This site uses cookies to improve your experience. By viewing our content, you are accepting the use of cookies. To help us insure we adhere to various privacy regulations, please select your country/region of residence. If you do not select a country we will assume you are from the United States. View our privacy policy and terms of use.
- Inventory Management Software
- Forecasting
- Sustainability
- Supply Chain Visibility


AI in the Retail Industry: Benefits, Case Studies & Examples
MARCH 27, 2024
Other Examples of AI in the Retail Industry AI in the retail industry is helping improve customer experiences on one hand and operational workflows on the other. The post AI in the Retail Industry: Benefits, Case Studies & Examples appeared first on ThroughPut. The result was significant: savings of €3-6.5

L’Oréal: A Case Study in Supply Chain Excellence
Supply Chain Shaman
OCTOBER 5, 2018
to This is an example of managing a balanced portfolio and of driving a supply chain revolution. This case study is the best example we have seen of a customer-centric supply chain. In China, for example , more than 40% of the company’s business through eCommerce. L’Oréal’s Performance Compared to the Peer Group.
This site is protected by reCAPTCHA and the Google Privacy Policy and Terms of Service apply.
- Scaling Logistics for Success: A White Claw Story
MORE WEBINARS
Trending Sources
Talking Logistics
- The Logistics of Logistics
- Enterra Insights
Logistics Viewpoints
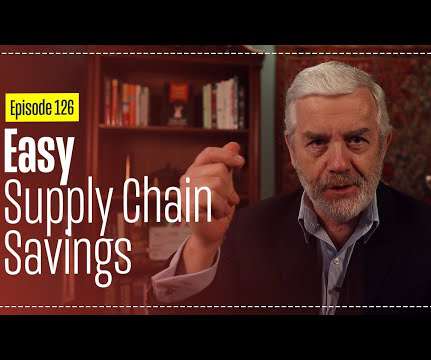
Easy Supply Chain Savings: A Simple Supply Chain Case Study
Logistics Bureau
AUGUST 31, 2021
Supply Chain & Logistics case studies are always interesting. Maybe you have some similar examples you can share in the comments? Check out this article related to this topic: 7 Mini Case Studies : Successful Supply Chain Cost Reduction and Management. And it was an easy problem to fix!
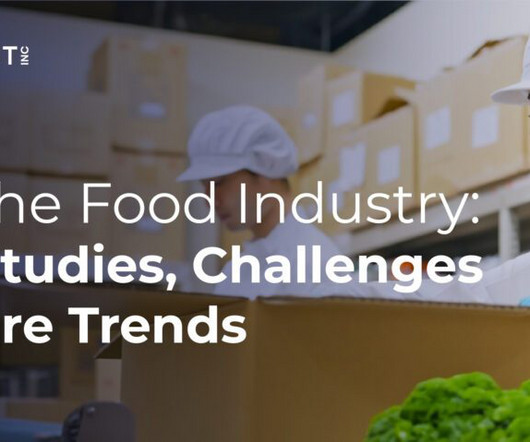
AI in the Food Industry: Case Studies, Challenges & Future Trends
MARCH 28, 2024
Case Studies of Successful AI Integration in Food Supply Chain Church Brothers Farms Church Brothers Farms, a family-owned vegetable business with a vast cultivation area of 40,000 acres, faced significant challenges due to product perishability, volatile market conditions and logistical issues, among others.
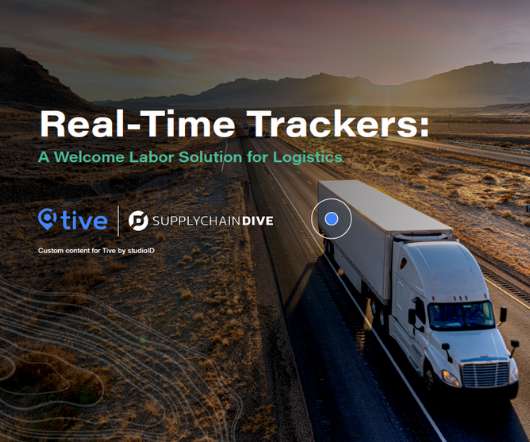
Real-Time Trackers: A Welcome Labor Solution for Logistics
Advertisement
Real-life case study examples of how real-time tracking helped two leading logistics providers overcome the challenges of the growing labor shortage. Why streamlining data simplifies the logistics role. The difference between real-time data tracking vs. passive data logging, and why the former is key to efficient operations.
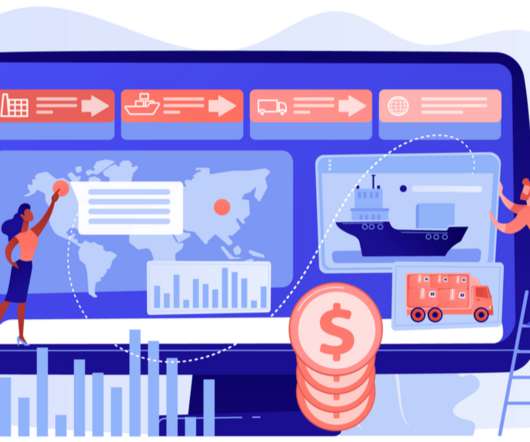
Supply Chain – Finance Connection: A Supply Chain Improvement Case Study
APRIL 27, 2021
Supply Chain – Finance Connection: A Supply Chain Improvement Case Study was first posted on April 27, 2021 at 7:57 am. This is a different approach to begin the journey of financial improvement using supply chain improvement projects.
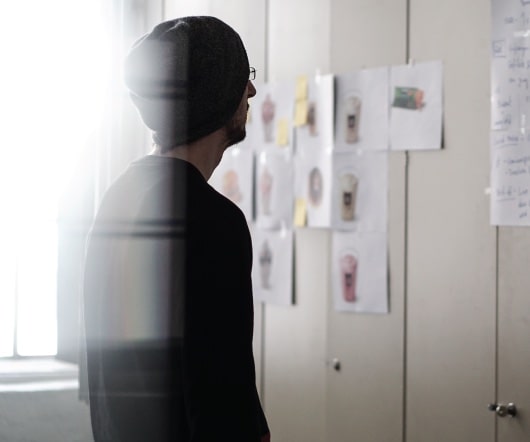
Supply Chain Case Study: the Executive's Guide
Supply Chain Opz
JUNE 1, 2014
Analysis of case study is certainly one of the most popular methods for people from business management background. In order to accelerate the learning, this article has gathered 20+ most sought-after supply chain case studies , analyzed/categorized them by industry and the findings are presented.
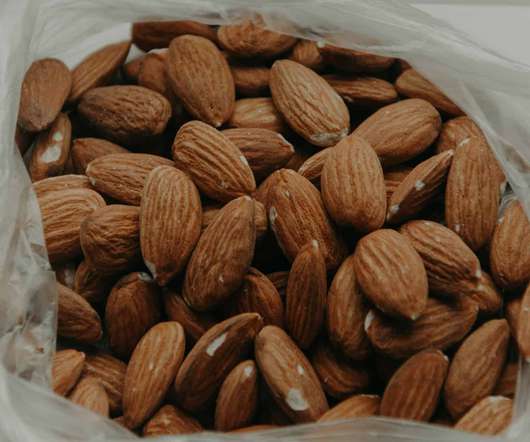
Alternative Protein: A Food Manufacturers Guide [+ Case Study]
AUGUST 12, 2021
How food manufacturers are taking advantage of the alternative protein trend: A case study One recently launched New Zealand company, Food Nation , is proving a winner in the alternative protein space. French company Ynsect, for example , farms mealworms to produce food products for humans and animals.
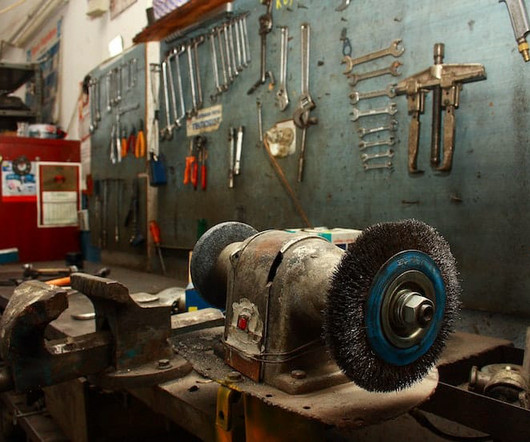
Machine Learning in Supply Chain: Definition, Uses, Case Studies
APRIL 4, 2023
We also break down several case studies of companies currently using machine learning in their supply chain processes. For example , if your customers buy large quantities of a certain product, machine learning software will be able to identify the surge in demand and feed the information back to the inventory management systems.
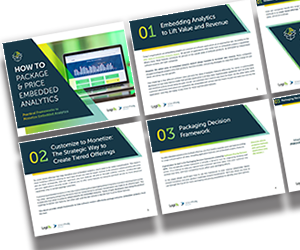
How to Package and Price Embedded Analytics
Just by embedding analytics, application owners can charge 24% more for their product. How much value could you add? This framework explains how application enhancements can extend your product offerings. Brought to you by Logi Analytics.

BASF Video Case Study: The Value of Real-Time Freight Visibility
MAY 3, 2018
In addition to improved customer satisfaction, Wehrle shared these examples : The data we’re getting has been hugely successful. The post BASF Video Case Study : The Value of Real-Time Freight Visibility appeared first on Talking Logistics with Adrian Gonzalez. Benefits of Real-Time Freight Visibility.
TMS for SMB: A Case Study with Carhartt
OCTOBER 19, 2016
Carhartt is a great example . At the end of the day, the best approach is making the effort to truly understand and address the unique needs and characteristics of every company — both today and where they’re aiming to be in the future. Gibson highlighted in her presentation, Carharrt is experiencing rapid growth.
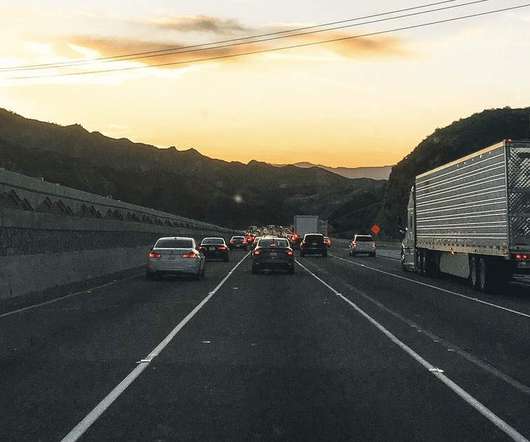
Cross Docking 101: What, Why and How? [with case studies]
SEPTEMBER 23, 2021
Time to deliver goods Cross docking can add additional time to the delivery process compared to, for example , a direct shipment strategy that involves the direct transfer to the end customer. Three case studies Cross docking strategies are used around the world and across different industries. Who uses cross docking?
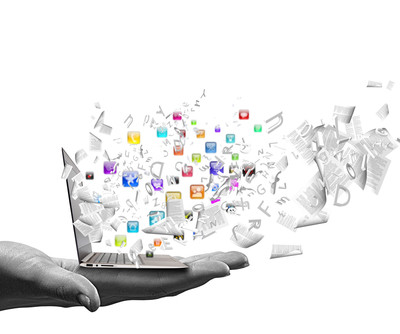
Trying to Push Content Above the Noise
JANUARY 2, 2024
Many discussions focus on driving improvement through planning, yet, when I take the client case studies on the websites of leading planning technologies and map the intersection of operating margin and inventory turns, I do not see metric improvement, sustained performance, or an increase in value. It is just accepted.
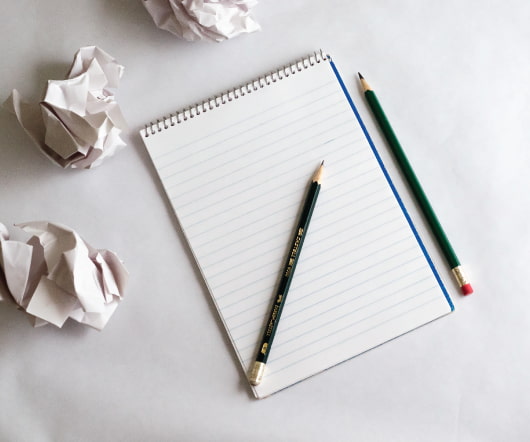
Redesign to Improve Value: A Case Study of a Supply Chain Leader
JUNE 21, 2014
For example , we discovered that transportation and duties are 5x the expense of labor and overhead. For example , people want prestige beauty from the US, Europe or Japan. Take another example – few people know where their TV was made, but the buyer cares greatly about the reliability of that product. It wasn’t that easy.
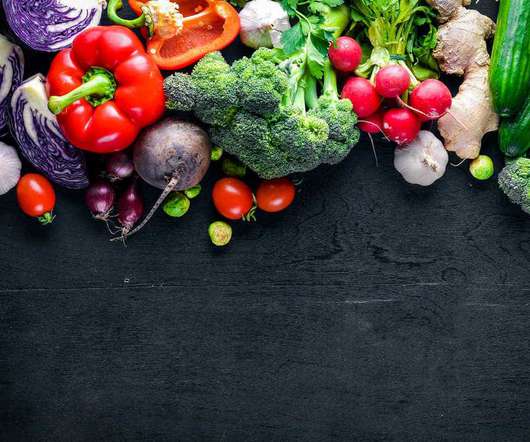
How Food Manufacturing Software Drives Profit [w Case Studies]
AUGUST 11, 2020
For example Stock Age by Stock Keeping Unit (SKU) can be cross-referenced with warehouse location to see which ingredients are sitting on the shelf and need to be moved (perhaps with a local promotion or price change). CASE STUDY 1: Gourmet Organic Herbs. CASE STUDY 2: Brandini Toffee.
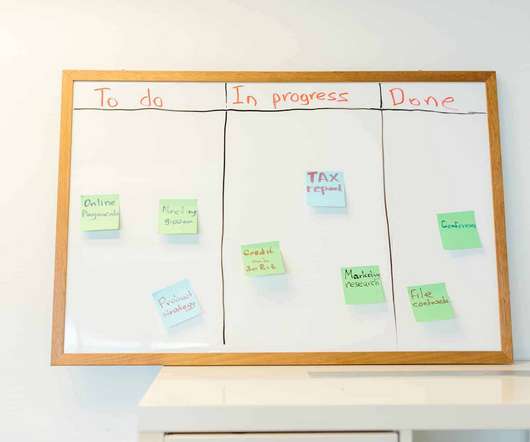
8 Examples of Kanban in Lean Manufacturing
MARCH 2, 2022
Here we give you eight real-world examples of how businesses use Kanban, a popular lean tool that’s helped companies in a huge range of sectors improve efficiency – especially those in the manufacturing industry. If you already know what Kanban is and just want the case studies , scroll down! Software development is an example .
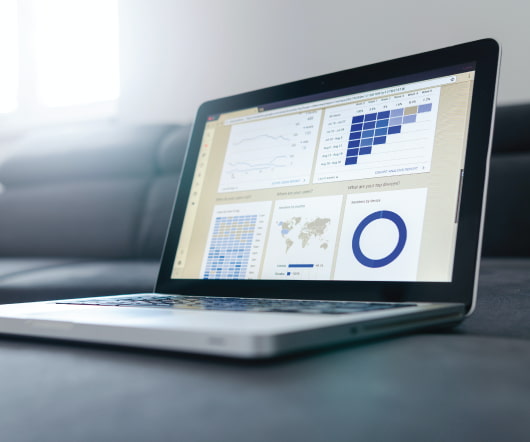
Client Case Study Video Interview
APRIL 19, 2019
Client Case Study Video Interview with Lucid Motors, Menlo Park, CA. For example , certain areas were not quite to our liking and some of the formatting we wanted to change and you were quick to do that and it made our senior management very happy. Q: Can you give me one example of how the system has saved you time and effort ?
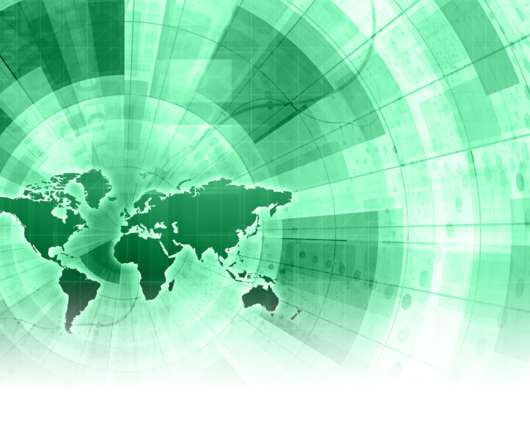
The Green Corridor: Saving Whales in California – A Case Study in Regional Collaboration
The Logistics & Supply Chain Management Society
AUGUST 19, 2022
The Green Corridor: Saving Whales in California – A Case Study in Regional Collaboration. This story is a great example of how, collaboration can happen in our fractured and decentralized commercial environment. The Green Corridor: Saving Whales in California – A Case Study in Regional Collaboration.
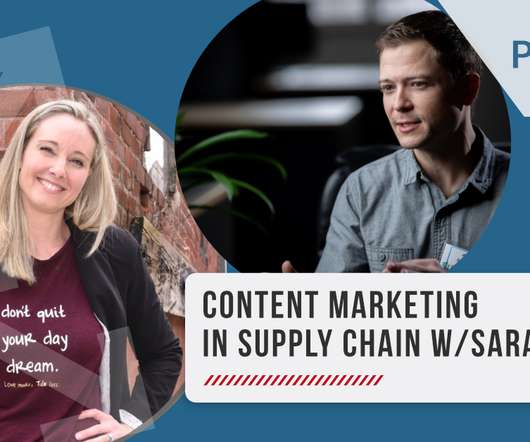
[PODCAST] The Growing “Influence” of Content Marketing in the Supply Chain
GlobalTranz
MARCH 3, 2020
Business and Marketing Resources Marketing Logistics Services: A Discussion on Getting Attention Online Listen to the Podcast Example of an Effective Transportation Management Case Study View Case Study How Industrial Companies Can Pivot to Inbound Organizations & Increase Customer Experience Listen.read More.
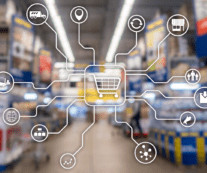
Understanding the Profitability of Omnichannel Retail is a Problem
NOVEMBER 20, 2023
But one thing you notice as you go to omnichannel software vendor’s web sites and examine customer case studies , the case studies may talk about retailers growing their revenues by 100% or more, but none talk about how much profitability grew. These new order fulfillment paths allowed retailers to rapidly grow sales.
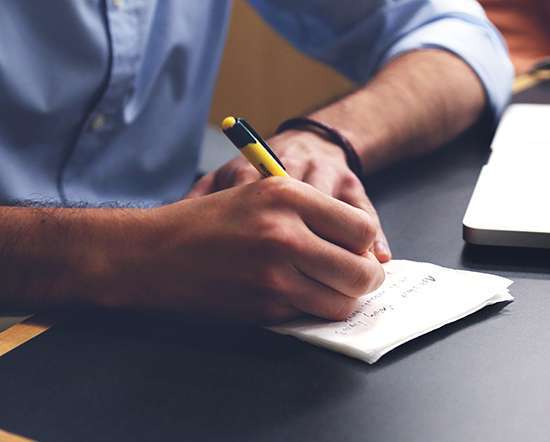
Surgery Center Case Study: Less Time at Computer, More Time in OR
FEBRUARY 6, 2019
We now know, on a real-time basis, whether a contract has expired, for example . The post Surgery Center Case Study : Less Time at Computer, More Time in OR appeared first on Hybrent. In addition, Hybrent ensures we’re staying in compliance on contracts. Ready to Update Your Supply Chain? Request a Demo.
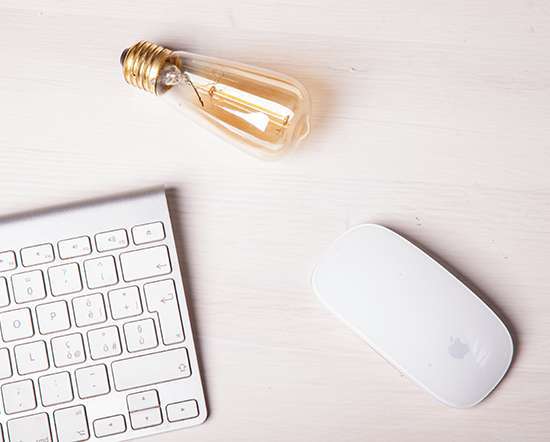
Examples of How Supplier Quality Management System Implementations Pay Off
JUNE 11, 2015
We conclude our series on supplier quality management (SQM) today with a look at some case studies and examples of benefits derived from the application of a supplier quality management system. Examples and Case Studies from the Implementation of a Supplier Quality Management System.
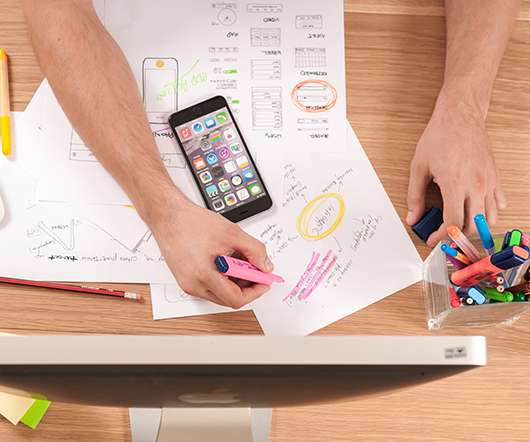
A Case Study in Reverse Logistics Optimization!
Supply Chain Game Changer
NOVEMBER 23, 2018
“This has been an excellent example of how ModusLink can deliver measurable value for our computing and hardware clients,“ explains ModusLink’s Vice President of Global Client Development. The post A Case Study in Reverse Logistics Optimization! Learn more at [link]. Check out Reverse Logistics and the Power of Your 3PL!
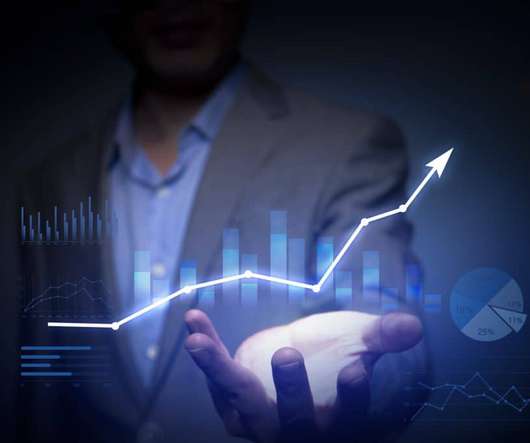
JAGGAER Webinar with Accenture Strategy and Attijariwafa Bank Case Study: Accelerating Trust in Banking – Internal, Suppliers and Customers
OCTOBER 22, 2020
A case study presentation by Youness Taghrichte provided a good example of how JAGGAER customers in the financial services sector are tackling these issues. Attijariwafa Bank has successfully implemented a source-to-contract solution with the JAGGAER ONE platform.
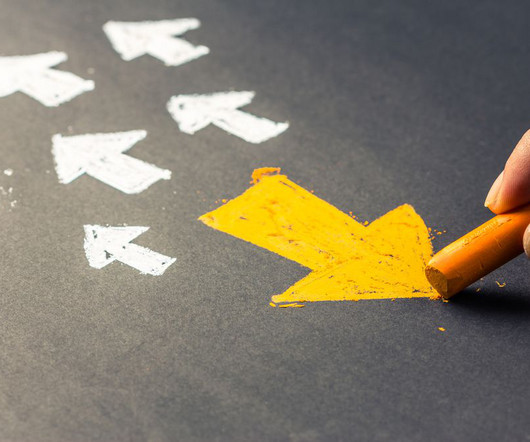
Elevating The Voice of the Supply Chain Contrarian
JUNE 21, 2023
Many of the case studies being presented at today’s conferences were born during the pandemic and the post-pandemic turbulence. For example , Monster Beverages beats Coca-Cola and PepsiCo, while Celanese outperforms Dow Chemical. While companies talk digital, the projects follow traditional supply-centric paths.

