
- SUGGESTED TOPICS
- The Magazine
- Newsletters
- Managing Yourself
- Managing Teams
- Work-life Balance
- The Big Idea
- Data & Visuals
- Reading Lists
- Case Selections
- HBR Learning
- Topic Feeds
- Account Settings
- Email Preferences

Supply chain management
- Business management
- Operations and supply chain management
- Operations strategy

Building a Supplier Diversity Program? Learn from the U.S. Government.
- Chris Parker
- Dwaipayan Roy
- February 09, 2024

One Way to Build More Resilient Medical Supply Chains in the U.S.
- Douglas Hannah
- February 16, 2021
Tug-of-War (HBR Case Study and Commentary)
- Yossi Sheffi
- Shakeel Mozaffar
- Robert W. Moffat Jr.
- John D. Blascovich
- Nick Lahowchic
- From the September 2005 Issue

What We've Learned About Fighting Ebola
- Ranu S Dhillon
- Devabhaktuni Srikrishna
- July 16, 2015
Crime and Management: An Interview with New York City Police Commissioner Lee P. Brown
- Alan M. Webber
- From the May–June 1991 Issue
The Japan Earthquake Rattles Supply Chains, Too
- Willy C. Shih
- March 23, 2011
Innovate at Your Own Risk: Deborah Wince-Smith on Competitiveness
- Gardiner Morse
- From the May 2005 Issue

Supplier Diversity Programs Are Failing Black-Owned Businesses
- Denise Hamilton
- April 19, 2021
Is Your Supply Chain Ready for the Congestion Crisis?
- George Stalk, Jr.
- Petros Paranikas
- June 22, 2015
Fit Products and Channels to Your Markets
- Robert E. Weigand
- From the January 1977 Issue

Aligning Incentives in Supply Chains (HBR OnPoint Enhanced Edition)
- V.G. Narayanan
- Ananth Raman
- November 01, 2004

How Kenvue De-Risked Its Supply Chain
- Michael Altman
- Atalay Atasu
- Evren Özkaya
- October 18, 2023

The Supply Chain Economy and the Future of Good Jobs in America
- Mercedes Delgado
- Karen Mills
- March 09, 2018

A Simpler Way to Modernize Your Supply Chain
- David Simchi-Levi
- Kris Timmermans
- From the September–October 2021 Issue

Global Supply Chains in a Post-Pandemic World
- Willy C Shih
- From the September–October 2020 Issue
Break the Paper Jam in B2B Payments
- Steve Berez
- Arpan Sheth
- From the November 2007 Issue

The Latest Supply Chain Disruption: Plastics
- Bindiya Vakil
- March 26, 2021
Talent Management for the Twenty-First Century
- Peter Cappelli
- From the March 2008 Issue
The New Tools of Trade
- Regina M. Abrami
- Leonard Bierman
Putting the Service-Profit Chain to Work
- James L. Heskett
- Thomas O. Jones
- Gary W. Loveman
- W. Earl Sasser, Jr.
- Leonard A. Schlesinger
- From the March–April 1994 Issue

How Machine Learning Will Transform Supply Chain Management
- Morris A. Cohen
- Rohan Deshpande
- Vinayak Deshpande
- From the March–April 2024 Issue

2023: A Strange, Tumultuous Year in Sustainability
- Andrew Winston
- December 28, 2023

How Global Companies Use AI to Prevent Supply Chain Disruptions
- Remko Van Hoek
- Mary Lacity
- November 21, 2023

Case Study: How Should We Diversify Our Supply Chain?
- Krishna G. Palepu
- From the November–December 2023 Issue

The Next Supply-Chain Challenge Isn’t a Shortage — It’s Inventory Glut
- PS Subramaniam
- September 29, 2023

Using Technology to Improve Supply-Chain Resilience
- Jonathan Colehower
- September 25, 2023

How Tony’s Chocolonely Created a Purpose-Driven (and Profitable) Supply Chain
- Frans Pannekoek
- Thomas Breugem
- Luk N. Van Wassenhove
- September 11, 2023

Forecasting in Flux: Navigating Uncertainty through Strategic Supply Chain Flexibility
- June 15, 2023

Reducing Forecast Risk with Supply Chain Flexibility Webinar
- June 01, 2023

Rethinking Supply Chains for Greater Efficiency, Resiliency, and Sustainability
- April 27, 2023

How Tracking ESG Metrics Can Help Reduce Costs and Build Supply-Chain Resilience
- April 26, 2023

How to Build Supply Chain Resilience Without Sacrificing ESG Goals or Inflating Costs
- March 29, 2023

A Resilient Supply Chain Built for Competitive Advantage
- March 07, 2023

Marico’s Chairman on Innovating Across Every Part of the Business
- Harsh Mariwala
- From the January–February 2023 Issue

Crate & Barrel Holdings CEO Janet Hayes on Navigating Turbulent Times for Retail
- December 15, 2022

How Smaller Companies Can Bring Manufacturing Closer to Home
- Arnd Huchzermeier
- December 07, 2022

How American Eagle Reinvented Its Fulfillment Strategy
- Shekar Natarajan
- Thales S. Teixeira
- November 07, 2022

3 Ways to Build Trust with Your Suppliers
- Kate Vitasek
- Karl Manrodt
- Gerald Ledlow
- November 04, 2022

Supply Chain Management
- October 09, 2018
STMicroelectronics E-Chain Optimization Project: Achieving Streamlined Operations Through Collaborative Forecasting and Inventory Management
- Barchi Peleg
- November 06, 2004
L'Oreal's ACD Supply Chain Puzzle: Diagnosing the Root Causes of Underperformance
- Ralf W. Seifert
- Richard Markoff
- September 22, 2017
Foremostco, Inc. (A)
- David M. Upton
- Virginia A. Fuller
- October 07, 2003
Marquee: Reinventing the Business of Nightlife
- Anita Elberse
- Ryan Barlow
- Sheldon Wong
- September 03, 2013
KFC UK: Don't Count Your Chickens Before they Hatch (B)
- Frank Rozemeijer
- Finn Wynstra
- December 31, 2019
Ozark Feed and Ag Corporation: The ERP Decision
- Janice H. Hammond
- Paul Kalmbach
- Eric Bernstein
- October 15, 2015
iPhone's Supply Chain Under Threat
- Benjamin Yen
- Minyi Huang
- June 01, 2021
Allbirds: Decarbonizing Fashion
- Michael W. Toffel
- Eren Kuzucu
- August 29, 2021
Hannaford Brothers: Leading the Grocery Channel Transformation
- James L. McKenney
- William T. Schiano
- Theodore H. Clark
- May 26, 1995
Potato Value Chain - A Tale of Two Farmers in Okara
- Syed Zahoor Hassan
- Jawwad Farid Khan
- Fahim Ahmad
- December 01, 2017
Rethinking Distribution Logistics at VASA, Pilkington
- Julio Sanchez-Loppacher
- Marcelo Pancotto
- Maximiliano Fernandez Vera
- November 01, 2013
Turning the Tide: DuPont, Sustainable Seaweed and Pre-Competitive Collaboration
- Andrew Hoffman
- June 11, 2020
- Andrew McAfee
- Mona Ashiya
- September 25, 2001
The Coronavirus (COVID-19) Pandemic and the Global Economy (A)
- Alberto F. Cavallo
- Christian Godwin
- May 12, 2020
Dell: Roadmap of a Digital Supply Chain Transformation
- Maria Jesus Saenz
- Inma Borrella
- Elena Revilla
- December 12, 2021

SATTVA eTECH: Challenges in Embedded New Product Development
- Jishnu Hazra
- January 01, 2017
Toys "R" Us in 1999
- Deidre Sorensen
- August 01, 2000
Environmental Risk Management at Chevron Corp.
- Forest L. Reinhardt
- Monica Mandelli
- Jennifer Burns
- March 10, 1999
Sibanye: Changing Mindsets in Mining through Contextual Leadership
- Caren Scheepers
- September 21, 2016

Patagonia's Path to Carbon Neutrality by 2025, Teaching Note
- Daniel M. Kammen
- Seren Pendleton-Knoll
- Robert Strand
- April 01, 2018

