work safely and at ease while wearing appropriate personal protective equipment including: respiratory protection, gloves, safety shoes, hearing protection, aprons, face shields and etc
- Follows all established safety rules and guidelines. Understands and communicates all hazards and safety issues to co-workers and managers/supervisors. Properly uses all personal protective equipment
- Must complete all required clean room training and maintain compliance at all times
- Observes all production, packaging and mechanical equipment, to include electrical, hydraulic, and pneumatic systems, to ensure proper and efficient operation
- Troubleshoots all production, packaging and mechanical equipment to locate
- Malfunctions and repair them
- Dismantles machinery and mechanical equipment using appropriate lockout/tagout procedures to remove defective parts; repairs or replaces the defective parts, using hand tools and power tools
- Determines and orders appropriate materials and parts needed for service/repair of equipment
- Performs preventative maintenance and changeovers on all machinery
- Troubleshoots and repairs electrical, hydraulic and pneumatic controls with the aid of schematics
- Uses blueprints, drawings, sketches, layouts, and equipment manuals to identify Machine malfunctions
- Inspects product for quality defects and notifies the quality technician and/or supervisor of quality issues. Ensures routine quality checks are appropriately performed
- Performs all tasks in accordance with established safety and quality standards
- Effectively communicates with all internal departments
- Performs and maintains housekeeping of all assigned areas. This includes applying Good Manufacturing Practices (GMP) to meet plant goals
- Ability to shut down any machine because of a quality problem so suspect material can be contained
- Ability to shut down any if it is down three times in one hour for the same mechanical problem
- Authority to contact any staff or management team member with concerns, questions or suggestions pertaining to their job or work environment
- Must complete all required injection molding training and maintain compliance at all times
- Observes all production and mechanical equipment, to include electrical, hydraulic, and pneumatic systems, to ensure proper and efficient operation
- Troubleshoots all injection molding equipment
- 1 Formal Qualifications and Experience
- 3-5 years work related experience in Hydraulic, pneumatic, mechanical and electrical fields
- Computer skills (Microsoft Office Products)
- Strong electrical background with emphasis around controls
- Proven ability to work safely
- Ability to troubleshoot mechanical, pneumatic, hydraulic, and electrical systems
- Able to work at all times of the day or night, as required
- Must have patience and perseverance and be flexible with the ability to prioritize
- Ability to research and cross-reference parts
- Ability to understand blue prints & electrical schematics and describe in detail completed repairs
- Strong organizational skills along with strong oral and written communication skills
- Able to work at heights using ladders, lifts and platforms
- Assess and repair equipment as problems arise for the machines and the building
- Attend and participate in maintenance department and plant meetings
- Assist in capital improvement projects
- Troubleshoot mechanical and electrical issues
- Make repairs in a timely manner, while working under pressure
- Assist other departments with improvement projects
- Complete required forms legibly
- Equipment Used: Hydraulic Presses, hand tools, lathes, milling machines, drills, ladders and scissor lift and PCs for troubleshooting
- Maintenance of building and grounds in order to structurally maintain the facility
- To provide proper preventative maintenance and repair for equipment
- All work performed in accordance with Company OSHE procedures and policies for facility and contractors
- Other duties assigned by Manager or Supervisor as needed
- Interprets drawings, calculates and determines indices, tapers, and other dimensions to be used for part(s), working raw materials into finished dimensions with exact tolerances per print
- Repairs and maintains all assigned machines and equipment, including preventative maintenance
- Troubleshoots, repairs, installs, erects, moves, and/or dismantles all types of machinery and auxiliary production equipment
- Initiates, reviews, and follows all standard operating procedures (SOPs) for area of responsibility
- Install, maintain, trouble-shoot, and repair industrial fixed, rotating, electrical, and instrumentation equipment such as pumps, valves, motors, and instrument transmitters
- Maintain utility equipment such as boilers and cooling towers through chemical treatment, testing, etc to provide reliable utilities for the safe and efficient operation of the plant process equipment
- Utilize electrical drawings, instrumentation loop sheets, P&ID’s, and equipment records to perform efficient and accurate work. Also assists with the maintenance of this technical information
- Demonstrate maintenance technical skills such as trouble-shooting, instrumentation calibration/repair, rotating equipment maintenance/repair, electrical equipment knowledge, piping installation, etc
- Demonstrate flexibility, creativity, and open mindedness
- Possess the ability to work well within a team environment
- Good organizational and communication (written/oral) skills
- Strong level of basic computer skills desirable
- Demonstrate a high level of professional behavior, displaying patience and respect for others
- Ability to use hand tools and power tools
- Must be capable of routinely walking, standing, climbing ladders
- Must be capable of lifting and walking with weights up to 50 lbs
- Ability to operate mobile equipment - fork truck, aerial lifts, etc
- Familiarity with engineering codes and standards preferred
- The individual will be very safety conscious when working with and around chemicals
- The individual must show initiative, have excellent attention to detail, be results oriented and customer focused
- The individual must possess the willingness and ability to work outside in various weather conditions
- The individual must also have basic computer skills and a willingness and ability to learn computer systems in use by BASF (SAP)
- Follow BASF corporate safety culture and procedures
- Install, repair, and maintain mechanical equipment per work instruction procedures
- Maintain proper documentation in according to site and government policies and regulations
- Responsible to follow site Quality, EHS, Legal Compliance policies and procedures
- Required: High School diploma or equivalent experience. BASF recognizes schools accredited by the Council for Higher Education Accreditation
- Preferred: a degreed industrial maintenance certificate from an accredited institution emphasizing mechanical system and equipment maintenance. Equivalent related experience, training, and skills will be considered
- 3 years Maintenance experience in an industrial setting
- Detailed knowledge of electrically and pneumatically driven mechanical equipment including rotating and reciprocating equipment and the ability to troubleshoot and rebuild this equipment
- Knowledge of piping and tubing system components and experience inspecting and rebuilding various types of valves (ball, gate, butterfly, etc.)