Melitta: Collaborating for an Improved Forecasting Process
NOVEMBER 2, 2020
For example , within an audit workflow multiple stakeholders across various regions can apply detailed market knowledge specific to their regions to the demand baseline forecast for a more accurate result. Read the full Melitta case study below. Read Case Study . Michael Youssef.
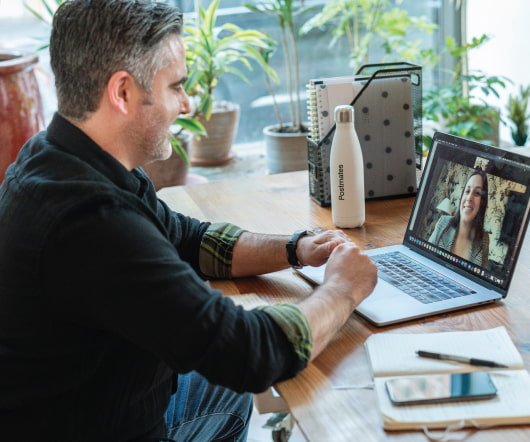
Tackling Item Complexity
JANUARY 9, 2019
In Figure 1, I share a case study from a client engagement. One of the most read case studies written for my first book, Bricks Matter, is a case study on managing item complexity. It is frequently requested, so I wanted to reshare this case study with my readers. Governance.

New Case Study on Alcatel-Lucent Sustainable Procurement Best Practices
JULY 9, 2015
Case Study . We are pleased to publish a new case study detailing Alcatel-Lucent’s sustainable procurement program. Download the Case Study from the library. Long-time EcoVadis client, Alcatel-Lucent, has done all this and more.
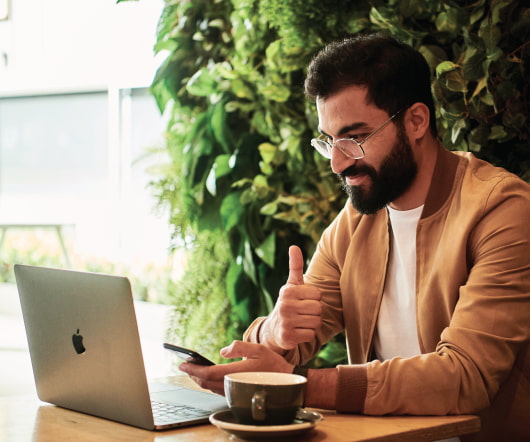
Unlocking the Value of Global Supply Chain: the Case Studies
JULY 7, 2014
For example , they make it easier for customers to locate products during shopping, pick the products, checkout, bringing products back home and install the furniture. Their unique selling points are products with good design at lower prices. To drive cost down, Ikea shifts some of their activities to customers or self service operating model.
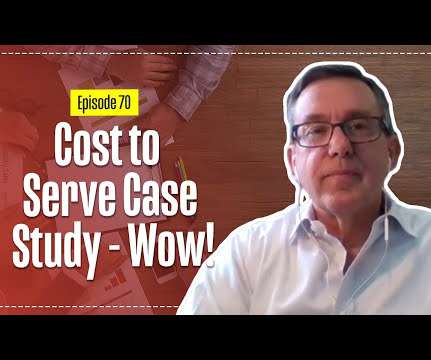
Cost to Serve Case Study that was Off the Scale! – with Steven Thacker
JULY 21, 2020
A Great Example . Let us watch the video below: Related articles on this topic have appeared throughout our websites, why not check them out? Robobyrne: Cost To Serve Lesson. Supply Chain Secrets: What is Cost to Serve? – Best Regards, Rob O’Byrne. Email: [email protected]. Phone: +61 417 417 307.
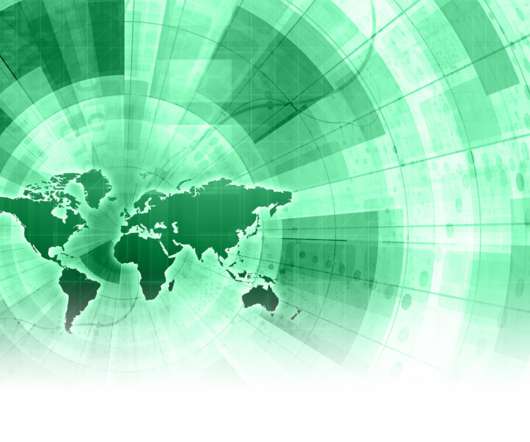
The Green Corridor: To Realise the Circular Economy Dream – Reach Out to Your Community
NOVEMBER 22, 2022
In one example , Crust Group in Singapore provides a Southeast Asian example of a cross industry “circular economy” partnership. In my compost example , I save on buying fertilizer (along with all the processing, packaging and transportation associated with it). This is the challenge that industries face all around the world.
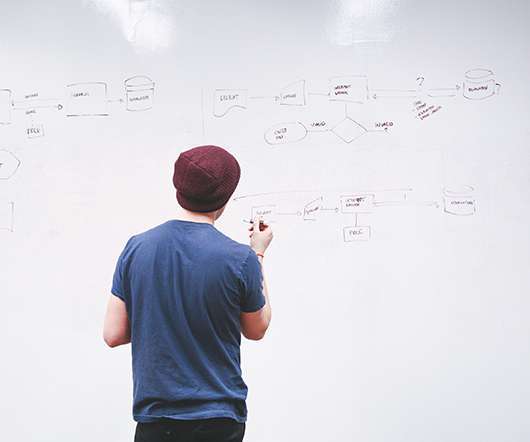
Case Study: How Generac Power Systems Cut Millions from Its Global Transportation Spend
CH Robinson Transportfolio
MARCH 28, 2018
For example , Generac works with our global forwarding and port services experts to optimize containerized freight moving from the West Coast to Chicago and beyond. The post Case Study : How Generac Power Systems Cut Millions from Its Global Transportation Spend appeared first on Transportfolio.
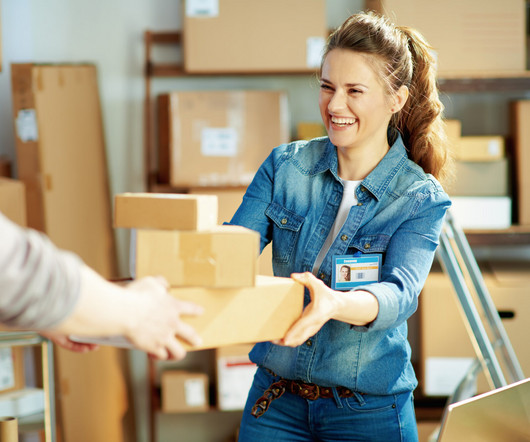
Dynamic Fulfillment 101: Achieving Multiple Objectives for Better Margins
OCTOBER 17, 2023
Plus, you’ll get to check out real-world examples of major retailers who leverage this technology every day – for good reason. In the example below, you can see three different fulfillment options for an order, each with its own ship cost, labor cost, and expected revenue. Real-World Examples Looking for a feel-good fulfillment story?
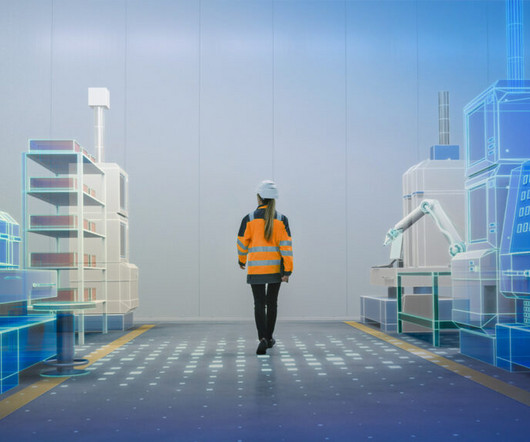
Achieving the Value of Digital Twins
DELMIA Quintiq
JUNE 5, 2023
While the promise is clear, and we see a growing number of case studies proving the benefits of the approach, many companies struggle to create and maintain digital twins. I encourage you to listen to the webinar replay to hear more about these examples . So, are they achievable, from a practical perspective?
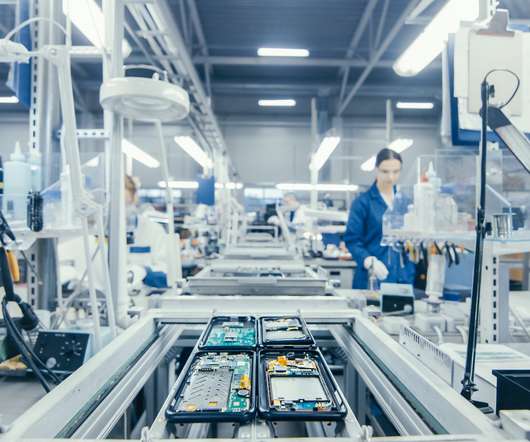
Optimization and Execution: How Manufacturing can lead the Industry Renaissance
JUNE 9, 2020
Companies that were unable to meet these challenges have been left behind (for example , in High Tech think Blackberry and Compaq). In numerous case studies , manufacturers have found that the limited visibility to shop floor activities and poor planning led to problems with over-scheduled machinery and equipment.
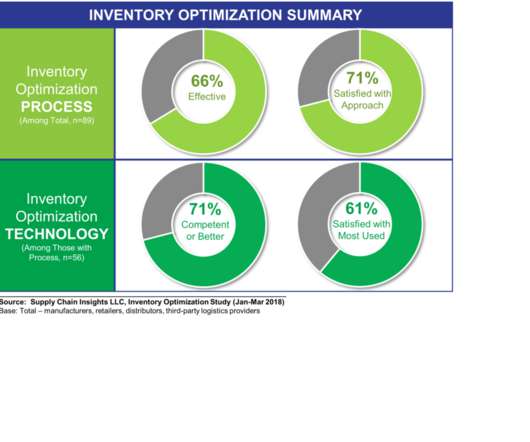
Strong Supply Chains Required For an Economic Rebound: Six Steps To Take
APRIL 15, 2020
No doubt about it, we are characters in a supply chain case study searching to define a new normal. Today, we find ourselves in the middle of a risk management case study . An example is a focus on moving and buying ventilators without an assessment of the availability of critical parts and skilled therapists.
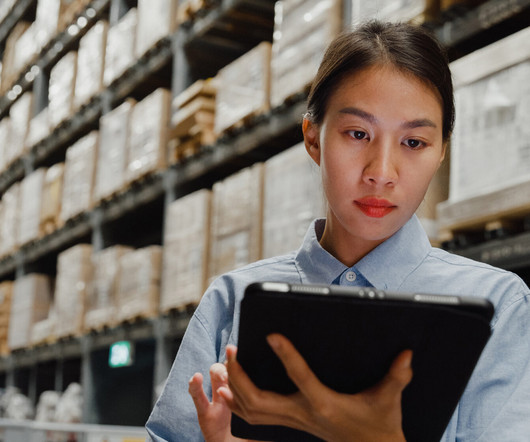
High Performance Inventory: The Supply Chain Differentiator
SEPTEMBER 13, 2023
Check out our library of videos, case studies , and other helpful resources here → Multi-Echelon Inventory Optimization So you have this great probabilistic forecast. Another example is Gaviota , a leading manufacturer of components, accessories, and systems for rolling shutters, awnings, and enclosures.
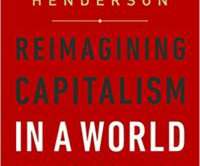
Walmart in a World on Fire
NOVEMBER 15, 2021
One of the companies she holds up as a positive example of a big company addressing environmental, social, and governance (ESG) issues is Walmart. A few years ago, for example , my oldest child explained to me that Walmart was a malignant force. Rebecca Henerson’s formula for fixing capitalism was a business best seller.
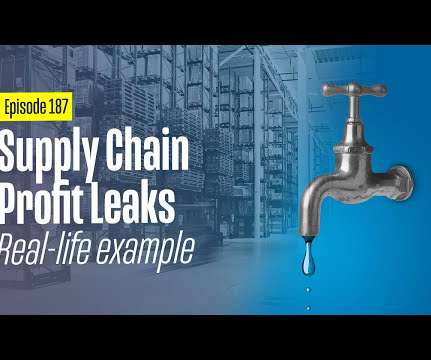
Supply Chain Profit Leaks in Real-Life
NOVEMBER 15, 2022
Here’s a real-life example . 7 Mini Case Studies : Successful Supply Chain Cost Reduction and Management. How to identify and fix your profit leaks? Related articles on this topic have appeared throughout our website, check them out: Cost to Serve – A Smarter Way to Improved Supply Chain Profitability.
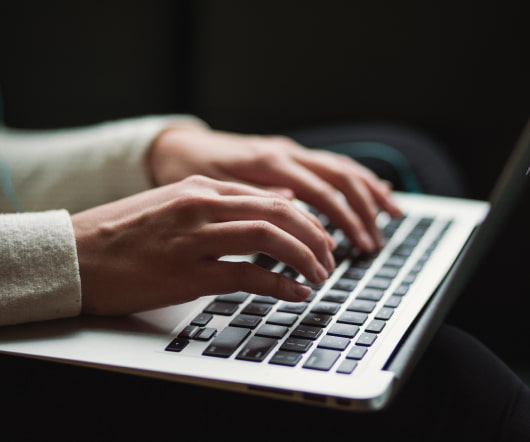
Rockwell Automation: A Case Study in Supply Chain Excellence
DECEMBER 4, 2018
Solutions, for example , can take from 12 to 16 weeks to manufacture. Rockwell Automation is a case study of a company working a long-term plan focused on improving flows for the customer. From a manufacturing perspective, products vary significantly in complexity. The Rockwell Automation Supply Chain.
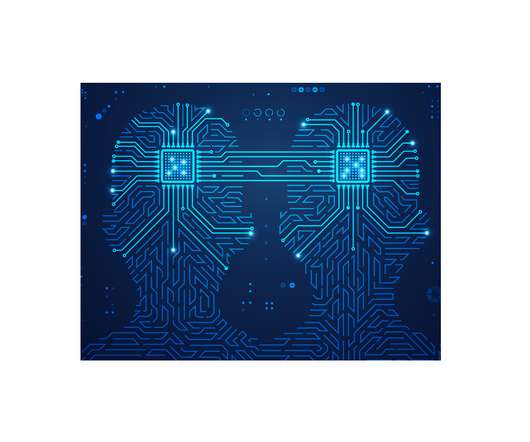
Philip Morris Drives Manufacturing Insights Using A Digital Twin
MARCH 16, 2021
To help readers sort through the hype, we are writing articles on digital twin use cases to help companies gain a competitive advantage. Here we share the case study of Philip Morris using a digital twin deployment. This case study is written in a Q&A format. Let’s take some examples .
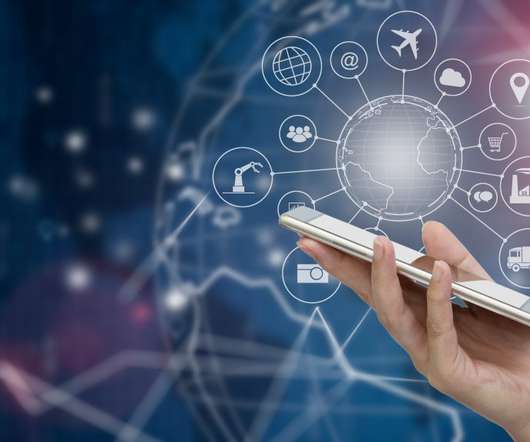
Importance of Digitalisation to Improve Supply Chains: Helping Businesses Navigate Through Supply Chain Disruptions
Automation, cargo tracking, robotics, and remote fleet management are all examples of how IoT can be used to harness organizational data and gain insights into key processes. The Green Corridor: Saving Whales in California – A Case Study in Regional Collaboration. Internet of Things (IoT).
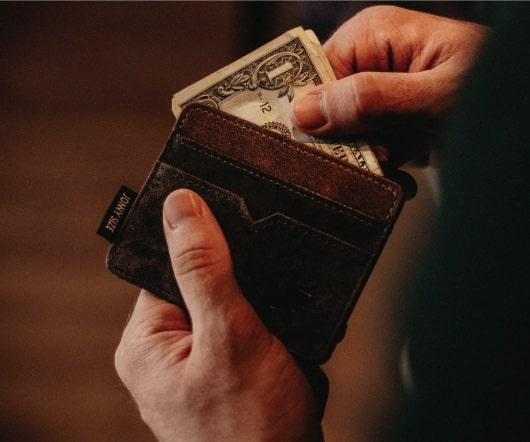
Blockchain: Reflections on a Webinar
NOVEMBER 16, 2017
Later that afternoon, I hosted a webinar featuring blockchain case studies . Yesterday, Bristlecone and IBM presented case studies . The case studies focus on cold chain safety/alerting for out-of-condition limits for milk transport in India and the use of blockchain for fresh produce monitoring.
Stay Connected
Join 136,000+ Insiders by signing up for our newsletter
- Participate in Supply Chain Brief
- How to achieve six-figure benefits from digitizing paper-based supply chain operation
- 2019 Supply Chain Brief Summer Reading List
- Stay At Home Reading List
- Add a Source
- Add a Resource
- See All
- 2018 Supply Chain Brief MVP Awards
- 2019 Supply Chain Brief MVP Awards
- 2020 Supply Chain Brief MVP Awards
- 2021 Supply Chain Brief MVP Awards
- 2022 Supply Chain Brief MVP Awards
- Sun. Apr 21
- Sat. Apr 20
- Fri. Apr 19
- Thu. Apr 18
- Apr 13 - Apr 19
- Warehousing
- Procurement
- Transportation
- Supply Chain
- More Topics

Input your email to sign up, or if you already have an account, log in here!
Enter your email address to reset your password. a temporary password will be e‑mailed to you., be in the know on.
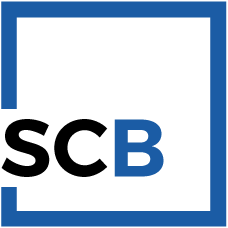
Supply Chain Brief
Expert insights. Personalized for you.
We organize all of the trending information in your field so you don't have to. Join 136,000+ users and stay up to date on the latest articles your peers are reading.

Get the good stuff
Subscribe to the following Supply Chain Brief newsletters:
You must accept the Privacy Policy and Terms & Conditions to proceed.

You know about us, now we want to get to know you!
Check your mail, we've sent an email to . please verify that you have received the email..
We have resent the email to
Let's personalize your content
Use social media to find articles.
We can use your profile and the content you share to understand your interests and provide content that is just for you.
Turn this off at any time. Your social media activity always remains private.
Let's get even more personalized
Choose topics that interest you., so, what do you do.
Are you sure you want to cancel your subscriptions?
Cancel my subscriptions
Don't cancel my subscriptions
Changing Country?
Accept terms & conditions.
It looks like you are changing your country/region of residence. In order to receive our emails, you must expressly agree. You can unsubscribe at any time by clicking the unsubscribe link at the bottom of our emails.
You appear to have previously removed your acceptance of the Terms & Conditions.

We noticed that you changed your country/region of residence; congratulations! In order to make this change, you must accept the Aggregage Terms and Conditions and Privacy Policy. Once you've accepted, then you will be able to choose which emails to receive from each site .
You must choose one option
Please choose which emails to receive from each site .
- Update All Sites
- Update Each Site
Please verify your previous choices for all sites
Sites have been updated - click Submit All Changes below to save your changes.
We recognize your account from another site in our network , please click 'Send Email' below to continue with verifying your account and setting a password.
You must accept the Privacy Policy and Terms & Conditions to proceed.
This is not me
- BECOME A CONTRIBUTOR
- WHITE PAPERS
- THE SUPPLY CHAIN DICTIONARY

What is Sales & Operations Planning?
The 4 supply chain metrics, static inventory an untapped source of working capital, s&op, a vision for the future. an interview with eric tinker, improving behaviours in support of world class s&op: coach for excellence.
- Planning & Forecasting Articles
How Can Data Improve Supplier Decisions
Information-based negotiations in the digital age, hurt, help or hero how to define and get more out of your most important suppliers, how to spot supplier risk during pickups & deliveries, how to spot supplier risk during on-site evaluations.
- Procurement & Sourcing Articles
The Long Tail of Inventory and Why It’s Important
No more excuses: transformative iot is staring you in the face, predictive analytics let manufacturers see more clearly into their supply chains, rise of the grocers, how 3d printing is set to shake up manufacturing supply chains.
- Manufacturing & Production Articles
6 Tips for Maximizing Efficiency and Productivity of Warehouse Operations
Robot trucks or autonomous vehicles will revolutionize the supply chain, data integration made sexy, how to avoid the most common warehouse safety hazards, out darn spot out, i say.
- Warhouse & Transport Articles
Returns – A Threat to the Bottom Line or an Opportunity to Cut Costs?
Supply chain sustainability takes root, why the 2030 sustainable development goals matter to packaging professionals, to build sustainable products, listen to your customers, getting packaging costs down to size.
- Reverse Logistics Articles
Transform Your Supply Chain For Omnichannel
The impact of maintenance operations on supply chain management, is your supply chain strategy inside-out or outside-in, how industry benchmarks can boost your asset recovery, supply chain visibility: we should be striving for more.
- Supply Chain Management articles
Accelerating the Shift to More Efficient Trucks
Insight – is it ok to lie, supply chain execution software convergence, 3d printing and the supply chains of the future, changing the production performance metric, supply chain management case study: the executive’s guide.
By Supplychainopz
Professionals in supply chain management use various methods to determine how to improve the performance of supply chain operations. Analysis of case study is certainly one of the most popular methods for people from business management background. In order to accelerate the learning, this article has gathered 20+ most sought-after supply chain case studies, analyzed/categorized them by industry and the findings are presented.