System Selection
- David L. Olson
- January 02, 2014
Farming Down the Drain: Unintended Consequences of the Food Safety Modernization Act's Produce Rule on Small and Very Small Farms
- Donnie Jr. F. Williams
- Ellie Falcone
- Brian Fugate
- May 14, 2021
The Future of Global Supply Chains in a Post-COVID-19 World
- Rajat Panwar
- Jonatan Pinkse
- Valentina De Marchi
- January 17, 2022
Sky Deutschland, Teaching Note
- Katrin Siebenburger Hacki
- July 27, 2017
Growth Strategies in the Pharmaceutical Industry, Teaching Note
- Shantanu Bhattacharya
- Sjiva De Meester
- Sameer Hasija
- August 21, 2015
Popular Topics
Partner center.
- The approach allows each function to understand the assumptions relating to transformation that affect it and how its own assumptions affect others.
- Understanding dependencies enables each function to perform its own design, building, and execution in coordination with other teams.
- A case study of a leading global retailer highlights how the approach harmonizes disparate elements, fosters cross-functional alignment, and promotes an end-to-end transformation.
Subscribe to our Operations E-Alert.
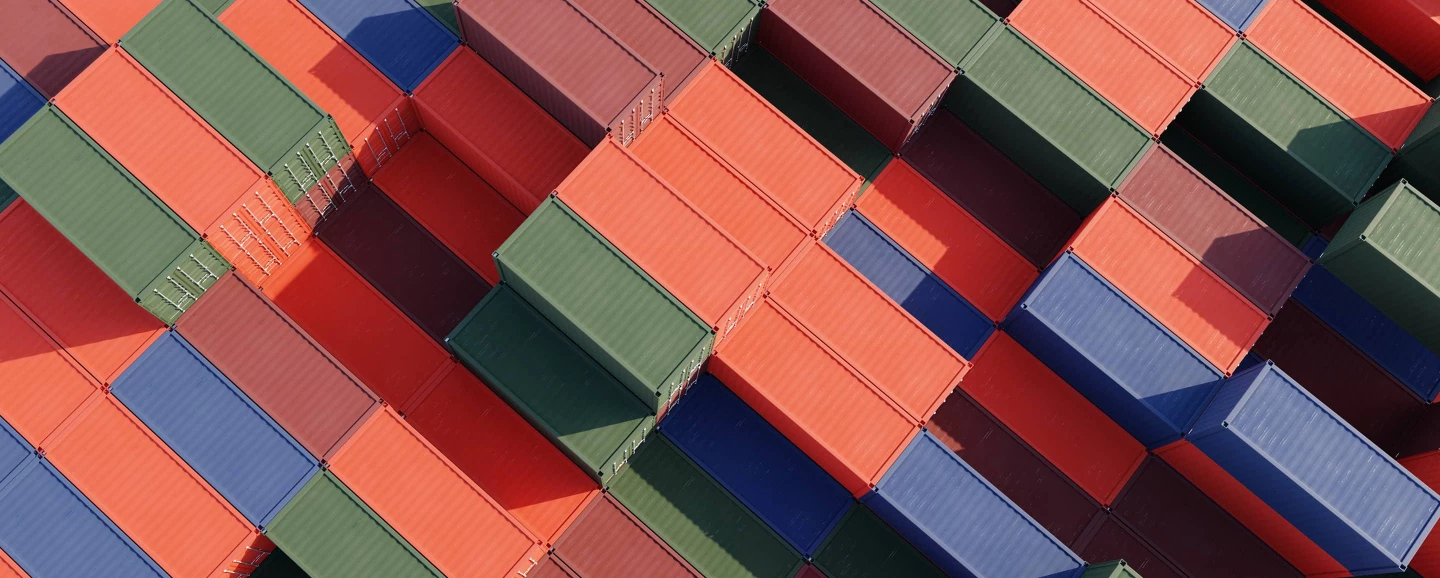
Supply Chain Management
/ article, a unified approach to end-to-end supply chain transformation.
By Michael Hu , Kartik Goel , John Cheru , Ravi Srivastava , and Michael Ryba
Key Takeaways
Supply chains play a leading role in enterprise growth . They are the engine of a virtuous cycle, driving customer satisfaction and, ultimately, higher revenue. But they are often vulnerable to the demand and supply uncertainties of the global landscape.
To increase resilience and improve performance, many companies have set out to transform their supply chains. Like builders constructing a complex house, however, they often must contend with the challenges of coordinating multiple teams, meeting ever-increasing demands for digitization, and adhering to accelerated timelines. As a result, their ambitious transformation initiatives fall short of expectations.
So how can companies ensure that every team involved in a supply chain transformation works in concert? We propose an innovative approach that allows companies to align their disparate supply chain elements with their broader business and commercial aspirations.
Supply Chains Are Essential but Fragile
By ensuring that the right products are available when and where they are needed, a high-performing supply chain enables exceptional customer experiences and fuels a virtuous cycle of growth. (See Exhibit 1.) The cycle starts with superior customer service, which drives demand and traffic. This, in turn, creates growth in revenue and margins. Ultimately, it provides the company with healthy coffers with which to further invest in capabilities such as talent, automation, and the data foundation that will improve customer service.