- Understanding of mechanical sealing technologies used to contain process materials in rotating pumping and agitation systems
- Familiarity with the use of optical alignment tools to align rotating equipment systems within industry accepted tolerances
- Detailed knowledge of piping, bolting, gasketing, and the ability to assemble systems with proper torqueing techniques
- Ability to read blueprints, piping and instrument diagrams, sketches, and detailed mechanical equipment diagrams
- Experience in rigging is a plus
- Demonstrated competency of Windows and Microsoft Office products
- Prior experience with Predictive Maintenance (PdM), Preventive Maintenance (PM) and Condition Monitoring programs with exposure to Process Safety Management (PSM) is preferred
- Performs repairs and maintenance in plant or office facilities, or on machines and equipment
- Typically performs work in one or more of the maintenance trades: carpentry, plumbing, painting, machine and equipment repair, electrical, and HVAC
- Uses hand and power tools. Tests, troubleshoots, and repairs machines and equipment
- Uses blueprints, sketches, layouts, wiring diagrams, drawings, and equipment specifications to perform work
- Monitors and/or repairs as needed on company owned machinery, equipment, vehicles, building and grounds as well as all other related properties, in a manner as to assure they remain in good operating condition and appearance
- Able to lift and push heavy equipment up to 50 lbs
- Certification in HVAC
- Satisfactory completion of a trade school electronics program or completion of a military electronic school
- Experience in a facilities maintenance environment
- Adhering to Company and Plant policies and guidelines
- Working safely and looking out for the safety of those around them
- Following Safe Reliable Methods (SRMs) or Job Safety Analyses (JSAs)
- Maintaining a safe and clean work environment according to plant housekeeping standards
- Attending and participating in Plant safety meetings
- Managing controllable costs through proper equipment, tool and consumable usage
- Reporting any safety or maintenance concerns
- Safely and efficiently perform maintenance tasks
- Administer preventive maintenance scheduling systems
- Troubleshoot/service and/or repair balers, conveyors, lift trucks, loaders, trucks, trailers and other equipment
- Plan, coordinate, communicate and perform all repairs and maintenance in a timely manner to minimize unscheduled downtime
- Perform some welding and fabrication
- Observe functioning of installed equipment and detect hazards or need for adjustments, relocation, or replacement
- Ensure that all plant maintenance and company compliance guideline as defined by the Omaha Recycling Plant Policy or Corporate EHS
- Train all new employees on preventive maintenance
- Seek and compare contractors for price and reliability
- Coordinate all contractor activities on or off site, including auditing their work and safety compliance
- Proactively audits contractors for quality and economy of service. Actively participate on the plant’s safety committee
- Frequently audits effectiveness of plant and trucking personnel performing preventative maintenance (P.M.’s) and vehicle condition reports (V.C.R’s)
- Maintains an adequate supply of pre-approved chemicals and ensures neat and orderly storage including labeling
- Maintains an accurate MSDS system
- Participate in safety and environmental audits
- Keep an accurate and adequate inventory of parts for processing equipment, tools and other maintenance related items
- Reports safety concerns to management
- Maintain a good working relationship with the plant management, staff and hourly employees
- Manages purchases through purchase order system
- Documents repairs and maintenance through maintenance management system
- Attend workshops to enhance knowledge and the capabilities of the plant
- Key Requirements
- Has a strong knowledge of hydraulics, lubrication, pneumatics, electrical and electronics technologies
- Able to recognize hazardous situations and develop a safe work plan
- Work schedule must be flexible to include occasional weekend duties
- Have excellent written, verbal, organizational, interpersonal skills and a positive attitude. Complete tasks in a timely, organized fashion; be able to work and be flexible with deadlines
- Self-motivated; ability to learn quickly and work independently with little direct supervision
- Possess mathematical, problem solving, analytical, communication skills
- Ability to remove, repair or replace AC/DC motors
- Has the ability to use a variety of hand tools, plus welding/fabrication skills
- Two years experience in a manufacturing environment with proven skills in the areas of hydraulic, electrical, PLC, computer-controlled equipment, and DOT (Department of Transportation) pre and post trip inspections strongly preferred
- Personal Protective Equipment
- Desire an individual with knowledge of food industry standards for production, safety, waste, and AIB/SQF housekeeping
- Strong mechanical and electrical aptitude skills
- Solid basic math skills. Ability to follow written instructions
- Interface with computer and have the ability to enter data into various software platforms. Previous CMMS experience desired
- Demonstrated work performance to be self-directed and self-motivated
- Proven track record on safety and quality. Professional attitude and good communication skills
- Performs routine preventive maintenance and emergency mechanical, hydraulic, pneumatic, and electrical maintenance on production systems and equipment, using knowledge of circuitry, electronics, electrical-mechanical devices, motors, wiring diagrams, schematics, and blueprints
- Trouble shoots, repairs, aligns, calibrates, inspects, and tests a variety of production systems and equipment
- Sets up assembly line equipment within established parameters
- Assists in installing new equipment and in moving equipment to new locations
- Disassembles machines and parts, and adjusts repairs or replaces defective parts and materials
- Uses a variety of basic hand and power tools and equipment including hand drill, bench grinder and band saw
- Instructs assemblers on proper use of equipment
- Cleans and lubricates parts and equipment as scheduled
- Removes and installs molds in machines following established procedures
- Learns all aspects of machine maintenance and becomes cross-trained in all areas of assembly equipment
- Requisitions parts needed for completion of preventive maintenance responsibilities
- Support all company safety and quality programs and initiatives
- High School Diploma/GED and 6 years of related experience or Associates Degree in related discipline and 4 years of related experience
- Requires a solid understanding of electronic circuitry and previous fabrication, assembly and/or test experience
- Solid knowledge of mechanical equipment and electrical and hydraulic drawings. Experience in mechanical and electrical troubleshooting, diagnosis and repair
- Ability to read and write English and interpret documents such as technical manuals, blueprints, safety rules, operating instructions and procedure manuals
- Knowledge and ability to use relevant hand tools in the repair of equipment
- H.S. diploma or GED
- Must pass pre-employment maintenance tests
- 2 years of maintenance experience in an industrial environment
Related Job Titles
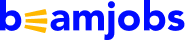
Build my resume

- Build a better resume in minutes
- Resume examples
- 2,000+ examples that work in 2024
- Resume templates
- 184 free templates for all levels
- Cover letters
- Cover letter generator
- It's like magic, we promise
- Cover letter examples
- Free downloads in Word & Docs
7 Maintenance Worker Resume Examples that Work in 2024
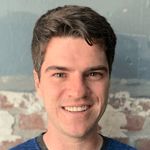
Maintenance Worker
Best for senior and mid-level candidates.
There’s plenty of room in our elegant resume template to add your professional experience while impressing recruiters with a sleek design.
Resume Builder
Like this template? Customize this resume and make it your own with the help of our Al-powered suggestions, accent colors, and modern fonts.
Maintenance Worker Resume
- Maintenance Resume by Experience
- Maintenance Resumes by Role
Maintenance workers are responsible for the upkeep of facilities across many industries. They’re skilled in a variety of areas, including plumbing, carpentry, and electrical systems, but all maintenance workers must be experienced with building inspections, maintaining inventory, and logistics of repairs.
With these wide-ranging duties, it’s tough to know what to include on your maintenance worker resume. Learning how to write a cover letter and how to make a resume is tricky enough, never mind having to check your resume for errors and tailor it to the job description every time you apply for a new job.
