Spare Parts Inventory Management System in a Service Sector Company
- Conference paper
- First Online: 11 November 2021
- Cite this conference paper
- Buse Atakay 11 ,
- Özge Onbaşılı 11 ,
- Simay Özcet 11 ,
- İrem Akbulak 11 ,
- Hatice Birce Cevher 11 ,
- Hümeyra Alcaz 11 ,
- İsmail Gördesli 11 ,
- Mert Paldrak 11 &
- Efthimia Staiou 11
Part of the book series: Lecture Notes in Mechanical Engineering ((LNME))
1992 Accesses
3 Citations
Spare parts inventory management is crucial in the success of a service providing company. In this study, the spare parts of a service provider in the automotive sector are classified according to their characteristics in groups and different inventory control policies are applied to the categorized groups. The Analytical Hierarchy Process (AHP), one of the Multi-Criteria Decision Making (MCDM) methods, is used to classify the spare parts into groups. As a result of the application of AHP, classes of spare parts are determined according to the VED analysis, classifying the spare parts according to their criticality. Furthermore, the ABC analysis performed by the company was improved by using cost and demand criteria. After performing both analysis, three new classes of spare parts are determined with the combination of ABC and VED classification techniques. For each class, an appropriate inventory control policy is decided according to the spare parts importance and criticality. Based on the literature review, the \(({\varvec{R}},{\varvec{S}},{\varvec{s}})\) inventory control policy is chosen to be applied in each class, taking into consideration the review period, order up-to-level and reorder point of items. In the inventory control model, the review period for the same class items is assumed to be constant based on the information provided by the company. For verification purposes, necessary cost calculations including total ordering and holding costs are performed by means of Microsoft Excel. In order to be able to vastly observe the system behavior, different cost scenarios are generated by increasing and decreasing the service level and review period of the system. Using, OptQuest, an optimization tool, embedded into ARENA simulation software, the different scenarios were analyzed and the total minimum cost is reached. For supporting the daily operations of the company, a user-friendly decision support system is built, where the end-user can easily add/remove spare parts to/from the system, classify them and compare the results of inventory control policies with the current system. The DSS will also assist the company to manage and control their real-time inventory and perform spare parts stock level tracking and decide when to place orders.
This is a preview of subscription content, log in via an institution to check access.

Access this chapter
- Available as PDF
- Read on any device
- Instant download
- Own it forever
- Available as EPUB and PDF
- Compact, lightweight edition
- Dispatched in 3 to 5 business days
- Free shipping worldwide - see info
- Durable hardcover edition
Tax calculation will be finalised at checkout
Purchases are for personal use only
Institutional subscriptions
Celebi, D., Bayraktar, D., Ozturkcan, S.: Multi criteria classification for spare parts inventory. SSRN Electron. J. (2008). https://doi.org/10.2139/ssrn.1362575
Article Google Scholar
do Jego, J.R., de Mesquita, M.A.: Spare parts inventory control: a literature review. Production 21 (4), 645–666 (2011). https://doi.org/10.1590/s010365132011005000002
Stoll, J., Kopf, R., Schneider, J., Lanza, G.: Criticality analysis of spare parts management: a multi-criteria classification regarding a cross-plant central warehouse strategy. Prod. Eng. 9 (2), 225–235 (2015). https://doi.org/10.1007/s11740-015-0602-2
Gupta, R., Gupta, K., Jain, B., Garg, R.: ABC and VED analysis in medical stores inventory control. Med. J. Armed Forces India 63 (4), 325–327 (2007). https://doi.org/10.1016/s0377-1237(07)80006-2
Velmurugan, R., Selvamuthukumar, S., Manavalan, R.: Multi criteria decision making to select the suitable method for the preparation of nanoparticles using an analytical hierarchy process. Department of Pharmacy, Faculty of Engineering and Technology, Annamalai University, Annamalai Nagar, Tamil Nadu, India (2011). https://doi.org/10.1691/ph.2011.1034