However, supply chains remain vulnerable to uncertainty and complexity arising from geopolitical volatility, macroeconomic challenges, climate change, technology disruptions, and changing consumer expectations. The pandemic-related supply chain shocks were not a temporary aberration but rather an especially acute illustration of supply chain fragility that will continue to threaten revenue growth.
In 2023, for example, despite an inflation rate exceeding 6%, retail sales continued to grow. The resulting strain on transportation and warehousing capacity drove higher costs—average freight costs in January 2023, for instance, were double those of four years earlier. Geopolitical factors, such as the war in Ukraine, have also intensified pressure on supply chains. Given this challenging environment, the need to strengthen supply chains has never been more pressing.
Transforming Supply Chains Is a Lot Like Building a House
Recognizing the urgency, many companies have launched end-to-end transformation initiatives to boost resilience and enhance their supply chain performance. But most of these efforts fail to meet expectations. In consumer sectors, less than 30% of large-scale supply chain transformations achieve their goals on time and within budget.
To grasp why supply chain transformations typically fall short, consider the building of a house. Homebuilders may start with a clear vision and a high-level blueprint. And they may employ the best architects, construction managers, masonry workers, plumbers, roofers, and electricians. But then the challenges begin. Although all the contractors may excel in their fields and follow the blueprint, they often lack the detailed information necessary to agree on key interfaces, dependencies, and design assumptions. Consequently, early prototypes may exhibit problems like rooms not connecting seamlessly with the roof or electrical wires laid in incorrect locations.
To improve coordination, homebuilders can hire a general contractor to orchestrate the various contractors. While this is a positive step, new problems arise: seamless integration is hampered by differing assumptions among the contractors, by the need to incorporate digital technologies for a “smart” house, and by the pressure to complete work within a reasonable timeframe.
Similar challenges occur when companies attempt to transform their supply chains. Many companies start with a piecemeal approach, addressing only specific aspects of the supply chain. Consider the example of an integrated business planning team establishing an AI-enabled multi-echelon revenue forecast for the end-to-end supply chain. Capturing the promised value from this initiative requires significant cross-functional coordination. The supply chain technology team must provide technological and data support, while the distribution and warehousing team must convert the new revenue forecast into daily labor, inventory, and trucking forecasts.
To remedy the shortcomings of a fragmented approach, the company may embark on an end-to-end transformation. It implements AI-enabled forecasting, for example, as one aspect of a broader transformation that also includes redefining the underlying processes and data foundations to ensure that an improved demand signal translates into better daily or weekly order fulfillment, replenishment, and inventory placement decisions across warehouses and store locations. While this holistic approach has the right level of ambition, it is challenging for three main reasons:
- Coordination. Defining new supply chain processes across various functions in a matrixed organization necessitates significant coordination, as well as collaboration with commercial teams.
- Digital Enablement. Companies need to understand how advanced digital technologies , such as AI and digital twins, can address the pain points in their supply chain. They must also ensure that the underlying data foundation and pipelines are set up to power the technologies.
- The Need for Speed. Transformations must be completed within one to two years, which demands a rapid and highly efficient mobilization to rework processes, capabilities, and data.
Ensuring That All Functions Pursue a Common Goal
To manage the complexity of an end-to-end supply chain transformation, companies need a blueprint that allows each function to understand the assumptions relating to the transformation that affect it and how its own assumptions affect others. The blueprint should also make dependencies, such as those between distribution and ordering, visible to all participants. This will enable each function to perform its own design, building, and execution in coordination with others.
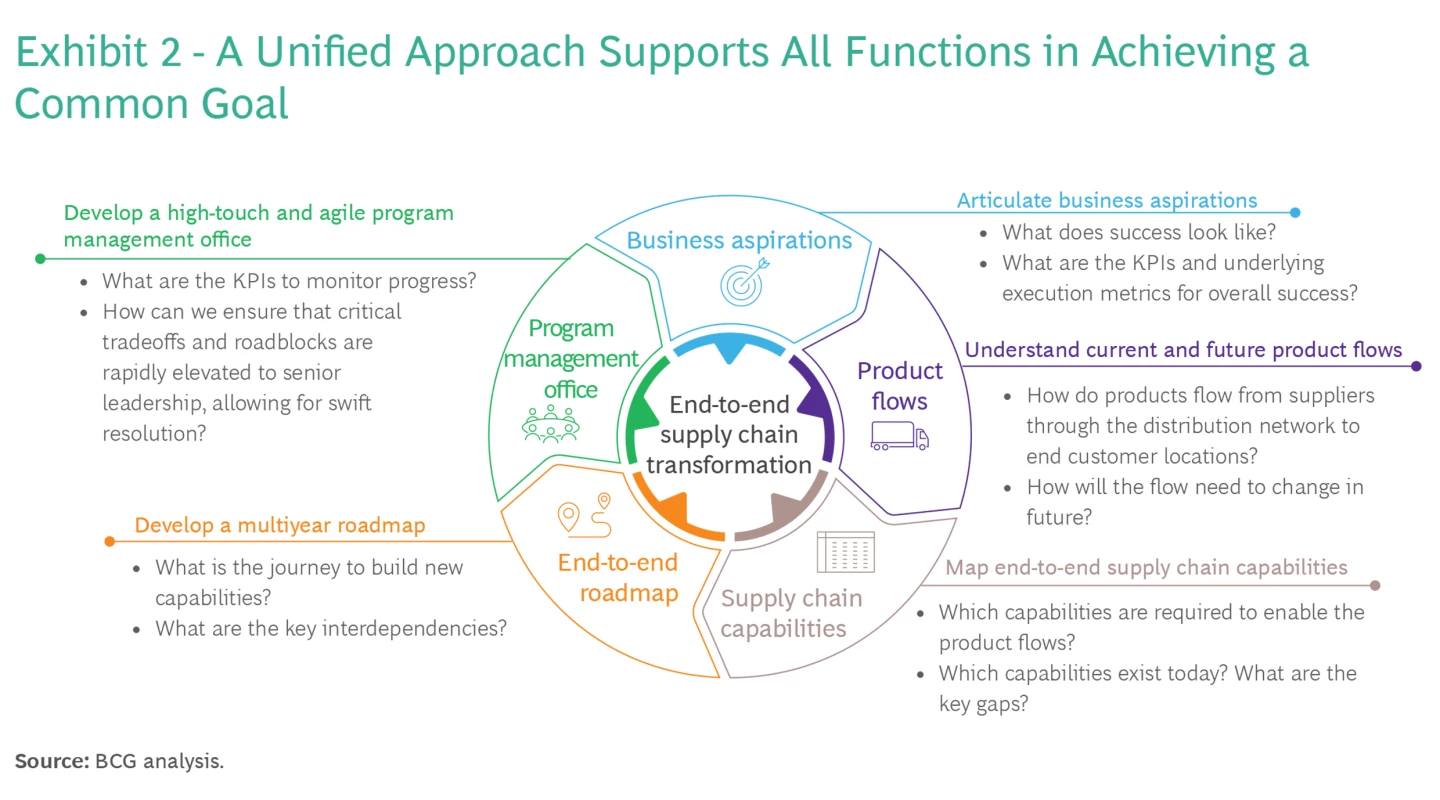
To facilitate the development of this blueprint, BCG has designed an approach composed of five interlocking steps. It ensures coordinated action by providing a strategic and execution roadmap across functions and teams. (See Exhibit 2.)
- Articulate and quantify business aspirations. To guide its efforts, the company must specify what it wants to achieve through the supply chain transformation. It can then determine the KPIs and the underlying execution metrics that contribute to meeting the overall success criteria.
- Understand current and future product flows. The company needs a baseline, granular understanding of how pallets, cases, and individual items flow from suppliers through distribution networks to end customer locations. It uses this information to assess how it must change the product flow to achieve its goals.
- Map end-to-end supply chain capabilities. Understanding product flows allows the company to determine which end-to-end supply chain capabilities it needs today and in the future. It can then pinpoint critical capability gaps and decide how to address them.
- Develop a multiyear capability-building roadmap . The company must determine how to build new capabilities that will enable current and future product flows. This requires identifying which capabilities are prerequisites for others and which ones are critical to completing the transformation.
- Establish a high-touch and agile program management office. To support execution, the company needs to appoint a high-touch and agile PMO. (See Exhibit 3.) This body sets up the transformation program, defining KPIs and key milestones. It also creates the governance structure by assigning responsibilities across functions and developing the meeting cadence for evaluating critical tradeoffs and resolving issues. In addition, the PMO establishes tools and reporting formats, including the use of data analytics to enable more effective and agile decision making.
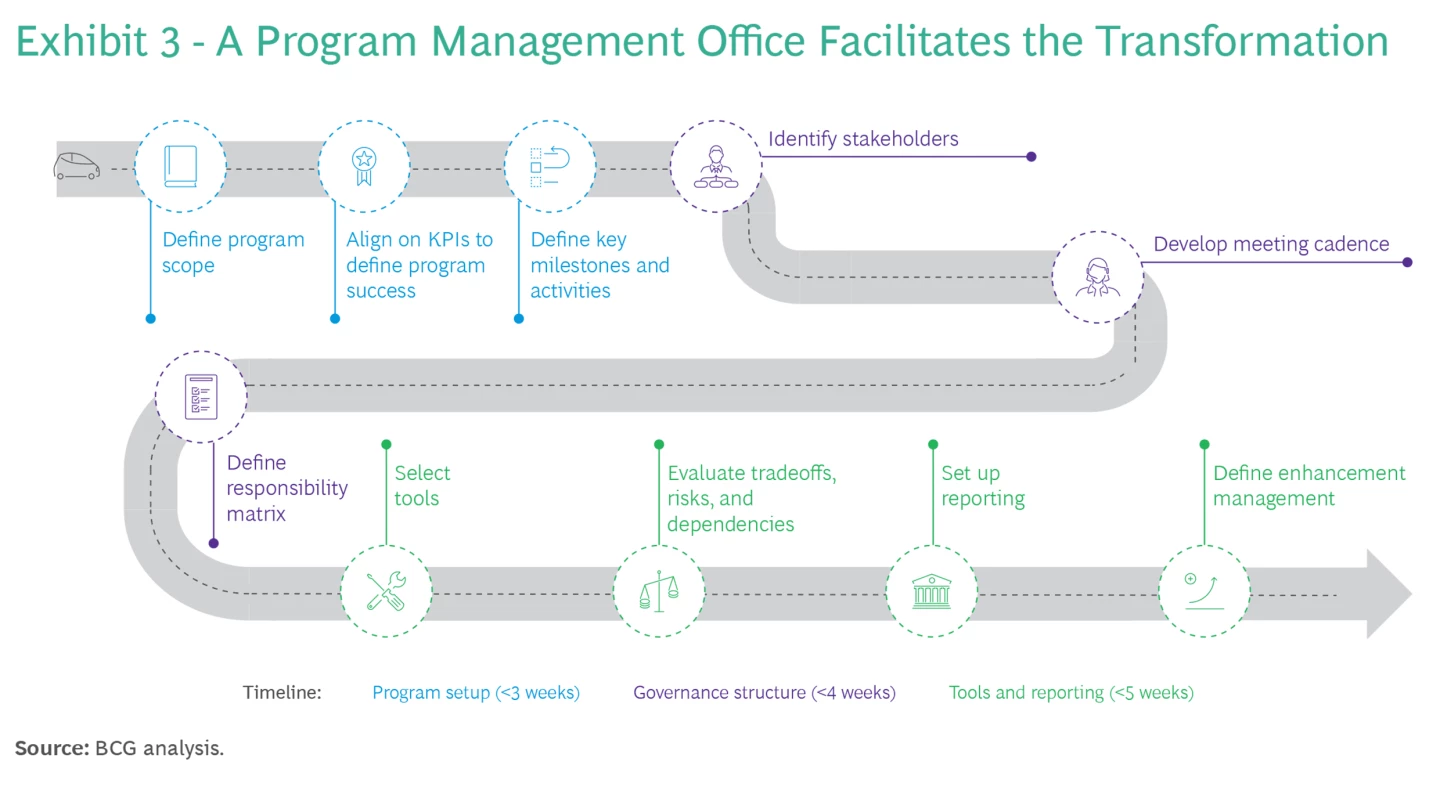
Case Study: Applying the Approach at a Leading Global Retailer
BCG applied this approach to support the end-to-end supply chain transformation of a global retailer. The company’s rapid growth had strained its supply chain and revealed key limitations, especially in cross-functional coordination and data enablement. Finding innovative solutions to these challenges was essential to realizing the company’s ambitious growth plans, including international expansion.
Deploying the Approach
The five-step approach described above provided key insights about the innovations and capabilities required to achieve the company’s goals.
Business Aspirations. We identified increasing revenue by 75% to 100% over the next decade as the primary business aspiration motivating the end-to-end supply chain transformation. We then developed an in-depth understanding of the supply chain implications, including numerical projections for case deliveries, stores in the network, and distribution centers required to service demand. We also identified supply chain innovations needed to achieve these goals, including the introduction of new nodes, such as market distribution centers that stock items closer to the stores and daily multiple deliveries from distribution centers to stores. Other necessary improvements were deploying different truck combinations at different times of day, having drivers manage drops during nonpeak hours, and using customized trucks to co-mingle selected products.
Product Flows. Mapping the end-to-end product flows for the current supply chain helped identify critical gaps. For example, the ordering process lacked essential functionalities for tracking order status, modifying orders, and rerouting orders when necessary. The product flow mapping also highlighted specific shortcomings in the current distribution network that limited its ability to support supply chain innovations.
We then mapped potential future product flows, considering delivery profile (number of drops, time of drop, and volume per drop), location of existing and new nodes (including the possibility of new nodes collocated with existing distribution centers), and type of transportation (including truck size and owned or leased fleets). This assessment helped narrow down the list of key future flows, which facilitated the development of the capability-building roadmap. For the shortlisted flows, we identified the activities needed at each node to realize the envisioned future supply chain.
Supply Chain Capabilities. We mapped each identified activity to an enabling supply chain capability. For example, the company needed an automated order forecasting engine to estimate the next day’s order based on starting inventory, the day’s sales, and heuristics-based forecasts of damaged orders. Such a system can significantly reduce the time that store owners spend placing orders each day.
Some of the key capabilities identified included the following:
- Revamped End-to-End Distribution Network. To support the identified innovations, we proposed investing in new distribution center capacity. This triggered the need to revamp the end-to-end distribution network. Although the new network entailed higher costs and complexity, it gave the retailer greater flexibility and control. The result was higher levels of service and support for product flows than the previous distribution network offered. To initiate implementation, we pinpointed portions of the distribution network that the company could prioritize in the short term and developed a full revamping plan for the long term.
- Digital-First Order Management Platform. The mapping of future product flows revealed that the company needed distributed order management capabilities. These include the ability to add or modify orders, track orders, reroute deliveries to contingent distribution centers in case of disruptions, and track end-to-end inventory. For instance, the company needed the ability to allocate a store owner’s order between the regional and market distribution center on a daily basis, depending on inventory levels at various nodes and delivery times. Recognizing the need for advanced capabilities, the company launched a digital-first order management platform and mobile app to facilitate intuitive and convenient ordering by its store owners.
- End-to-End Data Foundation. A cohesive end-to-end data foundation is a key enabler of a supply chain transformation. Considering future capabilities and product flow requirements, we identified several data gaps relating to, for example, KPIs (such as on-time in-full), end-to-end inventory across nodes, and recommendations for the daily order forecast. To address these gaps, we defined a strategy for capturing the right input data. Steps included requesting data from suppliers, placing GPS devices in trucks, and monitoring and reporting the temperature at distribution centers. We also determined the optimal flow of data to the company’s systems and tools to enable analytics, as well as the channels required to view and monitor output. Further, we supported the company in deploying these strategies, such as by developing and implementing a policy to send and receive key data from suppliers.
The data strategy and process design are mutually dependent. For example, the company needed end-to-end inventory data to support the daily order forecast. This insight led us to include an inventory module in the digital order management platform and to source the inventory data at stores directly from store owners at regular intervals.
Capability-Building Roadmap. We developed the capability-building roadmap for the next three to five years, including the critical interdependencies across various capabilities.
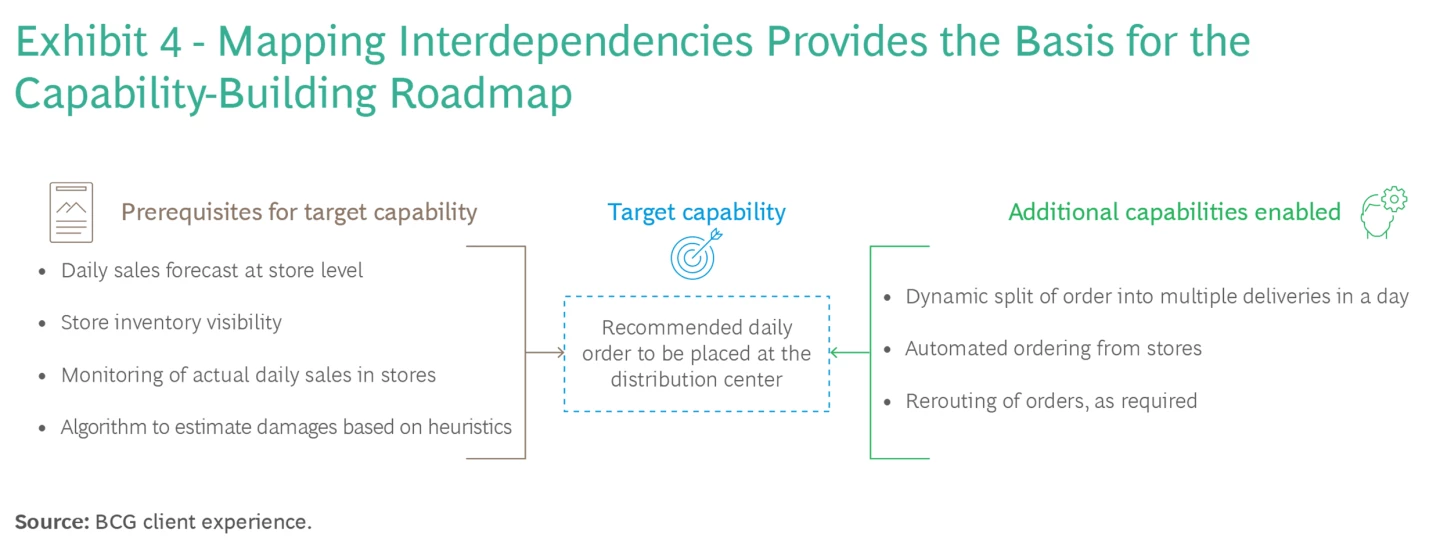
Exhibit 4 illustrates interdependencies relating to the ability to recommend the daily order that store owners should place with the distribution center. The company had to establish four capabilities to enable the daily recommendations. These recommendations, in turn, enable additional capabilities.
Many capabilities necessary to achieve the company’s goal entailed a long chain of interdependencies. Mapping all the capabilities from end to end revealed considerable complexity, necessitating an integrated roadmap to guide the capability-building sequence.
Program Management Office. The PMO facilitated the transformation by addressing several challenges. These included inconsistent ways of working across different teams, the complexity of the resource structure and layers, and an absence of unified incentives. The PMO also significantly streamlined end-to-end execution by developing a weekly meeting cadence for monitoring the most critical KPIs (such as those relating to reducing costs, increasing capacity, and improving quality) using a third-party tracking tool.
Summing Up the Benefits
Since adopting our approach, the company has seen significant improvements in the coordination of design and implementation across functions:
- Alignment on Success Goals. Leaders and their teams understand the key overall goals and how they relate to their own project goals and objectives over three to five years.
- Clear Understanding of Broader Integration. Functional leaders understand how their initiatives fits into the broader initiative, ensuring clear coordination with both upstream and downstream processes and solutions.
- Efficiency and Accountability. The approach has helped to reduce duplicative work and clarified ownership and accountability, streamlining the overall process.
BCG’s innovative transformation approach offers an integrative blueprint for companies seeking to fortify and streamline their supply chain processes. The approach emphasizes the importance of coordination, digital enablement, and speed. Recent successes highlight its efficacy in harmonizing disparate elements, fostering cross-functional alignment, and driving end-to-end transformation. By adopting such a comprehensive strategy, companies can navigate the challenges of supply chain transformation more effectively, thereby setting the foundation for long-term enterprise growth.