Never fear; we’ve analyzed tons of maintenance worker resume samples from all levels of experience to show you what works and what doesn’t to create a maintenance resume that gets more interviews in 2024!
or download as PDF
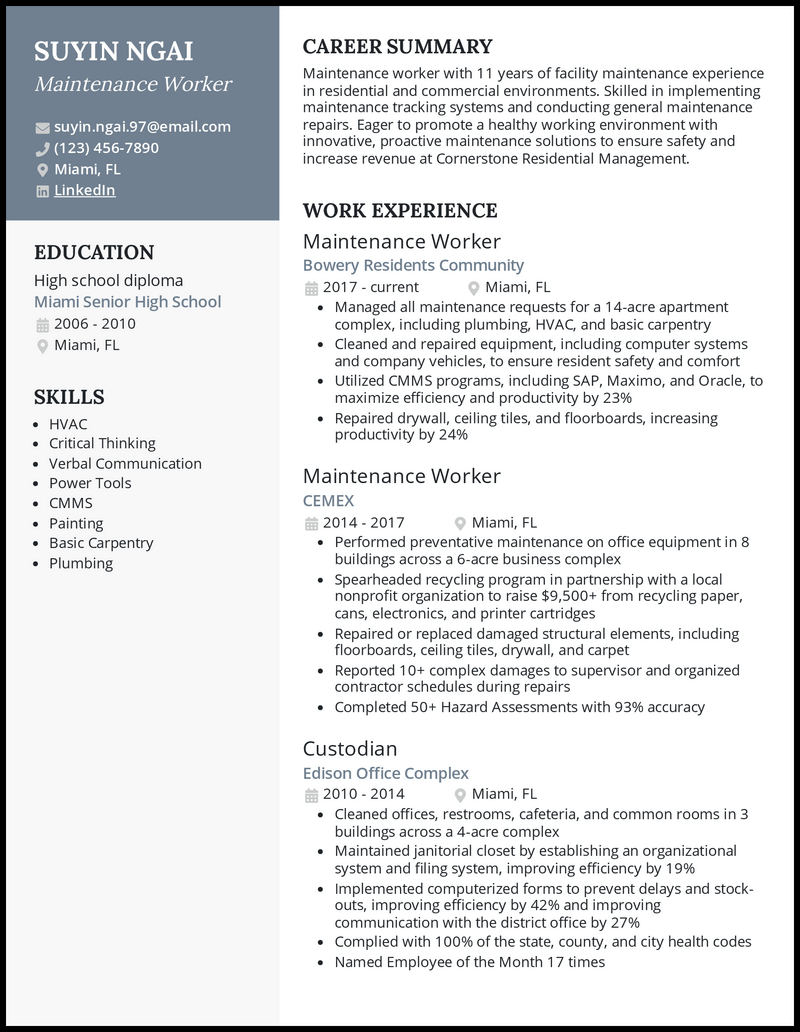
Why this resume works
- Want to emphasize your accomplishments? Include results-oriented data to demonstrate how you improved overall safety, customer satisfaction, efficiency, etc.
- Typos and grammatical errors are a natural part of the writing process, but don’t let them be the reason you don’t get hired— check your resume before submitting it to ensure everything is error-free.
Entry-Level Maintenance Worker Resume
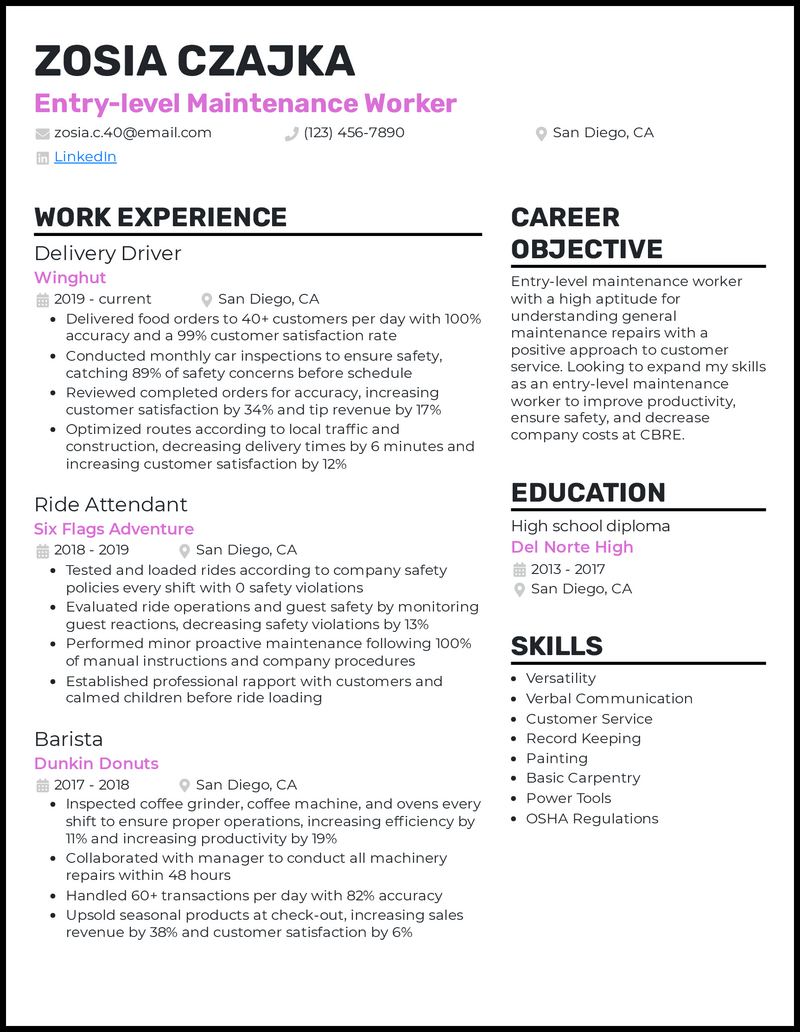
- Always show enthusiasm for the company in your objective, and mention how you want to help them once you’re hired.
- If you don’t have time to tailor your objective, don’t worry about it. Add more work experience instead.
- Did you repair machinery or follow procedural guidelines?
- Even if you haven’t done repair work, you can still mention versatile skills like collaboration, flexibility, and proactive communication.
Maintenance Supervisor Resume

- Let your piece speak of instances where you helped drive costs down through innovative ideas and adoption of frugal strategies to process and resource management.