Silva, L.A.D., Hernández, C.T., Brandalise, N.: Criticality evaluation of spare parts using the analytic hierarchy process with ratings. Syst. Manag. 14 (2019), 166–176 (2019). https://doi.org/10.20985/1980-5160.2019.v14n2.1500
Bacchetti, A., Plebani, F., Saccani, N., Syntetos A.A.: Spare parts classification and inventory management: a case study. Supply Chain and Service Management Research Centre - Department of Mechanical Engineering, Università di Brescia, Brescia, Italy University of Salford, Salford, UK (2010)
Google Scholar
Durán, O.: Spare parts criticality analysis using a fuzzy AHP approach. Tehnicki Vjesnik-Tech. Gaz. 22 (4), 899–905 (2015). https://doi.org/10.17559/tv-20140507002318
Tarim, S.A., Kingsman, B.G.: Modelling and computing (Rn, Sn) policies for inventory systems with non-stationary stochastic demand. Eur. J. Oper. Res. 174 (1), 581–599 (2006). https://doi.org/10.1016/j.ejor.2005.01.053
Article MATH Google Scholar
Aslantaş, M.: Bir Transformatör Firmasında Stok Kontrol Parametrelerinin Simülasyon Tabanlı Optimizasyonu. Yüksek Lisans Tezi, Master of Science, Fen Bilimleri Enstitüsü Endüstri Mühendisliği Anabilim Dalı, Balıkesir Üniversitesi, Türkiye (2019)
Pyke, D.A., Silver, E.A., Thomas, D.J.: Inventory and Production Management in Supply Chains, 4th edn.. CRC Press Taylor and Francis Group, 6000 Broken Sound Parkway NW, Suite 300 Boca Raton (2017)
Bravo, J.J., Delgado, L., Toro, H.H.: A Practical Approach to Develop Centralized Inventory Policies for 1-Warehouse/N-Retailers Systems Through Simulation/Optimization. Universidad del Valle, Colombia (2017)
Radasanu, A.C.: Inventory management, service level and safety stock. J. Public Admin. Financ. Law 09 , 145–153 (2016)
Accorsi, R., et al.: Weibull vs. normal distribution of demand to determine the safety stock level when using the continuous-review (S, s) model without backlogs. Int. J. Logist. Syst. Manag. 24 , 3 (2016)
Assis Lopes, J.Á., de Matos, J.M.L.: Heuristics in inventory control: operational empirical evidence. Int. J. Eng. Ind. Manag./Revista Internacional de Engenharia e Gestão Industrial (2014)
Benko, J.: Modeling stochastic inventory policy with simulation (2011)
Download references
Author information
Authors and affiliations.
Industrial Engineering, Yaşar University, Izmir, Turkey
Buse Atakay, Özge Onbaşılı, Simay Özcet, İrem Akbulak, Hatice Birce Cevher, Hümeyra Alcaz, İsmail Gördesli, Mert Paldrak & Efthimia Staiou
You can also search for this author in PubMed Google Scholar
Corresponding author
Correspondence to Efthimia Staiou .
Editor information
Editors and affiliations.
Faculty of Mechanical and Industrial Engineering, Institute of Production Engineering and Photonic Technologies, TU Wien (Vienna University of Technology), Vienna, Austria
Numan M. Durakbasa
Faculty of Engineering, Industrial Engineering Department, İstanbul Aydın University, İstanbul, Turkey
M. Güneş Gençyılmaz
Rights and permissions
Reprints and permissions
Copyright information
© 2022 The Author(s), under exclusive license to Springer Nature Switzerland AG
About this paper
Cite this paper.
Atakay, B. et al. (2022). Spare Parts Inventory Management System in a Service Sector Company. In: Durakbasa, N.M., Gençyılmaz, M.G. (eds) Digitizing Production Systems. Lecture Notes in Mechanical Engineering. Springer, Cham. https://doi.org/10.1007/978-3-030-90421-0_67
Download citation
DOI : https://doi.org/10.1007/978-3-030-90421-0_67
Published : 11 November 2021
Publisher Name : Springer, Cham
Print ISBN : 978-3-030-90420-3
Online ISBN : 978-3-030-90421-0
eBook Packages : Engineering Engineering (R0)
Share this paper
Anyone you share the following link with will be able to read this content:
Sorry, a shareable link is not currently available for this article.
Provided by the Springer Nature SharedIt content-sharing initiative
- Publish with us
Policies and ethics
- Find a journal
- Track your research
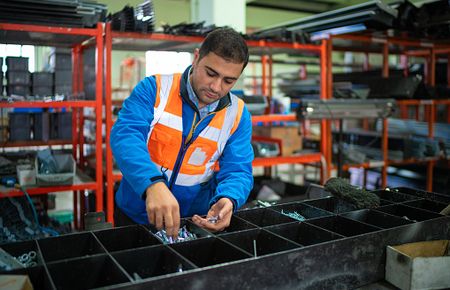
Spare Parts Inventory Management for Efficient Repairs
Insight - 76 min read, august 12, 2023.