Managing Director & Partner
Los Angeles

Managing Director & Senior Partner; Global Leader, Operations Practice

Partner and Director
ABOUT BOSTON CONSULTING GROUP
Boston Consulting Group partners with leaders in business and society to tackle their most important challenges and capture their greatest opportunities. BCG was the pioneer in business strategy when it was founded in 1963. Today, we work closely with clients to embrace a transformational approach aimed at benefiting all stakeholders—empowering organizations to grow, build sustainable competitive advantage, and drive positive societal impact.
Our diverse, global teams bring deep industry and functional expertise and a range of perspectives that question the status quo and spark change. BCG delivers solutions through leading-edge management consulting, technology and design, and corporate and digital ventures. We work in a uniquely collaborative model across the firm and throughout all levels of the client organization, fueled by the goal of helping our clients thrive and enabling them to make the world a better place.
© Boston Consulting Group 2024. All rights reserved.
For information or permission to reprint, please contact BCG at [email protected] . To find the latest BCG content and register to receive e-alerts on this topic or others, please visit bcg.com . Follow Boston Consulting Group on Facebook and X (formerly Twitter) .
- BECOME A CONTRIBUTOR
- WHITE PAPERS
- THE SUPPLY CHAIN DICTIONARY

What is Sales & Operations Planning?
The 4 supply chain metrics, static inventory an untapped source of working capital, s&op, a vision for the future. an interview with eric tinker, improving behaviours in support of world class s&op: coach for excellence.
- Planning & Forecasting Articles
How Can Data Improve Supplier Decisions
Information-based negotiations in the digital age, hurt, help or hero how to define and get more out of your most important suppliers, how to spot supplier risk during pickups & deliveries, how to spot supplier risk during on-site evaluations.
- Procurement & Sourcing Articles
The Long Tail of Inventory and Why It’s Important
No more excuses: transformative iot is staring you in the face, predictive analytics let manufacturers see more clearly into their supply chains, rise of the grocers, how 3d printing is set to shake up manufacturing supply chains.
- Manufacturing & Production Articles
6 Tips for Maximizing Efficiency and Productivity of Warehouse Operations
Robot trucks or autonomous vehicles will revolutionize the supply chain, data integration made sexy, how to avoid the most common warehouse safety hazards, out darn spot out, i say.
- Warhouse & Transport Articles
Returns – A Threat to the Bottom Line or an Opportunity to Cut Costs?
Supply chain sustainability takes root, why the 2030 sustainable development goals matter to packaging professionals, to build sustainable products, listen to your customers, getting packaging costs down to size.
- Reverse Logistics Articles
Transform Your Supply Chain For Omnichannel
The impact of maintenance operations on supply chain management, is your supply chain strategy inside-out or outside-in, how industry benchmarks can boost your asset recovery, supply chain visibility: we should be striving for more.
- Supply Chain Management articles
Accelerating the Shift to More Efficient Trucks
Insight – is it ok to lie, supply chain execution software convergence, 3d printing and the supply chains of the future, changing the production performance metric, supply chain management case study: the executive’s guide.
By Supplychainopz
Professionals in supply chain management use various methods to determine how to improve the performance of supply chain operations. Analysis of case study is certainly one of the most popular methods for people from business management background. In order to accelerate the learning, this article has gathered 20+ most sought-after supply chain case studies, analyzed/categorized them by industry and the findings are presented.

Boeing wants to encourage more flight frequency and direct route using a smaller capacity aircraft. Then they decide to outsource many things such as the design, testing and production of key components to key industrial partners and try to reduce number of components that go to assembly. The ultimate goal is to finish the final production process within 3 days. Airbus takes a bit different marketing approach. They want to utilize high capacity airplane to help airlines drive the operating cost down. They decide to selectively outsource the production of parts and keep the design and production of key components in-house.

Supply Chain of fashion industry involves a time based competition. Many customers have the unique product needs but a competition is very fierce because of the low barriers of entry. Many new players try to offer specialized products to customers all the time. This section features the supply chain case studies of H&M, Benetton, Zara and Adidas. – H&M aims to be the price leader in the fashion market.In order to materialize its vision, H&M tries to eliminate the middlemen in various stages of supply chain and consolidate the buying volumes. Product design is also the central part of its strategies. They don’t try to follow the high fashion designs but try to adopt the street trends which are easier to produce. At the end of the day, they can bring products to market within 2-3 weeks. – Benetton , in contrast, chooses to have a full control of its production but allow its licensees to operate the stores so they can focus on production and quality control. The reason is that they would like to create the worldwide brand awareness. For fast moving products, they use the production facilities in Europe. Asian suppliers will perform production for standardized products. – Zara is very famous for its time based strategy. In order to launch a new product within 15 days, Zara uses a small lot production. A new product will be tested in pilot stores. If product sales is good, a larger batch will be ordered. Otherwise, remaining products will be removed from the shelves and sold as mark-down in other stores. This creates the perception among consumers that Zara’s products are unique and you have to take it while stock lasts. Vertical integration contributes to the success of Zara, they own the majority of its production facilities and stores (this is the reason why Quick Response can be effectively implemented). Its automated distribution centers are strategically located between the center of populations so products are delivered to stores quickly. Zara also works with Air France, KLM Cargo and Emirates Air in order that they can coordinate directly with the airlines to make the outbound shipments to its stores and bring back some raw materials and semi-finished materials with return legs. The last supply chain case study in the fashion retailing industry is Adidas . In order to cope with changing customers’ demand, they decide to undertake Mass Customization strategy. The whole idea is to develop, market and deliver the product variety that most customers will find what they want. The first steps towards mass customization is to strategically offer the product choices. Too few variations will disappoint a customer but too many variations will simply postpone a buying decision. After that, Adidas asks the same key suppliers to produce custom components in order to achieve the economy of scale. In order to compensate a long waiting time, Adidas uses air freight or courier service. The reason why they can do this is that customized products are sold directly to customers so they have the higher profit margin to compensate the higher transportation cost. Supply chain strategy of the fashion retailing industry is summarized as below,

FMCG industry is typically the products sold to customers at a low cost and will be completely consumed within 1 year. The nature of this industry is the short product life cycle, low profit margin, high competition and demand fluctuation. This section will present the case studies of P&G, Unilever and Coca-Cola respectively. Forecasting and new product introduction has always been the issues for many FMCG companies, P&G is no exception. To cope with this, P&G conducts a merchandise testing at the pilot stores to determine the customer’s response to new product before the launch. The result is that the forecast accuracy is improved because a demand planner has an additional source data to make a better decision. Moreover, products can be shipped to stores in-time then lost sales is minimal. – Unilever also feels that the competition in FMCG industry has significantly increased. They have to launch the new products on regular basis but the forecasting of new product is difficult. So they create a better classification of new products (base, relaunch, repack, new) using a regression model to identify potential forecast errors for each type of new product. – Coca-Cola doesn’t really have many stock keep units when compared with other companies in the same industry. However, products go to over 2.4 million delivery points through over 430 distribution centers. Managing transportation at this scale is the absolute challenge. In order to streamline the delivery, Coca-Cola implemented a vehicle routing software. The reason is that is the software vendor has a very good relationship with Coca-Cola’s legacy ERP software vendor. Moreover, the vendor has a solid connection with the university who can help to develop the algorithm that fits in with the business’ needs. The result is that transportation planners at each distribution center can use the new tool to reduce travelling time/distance on daily basis.