Maintenance Technician Resume
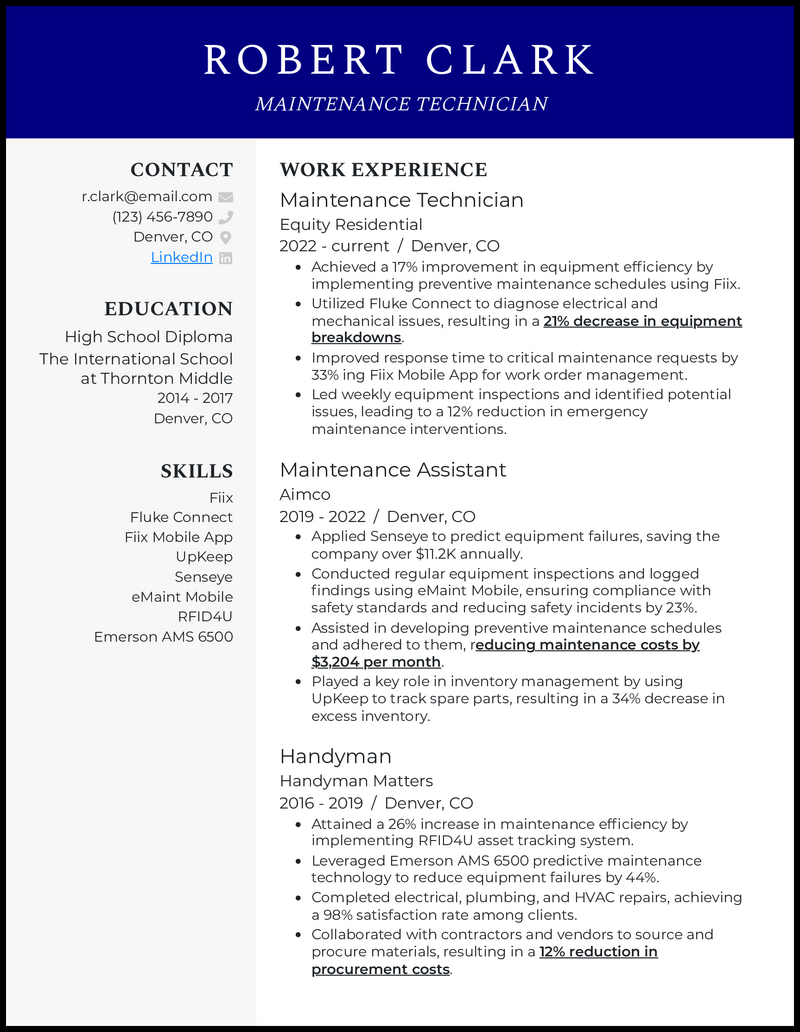
- You showcase your adept use of eMaint mobile app to track, predict, and conduct preventive maintenance to add that extra push for your application to succeed.
Industrial Maintenance Worker Resume
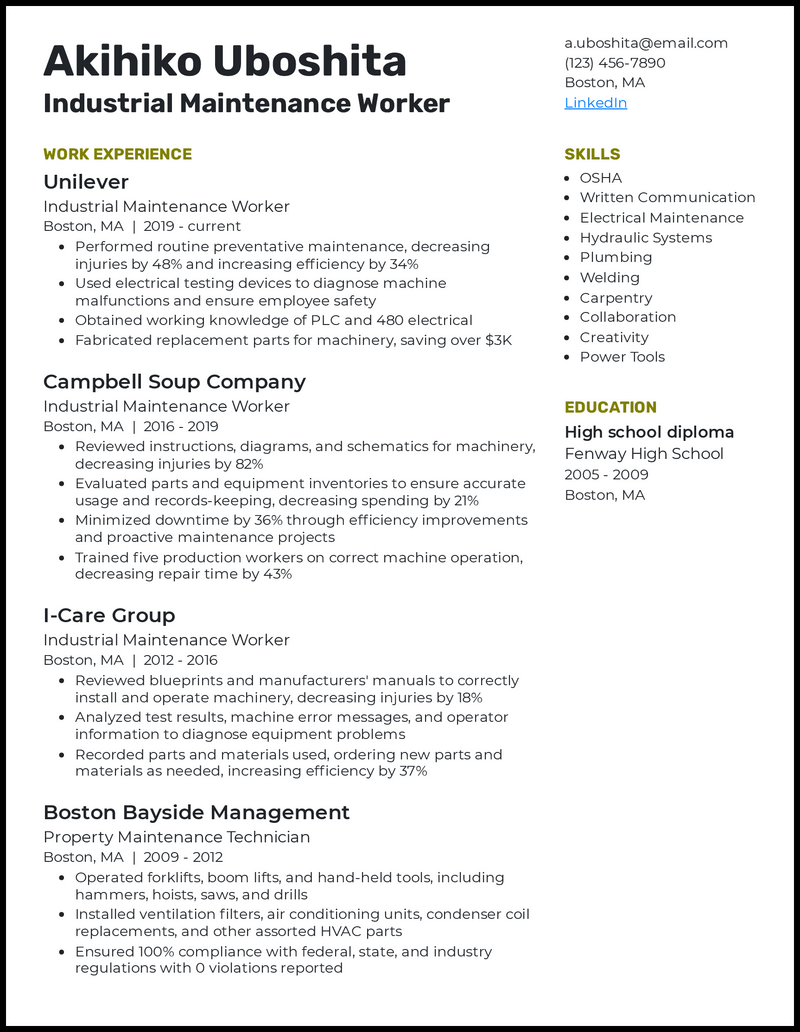
- Be sure to cite specific examples of how your work improved productivity, efficiency, or timeliness.
- Hiring managers are more apt to contact you for an interview if they see the job description’s requirements you met listed clearly on your resume.
Facility Maintenance Worker Resume
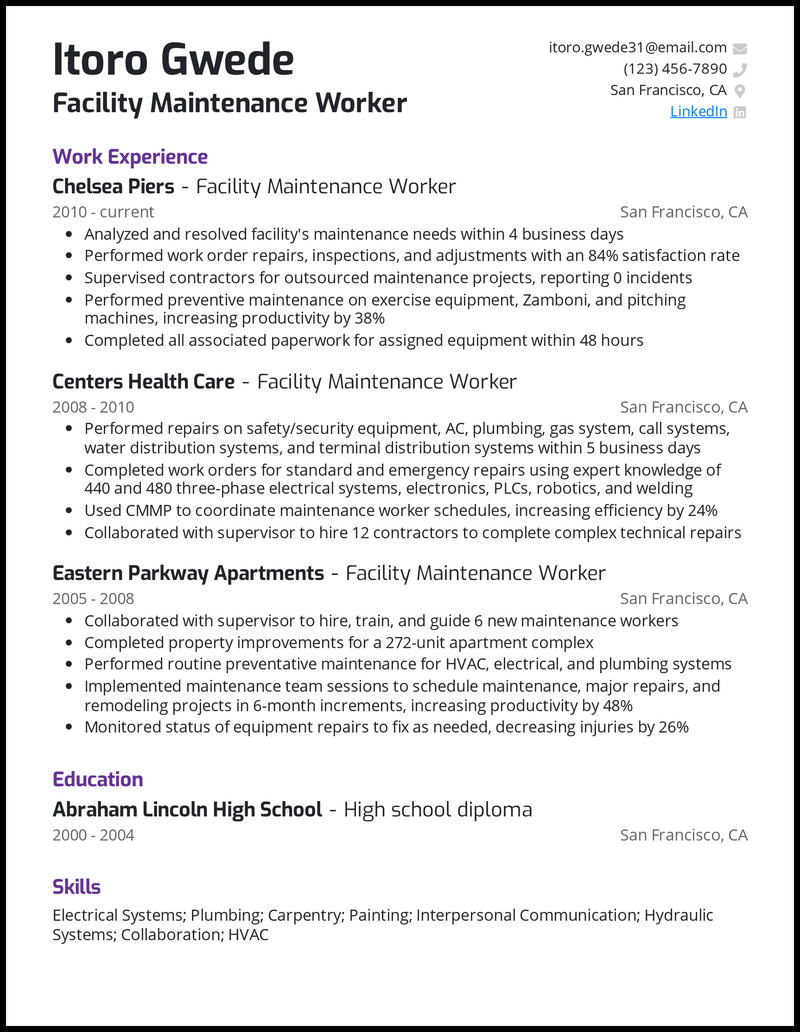
- Your facility maintenance worker resume should focus on specialty areas or special skills for a resume (i.e., electrical, HVAC, carpentry, plumbing), especially if they’re listed in the job description.