In any maintenance or repair operation, having a well-managed spare parts inventory is crucial for ensuring efficiency and minimizing downtime. Without proper inventory management, repair operations can be delayed, costs can skyrocket, and customer satisfaction may suffer. This article will delve into the importance of spare parts inventory management, the key elements of an effective system, the steps to implement one, case studies of successful management, and future trends in the field.
Understanding the Importance of Spare Parts Inventory Management
When it comes to repairing equipment, spare parts play a critical role. Imagine a scenario where a technician has to fix a malfunctioning machine. If the necessary spare parts are not readily available, repairs can be significantly delayed, causing frustration for both customers and technicians. Proper inventory management ensures that the right parts are always in stock, reducing repair times and improving overall efficiency.
The Role of Spare Parts in Efficient Repairs
Spare parts act as the lifeline of repair operations. They are essential components that help restore equipment to its working condition. Having the right spare parts readily available ensures that repairs can be completed quickly and accurately. This leads to reduced equipment downtime and increases the chances of fixing issues on the first visit, improving customer satisfaction.
For example, imagine a technician arriving at a customer's location to repair a faulty industrial machine. With a well-managed spare parts inventory, the technician can quickly identify and retrieve the required components, minimizing the time spent searching for them. This efficient process allows the technician to complete the repair swiftly, minimizing the impact on the customer's operations and ensuring their satisfaction.
In addition, proper spare parts inventory management enables technicians to perform preventive maintenance effectively. By having a comprehensive stock of commonly used spare parts, technicians can proactively replace worn-out components during routine maintenance visits. This proactive approach helps prevent unexpected equipment failures and prolongs the lifespan of the machinery.
The Impact of Poor Inventory Management on Repair Efficiency
On the flip side, poor inventory management can have dire consequences for repair efficiency. Without accurate tracking and forecasting of spare parts, technicians may waste time searching for components, ordering parts at the last minute, or even having to reschedule repair appointments. This not only slows down the repair process but also increases costs due to rush shipping or emergency orders.
Imagine a scenario where a technician is unable to find a specific spare part in a disorganized inventory. The technician spends valuable time rummaging through shelves and bins, causing frustration and delaying the repair. This wasted time could have been avoided with a well-organized inventory system, where spare parts are neatly labeled and easily accessible.
Inefficient storage and disorganized inventory can also exacerbate the problem. Technicians may struggle to locate specific parts, leading to frustration and wasted time. Moreover, excess, obsolete, or expired inventory can tie up resources and reduce available space for critical spare parts.
For instance, imagine a scenario where a company has a surplus of outdated spare parts for older equipment models. These obsolete parts take up valuable storage space that could have been utilized for more frequently used components. As a result, when a technician needs a crucial spare part for a newer machine, they may have to spend extra time searching for it or even order it externally, causing delays in the repair process.
Furthermore, inadequate inventory management can lead to inaccurate forecasting, resulting in stockouts or overstock situations. Stockouts occur when a required spare part is not available, causing delays in repairs. On the other hand, overstock situations tie up valuable capital and storage space, leading to increased costs and inefficiencies.
In conclusion, effective spare parts inventory management is crucial for efficient repairs. It ensures that the right components are readily available, minimizing equipment downtime and improving customer satisfaction. On the other hand, poor inventory management can lead to delays, increased costs, and frustration for technicians and customers alike. By implementing robust inventory tracking systems and maintaining well-organized storage, businesses can optimize their repair operations and enhance overall efficiency.
Key Elements of Effective Spare Parts Inventory Management
To achieve efficient repairs, several key elements need to be considered when implementing a spare parts inventory management system.
Effective spare parts inventory management is crucial for any organization that relies on equipment and machinery to carry out its operations. By ensuring that the right spare parts are available at the right time, businesses can minimize downtime, increase productivity, and reduce costs. Let's explore some key elements that contribute to the effectiveness of spare parts inventory management.
Accurate Forecasting of Spare Parts Demand
Accurate forecasting of spare parts demand is essential to ensure that the right inventory levels are maintained. By analyzing historical data, monitoring equipment failure rates, and considering upcoming maintenance schedules, a reliable demand forecast can be generated. This helps determine optimal reorder points and quantities, preventing stockouts or excess inventory.
Furthermore, accurate forecasting enables organizations to anticipate spikes in demand due to seasonal factors or specific events. For example, a manufacturing company may experience increased demand for spare parts during the holiday season when production is at its peak. By incorporating such factors into the demand forecast, businesses can ensure that they have sufficient inventory to meet customer needs.