Lean manufacturing concept has been implemented widely in the automotive industry so the case studies about lean manufacturing is very readily available. Due to the increasing competition in the automobile industry, car manufacturers have to launch a new model to the market more frequently. This section will show you how BMW manages a long term planning, how Ford applies lean concept to the new product development and how Hyundai manages the production planning and control. – BMW uses a 12-year planning horizon and divides it into an annual period. After that, they will make an annual sales forecast for the whole planning horizon. After the demand is obtained, they divide sales into 8 market and then select the appropriate production sites for each market, considering overall capacity constraints and total cost. As you may notice, this kind of a long range planning has to be done strategically. – Ford calls its product development system as “work streams” which include the body development, engine development, prototyping and launch process . The cross-functional team are the experts and their roles are to identify key processes, people, technology necessary for the development of new prototype. Each work stream team is responsible to develop timeline of each process. Detailed plan is usually presented on A3 sized paper. They clearly identifying current issues they are facing with supporting data, drawings and pictures. On weekly basis, they organize a big group meeting of all work stream team to discuss the coordination issues. – Hyundai deploys a centralized planning system covering both production and sales activities across the facilities and functional areas. They develop a 6-month master production plan and a weekly and a daily production schedule for each month in advance. During a short term planning (less than one month), they pay much attention to the coordination between purchasing, production and sales. Providing a long term planning data to its suppliers help to stabilize production of its part makers a lot.

Life cycle of technology products is getting shorter and shorter every day. Unlike FMCG, the launch of a new product in the hi-tech industry requires the investment in research and development quite extensively. Then, a poor planning will result in a massive loss. This section will cover JIT and outsourcing by Apple Inc, Supply Chain Risk Management by Cisco System, Technology Roadmap by Intel, Supply Chain Network Model by HP, Mass Customization by Dell and Quality Management by Sam Sung. Steve Jobs invited the Tim Cook to help to improve Apple’s Supply Chain in 1998. Jobs told Cook that he visited many manufacturing companies in Japan and he would like Cook to implement the JIT system for Apple. Jobs believed that Apple’ supply chain was too complex then both of them reduced the number of product availability and created 4 products segment, reduced on hand inventory and moved the assembling activities to Asia so they could focus on developing the breathtaking products that people wanted to buy. – Cisco Systems would like to be the brand of customer choice so they implement a very comprehensive supply chain risk management program by applying basic risk mitigation strategies, establishing appropriate metrics, monitoring potential supply chain disruptions on 24/7 basis and activate an incident management team when the level of disruption is significant. – Intel ‘s new product development is done by the process called Technology Roadmap. Basically, it’s the shared expectations among Intel, its customers and suppliers for the future product lineup. The first step to prepare the roadmap is to identify the expectations among semiconductor companies and suppliers. Then they identify key technological requirements needed to fulfill the expectations. The final step is to propose the plan to a final meeting to discuss about the feasibility of project. Some concerning parties such as downstream firms may try to alter some aspects of the roadmap. Technology Roadmap allows Intel to share its vision to its ecosystem and to utilize new technology from its suppliers. – HP ‘s case study is pretty unique. They face with a basic question, where to produce, localize and distribute products. Its simple supply chain network model is presented below,

From this example, only 3 possible locations result in 5 different way to design the supply chain. In reality, HP has more production facilities than the example above so there are so many scenarios to work with. How should HP decide which kind of a supply chain network configuration they should take to reduce cost and increase service to customer? The answer is that they use the multi-echelon inventory model to solve the problem. – Dell is one of the classic supply chain case studies of all time. Many industries try to imitate Dell’s success. The key ingredients of Dell’s supply chain are the partnership with suppliers, part modularity, vendor managed inventory program, demand management and mass customization. Also, you can find the simplified process map of Dell’s order-to-cash process as below,
– Sam Sung has proven to be the force to be reckoned with in the hi-tech industry. The secret behind its supply chain success is the use of Six Sigma approach. They studied how General Electric (GE), DuPont and Honeywell implemented six sigma. After that, they have created their own implementation methodology called DMAEV (define, measure, analyze, enable, verify). They use the global level KPI to ensure that each player in the same supply chain is measured the same way. Also, they utilize SCOR Model as the standard process. Any process changes will be reflected through an advance planning system (APS).

The last industry covered here is the general merchandise retailing industry. The critical success factor of this industry is to understand the drivers of consumer demand. Four case studies will be presented, namely, 7-11, Tesco, Walmart, Amazon and Zappos. – 7/11 is another popular case study in supply chain management. The integration of information technology between stores and its distribution centers play the important role. Since the size of 7/11 store is pretty small, it’s crucial that a store manager knows what kind of products should be displayed on shelves to maximize the revenue. This is achieved through the monitoring of sales data every morning. Sales data enables the company to create the right product mix and the new products on regular basis. 7/11 also uses something called combined delivery system aka cross docking. The products are categorized by the temperature (frozen, chilled, room temperature and warm foods). Each truck routes to multiple stores during off-peak time to avoid the traffic congestion and reduce the problems with loading/unloading at stores. – Tesco is one of the prominent retail stores in Europe. Since UK is relatively small when compared with the United States, centralized control of distribution operations and warehouse makes it easier to manage. They use the bigger trucks (with special compartments for multi-temperature products) and make a less frequent delivery to reduce transportation cost. Definitely, they use a computerized systems and electronic data interchange to connect the stores and the central processing system. – Wal-Mart ‘s “Every Day Low Prices” is the strategy mentioned in many textbooks. The idea is to try not to make the promotions that make the demand plunges and surges aka bullwhip effect. Wal-Mart has less than 100 distribution centers in total and each one serves a particular market. To make a decision about new DC location, Walmart uses 2 main factors, namely, the demand in the proposed DC area and the outbound logistics cost from DC to stores. Cost of inbound logistics is not taken into account. There are 3 types of the replenishment process in Wal-Mart supply chain network as below,
In contrary to general belief, Wal-mart doesn’t use cross-docking that often. About 20% of orders are direct-to-store (for example, dog food products). Another 80% of orders are handled by both warehouse and cross dock system. Wal-Mart has one of the largest private fleet in the United States. The delivery is made 50% by common carriers and 50% by private fleet. Private fleet is used to perform the backhauls (picks up cargoes from vendors to replenish DCs + sends returned products to vendors). Short-hauls (less than one working day drive) is also done by the a private fleet. For long-hauls, the common carriers will be used. There are 2 main information system deployed by Wal-Mart. “Retail Link” is the communication system developed in-house to store data, share data and help with the shipment routing assignments. Another system is called “Inforem” for the automation of a replenishment process. Inforem was originally developed by IBM and has been modified extensively by Wal-Mart. Inforem uses various factors such as POS data, current stock level and so on to suggest the order quantity many times a week. Level of collaboration between Wal-Mart and vendors is different from one vendor to the other. Some vendors can participate in VMI program but the level of information sharing is also different. VMI program at Wal-Mart is not 100% on consignment basis. – Amazon has a very grand business strategy to “ offer customers low prices, convenience, and a wide selection of merchandise “. Due to the lack of actual store front, the locations of warehouse facilities are strategically important to the company. Amazon makes a facility locations decision based on the distance to demand areas and tax implications. With 170 million items of physical products in the virtual stores, the back end of order processing and fulfillment is a bit complicated. Anyway, a simplified version of the order-to-cash process are illustrated as below,
Upon receipt of the orders, Amazon assign the orders to an appropriate DC with the lowest outbound logistics cost. In Amazon’s warehouse, there are 5 types of storage areas. Library Prime Storage is the area dedicated for book/magazine. Case Flow Prime Storage is for the products with a broken case and high demand. Pallet Prime Storage is for the products with a full case and high demand. Random Storage is for the smaller items with a moderate demand and Reserve Storage will be used for the low demand/irregular shaped products. Amazon uses an propitiatory warehouse management system to make the putaway decision and order picking decision. After the orders are picked and packed, Amazon ships the orders using common carriers so they can obtain the economy of scale. Orders will arrive at UPS facility near a delivery point and UPS will perform the last mile delivery to customers. Amazon is known to use Sales and Operations Planning (S&OP) to handle the sales forecast. Anyway, this must be S&OP process at product family/category level. To compete with other online retailers, Zappos pays much attention to the way they provide the services to customers. In stead of focusing on the call center productivity, Zappos encourages its staff to spend times over the phone with customers as long as they can so they can fully understand the customer’s requirements. They also upgrade the delivery from 3 days to 1 day delivery in order to exceed customer expectation.

All case study demonstrates that supply chain management is truly the strategic initiatives, not merely a cost cutting technique. Leading companies have a very strong customer focus because almost all of initiatives are something to fill the needs of customers. Relationship management is the unsung hero in supply chain management. It’s the prerequisite to the success of every supply chain. And at the end of the day, it comes down to the quality of supply chain people who analyze, improve and control supply chain operations. – See more at: http://www.supplychainopz.com/2014/04/supply-chain-management-case-study.html#sthash.MrnrGsyY.dpuf
Supply Chain Minded is a very active and fast growing online community in Supply Chain for Planning, Sourcing, Manufacturing, Delivery and Reverse Logistics professionals. The Supply Chain Minded community aims to inform and connect professionals active in Supply Chain, Purchasing, Manufacturing, Warehousing, Transport, Distribution; Reverse Logistics, Service Logistics, Lean & Six Sigma, 3PL.
© Copyright - Supply Chain Minded 2023
- Browse All Articles
- Newsletter Sign-Up
SupplyChainManagement →
No results found in working knowledge.
- Were any results found in one of the other content buckets on the left?
- Try removing some search filters.
- Use different search filters.
- Technical Support
- Find My Rep
You are here
Supply chain management free case studies.