- For example, did you monitor repairs to ensure they were correct, thus limiting workplace injuries? Or did you coordinate projects to better match employee schedules, increasing efficiency?
School Maintenance Worker Resume
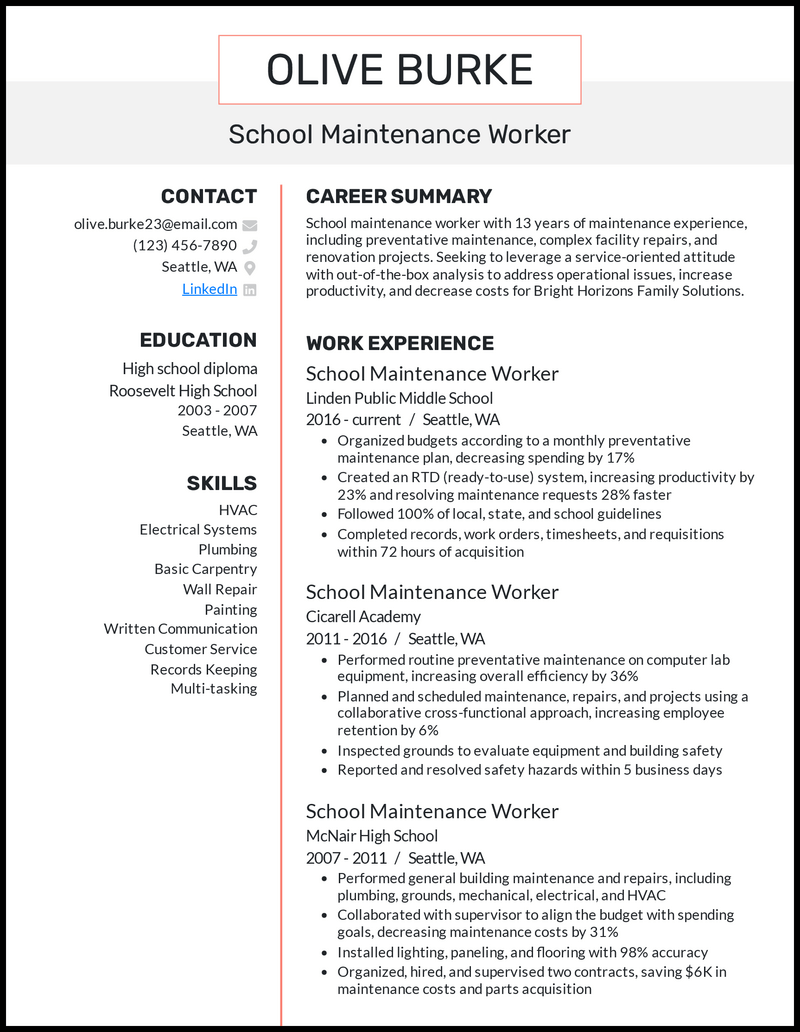
- Use a resume objective if you’ve recently changed positions or are new to the field. Use a resume summary if you have at least 10 years of experience in maintenance.
- No matter which one you choose, choose a professional resume template that allows you to add this option.
- Showing how you were involved in the school’s community is a guaranteed way to increase your chances of landing the job. For example, did you volunteer to help with any clubs or teams?
Related resume guides
- Auto Mechanic
- Construction Worker
- Electrician
Land your next job with our AI-powered, user-friendly tool.
Gut the guesswork in your job hunt. Upload your existing resume to check your score and make improvements. Build a resume with one of our eye-catching, recruiter-friendly templates.
• Work in real-time with immediate feedback and tips from our AI-powered experience. • Leverage thousands of pre-written, job-specific bullet points. • Edit your resume in-line like a Google Doc or let us walk you through each section at a time. • Enjoy peace of mind with our money-back guarantee and 5-star customer support.
Resume Checker Resume Builder
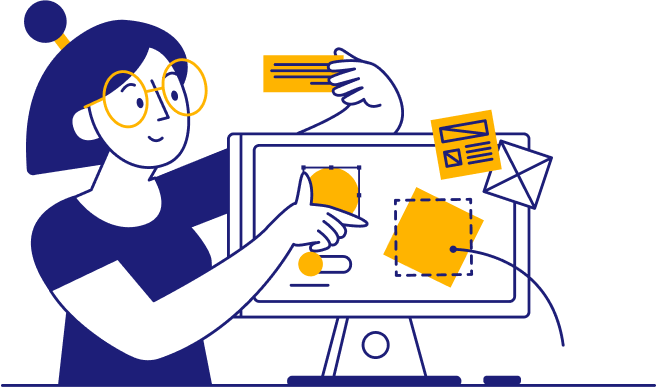
Samples › Maintenance Technician
Maintenance Technician Sample
Download and customize our resume template to land more interviews. Review our writing tips to learn everything you need to know for putting together the perfect resume.