Regular Review and Replenishment of Inventory
Regularly reviewing and replenishing inventory is essential to maintain optimal stock levels. It involves conducting periodic cycle counts, comparing physical counts to system records, and identifying any discrepancies. By promptly addressing stockouts or excess inventory, repairs can be completed without delays or unnecessary costs.
In addition to regular reviews, organizations should also establish effective communication channels with suppliers to ensure timely replenishment of spare parts. This includes setting up automated systems that trigger reorder notifications when inventory levels reach a predetermined threshold. By streamlining the replenishment process, organizations can avoid disruptions in operations and maintain a smooth workflow.
Proper Storage and Organization of Spare Parts
Proper storage and organization represent another crucial element of spare parts inventory management. Implementing a logical and consistent storage system improves efficiency by reducing search time and minimizing the risk of damage or misplacement. It is essential to label and segregate parts by type, size, and usage, maintaining a clean and well-organized storage area.
Furthermore, organizations should consider implementing a digital inventory management system that provides real-time visibility of spare parts availability. This allows employees to quickly locate and retrieve the required parts, reducing downtime and improving overall productivity. By investing in proper storage and organization, organizations can optimize their spare parts management process and enhance operational efficiency.
In conclusion, effective spare parts inventory management is a critical aspect of any organization's operations. By accurately forecasting spare parts demand, regularly reviewing and replenishing inventory, and implementing proper storage and organization practices, businesses can ensure that they have the right parts available when needed. This not only minimizes downtime but also contributes to increased productivity, reduced costs, and improved customer satisfaction.
Implementing a Spare Parts Inventory Management System
Implementing a spare parts inventory management system requires careful planning and execution. By following a structured approach, organizations can optimize their inventory and reap the benefits of efficient repairs.
When it comes to managing spare parts, having an effective inventory management system in place is crucial. This system allows organizations to keep track of their spare parts, ensure they have the right parts available when needed, and minimize downtime caused by equipment failures.
However, implementing such a system is not a simple task. It requires a thorough evaluation of different inventory management options available in the market. Factors such as scalability, ease of use, integration capabilities with existing systems, and cost should all be taken into consideration. Selecting the most suitable system for your organization's needs ensures a smooth transition and long-term success.

Evaluating Different Inventory Management Systems
Before implementing a system, it is crucial to evaluate different inventory management options available in the market. Consider factors such as scalability, ease of use, integration capabilities with existing systems, and cost. Selecting the most suitable system for your organization's needs ensures a smooth transition and long-term success.
During the evaluation process, it is important to involve key stakeholders from various departments within the organization. Their input and feedback will provide valuable insights into the specific requirements and challenges faced by each department.
Additionally, it is advisable to seek recommendations and reviews from other organizations that have already implemented similar systems. Their experiences can serve as valuable resource and help in making informed decision.
Steps to Implement an Inventory Management System
Implementing an inventory management system involves several steps:
Identify and categorize spare parts: Classify spare parts based on factors such as criticality, usage frequency, and lead time. This step is crucial as it lays the foundation for effective inventory management.
Establish reorder points and quantities: Determine optimal reorder points and quantities based on demand forecasting and desired service levels. This ensures that you always have enough spare parts on hand without overstocking.
Implement inventory tracking: Utilize a digital system or barcode technology to track inventory movements, ensuring accurate and real-time inventory data. This allows for better visibility and control over spare parts, reducing the risk of stockouts or excess inventory.
Train staff: Provide comprehensive training to employees involved in spare parts management to ensure proper system utilization and adherence to procedures. This includes training on how to use the inventory management system, as well as educating them on the importance of accurate data entry and following established protocols.
Each of these steps requires careful planning and coordination. It is important to involve all relevant stakeholders and ensure clear communication throughout the implementation process.
Training Staff on the New System
Training staff on the new inventory management system is vital for successful implementation. Conduct training sessions to familiarize employees with the system's features, data entry protocols, and reporting capabilities. This empowers them to make informed decisions and follow best practices, ultimately leading to efficient spare parts management.
Training should be tailored to the specific roles and responsibilities of each employee involved in spare parts management. This ensures that they are equipped with the necessary knowledge and skills to effectively utilize the system.
In addition to initial training, it is important to provide ongoing support and refresher training as needed. This helps to reinforce the importance of accurate data entry, adherence to procedures, and continuous improvement in spare parts management.
By investing time and resources into training staff on the new system, organizations can maximize the benefits of their inventory management system and ensure its long-term success.