Boeing wants to encourage more flight frequency and direct route using a smaller capacity aircraft. Then they decide to outsource many things such as the design, testing and production of key components to key industrial partners and try to reduce number of components that go to assembly. The ultimate goal is to finish the final production process within 3 days. Airbus takes a bit different marketing approach. They want to utilize high capacity airplane to help airlines drive the operating cost down. They decide to selectively outsource the production of parts and keep the design and production of key components in-house.

Supply Chain of fashion industry involves a time based competition. Many customers have the unique product needs but a competition is very fierce because of the low barriers of entry. Many new players try to offer specialized products to customers all the time. This section features the supply chain case studies of H&M, Benetton, Zara and Adidas. – H&M aims to be the price leader in the fashion market.In order to materialize its vision, H&M tries to eliminate the middlemen in various stages of supply chain and consolidate the buying volumes. Product design is also the central part of its strategies. They don’t try to follow the high fashion designs but try to adopt the street trends which are easier to produce. At the end of the day, they can bring products to market within 2-3 weeks. – Benetton , in contrast, chooses to have a full control of its production but allow its licensees to operate the stores so they can focus on production and quality control. The reason is that they would like to create the worldwide brand awareness. For fast moving products, they use the production facilities in Europe. Asian suppliers will perform production for standardized products. – Zara is very famous for its time based strategy. In order to launch a new product within 15 days, Zara uses a small lot production. A new product will be tested in pilot stores. If product sales is good, a larger batch will be ordered. Otherwise, remaining products will be removed from the shelves and sold as mark-down in other stores. This creates the perception among consumers that Zara’s products are unique and you have to take it while stock lasts. Vertical integration contributes to the success of Zara, they own the majority of its production facilities and stores (this is the reason why Quick Response can be effectively implemented). Its automated distribution centers are strategically located between the center of populations so products are delivered to stores quickly. Zara also works with Air France, KLM Cargo and Emirates Air in order that they can coordinate directly with the airlines to make the outbound shipments to its stores and bring back some raw materials and semi-finished materials with return legs. The last supply chain case study in the fashion retailing industry is Adidas . In order to cope with changing customers’ demand, they decide to undertake Mass Customization strategy. The whole idea is to develop, market and deliver the product variety that most customers will find what they want. The first steps towards mass customization is to strategically offer the product choices. Too few variations will disappoint a customer but too many variations will simply postpone a buying decision. After that, Adidas asks the same key suppliers to produce custom components in order to achieve the economy of scale. In order to compensate a long waiting time, Adidas uses air freight or courier service. The reason why they can do this is that customized products are sold directly to customers so they have the higher profit margin to compensate the higher transportation cost. Supply chain strategy of the fashion retailing industry is summarized as below,

FMCG industry is typically the products sold to customers at a low cost and will be completely consumed within 1 year. The nature of this industry is the short product life cycle, low profit margin, high competition and demand fluctuation. This section will present the case studies of P&G, Unilever and Coca-Cola respectively. Forecasting and new product introduction has always been the issues for many FMCG companies, P&G is no exception. To cope with this, P&G conducts a merchandise testing at the pilot stores to determine the customer’s response to new product before the launch. The result is that the forecast accuracy is improved because a demand planner has an additional source data to make a better decision. Moreover, products can be shipped to stores in-time then lost sales is minimal. – Unilever also feels that the competition in FMCG industry has significantly increased. They have to launch the new products on regular basis but the forecasting of new product is difficult. So they create a better classification of new products (base, relaunch, repack, new) using a regression model to identify potential forecast errors for each type of new product. – Coca-Cola doesn’t really have many stock keep units when compared with other companies in the same industry. However, products go to over 2.4 million delivery points through over 430 distribution centers. Managing transportation at this scale is the absolute challenge. In order to streamline the delivery, Coca-Cola implemented a vehicle routing software. The reason is that is the software vendor has a very good relationship with Coca-Cola’s legacy ERP software vendor. Moreover, the vendor has a solid connection with the university who can help to develop the algorithm that fits in with the business’ needs. The result is that transportation planners at each distribution center can use the new tool to reduce travelling time/distance on daily basis.

Lean manufacturing concept has been implemented widely in the automotive industry so the case studies about lean manufacturing is very readily available. Due to the increasing competition in the automobile industry, car manufacturers have to launch a new model to the market more frequently. This section will show you how BMW manages a long term planning, how Ford applies lean concept to the new product development and how Hyundai manages the production planning and control. – BMW uses a 12-year planning horizon and divides it into an annual period. After that, they will make an annual sales forecast for the whole planning horizon. After the demand is obtained, they divide sales into 8 market and then select the appropriate production sites for each market, considering overall capacity constraints and total cost. As you may notice, this kind of a long range planning has to be done strategically. – Ford calls its product development system as “work streams” which include the body development, engine development, prototyping and launch process . The cross-functional team are the experts and their roles are to identify key processes, people, technology necessary for the development of new prototype. Each work stream team is responsible to develop timeline of each process. Detailed plan is usually presented on A3 sized paper. They clearly identifying current issues they are facing with supporting data, drawings and pictures. On weekly basis, they organize a big group meeting of all work stream team to discuss the coordination issues. – Hyundai deploys a centralized planning system covering both production and sales activities across the facilities and functional areas. They develop a 6-month master production plan and a weekly and a daily production schedule for each month in advance. During a short term planning (less than one month), they pay much attention to the coordination between purchasing, production and sales. Providing a long term planning data to its suppliers help to stabilize production of its part makers a lot.

Life cycle of technology products is getting shorter and shorter every day. Unlike FMCG, the launch of a new product in the hi-tech industry requires the investment in research and development quite extensively. Then, a poor planning will result in a massive loss. This section will cover JIT and outsourcing by Apple Inc, Supply Chain Risk Management by Cisco System, Technology Roadmap by Intel, Supply Chain Network Model by HP, Mass Customization by Dell and Quality Management by Sam Sung. Steve Jobs invited the Tim Cook to help to improve Apple’s Supply Chain in 1998. Jobs told Cook that he visited many manufacturing companies in Japan and he would like Cook to implement the JIT system for Apple. Jobs believed that Apple’ supply chain was too complex then both of them reduced the number of product availability and created 4 products segment, reduced on hand inventory and moved the assembling activities to Asia so they could focus on developing the breathtaking products that people wanted to buy. – Cisco Systems would like to be the brand of customer choice so they implement a very comprehensive supply chain risk management program by applying basic risk mitigation strategies, establishing appropriate metrics, monitoring potential supply chain disruptions on 24/7 basis and activate an incident management team when the level of disruption is significant. – Intel ‘s new product development is done by the process called Technology Roadmap. Basically, it’s the shared expectations among Intel, its customers and suppliers for the future product lineup. The first step to prepare the roadmap is to identify the expectations among semiconductor companies and suppliers. Then they identify key technological requirements needed to fulfill the expectations. The final step is to propose the plan to a final meeting to discuss about the feasibility of project. Some concerning parties such as downstream firms may try to alter some aspects of the roadmap. Technology Roadmap allows Intel to share its vision to its ecosystem and to utilize new technology from its suppliers. – HP ‘s case study is pretty unique. They face with a basic question, where to produce, localize and distribute products. Its simple supply chain network model is presented below,

From this example, only 3 possible locations result in 5 different way to design the supply chain. In reality, HP has more production facilities than the example above so there are so many scenarios to work with. How should HP decide which kind of a supply chain network configuration they should take to reduce cost and increase service to customer? The answer is that they use the multi-echelon inventory model to solve the problem. – Dell is one of the classic supply chain case studies of all time. Many industries try to imitate Dell’s success. The key ingredients of Dell’s supply chain are the partnership with suppliers, part modularity, vendor managed inventory program, demand management and mass customization. Also, you can find the simplified process map of Dell’s order-to-cash process as below,
– Sam Sung has proven to be the force to be reckoned with in the hi-tech industry. The secret behind its supply chain success is the use of Six Sigma approach. They studied how General Electric (GE), DuPont and Honeywell implemented six sigma. After that, they have created their own implementation methodology called DMAEV (define, measure, analyze, enable, verify). They use the global level KPI to ensure that each player in the same supply chain is measured the same way. Also, they utilize SCOR Model as the standard process. Any process changes will be reflected through an advance planning system (APS).

The last industry covered here is the general merchandise retailing industry. The critical success factor of this industry is to understand the drivers of consumer demand. Four case studies will be presented, namely, 7-11, Tesco, Walmart, Amazon and Zappos. – 7/11 is another popular case study in supply chain management. The integration of information technology between stores and its distribution centers play the important role. Since the size of 7/11 store is pretty small, it’s crucial that a store manager knows what kind of products should be displayed on shelves to maximize the revenue. This is achieved through the monitoring of sales data every morning. Sales data enables the company to create the right product mix and the new products on regular basis. 7/11 also uses something called combined delivery system aka cross docking. The products are categorized by the temperature (frozen, chilled, room temperature and warm foods). Each truck routes to multiple stores during off-peak time to avoid the traffic congestion and reduce the problems with loading/unloading at stores. – Tesco is one of the prominent retail stores in Europe. Since UK is relatively small when compared with the United States, centralized control of distribution operations and warehouse makes it easier to manage. They use the bigger trucks (with special compartments for multi-temperature products) and make a less frequent delivery to reduce transportation cost. Definitely, they use a computerized systems and electronic data interchange to connect the stores and the central processing system. – Wal-Mart ‘s “Every Day Low Prices” is the strategy mentioned in many textbooks. The idea is to try not to make the promotions that make the demand plunges and surges aka bullwhip effect. Wal-Mart has less than 100 distribution centers in total and each one serves a particular market. To make a decision about new DC location, Walmart uses 2 main factors, namely, the demand in the proposed DC area and the outbound logistics cost from DC to stores. Cost of inbound logistics is not taken into account. There are 3 types of the replenishment process in Wal-Mart supply chain network as below,
In contrary to general belief, Wal-mart doesn’t use cross-docking that often. About 20% of orders are direct-to-store (for example, dog food products). Another 80% of orders are handled by both warehouse and cross dock system. Wal-Mart has one of the largest private fleet in the United States. The delivery is made 50% by common carriers and 50% by private fleet. Private fleet is used to perform the backhauls (picks up cargoes from vendors to replenish DCs + sends returned products to vendors). Short-hauls (less than one working day drive) is also done by the a private fleet. For long-hauls, the common carriers will be used. There are 2 main information system deployed by Wal-Mart. “Retail Link” is the communication system developed in-house to store data, share data and help with the shipment routing assignments. Another system is called “Inforem” for the automation of a replenishment process. Inforem was originally developed by IBM and has been modified extensively by Wal-Mart. Inforem uses various factors such as POS data, current stock level and so on to suggest the order quantity many times a week. Level of collaboration between Wal-Mart and vendors is different from one vendor to the other. Some vendors can participate in VMI program but the level of information sharing is also different. VMI program at Wal-Mart is not 100% on consignment basis. – Amazon has a very grand business strategy to “ offer customers low prices, convenience, and a wide selection of merchandise “. Due to the lack of actual store front, the locations of warehouse facilities are strategically important to the company. Amazon makes a facility locations decision based on the distance to demand areas and tax implications. With 170 million items of physical products in the virtual stores, the back end of order processing and fulfillment is a bit complicated. Anyway, a simplified version of the order-to-cash process are illustrated as below,
Upon receipt of the orders, Amazon assign the orders to an appropriate DC with the lowest outbound logistics cost. In Amazon’s warehouse, there are 5 types of storage areas. Library Prime Storage is the area dedicated for book/magazine. Case Flow Prime Storage is for the products with a broken case and high demand. Pallet Prime Storage is for the products with a full case and high demand. Random Storage is for the smaller items with a moderate demand and Reserve Storage will be used for the low demand/irregular shaped products. Amazon uses an propitiatory warehouse management system to make the putaway decision and order picking decision. After the orders are picked and packed, Amazon ships the orders using common carriers so they can obtain the economy of scale. Orders will arrive at UPS facility near a delivery point and UPS will perform the last mile delivery to customers. Amazon is known to use Sales and Operations Planning (S&OP) to handle the sales forecast. Anyway, this must be S&OP process at product family/category level. To compete with other online retailers, Zappos pays much attention to the way they provide the services to customers. In stead of focusing on the call center productivity, Zappos encourages its staff to spend times over the phone with customers as long as they can so they can fully understand the customer’s requirements. They also upgrade the delivery from 3 days to 1 day delivery in order to exceed customer expectation.

All case study demonstrates that supply chain management is truly the strategic initiatives, not merely a cost cutting technique. Leading companies have a very strong customer focus because almost all of initiatives are something to fill the needs of customers. Relationship management is the unsung hero in supply chain management. It’s the prerequisite to the success of every supply chain. And at the end of the day, it comes down to the quality of supply chain people who analyze, improve and control supply chain operations. – See more at: http://www.supplychainopz.com/2014/04/supply-chain-management-case-study.html#sthash.MrnrGsyY.dpuf
Supply Chain Minded is a very active and fast growing online community in Supply Chain for Planning, Sourcing, Manufacturing, Delivery and Reverse Logistics professionals. The Supply Chain Minded community aims to inform and connect professionals active in Supply Chain, Purchasing, Manufacturing, Warehousing, Transport, Distribution; Reverse Logistics, Service Logistics, Lean & Six Sigma, 3PL.
© Copyright - Supply Chain Minded 2023
- Skip to primary navigation
- Skip to main content
- Skip to primary sidebar
- Skip to footer

Supply Chain Management Design & Simulation Online
Supply Chain Case Studies
SCM Globe comes with a library of case studies that explore COMMERCIAL , HUMANITARIAN , and MILITARY supply chains. When you purchase an account you have access to all the case studies and their simulations.
The case studies range from relatively simple beginning cases like Cincinnati Seasonings , to quite challenging advanced cases such as Zara Clothing Company , or Nepal Earthquake Disaster Response . Case studies are laboratories where you apply what you learn in lectures and readings to solve supply chain problems in highly realistic simulations. Each case has a " CASE STUDY CONCEPT " showing the supply chain principles and practices highlighted in that case.
SEE WHAT PEOPLE ARE SAYING ABOUT SCM GLOBE

Case studies presently available in the online library are shown below. You are welcome to use any or all of them. You can also create your own case studies, or we can create them for you. Cases are shown in the three categories. As you work with these cases you will gain an intuitive understanding of supply chain dynamics, and develop the analytical skills for designing and managing real supply chains.
People new to SCM Globe should start with the Cincinnati Seasonings case study . Work individually at first, not in groups. Each person needs their own account. Do the three challenges shown in the online introduction to Cincinnati Seasonings. That's how you'll learn to use the software, and how to use simulations to analyze and design supply chains. Then you will be ready to work in groups or work on more advanced cases. Click on the case studies below to see a description and introduction to each case.
Commercial Supply Chain Case Studies

Collaborative Supply Chains

S&J Trading Company – Angola

Java Furniture Company – Indonesia

Cincinnati Seasonings

Supply Chains of the Roman Empire

Ancient Silk Road – First Global Supply Chain

Zara Clothing Company Supply Chain

Fantastic Corporation – Global Supply Chain

Fantastic Corporation – Unexpected Disruptions
Humanitarian supply chain case studies.

Disaster Response Supply Chains: Flooding Scenario

Nepal Earthquake Disaster Response Supply Chain

Humanitarian Supply Chains: Syria Evacuation Scenario (CIV and MIL)
Military supply chain case studies.

Burma Campaign – 1944 Invasion of India

Battle of Smolensk – 1941 Invasion of Russia

Alexander the Great Needed Great Supply Chains
New case studies.
New cases are added based on projects we do with instructors, students, and supply chain professionals. Here are the new supply chain models in the library:
- Local and Sustainable Supply Chains – Blue Ocean Cooperative
- Aerospace Manufacturing Cluster – Rockford IL
- Hyderabadi Biryani – Paramount Restaurant
- Western Desert War – May 1941
- Russian Logistics for the Invasion of Ukraine
Interactive Supply Chain Case Studies
Every case study has a main theme or concept that it illustrates. You will be challenged to use knowledge acquired in lectures and readings as well as your own real-world experience to expand and re-design the supply chains in these case studies.
In the commercial supply chain cases you need to improve and expand the supply chains to support new stores and still keep operating costs and inventory as low as possible. In cases that deal with humanitarian or military missions you need to create supply chains to deliver the right supplies to the right locations when they are needed, and do so at a reasonable cost.

We are glad to provide a free evaluation account to instructors, students and supply chain professionals interested in exploring SCM Globe simulations — click here to request an account — Get Your Free Trial Demo
See SCM Globe pricing for Academic and Business versions of the software.
The best case to start with is Cincinnati Seasonings . After working through the three challenges presented in the online introduction to this case you will be ready to handle further challenges in this case or move on to more advanced cases. Get a quick introduction to working with case studies in “ Working with Case Studies “.

As problems are found in the simulations, you make decisions about how to fix them. Make changes to your supply chain model in the Edit screen. Then go to the Simulate screen and run a simulation to see the results of your changes. Depending on the changes you make, your supply chain simulation runs for additional days and other problems arise. As you address these problems you see about how supply chains work. Apply what you learn in readings and and lectures plus your work experience to solve the problems you encounter.
Keep improving your supply chain model until you get the simulation to run for 30+ days. Then download your simulation results and create a monthly Profit & Loss Report plus KPIs (as shown below). This provides an objective basis for evaluating the merits of different supply chain solutions.

Monthly Profit & Loss Reports identify areas for improvement. They help you improve your supply chain to keep it running for 30 days and also lower operating costs and inventory levels. You can work on lowering the carbon footprint of your supply chain too. These are the challenges you address in SCM Globe, and they are the same challenges people face when managing real supply chains. What works well in the simulations will also work well with actual supply chains. Skills you develop in working with the simulations are directly transferable to the real world.
NOTE: You can run simulations for longer than 30 – 60 days, but there is usually no reason to do so. This is because most companies do not run their supply chains unchanged for longer than 30 days at a time. They use a 30 day S&OP ( sales and operations planning ) cycle and these simulations correspond to that monthly S&OP cycle. These simulations focus on the tactical realities of operating a supply chain from one month to the next, and finding what works best.
Accessing the Online Library of Case Studies
As shown in the screenshots below, logon to your account and access the case study library from your Account Management screen. Click on the “View Library” button (arrow 1) in upper right corner of the Account Management screen. In the Library screen you see a list of available supply chain case studies; click “ Import ” to load a selected case study into your account; give the imported case a Name , and click “ My Account ” to go back to your Account Management screen.
You are welcome to import any or as many of the supply chain models in the library as you wish. Once you have a copy of a supply chain model in your own account you can make any changes you want to it.

In Account Management, you “ Create a New Supply Chain ” or work with an existing supply chain by clicking the “ Edit ” button (arrow 2) next to the existing supply chain you want to work on. You can also upload copies of supply chain models sent to you by other SCM Globe users (arrow 3) , and check your account expiration date (arrow 4) .
Use the Default Values or Enter New Data
When you load any of the case study supply chain models from the SCM Globe library, they come with default numbers already plugged in. You can either accept the defaults or do some research to find more current data. This data (like data and prices everywhere) changes all the time.
Look for data on products, facilities and vehicles that are used in your supply chain and see what their specifications and costs are. Costs can vary widely in different parts of the world. Go to websites of commercial real estate brokers in cities of interest and see what you can find out about rent costs:
- for cities in North America start with www.cityfeet.com
- and for cities in other parts of the world start with www.knightfrank.com
Metric System of Weights and Measures
In the case studies all weights, volumes, distances and speeds are expressed using the metric system. The metric system is used around the world in every country except three: Liberia; Myanmar; and the United States. So it is good for supply chain professionals to feel comfortable with the metric system.
Register on SCM Globe for Access to all Supply Chain Simulations
Click the blue "Register" button on the app login page, and buy an account with a credit card or PayPal (unless you already have one). Then scan the "Getting Started" section, and you are ready to start. Go to the SCM Globe library and click "Import" next to the supply chain models you want.
- Browse All Articles
- Newsletter Sign-Up
SupplyChainManagement →
No results found in working knowledge.
- Were any results found in one of the other content buckets on the left?
- Try removing some search filters.
- Use different search filters.