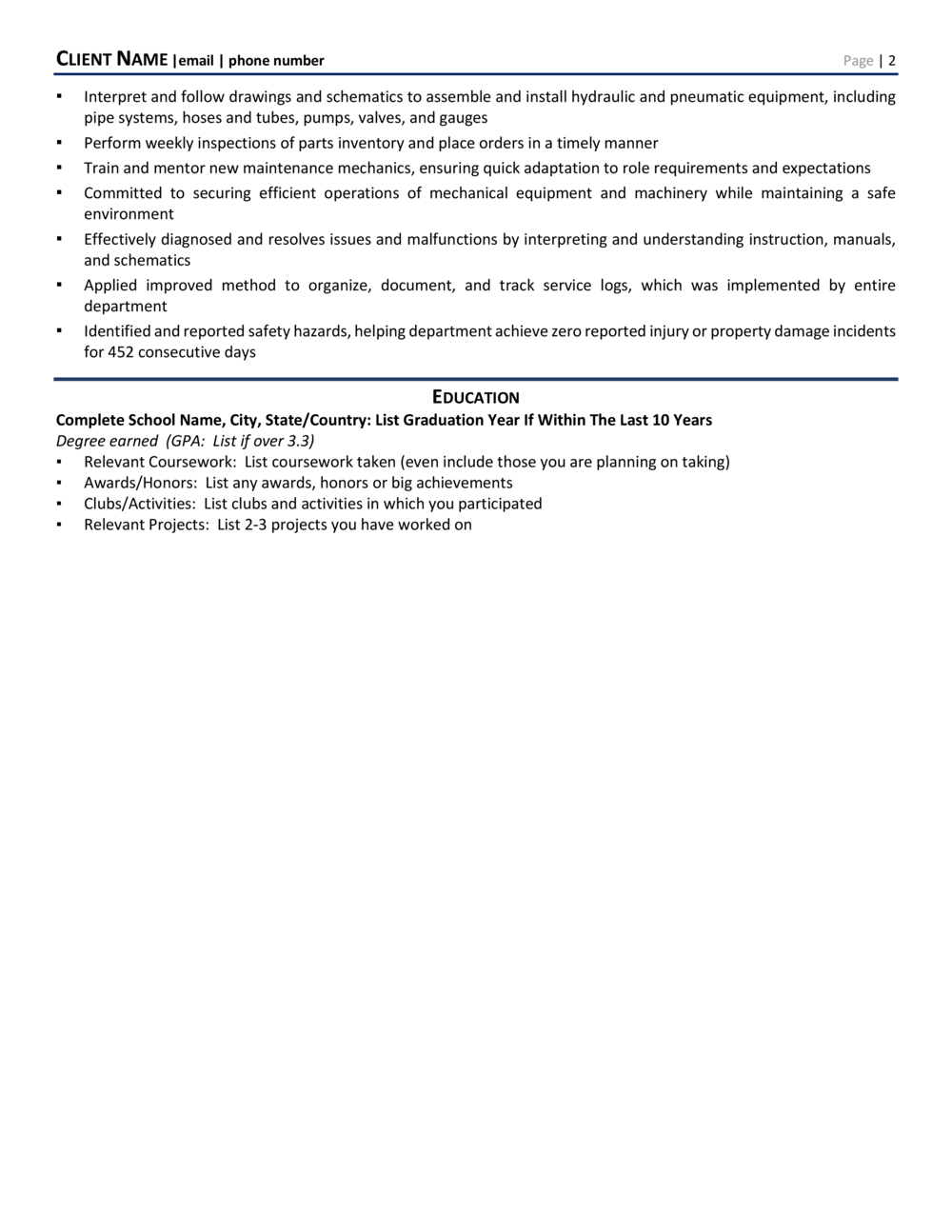
Not sure how to format your resume? Download our free guide and template .

In any industrial society, few roles are more challenging or vital than that of the Maintenance Technician. These technical professionals are tasked with regular maintenance of everything from plumbing and HVAC equipment to industrial machines that keep the economy’s engine running at full speed. As a result, technicians are typically skilled at repairing machines, have a keen eye for safety concerns, and understand the importance of collaborating as a team.
If that sounds like the type of career that fits your skill set, then having a resume that showcases your ability to succeed is a must. Just check out the resources, advice, writing tips, and Maintenance Technician resume example included below.
How to write a resume
Here are some tips to help you write your own job-winning Maintenance Technician resume, with an example resume to follow. After the heading at the top, you should always begin your resume with a summary section followed by core competencies and a solid work experience section. As for the look of your resume, use basic formatting with clear section headings and a traditional layout.
Let’s start with formatting your resume.
1. Formatting
It’s best to use a traditional reverse-chronological resume format for your resume. The reverse-chronological layout is the most commonly used and easily read by an employer’s Applicant Tracking System (ATS). In this layout, you’ll list your work experience with your most recent position listed first.
If you’re tempted to use a creative or more modern template because it’ll help you stand out from others, think again. Instead of helping you land an interview, a non-traditional format could cost you the interview. Most employers prefer a traditional layout since it’s familiar and easy to follow, and a traditional format also makes it easier to pass an ATS scan.
The standard sections for your resume include the heading with your contact information at the top followed by a resume summary. Other standard sections are Core Competencies, Work Experience, and Education, generally in that order.
A summary falls below the heading and summarizes the most impressive accomplishments and skills on your resume. The potential employer will quickly get a sense of whether you meet the minimum qualifications when you have a standout summary.
Summaries are brief and focused to grab the attention of the reader, enticing them to read more. Check out the Maintenance Technician resume example for more information.
3. Core competencies and skills
It’s good to list 10 to 15 of your core competencies below your summary and above your work history sections. When completing your core competency section, you want to list skills that also serve as keywords that align with the job description for two reasons. For one, these keywords can help you pass an ATS scan since they’ll be considered relevant to the job. Second, they’ll grab the attention of recruiters and hiring managers early on in the resume since they’re some of the competencies they’re seeking.
4. Work experience section
Your work experience section should make up the bulk of your Maintenance Technician resume. This section should include your relevant job titles, companies that employed you, and the dates you were employed.
While this section should include your relevant job titles, employers, and the dates you were employed, it should also highlight your accomplishments and key skills. For example, let's dissect two bullet points from the resume sample below:
Proposed plan and developed timeline to revise and reorganize standard operating procedures in compliance with industry regulations, increasing team efficiencies and reducing safety hazards
With this statement, the applicant showcases a commitment to safety and regulatory compliance, as well as a proactive approach to improving compliance. In addition, the example highlights creativity, organizational skills, and teamwork - important soft skills that employers are looking for.
Applied improved method to organize, document, and track service logs, which was implemented by entire department
This example reinforces the applicant’s innovative mindset, while describing the development of an improved system for documenting and managing repairs and maintenance. Moreover, they emphasize the achievement by noting that the changes were so efficient that they were adopted as the new standard by others at the company.
5. Education
Your education section includes your degrees and can also include your certifications and relevant training. If you have a college degree, forgo listing your high school diploma or GED.
Generally, your education is listed in reverse chronological order. The exception would be if you obtained a Master’s degree before receiving a second Bachelor’s degree. You always want to list your higher-level degrees first.