Case Studies of Successful Spare Parts Inventory Management
Examining real-life examples of successful spare parts inventory management provides valuable insights into best practices and benefits.
Effective spare parts inventory management is crucial for businesses to ensure smooth operations and minimize downtime. By implementing comprehensive systems and strategies, companies can optimize stock levels, streamline internal processes, and improve repair efficiency.
How Company A Improved Repair Efficiency
Company A, a large manufacturing facility, recognized the importance of efficient spare parts management and took proactive steps to enhance its processes. They implemented a comprehensive spare parts inventory management system that encompassed accurate demand forecasting, optimized stock levels, and streamlined internal processes.
By accurately forecasting demand, Company A was able to ensure that they had the necessary spare parts readily available when needed. This eliminated delays in repairs and significantly reduced equipment downtime by 30%. Technicians could access the required spare parts without delay, enabling faster repairs and improving overall repair efficiency.
Furthermore, the implementation of the inventory management system allowed Company A to identify and eliminate excess inventory, reducing costs and improving cash flow. The system also provided valuable data insights, enabling the company to make informed decisions regarding stock levels, procurement, and maintenance schedules.
Lessons from Company B's Inventory Management Overhaul
Company B, an industrial maintenance service provider, faced significant challenges due to ineffective spare parts management. They experienced delays in repairs, excessive inventory, and increased turnaround times, negatively impacting their overall service quality and customer satisfaction.
Realizing the need for a major overhaul, Company B implemented an inventory management system that addressed its pain points. The system incorporated proper demand forecasting, regular inventory review, and efficient organization practices.
With the new system in place, repair efficiency improved by 25% as technicians had easy access to the required spare parts, reducing repair time and minimizing equipment downtime. Furthermore, the implementation of proper demand forecasting allowed Company B to optimize stock levels, ensuring they had the right parts available without holding excessive inventory.
The inventory management overhaul also resulted in decreased turnaround times, enabling Company B to deliver high-quality repairs promptly. By streamlining its processes and eliminating inefficiencies, the company not only improved its service quality but also optimized costs and enhanced customer satisfaction.
These case studies highlight the importance of effective spare parts inventory management in various industries. By implementing comprehensive systems and strategies, businesses can reduce equipment downtime, improve repair efficiency, minimize inventory costs, and enhance overall operational performance.
Future Trends in Spare Parts Inventory Management
The field of spare parts inventory management continues to evolve, with emerging trends shaping the future.
As technology continues to advance at a rapid pace, it is no surprise that it is playing a significant role in spare parts inventory management. Advancements in predictive analytics and machine learning algorithms are revolutionizing the way organizations handle their inventory. These technologies help forecast demand more accurately, identify patterns in failure rates, and optimize inventory levels automatically. By implementing these tools, organizations can stay ahead of maintenance needs and maximize repair efficiency.
But technology is not the only factor shaping the future of spare parts inventory management. Sustainability is also gaining significant importance in this field. Organizations are increasingly adopting environmentally conscious practices to reduce waste and minimize the environmental impact of maintaining and repairing equipment. Recycling or reusing parts not only contributes to protecting the planet but also streamlines inventory management processes.
Furthermore, organizations are realizing the importance of spare parts inventory management in ensuring customer satisfaction. Efficient management of spare parts is crucial for minimizing repair time and meeting customer demands. By understanding the significance of spare parts, implementing key elements of an effective system, studying successful case studies, and considering future trends, organizations can optimize their repair operations and stay competitive in a rapidly evolving marketplace.
The future of spare parts inventory management is exciting and full of potential. With technology advancements and sustainable practices on the rise, organizations have the opportunity to transform their inventory management processes. By embracing these trends and continuously adapting to new developments, organizations can ensure they are well-prepared for the challenges and opportunities that lie ahead.
Join our inventory mailing list to get early access to our best deals
- Help & FAQ
Improved Spare Parts Inventory Management: A Case Study
- Research Group: Operations Research
Research output : Working paper › Discussion paper › Other research output
Publication series
- inventory models
- forecasting
Access to Document
Fingerprint.
- Spare Parts Business & Economics 100%
- Inventory Management Business & Economics 85%
- Service Levels Business & Economics 55%
- Lead Time Business & Economics 51%
- Intermittent Demand Business & Economics 42%
- Gamma Distribution Business & Economics 37%
- Production Plant Business & Economics 35%
- Demand Forecast Business & Economics 31%
T1 - Improved Spare Parts Inventory Management
T2 - A Case Study
AU - Strijbosch, L.W.G.
AU - Heuts, R.M.J.