- SUGGESTED TOPICS
- The Magazine
- Newsletters
- Managing Yourself
- Managing Teams
- Work-life Balance
- The Big Idea
- Data & Visuals
- Reading Lists
- Case Selections
- HBR Learning
- Topic Feeds
- Account Settings
- Email Preferences
Case Study: How Should We Diversify Our Supply Chain?
- Krishna G. Palepu

A Chinese appliance maker considers expanding production to Mexico.
In the wake of Covid-19’s disruptions, Kshore, a Chinese appliance maker, is thinking of realigning its supply chain. Like many other global manufacturers, it’s being pressured by its customers, which include Walmart and other large retailers, to reduce the time, expense, and environmental impact of shipping goods between countries.
On a trip to Monterrey, Mexico, Kshore’s CEO and COO tour factories that are closer to North American markets—and are impressed by their professionalism. But questions about transportation and staffing give the executives pause. Should Kshore start production in Mexico or consider other countries? Two experts weigh in.
On the sidewalk outside the airport in Mexico City, Yun Liu and Keith Smith, the CEO and COO of Kshore, a Chinese appliance maker with $150 million in annual revenues, waited for their town car. Their journey from Guangzhou, China, had been a long one.
- Krishna G. Palepu is the Ross Graham Walker Professor of Business Administration at Harvard Business School. His research focuses on globalization, emerging markets, and strategies for multinational and local companies in those markets. He cochairs the HBS executive program Leading Global Businesses.
Partner Center
Powering up resilience to mitigate supply chain disruption
When supply chain disruptions strike, grocery shelves go empty. Here’s how one company’s new system is keeping them full.
- Call for Change
- When Tech Meets Human Ingenuity
- A Valuable Difference
- Related Capabilities
Call for change
One of the world’s largest food and beverage companies has hundreds of brands under its belt. But amid global supply chain disruption , labor shortages and pandemic-fueled shifts in consumer demand, getting those products onto store shelves was becoming more difficult.
The company’s service level, measured by Case Fill Rate (CFR), was only reaching about 84%—some 11-12 percentage points below pre-pandemic performance. So, for example, a retailer looking to stock 100 bottles of a product may only receive 84 at the expected time of delivery.
With orders delayed or incomplete and shelves empty or understocked, the company was concerned about losing market share—and the trust of consumers. The company needed to rethink how it could effectively and efficiently handle supply chain management. So the company turned to Accenture to help identify the heart of the issue and collaborate on potential solutions.
When tech meets human ingenuity
Accenture helped the company build a roadmap to a more resilient system. They implemented a control tower to provide visibility across all operations. A new Sales and Operations Execution (S&OE) team was tapped to handle short-term issues so the supply chain planning team could focus on long-term strategy.
The teams found ways to make existing tools and data more useful and responsive, while adding new processes and governance to fill in the gaps. By connecting existing analytics dashboards to an ERP system and other data sources, the S&OE team could create predictive reports. By adding proactive alerts that addressed potential issues up to six weeks out, they could also make short-term adjustments to save valuable time and effort—and to actively plan for disruptions.
Supply chain control tower – visibility to value
Learn how you can make your supply chain networks more customer-centric, sustainable and agile
A valuable difference
With end-to-end visibility, more efficient organization and a set of new routines and best practices to connect disparate teams, supply chain network issues are now much more manageable. The results are evident in the numbers: The company saw its case fill rate pass 90%—a level it had not achieved in more than two years. Soon, it was finishing its month with record volumes.
The greater resiliency built into the new system means the company is prepared for what’s ahead and can react more efficiently to future supply chain disruption. In reimagining its operations, the company is orchestrating the change it needs to deliver customers what they expect. Now, retailers are more likely to get the products they want, when they want them—keeping shelves full and consumers happy.
Meet our lead
Gabriel Montoya
Related capabilities, supply chain & operations.
Reimagining tomorrow's supply networks to positively impact business, society and the planet.
Resilient supply chain
Build a secure, responsive supply chain network that anticipates and adapts to disruptions, market changes and customer demands.
Consumer goods & services
Welcome to the new era of commerce.
Asking the better questions that unlock new answers to the working world's most complex issues.
Trending topics
AI insights
EY podcasts
EY webcasts
Operations leaders
Technology leaders
Marketing and growth leaders
Cybersecurity and privacy leaders
Risk leaders
EY Center for Board Matters
EY helps clients create long-term value for all stakeholders. Enabled by data and technology, our services and solutions provide trust through assurance and help clients transform, grow and operate.
Artificial Intelligence (AI)
Strategy, transaction and transformation consulting
Technology transformation
Tax function operations
Climate change and sustainability services
EY Ecosystems
Supply chain and operations
EY Partner Ecosystem
Explore Services
We bring together extraordinary people, like you, to build a better working world.
Experienced professionals
MBA and advanced-degree students
Student and entry level programs
Contract workers
EY-Parthenon careers
Discover how EY insights and services are helping to reframe the future of your industry.
Case studies
Energy and resources
How data analytics can strengthen supply chain performance
13-Jul-2023 Ben Williams
How Takeda harnessed the power of the metaverse for positive human impact
26-Jun-2023 Edwina Fitzmaurice
Banking and Capital Markets
How cutting back infused higher quality in transaction monitoring
11-Jul-2023 Ron V. Giammarco
At EY, our purpose is building a better working world. The insights and services we provide help to create long-term value for clients, people and society, and to build trust in the capital markets.
EY is now carbon negative
19-Sep-2022 Carmine Di Sibio
Our commitment to audit quality
13-Nov-2023 Julie A. Boland
No results have been found
Recent Searches
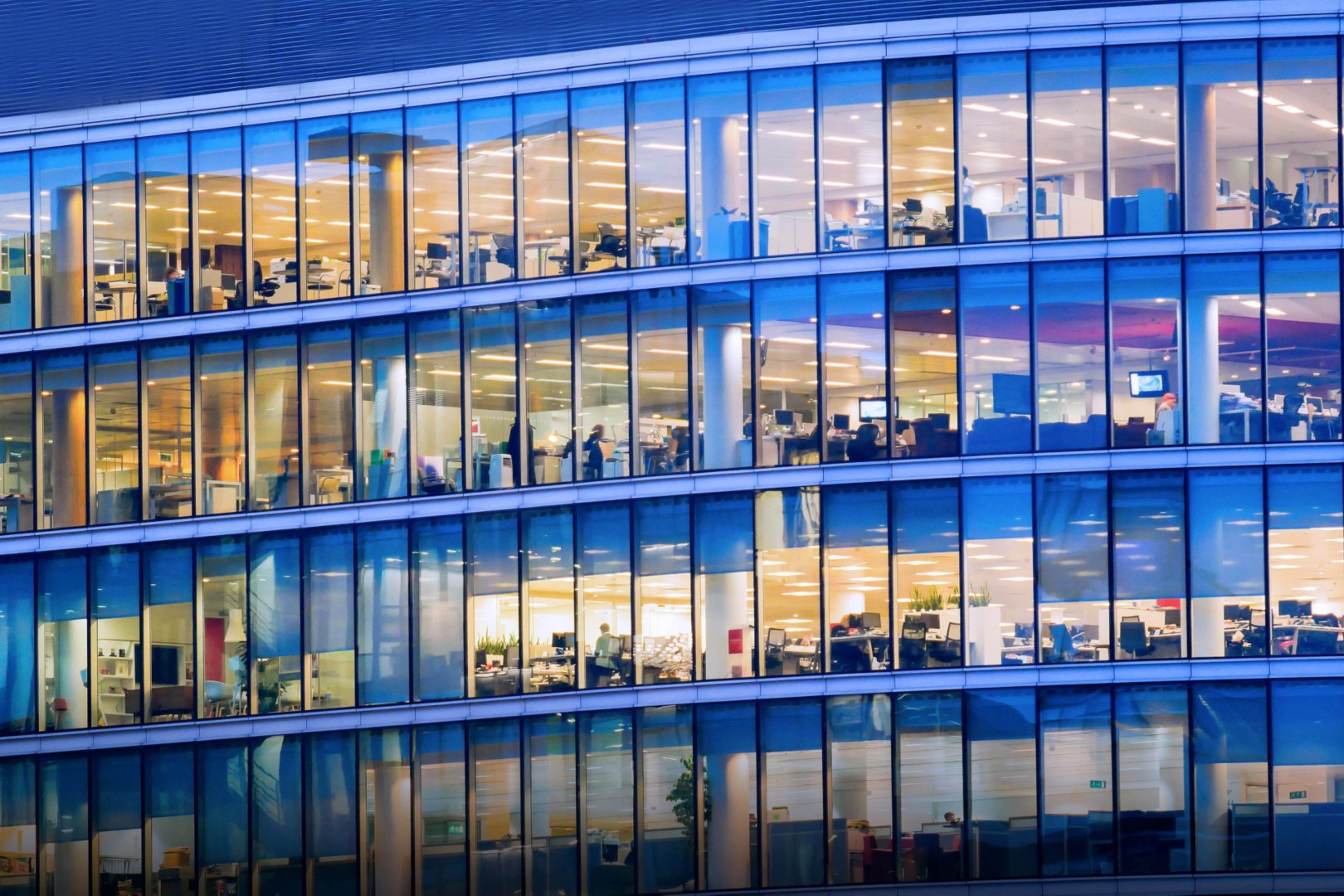
BEPS 2.0: as policies evolve, engagement is key
It remains to be seen whether the US will align its tax law with the OECD/G20’s global BEPS 2.0 rules. MNEs will feel the impact in 2024. Learn more.
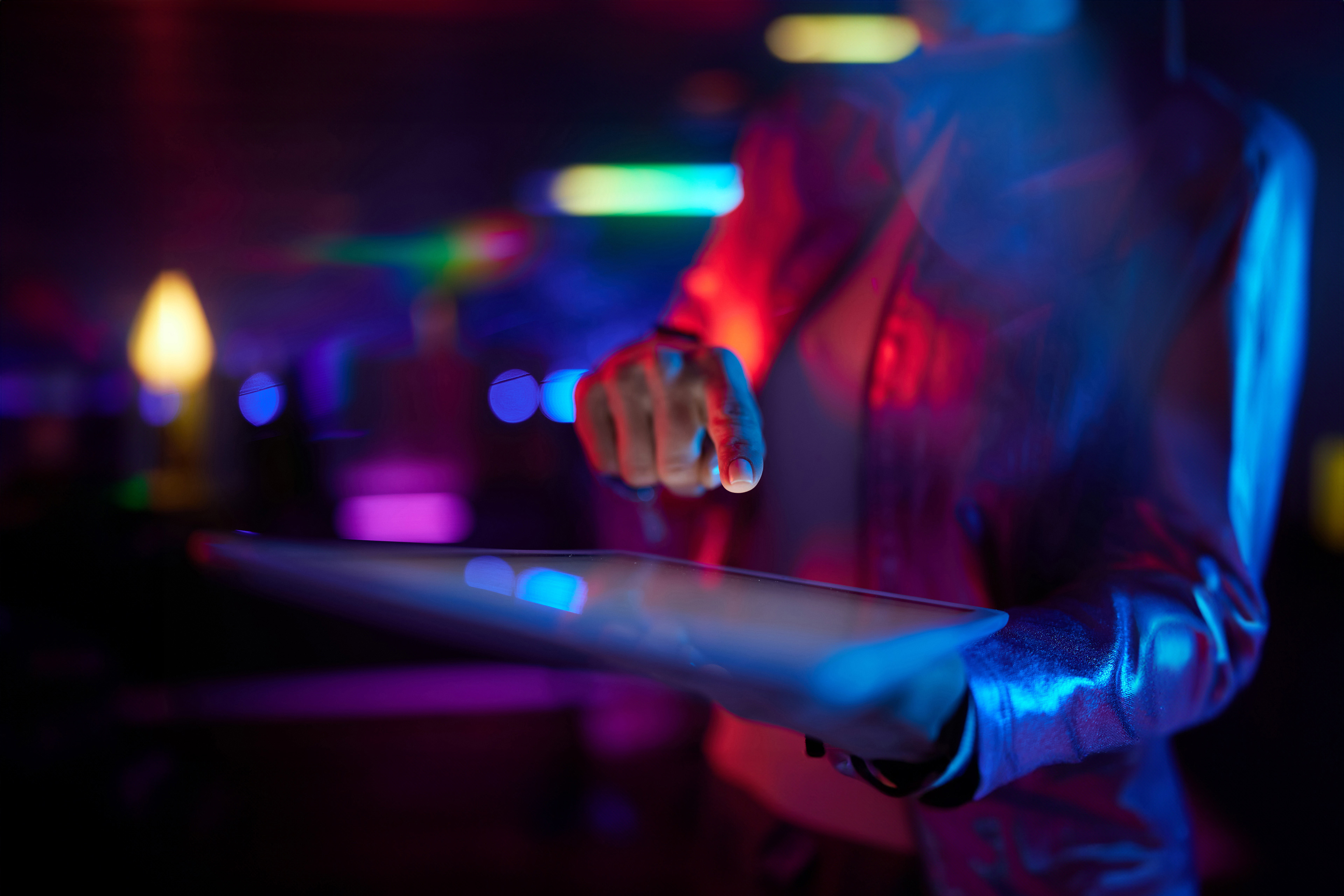
How GenAI strategy can transform innovation
Companies considering or investing in a transformative GenAI strategy should tie generative artificial intelligence use cases to revenue, cost and expense. Learn more
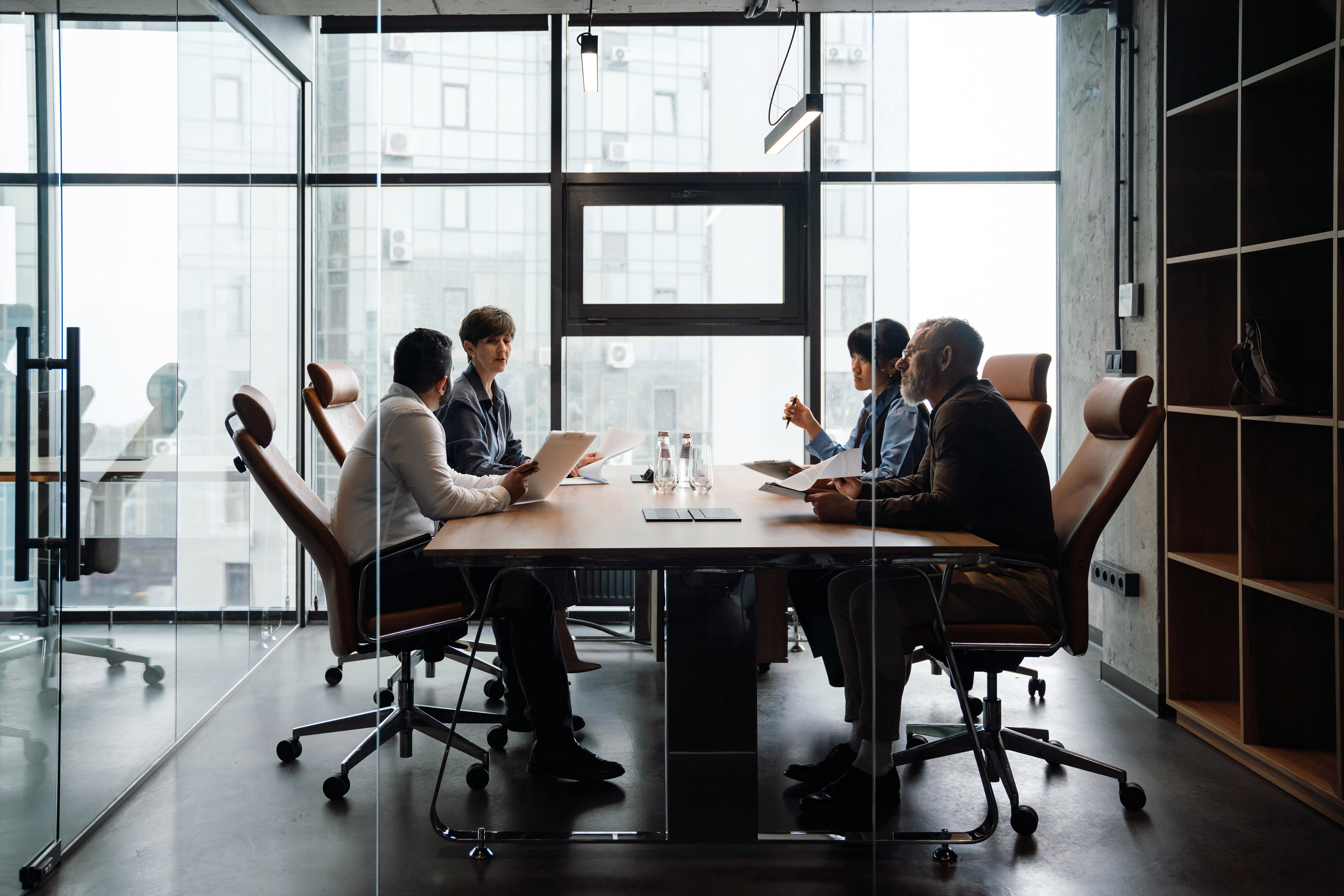
Top five private equity trends for 2024
Read about the five key trends private equity firms will emphasize in 2024 as they create value
Select your location
close expand_more
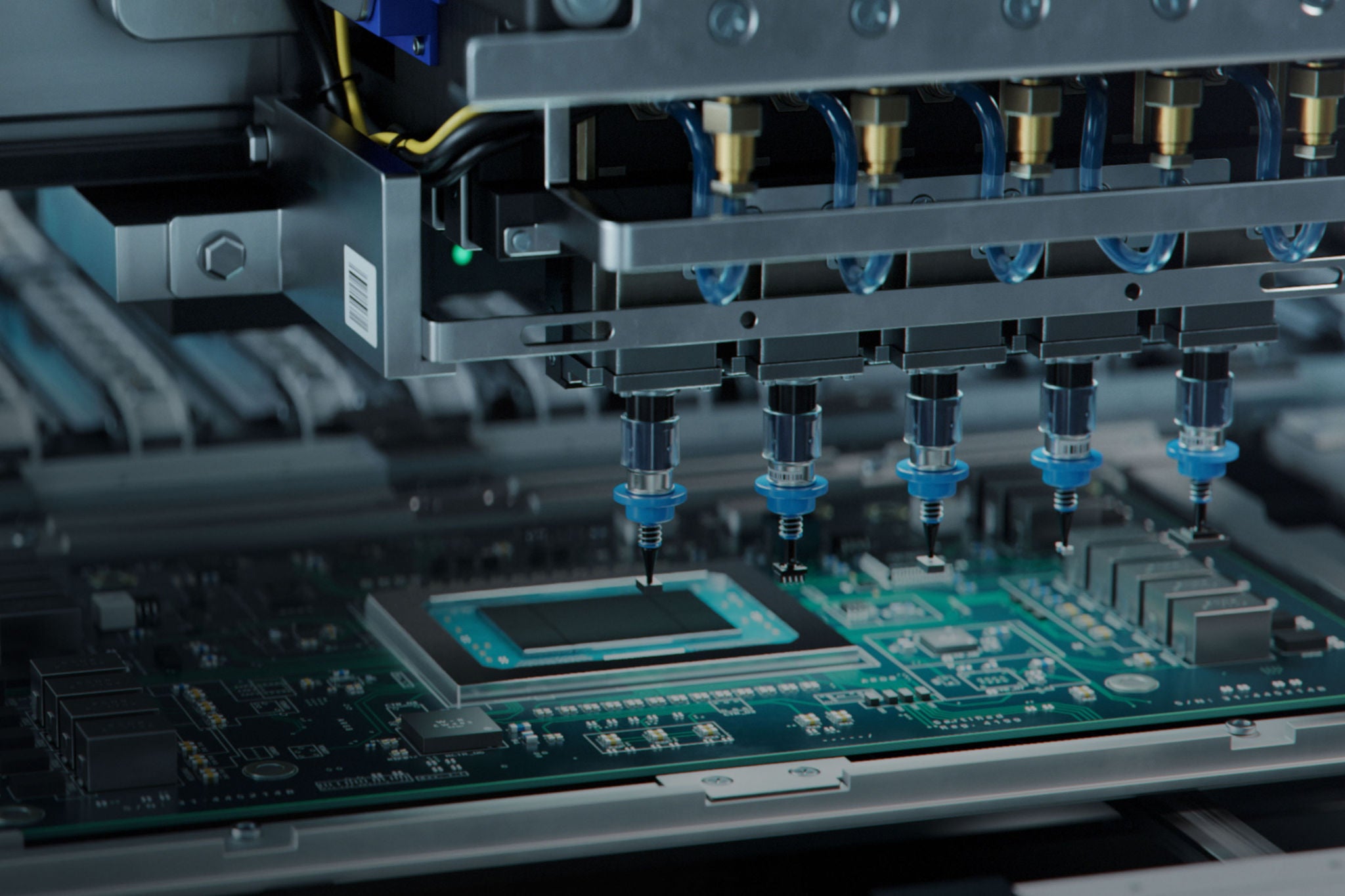
How supply chain helps an electronics manufacturer connect customers
A global electronics company diversifies its manufacturing locations to increase its supply chain resilience.
- 1. Better question
- 2. Better answer
- 3. Better working world
How EY can help
The better the question
How can a supply chain deliver electronic devices on demand?
A US-based electronics manufacturer reduces supply chain risk to keep its customers tuned to all the right channels.
Explore our Offerings
Supply Chain & Operations Consulting Services
Discover how EY's supply chain team can help your business redefine its end-to-end supply chain and operations to support your enterprise objectives.
The electronics industry is facing steep supply chain challenges, reaching all the way back to the raw materials that make up those tiny components keeping people connected in real time.
A leading electronics supplier that provides mobile devices to consumers and public entities was experiencing shortfalls due to overreliance on materials and manufacturing in Asia. A perfect storm of factors, including the COVID-19 global pandemic and widespread geopolitical instability, has weakened the global supply chain, and cross-border labor is no longer guaranteed.
Transportation delays, both in the air and on the water, are extending production lead times. Country-specific tax and trade regulations are also threatening shipping timelines and slowing product delivery dates for customers.
“Corporate leaders at this electronic device company recognized that supply chain resilience has become an urgent business imperative for their organization,” said Jim Morton, Executive Director for the Ernst & Young LLP Business Consulting supply chain practice. “With most of their customer base in the US, they recognized that they needed to diversify their sourcing and production options as effectively as possible, which meant varying manufacturing locations to complement their global portfolio.”
Leaders engaged an integrated EY team experienced in supply chain modeling and optimization , tax and trade. The team developed a comprehensive plan that would diversify manufacturing and alleviate the organization’s long-term supply chain risk.
EY teams’ extensive tax experience, deep understanding of global incentives and locations, and keen geopolitical business perspective showed the client how it can continue to help consumers access critical mobile devices and carve a sustainable new path forward for its business.
Diversified manufacturing locations reduce supply chain risk
An integrated digital model evaluates multiple operation sites to yield informed decisions.
Geostrategic Business Group
Our Geostrategic Business Group (GBG) can help your business translate geopolitical insights into business strategy to manage political risk. Find out how.
With its deepest manufacturing roots in Asia, the mobile device provider needed to diversify its production footprint. Supply chain disruptions, longer ocean transport times, region-specific trade restrictions and frequent unexpected delays were pushing leaders to consider adding manufacturing sites closer to the US – the location of their corporate headquarters and most of their customer base.
Research from EY teams shows that 64% of companies have re-shored some elements to improve sustainability. In addition, 42% of companies said that ensuring sustainable and diverse sourcing was a priority. With data such as these in mind, the company turned to an EY cross-practice team for a strategy to augment core operations in more accessible and stable locations, reducing its overall supply chain risk while maintaining existing operations in Asia and elsewhere. Faced with a daunting and costly business decision, leaders needed assurance they could diversify their manufacturing and still procure the right materials, maintain quality standards, and deliver reliable products to meet urgent user needs.
The EY team assessed and designed a more diverse supply chain network with the company’s global business in mind.
Supply chain optimization was done based on a computerized model to assess the global supply chain, mapping raw materials to flow of goods, to distribution centers and finally to customer locations. The model evaluated current networks against future state options, assessing millions of site variables rapidly to provide leadership with the informed perspective they needed. The EY digital model brought an integrated view of the tax considerations inherent in ramping up manufacturing in new sites and countries, including customs duties, direct and indirect tax implications and country-specific regulations. The EY Geostrategic Business Group provided clarity around government labor, trade policies and local laws to further optimize recommendations, blending speed and cost to enable on-demand inventory.
"With recent supply chain disruption, trade wars and geopolitical uncertainty, this global electronics leader needed an integrated supply chain model so they could successfully diversify their manufacturing portfolio, avoid production delays, and address country-specific issues,” said Morton. “The EY supply chain optimization model helped them make more informed decisions and select their new manufacturing site in North America.”
End-to-end supply chain analysis was conducted by tracking the company’s highest-priority devices. Validated data inputs were primed and transitioned from a flow-constrained model to a demand-driven model. The analysis evaluated economic value added with the future state footprint, insourcing vs. outsourcing manufacturing operations, tax considerations, skilled labor availability, geopolitical factors, ESG and carbon footprint impact, and the reduction of supply chain complexity.
A supply chain scorecard was created by the EY team to help leaders evaluate manufacturing sites more critically, assessing six key supply chain factors:
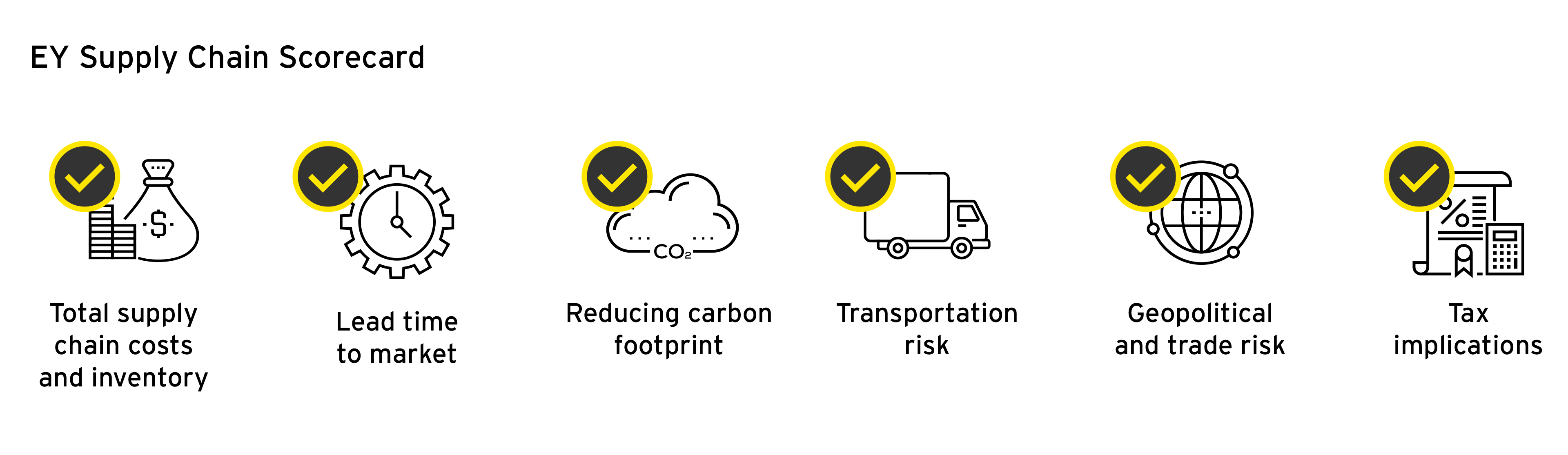
Using the information gathered by the EY scorecard and digital assessment tools, the electronics company was able to ultimately select a new near shore location as its next manufacturing site. With this new location identified, EY teams will now work with the client to build out a roadmap to ramp up operations – including manufacturing providers, tax implications, geopolitical and regulatory guidance.
The better the world works
Supply chain optimization keeps customers connected around the world
The forward-thinking EY supply chain model diversifies production and minimizes risk.
For a leading electronics provider that serves millions of customers around the world, keeping the organization’s supply chain operating smoothly is of paramount importance. Comprehensive EY supply chain modeling and optimization for this organization was designed with a future state supply chain in mind, so that the organization could vary its manufacturing portfolio, maintain current production quotas, mitigate risk and reduce excess product inventory by 27%.
The EY digital supply chain optimization model helped the electronics leader assess site locations across countries, geopolitical factors, trade implications, trade risk and tax regulations. The manufacturing site scorecard helped the company narrow down possible manufacturing sites and identify specific locations within countries that will help the organization further reduce their carbon emissions by 15%. The supply chain solution will also increase the organization’s efficiency by reducing the length of haul from production site to customer by 50%, and by lowering labor costs.
“Our integrated supply chain model, which included extensive tax experience and deep geopolitical business perspective across locations, provided this electronics powerhouse a solution that would help them diversify and de-risk their supply chain, allowing important communication devices to continue to be readily available worldwide,” said Morton.
As the company works to ramp up its newest manufacturing location in North America, EY teams will be on board to help it conduct continued geopolitical and tax analysis, develop end-to-end supply chain analysis, establish timing, and evaluate distribution footprint expansion.
- 50% reduction in the average length of haul from production to consumer
- 27% reduction of excess product inventory in the pipeline
- 15% reduction in future carbon emissions impact from transport
- Lower duty costs on products imported from the near shore location
- Potential cost savings gained from business incentives provided by the near shore location
EY OpsChain Contract Management Solution
Discover how EY's OpsChain Contract Management Solution can help your TMT business boost speed, visibility and trust along your digital value chain. Learn more.
Related topics
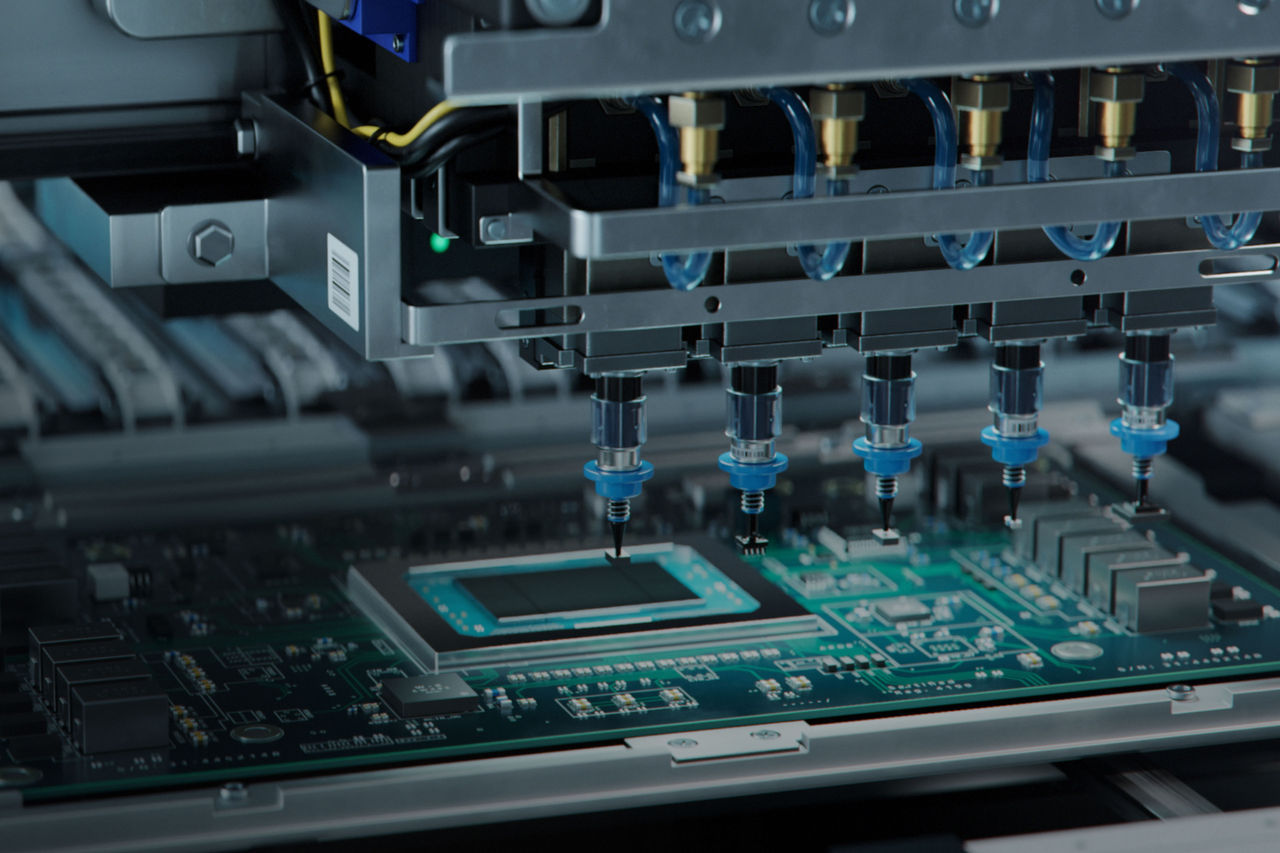