Share these free Supply Chain Management case studies with your class
Engage your students with real-world case studies that provide insights into supply chain practices, challenges, and opportunities. Share each case study with your students by simply copying and pasting the activity page URL into your learning management system (LMS).
Case 1: Rising Health Care Costs And The Role Of Outsourcing And Offshoring In The U.S. Health Care Sector
In this case study, your students will identify factors that are driving the health care costs higher in the United States than in peer countries. They will also discuss advantages and disadvantages of emerging trends in supply chain management such as adopting outsourcing in health care. After reading the case, they are encouraged to create an argument in favor of or against the view that health care offshoring is a threat to the U.S. health care industry. See case study .
- Case 2: McDonald’s Reinvents Itself Again
In this case study, your students will identify factors that are affecting demand management in the fast food industry and evaluate the reinvention strategy that McDonald’s has used to keep their fingers firmly on the pulse of their international customer base. Students will also be asked to advice McDonald’s with regards to future trends and the changes it should consider. After reading the case, they are encouraged to research areas in which the company plans to reinvent itself in the coming years, particularly in light of the appointment of its new CEO and the COVID-19 pandemic. See case study
Learn more about our offerings for your Supply Chain Management course:
Supply Chain Management
- Case 1: Rising Health Care Costs
- Sign up to receive new content alerts and special offers
- College Publishing Offerings
- Digital Solutions for Your Course
- Research Methods, Statistics, and Evaluation Catalog

Learn more about Sage Vantage
Future-proofing the supply chain
Supply chains matter. The plumbing of global commerce has rarely been a topic of much discussion in newsrooms or boardrooms, but the past two years have pushed the subject to the top of the agenda. The COVID-19 crisis , postpandemic economic effects , and the ongoing conflict in Ukraine have exposed the vulnerabilities of today’s global supply chains. They have also made heroes of the teams that keep products flowing in a complex, uncertain, and fast-changing environment . Supply chain leaders now find themselves in an unfamiliar position: they have the attention of top management and a mandate to make real change.
Forward-thinking chief supply chain officers (CSCOs) now have a once-in-a-generation opportunity to future-proof their supply chains. And they can do that by recognizing the three new priorities alongside the function’s traditional objectives of cost/capital, quality, and service 1 Employee safety, food safety, and employee retention are considered operational preconditions, not supply chain objectives. and redesigning their supply chains accordingly.
The first of these new priorities, resilience, addresses the challenges that have made supply chain a widespread topic of conversation. The second, agility, will equip companies with the ability to meet rapidly evolving, and increasingly volatile, customer and consumer needs. The third, sustainability, recognizes the key role that supply chains will play in the transition to a clean and socially just economy (Exhibit 1).
Boosting supply chain resilience
Supply chains have always been vulnerable to disruption . Prepandemic research by the McKinsey Global Institute found that, on average, companies experience a disruption of one to two months in duration every 3.7 years . In the consumer goods sector, for example, the financial fallout of these disruptions over a decade is likely to equal 30 percent of one year’s EBITDA.
Historical data also show that these costs are not inevitable. In 2011, Toyota suffered six months of reduced production following the devastating Tohoku earthquake and tsunami. But the carmaker revamped its production strategy, regionalized supply chains, and addressed supplier vulnerabilities. When another major earthquake hit Japan in April 2016, Toyota was able to resume production after only two weeks.
During the pandemic’s early stages, sportswear maker Nike accelerated a supply chain technology program that used radio frequency identification (RFID) technology to track products flowing through outsourced manufacturing operations. The company also used predictive-demand analytics to minimize the impact of store closures across China. By rerouting inventory from in-store to digital-sales channels and acting early to minimize excess inventory buildup across its network, the company was able to limit sales declines in the region to just 5 percent. Over the same period, major competitors suffered much more significant drops in sales.
Supply chain risk manifests at the intersection of vulnerability and exposure to unforeseen events (Exhibit 2). The first step in mitigating that risk is a clear understanding of the organization’s supply chain vulnerabilities. Which suppliers, processes, or facilities present potential single points of failure in the supply chain? Which critical inputs are at risk from shortages or price volatility?
Would you like to learn more about our Operations Practice ?
In 2021, for example, many companies in North America were affected by labor shortages across their supply chain operations. Tackling those shortages has forced companies to be creative in their hiring and staffing strategy. One food distributor created regional floating labor pools of drivers, warehouse workers, and supervisors, recruiting staff in areas where they were more available and deploying them wherever they were most needed. Other companies are building their labor pipeline-management capabilities—from recruiting through retention—and sharpening their labor planning as well.
Today, most organizations lack effective systems to measure and monitor those vulnerabilities, and few have such visibility beyond their direct suppliers. In a 2021 McKinsey survey of senior supply chain executives, just under half said they understood the location of their tier-one suppliers and the key risks those suppliers face. But only 2 percent could make the same claim about suppliers in the third tier and beyond. That matters because most disruptions originate in these deeper supply chain tiers.
Closing the industry’s current knowledge gaps will require it to increase its surveillance of supply chain participants and its understanding of the physical, financial, political, and social risks they may face (Exhibit 3). The complexity and diversity of supply chain risks require smart management tools, and leading companies are applying a range of new techniques, from digital alerting systems to track potential disruptive events to risk “heat maps” that help them focus their attention on high-risk regions and suppliers.
Companies will also need a management infrastructure to steer a proactive response to these risks. Such an infrastructure would include a dedicated team, headed by a senior leader, with the remit to identify, prioritize, and respond to vulnerabilities. Those responses might include structural changes to the supply chain, as well as the development of detailed contingency plans for disruptive events. Introducing resilience metrics into supply chain KPIs helps the whole organization to ensure supply chain design and execution decisions are made in a way that balances efficiency and vulnerability. And because supply chain risk is a continually moving target, the organization should conduct regular stress tests and reviews to ensure its resilience measures remain appropriate.
Increasing supply chain agility
Customer loyalty is no longer a given. During the COVID-19 pandemic, for example, 77 percent of US consumers changed stores, brands, or the way they shop . Much of that change was driven by necessity. People went online when they couldn’t access their regular stores, and two-thirds said that lack of availability was the primary reason for switching brands. The big winners of the crisis were companies, often the largest players, that could keep products flowing to their customers in a difficult operating environment.
In the postpandemic economy, established brands will face new challenges. As consumer-generated content replaces traditional brand marketing campaigns, companies have less control over the peaks or troughs of demand. Where a business might have once spent months preparing its supply chains for a carefully targeted promotional campaign, now a single viral video can bring attention from millions of consumers overnight. One consumer goods manufacturer experienced a surge in demand in 2020 after a video of a customer enjoying its product on a skateboard ride received millions of views and spawned dozens of imitators.
New players are disrupting retail channels too, widening available choices and creating space for smaller, independent manufacturers. While consumers opted for the security of big brands during the COVID-19 pandemic, a preference for smaller producers is rising, especially among younger cohorts. And the growth of comanufacturing businesses and third-party logistics (3PLs) organizations means new entrants can compete in consumer markets with fewer expensive manufacturing and supply chain assets.
For incumbents, the lesson is clear: move at the same speed as consumers. That means creating innovative products and brands that meet the changing needs of different consumer groups as those needs emerge. And it means greater skill in managing complex portfolios of brands with different market characteristics and delivering their products through multiple channels. These same pressures increasingly hold true for B2B businesses as well, as increased consumer product complexity and demand volatility trickle down the supply chain.
This fast-moving, fragmented, consumer-centric world will require a different sort of supply chain. Traditional supply chains sought to achieve stability and minimize costs. Future supply chains will need to be much more dynamic—and be able to predict, prepare, and respond to rapidly evolving demand and a continually changing product and channel mix. In short, supply chains will need to become agile .
The good news for CSCOs is that agility and resilience are highly complementary: an agile supply chain is inherently more resilient. To be truly effective, however, this agility would need to extend into R&D, procurement, planning, manufacturing, and logistics (Exhibit 4).
At the planning stage, for example, supply chain teams will need to work in a much more proactive way. As potential market opportunities are identified, the supply chain function can begin creating scenarios that are ready for implementation alongside the development of the new product or market offering. After launch, the use of advanced techniques for demand sensing and dynamic forecasting, aided by machine learning technologies, is set to become an essential part of day-to-day supply chain operations.
In supply chain execution, agility requires new capabilities and tools. Agile operations make extensive use of digital technologies in manufacturing, for example, and maximize the use of smart automation in both production and logistics settings. Unlike the rigid supply chain automation systems of the past, technologies such as collaborative robots and smart packaging machines are capable of faster changeovers and can handle a much wider range of products and shipment types.
The drive for agility may require companies to reassess make-versus-buy decisions. In manufacturing, for example, big players typically keep the production of their stable, high-volume products in-house, using comanufacturers for niche and special projects. Leading companies appear likely to invert this trend, investing in flexible core assets and skills that allow their own manufacturing to respond quickly to rapidly changing demands—and, in some cases, outsourcing stable, high-volume products to cost-advantaged external providers. In downstream logistics, meanwhile, greater use of 3PLs may become the most cost-effective way to increase asset flexibility and proximity to customers.
Agile supply chains will also need skilled, flexible people. An agile supply chain workforce is comfortable working with and alongside advanced technologies, and personnel may need a wider range of skills so they can move between tasks as business needs change. Accordingly, agile supply chains make use of agile teams and working methods, borrowing elements of the approach that have transformed flexibility, productivity, and quality in the software industry and beyond. Agile organizational principles are well-described elsewhere , but key elements of the approach include the use of tight-knit, cross-functional teams that work together to implement new concepts and solve difficult problems in short, incremental sprints. These principles are already gaining traction across a range of industries: one major consumer products manufacturer is using “flow to work” pools in its global support functions to dynamically allocate staff to projects, for example.