AU - van der Schoot, E.H.M.
N1 - Pagination: 24
N2 - This paper examines the performance of two different (s,Q) inventory models for spare parts in a production plant of confectionery in The Netherlands, a simple and an advanced model. The simple approach is more or less standard: undershoot of the reorder level is not taken into account, the normal distribution is used as the distribution of demand during lead-time. The advanced one takes undershoots into account, differentiates between zero and nonzero demands during lead-time, and utilizes the gamma distribution as the demand distribution. Both models are fed with parameters estimated by a procedure that forecasts demand sizes and time between demand occurrences separately (intermittent demand). The results show that the advanced approach yields service levels close to the desired one under many circumstances, while the simple approach is not consistent leading to much larger inventories if one wants to be sure that the service level is obtained for all spare parts.
AB - This paper examines the performance of two different (s,Q) inventory models for spare parts in a production plant of confectionery in The Netherlands, a simple and an advanced model. The simple approach is more or less standard: undershoot of the reorder level is not taken into account, the normal distribution is used as the distribution of demand during lead-time. The advanced one takes undershoots into account, differentiates between zero and nonzero demands during lead-time, and utilizes the gamma distribution as the demand distribution. Both models are fed with parameters estimated by a procedure that forecasts demand sizes and time between demand occurrences separately (intermittent demand). The results show that the advanced approach yields service levels close to the desired one under many circumstances, while the simple approach is not consistent leading to much larger inventories if one wants to be sure that the service level is obtained for all spare parts.
KW - inventory models
KW - simulation
KW - demand
KW - forecasting
M3 - Discussion paper
VL - 1998-135
T3 - CentER Discussion Paper
BT - Improved Spare Parts Inventory Management
PB - Econometrics
CY - Tilburg
- OSCM Publications
- Volume 11, Issue 3, 2018
Strategies for Managing Excess and Dead Inventories: A Case Study of Spare Parts Inventories in the Elevator Equipment Industry
- Oguji Nnamdi 1 (University of Vaasa, Finland)
DOI: http://doi.org/10.31387/oscm0320209
Get rights: open access
In this article:
- Introduction
- Related work
- Methodology
Article tags
Other links.
- Other articles in this volume
- OSCM volumes
- OSCM conference proceedings
- OSCM forthcoming list
APA Citation
Copyright © 2020 - All Rights Reserved - OSCM Journal .
Template by OS Templates , Bootstrap 4 empowered | OSCM Dev
Academia.edu no longer supports Internet Explorer.
To browse Academia.edu and the wider internet faster and more securely, please take a few seconds to upgrade your browser .
Enter the email address you signed up with and we'll email you a reset link.
- We're Hiring!
- Help Center
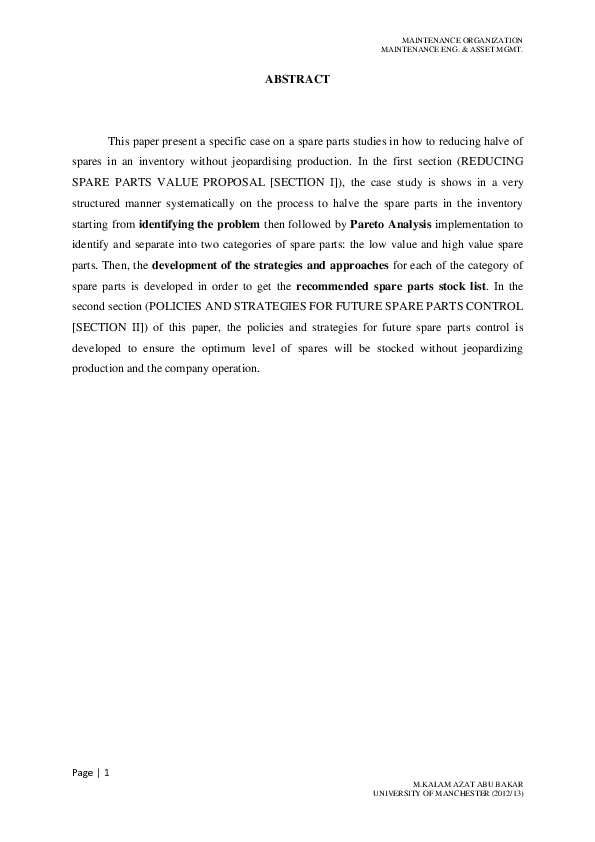
A STUDY OF SPARE PARTS INVENTORY MANAGEMENT: CASE STUDY OF REDUCTION HALVE SPARES INTO OPTIMUM LEVEL

This paper present a specific case on a spare parts studies in how to reducing halve of spares in an inventory without jeopardising production. In the first section (REDUCING SPARE PARTS VALUE PROPOSAL [SECTION I]), the case study is shows in a very structured manner systematically on the process to halve the spare parts in the inventory starting from identifying the problem then followed by Pareto Analysis implementation to identify and separate into two categories of spare parts: the low value and high value spare parts. Then, the development of the strategies and approaches for each of the category of spare parts is developed in order to get the recommended spare parts stock list. In the second section (POLICIES AND STRATEGIES FOR FUTURE SPARE PARTS CONTROL [SECTION II]) of this paper, the policies and strategies for future spare parts control is developed to ensure the optimum level of spares will be stocked without jeopardizing production and the company operation.