Glenn Steinberg
Helping companies transform, create value and optimize business performance. Thirsty for knowledge. Ski enthusiast. Husband and father of two Michigan Wolverines.
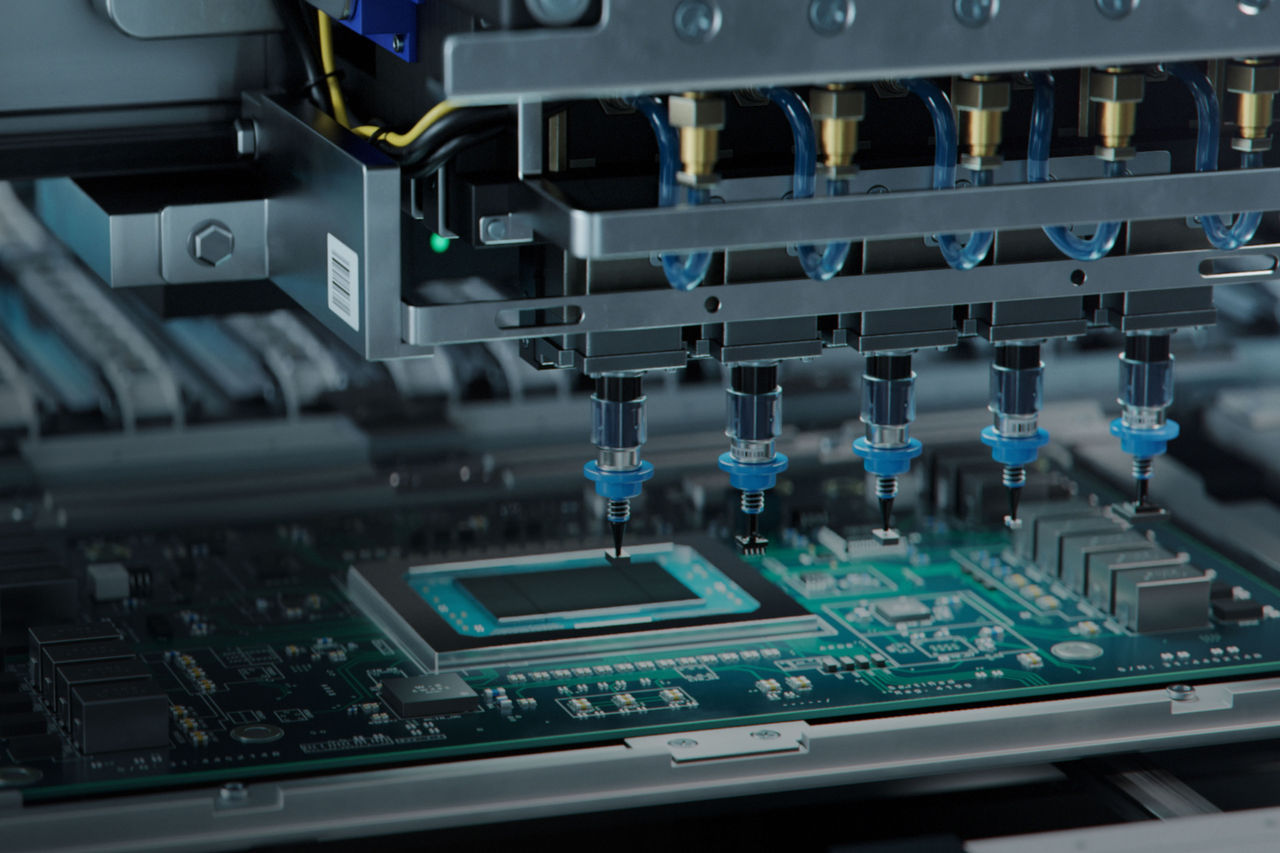
Greg Cudahy
Years of experience in global operations transformation, price and revenue optimization, sourcing, integrated planning, supply chain synchronization and collaborative applications.
Explore our case study library
EY Consulting case studies are a window into how we work alongside our clients to deliver strategic, sustainable growth.

- Connect with us
- Our locations
- Do Not Sell or Share My Personal Information
- Legal and privacy
- Accessibility
- Open Facebook profile
- Open X profile
- Open LinkedIn profile
- Open Youtube profile
EY refers to the global organization, and may refer to one or more, of the member firms of Ernst & Young Global Limited, each of which is a separate legal entity. Ernst & Young Global Limited, a UK company limited by guarantee, does not provide services to clients.
- Software Categories
Get results fast. Talk to an expert now.
855-718-1369
Creating an omnichannel supply chain: a macy’s case study.
In February 2020, Macy’s announced their Polaris plan , a three-year strategy created to stabilize profits and create growth. This plan included closing 125 underperforming stores and consolidating offices. It also included a major overhaul of their supply chain model.
But, of course, Macy’s had to close their doors less than 6 weeks later due to COVID-19. As their online presence was the only presence available, their longstanding supply chain strategy, which was already starting to cause major issues within the company, needed immediate attention.
Macy’s CEO Jeff Gennette stated in September 2020, “Everything on the digital agenda has been accelerated. We’re optimizing inventory placement to meet customer demand wherever and however they shop in our store.”
What’s so bad about Macy’s supply chain model?
Customers expect a strong omnichannel experience — one that integrates both the online and offline world of the retailer, enabling a frictionless shopping experience.
For retailers, the goal is to take the retailer’s replenishment cycle from days to hours and reduce inventory at stores. This way, retailers expand their use of stores to fulfil online orders and hold less inventory altogether, allowing them to dedicate more room for digital fulfillment.
Omnichannel shopping is the baseline expectation for customers, as companies such as Gap, Target, and many others have upped their omnichannel game.
And Macy’s is, er, behind.
Macy’s way of viewing their supply chain in the past was traditional: Move products from point A to point B and optimize costs at each stop along the way. Each delivery channel has its own transportation plan and technology stack, siloing all distribution and fulfillment centers.
This supply chain method was acceptable 10 years ago, but to stay afloat in the in-store and online retail spaces, Macy’s needed to make a change. Silos created major cost issues, not to mention slow speed and service in today’s two-day-delivery age.
The company’s supply chain model operated two separate warehouse networks, one for stores and the other for direct customer (online) orders. This system made rebalancing inventory nearly impossible, among other issues.
Macy’s supply chain also lacked a central platform for locating inventory at the SKU level across the chain, and the cost of goods were high compared to competitors since each private brand sold at May’s was sourced independently.
Creating a better supply chain
In 2019 Macy’s hired Dennis Mullahy , the first ever Chief Supply Chain Officer, to transform the supply chain into one that supports an omnichannel strategy.
Since then, Macy’s has made leaps and bounds in optimizing their supply flow, with COVID expediting the process.
The company is transitioning to a centralized warehouse model, implementing a flow and fold design, meaning a light initial allocation to stores and flexible replenishments. Multipurpose warehouses hold inventory, which can both replenish stores and fulfill e-commerce orders.
By having a centralized inventory, the retailer is better able to strengthen its margins and fulfill orders quicker and in the ways customers want.
“Our new model will leverage all of our assets much more productively and improve customer satisfaction by increasing speed of delivery as well as generate efficiencies in our operations and inventory utilization.” Dennis Mullahy wrote.
In addition, Macy’s is getting on board with using data and analytics to not only get items to customers faster, but also improve inventory forecasting and allocation and package consolidation.
The company plans to increase drop-shipping to boost margins in e-commerce, where delivery costs have been the largest drain on profits. They’ll also renew their efforts into Macy’s Backstage operations in order to compete with other off-price companies such as Nordstrom Rack and TJMaxx.
Behind the curve
And while these improvements are giving Macy’s the help it needs, they should’ve seen the warning signs sooner. Retailers of equal size have been making moves to change their supply chain for years now, and Macy’s is just catching up.
For example, Kohls has been working to integrate e-commerce and brick and mortar stores since the beginning of 2018. The company worked to change its purchase and inventory management system by starting with the smallest stores and working their way up.
Nordstrom has been working on omnichannel fulfillment for over 3 years, and brought in tech consulting firm Opex Analytics to help.
Walmart unveiled plans this month to install a high-tech automation system across 25 Walmart regional distribution centers through their partnership with Symbotic, a robotics and automation company — something they’ve been working toward since 2017. This system will digitize and modernize Walmart’s current supply chain facilities to enrich customer experience and support evolving demand.
But even though Macy’s may be a few steps behind, true omnichannel is a journey — and a difficult one at that. It requires a lot from the supply chain, especially in terms of speed, complexity, and efficiency. The global retailer is making strides in executing their Polaris plan by focusing more on the integrated fulfillment strategy and alternative fulfillment options and listening to what their customers want.
Looking for software? Try our IT Product Selection Tool
In this article...
Get FREE Expert Advice
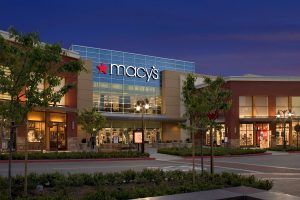
How should our experts reach you?
Learn everything you need to know about Creating an Omnichannel Supply Chain: A Macy’s Case Study. Our experts will reach out to you shortly.
By clicking the button above, I confirm that I have read and agree to the Terms of Use and Privacy Policy.
A more resilient supply chain from optimized operations planning
Across industries, companies that rely on transported materials for their operations have gained hard-earned knowledge from major disruptions over the past couple of decades, most notably the financial crisis of 2008, the COVID-19 pandemic, and geopolitical developments. During times of sudden upheaval, companies must quickly ramp down operations and then ramp up again once demand bounces back, adapt their execution, and revisit long-term plans. The supply chain has a special role to play, as companies rapidly shift their focus from cost-effectiveness to maximized throughput—all with the same assets and infrastructure.
About the authors
A poor response can have cascading effects, such as facility shutdowns or missed delivery obligations. In recent years, approaches that use data and analytics to identify answers and make recommendations to specific business problems have proved to be particularly relevant in bringing clarity to operations planning and thus improving supply chain resilience. However, the vast majority of companies have yet to implement such approaches in their supply chain, leaving a serious gap in their planning capabilities.
A recent McKinsey article 1 “ Building value-chain resilience with AI ,” November 26, 2021. examined three value chain approaches that can address this supply chain gap —simulations of reality, optimization of plans, and real-time control-tower monitoring (see sidebar, “How analytics supports different planning approaches”). Here, we examine the second approach in more detail, as it ranks among the most powerful tools businesses can use to navigate complex and changing environments, especially disruptions.
How analytics supports different planning approaches
Supply chain analytics can support planning efforts that broadly fall into three types. While optimization has been at the center of this article, two other tools are simulation and monitoring. All three require expert knowledge of the system, but simulation also relies on large historic data sets (exhibit).
Optimization models are prescriptive analytics tools. The main output is an optimal plan for the current environment. Optimization is most useful when an organization must create an ideal plan from scratch that factors in complex rules and constraints. A typical use case for optimization is building a monthly plan for operational production as part of the sales and operations planning process.
Simulations are descriptive analytics tools. In a simulation, a digital twin is constructed with uncertainty measures and operational inputs. Simulation is more appropriate for comparing or modifying existing plans in the face of uncertainty. Whereas optimization is more of a “black box” process, simulation produces explainable KPI-driven reports. A typical simulation use case involves examining an existing material network with uncertain production quantities, demand, and transit times to identify first- and second-order bottlenecks.
The third analytics approach is real-time monitoring. Most companies have a control tower serving as an operating nerve center. However, fully digital end-to-end control towers can increase resilience by expanding the scope of real-time monitoring to anticipate and respond to upcoming or potential supply chain disruption. Real-time monitoring is the most useful when seamless communication between various functions and integrated decision making are critical.
A combined approach is often best. For example, consider detailed railway scheduling. The complex rules and interactions require optimization methods to create valid plans, while simulation can then validate the performance and robustness of plans and determine the most effective delay-mitigation policies. Real-time monitoring ensures seamless communication between individual hubs in case of unexpected disruptions.
Organizations that want to get the most out of this powerful approach design their associated optimization tools and processes along five best practices: improve information flows between teams, elevate customer centricity, bridge the gap between long-term planning and day-to-day operations, understand true operational constraints, and use scenario analysis to ask critical “what if” questions.
As companies in manufacturing industries have discovered, following these design practices can increase supply chain throughput by 10 to 15 percent in the short term, with no change in assets or overall configuration. Organizations can also reduce costs by 5 to 10 percent and CO 2 emissions by 10 to 15 percent over the long term while increasing operational flexibility and resilience toward disruptions. This article details the design best practices that support this effort and how companies can get started integrating the necessary capabilities into their business.
Optimization in sales and operations planning
Optimization in operations planning involves determining the optimal choices for a set of decisions in a given business environment and business target. This type of optimization generally works best with prescriptive models that provide the ideal set of decisions as an output. The elegance of optimization is its ability to adapt to not only changing business environments but also shifts in the business target—for example, from minimum cost to maximum throughput, highest yield, zero environmental impact, or a combination of multiple factors.
For these reasons, optimization is the ideal approach to readjust a company’s operations as outside factors or strategic priorities change. For example, an agricultural company recently experienced dramatic rises in production costs combined with limited transport capacity, creating significant gaps in its ability to manage existing resource constraints. The company was able to respond by shifting its operations planning to an optimization approach that almost completely closed this gap.
Would you like to learn more about our Manufacturing & Supply Chain practice?
In essence, organizations can embrace optimization to support better, faster planning and thus increase value capture and resilience. Five best practices can sustainably improve supply chain decision making across the full coordination process (exhibit). To do so, the design of the corresponding optimization tools and processes must address all decision layers—from strategic orientation to operational execution. The best practices for optimization design explicitly address distinct layers and can thus enhance transparency and planning effectiveness.
1. Elevate customer centricity by enabling a pull principle for demand-driven operations
Customer-centric thinking is a foundational element for any type of operations planning. Tools and processes must be able to quickly translate demand into sequence and volume of production units and share this information with individual production sites. Optimization tools and processes can make these decisions rapidly and objectively, enabling both automated plan adjustments based on changing customer demand and faster responses by contact center agents to customer requests. Satisfying those requests can have a significant impact on operations. A commodity metals company was able to accelerate its decision-making process and thus more quickly react to urgent customer requests resulting from demand fluctuations caused by rapidly changing spot prices.
2. Bridge the gap between long-term planning and day-to-day operations
Short-term plans are typically shaped by current constraints, while long-term plans depend on outside factors that are likely to change. Effective operations planning addresses the in-between period, in which value can be lost in the gap between tactical vision and concrete implementation. Optimization tools and processes can translate mid- and long-term plans into detailed operational schedules, automatically accounting for dynamic conditions and complex operational constraints while allowing users to refine and explore possibilities. The gap is bridged in the other direction by feeding information on actual operations and deviations from control-tower monitoring back to optimization or simulation tools to continually minimize any loss in value. The agricultural company mentioned above was able to ensure its day-to-day operations remained in line with the long-term strategic goals and tactical monthly plans despite significant changes in the overall business environment.
3. Improve information flows between operations and marketing and sales
Organizations need to enable a consistent flow of information among stakeholders. Integrated supply chain planning tools already bring together information from multiple systems and business functions, creating transparency and empowering decision makers while enabling analytics tools. Optimization tools and processes can be added to improve decision making. A tangible example of this interplay can be a sudden change in production capacity due to an unforeseen dumper breakdown. Integrated planning tools ensure all relevant stakeholders are aware of this change, but only optimization tools will actively steer and synchronize the decisions of the entire organization toward the ideal target in this new environment. Actions could include modified marketing and pricing of the respective products or the realignment of the supply chain. Comprehensive control-tower dashboards are then used by teams from various functions to support real-time decision making.
For instance, a mining company was able to quickly and regularly make updates to its product portfolio based on recommendations from the marketing and sales team. This coordinated rapid response enabled the company to keep its portfolio closely aligned with market demand at all times.
4. Understand true operational constraints by dissecting the infeasible plans
The exercise of identifying and avoiding infeasible plans often leads planners to review and adjust their operations. This infeasibility can come in the form of forced stoppages when operators are tasked with following an impossible plan or situations in which plans are unable to meet all known operational constraints. Control-tower dashboards can aid in understanding these constraints and providing feedback. Optimization tools can then progressively integrate all these constraints into actual operations planning, thus providing consistently feasible solutions. In this way, the impact of optimization tools results in higher adoption, as they reduce the overall frustration level across the organization associated with these infeasible solutions. For one automotive company facing a shortage of semiconductor chips, a control-tower tool in combination with optimization-based processes generated more than $100 million in margin improvement.
5. Use scenario analysis to ask critical what-if questions
Planners must have an operational process that can run, understand, and evaluate scenarios for planning and scheduling. This process produces what-if questions that can inform discussions with sales, customers, and third parties and support better decision making. Optimization tools allow decision makers to focus on the “what if?” and receive immediate and risk-free feedback on the consequences, thus streamlining and lowering the barriers to asking insightful questions. Recently, a pharmaceutical company was able to improve overall throughput and on-time delivery by using optimization tools that enabled asking what-if questions regarding rush orders, staffing shortfalls, and capital expenditure investments.
Get started with an appropriate business opportunity
Many companies have yet to make significant investments in optimization for their operations planning. Often, organizations have not even undertaken the analysis to select the business opportunity. In addition, discussions around optimal business targets that cover the most relevant trade-offs are often ignored, as they reside between functions and are thus considered “off limits.” Picking the wrong operations element or business target for optimization diverts finite resources from what truly matters and represents the biggest risk of failure.
The key is to identify a process that satisfies three criteria: first, the overall decision space must be so large that an individual planner can’t explore and understand all the possibilities at once; second, the quality of outcomes must be objectively measured and assessed according to a well-defined and accepted target; and third, the potential for improvement must be measurable and ideally quantifiable—for example, costs, throughput, CO 2 emissions, profit, or a combination of multiple factors. The mining company focused on profit by adjusting the supply chain in line with the optimal product portfolio, and the agriculture company emphasized the marginal costs of incremental production. The metals company selected a combination of throughput and yield while maintaining high customer satisfaction. The automotive company minimized lost revenue coming from supply chain disruptions. And the pharmaceutical maximized on-time, in-full delivery.
Companies must ensure their optimization program identifies business opportunities and associated targets that are not properly covered by the existing manual processes. However, any optimization-based approach must retain an adequate level of human judgment and expertise to account for unexpected situations and outliers. Optimization should aim to augment and empower human decision makers but not replace them.
Common pitfalls in data gathering and infrastructure
Companies should avoid directing time and resources to elements that aren’t necessary for high-functioning operations planning. For example, contrary to conventional wisdom, large longitudinal data sets are not required. Optimization for supply chain planning can typically be built by drawing on knowledge gained through expert interviews as well as snapshots using a small amount of the latest business data. Both elements are present today, as organizations need access to this information to monitor supply chain performance in the first place.