Digital twins: The art of the possible in product development and beyond
Achieving supply chain sustainability.
Post-COVID-19 consumers have become even more likely to prefer brands that offer robust sustainability credentials and a strong purpose, but industry surveys conducted in mid-2020 suggested that environmental, social, and governance (ESG) topics slipped down companies’ list of priorities during the pandemic. Big players are now making up for lost time. In 2021, 29 percent of companies included ESG metrics in their staff incentive plans, for example, a seven percentage-point uptick over the previous year.
Companies looking to avoid the increasing reputational, regulatory, and financial risks of poor ESG performance are being pressed to act. And as companies such as Henkel have shown, strong environmental actions are also delivering real operational results: a digital twin connects and benchmarks 30 factories and prescribes real-time sustainability actions, which over ten years have reduced energy consumption by almost 40 percent and waste by 20 percent.
The supply chain has a central role to play in the enterprise sustainability transformation. Of nine ESG initiatives highlighted by senior executives in a 2020 industry survey, most either involve the supply chain directly, or have significant implications for supply chain setups (Exhibit 5).
The foundation for an ESG-focused transformation is a clear understanding of the organization’s baseline impact. That would include, for example, quantification of the resources consumed and emissions generated by the company’s direct activities (Scopes 1 and 2) and by participants in its wider supply chain (Scope 3). This baseline allows an organization to identify the largest opportunities for improvement, helping it set challenging but realistic goals and timescales that can be communicated to external stakeholders. Capturing those improvements requires rigorous sustainability KPIs and changes from the shop floor to the boardroom, including optimized operating practices, an ESG focus in procurement decisions , and the adoption of more sustainable technologies in existing and planned manufacturing or logistics projects.
These new priorities of resilience, agility, and sustainability can’t be tacked on to existing supply chain setups. Realistically, they will need to be built in from the foundation and considered in every element of supply chain design, organization, and operation. For many companies, that will likely require a change in mindset from the top, with risk, agility, and sustainability KPIs considered alongside traditional ones focused on cost, capital usage, service, and quality. To excel in these six supply chain dimensions, workforce management and digital capabilities will be essential.
Jan Henrich is a senior partner in McKinsey’s Chicago office; Jason D. Li is an associate partner in the Toronto office; and Carolina Mazuera is an associate partner in the Miami office, where Fernando Perez is a partner.
Explore a career with us
Related articles.
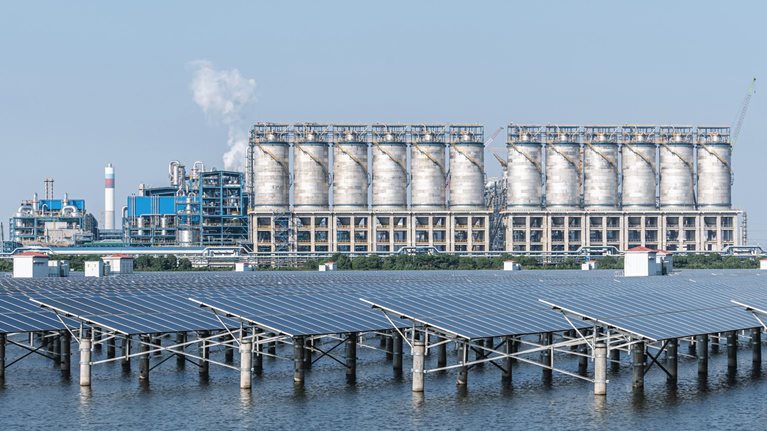
Outsprinting the energy crisis
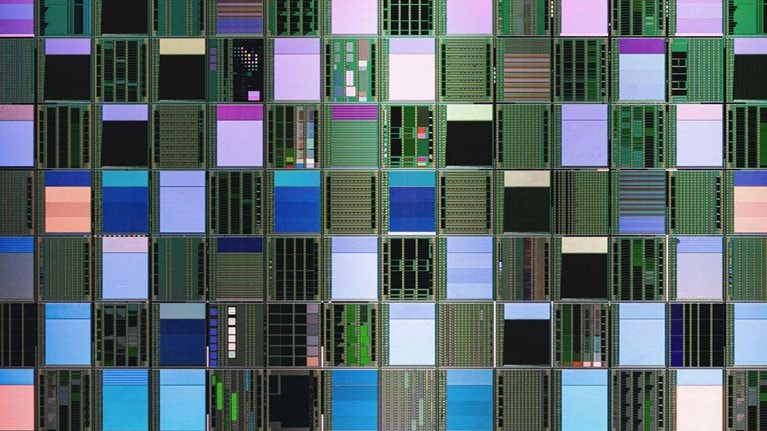
Navigating the semiconductor chip shortage: A control-tower case study
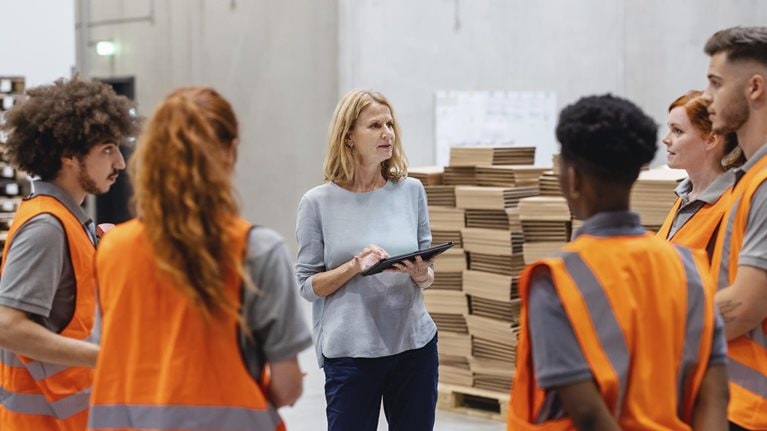
Transforming supply chains: Do you have the skills to accelerate your capabilities?
Blockchain Technology: A case study in supply chain management
Ieee account.
- Change Username/Password
- Update Address
Purchase Details
- Payment Options
- Order History
- View Purchased Documents
Profile Information
- Communications Preferences
- Profession and Education
- Technical Interests
- US & Canada: +1 800 678 4333
- Worldwide: +1 732 981 0060
- Contact & Support
- About IEEE Xplore
- Accessibility
- Terms of Use
- Nondiscrimination Policy
- Privacy & Opting Out of Cookies
A not-for-profit organization, IEEE is the world's largest technical professional organization dedicated to advancing technology for the benefit of humanity. © Copyright 2024 IEEE - All rights reserved. Use of this web site signifies your agreement to the terms and conditions.
Trade-offs among Lean, Agile, Resilient and Green Paradigms in Supply Chain Management: A Case Study Approach
- Conference paper
- First Online: 01 January 2013
- Cite this conference paper
- Helena Carvalho 5 ,
- Susana Azevedo 5 &
- Virg´ılio Cruz-Machado 5
Part of the book series: Lecture Notes in Electrical Engineering ((LNEE,volume 242))
3346 Accesses
14 Citations
3 Altmetric
Lean, Agile, Resilient and Green (LARG) management paradigms may help companies and supply chains to become more competitive and sustainable. However, the deployment of those management paradigms could lead to opposite results. This paper intends to identify and the necessary understanding of those paradigms trade-offs. An exploratory case study approach is used to identify the trade-offs in the automotive supply chain context. The case study findings show that not all the companies belonging to the same supply chain need to have a higher implementation level for all LARG practices. Some companies can be more Resilient than others, and the same happens with the Lean paradigm: not all companies in supply chain need to be totally Lean. Because of the differences in the LARG practices implementation level among supply chain echelons, two separate sequences of capabilities were found. For the automaker “quality” should be developed first, then “flexibility”, “environmental protection” in addition to “cost”, and finally “delivery”. In the first-tier supplier echelon “quality” should be developed first, subsequently “flexibility”, “delivery”, and ultimately “cost” and “environmental protection”.
This is a preview of subscription content, log in via an institution to check access.
Access this chapter
- Available as PDF
- Read on any device
- Instant download
- Own it forever
- Compact, lightweight edition
- Dispatched in 3 to 5 business days
- Free shipping worldwide - see info
- Durable hardcover edition
Tax calculation will be finalised at checkout
Purchases are for personal use only
Institutional subscriptions
Unable to display preview. Download preview PDF.
Stevens GC (1989) Integrating the supply chain. International Journal of Physical Distribution & Logistics Management 19(8):3–8
Google Scholar
Gunasekaran A, Patel C, Tirtiroglu E (2001) Performance measures and metrics in a supply chain environment. International Journal of Operations & Production Management 21(1/2):71–87
Carvalho H, Cruz-Machado V (2009) Lean, agile, resilient and green supply chain: A review. In: Proceedings of the Third International Conference on Management Science and Engineering Management, Bangkok, Thailand 3–14
Azevedo SG, Carvalho H, Cruz-Machado V (2011) A proposal of LARG supply chain management practices and a performance measurement system. International Journal of e-Education, e-Business, e-Management and e-Learning 1(1):7–14
Carvalho H, Duarte S, Machado VC (2011) Lean, agile, resilient and green: Divergencies and synergies. International Journal of Lean Six Sigma 2(2):51–179
Azevedo SG, Carvalho H, Cruz-Machado V (2011) Pathways between lean and green paradigms and supply chain performance. In: Proceedings of 2011 International Conference on Economics, Business and Marketing Management-EBMM, Shangai, China
Azevedo SG, Carvalho H, Duarte S et al (2012) Influence of green and lean upstream supply chain management practices on business sustainability. IEEE Transactions on Engineering Management 59(4):1–13
Azevedo SG, Govindan K, Carvalho H et al (2012) Ecosilient index to assess the greenness and resilience of the upstream automotive supply chain. Journal of Cleaner Production doi.org/10.1016/j.jclepro.2012.04.011
Carvalho H, Azevedo SG, Cruz-Machado V (2013) An innovate agile and resilience index for the automotive supply chain. International Journal of Agile Systems and Management (In Press)
Carvalho H, Azevedo SG, Cruz-Machado V (2012) Agile and resilient approaches to supply chain management: Influence on performance and competitiveness. Logistics Research 4(1-2):49–62
Wu YC (2003) Lean manufacturing: A perspective of lean suppliers. International Journal of Operations & Production Management 23(11):1349–1376
Elkins DA, Huang N, Alden JM (2004) Agile manufacturing systems in the automotive industry. International Journal of Production Economics 91(3):201–214
Azevedo SA, Machado VH, Barroso AP et al (2008) Supply chain vulnerability: Environment changes and dependencies. International Journal of Logistics and Transport 2(1):41–55
Azevedo SG, Carvalho H, Cruz-Machado V (2011) The influence of green practices on supply chain performance: A case study approach. Transportation Research Part E: Logistics and Transportation Review 47(6):850–871
Naylor BJ, Naim MM, Berry D (1999) Leagility: Integrating the lean and agile manufacturing paradigms in the total supply chain. International Journal of Production Economics 62(1-2):107–118
Tice J, Ahouse L, Larson T (2005) Lean production and EMSs: Aligning environmental management with business priorities. Environmental Quality Management 15(2):1–12
Kuriger G, Chen F (2010) Lean and green: A current state view. In: Proceedings of the 2010 Industrial Engineering Research Conference, Cancun, Mexico
Price JL, Joseph JB (2000) Demand management — A basis for waste policy: A critical review of the applicability of the waste hierarchy in terms of achieving sustainable waste management. Sustainable Development 8(2):6–105
Christopher M, Peck H (2004) Building the resilient supply chain. The International Journal of Logistics Management 15(2):1–14
Kannan VR, Tan KC (2005) Just in time, total quality management, and supply chain management: Understanding their linkages and impact on business performance. Omega 33(2):153–162
Anand G, Kodali R (2008) A conceptual framework for lean supply chain and its implementation. International Journal of Value Chain Management 2(3):313–357
Lyons A, Coronado A, Michaelides Z (2006) The relationship between proximate supply and build-to-order capability. Industrial Management & Data Systems 106(8):1095–1111
Huang GQ, Zhang XY, Liang L (2005) Towards integrated optimal configuration of platform products, manufacturing processes, and supply chains. Journal of Operations Management 23(3-4):267–290
Banerjee SK (2000) Developing manufacturing management strategies: Influence of technology and other issues. International Journal of Production Economics 64(1-3):79–90
Carvalho H, Barroso AP, Machado VH et al (2012) Supply chain redesign for resilience using simulation. Computers & Industrial Engineering 62(1):329–341
Rosic H, Bauer G, JammerneggW(2009) A framework for economic and environmental sustain ability and resilience of supply chains. Rapid Modelling for Increasing Competitiveness 91–104
Tang CS (2006) Robust strategies for mitigating supply chain disruptions. International Journal of Logistics Research and Applications: A Leading Journal of Supply Chain Management 9(1):33–45
K Nishitani (2010) Demand for ISO 14001 adoption in the global supply chain: An empirical analysis focusing on environmentally conscious markets. Resource and Energy Economics 32(3):395–407
Nawrocka D, Brorson T, Lindhqvist T (2009) ISO 14001 in environmental supply chain practices. Journal of Cleaner Production 17(16):1435–1443
Huang YA, Matthews HS (2008) Seeking opportunities to reduce life cycle impacts of consumer goods-An economy-wide assessment. In: Proceedings of the 2008 IEEE International Symposium on Electronics and the Environment 1–6
Nair SR, Menon CG (2008) An environmental marketing system—A proposed model based on Indian experience. Business Strategy and the Environment 17(8):467–479
Mollenkopf D, Stolze H, Tate WL et al (2010) Green, lean, and global supply chains. International Journal of Physical Distribution & Logistics Management 40(1/2):14–41
Venkat K, Wakeland W (2006) Is lean necessarily green? In: Proceedings of the 50th Annual Meeting of the ISSS, North America
Winter SG (2003) Understanding dynamic capabilities. Strategic Management Journal 24(10):991–995
Morash EA, Droge CL, Vickery SK (1996) Strategic logistics capabilities for competitive advantage and firm success. Journal of Business Logistics 17(1):1–22
Flynn BB, Flynn EJ (2004) An exploratory study of the nature of cumulative capabilities. Journal of Operations Management 22(5):439–457
Vitasek KL, Manrodt KB, Abbott J (2005) What makes a lean supply chain? Supply Chain Management Review 9(7):39–45
Hoek RV, Harrison A, ChristopherM(2001) Measuring agile capabilities in the supply chain. International Journal of Operations & Production Management 21(1/2):126–148
Parmigiani A, Klassen RD, Russo MV (2011) Efficiency meets accountability: Performance implications of supply chain configuration, control, and capabilities. Journal of Operations Management 29(3):212–223
Avella L, Vazquez-Bustelo D, Fernandez E (2011) Cumulative manufacturing capabilities: An extended model and new empirical evidence. International Journal of Production Research 49(3):707–729
Da Silveira GJC (2005) Improving trade-offs in manufacturing: Method and illustration. International Journal of Production Economics 95(1):27–38
Ferdows K, De Meyer A (1990) Lasting improvements in manufacturing performance: In search of a new theory. Journal of Operations Management 9(2):168–184
Schmenner RW, Swink ML (1998) On theory in operations management. Journal of Operations Management 17(1):97–113
Rosenzweig ED, Easton GS (2010) Tradeoffs in manufacturing? A meta-analysis and critique of the literature. Production and Operations Management 19(2):127–141
Seuring S (2009) The product-relationship-matrix as framework for strategic supply chain design based on operations theory. International Journal of Production Economics 120(1):221–232
Yin RK (2002) Case study research: Design and methods. SAGE Publications, Incorporated 5
Curkovic S, Sroufe R (2011) Using ISO 14001 to promote a sustainable supply chain strategy. Business Strategy and the Environment 20(2):71–93
Download references
Author information
Authors and affiliations.
UNIDEMI, Departamento de Engenharia Mecˆanica e Industrial Faculdade de Ciˆencias e Tecnologia (FCT), Universidade Nova de Lisboa, Caparica, 2829-516, Portugal
Helena Carvalho, Susana Azevedo & Virg´ılio Cruz-Machado
You can also search for this author in PubMed Google Scholar
Corresponding authors
Correspondence to Helena Carvalho or Virg´ılio Cruz-Machado .
Editor information
Editors and affiliations.
Business School, Sichuan University, Chengdu, China, People's Republic
Drexel University, Philadelphia, PA, USA
John A. Fry
LeBow College of Business Department of Decision Sciences, Drexel University, Philadelphia, Pennsylvania, USA
Benjamin Lev
Azerbaijan National Academy of Sciences, Institute of Cybernetics, Baku, Azerbaijan
Asaf Hajiyev
Rights and permissions
Reprints and permissions
Copyright information
© 2014 Springer-Verlag Berlin Heidelberg
About this paper
Cite this paper.
Carvalho, H., Azevedo, S., Cruz-Machado, V. (2014). Trade-offs among Lean, Agile, Resilient and Green Paradigms in Supply Chain Management: A Case Study Approach. In: Xu, J., Fry, J., Lev, B., Hajiyev, A. (eds) Proceedings of the Seventh International Conference on Management Science and Engineering Management. Lecture Notes in Electrical Engineering, vol 242. Springer, Berlin, Heidelberg. https://doi.org/10.1007/978-3-642-40081-0_81
Download citation
DOI : https://doi.org/10.1007/978-3-642-40081-0_81
Published : 24 September 2013
Publisher Name : Springer, Berlin, Heidelberg
Print ISBN : 978-3-642-40080-3
Online ISBN : 978-3-642-40081-0
eBook Packages : Business and Economics Business and Management (R0)
Share this paper
Anyone you share the following link with will be able to read this content:
Sorry, a shareable link is not currently available for this article.
Provided by the Springer Nature SharedIt content-sharing initiative
- Publish with us
Policies and ethics
- Find a journal
- Track your research