Related Papers
Evaluating Effective Spare-parts Inventory Management for Equipment Reliability in Manufacturing Industries
Nazim Baluch
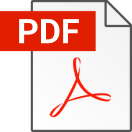
International Journal of Production Economics
Liliane Pintelon , Geert Waeyenbergh , Herman Baets
Mohamed Abdisalam
Aleksandar Pudar
i. Abstract An improvement of the inventory policy at RNBV was made in the first quarter of 2015. At the start we have determined that significant inventoried spares have been used randomly, i.e. spares were used when parts fail or as apart of PMS scheduled overhaul. To solve the problem of reducing an extensive inventory but keep enough to allow an uninterrupted service and be in line with industry standards and TMSA 3 requirements. We created a proper and financially efficient multi-layered inventory policy using classification scale and method linked to vibration monitoring and predictive maintenance together with risk assessment for each equipment and spare part within machinery. The arrangement can be divided in to: • Start – the parts were nominated with regards to suppliers lead time and the cost of off-hire due to failure and an RA matrix to ensure that the most critical items were identified. • Development - use of a developed preventive maintenance program and vibration monitoring results where applicable for the most critical parts to minimise downtime due to failure was ensured. • Standardisation - critical parts were standardised across the fleet to reduce the inventory rating financial savings while keeping the same level of service to the customers, and in the same time, we kept spares on the Critical Spare Parts List ship specific to avoid mix up. Preparation for this showed that the company had an extensive inventory and efficient reduction of its size was possible by focusing on critical parts. This article objective is to demonstrate a real and economically efficient inventory policy used in RNBV Company.
Journal of Manufacturing Technology Management
Jukka Tuomi
Production Planning & Control
Nicola Saccani
pasquale colonna
Resenha do livro: ALMEIDA, Maria Elizabeth Bianconcini de; VALENTE, José Armando. Tecnologias e currículo: trajetórias convergentes ou divergentes? São Paulo: Paulus, 2011.
RELATED PAPERS
Proceedings of the 7th WSEAS International …
Toomas Raus
Balanici Alexandru
Journal of Coordination Chemistry
Ricardo Valdez González
Information Polity
Pauline Pollard
Jane Moreira
Revista Brasileira de Otorrinolaringologia
Antônio José Cortez Juares
Diamond and Related Materials
Enciclopédia Biosfera
Aline Silva
Plant and Soil
Thiago Viana Barbosa
Archives of Pediatrics & Adolescent Medicine
Critical Reviews in Neurosurgery
Wojtek Kociemba
Pesquisa Agropecuária Tropical
Antonella Perez
Proceedings of the 19th …
Keith Bristow
Pinisi discretion review
Amalia Intan
Journal-Financial Economy
Eliseo Cano Ramírez
BMC Public Health
Yvonne Heerkens
Physical Review A
Flavia Dabbur
Accreditation and Quality Assurance
Adriaan M.H. van der Veen
Sanket Patel
多伦多大学毕业证书 购买加拿大学历Uof文凭学位证书
실시간카지노 토토사이트
RELATED TOPICS
- We're Hiring!
- Help Center
- Find new research papers in:
- Health Sciences
- Earth Sciences
- Cognitive Science
- Mathematics
- Computer Science
- Academia ©2024

IMAGES
VIDEO
COMMENTS
The case study presented in this paper shows how the adoption of a s tructured spare parts (inventory) manag ement methodology m ay provide significant benefits t o industrial org anisations that ...
Spare parts are held as inventory to support product maintenance in order to reduce downtime and extend the lifetime of products. Recently, spare parts inventory management has been attracting more attention due to the "right-to-repair" movement which requires that manufacturers provide sufficient spare parts throughout the life-cyle of their products to reduce waste so as to achieve ...