Future-proofing the supply chain
Similarly, companies should avoid focusing on building new data-centric infrastructure as an initial enabler for operations planning—either to capture and ingest data more frequently or to host new, complex analytics solutions. Instead, operations planning solutions can run infrequently, use small-scale data, and typically be implemented alongside and connected to existing tools and systems. In this way, these solutions are complementary to common end-to-end planning cloud solutions and maximize the value organizations can extract from existing resources.
In a recent case study, the large mining player developed an optimization-based process to improve the supply chain of its trains, vessels, and mine operations over short- and medium-term horizons. The process was aligned with the company’s strategic target regarding customer specifications and overall production goals. Embedding the optimization process into overall decision making allowed the company to improve operations significantly. This move alone captured many millions of dollars in cost savings.
In a world characterized by increasing volatility and major disruptions, the maturity of operations planning has the potential to increase the performance spread between first movers and laggards. So far, bigger corporations have taken the lead in implementing approaches to optimize their operations planning, given the resources and capabilities required. Whether optimization is within the reach of all companies is still an open question.
Hossein Aghai-Khozani is a consultant in McKinsey’s Munich office, where Sebastian Reiter is a partner; Simon Bull is a consultant in the Copenhagen office; Valerio Dilda is a senior partner in the Paris office; and Lapo Mori is a partner in the Denver office.
The authors wish to thank Eddie Elizondo, Shailesh Lekhwani, and Tarusha Moonsamy for their contributions to this article.
Explore a career with us
Related articles.
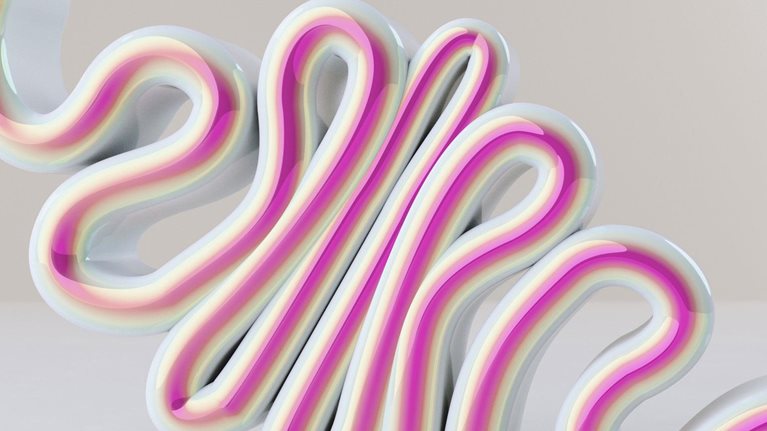
Building value-chain resilience with AI
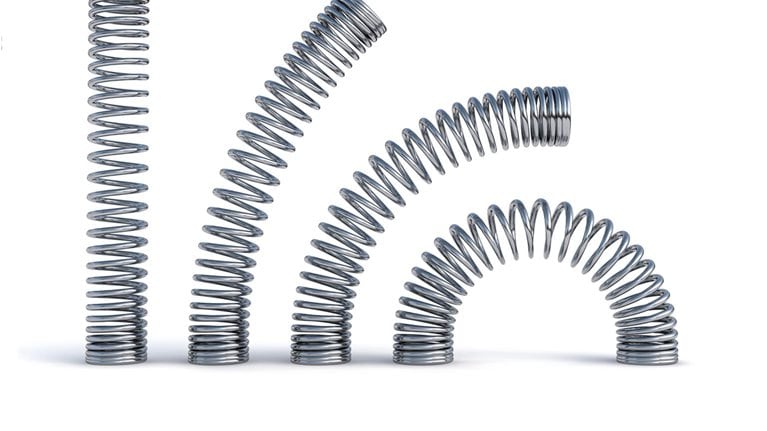
A better way to drive your business

Photo: Pixabay/geralt
7 mini case studies: successful supply chain cost-reduction and management

Rob O'Byrne
Group Managing Director - Logistics Bureau
If you were to tell me that your company had never looked at its supply chain costs and sought to deliver reductions, I would be mightily surprised. On the other hand, if you told me your company hasn’t been able to sustain any progress in supply chain cost reduction, I wouldn’t be surprised at all.
Most companies begin with the best intentions to achieve successful and sustainable supply chain cost management, but somehow seem to lose momentum, only to see costs increase again in short order.
The following seven mini case studies explore a few high-profile companies that have managed to sustain their supply chain cost-reduction efforts and keep expenses under control. The challenges faced by these organisations and the steps they took, may provide some inspiration for successful long-term cost management within your organisation.
1. Deere & Company
Deere & Company (brand name John Deere) is famed for the manufacture and supply of machinery used in agriculture, construction, and forestry, as well as diesel engines and lawn care equipment. In 2014, Deere & Company was listed 80th in the Fortune 500 America’s ranking and was 307th in the 2013 Fortune Global 500 ranking.
Supply Chain Cost Reduction Challenges: Deere and Company has a diverse product range, which includes a mix of heavy machinery for the consumer market, and industrial equipment, which is made to order. Retail activity is extremely seasonal, with the majority of sales occurring between March and July.
The company was replenishing dealers’ inventory weekly, using direct shipment and cross-docking operations from source warehouses located near Deere & Company’s manufacturing facilities. This operation was proving too costly and too slow, so the company launched an initiative to achieve a 10% supply chain cost reduction within four years.
The Path to Cost Reduction: The company undertook a supply chain network-redesign program, resulting in the commissioning of intermediate “merge centers” and optimization of cross-dock terminal locations.
Deere & Company also began consolidating shipments and using break-bulk terminals during the seasonal peak. The company also increased its use of third-party logistics providers and effectively created a network that could be optimized tactically at any given point in time.
Supply Chain Cost Management Results: Deere & Company’s supply chain cost-management achievements included an inventory decrease of $1 billion, a significant reduction in customer delivery lead times (from ten days to five or less) and annual transportation cost savings of around 5%.
One of the world’s largest manufacturers of computer chips, Intel needs little introduction. However, the company needed to reduce supply chain expenditure significantly after bringing its low-cost “Atom” chip to market. Supply chain costs of around $5.50 per chip were bearable for units selling for $100, but the price of the new chip was a fraction of that, at about $20.
The Supply Chain Cost Reduction Challenge: Somehow, Intel had to reduce the supply chain costs for the Atom chip, but had only one area of leverage—inventory.
The chip had to work, so Intel could make no service trade-offs. With each Atom product being a single component, there was also no way to reduce duty payments. Intel had already whittled packaging down to a minimum, and with a high value-to-weight ratio, the chips’ distribution costs could not be pared down any further.
The only option was to try to reduce levels of inventory, which, up to that point, had been kept very high to support a nine-week order cycle. The only way Intel could find to make supply chain cost reductions was to bring this cycle time down and therefore reduce inventory.
The Path to Cost Reduction: Intel decided to try what was considered an unlikely supply chain strategy for the semiconductor industry: make to order . The company began with a pilot operation using a manufacturer in Malaysia. Through a process of iteration, they gradually sought out and eliminated supply chain inefficiencies to reduce order cycle time incrementally. Further improvement initiatives included:
- Cutting the chip assembly test window from a five-day schedule, to a bi-weekly, 2-day-long process
- Introducing a formal S&OP planning process
- Moving to a vendor-managed inventory model wherever it was possible to do so
Supply Chain Cost Management Results: Through its incremental approach to cycle time improvement, Intel eventually drove the order cycle time for the Atom chip down from nine weeks to just two. As a result, the company achieved a supply chain cost reduction of more than $4 per unit for the $20 Atom chip—a far more palatable rate than the original figure of $5.50.
3. Starbucks
Like Intel, Starbucks is pretty much a household name, but like many of the most successful worldwide brands, the coffee-shop giant has been through its periods of supply chain pain. In fact, during 2007 and 2008, Starbucks leadership began to have severe doubts about the company’s ability to supply its 16,700 outlets. As in most commercial sectors at that time, sales were falling. At the same time, though, supply chain costs rose by more than $75 million.
Supply Chain Cost Reduction Challenges: When the supply chain executive team began investigating the rising costs and supply chain performance issues, they found that service was indeed falling short of expectations. Findings included the following problems
- Fewer than 50% of outlet deliveries were arriving on time
- Several poor outsourcing decisions had led to excessive 3PL expenses
- The supply chain had, (like those of many global organisations) evolved, rather than grown by design, and had hence become unnecessarily complex
The Path to Cost Reduction: Starbucks’ leadership had three main objectives in mind to achieve improved performance and supply chain cost reduction. These were to:
- Reorganize the supply chain
- Reduce cost to serve
- Lay the groundwork for future capability in the supply chain
To meet these objectives, Starbucks divided all its supply chain functions into three main groups, known as “plan” “make” and “deliver”. It also opened a new production facility, bringing the total number of U.S. plants to four.
Next, the company set about terminating partnerships with all but its most effective 3PLs . It then began managing the remaining partners via a weekly scorecard system, aligned with renewed service level agreements.
Supply Chain Cost Management Results: By the time Starbucks had completed its transformation program, it had saved more than $500 million over the course of 2009 and 2010, of which a large proportion came out of the supply chain, according to Peter Gibbons, then Executive Vice President of Global Supply Chain Operations.
Like Deere & Company, AGCO is a leading global force in the manufacture and supply of agricultural machinery. The company grew substantially over the course of two decades, achieving a considerable portion of that growth by way of acquisitions.
As commonly happens when enterprises grow in this way, AGCO experienced increasing degrees of supply chain complexity, along with associated increases in cost, but for many years, did little to address the issue directly, primarily due to the decentralized and fragmented nature of its global network.
In 2012, AGCO’s leaders recognised that this state of affairs could not continue and decided to establish a long-term program of strategic optimisation.
Supply Chain Cost Reduction Challenges: With five separate brands under its umbrella, AGCO’s product portfolio is vast. At the point when optimisation planning began, sourcing and inbound logistics were managed by teams in various countries, each with different levels of SCM maturity, and using different tools and systems.
As a result of the decentralised environment, in which inbound logistics and transport management were separate operational fields, there was insufficient transparency in the supply chain. The enterprise as a whole was not taking advantage of synergies and economies of scale (and the benefits of the same). These issues existed against a backdrop of a volatile, seasonal market.
The Path to Cost Reduction: Following a SCOR supply chain benchmarking exercise, AGCO decided to approach its cost reduction and efficiency goals by blending new technology—in the form of a globally integrated transport management system (TMS)—with a commitment to form a partnership with a suitably capable 3PL provider.
As North and South American divisions of the company were already working with a recently implemented TMS, leaders decided to introduce the blended approach in Europe, with commitments to replicate the model, if successful, in its other operating regions.
With the technology and partnership in place, a logistics control tower was developed, which integrates and coordinates all daily inbound supply activities within Europe, from the negotiation of carrier freight rates, through inbound shipment scheduling and transport plan optimisation to self-billing for carrier payment.
Supply Chain Cost Management Results: Within a year and a half of their European logistics solution’s go-live, AGCO achieved freight cost reductions of some 18%, and has continued to save between three and five percent on freight expenditure, year-on-year, ever since. Having since rolled the new operating model out in China and North America, the company has reduced inbound logistics costs by 28%, increased network performance by 25% and cut inventory levels by a quarter.
Headquartered in Westport Connecticut, Terex Corporation may not be such a well-known name, but if your company has ever rented an aerial working platform (a scissor-lift or similar), there is a good chance it was manufactured by Terex and dispatched to the rental company from its transfer center in North Bend, Washington.
The North Bend facility is always full of lifting equipment. The company makes most pieces to order and customizes them to meet customers’ unique preferences. Terex maintained a manual system for yard management at the transfer centre, which generated excessive costs for what should have been a relatively simple process of locating customers’ units to prepare them for delivery.
The Supply Chain Cost Reduction Challenge: A wallboard and sticker system was a low-tech solution for identifying equipment items in the yard at Terex. While inexpensive in itself, the solution cost around six minutes every time an employee had to locate a unit in the yard. It also required a considerable number of hours to be spent each month taking physical inventories and updating the company’s ERP platform.
The Path to Cost Reduction: Terex decided to replace the outdated manual yard management process with a new, digital solution using RFID tracking. Terex decided to replace the outdated manual yard management process with a new, digital solution using RFID tracking. Decision-makers chose a yard management software (YMS) product, and then had the transfer centre surveyed before initiating a pilot project covering a small portion of the yard.
After a successful pilot, the company approved the solution for full-scale implementation, replacing stickers, yard maps, and wallboard with electronic tracking and digital inventory management. As of December 2017, Terex was planning to integrate the yard management solution with its ERP platform to enable even greater functionality.
Supply Chain Cost Management Results: While the YMS cannot reconcile inventory automatically with the Terex ERP application, it does at least provide a daily inventory count via its business intelligence module. That alone has saved the labour costs previously incurred in carrying out manual counts.
More importantly, though, the RFID-based unit identification and location processes have saved the company around 70 weeks per year in labour costs, by cutting the process-time down from six minutes, to a mere 30 seconds per unit.
Avaya is a global force in business collaboration and communications technology, and not so many years ago, was operating what, by its own executives’ admission, was a worst-in-class supply chain. That situation arose as the result of multiple corporate acquisitions over a short space of time. The company was suffering from a range of supply chain maladies, including a long cash-to-cash cycle, an imbalance in supplier terms and conditions, excess inventory, and supply chain processes that were inefficient and wholly manual.
The Supply Chain Cost Reduction Challenge: After Avaya purchased Nortel Enterprise Solutions in 2009, the freshly merged company found itself but loosely in control of an unstable and ineffective supply chain operation. Aside from having too many disparate and redundant processes, the company had multiple IT solutions, none of which provided a holistic view of the supply chain or supported focused analysis.
The Path to Cost Reduction: Avaya’s senior management team realized that its technology solutions, which varied from being inadequate to inappropriate, were causing many of its problems. The various acquisitions and mergers had transformed Avaya into a different kind of enterprise, and what it needed, rather than a replacement for all the discrete systems, was one solution to tie them all together.
To that end, the company put its trust in cloud technology, which was relatively immature at the time, and migrated all processes onto one platform, which was designed to automate non-value-added activities and integrate those critical to proactive supply chain management, namely:
- Point of sale analysis
- Procurement analysis
- Supplier communication
- Supply and demand planning
- Inventory planning
- Inbound and outbound logistics planning
Of course, the technology was merely an enabler, and to transform its supply chain operation, Avaya embarked on a long-term, phased program to standardize processes, initiate a culture change, invest in top talent, and implement a system of rigorous benchmarking and KPI tracking .
Supply Chain Cost Management Results: Avaya’s program of transformation took place over a period of three to four years, between 2010 and 2014. The path to cost reduction was a long one, but ultimately successful.
By making a conscious effort to lead the enterprise into a new way of thinking, change business culture, and unify technology under a single platform, Avaya has improved inventory turns by more than 200%, reduced cash tied-up in stock by 94%, and cut its overall supply chain expenditure in half.
This dramatic turnaround also required the company to switch from a preoccupation with improving what it was doing, to a process of questioning what it was doing and why.
7. Sunsweet Growers
This final mini-case study in our collection, highlights how sometimes, excess supply chain costs are not about warehousing and transportation, but can be attributable to inefficiencies in manufacturing or production and—often at the root of it all—forecasting and planning.
Sunsweet Growers is the world’s biggest producer of dried fruits and a little over a decade ago, found that while it was managing distribution operations well, high production costs were inflating end-to-end supply chain expenditure.
The Supply Chain Cost Reduction Challenge: When the leadership at Sunsweet looked into the company’s production cost issues, recognition soon dawned that the distribution network was at least partly behind the problems. As a result, the company looked at how it could redesign the network to take out some of the production costs.
Later, it became apparent that although a redesign would yield some benefits, one of the most significant issues was in the approach to demand forecasting. Sunsweet was using a manual forecasting approach, with spreadsheets being the only technology involved.
The inefficiencies of this approach proved not only to hamper effective forecasting and production planning, but the knock-effect was an excess of warehouses in the network—so forecasting proved to be both a driver of production cost, and a key to improving the distribution network.
The Path to Cost Reduction: As in a number of the studies we’ve explored here, technology played a large part in solving Sunsweet’s problems. After evaluating some 30 different software solutions, the company finally settled on a supply chain planning suite, and planned its improvement program to make use of each of the solution’s modules in sequence, allowing ROI to be realized in phases as each module was implemented and leveraged.
At the same time, Sunsweet implemented a sales and operations planning program (S&OP) that once established, enabled plant resource requirements to be anticipated months—rather than weeks—in advance. As the overall improvement plan passed through its five phases, positive results accumulated and as hoped, software ROI reached 100% even before the company completed its full implementation.
Supply Chain Cost Management Results: Of course, the objective of Sunsweet’s improvement program was not merely to achieve a 100% return on investment in its supply chain planning platform. The aim was to reduce production costs, and although the company hasn’t published hard figures to quantify the total financial gain, it has claimed the following wins:
- A 15 to 20% increase in forecasting accuracy
- A reduction in overtime from 25% to 8% in production facilities
- A 30% reduction in finished-goods spoilage
- Number of warehouses in the United States cut from 28 to just eight
- A transportation cost-per-unit that remained static for two years despite increased utilization of costly refrigerated transport and rising fuel costs
From the achievements documented above, and highlighted in several industry publications and articles, you don’t need to be too much of a mathematician to deduce that cost savings would have been considerable.
Making Supply Chain Cost Reductions Stick
Of course, the above case studies are merely summaries of the changes these high-profile brands made to their supply chains. What can be seen from these brief accounts, though, is that for an enterprise to make significant and sustainable cost improvements, substantial change must take place.
- Deere & Company had to overhaul its network completely.
- Intel had to shift an entire supply chain to a new and previously unheard of strategy in its sector.
- Starbucks had to shake up its third-party relationships and increase production capacity.
- AGCO had to invest in technology and collaborative partnerships with external service providers.
- Terex had to implement costly (but effective) RFID tracking capabilities.
- Sunsweet Growers needed a best-of-breed software solution, and an S&OP program to improve forecasting and planning.
- Avaya needed to change company culture, implement cloud technology, rethink processes completely, and invest in the best supply chain talent it could find.
At the same time, none of the changes took place overnight. Each of the companies tackled issues in phases, effectively learning more as they went along.
You Won’t Find Savings in the Comfort Zone
When it comes to making supply chain cost reductions that stick, you should explore every avenue. However, at the root of high costs, there will usually be one major factor requiring innovation, whether it’s the network, inventory strategy, the working relationships with supply chain partners, or some other element of your operation.
Seldom do companies make decent savings by whittling away piecemeal at what seem, on the face of it, to be the most pressing issues of the day (such as direct transportation costs or supplier pricing).
If you want to see sustainable cost reductions, your company will need to view the big picture from a new angle or two, and be prepared to step outside of the comfort zone to which it will have become accustomed.
Rob O’Byrne is a supply chain consultant, coach and author with 40+ years experience in Supply Chain management. He is the expert making the blog called Logistics Bureau .
- # case studies
- # management
- # Supply Chain Management
- # T&L
Logistics and Supply Chain Case Studies
Review our case studies to see how we’ve helped major corporations turn logistical ideas into a reality., leading beverage distributor, penske logistics helps beverage distributor rapidly establish new warehousing operations.
When this distributor had to expand its operation quickly to counter a competitor, they turned to Penske to deploy a customized solution.
Baby2Baby Donation Transportation
Coordination and planning lead to successful transport of $3 million clothing donation.
Penske Logistics worked with Baby2Baby, a nonprofit that provides basic essentials to impoverished children, and Old Navy to transport $3M of clothing donations.
Luxury Product Manufacturer
Penske logistics reduces inventory shrinkage, improves overall inventory management.
A leading producer of fine luxury products required a partner who could improve their warehouse and distribution operations and reduce the theft.
Poultry Supplier
Transporting food items requires extra care and expertise.
Poultry producers, navigate a complex array of supply and delivery challenges to ensure their food arrives fresh, wholesome, and on-time.
Building Products Manufacturer
Customized fleet technology solution.
A leading building products manufacturer sought to streamline its supply chain operations and expand its fleet while improving visibility through the implementation of fleet management technology.
National Wholesale Distributor
A national wholesale distributor case study.
A national wholesale distributor of heating and air conditioning supplies was struggling to manage its complex supply chain and maintain high levels of customer service, which is a top priority.
Looping Process Ensures Continuous Production
Penske collaborated with Novelis to create a closed-loop recycling network that moves finished aluminum coils and transports scrap for new production.
A Global Manufacturer
Optimizing activities in the distribution center.
Penske worked with this global manufacturer to optimize its inventory routing and mode selection and to improve visibility to its supply chain.
Quick Service Restaurant
Food and beverage in-store delivery and warehousing.
Penske helped this restaurant chain get its supply chain fundamentals in place with the right logistics tools, truck driver training and warehousing solutions.
Tier 1 Automotive Component Supplier
Managing the inbound supply chain.
Penske helped this supplier minimize supply chain disruptions by designing a network that optimized mode selection, routing and analysis.
- Supply Chain Management
- Lead Logistics Provider
- Consulting Services
- Network Design
- Dedicated Contract Carriage
- Shared Dedicated Transportation
- Freight Management
- ClearChain ® Control
- Transportation Services
- Transportation Management Solutions
- Truckload Shipping Services
- Warehousing and Distribution
- Warehouse Design
- Warehouse Operations
- Multi-Client Warehousing
- Freight Brokerage
- Freight Forwarding
- Become a Carrier for Penske
Contact Penske Logistics about our services.