6. Optional Sections
Resumes can include other sections, like Awards, Volunteer Experience , or Technical Skills . Additional optional sections are certifications, publications, speaking engagements, and technical skills. The additional sections you might choose to include are based on your specific circumstances.
Maintenance Technician Resume example
How confident are you feeling about creating or updating your resume at this point? If you still need clarification, refer to the following Maintenance Technician resume example provided below. Feel free to use this template to create your own attention-grabbing resume.
City, State or Country if international
Phone | Email
LinkedIn URL
MAINTENANCE TECHNICIAN PROFESSIONAL
Analytically-driven Maintenance Mechanic with 13+ years of experience focusing on the intricacies of equipment and instrumentation. Highly adaptable and dedicated to producing error-free results, safe working conditions, and quality service.
CORE COMPETENCIES
Attention to Detail
Problem-Solving
Collaboration
Time Management
Written Documentation
Verbal Communication
Technical Proficiency
Analytical Skills
Adaptability
Troubleshooting Proficiency
Compliance & Safety
PROFESSIONAL EXPERIENCE
Maintenance Technician
Company, City, ST | Year-to-Year
Responsibilities
Routinely calibrate and perform preventative maintenance of laboratory and medical instrumentation and equipment
Proposed plan and developed timeline to revise and reorganize standard operating procedures in compliance with industry regulations, increasing team efficiencies and reducing safety hazards
Exercise critical-thinking skills when inspecting, troubleshooting, and diagnosing instrumentation and equipment
Maintenance Mechanic
Maintained, troubleshooted, and repaired equipment estimated at $200K+, including electrical circuits and high-pressure testing equipment
Professionally and promptly responded to maintenance repair requests, applying knowledge of machinery, tools, and process guidelines to identify root causes and resolve issues
Devised paperless system to maintain detailed data logs, enabling team to quickly reference integral information related to service calls
Responsible for inspecting and coordinating the tasks of subordinates and provide corrective actions as required
Assigned the tasks of checking that the repairing and maintenance work meets the established standard
Performed responsibilities of providing guidelines in electrical wiring and maintenance of machinery to staff
Skilled in the the care of machinery and auxiliary equipment for multiple departments
Instituted department-wide preventative maintenance schedule to maintain equipment efficiency and proactively identify potential issues
Interpret and follow drawings and schematics to assemble and install hydraulic and pneumatic equipment, including pipe systems, hoses and tubes, pumps, valves, and gauges
Perform weekly inspections of parts inventory and place orders in a timely manner
Train and mentor new maintenance mechanics, ensuring quick adaptation to role requirements and expectations
Committed to securing efficient operations of mechanical equipment and machinery while maintaining a safe environment
Effectively diagnosed and resolves issues and malfunctions by interpreting and understanding instruction, manuals, and schematics
Applied improved method to organize, document, and track service logs, which was implemented by entire department
Identified and reported safety hazards, helping department achieve zero reported injury or property damage incidents for 452 consecutive days
Complete School Name, City, St/Country: List Graduation Years If Within the Last Ten Years Complete Degree Name (Candidate) – Major (GPA: List if over 3.3)
Relevant Coursework: List coursework taken (even include those you are planning on taking)
Awards/Honors: List any awards, honors or big achievements
Clubs/Activities: List clubs and activities in which you participated
Relevant Projects: List 2-3 projects you have worked on
Key hard & soft skills for Maintenance Technician
Including key skills that align with the job throughout your resume is essential. You want to have not only the technical skills that show you know how to do the job but the skills that help you go above and beyond to succeed on the job, as well. In other words, you want to include a healthy mix of both hard and soft skills.
Below, we’ve included several examples of each that are common for Maintenance Technicians to emphasize.
Hard skills
Hard skills are the technical skills required to successfully complete a task or job. Unlike soft skills, hard skills are measurable. Here are some hard skills you might find on a Maintenance Technician resume:
General maintenance procedures
Technical proficiency with machines and equipment
Electrical and mechanical principles
OSHA safety and local regulations
Microsoft Office
Shop mathematics
Blueprint reading
Diagnostic testing
Soft skills
Soft skills are challenging to measure, though they’re important to succeed in most jobs. Some common soft skills for a Maintenance Technician include:
Ability to prioritize
Communication
Compliance and Safety
Critical thinking
Summary & last words
Standout resumes will include a resume summary, a traditional reverse-chronological layout, and the skills and experience relevant to your job target. This resume example shows how to incorporate those elements on a page. It’s up to you to insert your personal compelling qualifications.
Keep your resume format easy to scan by both humans and computers; our resume template is designed by our experts to satisfy both audiences. And be sure to include your own skills, achievements, and experiences. Job-winning resumes are those that successfully market you, leading recruiters and hiring managers to want to learn more!
Finally, emphasize your interest with a customized cover letter. When writing, remember that the resume and cover letter should support each other. Check out our cover letter tips and examples for more advice.
Still wondering if you have what it takes to write a stellar resume? Hire a professional resume writer to get the advice you need to land your next job, as outlined below.
Introduction to ZipJob: Professional Resume Writers
If writing and talking yourself up aren’t your most favorite things to do, you’re in luck. Why? Because you have access to a team of professional resume writers to support you in writing your resume to help you stand out in the best light possible. Collaborating with ZipJob writers means you have experts to help you create a resume to boost your confidence and land interviews with your Maintenance Technician resume.
Why You Should Make Use of Our Resume Writing Services to Land Your Next Job as Maintenance Technician
You know you’re great at putting things back together, fixing broken equipment, and using software to support a variety of maintenance needs, but when it comes to writing your Maintenance Technician resume, you might cringe at the thought. Fortunately, the ZipJob team of resume writers can do the heavy lifting for you in this area. We’ll ensure you have a resume that you can be proud of - a resume that lands you interview after interview and, from there, a job!
Resume Writing Service for Maintenance Technician: Let us write your resume
At ZipJobs, we have writers with expertise across hundreds of industries and have written thousands of resumes for candidates in numerous fields, including those in the Maintenance Technician field. Our resume writing service will put your mind at ease when it comes to passing a prospective employer’s Applicant Tracking System so it lands in the hands of a hiring manager. From there, they’ll see your outstanding skills and a work history that sets you apart and proves you have what it takes to succeed on the job. You can trust our team of writers to support your success with your next career move!
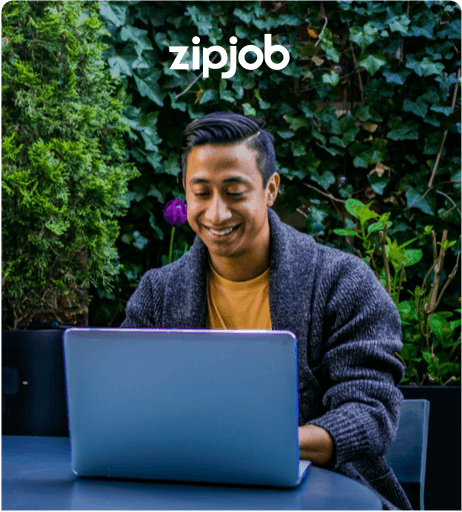
Our resume services get results.