3. Methodology The proposed approach consists of two sequential steps: 1) the classification of spare parts and 2) the development of a simulation model to reproduce the inventory policy and identify the optimal setting for the relevant items. The classification of items has been structured into two sequential phases.
Abstract. Spare parts inventory management is crucial in the success of a service providing company. In this study, the spare parts of a service provider in the automotive sector are classified according to their characteristics in groups and different inventory control policies are applied to the categorized groups.
The proposed multi-criteria spare parts classificati approach is simple and straightforward enough to be understood by company managers, thus increasing the probability of its adoption (in the same or similar form) in other settings. The aim of this paper is to propose and discuss a h ier rchical multi-criteria spare parts classificati on method developed for inventory management purposes and ...
Spare parts management is not currently supported by the CMMS of the company. The inventory management of spare parts is done by performing the record in the ERP system and also in a "supermarket" of material that is used for maintenance actions. In this paper, a multi-criteria classification of spare parts is developed in order to assign an ...
22 CHAPTER 4 Case Study 4.1 Spare Parts Inventory Management system - a Case Study The spare part inventory management system (SPIMS) of dealers was studied of XYZ Company. This research was limited to focus on the spare part dealers to the area of Punjab. To carry out the study, an elaborate schedule of visits to the dealers was chalked out.
1 Improved spare parts inventory management: a case study L.W.G. Strijbosch 1, R.M.J. Heuts2 and E.H.M. van der Schoot3 1 Faculty of Economics and Business Administration, Tilburg University, P.O. Box 90153, 5000 LE Tilburg, The Netherlands 2 CentER for Economic Research, Tilburg University, P.O. Box 90153, 5000 LE Tilburg, The Netherlands 3 CMG Trade, Transport & Industry, SAP Competence ...
2.1 Spare Parts Management The relevance of the management of spare parts, and its impact on inventory costs among several industries, especially manufacturing, have been discussed in the literature (Gallagher, Mitchke, & Rogers, 2005). The appropriate inventory management is of critical importance in every industry. However, the
Improved Spare Parts Inventory Management: A Case Study. This paper examines the performance of two different (s,Q) inventory models for spare parts in a production plant of confectionery in The Netherlands, a simple and an advanced model. The simple approach is more or less standard: undershoot of the reorder level is not taken into account ...
These case studies highlight the importance of effective spare parts inventory management in various industries. By implementing comprehensive systems and strategies, businesses can reduce equipment downtime, improve repair efficiency, minimize inventory costs, and enhance overall operational performance.
Abstract. This paper examines the performance of two different (s,Q) inventory models for spare parts in a production plant of confectionery in The Netherlands, a simple and an advanced model. The simple approach is more or less standard: undershoot of the reorder level is not taken into account, the normal distribution is used as the ...
A case study-based analysis of spare parts management in the engineering industry. ... previous research in spare parts supply chain management has principally been limited to planning and operational aspects such as the determination of spare parts inventory levels and re-order policies. Taking the sellers' perspective in the supply chain ...
Improved Spare Parts Inventory Management: A Case Study. This paper examines the performance of two different (s,Q) inventory models for spare parts in a production plant of confectionery in The Netherlands, a simple and an advanced model. The simple approach is more or less standard: undershoot of the reorder level is not taken into account ...
This case study Phillip Slater takes you through a program of designing and then implementing policies and procedures for engineering materials and inventory...
The paper deals with three aspects: 1) a description of the elements of complexity peculiar to the spare parts supply chain; 2) a framework and a literature review about spare parts demand and inventory management approaches and models; 3) the analysis of five case studies, suggesting a gap between theoretical approaches and the ones adopted in ...
Q2: How can the selected forecasting methods be implemented in the company's case? 1.3. Research methodology In order to answer the research questions, the study is designed so that the research methodology is a quantitative method in a single case study. In detail, the study employs a
Nnamdi, O. (2018). Strategies for Managing Excess and Dead Inventories: A Case Study of Spare Parts Inventories in the Elevator Equipment Industry. Operations and Supply Chain Management: An International Journal, 11(3), 128-138.
A STUDY OF SPARE PARTS INVENTORY MANAGEMENT: CASE STUDY OF REDUCTION HALVE SPARES INTO OPTIMUM LEVEL. M.Kalam Azat. This paper present a specific case on a spare parts studies in how to reducing halve of spares in an inventory without jeopardising production. In the first section (REDUCING SPARE PARTS VALUE PROPOSAL [SECTION I]), the case study ...