Library subject guides
Logistics and supply chain management.
- Key Resources
- Journals and Magazines
- Books and eBooks
- Company and Industry Information
Where to find case studies
- Additional information
Case studies generally describe real world practical examples from which others can gain insight for their own application. They can provide both positive examples and well as raise issues and challenges for others to be aware of.
To locate case studies in LibrarySearch , enter the search terms "case studies" or "case study*" and the keywords describing your topic.
Case studies can be located within the RMIT databases and across various subject areas.
Emerald Emerging Markets Case Studies (EEMCS)
Cases are written by case writers working in, or closely with, developing economies. They offer local perspectives with global appeal. The collection receives regular content updates throughout the year and all cases benefit from a supportive peer-review process to ensure the highest quality content.
- Emerald Insight A powerful business research tool that provides critical information when it is most needed. Users have instant access to over 35,000 full text articles from Emerald's international management portfolio, complete with full text archives back to 1994. Subject coverage spans a spectrum of management disciplines including: strategy; leadership; library and information management; marketing and human resource management; plus a substantial number of engineering, applied science and technology titles
Datamonitor Case Study Series
Short (10-page) company case studies examining the reasoning behind the success of specific companies.
- Datamonitor Case Study series Short (10-page) company case studies examining the reasoning behind the success of specific companies.
MarketLine Case Studies
Concise evaluations of the latest innovative company strategies to help you quickly and easily understand exactly what makes them successful. From social media initiatives to unusual store formats and online retailing, Case Studies present examples of best practice across a wide variety of industries and geographies, bringing innovation into full focus.
- MarketLine Reports & Briefs: Business Insights reports, company profiles,SWOT analyses, industry profiles, Porters Five Forces Scorecards, country profiles. Databooks: Company Financial & Top Ten Industry Players Guide, Financial Deals: tracks 195,000+ deals of over $5 million in value each month globally, News & Opinions: live news feed, Market Data Analytics: data for 150+ consumer products in 55 countries. Country Statistics: data for 215 global countries
ProQuest Case Studies
- ProQuest Covering over 90,000 authoritative sources ProQuest is one of the world's most comprehensive collections of digital information. Millions of complete articles are available online in various formats.
EbscoHost Case Studies
- Business Source Complete (EBSCO) Business Source Complete is the world's definitive scholarly business database, providing the ultimate collection of bibliographic and full text content. As part of the comprehensive coverage offered by this database, indexing and abstracts for the most important scholarly business journals back to 1886 are included. In addition to the searchable cited references, Business Source Complete contains detailed author profiles for the most-cited authors in the database.
Case studies
Case studies describe real world practical examples, including successes, issues and challenges. To find case studies using LibrarySearch or databases, add "case study" to your search terms.
- The case study handbook a student's guide This e-book provides tips on how to read, analyse and write about cases.
Finding case studies
The Library's Finding Case Studies guide explains different types of case studies and how to find them.
Writing a case study
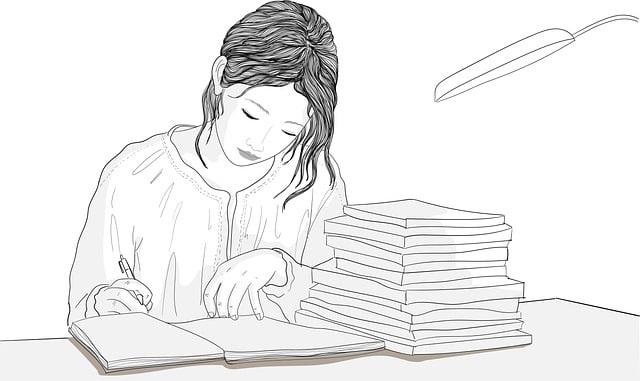
See the Learning Lab tutorial on Writing a Case Study to find out how to read, analyse and respond to a case study.
- << Previous: Websites
- Next: Statistics >>
- Last Updated: Feb 13, 2024 3:25 PM
- URL: https://rmit.libguides.com/logistics

7 Compelling Examples of Supply Chain Management – Apple, Walmart, CocaCola, Amazon, Nike, Starbucks, Zara
In this comprehensive pist we discuss the examples of Supply chain management of Iconic companies that have redefined our lives in many ways. From technology companies like Apple to Retail Giants like Walmart and Zara and to our everyday coffee from Satrbucks, we have covered it all.
Examples of Supply Chain Management: Apple with Case Studies
The Apple supply chain is a prime example of innovation at its best. From product conception to customer delivery, Apple’s supply chain management is renowned for its efficiency and effectiveness. This is evident in their ability to consistently produce high-quality products and meet customer demands while maintaining a competitive edge in the market.
One key aspect of Apple’s supply chain is their focus on vertical integration. By owning and controlling various stages of the supply chain process, such as manufacturing, distribution, and retail, Apple can ensure a seamless flow of products from production to the hands of consumers. This not only allows for more control over quality and delivery times but also enables them to respond quickly to changing market trends and customer demands.
A case study that highlights Apple’s efficient supply chain management is their launch of the iPhone X. Despite the complexity of manufacturing and assembling the device, Apple was able to successfully meet the high demand and deliver it to customers in a relatively short period. This was made possible by their meticulous planning and coordination with suppliers, ensuring a steady supply of necessary components and materials.
Another notable aspect of Apple’s supply chain is their commitment to sustainability . This is demonstrated through their efforts to reduce the environmental impact of their operations, such as using renewable energy sources and recycling materials. Apple’s dedication to sustainability not only benefits the environment but also positively impacts their bottom line by reducing costs and enhancing their brand reputation.
Furthermore, Apple’s supply chain management is supported by advanced technology and data analytics. With the help of cutting-edge software and real-time data, Apple can track inventory levels, monitor supplier performance, and optimize their supply chain processes. This enables them to make informed decisions, minimize waste, and improve overall efficiency.
Overall, the Apple supply chain exemplifies innovation at its best. Through vertical integration, sustainability initiatives, and the use of advanced technology, Apple continues to revolutionize the way products are manufactured, distributed, and consumed. Their supply chain management serves as a benchmark for other companies, showcasing the importance of agility, sustainability, and technology in achieving success in today’s dynamic market.

Examples of Supply Chain Management: Supply Chain Management for Walmart
Walmart’s efficient supply chain is the backbone of its success in keeping prices low and shelves stocked. With over 11,000 stores worldwide and a revenue of $524 billion in 2020, Walmart is known for its ability to deliver quality products at affordable prices. This is largely due to the company’s strategic approach to its supply chain management.
One key factor in Walmart’s efficient supply chain is its strong vendor relationships. The company works closely with its suppliers to ensure a steady flow of goods, negotiate lower prices, and reduce lead times. For example, Walmart partnered with Procter & Gamble, one of its largest suppliers , to implement a collaborative planning, forecasting, and replenishment ( CPFR ) system. This system allows Walmart to share sales data with P&G, enabling both companies to better forecast demand and restock inventory in a timely manner.
Another aspect of Walmart’s efficient supply chain is its advanced technology and data analytics capabilities. The company utilizes a cutting-edge inventory management system that tracks sales in real-time and automatically triggers reordering when necessary. This system helps Walmart optimize its inventory levels, reducing the risk of overstocking or stockouts.
Additionally, Walmart’s distribution network plays a crucial role in its supply chain efficiency. The company operates a vast network of distribution centers strategically located near its stores. This allows for shorter transportation times and enables Walmart to quickly restock shelves. In fact, the retailer’s distribution centers are known for their quick turnaround times, with an average of just 24 hours from receiving goods to shipping them to stores.
Lastly, Walmart’s supply chain efficiency is achieved through a strong emphasis on sustainability and environmental responsibility. The company has implemented various initiatives to reduce waste and increase energy efficiency in its supply chain operations. For instance, Walmart aims to achieve zero waste to landfill in its U.S. operations and has made significant investments in renewable energy.
In conclusion, Walmart’s efficient supply chain is a driving force behind its ability to keep prices low and shelves stocked. By maintaining strong vendor relationships, leveraging advanced technology and data analytics, optimizing its distribution network, and prioritizing sustainability, Walmart has built a supply chain that maximizes efficiency and ultimately benefits its customers.

Examples of Supply Chain Management: Supply Chain Management for Coca-Cola

Coca-Cola is known for its refreshing beverages, but behind the scenes, it also boasts a global supply chain that ensures its products reach consumers around the world. With operations in over 200 countries, the company’s supply chain is a complex and highly efficient network.
One key aspect of Coca-Cola’s supply chain is its distribution system. The company has strategically located bottling plants, warehouses, and distribution centers to minimize transportation costs and ensure timely product availability. For example, in 2020, Coca-Cola opened a new distribution center in Singapore, strategically positioning itself to serve the Southeast Asian market.
Another crucial element of Coca-Cola’s supply chain success is its focus on sustainability. The company has set ambitious goals to reduce its carbon emissions and improve water stewardship. For instance, by 2020, Coca-Cola successfully replenished 100% of the water it used in its beverages, making it the first Fortune 500 company to achieve this feat.
Technology also plays a significant role in Coca-Cola’s supply chain management. The company utilizes advanced analytics and artificial intelligence to optimize its production processes and enhance demand forecasting. By harnessing the power of data, Coca-Cola can streamline its operations, minimize waste, and meet customer demands more efficiently.
Furthermore, Coca-Cola has implemented an effective supplier management system to ensure quality and consistency throughout its supply chain. The company works closely with its suppliers to maintain high-quality ingredients and materials, fostering long-term relationships based on trust and collaboration.
Overall, Coca-Cola’s global supply chain is an exemplar of efficiency, sustainability, and innovation. With its strategic distribution system, focus on sustainability, utilization of technology, and strong supplier management, the company continues to refresh the world with its products while minimizing its environmental impact.
Examples of Supply Chain Management: Amazon’s Supply Chain Management

Amazon’s supply chain success can be attributed to several factors that have allowed the company to transform from an online bookstore to the world’s largest online retailer of virtually everything. One of the key elements of Amazon’s success is its ability to anticipate customer demand and deliver products quickly and efficiently. This is made possible through the company’s extensive network of distribution centers strategically located around the world, which has allowed Amazon to achieve fast delivery times and low shipping costs.
Another factor contributing to Amazon’s supply chain success is its use of advanced technology and data analysis. The company’s sophisticated algorithms and machine learning capabilities enable it to optimize inventory management and streamline order fulfillment processes. This has resulted in reduced inventory holding costs and improved overall operational efficiency.
In addition, Amazon has leveraged its vast network of third-party sellers to expand its product offerings and increase customer choice. This has not only allowed the company to diversify its revenue streams but also enabled it to take advantage of economies of scale and reduce costs. By collaborating with third-party sellers, Amazon has been able to tap into their existing supply chains, further strengthening its own supply chain capabilities.
Furthermore, Amazon’s success can also be attributed to its relentless focus on customer satisfaction. The company’s commitment to delivering exceptional customer service has resulted in high customer loyalty and repeat business . Amazon’s supply chain plays a crucial role in ensuring that customers receive their orders on time and in good condition, which has contributed to its reputation for reliability and trustworthiness.
Overall, Amazon’s supply chain success can be attributed to its ability to anticipate customer demand, use advanced technology and data analysis, leverage its third-party seller network, and prioritize customer satisfaction. These factors have allowed Amazon to expand its product offerings, reduce costs, and provide an unparalleled online shopping experience for consumers worldwide.
Examples of Supply Chain Management: Nike’s Supply Chain Management
Nike, the global sportswear giant, has revolutionized the athletic footwear and apparel industry with its efficient and stylish supply chain. The company’s supply chain management practices have enabled it to quickly respond to market trends, reduce costs, and deliver products to consumers all over the world.
One of the major strengths of Nike’s supply chain is its strong relationships with suppliers. Through collaborations and partnerships, Nike has been able to ensure consistent quality and timely delivery of materials. For example, Nike collaborated with suppliers to develop the Flyknit technology, which allowed for lighter and more sustainable footwear. This not only lowered production costs, but also reduced waste and improved the overall sustainability of Nike’s supply chain.
Furthermore, Nike has implemented cutting-edge technology to optimize its supply chain operations. The company constantly monitors and analyzes data to identify areas for improvement and make informed decisions. In fact, Nike leverages data analytics to forecast demand, and this helps the company optimize inventory levels and reduce production costs. For instance, by using demand sensing technology, Nike reduced its lead time by 83%, resulting in faster product delivery and increased customer satisfaction.
Nike’s supply chain also stands out for its commitment to social responsibility. The company is dedicated to ensuring safe and fair working conditions in its supply chain facilities. Through its Supplier Code of Conduct and Sustainable Manufacturing and Sourcing Program, Nike has implemented initiatives to address issues such as child labor, forced labor, and environmental sustainability. This commitment to responsible sourcing has not only enhanced Nike’s brand image, but also helped attract socially conscious consumers.
Lastly, Nike’s supply chain is known for its agility and responsiveness. The company has a robust distribution network that enables it to quickly respond to changing market demands and deliver products to consumers in a timely manner. Moreover, Nike’s focus on customization and personalization has allowed it to offer unique and innovative products tailored to individual customers. By leveraging digital technologies and advanced manufacturing techniques, Nike has been able to provide a seamless customer experience and stay ahead in the highly competitive athletic apparel industry.

Examples of Supply Chain Management: Starbuck’s Supply Chain Management
Starbucks’ supply chain is renowned for its efficiency and innovation, playing a crucial role in the company’s success. With over 31,000 stores worldwide and millions of loyal customers, Starbucks has built a robust supply chain that ensures a steady flow of quality products from farm to cup.
One key aspect of Starbucks’ supply chain success is its commitment to ethical sourcing . The company works directly with farmers to ensure the sustainability and traceability of its coffee beans. According to a case study by the Harvard Business Review, Starbucks invested in farmer support centers in coffee-growing regions, providing resources and expertise to improve farming practices. This approach not only benefits the farmers by increasing their productivity and income but also ensures a reliable supply of high-quality coffee for Starbucks.
Another major strength of Starbucks’ supply chain is its focus on vertical integration. By owning its coffee farms, processing facilities, and distribution centers, Starbucks has greater control over its supply chain and can respond quickly to changing market demands. This vertical integration strategy has allowed the company to reduce lead times and maintain consistent quality across its stores. For example, Starbucks’ centralized distribution system enables it to deliver fresh coffee beans to its stores within 48 hours of roasting, ensuring a flavorful and aromatic experience for customers.
Innovation is also at the heart of Starbucks’ supply chain success. The company invests heavily in technology to streamline its operations and optimize efficiency. For instance, Starbucks uses predictive analytics to forecast customer demand and manage inventory effectively. By analyzing historical sales data and external factors such as weather patterns, Starbucks can adjust its supply chain accordingly, minimizing waste and ensuring products are available when and where customers want them.
Furthermore, Starbucks’ supply chain is committed to environmental sustainability. The company has set ambitious goals to reduce its carbon footprint and increase the use of renewable energy. According to Starbucks’ 2020 Global Social Impact Report, the company aims to achieve carbon neutrality for its stores and supply chain by 2030. This commitment to sustainability not only aligns with consumers’ increasing demand for eco-friendly products but also helps Starbucks future-proof its supply chain by mitigating the risks associated with climate change.
In conclusion, Starbucks’ supply chain success can be attributed to several key factors: ethical sourcing, vertical integration, innovation, and environmental sustainability. By working directly with farmers, owning its supply chain infrastructure, leveraging technology, and prioritizing sustainability, Starbucks has built a resilient and efficient supply chain that brews success one cup at a time.
Examples of Supply Chain Management: Zara’s Supply chain Management
Zara, the Spanish fashion brand known for its trendy and affordable clothing, has revolutionized the fashion industry with its agile supply chain. By leveraging technology and embracing a fast-fashion business model, Zara has been able to stay ahead of its competitors and rapidly respond to changing consumer demands.
One of the key factors that sets Zara apart is its ability to quickly design, produce, and distribute new clothing lines. Unlike many of its competitors, who may take several months to bring new designs to market, Zara can do it in just a few weeks. This speed is made possible by Zara’s fast and efficient supply chain, which allows the company to quickly analyze trends, design new products, and deliver them to stores in record time.
To achieve this agility, Zara has invested heavily in technology and data analytics. The company uses sales data and customer feedback to identify emerging trends and make data-driven decisions about what products to produce and in what quantities. This data-driven approach has helped Zara minimize the risk of overstock and reduce waste, leading to higher profit margins.
Another key aspect of Zara’s agile supply chain is its vertically integrated production process. Unlike many of its competitors, who outsource their production to third-party manufacturers, Zara produces over half of its clothing in-house. This allows the company to have greater control over the production process, ensuring that it can quickly respond to changes in demand and deliver new products to stores in a timely manner.
Zara’s agile supply chain has not only helped the company stay ahead of its competitors, but it has also contributed to its financial success. According to a case study by Harvard Business School, Zara’s sales have grown by an average of 17% per year over the past decade, while its competitors have struggled to maintain single-digit growth rates. This success can be attributed in large part to Zara’s ability to quickly adapt to changing fashion trends and deliver new products to consumers faster than anyone else in the industry.
In conclusion, Zara’s agile supply chain has revolutionized the fashion industry and set new standards for speed and efficiency. By leveraging technology, embracing a fast-fashion business model, and investing in vertically integrated production, Zara has been able to quickly respond to changing consumer demands and stay ahead of its competitors. This agility has not only helped Zara achieve financial success, but it has also allowed the company to maintain its position as a trendsetter in the fashion world