We’ve helped change over 30,000 careers.
PROTECT YOUR DATA
This site uses cookies and related technologies for site operation, and analytics as described in our Privacy Policy. You may choose to consent to our use of these technologies, reject non-essential technologies, or further manage your preferences.

IMAGES
VIDEO
COMMENTS
Here's a maintenance technician resume template to help you create your own: ... Tips and Examples of 3 Common Resumes 2. Review the job description Review the maintenance technician job listing and highlight key terms that show what the employer is seeking in candidates. On your resume, use the same words and phrases to help your resume pass ...
You can complete your entire resume in 15 minutes! 1. Enter the details about the job title you held. The builder comes preloaded with auto-suggested phrasing written by resume experts. 2. Then, just pick from these suggested phrases that best frame your experience and customize them to your liking! 3.
These maintenance technician resume examples show how: Maintenance Technician Job Description for a Resume Good Example. Maintenance Technician. Bargill, Miami, FL. Oct 2018-present. Conducted quarterly inventory audits of furniture, supplies, materials, and equipment. Oversaw onsite safety compliance and reduced overall annual incidents by ...
Aerospace technician specialist responsible for ensuring management of all processes within the $339 million F-22 Raptor program is maintained to the most rigorous standards. Additional responsibilities include performing scheduled inspections, functional checks and preventive maintenance on tactical aircraft and aircraft-installed equipment.
Resume Builder offers free, HR-approved resume templates to help you create a professional resume in minutes. Start Building. 1. Summarize your maintenance technician qualifications in a dynamic profile. Your professional profile should set the tone for your resume and entice the hiring manager to read further.
ZAIN BLACKWELL. Danvers, MA 01923. (555) 555-5555. [email protected]. Professional Summary. Talented maintenance technician with experience in general maintenance and repair of building equipment including plumbing, heating/cooling and electrical systems. Committed to thorough repairs and accurate supply inventory.
Maintenance Technician Summary 1. " Service-oriented expert with 11 years of experience seeking to use knowledge of electrical systems as a general maintenance technician at DDC company. Also, seeking to build on the experience in HVAC installation and repairs as a general maintenance technician at DDC company.
Put your job title, dates worked, name of the company you worked for, and the city and state where your job was located. Document your maintenance job responsibilities and technician duties in 5 or 6 bullet points. Use an action word (e.g., fixed, troubleshooted, etc.) to start each of those bullet point entries.
Maintenance technicians there earn an average of $52,913, according to Zippia.com. Wisconsin ($45,525), Iowa ($42,699), Kentucky ($42,039) and Minnesota ($45,248). Industrial machinery mechanics, machinery maintenance workers and millwrights earn almost $10,000 a year more, at $54,920 per year, the U.S. Bureau of Labor Statistics (BLS) reports ...
Maintenance Job Description for a Resume Good Example. Maintenance Technician. Macasa, Tampa, FL. Sept 2019-present. Installed and maintained HVAC equipment worth over $100,000. Repaired and maintained production equipment in accordance with vendor specifications, saving the company $10,200 p.a. in specialist contractor fees.
As a maintenance technician, your job is to ensure that equipment, machinery, and facilities are functioning properly. However, before you can even begin to showcase your skills, you need a winning resume to catch the attention of potential employers. Overview of Maintenance Technician Resume A maintenance technician resume is a document that showcases your relevant skills, experience, and ...
Template 1 of 4: Maintenance Technician Resume Example. A maintenance technician is an in-house employee that is responsible for repairs and maintenance in a particular facility. They inspect the building's electrical systems, HVAC, and structure to see if there's a need for troubleshooting or restoration.
If the maintenance technician resume isn't the right one for you, take a look at other related guides we have: Custodian Resume Example. Electronic Technician Resume Example. Handyman Resume Example. Cleaning Manager Resume Example. Facilities Manager Resume Example. Cable Technician Resume Example. Regional Property Manager Resume Example.
For example, suppose the job description for the maintenance technician role you seek asks for strong electrical and plumbing skills and experience with building management. In that case, you'll want to use those exact words in your maintenance technician resume. Look for opportunities in your professional summary, skills section and work ...
Maintenance Technician Resume Examples & Samples. At least 5 years experience in the maintenance of a Distribution center. Must have conveyor maintenance and repair experience including Shoe sorters and Tilt tray sorters. Must have electrical experience with Direct current and Alternating current up to 480 volts.
Perform maintenance of electrical systems (replace light bulbs and sockets, clean and repair circuit breaker panels etc.) Assist in the setup of ventilation, refrigeration and other systems and conduct repairs when necessary. Maintain heating and plumbing systems to ensure functionality. Inspect alarm systems (fire, protection) and schedule ...
Why this resume works. Your facility maintenance worker resume should focus on specialty areas or special skills for a resume (i.e., electrical, HVAC, carpentry, plumbing), especially if they're listed in the job description.; Don't just say you completed a task; include the results of your responsibilities to demonstrate how you made a significant impact at your workplace.
Here are some tips to help you write your own job-winning Maintenance Technician resume, with an example resume to follow. After the heading at the top, you should always begin your resume with a summary section followed by core competencies and a solid work experience section. As for the look of your resume, use basic formatting with clear ...
The average salary for these jobs is approximately $35,000 annually or about $17-20 per hour. Construct your general maintenance technician resume with MyPerfectResume's Resume Builder. Individuals with solid training or previous experience tend to have the best prospects since many employers in this field tend to prefer someone who can be a ...
Sample Job Duties for Maintenance Technician Resume • Chart out and implement general and preventative maintenance tasks on buildings and grounds • Handle installation, repairs, plumbing, and electrical issues • Respond to maintenance requests put forward by residents or staff in terms of electrical, heating, and plumbing needs
Enrico L. Salvador. Address: 5478 E 8th Street, Boyle Heights, Los Angeles, CA. Phone: (213) 998 3632 Email: [email protected] Current Job: Maintenance Technician; Pueblo del Sol Apartments, Boyle Heights, Los Angeles, CA.. Objective. More than 5 years experience as Maintenance Technician with an Associate Degree in Industrial Maintenance seeks work as Senior Maintenance Technician for Boyle ...
What are maintenance technician certifications? Maintenance technician certifications are professional credentials granted by accredited institutions that validate a technician's competence in different aspects of maintenance, including troubleshooting, repair and preventive maintenance. These programs aim to ensure that technicians are up-to-date with the latest industry standards and ...