COMMENTS
case study. Abstract. By the end of the decade, there are H&M stores in several European countries including. France, where the first H&M store opens 1998 in Paris. COS is offered online in 21 ...
Harvard University aims to be fossil-fuel neutral by 2026 and totally free of fossil fuels by 2050. As part of this goal, the university is trying to decarbonize its supply chain and considers replacing cement with a low-carbon substitute called Pozzotive®, made with post-consumer recycled glass. A successful pilot project could jump start ...
Organizations undertake strategic supply chain initiatives through project implementation. However, selecting the right supply chain projects can be difficult due to high levels of organizational risk and technical complexity. Although the literature is rich in quantitative and qualitative methods for project management, prior research into best management practices specific to supply chain ...
The Next Supply-Chain Challenge Isn't a Shortage — It's Inventory Glut. Operations and supply chain management Digital Article. PS Subramaniam. Strategies for reducing excess inventory ...
Case Study: Applying the Approach at a Leading Global Retailer. BCG applied this approach to support the end-to-end supply chain transformation of a global retailer. The company's rapid growth had strained its supply chain and revealed key limitations, especially in cross-functional coordination and data enablement.
Four case studies will be presented, namely, 7-11, Tesco, Walmart, Amazon and Zappos. - 7/11 is another popular case study in supply chain management. The integration of information technology between stores and its distribution centers play the important role. Since the size of 7/11 store is pretty small, it's crucial that a store manager ...
can be and is applied in supply chain management, the use of case study research is an interesting option. Frequently, the analysis of a supply chain and managerial issues therein are highly unstructured problems which can be dealt with in an exploratory research design using case studies (Yin, 2003). Stuart et al. (2002)
New research on supply chain management from Harvard Business School faculty on issues including what brands can do to monitor their suppliers' factory conditions, how Japan's earthquake and tsunami and caused havoc on retailers and car manufacturers, and the push to improve labor standards in global supply chains. ... In a recent case study ...
This paper outlines the importance and benefits and an organization can achieve through supply chain integration. These benefits an primarily in the area of achieving superior customer service levels and operating at lower working capital level, two of the most important drivers of business profitability.
Sustainability in supply chain management (SSCM) has become established in both academia and increasingly in practice. As stakeholders continue to require focal companies (FCs) to take more responsibility for their entire supply chains (SCs), this has led to the development of multi-tier SSCM (MT-SSCM). Much extant research has focused on simple supply chains from certain industries. Recently ...
This Case Study, combined with the Literature Review, allowed the construction of a framework for the Sustainable Supply Chain Management. The key feature differentiating of this framework its operational nature, by integrating a set of supporting sustainability practices. Download conference paper PDF.
Share these free Supply Chain Management case studies with your class Engage your students with real-world case studies that provide insights into supply chain practices, challenges, and opportunities. Share each case study with your students by simply copying and pasting the activity page URL into your learning management system (LMS). Case 1 ...
The first of these new priorities, resilience, addresses the challenges that have made supply chain a widespread topic of conversation. The second, agility, will equip companies with the ability to meet rapidly evolving, and increasingly volatile, customer and consumer needs. The third, sustainability, recognizes the key role that supply chains ...
They cover different aspects of supply chain management and feature a broad range of companies and situations. SCM case study examples would include an SCM selection project for a manufacturer, or an SCM implementation for a distributor or logistics provider. SCM case studies also feature TEC's own case studies, showing how we've helped ...
This paper provides perspectives on how to design lean supply chains. It describes a real case study related to construction materials supply chain. In the case study is considered a supply chain setting where the dealer's have dominant bargaining power over the manufacturer. It intents to analyze the impact of this setup in overall ...
Case studies: Supply chain disruptions: ... 2000), the present struggles, with one of the most severe financial downturns since the Great Depression, demand a new approach to risk management (Ariba, 2009, Power, 2009). The degree of an enterprise's interconnection with its suppliers today is also unprecedented in business history, presenting ...
Supply Chain Risk Management has become a key concern for organizations, which is even further emphasized by the current economic and financial crisis. Against ... 'Supply Risk Management in Financial Crises - A Multiple Case-Study Approach,' International Journal of Production Economics, Vol. 134, No. 1, pp. 43-57, 2011. 43 Pages Posted: 1 ...
This study provides both theoretical and practical contributions. The article contains four sections. First, the literature is reviewed from the supply chain management (SCM) customer service notion and customer service performance measurement logic. Second, an explanation of the case study methodology is provided.
As blockchain technology has already become a critical priority for enterprises, it is acknowledged that it might be as much important as to reform and reconstruct businesses in the near future. In this paper we review the strengths and weaknesses of the blockchain technology, and present an example application in supply chain management. We start by presenting the key characteristics of the ...
An exploratory case study approach is used to identify the trade-offs in the automotive supply chain context. The case study findings show that not all the companies belonging to the same supply chain need to have a higher implementation level for all LARG practices.