Samrat is a Delhi-based MBA from the Indian Institute of Management. He is a Strategy, AI, and Marketing Enthusiast and passionately writes about core and emerging topics in Management studies. Reach out to his LinkedIn for a discussion or follow his Quora Page
How to Solve a Supply Chain Case Study Interview
- Last Updated January, 2022
Former Accenture
People can be nervous about approaching a supply chain case study interview.
Everyone has some level of experience with marketing and sales because they see these functions in stores and advertisements every day.
The supply chain that gets the product on a store shelf (whether it’s a physical one or digital) can be more opaque.
Supply chain management is the optimization of the process of designing and creating a good or service and getting it to the customer in the most efficient way possible.
Breaking the supply chain down into its component steps will allow you to look at essential parts of the process and uncover which steps may have problems that need to be addressed to better meet customer needs.
In this article, we’ll discuss:
- The types of business problems that fall under supply chain management,
- Why supply chain matters,
- Key factors to consider in a supply chain case,
- A supply chain case example, and
- Our 7 tips on answering a supply chain case interview question.
Let’s get started!
What Types of Business Problems Fall into Supply Chain Management?
Supply chain management includes:
- Product development,
- Sourcing parts and materials,
- Production,
- Logistics, and
- Information systems that support this process.
Each consulting firm breaks down the group of consultants who work on supply chain problems differently. Some firms put the entire process under supply chain.
In others, “production” problems are managed by an operations practice or service line. The supply chain practice is responsible for issues like:
- How does a company get the necessary components that go into making its product in a cost-effective and timely fashion?
- And how does the company deliver that product to the end-customer efficiently and at the required service level?
For example, before a company can manufacture a bike, it needs tires, steel, or aluminum for the frame, the bike chain, etc. To get the finished bike to market, they need transportation to retail stores or a chain’s distribution warehouse.
For the purpose of this article, we’ll look at the broader definition of supply chain, the entire process from getting components parts, to manufacturing the product and delivering finished goods as cheaply and efficiently as possible while meeting or exceeding service level expectations.
Nail the case & fit interview with strategies from former MBB Interviewers that have helped 89.6% of our clients pass the case interview.
Why Does the Movement of Goods To & From a Factory Matter So Much?
Moving goods to and from a factory might not seem to be the most exciting thing in the world but it’s fundamental to business success. If you can’t get your innovative new product to market so your customers can buy it, it can’t add value to your bottom line.
From a financial perspective, there are both inbound and outbound considerations.
Inbound considerations include:
- Transportation costs from supplier to factory/warehouse
- Warehousing cost
- Carrying cost of inventory
Outbound considerations include:
- Transportation costs from factory to customer or store
Let’s look at these in more detail.
Transportation Cost
Transportation costs include both receiving goods from suppliers and distributing them to the customer. There are several factors to be considered when calculating transportation costs, and they may have to be weighed against other factors.
For example, is it more beneficial to use a cheaper supplier that has higher inbound transportation costs? Is it better to use a more expensive carrier service that results in a lower rate of damaged goods or quicker transit time?
Warehousing Cost
The cost of storing inventory, whether component parts or finished products, needs to be considered in effective supply chain management. Warehousing costs can be significant and can be optimized in a number of ways:
- Only renting the storage space you need and using it efficiently.
- Optimizing product packaging to reduce the storage space required.
- Researching less expensive potential warehousing locations.
- Using a multi-client facility where several businesses share the cost (if not a lot of space is required.)
It’s worth bearing in mind that, like many things in supply chain management, there may be tradeoffs. Cheaper warehousing that’s poorly connected to a company’s distribution network could end up costing you more time and money than more expensive storage that’s well connected. It’s important to optimize total supply chain costs, not each individual cost in the supply chain.
Inventory Carrying Cost
In addition to storage costs, there are several other costs associated with holding inventory. These include:
- Capital cost . Money that’s been invested in inventory cannot be used elsewhere.
- Insurance . Storing inventory requires insurance to cover the risk of theft or damage.
- Risk . Products may decrease in value or become obsolete during the time they’re stored.
Similarly, from a customer service level perspective, there are both inbound and outbound considerations.
- Factory/production cell downtime due to lack of component parts.
- Missed sales due to stockout at retail stores.
- Failure to meet customer service-level expectations.
In short, inventory levels are about managing supply vs. demand. If there is a problem with inbound supply, production will slow or cease. This is highly inefficient and reduces potential product profitability.
For example, the blockage of the Suez Canal in early 2021 due to a container ship that ran aground was expected to delay shipment of $9.6 billion in goods a day on the 150+ vessels waiting to travel through the canal according to a BBC article. These delays are expected to cost companies substantial sums due to:
- Lost sales as customers look to competitors to purchase out-of-stock goods,
- Production downtime at manufacturers resulting from parts shortages,
- Higher shipping costs on ships detoured to longer, more expensive sea routes to avoid the canal, and
- Higher shipping costs due to a worldwide shortage of shipping containers that was exacerbated by this accident.
Key Factors to Consider in a Supply Chain Case Study Interview
A supply chain process map.
When analyzing a supply chain case, the best place to start is by mapping out the steps parts go through as they come into the factory, go through the manufacturing and quality control processes, and then are finally shipped to the customer. A process map like the one above will help you identify key steps.
Imagine yourself walking the production floor following the process the parts and end-product go through. In a supply chain case with an actual client, you’ll do this.
An effective supply chain moves the various elements seamlessly in the most efficient manner, minimizing waste and maximizing profitability. The flow of information between supplier and buyer, production, and the market should also move freely. This means it can be used to improve supply chain decisions. For example, an increase in orders at Manufacturer A will be communicated to their supplier, Company B, so that they know that they expect a larger than normal parts order and are prepared to fulfill it.
Imagine How Raw Materials Arrive at a Factory and Move Through It
- What steps are required to get parts into inventory?
- Where are they stored?
- How are they moved around the factory?
- How are they changed to outputs – single step or multiple?
- Is there an assembly step? A quality control step?
- How are they packaged and stored?
- Where and how are they prepared and loaded for delivery to market?
Tip! Look for steps in the process where inventory is piling up. This may be because parts supply or production is unbalanced, reducing efficiency. Find ways to improve these bottlenecks.
Tip! Look for areas where there are significant problems with quality control. Parts or products that need to be sent back to suppliers or go through production rework are opportunities to improve efficiency and quality and, by doing so, save money.
After you have a clear understanding of the company’s supply chain, there are 4 factors you’ll want to dive deeper into to find opportunities to improve efficiency:
- Operational considerations,
- Financial considerations,
- Service levels, and
- Matching supply and demand.
Operational Considerations
The best supply chains are highly efficient, which means they have low to minimal waste and consistently operate at optimum levels. This means that labor capacity is well-matched to production requirements.
They are also reliable with robust supplier relationships and an effective transportation solution.
Questions to Ask about Operational Efficiency
- Product development
- How well do we understand customer needs and use that insight to develop next-generation products?
- How efficient are we at designing new products to meet these customer needs?
- Is there a good split of engineering resources allocated to incremental product improvements versus next-generation product design?
- Do we regularly review contracts for cost-savings opportunities (both for direct spend on components that go into our end-products and indirect spend on things such as travel and office supplies)?
- Do we optimize total cost of ownership rather than individual component costs?
- Is the production process optimized or does work-in-process accumulate behind bottlenecked resources (equipment or employees)?
- Does the factory experience production shut-downs due to a lack of raw materials?
- Does the factory experience unexpected equipment downtime?
- Are employees cross-trained to minimize rework?
- How efficient is the inbound transportation network? Are raw materials received on a just-in-time basis? How often are there stock-outs?
- How efficient is the outbound transportation network? Are end products received by customers on time?
- Are there product defects or quality issues caused by transport?
- Information systems that support this process
- Do information systems support the exchange of data up and down the supply chain to optimize decision-making?
Financial Considerations
There are both fixed and variable costs associated with getting a product to market that should be considered.
Fixed Production Costs
Fixed costs are costs that are independent of production volume (at least over the short term) — for example, factory leasing costs.
Let’s assume a factory can produce a maximum of 10,000 units of a product a year. To lease the factory is the same price whether you produce 1 unit or 10,000 units a year.
Fixed costs can depend on production volume only when it exceeds a threshold volume.
For example, if sales increase and the business needed to produce 15,000 units a year, the company would need to lease another factory to deal with the increased production. In this case, volume does affect a fixed cost.
Fixed costs do directly influence the cost per unit, however. The higher the utilization of the fixed production volume, the lower the cost per unit.
For example, if the factory mentioned above costs $10,000 to lease and the factory is producing at its full capacity of 10,000 units, then the fixed cost/unit of output is $1. If the factory is only running at 50% capacity, the fixed costs/unit of output would double to $2.
Variable Production Costs
Variable costs change in proportion to production volume. For every additional unit produced, an additional $x of variable cost is incurred. Examples of variable cost items include raw materials and hourly labor costs.
There are times when rebalancing fixed and variable costs can be an opportunity for savings. For example, is it beneficial to invest in machinery or automation (fixed cost) if it reduces high labor costs? Be sure to look for opportunities like this as well as optimizing fixed and variable costs on their own.
Questions To Ask About Financial Optimization
- How do increases and decreases in production impact fixed and variable costs?
- Are there variable costs that fixed costs could replace? (Example: new machinery that could reduce labor costs as well as total costs of production?)
- Are there fixed costs that could be reduced through outsourcing? (Example: costs of leasing and managing a warehouse that could be reduced by outsourcing?)
- Where are the biggest opportunities for financial savings?
- How could reducing or increasing costs affect other considerations such as operational efficiency?
Service Levels
In supply chain management, the term service level has a specific meaning. It relates to how well inventory levels fulfill customer orders. A good service level is one that can fulfill customer orders without incurring a delay.
This is important because customer loyalty may decrease if products are consistently out of stock.
Questions To Ask About Service Levels
- What are the clients’ service level expectations?
- How often are customer orders fulfilled successfully?
- How would changing service levels affect buyer behavior or customer retention?
- How would changing service levels increase or decrease costs?
Supply and Demand
Effective supply chain management is about ensuring demand for the product is equaled by supply, at the lowest cost to the business.
If demand is higher than supply, customers could turn to a competitor.
If supply is higher than demand, inventory costs can reduce profit margins. Storing inventory also increases business risk as the product may decrease in value or become obsolete as it waits to reach the market.
Questions To Ask About Supply And Demand
- What factors influence supply?
- What factors influence demand?
- How good is the organization at forecasting demand?
- How flexible is the organization at changing output (e.g., are workers cross-trained for different production cells?)
- How well are supply and demand currently balanced?
- If they are imbalanced, what factors are contributing to this and how can those issues be fixed?
Supply Chain Case Study Interview – A Sample Question
Problem: Intel is the world’s largest manufacturer of computer chips. In 2008, Intel launched its low-cost “Atom” chip . The supply chain costs of Intel’s chips were about $5.50 a chip, which were acceptable for chips that sold for $100 each. For the Atom chips, priced at $20, these costs were too high to generate a profit.
What factors should Intel consider in order to reduce its supply chain costs, and what actions would you recommend as a priority?
Mapping the Supply Chain
Mapping out the supply chain process for Intel’s Atom chip identified several steps that had already been optimized including:
- Raw material costs,
- Packaging costs, and
- Duty payments.
It also identified that customers required a 2-week service level for receiving orders after a purchase order was submitted.
However, the order cycle for the Atom chip was 9 weeks. Order-cycle time is the time between when a customer order is received and when the goods are shipped. High levels of inventory were required to ensure that customer service levels could be met despite the long production cycle time.
Because of this, production time/inventory was identified as the key step that had opportunities for improvement.
Identifying Opportunities to Reduce Production Time and Inventory
The process for reducing inventory required reducing the order cycle time to meet the customer’s 2-week required service level. Getting to a 2-week cycle time from a 9-week cycle time was a considerable challenge. To meet this challenge, opportunities to improve order cycle time were addressed throughout the supply chain process.
As described above, for a supply chain case, there are 4 main factors to consider:
- Service levels, and
- Supply and demand.
In drilling down on this case, the following opportunities were identified:
- Financial: Intel moved to a vendor-managed inventory model where possible to save inventory carrying costs. Vendor-managed inventory is the process of having a parts manufacturer take responsibility for holding the required amount of inventory at the customer location.
- Operational: The team was able to identify multiple production process improvements to reduce order cycle time, such as cutting the chip assembly test from 5 days to 2 days.
- Service levels : As mentioned, the 2-week required service level was not flexible, providing no opportunities in this area.
- Balancing supply and demand: Intel introduced a formal sales and operation planning process to provide better demand forecasts and time production to better meet demand.
Our 7 Tips on Answering a Supply Chain Case Interview Question
Tip 1: walk through the supply chain process.
Start by mapping out the step-by-step supply chain process.
Understanding how materials arrive from suppliers, the steps to turn them into outputs, and what’s needed to get them to market is an important first step. Once you’ve done this, look for bottlenecks or inefficiencies in the system.
Tip 2: Clarify Your Understanding of the Case
At the start of any case study, it’s important to make sure you understand the question. This includes any information you’ve received about the case and also what you think you need to do to solve it.
A simple way to do this is to repeat back to the interviewer what you know about the case and what you believe the task to be. This gives them an early opportunity to guide your thinking if you look to be going off track.
Tip 3: Ask Questions
If you don’t understand anything, ask! Even if you feel you should know something, there’s no point wasting time worrying about it. Just ask the question and move on.
Similarly, if there are gaps in the data provided, or you need more information in order to form a hypothesis or conclusion, ask your interviewer for more detail. They may provide further information that helps you choose an approach or strengthens your analysis.
Tip 4: Take Time to Structure your Thinking
Don’t be afraid to take your time when structuring your approach to the case.
Moments of silence can feel endless in an interview situation, but it’s better to use some extra thinking time and respond clearly and logically than answer immediately in a rushed or haphazard manner.
If you need more time to think, it’s perfectly ok to signpost that to your interviewer by asking for a little more time to organize your thoughts.
Tip 5: Use A Framework
Frameworks are popular with both candidates and interviewers alike as they bring structure to your analysis.
Case interviews can be daunting, and anxiety can make it tricky to think things through logically. Using a framework provides an anchor to organize your thoughts around and makes it less likely you’ll leave anything out.
In supply chain cases, the supply chain process itself can often be used as your framework.
Tip 6: Share Your Analysis
Speaking of analysis, don’t be afraid to share your thoughts aloud. A case interview should be more of a conversation than an interrogation!
Remember your math teacher always telling you to show your work? The same is true in case interviews.
Explaining your thought process helps the interviewer see how you process and make connections between pieces of information. They may also point out small mistakes in your arithmetic so that they don’t mess up your conclusion.
Tip 7: Provide a Recommendation
At the end of the interview, briefly summarize the information you’ve uncovered about the case and how it’s influenced your thinking. Then clearly state your recommendation for the client’s next steps.
Make sure you also share any other important details, such as any risks associated with your recommendation and how they might be overcome.
In this article, we’ve covered:
- Which business problems supply chain management covers,
- The reasons supply chain management is important,
- The essential considerations of a supply chain case,
- An example of a supply chain case, and
- Our top 7 tips for acing the supply chain case interview.
Still have questions?
If you have more questions about supply chain case study interview questions, leave them in the comments below. One of My Consulting Offer’s case coaches will answer them. Other people prepping for supply chain case interviews found the following pages helpful:
- Our Complete Guide to Case Interview Prep ,
- Case Interview Types , and
- Case Interview Examples .
Help with Consulting Interview Prep
Thanks for turning to My Consulting Offer for advice on supply chain case study interview questions. My Consulting Offer has helped almost 85% of the people we’ve worked with to get a job in management consulting. We want you to be successful in your consulting interviews too. For example, here is how Tanya was able to get her offer from McKinsey.
4 thoughts on “How to Solve a Supply Chain Case Study Interview”
I need to do a power point for an interview. I have to do a Logistics Analyst Case Study answering questions regarding delivery data for the supply chain and I can’t seem to figure out how to go about answering the questions. I need some professional guidance to help me through the process. Thank you.
Supply chain cases are challenging.
If you’d like an overview of how to approach answering a consulting case interview, our Ultimate Guide to Case Interview Prep is your best source. If you’d like a one-on-one coach for case interviews, including learning how to case in as short as a week, you can apply here .
I would like some more information on supply chain cases – interview’s specifically but not only
Hey, Michael,
Here are a couple publically available cases that might help you: Steel Co. from the NYU Stern 2019 casebook. https://drive.google.com/drive/folders/1AImB14ysaUoYBNw-ArtoCtzZA5cADUhy S.A. Shipping from the McCombs Texas MBA Casebook 2017-2018.
Best of luck on your supply chain case prep!
Leave a Comment Cancel reply
Save my name, email, and website in this browser for the next time I comment.
© My CONSULTING Offer
3 Top Strategies to Master the Case Interview in Under a Week
We are sharing our powerful strategies to pass the case interview even if you have no business background, zero casing experience, or only have a week to prepare.
No thanks, I don't want free strategies to get into consulting.
We are excited to invite you to the online event., where should we send you the calendar invite and login information.
Watch: Navigating Your Supply Chain Challenges — Help Is on the Way
Uncertainty is the only certainty in supply chain these days, so implementing the right technology in your operations is key, says Benji Fountain, account manager at enVista .
In Fountain’s view, three major areas have captured the attention of warehouse and supply chain operators today: automation and robotics, applications in the cloud, and artificial intelligence.
“A lot of people are looking to combat the challenges of getting people to work in the warehouse or of retaining them,” he says. “So they're looking at automation and robotics to make their operations more efficient.
“Second,” he says, “I think we've seen a clear shift to the cloud and supply chain applications. A lot of these on-premise solutions are now being hosted in the cloud.
“And the last one that's on everyone's mind is incorporating AI into our supply chain to make it more efficient.”
Fountain believes artificial intelligence may be highly beneficial in inventory management. “Think about where that inventory is sitting, and the analysis you can do when looking at the flow of your inventory,” he says. “Incorporating those metrics that you're pulling from all these different data sources allows you to make the best decisions.”
Sustainability and resilience could easily be two of the most frequently used words by supply chain managers, but “adaptability” is the word Fountain uses to characterize the supply chain space in 2024. When he reviews disruptions in recent years, not least of which is what the pandemic brought on, he says being able to adapt to whatever comes one’s way is essential. COVID-19 revealed the inadequacy of the just-in-time inventory model, he says. Then, in post-pandemic days, too much safety stock was kept on hand.
“I think being able to adapt on your feet and make those decisions to run an optimal supply chain is going to be the key,” Fountain says.
RELATED CONTENT
RELATED VIDEOS
Watch: Supply Chain Ecosystem Integration: Tearing Down the Silos
Subscribe to our daily newsletter.
Timely, incisive articles delivered directly to your inbox.
Popular Stories
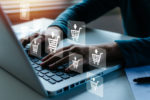
E-Commerce Boom: Easing Supply Chain Pressure with Omnichannel Supply Chains
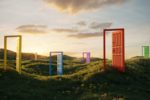
Podcast | Thinking Beyond Cost: New Executive Priorities for Supply Chains
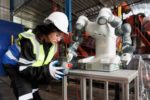
The Imperative for Responsible AI Integration in Manufacturing
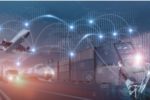
Driving Tech Adoption for Supply Chain Visibility and Sustainability
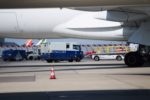
Air Canada Staff Are Suspects in Heist of 6,600 Gold Bars
Digital edition.
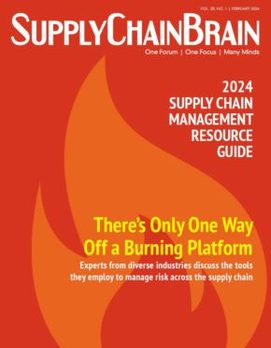
2024 Supply Chain Management Resource Guide: There's Only One Way Off a Burning Platform
Case studies, recycled tagging fasteners: small changes make a big impact.

Enhancing High-Value Electronics Shipment Security with Tive's Real-Time Tracking

Moving Robots Site-to-Site
Jll finds perfect warehouse location, leading to $15m grant for startup, robots speed fulfillment to help apparel company scale for growth.

IMAGES
VIDEO
COMMENTS
L'Oréal: A Case Study in Supply Chain Excellence. Supply Chain Shaman. OCTOBER 5, 2018. to This is an example of managing a balanced portfolio and of driving a supply chain revolution. This case study is the best example we have seen of a customer-centric supply chain. In China, for example, more than 40% of the company's business through eCommerce.L'Oréal's Performance Compared to ...
Four case studies will be presented, namely, 7-11, Tesco, Walmart, Amazon and Zappos. - 7/11 is another popular case study in supply chain management. The integration of information technology between stores and its distribution centers play the important role. Since the size of 7/11 store is pretty small, it's crucial that a store manager ...
New research on supply chains from Harvard Business School faculty on issues including supply chain management, digital supply chains, and improving global supply chains. Page 1 of 59 Results ... In a recent case study, Willy Shih examines factors that go into deciding where companies should locate production centers. ...
Click on the "View Library" button (arrow 1) in upper right corner of the Account Management screen. In the Library screen you see a list of available supply chain case studies; click " Import " to load a selected case study into your account; give the imported case a Name, and click " My Account " to go back to your Account ...
From a fundamental perspective, supply chain management (SCM) is the management of the flow of goods, data, and finances related to a product or service. In manufacturing, it involves all the processes for creating and delivering a product from the raw material stage to finished goods ready for the customer. ... SCM case study examples would ...
Enhance profitability. Optimization typically leads to 5%- 10% net annual savings in total logistics operating costs, impacting: Transport costs. Fixed facility costs. Variable handling costs. Terminal productivity increases resulting from 'right-sizing'. Network analysis secures future performance of the supply chain given volatility in ...
New research on supply chain management from Harvard Business School faculty on issues including what brands can do to monitor their suppliers' factory conditions, how Japan's earthquake and tsunami and caused havoc on retailers and car manufacturers, and the push to improve labor standards in global supply chains. ... A case study by William ...
Case Study: How Should We Diversify Our Supply Chain? Summary. In the wake of Covid-19's disruptions, Kshore, a Chinese appliance maker, is thinking of realigning its supply chain. Like many ...
Accenture's supply chain resilience case study shows how it optimized supply chain operations for leading food & beverage companies. ... Fill Rate (CFR), was only reaching about 84%—some 11-12 percentage points below pre-pandemic performance. So, for example, a retailer looking to stock 100 bottles of a product may only receive 84 at the ...
Supply chain optimization keeps customers connected around the world. The forward-thinking EY supply chain model diversifies production and minimizes risk. 3. For a leading electronics provider that serves millions of customers around the world, keeping the organization's supply chain operating smoothly is of paramount importance.
Omnichannel shopping is the baseline expectation for customers, as companies such as Gap, Target, and many others have upped their omnichannel game. And Macy's is, er, behind. Macy's way of viewing their supply chain in the past was traditional: Move products from point A to point B and optimize costs at each stop along the way.
In this context, Walmart, the world's largest retailer, has demonstrated a highly successful and integrated Walmart supply chain, propelling its growth and dominance in the retail industry. This case study aims to delve into the significance of supply chain capability for enhancing a company's competitiveness and how it serves as a ...
In a recent case study, the large mining player developed an optimization-based process to improve the supply chain of its trains, vessels, and mine operations over short- and medium-term horizons. The process was aligned with the company's strategic target regarding customer specifications and overall production goals.
The seven case studies in this article each highlight a supply chain cost-management challenge faced by a large enterprise. Each case study briefly describes the company and its background, the nature of the challenge, the approach that was taken to overcome it, and the successes achieved.
The following seven mini case studies explore a few high-profile companies that have managed to sustain their supply chain cost-reduction efforts and keep expenses under control. The challenges faced by these organisations and the steps they took, may provide some inspiration for successful long-term cost management within your organisation ...
Limitations of this study are primarily based on IKEAs available of information on its sustainability efforts, to. vast to be explored in this case study. IKEA is recognised for a strong corporate ...
Case Study Research 237 2 Supply Chain Management "The supply chain encompasses all activities associated with the flow and trans-formation of goods from raw materials stage (extraction), through to the end user, as well as the associated information flows. Material and information flow both up and down the supply chain.
Managing the Inbound Supply Chain. Penske helped this supplier minimize supply chain disruptions by designing a network that optimized mode selection, routing and analysis. Read supply chain case studies about our work with customers to create supply chain management solutions that support long-term growth and profitability.
Emerald Emerging Markets Case Studies (EEMCS) Cases are written by case writers working in, or closely with, developing economies. They offer local perspectives with global appeal. The collection receives regular content updates throughout the year and all cases benefit from a supportive peer-review process to ensure the highest quality content.
This case study will show you the analysis of Apple's Supply Chain core processes, challenging issues and complexities of its operations. Supply Chain 24/7 Transportation. ... Supply chain management is about the relationship between trading partners. ... based on example characteristics, Amazon's Supply Chain is far more complicated than ...
Examples of Supply Chain Management: Apple with Case Studies The Apple supply chain is a prime example of innovation at its best. From product conception to customer delivery, Apple's supply chain management is renowned for its efficiency and effectiveness. This is evident in their ability to consistently produce high-quality products and meet customer demands while maintaining a competitive ...
Invest a set number of hours in case interview practice each week. This way, it will become clear how many hours exactly you'll need to improve. Normally 4-5 hours per week of case practice per week is the minimum needed. Time spent reviewing past cases is one of the most important things you can do to improve.
This Summary of Findings and Recommendations summarizes the Case Studies in Cyber Supply Chain Risk Management series' major findings and recommendations based on expert interviews. The Case Studies in Cyber Supply Chain Risk Management series engaged information security, supply chain, and risk leaders across a diverse set of organizations.
Effective supply chain management is about ensuring demand for the product is equaled by supply, at the lowest cost to the business. ... An example of a supply chain case, and; Our top 7 tips for acing the supply chain case interview. ... Thanks for turning to My Consulting Offer for advice on supply chain case study interview questions. My ...
Uncertainty is the only certainty in supply chain these days, so implementing the right technology in your operations is key, says Benji Fountain, account manager at enVista.. In Fountain's view, three major areas have captured the attention of warehouse and supply chain operators today: automation and robotics, applications in the cloud, and artificial intelligence.